Сварные нахлесточные соединения (сварка внахлест)
МИНИСТЕРСТВО НАУКИ И ВЫСШЕГО ОБРАЗОВАНИЯ РФ
КАЗАНСКИЙ ГОСУДАРСВЕННЫЙ АРХИТЕКТУРНО - СТРОИТЕЛЬНЫЙ УНИВЕРСИТЕТ
Кафедра железобетонные и каменные конструкции
РЕФЕРАТ
по дисциплине «Основы строительных конструкций»
на тему:
СВАРНЫЕ СОЕДИНЕНИЯ: ВИДЫ, ОСОБЕННОСТИ РАСЧЕТОВ
Выполнил: ст. гр. 0ПГ02
Данилов О.Ю.
Проверил: канд.техн.наук
Фабричная К.А.
Казань 2022
СОДЕРЖАНИЕ
Введение.........................................................................................................................................3
1.История развития сварки...........................................................................................................4
2.Процессы и виды сварки............................................................................................................5
2.1.Стыковые сварные соединения..............................................................................................6
2.2.Нахлесточные сварные соединения.......................................................................................8
2.3.Торцевые сварные соединения.............................................................................................10
2.4.Угловые сварные соединения...............................................................................................11
3.Основные способы сварки.......................................................................................................13
Заключение...................................................................................................................................18
Список литературы......................................................................................................................19
Введение
Сварка металлоконструкций – технология соединения деталей из металла различной степени сложности в единое целое при помощи специального оборудования.
|
|
Она может активно применяться в промышленном масштабе на крупных производствах опытными специалистами, а также для выполнения бытовых операций сварщиками-любителями. В любом варианте, соединения металлоконструкций характеризуется определенными особенностями, которые важно понимать при работе.
Сегодня, сварка - один из наиболее распространенных технологических процессов в ряде отраслей производства. Она необходима и в быту, и в малом строительстве и т. д.
В древности, сварки как самостоятельной технологии не существовало, а простейшие сварочные операции выполняли кузнецы и литейщики. Кузнецы разогревали детали в горне, соединяли, а затем проковывали их. Этот способ известен и сегодня под названием кузнечной, или горновой, сварки.
Именно так сваривали металлические детали вплоть до конца XIX века.
Литейщики пользовались несколько иными способами: они заформовывали и соединяли детали, а участок соединения заливали расплавленным металлом. Сегодня этот способ используется, в частности, при изготовлении художественного литья. Открытие электрической дуги раз и навсегда изменило способы соединения металлических деталей. В 1802 году при экспериментах с электрической дугой удалось получить пламя, способное плавить металл. Однако до разработки сварочного аппарата дело не дошло: ученые опередили свое время, ведь для питания такого мощного устройства был необходим источник электрического тока, а их в начале XIX века еще не существовало.
|
|
Кроме того, промышленность того времени была развита слабо и острой необходимости в сварочном устройстве не было. И только через 80 лет, в конце XIX века, было предложено первое устройство для электрической дуговой сварки с помощью угольного электрода.
Это изобретение вскоре получило самое широкое распространение, причем первыми его оценили по достоинству ремонтники железнодорожных депо.
А еще через несколько лет был изобретен способ, обеспечивающий непрерывное плавление материала и улучшающий качество сварного шва. В ХХ веке были значительно усовершенствованы старые и изобретены новые способы сварки.
В нынешнее время с ростом научно-технического прогресса проблема осуществления и способа сварки изделий имеет достаточно большую актуальность.
Цель: рассмотреть и изучить, что из себя сварные соединения
|
|
Для достижения цели необходимо выполнение следующих задач:
1)Рассмотреть виды, достоинства и недостатки, свойства сварных соединений
2)Ознакомиться с соответствующей литературой, характерной для нашей темы
История развития сварки
Первые способы сварки возникли у истоков цивилизации — с началом использования и обработки металлов.
