ТО и ТР системы смазки и охлаждения двигателя
Тема 4.1 . Оборудование и технологическая оснастка для технического обслуживания и ремонта двигателей
Конспект : время на выполнение 2 часа.
Технология технического обслуживания и ремонта механизмов и систем двигателя.
Вопросы темы:
Отказы и неисправности двигателя. Общая диагностика ДВС
Диагностика технического состояния и техническое обслуживание газораспределительного механизма и цилиндропоршневой группы
ТО и ТР системы смазки и охлаждения двигателя
Отказы и неисправности двигателя. Общая диагностика ДВС.
Отказы и неисправности. При эксплуатации двигателя в цилиндропоршневой группе (ЦПГ), кривошипно-шатунном механизме (КШМ), газораспределительном механизме (ГРМ), вспомогательных узлах и агрегатах появляются дефекты, которые могут быть вызваны как естественным и ускоренным износом деталей, так и внезапным появлением дефектов, потерей работоспособности деталей. Практика эксплуатации отечественных легковых автомобилей показывает, что примерно 20% всех отказов приходится на двигатель и его системы.
К основным отказам и неисправностям КШМ относят: износ, заклинивание, разрушение вкладышей; деформацию постелей в блоке; деформацию коленчатого вала; деформацию, износ отверстий нижней головки шатуна; обрыв шатуна или шатунных болтов; износ втулки верхней головки шатуна; износ подшипников балансирных валов; заклинивание, разрушение подшипников балансирных валов.
|
|
Для ЦПГ характерны появление разрушений перемычек, трещин в поршне; прогорание днища поршня; износ поршней, колец, цилиндров, поршневых пальцев; разрушение поршневых колец; деформация юбки поршня, задиры на юбке и поверхности цилиндра, возникновение пробоин, трещин в цилиндре или блоке; коробление плоскостей блока; выпадение фиксаторов поршневого пальца в поршне.
Основными признаками неисправности КШМ и ЦПГ являются: падение компрессии в цилиндрах, появление посторонних шумов и стуков при работе двигателя; появление из маслозаливной горловины голубоватого дыма с резким запахом; увеличение расхода масла, разжижение моторного масла.
Существенный перечень отказов и неисправностей имеет ГРМ: износ седла, клапана и направляющих втулок; разрушение, прогар клапанов; разрушение пружин; износ подшипников распределительного вала; перегрев и разрушение подшипников распределительного вала; износ кулачков распределительного вала и толкателей; износ коромысел и их осей; разрушение седла клапана; заклинивание гидротолкателей; износ цепи (ремня) и звездочек (шкивов) привода распределительного вала; разрушение зубьев звездочек; заклинивание гидронатяжителя; износ плунжера натяжителя цепи; прогар головки блока цилиндров; трещина, пробоина в головке блока; коробление головки блока.
|
|
Признаками неисправности ГРМ являются стуки, вспышки в карбюраторе и хлопки в глушителе.
Общим признаком неисправностей КШМ, ЦПГ и ГРМ является повышение расхода топлива и снижения мощности двигателя.
К основным отказам и неисправностям вспомогательных узлов и агрегатов следует отнести: износ шестерен, корпуса маслонасоса; заклинивание маслонасоса; негерметичность, заклинивание редукционного клапана; разрушение, негерметичность маслоприемника; негерметичность насоса охлаждающей жидкости; разрушение уплотнения и подшипника насоса охлаждающей жидкости; износ, разрушение подшипников и уплотнений турбокомпрессора.
Диагностика технического состояния и техническое обслуживание газораспределительного механизма и цилиндропоршневой группы.
