Десульфурация металла при вакуум-шлаковой обработке
Технологическиее расчеты
Десульфурация металла в открытом процессе
1) Постановка задачи
Обосновать расчетом влияние интенсивности продувки инертным газом на динамику десульфурации металла шлаком в ковше при атмосферном давлении.
2) Исходные данные
Химический состав шлака представлен в таблице 4.1
Таблица 4.1– Химический состав шлака
Химический состав шлака, мас% | ||||||
CaO | MgO | MnO | FeO | SiO2 | Al2O3 | сумма |
67,88 | 6,91 | 0,94 | 0,92 | 19,24 | 4,11 | 100 |
Кратность шлака =0.03
Химический состав металла представлен в таблице 4.2
Таблица 4.2– Химический состав металла
Химический состав металла перед обработкой, мас % | |||||
C | Si | Mn | Cr | Ni | Mo |
0,62 | 0,51 | 0,70 | 0,381 | 0,048 | <0,005 |
V | Ti | Al | P | S | Cu |
0,0052 | 0,0026 | 0,0021 | 0,0093 | 0,02 | 0,009 |
Температура,оС………………………………………………………….. 1550
Масса металла в ковше,т………………………………………………….150
Глубина металла в ковше, м…………………………………………….… 4
Расходы инертного газа, л/мин…………………………………...……...300;
3) Расчет
Оценить сульфидную емкость шлака можно, используя соотношение, авторами которого являются Тинг и Катаяма
, , (4.1)
где СS – сульфидная емкость шлака;
Т – температура, К;
Ni – мольные доли соответствующих оксидов.
Расчет мольных долей компонентов шлака
Результаты представим в таблицу 4.3.
Таблица 4.3– Мольные доли компонентов шлака
|
|
Компонент | CaO | MgO | MnO | FeO | SiO2 | Al2O3 | сумма |
мас% | 67,88 | 6,91 | 0,94 | 0,92 | 19,24 | 4,11 | 100 |
М,г/моль | 56 | 40 | 71 | 72 | 60 | 102 | |
n, моль | 1,21 | 0,17 | 0,013 | 0,012 | 0,32 | 0,04 | 1,765 |
Х, доли | 0,69 | 0,097 | 0,007 | 0,0067 | 0,18 | 0,023 |
0,022.
3.3) Расчет окислительного потенциала системы
Расчет окисленности металла
Принимаем окисленность металла 30 ppm.
Соответственно, [O] = 3,0·10-3 %.
Расчет окислительного потенциала системы
(4.2)
3.4) Расчет коэффициента активности серы в металле
Для расчета необходимы справочные данные по параметрам взаимодействия см. таблицу 4.4.
Таблица 4.4–Параметры взаимодействия первого порядка esi * 102 C
Химический состав металла перед обработкой, мас % | |||||
C | Si | Mn | Cr | Ni | Mo |
11 | 6,3 | -2,6 | -1,1 | 0 | 0,27 |
V | Ti | Al | P | S | Cu |
-1,6 | -7,2 | 3,5 | 29 | -2,8 | -0,84 |
(4.3)
где - параметры взаимодействия газа с компонентами металла;
[% i] – концентрации компонентов металла, %
lg ɣs = 0,078;
ɣs = 1,2.
3.5) Расчет константы равновесия реакции ½{S2} = [S]
(4.4)
Тогда K[S] = 397,83.
3.6) Расчет коэффициента распределения серы
|
|
(4.5)
3.7) Расчет равновесной концентрации серы
(4.6)
3.8) Расчет удельной мощности перемешивания
Расчет удельной интенсивности продувки
(4.7)
где Q – расход газа, л/мин;
М – масса металла, т.
Результаты расчета представлены в таблице 4.5.
Таблица 4.5– Удельная интенсивность продувки
Q, л/мин | 300 |
G, м3/(кг·с) | 3,3·10-8 |
Расчет удельной мощности перемешивания
(4.8)
где G – удельная интенсивность продувки;
м3/(кг·с);
ρ – плотность металла, кг/м3;
g – ускорение свободного падения;
H – высота металла в ковше (глубина погружения фурмы), м.
Результаты расчета представлены в таблице 4.6.
Таблица 4.6– Удельная мощность перемешивания
Q, л/мин | 300 |
ɛ, Вт/кг | 0,057 |
3.9) Расчет коэффициента объемного массопереноса
(4.9)
Результаты расчета представлены в таблице 4.7.
Таблица 4.7–Коэффициент объемного массопроцесса
Q, л/мин | 300 |
kv, 1/c | 1,2·10-3 |
3.10) Расчет динамики десульфурации
Пример расчета текущего содержания серы через 10 минут обработки для расхода аргона 300 л/мин приведен ниже (время подставляется в секундах).
|
|
[S]=0,0076+(0,02-0,0076)*eхр(-1,2·10-4*10*60)=0,0136 %
Минимальное значение обработки рельсовой стали по регламенту на «печь-ковше» не менее 30 мин.
Данные расчетов приведем таблице 4.8.
