Эксплуатационные свойства и область применения композитов
Композиты с полимерной матрицей. К их достоинствам следует отнести высокие удельные прочностные и упругие характеристики, стойкость в химически агрессивных средах, а также достаточную простоту изготовления,— для их производства не требуется высоких температур и давлений. Однако им присущ ряд недостатков, определяемых свойствами полимерной матрицы. Это, прежде всего, низкие значения прочности при сжатии и сдвиге (при их высоких удельных значениях), низкая теплостойкость, гигроскопичность и склонность к старению, т. е. к изменению физико-механических свойств под воздействием климатических факторов.
Композиты с углеродной матрицей. В качестве армирующего компонента таких композитов используется углеродное волокно. Основное назначение таких композитов — тепловая защита. Они сохраняют высокие механические свойства при очень высоких температурах. При нагреве до 2000 °С наблюдается даже некоторое повышение пределов прочности при растяжении и сжатии. По прочности «углерод — углеродный» композит в 5—10 раз превосходит специальные графиты. Высокие теплозащитные свойства композита определяются также тем, что при нагреве происходит снижение теплопроводности и рост теплоемкости графита. «Углерод — углеродные» композиты нашли применение для изготовления дисков авиационных тормозов.
Композиты с металлической матрицей сочетают в себе достоинства и металлов, и композитов. Они обладают высокими значениями модуля упругости, предела прочности, ударной вязкости. Эти материалы сохраняют свои свойства при температурах значительно более высоких, чем композиты с полимерной матрицей. Важным является то, что прочная металлическая матрица обеспечивает высокие механические свойства в направлении, перпендикулярном оси волокон. Это определило конструкцию композитов с металлической матрицей как одноосную, т. е. более технологичную. Особо следует отметить, что только такие композиты возможно упрочнить путем термической обработки или наклепа. Повышение механических характеристик достигается при этом за счет упрочнения материала матрицы.
|
|
Наиболее распространены композиты с матрицей из алюминия или сплавов на его основе вследствие их высокой технологичности при производстве композитов. В качестве армирующего компонента используют борные и углеродные волокна, стальную проволоку.
Предел прочности бороалюминия (композит марки ВКА-1) вдоль направления волокна при комнатной температуре в два раза выше, чем у конструкционных алюминиевых сплавов (1000÷1200 МПа). При повышенных температурах его преимущество становится еще заметнее (при 500 °С предел прочности композита составляет 500 МПа). Прочность в поперечном направлении этого композита достаточно низкая, около 60 МПа, так как материал матрицы — неупрочняемый сплав. При изготовлении матрицы из сплава Д16 и упрочнении композита путем термической обработки (закалка + старение) его прочность в поперечном направлении возрастает до 200 МПа.
|
|
Композиты с углеродным волокном (КАУ) получают методом пропитки, т. е. заливкой волокнистого каркаса. Материал матрицы в этом случае — литейный сплав алюминия. При армировании силумина АЛ-2 углеродными волокнами достигается прочность до 1000 МПа и теплостойкость до 500 °С.
Использование для армирования стальной проволоки (композит КАС-1) позволяет повысить предел прочности до 1300÷1450 МПа. В качестве матричного материала для композита КАС-1 используют упрочняемые сплавы алюминия, поэтому предел прочности в поперечном направлении достаточно высок — после термической обработки его значения приближаются к 300 МПа (материал матрицы сплав САП-1, т. е. в этом случае имеем комбинированное упрочнение — дисперсно-упрочненный волокнистый композит).
Основное применение композитов с матрицей на основе алюминиевых сплавов — авиационная промышленность. Их используют вместо алюминиевых сплавов для повышения механических свойств, наиболее важно — увеличение модуля упругости. Так, замена сплава Д16 на композит ВКА-1 позволила повысить жесткость лонжерона крыла примерно в 1,5 раза.
|
|
Композиты с магниевой матрицей обладают более высокой удельной прочностью, чем композиты на основе алюминия из-за малой плотности магния (плотности магния и алюминия составляют соответственно 1,74 и 2,7 г/см3). Предел прочности боромагния при комнатной температуре приближается к 1000 МПа, а при температуре 400 °С его значение составляют около 500 МПа. Однако производство композитов с магниевой матрицей связано со значительными технологическими трудностями из-за низкой пластичности и свариваемости магниевых сплавов, а также присутствия на поверхности рыхлой оксидной пленки магния.
