Сборка, обкатка и испытание двигателей
Тема 10. Ремонт двигателей.
План.
1.Ремонт КШМ.
2.Ремонт ГРМ.
3.Ремонт системы питания.
4.Ремонт электрооборудования.
5.Ремонт системы смазки.
6.Ремонт системы охлаждения.
7.Сборка, обкатка, испытание двигателей.
Ремонт кривошипно-шатунного механизма
Кривошипно-шатунный механизм определяет ресурс двигателя. Интенсивное изнашивание цилиндропоршневой группы вызывает утечки газов в картер, ускоренное старение масла, увеличение расхода топлива и динамических нагрузок на детали, снижение мощности двигателя.
Текущий ремонт кривошипно-шатунного механизма рекомендуется проводить при достижении расхода масла на угар 1,5 % от расхода топлива. При ремонте снимают головку цилиндров в сборе, нижнюю крышку блок-картера (поддон) и масляный насос в сборе с трубопроводами. Затем поочередно устанавливают шатунные шейки в нижнее положение, отворачивают шатунные болты и снимают крышки шатунов в сборе с вкладышами. После этого очищают верхний пояс гильз цилиндров от нагара и вынимают из них поршни вместе с шатунами.
При капитальном ремонте двигателя детали шатунно-поршневой группы в случае замены или восстановления подбирают по массе с целью уменьшения инерционных сил. Допустимая разница в массе деталей этой группы, устанавливаемых в двигатель, приведена в технических требованиях. Например, для двигателя Д-240 и его модификаций допустимая разница в массе поршней равна 10 г, поршневых пальцев — 10 г, шатунов в сборе с поршнями — 30 г. Массу поршня обычно указывают на днище, а массу шатуна — на боковой поверхности крышки в месте прилива под шатунный болт.
|
|
Ремонт газораспределительного механизма.
Износ деталей газораспределительного механизма приводит к нарушению процессов, происходящих в цилиндрах, ухудшая такие показатели двигателя, как мощность, расход топлива, компрессия в цилиндрах и др. Регулируя зазор в клапанах, можно компенсировать износ многих деталей газораспределительного механизма, за исключением износа кулачков распределительного вала. Износ деталей газораспределительного механизма приводит к уменьшению степени сжатия и коэффициента наполнения цилиндров двигателя, в результате чего ухудшаются пусковые качества дизеля и снижается его мощность. Особенно это относится к соединению фаска клапана—гнездо. При изнашивании этих деталей нарушается герметичность соединения, увеличивается глубина утопания тарелки клапана относительно поверхности головки цилиндров. Допустимые значения утопания тарелки клапана приведены в технических требованиях на ремонт двигателей. Например, для двигателя Д-240 и его модификаций глубина утопания тарелки клапана по чертежу равна 1,05... 1,25 мм, а допустимая — 3,5 мм. При ремонте этого механизма головку цилиндров снимают с двигателя и осматривают. Если головка имеет трещины по перемычкам клапанных гнезд или предельное отклонение от плоскости рабочей поверхности, или глубину утопания тарелок клапанов больше допустимой, то ее отправляют в капитальный ремонт. Перед сборкой обдувают головку цилиндров сжатым воздухом. Собрав головку с клапанами, проверяют герметичность клапанных соединений, заливая керосин во впускные и выпускные каналы. Керосин выдерживают в каналах в течение 2 мин. Если керосин просачивается, то следует повторить притирку клапанов к гнездам. Регулировку зазоров в клапанном механизме проводят после установки головки цилиндров на двигатель.
|
|
Ремонт системы питания
Демонтаж топливного насоса с двигателя осуществляют в следующей последовательности: перекрывают расходный кран топливного бака, очищают корпус топливного насоса и топливопро-
воды от грязи, отсоединяют и снимают топливопроводы высокого и низкого давления, скобы их крепления, вывертывают болты крепления топливного насоса и снимают его.
|
|
Отверстия топливопроводов после их отсоединения, а также отверстия подвода и отвода топлива в корпусе насоса закрывают пробками и заглушками.