Состояние цилиндропоршневой группы и клапанного механизма проверяют по давлению в цилиндре в конце такта сжатия. Состояние цилиндропоршневой группы и клапанного механизма можно проверить, измеряя утечку сжатого воздуха, подаваемого в цилиндры (рис. 8). Сравнительно быстро и просто определяют наличие в любом из них следующих характерных дефектов: износ цилиндров, износ поршневых колец, негерметичность и прогорание клапанов, задиры по длине цилиндра, поломка пружин и зависание клапанов, поломка и "залегание" поршневых колец, прогорание внутренней части прокладки головки блока.
|
|
Рис. 8. Принципиальная схема прибора для проверки герметичности надпоршневого пространства цилиндров двигателя: 1 - быстросъемная муфта; 2 - входной штуцер; 3 - редуктор; 4 - калиброванное сопло; 5 - манометр; 6 - демпфер стрелки манометра; 7 - регулировочный винт; 8 - выходной штуцер; 9 - соединительная муфта; 10 - присоединительный штуцер
Техническое обслуживание. Для предотвращения отказов и неисправностей двигателя на автотранспортных предприятиях выполняется комплекс профилактических мероприятий, включающих диагностику; ЕО двигателя; ТО-1, ТО-2, СО, Для легковых автомобилей, принадлежащих гражданам, с этой же целью выполняется перечень операций, регламентированных талонами сервисной книжки.
Регулировка зазоров привода клапанов в механизме газораспределения (без гидротолкателей) выполняется на холодном двигателе при полностью закрытых клапанах. Перед началом регулировки поршень первого цилиндра подводится в положение верхней мертвой точки (ВМТ) при такте сжатия, что можно контролировать по закрытию обоих клапанов первого цилиндра. Зазор, как правило, измеряют плоским щупом (возможно использование приспособления с индикаторной головкой часового типа).
|
|
Появление в конструкции ГРМ гидротолкателей позволяет автоматически выбирать зазор в приводе клапана. Однако гидротолкатели очень чувствительны к качеству масла и степени его очистки. Коксование масла, частицы износившихся и разрушившихся деталей способствуют заклиниванию гидротолкателей. В таком случае возникают ударные нагрузки, на которые механизм не рассчитан. Они быстро приводят к поломкам, или к таким износам деталей (толкатели, кулачки распределительного вала), при которых их дальнейшая эксплуатация невозможна.
Ремонт головки блока. При перегреве двигателя, перетяжке головки, а также при длительной эксплуатации нижняя плоскость головки блока деформируется.
В большинстве случаев имеет место деформация местного характера, при которой наружные края плоскости головки "возвышаются" над серединой (обычно не более 0,1 мм) Допустимым искривлением головки считается величина 0,05-0,06 мм.
Седла клапанов в процессе эксплуатации приобретают форму, отличную от конической: появляется овальность седла по фаске из-за неравномерного износа седла. Кроме того, при перегреве и деформации головки часто возникает несоосность направляющих втулок и седел клапанов. Встречаются случаи, когда на фаске седла (обычно выпускного клапана) появляются раковины из-за нарушения процесса сгорания и перегрева.
Основными способами ремонта седел клапанов являются фрезерование (
В качестве абразива предпочтительно использовать корундовую пасту зернистостью 28-40 мкм или аналогичный порошок с трансмиссионным маслом. Алмазные пасты применять нежелательно, так как из-за внедрения твердых частиц в металл ускоряется износ рабочих фасок седла и клапана в эксплуатации после ремонта.
Для контроля качества прилегания клапана к седлу после притирки существует несколько методов: по индикатору специального вакуумного измерительного приспособления, по краске, по "карандашу", а также по утечке керосина, налитого в камеру сгорания при собранных клапанах и пружинах. Наиболее простой является проверка с помощью мягкого карандаша, при которой на фаску клапана равномерно наносится 6-8 радиальных линий. После установки клапана необходимо нажать на тарелку и повернуть клапан на 180° в обе стороны. Если все сделано правильно, линии будут стерты.
ТО и ТР системы смазки и охлаждения двигателя
Система смазки. Внешними признаками неисправности системы являются потеря герметичности, загрязнение масла и несоответствие давления в системе нормативным значениям. Для многих грузовых автомобилей при скорости 40-50 км/ч на прямой передаче давление в системе должно быть примерно 0,2-0,5 МПа. Например, в прогретом двигателе КамАЗ-740 при 2600 об./мин. коленчатого вала рабочее давление масла должно быть 0,45-0,5 МПа. При падении давления до 0,09-0,04 МПа на щитке приборов ряда автомобилей загорается сигнальная лампа.
Удаление осадков, т.е. промывка системы смазки, является необходимой технологической операцией, особенно при сезонном переводе работы двигателя на масло другой марки. Промывочные масла - это маловязкие жидкости с особыми присадками. У каждой марки масла своя технология применения, но эффект примерно одинаков.
