Отпуск и термомеханическая обработка стали
Урок №42-43
Классификация видов термической обработки. Закалка. Отжиг. Отпуск. Нормализация. Дефекты технической обработки.
Отжиг и нормализация углеродистой стали
После литья, проката, ковки и других видов обработки происходит неравномерное охлаждение заготовок. Результатом является неоднородность структуры и свойств в различных местах заготовок, а также появление внутренних напряжений. Кроме того, при затвердевании отливки получаются неоднородными по химическому составу вследствие ликвации. Для устранения таких дефектов производят термообработку, к которой относятся отжиг и нормализация.
Отжиг заключается в нагреве заготовок или изделий до определенной температуры, в выдержке при данной температуре с последующим медленным охлаждением со скоростью около 200 СС в час для углеродистых сталей и 30—100 °С в час для легированных сталей. При этом получают устойчивую структуру без остаточных напряжений. Цель отжига — снятие внутренних напряжений, устранение структурной неоднородности, улучшение обрабатываемости и подготовка к последующей операции термообработки. Отжиг бывает полный, неполный, гомогенизирующий и низкий.
Полному отжигу подвергают доэвтектоидные стали путем нагрева их выше линии GS , т. е. выше линии Ас3, на 20—30° (рис. 27) и выдержке при этой температуре в течение 0,25 продолжительности нагрева, а затем медленному охлаждению вместе с печью до температуры
|
|
660—400 °С. Охлаждение ведут со скоростью 100—150 °С в час. Отжиг сопровождается фазовой перекристаллизацией, в результате чего в стали получается мелкозернистая структура. При полном отжиге снижаются твердость и прочность стали, значительно улучшается структура и образуется пластинчатый перлит.
Неполный отжиг состоит в следующем: сталь нагревается на 30—40°С выше линии SK (рис. 27), примерно до температуры 750—760 °С. Для инструментальных углеродистых сталей этот отжиг является единственным видом термообработки. При этом получается зернистый перлит, вследствие чего улучшается обрабатываемость стали и снижаются напряжения. Отжигают до получения зернистого перлита эвтектоидные и заэвтектоидные стали. После нагрева и выдержки (3—5 ч) при заданной температуре их медленно охлаждают вместе с печью.
Гомогенизация (диффузионный отжиг) применяется для слитков и крупных отливок в целях выравнивания (диффузии) химического состава стали. Сталь нагревают до температуры 1000—1100°С и выдерживают при этой температуре 10—15 ч, а затем медленно охлаждают до 600—550 °С. Диффузионный отжиг приводит к росту .зерен стали: этот дефект устраняется повторным отжигом до образования мелкого зерна (полный отжиг). Сталь приобретает высокие механические свойства.
|
|
Низкий отжиг используют в тех случаях, когда полученная в результате литья или другой обработки структура стали удовлетворительна и нужно только снять внутренние напряжения. В этом случае сталь нагревают до температуры значительно ниже линии Ac 1 (рис. 27), выдерживают при данной температуре и охлаждают; как правило, на воздухе. Низкий отжиг часто называют сфероидизацией, цементитные пластинки перлита принимают округлую сферообразную форму.
Нормализация стали представляет собой нагрев стали выше линии GSE на 30—50 °С (рис. 27) с выдержкой при заданной температуре и последующим охлаждением на воздухе. Нормализацию применяют для устранения внутренних напряжений и явлений наклепа с целью повысить механические свойства стали. В результате нормализации структура стали становится нормальной, мелкозернистой. Благодаря ускоренному охлаждению по Сравнению с отжигом операция нормализации часто служит подготовкой стали к закалке. Малоуглеродистые стали рекомендуется не отжигать, а нормализовать, так как для них практически нет разницы в механических свойствах после отжига или нормализации, но нормализация значительно производительнее отжига.
|
|
Закалка стали
Закалку используют для повышения твердости, прочности и упругости стали. Она включает нагрев до температур, превышающих температуру фазовых превращений, выдержку при этой температуре и последующее быстрое охлаждение.