Известны древнейшие образцы сварки, выполненные в VIII-VII тысячелетиях до н.э. Древнейшим источником металла были случайно находимые кусочки самородных металлов - золота, меди, метеоритного железа. Ковкой их превращали в листочки, пластинки, острия. Ковка с небольшим подогревом позволяла соединять мелкие кусочки более крупные, пригодные для изготовления простейших изделий.
Позже научились выплавлять металл из руд, плавить его и литьем изготовлять уже более крупные и часто весьма совершенные изделия из меди и бронзы.
С освоением литейного производства возникла литейная сварка по так называемому способу промежуточного литья – соединяемые детали заформовывались, и место сварки заливалось расплавленным металлом. В дальнейшем были созданы особые легкоплавкие сплавы для заполнения соединительных твои и наряду с литейной сваркой появилась пайка, имеющая большое значение и сейчас.
|
|
Весьма важным этапом стало освоение железа около 3000 лет назад. Железные руды имеются повсеместно, и восстановление железа из них производится сравнительно легко. Но в древности плавить железо не умели и из руды получали продукт, состоявший из мельчайших частиц железа, перемешанных с частицами руды, угля и шлака. Лишь многочасовой ковкой нагретого продукта удавалось отжать неметаллические примеси и сварить частицы железа в кусок платного металла. Таким образом, древний способ производства железа включал в себя процесс сварки частиц железа в более крупные заготовки. Из полученных заготовок кузнечной сваркой изготовляли всевозможные изделия: орудии труда, оружие и пр. Многовековой опыт, интуиции и чутье позволяли древним Мистерам иногда получать сталь очень высокого качества (булат) и кузнечной сваркой изготовлять изделия поразительного совершенства и красоты.
Кузнечная сварка и пайка были ведущими процессами сварочной техники вплоть до конца ХIХ в., когда начался совершенно новый, современный период развития сварки. Несоизмеримо выросло производство металла и всевозможных изделий из него, многократно - потребность в сварочных работах, которую не могли уже удовлетворить существовавшие способы сварки. Началось стремительное развитие сварочной техники - за десятилетие она совершенствовалась больше, чек за столетие предшествующего периода. Быстро развивались и новые источники нагрева, легко расплавлявшие железо: электрический ток и газокислородное пламя.[2]
Процессы и виды сварки
Сварка – это технологический процесс создания надежных соединений путем нагревания, либо пластической деформации с установлением межатомных связей в последствии. Структура изделий получается не прерывной. К электроду и сварочному материалу через инвертор подводится энергия. Сначала плавится металл электрода, так получается сварочная ванна, в этой ванне происходит смешивание электрода с основным материалом, а шлаки, всплывающие на поверхность служат защитной пленкой. Процесс сварки – это ничто иной, как затвердевание металла после всех вышеперечисленных воздействий. Электроды бывают нескольких видов – плавящиеся (плавится прут электрода) и неплавящиеся (при неплавящемся электроде применяют присадочную проволоку, которая плавится в ванной отдельно).
Вне зависимости от количества видов сварки существуют 3 основных этапа процесса сварки, присущей всем технологическим разновидностям, это:
- Формирование контакта;
- Образование связи;
- Создание шва.
Формирование контакта происходит в результате доведения металла до температуры плавления или кипения, главное не перепутать сварочную ванну с плавкой железа.
Второй, наиболее важный шаг – образование сварочной ванны, она всегда выглядит одинаково вне зависимости от вида сварки. Ванна возникает в результате сплавления металла и вспомогательного материала, к примеру электрода под воздействием, температуры, на вид как белое пятно. От ширины и длины этого пятна зависит качество шва.
По типу соединения выделяют (самые распространенные):
1) Стыковые – детали в одной плоскости (сваривают трубы, листы и тд).
2) Нахлесточные – детали располагаются параллельно, только одна идет внахлест к другой (сваривают листы, толщина которых не более 12 мм).
3) Торцевые – сваривают 2 торца элементов.
4) Угловые – элементы располагаются под углом друстыкг к другу.