Ремонт и регулировку топливной аппаратуры тракторов и комбайнов, а также устранение неисправностей, возникающих в процессе эксплуатации машин, производят на специализированных рабочих местах, оснащенных необходимым оборудованием, инструментом и приспособлениями ПИМ-6401, ПИМ-1878.
Перед разборкой топливную аппаратуру промывают в моечных машинах растворами CMC типа МС-18, лабомид 101 и др. Если нет моечных машин для очистки агрегатов и деталей топливной аппаратуры, то можно использовать моечные ванны ОМ-1316. В качестве моющей жидкости используют керосин.
Неисправные агрегаты топливной аппаратуры разбирают и собирают в определенной последовательности, приведенной в типовой технологии.
Ремонт электрооборудования.
Ремонт аккумуляторных батарей. Характерными неисправностями аккумуляторных батарей являются: ускоренный саморазряд; обломы выводных штырей; трещины и обломы в баках и крышках; вспучивание, отслаивание и повреждение заливочной мастики; разрушение сепараторов; коробление, короткое замыкание, сульфатация и разрушение пластин.
|
|
Аккумуляторные батареи, поступающие в ремонт, очищают от загрязнений и подвергают внешнему осмотру. При наличии трещин в баках и крышках, вспучивания и отслаивания мастики батареи разбирают и ремонтируют. Если таких дефектов нет, то проверяют уровень и плотность электролита, с помощью нагрузочной вилки измеряют напряжение каждого аккумулятора. Чтобы избежать разрушения пластин аккумуляторов, напряжение нагрузочной вилкой определяют только у тех аккумуляторов, у которых плотность электролита не ниже 1,20 г/см3.
Сборку аккумуляторных батарей начинают с блоков пластин. Полублоки вставляют один в другой так, чтобы каждая положительная пластина находилась между двумя отрицательными. Сепараторы устанавливают ребрами в сторону положительных пластин.
В собранную аккумуляторную батарею заливают электролит плотностью 1,22... 1,25 г/см3 до нормального уровня для пропитки пластин. Через 4... 6 ч проверяют уровень электролита и при необходимости его доливают.
Ремонт генераторов. На тракторах и комбайнах применяют в основном генераторы переменного тока, поскольку они обладают более высокой надежностью, меньшими габаритными размерами и массой, чем генераторы постоянного тока.
На большинстве тракторов и комбайнов используют трехфазные генераторы с кремниевыми или селеновыми выпрямителями. Базовой моделью таких генераторов является генератор типа Г-250, который работает в комплексе с реле-регулятором РР-362 и др. Катушка возбуждения питается постоянным током через реле- регулятор.
К механическим дефектам относятся подгорание контактных колец и их износ по диаметру более 0,25 мм, износ шейки вала под шарикоподшипник, смятие и забой резьбы, износ шпоночной канавки вала ротора по ширине, износ гнезда крышки под шарикоподшипник, щеток и др.
Наиболее распространенными электрическими дефектами являются обрывы в обмотках ротора и статора, повреждение наружной изоляции и межвитковые замыкания.
Обрывы или замыкания на «массу» обмоток ротора и статора определяют с помощью контрольной лампы или омметром. При отсутствии обрыва или замыкании лампа загорается. Ремонт статора. Поврежденную изоляцию обмотки статора удаляют, обматывают изоляционными материалами, пропитывают лаком MJI92 или ГФ95 и сушат в сушильном шкафу при температуре 100... 120 "С в течение 2...4 ч.
При обрывах выводов снимают изоляцию в месте соединения вывода с катушкой и облуживают припоем ПОС-40 концы, используя в качестве флюса канифоль. Затем припаивают вывод катушки, изолируют место спая хлопчатобумажной лентой, пропитывают лаком и сушат.
Ремонт ротора. Подогревание наружной поверхности контактных колец устраняют шлифованием стеклянной шкуркой. Небольшие износы устраняют проточкой на специальных станках. Проточку производят до выведения следов износа, но на глубину не более 0,5 мм.
