РЕМОНТ СИСТЕМЫ ПИТАНИЯ ДВИГАТЕЛЕЙ С ГАЗОБАЛЛОННЫМИ УСТАНОВКАМИ
Ремонт регулятора частоты вращения
В результате износа деталей регулятора наблюдается нарушение его работоспособности, заключающееся в потере чувствительности, несвоевременном действии регулятора, большом свободном ходе рейки топливного насоса и других неисправностях. Все эти неисправности приводят к неустойчивой работе двигателя при различных нагрузках. Для обеспечения нормальной работы регулятора при проведении ремонтных работ необходимо: правильно подбирать и затягивать пружины; правильно подбирать и закреплять грузики; устранять увеличенные зазоры, заедание и перекосы в сочленениях механизмов; нормально смазывать механизмы регулятора.
Изношенную рабочую поверхность грузиков (плечи) восстанавливают наплавкой сплавом сормайт.
После наплавки грузики обрабатывают по шаблону и их массу со втулками сравнивают с данными, приведенными в технических условиях.
Изношенные оси грузика и сухарика заменяют новыми, изготовленными из стали 45 и подвергнутыми термообработке.
У крестовины обычно изнашиваются посадочные места под оси грузиков, валик регулятора и подшипник. Изношенные отверстия под оси грузиков развертывают до ремонтного размера, обеспечив нормальный зазор в сопряжении крестовина — ось.
Износ посадочной поверхности под подшипник устраняют электроискровым наращиванием с последующим шлифованием до размера, обеспечивающего необходимую посадку в сопряжении крестовина — подшипник.
|
|
Изношенную поверхность валика регулятора под втулку шлифуют, хромируют, а затем снова шлифуют. В этом случае шейку под подшипник также хромируют, а не наращивают электроискровым способом. Вместо хромирования применяют также осталивание.
Значительное место при ремонте регулятора занимает восстановление шарнирных соединений (рычаги и тяги), а также других деталей.
Для восстановления изношенных посадок рассверливают и развертывают отверстия и используют пальцы и оси увеличенного диаметра.
Ремонт форсунок. В процессе эксплуатации дизеля наблюдается ухудшение качества распыла, изменяются направление и дальнобойность струи топлива. Это происходит в результате снижения давления начала впрыска, попадания воды и грязи в топливо, износа или закоксовывания распылителя, неправильной сборки и крепления форсунки на двигателе.
Основные износы. Во время работы форсунки изнашиваются сопрягаемые поверхности опорных витков пружины и деталей, воспринимающих ее давление. Вследствие этого уменьшается давление начала впрыска топлива, увеличивается подъем иглы распылителя, повышается пропускная способность форсунки, возрастают угол опережения впрыска топлива в цилиндр и расход топлива. В результате неравномерного износа деталей отдельных форсунок повышается неравномерность подачи топлива в отдельные цилиндры. Интенсивному изнашиванию форсунок способствует попадание в них вместе с топливом воды, пыли и грязи. При износе начинает подтекать и закоксовываться распылитель, нарушаются форма конуса распыла топлива и пропускная способность форсунки.
|
|
У штифтовых форсунок механические частицы вместе с топливом с большой скоростью проходят через зазор между штифтом иглы и стенками сопла и срезают частицы металла. Вследствие этого искажается форма и изменяются размеры сопла и штифтов. Кольцевой зазор между штифтом иглы и стенками сопла распылителя увеличивается, что приводит к ухудшению качества распыла топлива.
У бесштифтовой форсунки во время работы нарушается плотность прилегания торца иглы и распылителя к донышку, изнашивается донышко, изменяются форма и размер соплового отверстия.
Изнашиваются, кроме того направляющая часть иглы и корпус распылителя. Все это приводит к появлению течи топлива.
Плотность соединения корпусов распылителя и форсунки в основном нарушается из-за коррозии торцовых поверхностей или в результате неправильной сборки форсунки. Распылитель деформируется в результате перегрева и заедания иглы, прорыва газов из-под прокладки при перекосе, возникающем при неравномерной затяжке гаек крепления форсунки.
|
|
Восстановление распылителя форсунки, как и других прецизионных деталей дизельной топливной аппаратуры, сводится к устранению износов сопрягаемых поверхностей притиркой с применением притирочных паст.
Притиркой можно восстановить большинство сопрягаемых деталей распылителей без их раскомплектовывания. Это объясняется тем, что направляющие части иглы и корпуса распылителя изнашиваются незначительно и равномерно, вследствие чего сохраняется база для выполнения ремонтных операций.
Распылители с изношенной направляющей частью иглы могут быть восстановлены хромированием, притиркой и подбором сопрягаемых деталей.
