Организация рабочих мест и техника безопасности.
ЛАБОРАТОРНАЯ РАБОТА № 18
Разработка технологического процесса восстановления деталей гальваническими покрытиями
Цель работы: ознакомиться с технологией нанесения гальванических покрытий, научиться рассчитывать режимы и нормы времени.
Выполнил: ст. Прохоров К. , гр.18СХТ-1
Хромирование шеек под подшипники на ведущей шестерне заднего моста автомобиля I A 5-53А:
1. Токоподводящая штанга;
2. Крючок;
3. Гайка;
4. Изоляционная втулка;
5. Хромируемые поверхности;
6. Защитный чехол.
Порядок выполнения
1.Подготовка детали
- механическая обработка поверхностей, подлежащих наращиванию: путем обработки шлифовальной шкуркой или мягкими кругами с полировальной пастой
- очистка детали от окислов и предварительное обезжиривание: : путем промывки в растворителях (уайт-спирите, дихлорэтане, бензине и др.) с последующей промывкой в воде;
- монтаж детали на подвесное приспособление: необходимо обеспечить их надежный электрический контакт с токопроводящей штангой
- изоляция поверхностей, не подлежащих покрытию: используют цапонлак в смеси с нитроэмалью в соотношении 1:2 (его наносят в несколько слоев при послойной сушке на воздухе); чехлы из полихлорвинилового пластиката толщиной 0,3 ... 0,5 мм; различные футляры, втулки, экраны, изготовленные из неэлектропроводных кислотостойких материалов (эбонит, текстолит, винипласт и т. п.).
|
|
- обезжиривание детали: путем электрохимической обработки в щелочных растворах следующего состава: едкий натр -10 кг/м3, сода кальцинированная — 25 кг/м3, тринатрийфосфат — 25 кг/м3, эмульгатор ОП-7 3...5 кг/м3. Режим обезжиривания: температура раствора 70...80°С; плотность тока 5... 10 А/дм; длительность процесса 1 ... 2 мин; промывают в горячей, а затем в холодной воде. Сплошная без разрывов пленка воды на обезжиренной поверхности свидетельствует о хорошем качестве удаления жиров.
- анодная обработка (активация): производят в основном электролите. Детали завешивают в ванну для хромирования и для прогрева выдерживают 1 ...2 мин без тока, а затем подвергают обработке на аноде в течение 30... 45 с при анодной плотности тока 25 ... 35 А/дм.
Режим процессов
<Молочный> хром - осадки беловатого цвета -имеет очень низкую пористость и почти не имеет трещин; его осаждают при температуре 65-70 °С и пониженной плотности тока 30-40 А/дм 2 . Максимальная твердость покрытий достигается при температуре около 40 °С и при плотности тока около 40 Nдм 2 , а максимальная износостойкость - при 60 °С и 60 А/дм 2 . В среднем оптимальная температура процесса 55-60 °С.
Приготовление электролита
В качестве электролита при хромировании применяется водный раствор хромового ангидрида (СгОз) , раствор которого в воде является сильной кислотой, точнее, смесью кислот H 2 Cr0 4 и H 2 Cr 2 O 7 . Добавление анионов сульфата $0 4 , обычно в виде серной кислоты. Концентрация хромового ангидрида может изменяться в электролите в пределах 150.. .400 кг/м3. Концентрация серной кислоты должна соответствовать отношению H2SO4: СгОз = 1:100.
|
|
. Расчетное количество CrO 3 растворяют (если необходимо, большие куски предварительно дробят) в 0,6 общего объема воды при температуре 60-80 °С. Вода должна быть свободна от ионов железа, поэтому лучше использовать конденсат или дистиллат. Прежде чем добавлять сульфат, необходимо проанализировать полученный раствор на содержание ионов сульфата. Если сульфат находится в избытке, его следует высадить путем добавления рассчитанного количества углекислого бария (предварительно смешанного с водой). Количество углекислого бария должно превышать количество сульфата в 2,2 раза. Затем раствор перемешивают и дают отстояться, после чего декантируют (сливают с осадка). Только после этого можно добавлять серную кислоту. Готовый раствор должен содержать около 3 г /л трехвалентных ионов хрома (не более 10 r/л) и не более 10 г/л ионов железа. Раствор прорабатывают током при температуре 50 °С при катодной плотности тока 15-20 А/дм 2 и анодной плотности тока 1,5-2 А/дм 2 . Пропускают до 6-8 ампер-часов на литр раствора. Окончательно полученный раствор не должен содержать нитратов.
|
|
Условием нормальной эксrшуатации электролита является содержание в нем 3-8 r / л этих ионов, так как они непосредственно участвуют в механизме хромирования, входя в состав прикатодноrо слоя Слишком большие концентрации ионов Cr3+ также недопустимы.