2.1 Стыковые сварные соединения (сварка встык) - Стыковое соединение сваркой представляет собой примыкание двух деталей торцевыми поверхностями друг к другу, лежащие на одной плоскости.
Такое соединение простое и надежное, рекомендуется в конструкциях, которые подвергаются воздействию переменных напряжений. Стыковое соединение применяется когда утолщение металла исключено или не подходит, оно обеспечивает красивый внешний вид без выступающих кромок. Стыковое соединение применяют в авиакосмической и автомобильной промышленности. Применяется для образования неразъёмного соединения деталей различных металлических конструкций в том случае, когда поверхности деталей лежат в одной плоскости и и примыкают друг к другу своими торцами. Встык свариваются части различных трубопроводов, обечайки различных емкостей, баллонов, цистерн, листовые конструкции, швеллеры, уголки и прочие фасонные профили.
Преимущества и недостатки
Преимущества при стыковом соединении
- электродный металл используется меньше,
- контролировать процесс не сложно, конструкции получаются надежные,
- техника сварки более простая, чем техника углового шва,
- стыковые соединения обеспечивают плоскостность поверхности конструкции,
- обеспечивают получение соединения деталей различной толщины,
- есть возможность выполнения сварки металла большой толщины односторонним швом.
Недостатки стыкового соединения
- не обеспечивает дополнительной жесткости в сравнении с нахлесточным,
- так же могут образоваться значительные деформации поверхности после сварки (особенно при сварке тонкого металла).
Сварные нахлесточные соединения (сварка внахлест)
Нахлесточный сварной шов относится к распространенным разновидностям сварных соединений, которые используются во многих сферах. Он применяется в тех случаях, когда соединяемые детали находятся параллельно друг другу и их поверхности плотно прилегают одна к другой. При таком расположении и обеспечивается нахлест деталей, благодаря которому их части перекрываются противолежащими. Наличие наложения помогает снять все возможные погрешности и упрощает работу мастеру. Нахлесточное сварное соединение может быть выполнено качественно даже начинающим сварщиком.
Обозначение нахлесточного шва идет по ГОСТ 2602-84, в котором указываются основные понятия, в том числе и стандартные швы. При производстве соединение внахлест обусловлено техническим заданием при конструировании изделия, но в домашних условиях такое соединение часто выбирают благодаря тому, что его можно легко сделать, даже не имея большого опыта в сварке.
Область применения
Применяются такие соединения в тех местах, где требуется достигнуть максимальной прочности на растяжение. Здесь создается сварное соединение с разных сторон, причем швы располагаются не параллельно друг другу, а находятся на определенном расстоянии под углом. Это создает дополнительную прочность при нагрузках на растяжение. В то же время такие швы не стоит применять в тех случаях, когда нагрузка будет действовать на излом. Расчет нахлесточного сварного соединения должен включать в себя все возможные виды нагрузок, которые будут воздействовать на деталь, чтобы она обладала достаточным запасом прочности.
Преимущества и недостатки
Преимущества при нахлесточным соединении:
- Простота создания швов;
- Нет необходимости точно придерживаться всех размеров и параметров, так как погрешности здесь вполне допустимы и не влияют на конечный результат;
- Изделие получает высокую прочность на разрыв;
- Создание швов относительно недорогое в производстве.
Недостатки при нахлесточным соединении:
- Сложности с переносимостью динамических нагрузок (в этом параметре они сильно уступают нахлесточным соединениям);
- Для создания качественных швов для повсеместного использования нужно усиливать их;
- Имеют относительно узкий круг применения при создании техники.
Сварные торцевые соединения
При выполнении таких соединений сваривают торцы заготовок, которые плотно примыкают одна к другой или расходятся от места стыка под углом не больше 30⁰. Способ применяют при производстве кожухов, вентиляционных коробов, контейнеров, металлических шкафов и пр. К достоинствам торцевого типа сварочных соединений относят низкую вероятность образования прожогов и внутренних напряжений, вызывающих деформацию. Недостатками считают завышенный расход материала и появление коррозии при проникновении воды между листами через дефекты шва. Даже в одном типе соединения сварочные швы могут отличаться по конфигурации, протяженности, технологии и т. д. Поэтому в нормативных документах они сгруппированы по параметрам.