Если износ колец более 0,5 мм, то их заменяют новыми. Для этого концы обмотки возбуждения отпаивают от колец, а кольца спрессовывают с вала. Затем, используя оправку и ручной пресс, напрессовывают новые кольца, протачивают их на токарном станке и шлифуют стеклянной шкуркой. Выводы обмотки возбуждения припаивают припоем ПОС-40.
Смятие и забой резьбы вала устраняют наплавкой с последующей нарезкой новой резьбы или нарезкой резьбы ремонтного размера.
Износ посадочных мест под подшипники устраняют наплавкой либо постановкой ремонтных втулок на предварительно проточенную поверхность шеек вала, с последующей механической обработкой под номинальный размер. Задиры на наружной поверхности ротора устраняют шабрением.
Ремонт стартера. При разборке стартера СТ 362 отсоединяют провод от контактного болта тягового реле стартера, снимают реле, извлекают из крышки со стороны привода якорь реле в сборе с пружиной.
Отвернув стяжные болты, снимают защитный колпак и вынимают пружины щеток, снимают крышку со стороны коллектора. Пригодные для дальнейшей работы щетки и щеткодержатели помечают и не раскомплектовывают. Из корпуса стартера вынимают якорь в сборе с крышкой, снимают с корпуса уплотнительную прокладку, а с шейки вала якоря — фибровую и стальную шайбы. Вынимают ось рычага включения и отделяют якорь в сборе от крышки со стороны привода. С шейки вала якоря снимают привод в сборе, вынимают две щетки из щеткодержателей крышки со стороны коллектора.
С помощью лампы напряжением 220 В или мегомметра проверяют отсутствие замыкания обмоток статора на «массу». В случае горения лампы или показаний мегомметра менее 10 кОм обмотку заменяют. Крышки стартера с трещинами заменяют. Изношенные втулки заменяют на новые и развертывают. Проверяют надежность крепления щеткодержателей. Щетки, изношенные по высоте (менее 12 мм), заменяют и притирают к коллектору. Щетки должны свободно перемещаться в пазах.
С помощью динамометра проверяют усилие давления пружин на щетки. Это усилие должно составлять 10+1 Н.
Проверяют легкость перемещения якоря реле и состояние контактов. Если они подгорели, то их зачищают шлифовальной шкуркой или бархатным напильником. Затем проверяют сопротивление обмоток реле, надежность соединения их выводов со штекером и «массой».
Сборка стартера производится в порядке, обратном разборке. Якорь должен вращаться свободно от руки. На стенде КИ-968- ГосНИТИ (Э-242, КИ-18750-ГосНИТИ, КИ-532М-ГосНИТИ) производят обкатку и испытание стартера в режимах холостого хода и полного торможения.
В режиме холостого хода определяют частоту вращения якоря стартера и потребляемый ток. Электрические параметры и частоту вращения стартера измеряют не раньше чем через 30 с после включения стартера. В режиме полного торможения определяют величину тока; при этом якорь стартера не должен проворачиваться. Продолжительность полного торможения не должна превышать 5 с.
Ремонт магнето. При разборке магнето М 124-Б1 отвертывают гайку крепления полумуфты, снимают полумуфту с вала ротора, вынимают высоковольтный провод с резиновой шайбой, снимают крышку прерывателя, вынимают из стоек магнето войлочный фильц, снимают крышку магнето и конденсатор, вынимают из корпуса магнето ротор и пружины конденсатора, снимают с вала ротора сепараторы подшипников, вынимают из корпуса трансформатор, снимают с крышки магнето высоковольтный вывод, снимают рычаг прерывателя с пружиной и контактную стойку.
При наличии трещин и сколов корпус магнето выбраковывают. Задиры и коррозионные повреждения на поверхности полюсных башмаков удаляют шлифовальной шкуркой. В отверстиях с сорванной резьбой нарезают резьбу ремонтного размера.