Аустенит устойчив только при температурах выше линии GSE (рис. 27). При быстром охлаждении аустенит начинает распадаться. Если медленное охлаждение (при отжиге) приводит к образованию перлита, то при быстром охлаждении аустенит распадается с образованием новой структуры, представляющей собой мелкозернистую ферритно-цементитную смесь, причем чем выше скорость охлаждения, тем зерна мельче, ее структура резко отличается по своим свойствам от перлита. Образование структур зависит от скорости охлаждения. Присравнительно медленном охлаждении, например на воздухе, аустенит превращается в структуру, называемую сорбитом. При охлаждении в масле образуется троостит. Сорбит образуется в интервале температур от 600 до 500 °С. Ферритно-цементитные пластинки в нем мельче перлитных. Троостит образуется при еще более низких температурах в процессе охлаждения (500—200 °С). Ферритно-цементитные пластинки троостита еще мельче, чем сорбита. Троостит тверже сорбита. Так, твердость сорбита НВ 250—300, а троостита НВ 350—450. Обе структуры представляют собой механические смеси (феррита с цементитом). При охлаждении в воде (это наибольшая скорость охлаждения) аустенит сохраняется в углеродистой стали примерно до температуры 250—200 °С,. а затем мгновенно превращается в новую структуру, называемую мартенситом. Однако в сталях с высоким содержанием углерода аустенит не полностью превращается в мартенсит. Эта сохранившаяся часть аустенита называется остаточной.
|
|
Мартенсит отличается от сорбита и троостита и структурой, и свойствами. Это пересыщенный твердый раствор углерода в α-железе, обладающий характерной игольчатой структурой. Мартенсит — самая твердая и
хрупкая структура, его твердость 600—700 НВ (62— 72 HRCэ), а ударная вязкость близка к нулю. Мартенсит магнитен и сохраняет остаточный магнетизм, поэтому изготовленные магниты закаливают до мартенсита. Закалка заключается в нагреве стали до температур на 30—50 °С выше критических точек Ас3 для доэвтектоидной стали и Ас1 — для заэвтектоидной (рис. 28) с выдержкой при данной температуре и последующим быстрым охлаждением в различных жидкостях (воде, масле, растворах солей и др.). Для закалки углеродистых сталей рекомендуется вода при температуре 18°С. В зависимости от скорости охлаждения при закалке кроме мартенсита могут получаться сорбит и троостит. Они образуются при меньших скоростях охлаждения. Скорость охлаждения, при которой получается мартенсит, называется критической скоростью закалки.
Выбор температуры закалки. Температура нагрева при закалке стали зависит от ее химического состава. В доэвтектоидных сталях, нагреваемых на 30—50 °С выше линии Ас3 (рис. 28), получается аустенит, при последующем охлаждении, превышающем критическую скорость закалки, он преобразуется в мартенсит. Такую закалку называют полной. При нагреве этой стали до температуры в интервале Ас3 — Ас1 в структуре мартенсита сохраняется часть оставшегося при закалке феррита, снижающего твердость закаленной стали. Такую закалку называют неполной. Для закалки заэвтектоидной стали наилучшей температурой является нагрев на 30—50 °С выше линии Ac 1 . В этом случае в стали сохраняется цементит и при нагреве, и при охлаждении, а это способствует повышению твердости, так как твердость цементита больше, чем твердость мартенсита. Нагрев заэвтектоидной стали до температуры выше линии SE излишний, так как твердость при этом меньше, чем при закалке выше линии Ас3 за счет растворенного цементита. Кроме того, при охлаждении после нагрева до более высоких температур могут возникнуть большие внутренние напряжения.
Скорость охлаждения. Для получения структуры мартенсита следует переохладить аустенит путем быстрого охлаждения стали в интервале температур наименьшей его устойчивости, т. е. при температуре 550—650 °С. В зоне температур мартенситного превращения (ниже 250 °С) выгоднее применять замедленное охлаждение, так как образующиеся структурные напряжения, связанные с получением новой кристаллической решетки, могут успеть выровняться, а твердость мартенсита не снизится. Для успешного проведения закалки имеет значение выбор закалочной среды (вода, водные растворы солей, минеральное масло). При закалке легированных сталей применяется масло.