Преимущества и недостатки
Преимущества
- Возможна сварка деталей с неровными торцевыми поверхностями, простота сборки.
Недостатки
- Соединение хорошо подходит для нагрузки, но в отличие от таврового, торцевое не имеет такой жесткости.
- Так же недостатком является расход свариваемого материала, коррозия металла при попадании влаги между свариваемыми листами при наличии дефектов (например непровар.
Угловые сварные соединения
Угловое соединение получается в том случае, если край одной детали соединяется сваркой с краем другой детали образуя между собой угол (чаще 90 градусов, но угол может быть под любым углом не менее 30°, если менее, то это уже торцевое).
Электрод должен быть расположен так, что бы сварочная дуга расплавляла кромки обеих деталей.
Сварщик должен выполнять любое сварное соединение качественно с первого раза, так как любые дефекты полученные в процессе сварки влияют на прочность сварного шва. Широкое применение в строительстве, монтаж от небольших до огромных конструкций, в машиностроении, металлическая мебель, каркасы, фермы, емкости, резервуары, строительство мостов и многое другое.
Преимущества и недостатки
Угловое соединение является прочным и распространенным, однако важно учесть, что угловой шов в то же время сложный и требует определенных навыков и опыта. При несоблюдении правил сваривания угловых швов возникнут дефекты в виде
- прожегов ( сквозное отверстие в шве, причина высокий ток, задержка электродом на одном месте, большой зазор),
- свищей ( это трубчатая полость в сварном шве. Образуется за счет коротких замыканий электрода или резком прерывании дуги, так же причиной может стать отсутствие хорошей технологической подготовки свариваемых деталей),
- подрезов ( углубления, образующиеся из-за неправильной техники сварки, неправильное положение электрода, что приводит к ослаблению сечения),
- непроваров ( возникающих из-за силы тока, высокой скорости перемещения электрода, некачественная зачистка, смещение электрода и т.д.),
- наплывов ( стекший металл, так же образованный из-за не правильной техники сварки) и т.д.
Основные способы сварки
Ручная дуговая сварка – это сварка покрытым металлическим электродом. Является наиболее старой и универсальной технологией дуговой сварки.
Для образования и поддержания электрической дуги к электроду и свариваемому изделию от источника питания подводится сварочный ток (переменный или постоянный).
Если положительный полюс источника питания (анод) присоединен к изделию, говорят, что ручная дуговая сварка производится на прямой полярности. Если на изделии отрицательный полюс, то полярность обратная. Под действием дуги расплавляются металлический стержень электрода (электродный металл), его покрытие и металл изделия (основной металл). Электродный металл в виде отдельных капель, покрытых шлаком, переходит в сварочную ванну, где смешивается с основным металлом, а расплавленный шлак всплывает на поверхность.
Размеры сварочной ванны зависят от режимов и пространственного положения сварки, скорости перемещения дуги по поверхности изделия, конструкции сварного соединения, формы и размера разделки свариваемых кромок и т.д. ни обычно находятся в следующих пределах: глубина до 6 мм, ширина 8– 15 мм, длина 10–30 мм.
В результате плавления покрытия электрода вокруг дуги и над сварочной ванной образуется газовая атмосфера, оттесняющая воздух из зоны сварки для предотвращения его взаимодействия с расплавленным металлом. В газовой атмосфере также присутствуют пары легирующих элементов, основного и электродного металлов. Шлак, покрывая капли расплавленного электродного металла и поверхность сварочной ванны, препятствует их взаимодействию с воздухом, а также способствует очищению расплавленного металла от примесей.
По мере удаления дуги металл сварочной ванны кристаллизуется с образованием шва, соединяющего свариваемые детали. На поверхности шва образуется слой затвердевшего шлака.