Таблица 4.8– Динамика десульфурации при перемещивании 300 л/мин
Время, мин | % удаления [S] |
0 | 0,02 |
30 | 0,009 |
35 | 0,0085 |
40 | 0,0082 |
45 | 0,0081 |
50 | 0,0079 |
55 | 0,0078 |
60 | 0,0077 |
Полученные данные представим в виде графика на рис. 4.1.
Время, мин |

Рисунок 4.1– Динамика десульфурации
Десульфурация металла при вакуум-шлаковой обработке
1) Постановка задачи Оценить кратность шлака для заданной глубины рафинирования металла от серы в условиях вакуум-шлаковой обработки.
Исходные данные представлены в таблице 4.9 – 4.11.
Таблица 4.9– Химический состав шлака
Химический состав шлака, мас% | ||||||
CaO | MgO | MnO | FeO | SiO2 | Al2O3 | сумма |
67,8 | 6,91 | 0,94 | 0,92 | 19,24 | 4,11 | 100 |
Кратность шлака =0.03
Таблица 4.10– Химический состав металла
Химический состав металла перед обработкой, мас % | |||||
C | Si | Mn | Cr | Ni | Mo |
0,76 | 0,55 | 0,78 | 0,414 | 0,049 | <0,005 |
V | Ti | Al | P | S | Cu |
0,011 | 0,0031 | 0,0036 | 0,011 | 0,014 | 0,009 |
Температура, оС …………………………………………………………1550
|
|
Масса металла в ковше, т ………………………………………………..150
Остаточное давление в вакуумной камере, атм ……………………... 0,001
Доля СО в удаляемых газах ………………………………………………0,3
Таблица 4.11– Содержание серы в металле
Содержание серы в металле после обработки, % | ||||
0.005 | 0.004 | 0.003 | 0.002 | 0.001 |
3) Расчет
Оценить сульфидную емкость шлака можно, используя соотношение, авторами которого являются Тинг и Катаяма (4.1)
Результаты представим в таблицу 4.12.
Таблица 4.12– Мольные доли компонентов шлака
Компонент | CaO | MgO | MnO | FeO | SiO2 | Al2O3 | сумма |
мас% | 67,88 | 6,91 | 0,94 | 0,92 | 19,24 | 4,11 | 100 |
М,г/моль | 56 | 40 | 71 | 72 | 60 | 102 | |
n, моль | 1,21 | 0,17 | 0 | 0 | 0,32 | 0,04 | 1,74 |
Х, доли | 0,69 | 0,097 | 0 | 0 | 0,18 | 0,023 |
;
0,022.
3.3) Расчет окислительного потенциала системы
Расчет окисленности металла
Принимаем окисленность металла 5 ppm.
Соответственно, [O] = 5,0·10-4 %.
Расчет окислительного потенциала системы (4.2)
3.4) Расчет коэффициента активности серы в металле
Для расчета необходимы справочные данные по параметрам взаимодействия, которые представлены в таблице 4.13.
Таблица 4.13– Параметры взаимодействия первого порядка esi * 102 C
Химический состав металла перед обработкой, мас % | |||||
C | Si | Mn | Cr | Ni | Mo |
11 | 6,3 | -2,6 | -1,1 | 0 | 0,27 |
V | Ti | Al | P | S | Cu |
-1,6 | -7,2 | 3,5 | 29 | -2,8 | -0,84 |
Расчет ктивности серы в металле произведем по формуле (4.3)
;
lg ɣs = 0,094;
ɣs = 1,3.
3.5) Расчет константы равновесия реакции (4.4)
Тогда K[S] = 397,83.
3.6) Расчет коэффициента распределения серы (4.5)
Ls=0,0031*( ) -1/2*1,3*1/397,83= 440
3.7) Расчет требуемой кратности шлака
Для получения в конце обработки в металле 0,005% серы необходима кратность шлака не менее
(4.10)
Для других содержаний серы результаты расчета представлены в таблице 4.14
Таблица 4.14– Отношение содержания серы в металле к кратности шлака
[S]к, % | 0.005 | 0.004 | 0.003 | 0.002 | 0.001 |
λ | 0,004 | 0,005 | 0,008 | 0,013 | 0,029 |
На основании расчета строим зависимость требуемой кратности шлака от конечного содержания серы, которая отображена на рис. 4.2
Конечное содержание серы, % |


Рисунок 4.2– Зависимость кратности шлака от [S]
Дата добавления: 2022-11-11; просмотров: 36; Мы поможем в написании вашей работы! |
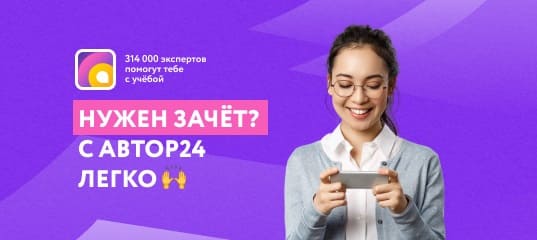
Мы поможем в написании ваших работ!