Композиты с титановой матрицей армируют волокнами бора, борсика, карбида кремния, бериллия, молибдена. Основное достоинство этих композитов — высокая теплостойкость. Высокие значения прочности сохраняются до 650÷700 °С. В продольном направлении предел прочности композитов составляет 1100÷1300 МПа (в зависимости от вида волокон и их свойств), а в поперечном достигает 650 МПа из-за высокой прочности матрицы. При получении композитов на основе титана возникают значительные технологические трудности, связанные с необходимостью нагрева до высоких температур. При этом титан становится химически активным и взаимодействует с волокнистым наполнителем, что приводит к образованию хрупких фаз по границам раздела. Это требует контроля технологии изготовления с учетом протекающих реакций и степени их развития. Наибольшая совместимость достигается в системах Тi—SiC.
|
|
Композиты в автомобилестроении
Композиционные материалы и изделия на основе непрерывных волокон и армирующих тканей
широко используются для производства внешних деталей автомобиля. Чаще всего из них делают:
Силовые конструкции – силовые структуры дверей и сидений, защитные элементы днища.
Элементы крепления бамперов и радиаторов.
Декоративные элементы – декоративные панели салона, внешние декоративные панели.
Крышки багажников, кузовные панели, тормозные диски, элементы кузова, термо- и звукоизоляцию.
Всё чаще кузова многих типов машин (в том числе тяжёлых грузовиков) полностью создаются из легких, прочных и недорогих углепластиков.
Углепластик в автомобилестроении
Композитные материалы для автомобилестроения – это в первую очередь продукция из углеродного волокна. Она используется в автомобилестроении уже много лет, и с каждым годом объём его применения растёт. Наиболее важное преимущество углеволокна — небольшой вес и высокая прочность.
Углепластик в 5 раз легче стали и в 1,8 раза легче алюминия. Использование композитов в автомобилестроении позволяет снизить массу транспортного средства на 20-25%.
За счёт этого заметно повышается эффективность работы двигателя и снижается расход горючего.
Углеродные волокна производят из синтетических и природных волокон на основе полимеров.
В зависимости от режима обработки и исходного сырья получают материалы разной структуры и с разными свойствами. В этом заключается главное преимущество композитных материалов.
Их можно создавать с изначально заданными свойствами под определённую задачу.
Карбон в автомобилестроении
По прочности карбон превосходит сталь (чёрный металлопрокат) в 12,5 раз. Когда мы говорим «карбон», то вспоминаем, конечно, капоты тюнинг-каров. Сейчас нет ни одной кузовной детали, которая не была бы сделана из карбона. Из него изготавливают не только капоты, но и крылья, бампера, двери и крыши.
Факт экономии веса очевиден. Средний выигрыш в весе при замене капота на карбоновый составляет 8 кг.
Впрочем, для многих главным будет тот факт, что карбоновые детали практически на любой машине выглядят очень стильно.
Углеродное волокно для автомобилей широко применяется в гоночной одежде. Это карбоновые шлемы, ботинки с карбоновыми вставками, перчатки, костюмы, защита спины и. т. д.
Такая экипировка не только хорошо смотрится, но и повышает безопасность и снижает вес костюма (очень важно для шлема).
Особой популярностью карбон пользуется у мотоциклистов. Самые продвинутые байкеры одевают себя в карбон с ног до головы.
Развитие технологии в автомобилестроении в первую очередь связано с развитием автоспорта.
Наблюдая технический прогресс в области развития и применения композиционных материалов, можно уверенно сказать, что в ближайшем будущем появятся серийные автомобили с полностью
композитным кузовом и многими узлами и агрегатами.
ЗАДАНИЕ:
- В письменном виде оформить таблицу1 по видам композитов (смотреть лекционный материал)
Наименование композитов | Физические свойства | Отношение к нагреванию | Ремонтопригодность |
Дата добавления: 2022-07-01; просмотров: 28; Мы поможем в написании вашей работы! |
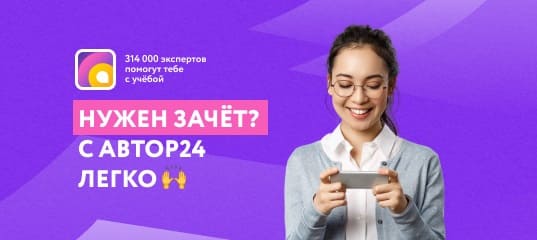
Мы поможем в написании ваших работ!