Целостность обмоток трансформатора проверяют контрольной лампой (12 В) или комбинированным прибором Ф-4313 (Ф-4320). Трансформатор с оборванными обмотками заменяют. Изоляцию трансформатора проверяют на пробой. Забоины и следы коррозии на поверхности полюсных наконечников зачищают шлифовальной шкуркой. Диаметр шеек под подшипники должен быть не меньше 11,99 мм, шейки под кулачок — не меньше 8,47 мм. Сборку магнето производят в последовательности, обратной разборке. Ротор магнето должен вращаться свободно, без заеданий, от руки.
Ремонт смазочной системы
Техническое состояние масляного насоса оценивают без разборки, по падению подачи, проводя испытания на стенде КИ-5278М- ГосНИТИ или др. При этом используют состав из 50 % дизельного масла и 50 % дизельного топлива с вязкостью 16... 18 мм2/с. Подача должна быть не ниже допустимой. Например, для двигателя Д-240 и его модификаций номинальная объемная подача равна 36 дм3/мин, а допустимая — 34 дм3/мин.
При разборке не допускается раскомплектовывать пары шестерен с корпусами секций.
Основными дефектами деталей масляных насосов являются износы колодцев корпуса, плоскостей крышек (проставок), торцевых поверхностей шестерен, поверхностей валов, осей и втулок, срыв резьбы.
Одной из причин снижения подачи масла является увеличение торцевого зазора между шестернями и крышками (простав- ками) масляного насоса, который должен составлять для двигателей типа СМД, А-41 и А-01А 0,07...0,22 мм, а допустимый без ремонта — 0,30 мм.
Шестерни при износе заменяют новыми или обрабатывают торцевые поверхности корпуса и крышек до получения требуемого зазора, а изношенные боковые поверхности корпуса восстанавливают железнением, цинкованием, нанесением эпоксидного состава до
получения требуемого зазора. Бронзовые втулки восстанавливают термодиффузионным хромированием и обрабатывают совместно в корпусе и крышке под номинальный или ремонтный размер. Плоскости на крышках и проставках обрабатывают шабрением или шлифованием с отклонением не более 0,03 мм на 100 мм длины. Шарики клапанов заменяют и обчеканивают, а фаски гнезд под них зенкуют.
Поврежденный участок сетки маслосборника не должен быть более 10 % площади всей сетки. Поврежденный участок большего размера либо запаивают мягким припоем, либо устанавливают на него накладку из такой же сетки и припаивают ее по кругу.
После ремонта детали промывают и собирают масляный насос.
Нарушение работы центрифуги определяют по шуму и времени выбега ротора при остановке дизеля. Оно должно быть не менее 30 с для двигателей типа СМД. При меньшем времени выбега ротор разбирают, удаляют отложения и промывают детали в ди-
зельном топливе. Выходные отверстия форсунок прочищают медной проволокой диаметром 1,5... 1,8 мм. При увеличении зазора между осью и втулками более допустимого (0,2 мм) втулки заменяют и развертывают их совместно в корпусе и крышке, выдерживая зазор 0,016...0,090 мм. Осевое перемещение ротора должно составлять 0,4... 1,0 мм при затягивании гайки оси с моментом 80... 100 Нм.
Собранные фильтры испытывают и регулируют на стенде КИ-9158-ГосНИТИ на давление открытия клапанов, а также частоту вращения и герметичность центрифуги. Так, для двигателей СМД-60, СМД-62 и СМД-64 давление открытия дифференциального клапана должно составлять 0,45...0,57 МПа, перепускного клапана — 0,60...0,70 МПа, а при проверке показателей полнопоточных центрифуг тех же двигателей давление масла на входе в центрифугу должно составлять 0,80 МПа, давление масла за центрифугой — 0,30...0,35 МПа, расход масла через ротор центрифуги — 45 л/мин при частоте вращения ротора 5400 мин"1.
Для проверки герметичности центрифуги и частоты вращения ротора с центрифуги снимают колпак и ставят на нее защитный кожух. Придерживая рукой ротор центрифуги, включают стенд и дросселем создают требуемое давление рабочей жидкости. При этом допускается небольшое просачивание масла из-под втулки ротора. Частоту вращения ротора центрифуги определяют прибором КИ-1308В-ГосНИТИ, корпус которого навинчивают на ось ротора, включают стенд и добиваются максимальной амплитуды колебания язычка прибора. Ориентировочно частоту вращения ротора центрифуги можно определить по времени вращения центрифуги после выключения стенда (для центрифуг двигателей типа СМД оно должно быть не меньше 30 с).