Плотность тока, при которой работают ванны хромирования, значительно выше, чем обычно применяют в гальванотехнике, и достигает 100 А/дм 2 . Рабочая температура при хромировании в среднем около 55 °С, плотность тока 0,50-0,55 А/см 2 . Важно при хромировании поддерживать соотношение между температурой и плотностью тока. Обычно повышение температуры на l rр или повышение концентрации хромовой кислоты на 10 r /л соответствует повышению плотности тока на 2 А/дм 2. Массивные детали иногда приходится предварительно прогревать в воде (это лучше, чем прогревать уже в раствор•е хромирования до включения тока.
Аноды
Хромирование выполняют с нерастворимыми свинцовыми анодами. Лучше себя ведут свинцовые аноды, содержащие сурьму или олово (5-8%) либо сурьму вместе с оловом.
|
|
Расчёт режима и норм времени
Толщина h, мм, осаждаемого металлического покрытия
= = 0,0000021мм
где Dк - рекомендованная для данного электролита и его температуры катодная плотность тока, А/дм2;
c - электрохимический эквивалент, г/ А*ч; (железнение c =1,042; хромирование c =0,323; никелирование c =1,095)
η — выход по току, %, (железнение – 90%; хромирование – 15%; никелирование – 50%)
t — продолжительность электролиза, ч;
γ — плотность металла, г/см3; (железнение γ =7,8; хромирование γ =6,9; никелирование γ =8,9).
Сила тока при нанесении покрытий
=0,5х 17,55= 9А
где - катодная плотность тока, А/дм2;
- площадь покрываемой поверхности, дм2.
Площадь анода
=2 17,55=35,1
Основное время :
= =0,57 ч
Норма времени
= = 0,5 ч
где Т1 - время на загрузку и выгрузку деталей (Т1 =0,2 ч);
КПЗ - коэффициент подготовительно-заключительного времени (КПЗ=1,2);
пД - число деталей, одновременно наращиваемых в ванне (пД =1);
пн - коэффициент использования ванны ( пн =0,8).
Организация рабочих мест и техника безопасности.
Ванны для нанесения покрытий и вспомогательных ванн для обезжиривания, травления и промывки деталей необходимо устанавливать в строгом соответствии с технологическим процессом. Учитывая, что в авторемонтном производстве применяют несколько различных процессов нанесения покрытий, в целях экономии площади рекомендуется основные ванны устанавливать у стен участка, а вспомогательные — посредине.
Если в качестве источников питания применяют выпрямители, то их следует устанавливать вблизи от ванн — потребителей тока.
Для загрузки и выгрузки деталей, а также для транспортировки от одной ванны к другой обычно применяют электротельферы.
Наиболее вредными для здоровья работающих на гальванических участках, являются электролиты. Большинство кислотных и щелочных электролитов очень токсично и отрицательно действует на дыхательные пути и кожные покровы работающих. Гальванические процессы протекают, как правило, с выделением кислорода и водорода. Выделяющиеся газы увлекают с собой мельчайшие частички электролита и таким образом насыщают воздух в помещении вредными парами.
Особое внимание уделяют вентиляции помещений, так как большинство кислотных и щелочных электролитов очень токсично и отрицательно действует на дыхательные пути и кожные покровы работающих . Поэтому рекомендуется иметь общую приточно-вытяжную вентиляцию с 8... 10-кратным обменом воздуха в час. Кроме общей вентиляции, каждая ванна с вредными выделениями должна иметь двусторонний бортовой отсос воздуха. Мощность бортовых отсосов определяют исходя из объема воздуха, забираемого с 1 м2 поверхности ванны в час. Для ванн хромирования этот показатель должен быть 6000 м3/ч, для железнения 4800, для никелирования 2500, для меднения 2000, для электролитического обезжиривания 3000 мэ/ч.
Применять резиновую обувь, перчатки и фартуки. Устанавливать фонтанчики с водой для обмывки кожных покровов, на которые может случайно попасть электролит. Полы и стены гальванического участка должны быть покрыты керамической плиткой и ежедневно промываться.
В целях охраны окружающей среды сточные воды после промывки деталей необходимо прежде, чем спускать в канализацию, пропускать через очистные сооружения.
Дата добавления: 2022-11-11; просмотров: 14; Мы поможем в написании вашей работы! |
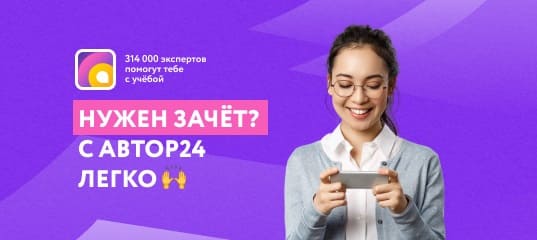
Мы поможем в написании ваших работ!