Окончательно детали притирают без пасты, смазав их сопрягаемые поверхности чистым дизельным маслом.
Распылитель штифтовой форсунки можно восстановить отрезанием изношенного штифта иглы на шлифовальном станке и нарезанием на таком же станке новых распыливающего и запирающего конусов и штифта за счет оставшейся части иглы. В результате такой обработки игла укорачивается на 1 мм. Штифт изготавливают увеличенного ремонтного размера.
|
|
Запирающий конус корпуса распылителя восстанавливают на станке, который применяют при изготовлении новых распылителей, путем электроискровой обработки. В результате такой обработки толщина донышка в месте соплового отверстия должна быть не меньше 1,4 мм.
После этого на другом электроискровом станке обрабатывают поверхность соплового отверстия, исправляя его форму и увеличивая диаметр до ремонтного размера.
Чтобы сохранить ход укороченной иглы при впрыске топлива, у восстановленного распылителя подрезают, шлифуют и доводят торец корпуса распылителя, сопрягаемый с корпусом форсунки.
Иглу и корпус после восстановления взаимно притирают по запирающему конусу на специальном станке.
Верхнюю торцовую поверхность корпуса распылителя и донышко бесштифтового распылителя притирают на притирочных плитах. При появлении рисок и забоин для притирки используют поочередно пасты ГОИ № 25—30, 10—14 и 2—4 или соответствующие пасты НЗТА (тридцатимикронную, десятимикронную и трехмикронную).
Торец корпуса распылителя притирают так же, как и торец гильзы топливного насоса.
Во время притирки корпус распылителя нужно прижимать к плите с усилием около 5Н.
Рабочие торцы корпуса распылителя и иглы притирают совместно на притирочной плите. Вовремя притирки иглу надо постепенно поворачивать в корпусе распылителя.
Возможный перекос деталей при этом обнаруживают следующим образом. Очищают донышко, торцы корпуса распылителя и иглы от притирочных материалов. Собирают распылитель и поворачивают иглу, на половину оборота. Если на донышке, распылителя будут иметься односторонние риски в месте прилегания иглы, значит, детали перекошены. Перекос устраняют дополнительной притиркой.
Сферическую поверхность торца корпуса распылителя притирают совместно с торцом корпуса форсунки. Качество притирки проверяют сравнением с новым распылителем. При заедании иглу и корпус распылителя притирают совместно, применяя микронную пасту.
После доводки промытая в дизельном топливе игла должна перемещаться в распылителе под действием собственного веса.
Торец корпуса штифтовой форсунки притирают на плите так же, как и торец корпуса распылителя, до выведения следов кольцевого износа от заплечиков иглы распылителя.
Ремонт глушителей. У глушителей чаще всего наблюдается прогорание обшивки, которое устраняется сваркой или заменой обшивки из другого тонколистового материала.
При разборке карбюратора необходимо соблюдать осторожность чтобы не повредить прокладки и детали. Жиклеры, клапаны, иглы и каналы промывают чистым керосином или неэтилированным бензином после промывки жиклеры и каналы в корпусе карбюратора продувают сжатым воздухом. Для прочисти жиклеров каналов и отверстий нельзя применять жесткую проволоку или какие либо металлические предметы. Не допускается так же продувание сжатым воздухом собранного карбюратора через проводящий штуцер и балансировочное отверстие так как это приводит к повреждению поплавка. Жиклеры проверяют на пропускную способность, если она больше предусмотренной техническими условиями тоже жиклер изношен и подлежит замене. Игольчатый запорный клапан восстанавливают притиркой. Поврежденную резьбу восстанавливают нарезанием резьбы ремонтного размера или заваркой с последующим сверлением и нарезанием номинальной резьбы.
Трещина в поплавке запаивают мягкими припоями перед пайкой необходимо выпарить бензин, оставшийся внутри поплавка. Для этого его помещают в горячую воду и выдерживают в ней в течении нескольких минут. Одновременно по выходным пузырькам определяют место повреждения. После ремонта поплавок следует взвесить и при необходимости спилить часть напаянного металла. Проверка состояния корпусных деталей карбюратора состоит в осмотре приварочных поверхностей. При короблении корпусных деталей, неплоскостность приварочных поверхностей восстанавливается их притиркой на месте мелкой наждачной шкуркой , помещенной на ровной поверхности (например на стекле). Для ремонта карбюраторов выпускают специальные ремонтные комплекты, включающие все наиболее ответственные и наиболее часто заменяемые детали – прокладки, диафрагмы, клапаны, жиклеры, крепежные элементы.