Ремонт системы охлаждения.
Основной параметр, характеризующий работу системы охлаждения, — это температура охлаждающей жидкости. Повышение температуры (перегрев двигателя) объясняется неисправностью агрегатов и приборов системы, а также поздним впрыскиванием топлива или поздним зажиганием.
Ремонт водяного насоса. Водяной насос может иметь трещины корпуса; срыв резьбы в отверстиях; износ посадочных мест под подшипники и упорную втулку; износ посадочного места под крыльчатку на валике, под втулками, сальниками и шкивами вентилятора; износ, трещины и коррозию поверхностей лопаток крыльчатки; износ внутренней поверхности втулок.
Трещины в корпусах устраняют заваркой проволокой ПАНЧ-П или латунными прутками Ломна и др. Изношенные поверхности под подшипники при зазорах менее 0,25 мм восстанавливают герметиками; крыльчатки заменяют новыми, изготовленными из алюминиевого сплава или полимерного материала, но при этом ступица (втулка) должна быть стальной Изношенные поверхности валиков восстанавливают наплавкой или железнением. На уплотнительной шайбе допускаются царапины и износы глубиной не более 0,5 мм.
При сборке водяного насоса в подшипниковую зону закладывают 100 г смазки «Литол-24», а уплотняющую шайбу и торец опорной втулки покрывают тонким слоем герметика или смазкой, состоящей из 60 % дизельного масла и 40 % графита. Зазор между корпусом водяного насоса и лопастями крыльчатки должен составлять 0,1... 1,5 мм, а валик должен легко вращаться.
Отремонтированный насос проверяют на герметичность при давлении 0,12...0,15 МПа, обкатывают и испытывают на стенде КИ-1803-ГосНИТИ. Утечка воды через уплотнения и резьбу шпилек не допускается. Обкатку в течение 3 мин выполняют при температуре воды 85... 90 "С. Для двигателей типа СМД подача насоса должна быть не менее 425 л/мин при частоте вращения 2300 ±115 мин-1 и противодавлении на выходном патрубке 0,030...0,035 МПа.
Ремонт вентиляторов. Вентиляторы могут иметь износы посадочных мест в шкивах под наружные кольца подшипников, износ ручьев под ремень, ослабление заклепок на крестовине, изгиб крестовины и лопастей.
Изношенные посадочные места под подшипники восстанавливают электролитическим наращиванием или полимерными материалами. Ручьи шкивов при износе до 1 мм протачивают. Ослабленные заклепки на крестовине лопастей подтягивают, а отверстия под заклепки при износе рассверливают на увеличенный диаметр. Шаблоном проверяют форму лопастей и угол их наклона относительно плоскости вращения, который должен составлять 30...35°, и при необходимости лопасти правят.
Собранный со шкивом вентилятор статически балансируют и при дисбалансе сверлят углубления в торце шкива или утяжеляют лопасть с ее выпуклой стороны, приваривая или приклепывая к ней пластины.
Ремонт гидромуфты привода вентилятора. В гидромуфте привода вентилятора двигателя ЯМЗ-240Б могут быть следующие неисправности: подтекание масла через уплотнения, заедание ведомого или ведущего валов при вращении лопастей и увеличенный осевой зазор. Шкив привода гидромуфты при неподвижной ступице вентилятора и ступица при неподвижном шкиве после сборки должны вращаться свободно.
Термосиловой датчик включателя гидромуфты регулируют постановкой шайб на включение при температуре охлаждающей жидкости 90... 95 °С и на выключение — при температуре 75... 80 "С.