Закаливаемость и прокаливаемость стали. Закаливаемость зависит от содержания в стали углерода. Чем больше углерода в стали, тем она лучше закаливается. Сталь с очень низким содержанием углерода (менее 0,3%) не закаливается. Прокаливаемость стали характеризуется ее способностью закаливаться на определенную глубину. Это очень важное свойство закаленной стали. При сквозной прокаливаемости все сечение закаливаемой детали приобретает однородную структуру непосредственно после закалки и отпуска. При малой прокаливаемости структуры слоев, лежащих ближе к поверхности, и внутренних слоев резко различаются: внутренние слои намного мягче и прочность их ниже прочности закаленных слоев. Прокаливаемость зависит от критической скорости закалки. На глубину закалки влияют температура нагрева и закалочная среда. Условились закаленными считать слои, в которых содержание мартенсита не менее 50%.
Виды закалки стали. По способу охлаждения различают виды закалки: в одной среде, в двух средах (прерывистая), ступенчатая и изотермическая. Закалка в одной среде проще и применяется чаще для изделий несложной формы. Заэвтектоидные стали, если детали имеют простую форму, закаливают в одной среде. При прерывистой закалке изделие охлаждают, сначала в одной среде (например, в воде), а затем в масле или на воздухе. Ступенчатую закалку производят путем быстрого охлаждения в соляной ванне, температура которой немного выше 240—250 °С (соответствующей началу мартенситного превращения), затем дают выдержку при данной температуре и охлаждают на воздухе. Короткая остановка при охлаждении способствует выравниванию температуры по всему сечению детали, что уменьшает напряжения, возникающие в процессе закалки.
Ступенчатую закалку применяют для деталей из углеродистой стали небольшого сечения (8—-10 мм). Для сталей, имеющих небольшую критическую скорость закалки, ступенчатая закалка применяется в основном для 'изделий большого сечения. При изотермической закалке, как и при ступенчатой, детали переохлаждают в среде, нагретой выше температуры начала мартенситного превращения, однако выдержка при этой температуре продолжительная — до полного распада аустенита. Получается структура не мартенсита, а близкого по твердости игольчатого троостита, но более прочного и пластичного дальнейшее охлаждение производят на воздухе. Преимущества изотермической закалки заключаются в большей вязкости, отсутствии трещин, минимальных короблений. Изотермическую закалку применяют для изделий сложной формы.
Способы охлаждения при закалке имеют важное значение, так как при этом возникают большие внутренние напряжения, которые могут привести к короблению детали, поэтому важно не только правильно подобрать охлаждающую среду, но применять правильные способы погружения. Например, длинные изделия вытянутой формы (сверла, метчики) нужно погружать в строго вертикальном положении, чтобы избежать коробления.
Отпуск и термомеханическая обработка стали
Отпуск — заключительная операция термообработки, состоящая в нагреве закаленной стали до температуры ниже критической (Ас1) с выдержкой при этой температуре и с последующим охлаждением: медленным или быстрым. Цель отпуска — устранить или уменьшить напряжение в стали, повысить вязкость и понизить твердость. Для отпуска сталь нагревают до температуры 150—600 °С. В зависимости от температуры нагрева различают три вида отпуска: низкотемпературный, средне-температурный и высокотемпературный
При низкотемпературном отпуске закаленную сталь нагревают до температуры 150—250 °С. После соответствующей выдержки при этой температуре (обычно 1—3 ч) в детали получают структуру отпущенного мартенсита. При низком отпуске частично снимаются закалочные напряжения. Если в стали было значительное количество остаточного аустенита, то твердость после низкого отпуска может увеличиваться на 2—3 ед. Низкий отпуск применяют для инструментальных сталей после цементации, поверхностной закалки и т. д.
При среднетемпературном отпуске закаленную сталь нагревают до температуры 350—400 °С. В результате образуется структура троостита. После такого отпуска в изделиях получается сочетание сравнительно высоких твердости (41—46 HRCэ) и прочности с хорошей упругостью и достаточной вязкостью. Поэтому среднему отпуску подвергаются главным образом пружины и рессоры.