РЕМОНТ СИСТЕМЫ ПИТАНИЯ ДВИГАТЕЛЕЙ С ГАЗОБАЛЛОННЫМИ УСТАНОВКАМИ
Ремонт газового редуктора МКЗ-НАМИ
Редуктор МКЗ-НАМИ ремонтируют при возникновении неисправностей, для устранения которых требуется снятие его с автомобиля. К таким неисправностям относятся негерметичность клапана первой ступени, разбухание мембраны, негерметичность вакуумных полостей разгрузочного и экономайзерного устройств, отказ в работе клапана или мембраны второй ступени, срыв резьбы в корпусе редуктора и др. Снятый редуктор моют и в зависимости от характера неисправностей полностью или частично разбирают.
При разборке первой ступени придерживаются последовательности: ослабляют гайки, вывертывают болт пружины высокого давления и вынимают пружину, отвертывают гайки и снимают нижнюю крышку редуктора. Разъединив шток мембраны первой ступени с рычажком, снимают мембрану, вывертывают ось рычажка и вынимают рычажок вместе с клапаном. Отвернув две гайки, снимают фильтр вместе с седлом клапана.
При разборке второй ступени редуктора отвертывают гайки и снимают дозирующе-экономайзерное устройство. Затем извлекают клапан . Для этого снимают фланец трубки холостого хода, вывертывают ось рычажка мембраны и снимают рычажок со штока.
Мембрану снимают в такой последовательности: ослабляют стопорный винт и отвертывают колпак седла пружины, вынимают из штока -шплинт , снимают упорную шайбу и пружину . Затем ослабляют контргайку и вывертывают седло пружины, отвертывают болты, снимают верхнюю крышку редуктора и мембрану в сборе.
Разгрузочное устройство извлекают после разборки второй ступени. Для этого достаточно отвернуть на 2—3 оборота гайку сальника в корпусе редуктора. Разборка разгрузочного устройства не представляет особых сложностей. Детали устройства с учетом последовательности разборки приведены на рис. 9.
Дозирующе-зкономайзерное устройство разбирают в такой последовательности: отвертывают винты и снимают пластину 12
| ||
Рис. 9. Детали разгрузочного устройства: 1 — корпус, 2 — фланец, 3 — мембрана, 4, 7 — шайбы, 5 — пружина, 6 — крышка, 8 — штуцер, 9 — винт клапана | Рис. 10. Детали дозирующе-эковомайзерного устройства: 1 — винт, 2, 7 — шайбы, 3 — крышка, 4 — пружина экоио- майзера, 5 — мембрана, 6 — замочная шайба, 8 — пружина, 9 — корпус, 10 — клапан экономайзера, 11 — прокладка, 12 — пластина |
(рис. 10) с дозирующими шайбами, снимают крышку 3, извлекают пружину 4 экономайзера и мембрану 5, снимают со штока клапана замочную шайбу 6, вынимают клапан 10 экономайзера и пружину 8 клапана. Снятые детали моют, дефектуют и ремонтируют.
Основными неисправностями корпуса редуктора, которые подлежат устранению, являются повреждение резьбы отверстий и прилегающих плоскостей. Резьбовые отверстия восстанавливают нарезанием резьбы большего размера или постановкой втулок. При ремонте резьбовых отверстий способом увеличения размера резьбы соответственно новому размеру изготовляют шпильки, резьбовые штуцера и т. п.
Повреждения плоскостей прилегания (риски, забоины) устраняют шабрением поверхностей. При обломе ушек под оси рычажков, связывающих клапан и мембрану в первой и второй ступенях, а также при появлении трещин корпус редуктора бракуют.
Негерметичность пары клапан — седло в первой и второй ступенях редуктора устраняют обработкой поверхностей седел и ремонтом клапанов. Повреждения рабочих кромок седел удаляют зачисткой или подрезкой их торца. В клапанах переворачивают или заменяют поврежденные детали вставки. При заедании клапанов зачищают трущиеся поверхности клапанов, а также оси вращения рычажка.
Негерметичкость вакуумных полостей разгрузочного и эконо-майзерного устройств является следствием нарушения целостности или повреждения прилегающих поверхностей. Такие повреждения устраняют шабрением, а поврежденные мембраны заменяют. Мембраны изготовляют по чертежам или образцам из прорезиненной маслобензостойкой ткани толщиной 0,35 мм.
После ремонта редуктор собирают в обратной последовательности. При этом проверяют все подвижные соединения, которые должны перемещаться легко без заеданий. При установке мембран обращают внимание на правильное расположение отверстий для болтов и стержня штока. При прижатии мембран не должно образовываться складок и загибов.