Ремонт термостатов. В термостатах удаляют накипь, обрабатывая их 10... 12 %-ным раствором ингибированной соляной кислоты при температуре 75...80°С в течение 20...25 мин или синтетическим моющим средством МС-37. Поврежденные места пружинной коробки запаивают припоем Г10С-40 и заполняют ее 15%-ным раствором этилового спирта. При испытании термостата в ванне с водой клапан должен начинать открываться при температуре 70 "С, а полностью открываться — при температуре 85 "С. Высота полного подъема клапана должна составлять 9,0... 9,5 мм; ее регулируют, вращая клапан на резьбовом конце хвостовика пружинной коробки.
Ремонт радиатора. При испытании радиатор наполняют водой, и при давлении 0,05...0,10 МПа течи радиатора не допускается. Наружные поврежденные трубки запаивают, а во внутренних рядах заглушают с обоих концов. Допускается запаивать не более 5 % трубок. Возможна замена трубок за счет распайки их нагретым до 600 °С воздухом или нагретыми до 800 °С шомполами. Трубки припаивают к опорным пластинам припоем ПОС-ЗО.
Допускается дефектную трубку развальцовывать на больший диаметр и вставлять новую трубку, припаивая ее по концам к опорной пластине припоем ПОС-ЗО. Общее число вновь установленных или гильзованных трубок для дизелей должно быть не более 20 % от их общего числа.
Трещины в чугунных баках устраняют сваркой, а в латунных — пайкой.
Отремонтированные радиаторы испытывают на стенде КИ-1377- ГосНИТИ при давлении 0,15 МПа, течь не допускается.
Сборка, обкатка и испытание двигателей
Сборка двигателя. При сборке двигателя необходимо соблюдать последовательность операций, изложенную в технологических картах. Масло- и топливопроводящие каналы (трубки) и отверстия перед сборкой необходимо тщательно очистить и продуть сжатым воздухом. Перед установкой на двигатель сопрягаемые поверхности деталей в зависимости от условий работы необходимо смазать соответствующим смазочным материалом или герметиком.
Гильзы цилиндров устанавливают в блок только одного ремонтного размера и одной размерной группы. После установки гильз цилиндров блок испытывают на герметичность водой под давлением в соответствии с техническими требованиями.
При замене гильз цилиндров заменяют и уплотнительные кольца. После запрессовки гильз в блок замеряют выступание их торцов над плоскостью блока, которое должно соответствовать техническим требованиям. Например, для двигателей Д-240 и Д-240Л оно составляет 0,05...0,11 мм, допустимое значение — 0,04 мм. Если выступание гильзы меньше допустимого значения, то под буртик гильзы ставят кольцо-прокладку.
Перед установкой коленчатого вала необходимо проверить зенковку отверстий для подвода масла к подшипникам, особенно у валов третьего и больших ремонтных размеров, так как недостаточная зенковка может привести к задирам шеек при работе двигателя. Вначале рекомендуется собрать и затянуть коренные подшипники без
коленчатого вала. После этого проверяют овальность, конусность, масляный зазор и смещение верхнего вкладыша относительно нижнего. Значения этих величин должны соответствовать техническим требованиям. Например, для двигателей типа СМД зазор не должен превышать 0,156 мм. После проверки разбирают коренные подшипники и устанавливают коленчатый вал.
При установке коленчатого вала его коренные шейки смазывают маслом и затягивают равномерно в 2... 3 приема средний коренной подшипник с заданным моментом (например, для двигателя Д-240, Д-240Л он равен 160... 180 Нм). Если после этого вал легко проворачивается за болт во фланце, то равномерно затягивают остальные крышки подшипников.
Правильно установленный вал должен проворачиваться от усилия руки, приложенного к шатунной шейке. Если вал туго проворачивается, то его снимают и шейки смазывают тонким слоем краски. После его установки и проворачивания определяют причину тугого проворачивания и устраняют ее. Осевой разбег коленчатого вала проверяют щупом. Для дизелей он должен составлять 0,1 ...0,4 мм.