Дуга зажигается кратковременным прикосновением конца электрода к свариваемому изделию. В результате протекания тока короткого замыкания и наличия контактного сопротивления торец электрода быстро нагревается до высокой температуры, при которой после отрыва электрода происходит ионизация газового промежутка и возникает сварочная дуга.
Электроды для ручной дуговой сварки (ГОСТ 9466-75) изготавливают из сварочной проволоки диаметром 1,6; 2; 2,5; 3; 4; 5; 6; 8; 10 и 12 мм. При использовании в качестве электрода голой проволоки дуга горит неустойчиво из-за плохой проводимости тока между электродом и свариваемой деталью (мало ионов), шов получается низкого качества (выгорание углерода, легирующих добавок, окисление стали и т. п.). Для защиты зоны сварки от кислорода воздуха и устойчивого горения дуги электроды имеют покрытие (обмазку) толщиной 3 – 5 мм. В ее состав входят:
1) ионообразующие вещества – молотый мел, поташ, мрамор. Сгорая в дуге, они образуют ионы и стабилизируют горение дуги;
2) раскислители и легирующие вещества – ферросилиций, ферромарганец, ферротитан, а также уголь – восполняют выгоревшие при сварке;
3) газообразующие – крахмал, древесные опилки. Сгорая в дуге, они оттесняют кислород и азот воздуха от сварочной ванны;
4) шлакообразующие – полевой шпат, расплавляясь и вспучиваясь, он образует над швом шлаковую корочку, которая замедляет остывание шва и снижает сварочные напряжения в нем.
Связующим материалом является жидкое стекло.
Вследствие малой длины электродов, сварку часто приходится прерывать и снова начинать, это снижает производительность и качество шва.
По назначению электроды подразделяют на ряд видов:
- для сварки конструкционных и теплоустойчивых сталей (ГОСТ 9467— 75);
- для сварки высоколегированных сталей с особыми свойствами (ГОСТ 10052—75);
- электроды для наплавки (ГОСТ 10051—75); - электроды для сварки чугуна, цветных сплавов и т. д.
Полуавтоматическая сварка – дуговая сварка автоматически подающимся проволочным электродом (проволокой) в среде защитного газа. Защитный газ, выходя из сопла, вытесняет воздух из зоны сварки. Сварочная проволока подается вниз роликами, которые вращаются двигателем подающего механизма. Подвод сварочного тока к проволоке осуществляется через скользящий контакт.
Химический состав стальной сварочной проволоки выбирают в зависимости от марки свариваемых сталей. Обычно сварочная проволока должна иметь меньшее содержание углерода и большее содержание легирующих элементов, чем свариваемые детали. В этом случае можно получить сварной шов равнопрочным с основным металлом и аналогичными физикохимическими свойствами. Проволока имеет буквенно-цифровое обозначение, включающее диаметр, ее назначение (сварочная, для электродов) и химический состав. Пример условного обозначения сварочной проволоки диаметром 3 мм, содержащей 0,04 % углерода, 20 % хрома и 9 % никеля: проволока ЗСв-04Х20Н9 ГОСТ 2246—70. В конце марки через дефис может быть указано: О - омедненная проволока, Э — проволока для изготовления электродов.
В качестве защитных газов наибольшее распространение получили углекислый газ (СО2), аргон и смесь углекислого газа с аргоном.
Полуавтоматическая сварка в углекислом газе (СО2) является основной и наиболее распространенной технологией сварки плавлением на предприятиях машиностроительной отрасли. Она является экономичной, обеспечивает достаточно высокое качество сварных швов, особенно при сварке низкоуглеродистых сталей, возможна в различных пространственных положениях, требует более низкой квалификации сварщика, чем ручная дуговая сварка.
Углекислый газ обеспечивает защиту зоны сварки, но металл сварного шва получается недостаточно раскисленным, поэтому необходимо выбирать сварочную проволоку с повышенным содержанием марганца (Св-08Г2С, Св- 08ХН2Г2СМЮ и др.).