При высокотемпературном отпуске закаленные изделия нагревают до температуры 450—650 °С. После такого нагрева и соответствующей выдержки образуется структура сорбита. В отличие от сорбита, полученного после нормализации, когда цементит пластинчатый, после высокого отпуска цементит приобретает зернистую структуру. Это существенно повышает ударную вязкость. Поэтому такой отпуск применяют для деталей машин, испытывающих при эксплуатации ударные нагрузки.
Закалку с высоким отпуском называют улучшением. Чем выше температура отпуска, тем больше увеличивается ударная вязкость, но для некоторых конструкционных сталей наблюдается уменьшение ударной вязкости. Этот дефект называется отпускной хрупкостью, он зависит от скорости охлаждения при отпуске, объясняется неравномерностью превращений мартенсита в сорбит. Для углеродистых сталей отпускная хрупкость при повторных нагревах тех же деталей не наблюдается. Для легированных сталей она обратима, поэтому изделия из стали, •склонной к отпускной хрупкости, нельзя использовать для эксплуатации при нагреве.
Обработка холодом. Этот метод разработан советским ученым А. П. Гуляевым. Сущность способа заключается в дополнительном, более полном превращении остаточного аустенита закаленной стали в мартенсит, Остаточный аустенит снижает твердость, ухудшает магнитность, приводит к изменению размеров деталей в процессе эксплуатации.
Обработка холодом состоит в том, что закаливаемые детали на некоторое время погружают в среду, имеющую температуру ниже 0°С. Наиболее частая температура —80 °С, охлаждением при такой температуре добиваются полного или почти полного мартенситното превращения. Производить обработку холодом нужно сразу же после закалки. Такой обработке подвергают измерительный инструмент, части точных механизмов, детали шарикоподшипников и т. п. Обработка холодом не уменьшает внутренних напряжений, поэтому после нее необходим отпуск.
При обработке деталей холодом следует учитывать, свойства стали и способность остаточного аустенита при комнатных температурах стабилизироваться. Поэтому, например, для среднеуглеродистых конструкционных сталей разрыв между закалкой и обработкой холодом регламентируется во времени. Для некоторых сталей, не особенно склонных к стабилизации остаточного аустенита, выдержку во времени между закалкой и обработкой холодом можно увеличить до 3 ч.
Термомеханическая обработка (ТМО). В настоящее время является самой эффективной в машиностроении.. Она относится к комбинированным способам изменения-строения и свойств металла, совмещает механическую-деформацию металла в горячем состоянии с термообработкой. Как при термической, так и при пластической деформации повышение прочности всегда связано с уменьшением пластичности. Это часто является ограничением применения той или иной обработки. Преимуществом ТМО является то, что при существенном увеличении прочности характеристики пластичности снижаются незначительно, а ударная вязкость в 1,5—2 раза выше по сравнению с ударной вязкостью той же марки стали после закалки с низким отпуском.
Сущность ТМО состоит в том, что заготовки сразу после окончания горячей обработки давлением (ковки, проката) подвергаются закалке без специального нагрева, используя остаточное тепло после горячего деформирования. Нужно, чтобы температура в конце горячей обработки давлением была на 20—30 °С выше линии Ас3 (рис. 28). Повышение прочности при ТМО объясняется тем, что в результате деформации аустенита происходит
дробление его зерен, их уменьшение в 2—4 раза по сравнению с обычной закалкой, что приводит к повышению плотности стали. Преимущество совмещенного процесса состоит в экономии топлива для нагрева под закалку, сокращении времени изготовления деталей, существенном повышении механических свойств, значительном увеличении прочности, ударной вязкости и незначительном снижении пластичности. ТМО применяют для упрочнения не только конструкционных сталей, но и других сплавов, в частности титановых и жаропрочных.
Дата добавления: 2022-06-11; просмотров: 83; Мы поможем в написании вашей работы! |
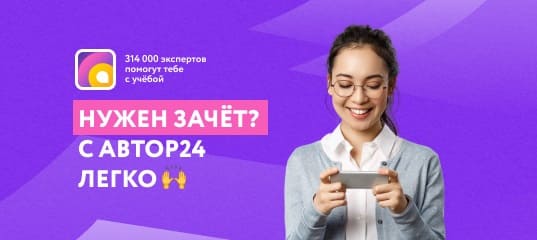
Мы поможем в написании ваших работ!