При установке шатунно-поршневой группы ее детали и внутреннюю поверхность гильзы смазывают маслом. Поршень в сборе с шатуном и кольцами устанавливают в гильзу с помощью специального приспособления — сжимающего кольца. На большинстве двигателей замки поршневых колец располагают под углом 120° один относительно другого и не устанавливают напротив оси поршневого пальца. Шатунно-поршневую группу устанавливают в определенном положении относительно блока цилиндров в соответствии с техническими требованиями. Крышки устанавливают на шатуны по меткам. Гайки и болты шатунных подшипников затягивают динамометрическим ключом с моментом, предусмотренным техническими требованиями. Например, для двигателя Д-240 и его модификаций он равен 180...200 Н-м. Момент проворачивания коленчатого вала после затягивания всех шатунных болтов не должен превышать 60 Н • м.
Затем ставят картер маховика, корпус сцепления и маховик. Маховик устанавливают так, чтобы метка на нем совпала с меткой на торце коленчатого вала. Болты крепления маховика затягивают равномерно в несколько приемов с моментом, указанным в технических требованиях.
Обкатка двигателя. Для приработки трущихся поверхностей деталей двигатель после сборки обкатывают. При капитальном ремонте двигатели подвергают холодной и горячей обкатке. Режимы обкатки приведены в технических требованиях. Обкатку двигателя после текущего ремонта проводят только в том случае, если были заменены поршневые кольца или другие детали кривошипно-шатунного механизма.
После текущего ремонта дизель обкатывают в три стадии: холодная обкатка, обкатка на холостом ходу и обкатка под нагрузкой.
При холодной обкатке дизеля включают электродвигатель стенда и устанавливают частоту вращения коленчатого вала 500... 700 мин-1. Продолжительность холодной обкатки — 3... 5 мин. При этом нужно убедиться в подаче масла на регулировочные винты коромысел и штанги толкателей. Течь воды, масла и топлива не допускается. После холодной обкатки двигателя на маловязких жидкостях их сливают из полостей двигателя, промывают масляные фильтры и картер.
Горячую обкатку дизеля на холостом ходу проводят в течение 10 мин при плавном повышении частоты вращения коленчатого вала от минимальной устойчивой до максимальной холостого хода. Двигатель во время обкатки должен работать бесперебойно на всех диапазонах частоты вала. По окончании обкатки на холостом ходу устраняют возникшие неисправности, выполняют необходимые регулировочные работы, проверяют затяжку гаек крепления головки цилиндров.
Горячую обкатку дизеля под нагрузкой проводят в течение 20 мин при положении рычага управления регулятором частоты вращения, соответствующем полной подаче топлива.
Температура охлаждающей жидкости на выходе из дизеля при обкатке должна составлять 75...85 °С, а температура масла в картере или перед масляным радиатором — 85...95 "С.
Испытание двигателя. По окончании обкатки двигатель испытывают. Перед началом измерений дизель должен проработать в режиме испытаний не менее 5 мин и иметь нормальный тепловой режим. После текущего ремонта при испытании определяют максимальную и минимальную частоту вращения коленчатого вала на холостом ходу; мощность и расход топлива при номинальной частоте вращения и положении рычага управления регулятором, соответствующем полной подаче топлива. Допустимые значения этих параметров приведены в технических требованиях на текущий ремонт двигателей.
Двигатель считается не выдержавшим испытание, если развиваемая им мощность ниже, а удельный расход топлива выше значений, приведенных в технических требованиях.
Контрольные вопросы
1.Назовите основные неисправности двигателей.
2.Расскажите о комплектовании деталей цилиндропоршневой группы.
3.Расскажите о технологии ремонта газораспределительного механизма.
4.Перечислите основные дефекты блоков цилиндров и способы их устранения.
5. Каково назначение обкатки и испытания двигателей.
Дата добавления: 2022-07-02; просмотров: 65; Мы поможем в написании вашей работы! |
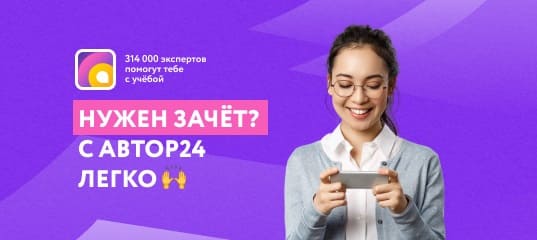
Мы поможем в написании ваших работ!