Аргонодуговая сварка – дуговая сварка в среде инертного газа аргона. Аргон наиболее эффективен, но имеет высокую стоимость, его применяют в основном при сварке цветных сплавов и ответственных изделий из высоколегированных сталей. Может осуществляться плавящимся или неплавящимся электродом. В качестве неплавящегося электрода обычно используется вольфрамовый электрод.
Аргон практически не вступает в химические взаимодействия с расплавленным металлом и другими газами в зоне горения дуги. Будучи на 38 % тяжелее воздуха, аргон вытесняет его из зоны сварки и надежно изолирует сварочную ванну от контакта с атмосферой.
Дуга горит между свариваемым изделием и неплавящимся электродом (обычно из вольфрама). Электрод расположен в горелке, через сопло которой вдувается защитный газ. Присадочный материал подается в зону дуги со стороны и в электрическую цепь не включен.
Аргонная сварка может быть ручной, когда горелка и присадочный пруток находятся в руках сварщика, и автоматической, когда горелка и присадочная проволока перемещаются без непосредственного участия сварщика.
Для улучшения борьбы с пористостью к аргону иногда добавляют кислород в количестве 3–5 %. При этом защита металла становится более активной. Чистый аргон не защищает металл от загрязнений, влаги и других включений, попавших в зону сварки из свариваемых кромок или присадочного металла. Кислород же, вступая в химические реакции с вредными примесями, обеспечивает их выгорание или превращение в соединения, всплывающие на поверхность сварочной ванны. Это предотвращает пористость. При аргонной сварке неплавящимся электродом для зажигания дуги параллельно источнику питания подключается устройство, которое называется «осциллятор». Осциллятор для зажигания дуги подает на электрод высокочастотные высоковольтные импульсы, которые ионизируют дуговой промежуток и обеспечивают зажигание дуги после включения сварочного тока.
Автоматическая сварка под флюсом – дуговая сварка проволокой (проволочным электродом) под слоем флюса с механизированными операциями подачи проволоки и перемещения дуги вдоль линии шва. Флюс — гранулированный порошок, получаемый чаще всего сплавлением компонентов с последующим дроблением. По назначению флюсы подразделяют на три группы: для сварки углеродистых и легированных конструкционных сталей; для сварки высоколегированных сталей и сварки цветных сплавов. По способу изготовления флюсы разделяют на плавленые и керамические. Плавленый флюс получают спеканием его составляющих и последующим дроблением до величины зерен от 0,25 до 3,0 мм. Керамические флюсы представляют собой механическую смесь порошкообразных и зернистых материалов. В состав флюсов входят шлакообразующие компоненты (кремний, марганец, алюминий в виде кремнезема, закиси марганца, глинозема, окись кальция), раскислители (Si, Mn) и легирующие элементы.
Дуговая сварка под флюсом может выполняться автоматами и полуавтоматами, однако последние используются редко. Проволока подается в зону сварки с помощью подающих роликов.
Подвод тока к проволоке осуществляется скользящим контактом. Плотный слой флюса, высыпаемого из бункера во время движения сварочного автомата, обеспечивает эффективную защиту расплавленного металла сварочной ванны от взаимодействия с воздухом. Дуга горит в газовом пузыре, который образуется парами и газами флюса и расплавленного металла. В результате металлургического взаимодействия шлака и расплавленного металла и кристаллизации металла сварочной ванны формируется шов с необходимым химическим составом и механическими свойствами. На поверхности шва располагается легко отделяемая шлаковая корка из затвердевшего флюса. Неизрасходованный флюс собирается во флюсоаппарат для дальнейшего применения при сварке.