Некоторые марки промывочных масел после отстаивания можно еще использовать 1-2 раза. При отсутствии промывочных масел можно использовать обычные маловязкие масла, время промывки - примерно 10 мин., или, как исключение, летнее дизельное топливо, время промывки - не более 5 мин.
Надежность работы системы во многом зависит от состояния фильтров. Многие двигатели грузовых автомобилей имеют два фильтра: полнопоточный (грубой очистки) и центробежный (тонкой очистки). При ТО-2 у полнопоточных фильтров заменяют фильтрующие элементы, а центробежные разбирают, осматривают и промывают.
В обычных условиях эксплуатации, когда центрифуга работает исправно, в колпаке ротора после 10-12 тыс. км пробега скапливается 150-200 г отложений, в тяжелых условиях - до 600 г (толщина слоя отложений в 4 мм соответствует примерно 100 г). Следует иметь в виду, что в некоторых фильтрах ротор имеет частоту вращения до 5000 об./мин. При неправильной сборке будет сильная вибрация со всеми возможными последствиями. У правильно собранного и чистого фильтра после остановки двигателя ротор продолжает вращаться 2-3 мин., издавая характерное гудение.
Периодичность замены масла назначают в зависимости от марки масла и модели автомобиля. Уровень масла проверяют через 2-3 мин. после остановки двигателя. Он должен быть между метками маслоизмерительного щупа.
Система охлаждения. Внешними признаками неисправности системы охлаждения являются перегрев или недостаточный прогрев двигателя, потеря герметичности. Перегрев возможен даже при небольшом снижении уровня охлаждающей жидкости в системе. Особенно это проявляется при применении антифризов, которые могут вспениваться из-за наличия в системе воздуха и замедлять отвод тепла. Для предотвращения замерзания антифриза необходимо поддерживать его нормативную плотность. Так, при 20 °С плотность антифриза А-40 должна быть 1,067-1,072 г/см3, а антифриза Тосол А-40 - 1,075-1,085 г/см3.
Если охлаждающей жидкостью является вода, в системе образуется накипь, ухудшающая теплообмен. Удаляют накипь специальными составами. При их отсутствии в условиях АТП для двигателей с чугунной головкой блока можно использовать раствор каустика (700-1000 г каустика и 150 г керосина на 10 л воды), для двигателей с головкой и блоком из алюминиевого сплава - раствор хромпика или хромового ангидрида (200г на 10л воды). Раствор заливают и выдерживают в системе охлаждения 7-10 ч. Затем запускают двигатель на 15-20 мин. (на малой частоте вращения) и раствор сливают. Для удаления шлама систему промывают водой в направлении, обратном циркуляции охлаждающей жидкости.
Герметичность радиаторов восстанавливают пайкой мест повреждения. Сильно поврежденные трубки заменяют на новые или удаляют (заглушают), места установки пропаивают.
Пайка радиаторов из латунных сплавов сложностей не вызывает. Труднее ремонтировать радиаторы из сплавов алюминия. Для этого используют газовые горелки, специальный присадочный материал и припой. По некоторым технологиям место для пайки надо нагреть до 400-560 °С. Если деталь прогрета недостаточно, то припой будет распределяться по поверхности не равномерно, как требуется, а отдельными наплывами.
Перед установкой на автомобиль герметичность радиатора испытывают сжатым воздухом под давлением 0,1 МПа в течение 3-5 мин. При испытании водой давление должно быть 0,1-0,15 МПа.
Контрольные вопросы темы:
Дата добавления: 2022-06-11; просмотров: 88; Мы поможем в написании вашей работы! |
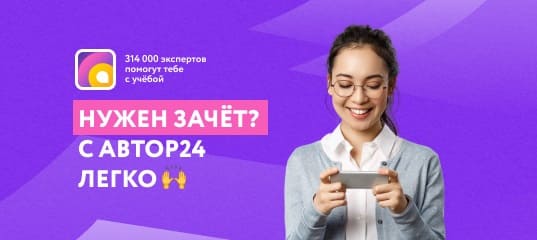
Мы поможем в написании ваших работ!