Материалы подшипников скольжения.
Материалы вкладышей подразделяются на три группы: металлические, металлокерамические, неметаллические. В качестве металлических материалов в подшипниках скольжения используются твердые (не менее 100 НВ), мягкие (50... 100 НВ) и пластичные (твердость не более 50 НВ). К твердым материалам относятся чугуны и алюминиево-железистые бронзы, к мягким — оловянные бронзы, а к пластичным — свинцовые бронзы, баббиты и алюминиевые сплавы. Серый чугун применяется при невысоких скоростях. Применяются также чугуны антифрикционные, высокопрочные АВЧ и ковкие АЧК.
Бронзы, являющиеся медными сплавами с различными легирующими элементами, по химическому составу подразделяются на оловянные и безоловянные. Они характеризуются лучшими по сравнению с чугунами антифрикционными свойствами, хорошей коррозионной стойкостью и повышенным сопротивлением усталости, эффективно обрабатываются резанием.
Баббиты — сплавы на основе олова и свинца — отличаются лучшими антифрикционными свойствами, хорошей прирабатываемостью, износостойкостью, пластичностью и небольшим коэффициентом трения. Основным недостатком баббитов является сравнительно низкая выносливость, особенно при высокой температуре. Заменителями баббитов и бронз могут быть достаточно дешевые сплавы на основе цинк — алюминий — медь, обладающие хорошими антифрикционными свойствами, но при этом плохой прирабатываемостью и низкой допустимой рабочей температурой.
|
|
При больших нагрузках, но малых скоростях скольжения возможно использование латунных вкладышей, которые относительно дешевы и легко обрабатываются.
Металлокерамические материалы для изготовления вкладышей подшипников получаются путем высокотемпературного прессования (спекания) порошков бронзы или железа с добавлением графита, меди, олова или свинца, что обеспечивает их высокую (до 30 % объема) пористость и, следовательно, хорошую пропитку маслом — до 15... 30 % объема вкладыша.
К неметаллическим материалам относятся полимерные и композиционные материалы, пластмассы, текстолит, фторопласт ДСП, дерево (бакаут, самшит и другие твердые породы), резина.
Порядок сборки подшипников скольжения.
Сборка цельных подшипников скольжения заключается в установке втулки в корпус, стопорении ее во избежание проворачивания и подгонке отверстия по валу. Перед сборкой сопрягаемые поверхности втулки, корпуса и вала очищают, удаляют риски и задиры. Перед запрессовкой втулки ее смазывают маслом.
Втулки с отверстиями для подачи смазки к валу устанавливают так, чтобы масляные отверстия и отверстия под стопорные болты во втулках совпадали с соответствующими отверстиями в корпусе. Втулки запрессовывают вручную при помощи молотка и накладки, под прессом или при помощи приспособления.
|
|
После запрессовки втулку закрепляют, чтобы она не проворачивалась. При стопорении втулки штифтом его устанавливают в отверстие с натягом и с торца расклепывают, а затем зачищают заподлицо с основным металлом.
При запрессовке цельных тонкостенных втулок их внутренний диаметр уменьшается. Поэтому такие втулки дополнительно обрабатывают (развертывают, растачивают или протягивают) под требуемый размер. После обработки втулки по внутреннему диаметру она должна иметь правильную цилиндрическую форму, не иметь вмятин, выпуклостей и забоин.
Неправильно установленную втулку необходимо выпрессовать и на ее место запрессовать новую.
Контроль качества сборки подшипников качения и скольжения
В подшипниках качения различают радиальные и осевые зазоры.
Радиальные зазоры проверяют на отсутствие качки после установки колец на вал и в корпус. При этом подшипник при проворачивании вручную должен вращаться легко и плавно.
Осевые зазоры регулируют за счет смещения одного кольца относительно другого, проворачивая кольцо с телами качения для правильной их самоустановки.
|
|
Напрессованные на вал кольца упорных подшипников проверяют на осевое биение с помощью индикатора. После установки подшипников качения проверяют плотность прилегания колец к заплечникам вала с помощью щупа, который вводят в зазор между заплечником вала и подшипниковым кольцом.
Для демонтажа подшипниковых узлов применяют специальные приспособления — съемники.
Основной критерий работоспособности подшипника скольжения — правильная установка подшипниковых опор, обеспечивающая их соосность. Соосность установки подшипниковых опор можно проверить: эталонным валом, линейкой (рис. 3, а) и щупом, струной (рис. 3, б) и штихмасом, микрометрическим нутромером, оптическим методом
Рис. 3. Схемы проверки подшипников
а — линейкой; б — струной; в –струной, включенной в электрическую цепь; 1 — стойка; 2 — ролик; Н— расстояние между струной и основанием опоры; h — расстояние от нониуса линейки до опоры
Эталонный вал рассчитывают таким образом, чтобы его диаметр имел отклонения от номинального размера, соответствующие допустимым отклонениям от соосности. Он должен проходить во все втулки и легко вращаться в подшипниках.
|
|
Струну, которую подключают к электрической схеме низкого напряжения (рис. 3, в), применяют в тех случаях, когда требуется повысить точность установки опор. В момент касания измерительным инструментом струны и расточки в корпусе подшипника происходит замыкание электрической цепи, загорается сигнальная лампочка.
Оптические методы контроля с применением специальных приборов — коллиматора и телескопа или автоколлиматора и зеркала дают наибольшую точность соосности подшипниковых опор.
Динамометры применяют для контроля точности сборки отдельно стоящих подшипниковых опор. С их помощью измеряют нагрузки под каждой опорой. Динамометры устанавливают в лапах подшипниковых опор и по их показаниям регулируют положение осей. Этот метод применяют при контроле соосности крупногабаритных подшипников.
После контроля соосности опор подшипников скольжения приступают к сборке и пригонке вкладышей подшипников к шейкам валов, предварительно притертым и покрытым тонким слоем краски.
Дата добавления: 2022-11-11; просмотров: 31; Мы поможем в написании вашей работы! |
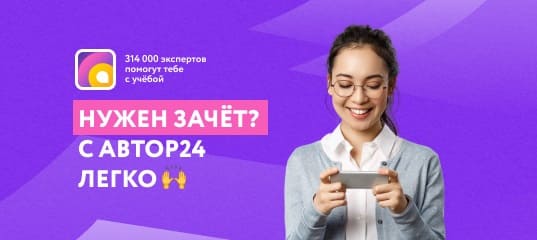
Мы поможем в написании ваших работ!