Для полуавтоматической и автоматической сварки может применяться порошковая проволока, представляющая собой оболочку, выполненную из стальной полосы, полость которой заполнена флюсом
. Конструкция порошковой проволоки определяет некоторые особенности ее расплавления дугой. Сердечник проволоки на 50-70 % состоит из неметаллических материалов, и поэтому его электрическое сопротивление велико - в сотни раз больше, чем металлической оболочки. Поэтому практически весь сварочный ток проходит через металлическую оболочку, расплавляя ее. Плавление же сердечника, расположенного внутри металлической оболочки, происходит в основном за счет теплоизлучения дуги и теплопередачи от расплавляющегося металла оболочки. Ввиду этого сердечник может выступать из оболочки, касаться ванны жидкого металла или переходить в нее частично в нерасплавленном состоянии. Это увеличивает засорение металла шва неметаллическими включениями.
Существенный недостаток порошковых проволок, сдерживающий их широкое промышленное применение, - повышенная вероятность образования в швах пор, вызываемого наличием пустот в проволоке. Кроме того, нерасплавившиеся компоненты сердечника, переходя в сварочную ванну, способствуют появлению газообразных продуктов. Диссоциация мрамора, окисление и восстановление углерода при нагреве и плавлении ферромарганца в сочетании с мрамором и другие процессы также могут привести к образованию в металле сварочной ванны газовой фазы. В результате этого в швах появляются внутренние и поверхностные поры. Порошковую проволоку можно использовать и при сварке в углекислом газе. Вероятность образования в швах пористости в этом случае снижается.
Электрошлаковая сварка основана на плавлении свариваемого и присадочного металлов теплотой, выделяемой при прохождении электрического тока через расплавленный шлак в период установившегося процесса сварки.
При электрошлаковой сварке дуговой разряд возникает только в самом начале процесса для создания жидкой шлаковой ванны, а затем плавление непрерывно подаваемого электродного металла и оплавление кромок изделия происходит за счет теплоты тока при прохождении его через расплавленный шлак.
Две свариваемые детали устанавливаются вертикально с зазором между кромками. Зазор с двух сторон закрывают медные водоохлаждаемые ползуны. Снизу зазор также закрывается специальным карманом. В зазор засыпается сварочный флюс и опускается сварочная проволока. В процессе сварки проволока подается вниз роликами, токоподвод осуществляется мундштуком. За счет прохождения тока между проволокой и изделием флюс нагревается и расплавляется. Расплавленный флюс образует шлак, который, будучи электропроводным, является источником тепла, приводящим к расплавлению проволоки и кромок и образованию сварочной ванны. Электрическая дуга отсутствует, так как она шунтируется расплавленным шлаком. Процесс сварки идет снизу вверх. Ползуны, охлаждаемые водой через трубки, перемещаются вверх вместе со сварочным автоматом и формируют сварной шов. Расплавленный флюс одновременно обеспечивает защиту сварочной ванны и участвует в металлургических процессах, обеспечивающих требуемое качество сварного шва.
Расход флюса при этом способе сварки невелик и не превышает 5 %-й массы наплавленного металла. Флюс используется такой же, как и для дуговой сварки, или специальный.
Так как выделение теплоты в шлаковой ванне происходит главным образом в области электрода, максимальная толщина металла, свариваемого одной проволокой, обычно ограничена 60 мм. При больших толщинах целесообразно использовать несколько проволок – обычно кратно трем – числу фаз источника питания. При необходимости проволокам придают колебания поперек зазора для его лучшего заполнения.
Электрошлаковая сварка широко используется для соединения металлов повышенной толщины: стали и чугуна различного состава, меди, алюминия, титана и их сплавов.
К преимуществам способа относится возможность сварки за один проход металла практически любой толщины, что не требует удаления шлака и соответствующей настройки сварочной установки перед сваркой последующего прохода, как при других способах сварки. При этом сварку выполняют без снятия фасок на кромках. Для сварки можно использовать один или несколько проволочных электродов или электродов другого увеличенного сечения. В результате этого достигается высокая производительность и экономичность процесса, повышающиеся с ростом толщины свариваемого металла.