В процессе сборки первой ступени редуктора при необходимости регулируют положение рычажка 5 (см. рис. 2) винтом 3 и контргайкой 4 до момента, когда плечо рычажка 5 займет горизонтальное положение при полностью закрытом клапане.
После сборки газовый редуктор испытывают на стенде (рис. 11). Стенд позволяет произвести проверки и регулировки I и II ступеней редуктора, разгрузочного и экономайзерного устройств. Для проведения работ редуктор 1 закрепляют на стенде посредством пневматического приспособления. Проверка работоспособности систем редуктора осуществляется сжатым воздухом с давлением 1,6 МПа и разрежением до 665 Па, создаваемым диаф-рагменной камерой. Входящее давление воздуха и давление в I ступени редуктора контролируются манометрами 2 и 3. Для замера разрежения во время испытаний используют вакуумметр 4 и пьезометр 5.
В I ступени регулируют величину давления газа, проверяют быстроту наполнения камеры и герметичность соединений. Во II ступени регулируют ход клапана, его герметичность и момент открытия.
Отремонтированные зкономайзерные устройства проверяют на герметичность. При проверке создают разрежение под мембранами не менее 265 Па. Падение вакуума в течение 3 мин не допускается. Кроме того, в экономайзерном устройстве проверяют момент открытия клапана, а в разгрузочном — минимальное разрежение, нейтрализующее усилие конической пружины.
Ремонт испарителя, фильтра, смесителя и предохранительного клапана
Негерметичность по плоскости разъема может возникнуть вследствие повреждения прокладки или плоскости прилегания (заусенцы, забоины и т. п.). При ремонте испарителя прокладку заменяют, а повреждения плоскости разъема исправляют шабрением. Раковины и трещины устраняют заваркой алюминием. Мелкие поры заделывают чеканкой или пропиткой корпусов бакелитовым лаком.
Перед пропиткой газовых каналов бакелитовым лаком испаритель собирают, на выходной штуцер устанавливают заглушку и нагревают его до температуры 80—100°С. Затем через входной штуцер полость заполняют нагретым до такой же температуры бакелитовым лаком и подают воздух под давлением 1,6 МПа.
После непродолжительного времени (около одной минуты) давление снимают, лак из полости выливают и испаритель просушивают до полного высыхания пленки лака. Отремонтированный таким образом испаритель подвергают на стенде пневматическим испытаниям на герметичность, конструкция стенда позволяет проверить отдельно в ванне с водой герметичность газовой и водяной полостей испарителя. Подъем и опускание ванны с водой и крепление испарителя осуществляется с помощью пневматической системы.
Проверяют сначала газовую полость под давлением воздуха 1,6 МПа, затем водяную —под давлением воздуха 0,15 МПа. Проверка каждой полости производится в течение 2 мин. Контроль параметров производится по манометрам 2 и 3 и реле времени 4, установленными на панели приборов стенда.
Ремонт смесителя. В смесителе газа наиболее часто ремонтируют обратный клапан. Для разборки клапана отвертывают винты и открывают крышку клапанной коробки, после чего клапан вместе со стержнем легко вынимается. К неисправностям клапана относится засмоление его или пропуск газа (негерметичность) при работе двигателя на холостом ходу.
Смолистые отложения удаляют промывкой клапана и его стержня в бензине. Негерметичность пары клапан — седло устраняют снятием заусенцев с торцовой поверхности седла и притиркой клапана пастой ГОИ.
После ремонта обратный клапан проверяют на герметичность под давлением воздуха 0,2 МПа и легкость его перемещения. Клапан в любых положениях не должен зависать.
Повреждения вставки клапана устраняют зачисткой неровности на прилегающей поверхности бархатным напильником, а раковины на седле —подрезкой или зачисткой его торцовой поверхности. Давление пружины на клапан изменяют набором регулировочных шайб. При увеличении толщины набора шайб давление пружины увеличивается, а при уменьшении — клапан будет открываться при меньшем давлении газа в баллоне. После ремонта, вне зависимости от характера неисправности, предохранительный клапан проверяют и регулируют на давление открытия и закрытия клапана.
Используя различные доступные источники запишите конспект:
Дата добавления: 2022-11-11; просмотров: 26; Мы поможем в написании вашей работы! |
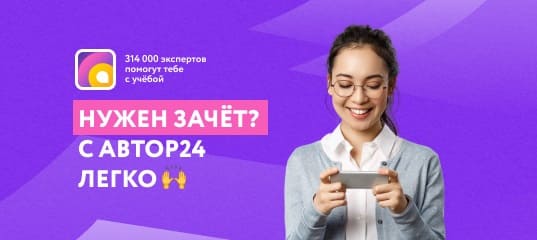
Мы поможем в написании ваших работ!