К недостаткам способа следует отнести то, что электрошлаковая сварка технически возможна при толщине металла более 16 мм и за редкими исключениями экономически выгодна при сварке металла толщиной более 40 мм. Чаще всего она используется для сварки изделий толщиной 100–500 мм. Способ позволяет сваривать только вертикальные швы. Недостатком электрошлаковой сварки является также увеличенная зона термического влияния, вызванная медленным нагревом и охлаждением металла. Это часто приводит к образованию неблагоприятных, крупнозернистых структур и требует термообработки для получения необходимых свойств сварного соединения.
Электрошлаковая сварка применяется при изготовлении массивных станин, валов мощных турбин, толстостенных котлов и барабанов. Ее применение вносит коренные изменения в технологию производства крупногабаритных изделий. Появляется возможность замены крупных литых или кованых деталей сварно-литыми или сварно-коваными из более мелких поковок или отливок.
Заключение
Сварка представляет собой процесс создания неразъемного соединения металлических деталей, важнейшую операцию сборки деталей в узлы и целые конструкции. Сегодня в промышленности внедрено более 100 способов сварки, появляются новые способы, совершенствуются старые. Но прежде чем сварка заняла свое место в современной технике, она прошла долгий путь.
Способ получения неразъемных соединений деталей путем сварки и пайки стал известен людям в глубокой древности. В Египетских пирамидах при раскопках были найдены золотые изделия, которые имели пьяные оловом соединения, а при раскопках Помпеи обнаружены свинцовые водопроводные трубы с продольным паяным швом.
Список литературы
1. Сварка и резка металлов. Глизманенко Д.Л. Москва К-51, Неглинная ул., 29/14 издательство “Высшая школа” 1975 г.
2. Стыковые сварные соединения [Электронный ресурс]. – Режим доступа: https://weldelec.com/svarka/nauchitsya/soedineniya/stykovye/ – Заглавие с экрана. – (Дата обращения 16.07.2019).
3. Нахлесточные сварные соединения [Электронный ресурс]. – Режим доступа: https://svarkaipayka.ru/tehnologia/drugoe/nahlestochnoe-svarnoe-soedinenie.html – Заглавие с экрана. – (Дата обращения 13.02.2019).
4. Коновалов А.Б., Кириленко А.Л., Аввакумов М.В. Сварные соединения: Учебное пособие. Санкт-Петербург, 2010 г.
5. Расчет сварных соединений и конструкций. Примеры и задачи. Серенко А.Н., Крумбольт М.Н., Багрянский К.В. - Киев: Издательское объединение «Вища школа», 1977. - 336 с.
6. Николаев Г.А., Винокуров В.А. Сварные конструкции. Расчет и проектирование: учебник для вузов / под ред. Г.А. Николаева. – М.: Высш. шк., 1990. – 446 с.
7. Сварка металлоконструкций [Электронный ресурс]. – Режим доступа: https://mydocx.ru/6-124208.html – Заглавие с экрана. – (Дата обращения 7.04.2017).
8. . Сварка угловых соединений [Электронный ресурс]. – Режим доступа: https://weldelec.com/svarka/nauchitsya/soedineniya/uglovye/– Заглавие с экрана. – (Дата обращения 27.09.2017).
9. Сварка металлических конструкций [Электронный ресурс]. – Режим доступа: https://tutsvarka.ru/vidy/svarka-metallokonstruktsij – Заглавие с экрана. – (Дата обращения 23.08.2013).
10. Виды сварки металлов [Электронный ресурс]. – Режим доступа: https://tutsvarka.ru/vidy/vidy-svarki – Заглавие с экрана. – (Дата обращения 05.11.2018).
Дата добавления: 2022-06-11; просмотров: 129; Мы поможем в написании вашей работы! |
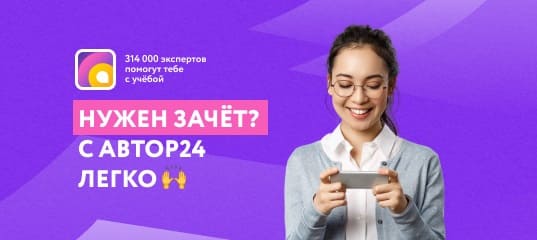
Мы поможем в написании ваших работ!