Температура нагрева при закалке стали
Выбор температуры закалки производится в зависимости от температуры критических точек, как показано на рис 1.2.7
Рис 1.2.7 Оптимальный интервал закалочных температур углеродистой стали
Доэвтектоидные стали нагреваются выше температуры точки Асз на 30. ..50 °С., то-есть производят полную закалку. Заштрихованная область соответствует структуре мелкозернистого аустенита. Такой нагрев обеспечивает получение мелкоигольчатого мартенсита Нагрев этих сталей выше температуры точки Ас1 но ниже Асз приведет при последующем быстром охлаждении к структуре неполной закалки, при этом образуется смесь структур мартенсита и феррита.
Рис Структура неполной закалки стали стали 40 (мартенсит и феррит)
Из-за низкой твердости феррита (800НВ) твердость стали после закалки будет существенно понижена. Поэтому, среднеуглеродистые стали такой закалке не подвергают, но низкоуглеродистые стали ( типа 09Г2) иногда подвергаются такой закалке. В этом случае их структуру называют двухфазной
Для заэвтектоидных сталей оптимальной является температура нагрева выше температуры точки Ас1, на 30... 40 °С., то-есть выполняют неполную закалку . Почему заэтектоидные стали подвергают неполной закалке? Дело в том , что в этом случае при закалке образуется структура мартенсита закалки и вторичного цементита. При таком сочетании структурных составляющих обеспечивается максимальная твердость стали после закалки, так как твердость цементита (7500НВ) даже выше, чем твердость мартенсита высокоуглеродистой стали (7000НВ). В то же время, при полной закалке заэвтектоидных сталей в структуре образуется большое количество остаточного аустенита, понижающего твердость стали. Кроме того, более высокая температура нагрева вызывает рост зерна аустенита, что приводит к крупноигольчатому мартенситу.
|
|
Время нагрева и выдержки
Скорость нагрева. Нагрев стали определяется не только допустимой, но и возможной скоростью нагрева. Допустимая скорость должна быть такой, чтобы нагрев не вызывал больших напряжений, приводящих к образованию трещин в деталях.
Скорость нагрева зависит от формы и материала деталей, типа нагревательных печей и нагревательной среды. Например, шар нагревается в три раза, а цилиндр - в два раза медленнее, чем пластинка. Легированные стали нагреваются медленнее, чем углеродистые из-за меньшей теплопроводности.
Скорость нагрева зависит также от расположения деталей в печи. Если детали плотно располагаются одна к другой и мешают необходимому доступу тепла, то потребуется больше времени для их прогрева.
|
|
На практике для определения времени рнагрева часто пользуются эмпирическими ( полученными из опыта) формулами. Так, для тел простой формы и небольшого размера применима формула для расчета времени нагрева:
τ = s· k· f· L
здесь τ - время нагрева деталей в минутах
f - фактор раскладки деталей в печи
s - характеристический размер ( диаметр цилиндра, толщина пластины) в миллиметрах
k- коэффициент формы ( шар к = 0,7, пластина к= 1,5 )
L- коэффициент легированности стали (для нелегированных сталей равен 1)
Рис Фактор раскладки для определения продолжительности нагрева при различных методах загрузки печи
Для расчета времени нагрева деталей термисты обычно пользуются технологическими картами.
В технологическую карту входит перечень всех операций обработки детали или группы деталей с указанием подробных данных по этим операциям (температура, время выдержки, среда и температура охлаждения и применяемые приспособления).
.
Время нагрева деталей под закалку в различных средах
Нагревательные устройства | Температура нагрева,°С | Время нагрева (сек.) 1 мм диаметра или толщины деталей с сечением | ||
круглым | квадратным | прямоугольным | ||
Электрическая печь Пламенная печь Соляная ванна | 800 800 1300 800 1300 | 40-50 35-40 15-17 12-15 7-8 | 50-60 45-50 17-19 15-18 8-10 | 60-75 55-60 19-22 18-22 10-12 |
Для проведения любого теплового процесса термической обработки нужно не только нагревать металл до заданной температуры, но и выдерживать при этой температуре до полных структурных превращений (растворения карбидов, гомогенизации аустенита) и полного прогрева деталей. Таким образом, общее время пребывания деталей в нагревательной среде состоит из времени нагрева и времени выдержки. Время выдержки углеродистых сталей обычно составляет одну пятую от времени нагрева.
|
|
Нагрев под закалку обычно осуществляют в электрических печах. Часто так же применяют нагрев в ваннах с солевым расплавом. В этом случае нагрев происходит гораздо быстрее и поверхность детали не окисляется. В крупносерийном производстве часто используют нагрев деталей ( валов, зубчатых колес) токами высокой частоты (ТВЧ). При этом нагрев осуществляется за несколько секунд, и все операции нагрева и последующего охлаждения могут быть автоматизированы.
3. Скорость охлаждения при закалке и способы закалки.
Наиболее ответственной операцией при закалке является охлаждение, которое должно осуществляться со скоростью выше критической для получения структуры мартенсита.
|
|
Как было сказано выше, степень переохлаждения аустенита зависит от скорости охлаждения : чем выше эта скорость, тем больше переохлаждение аустенита, т.е. его превращение начнется при более низкой температуре. Поэтому наложение кривых охлаждения на диаграмму изотермического превращения аустенита позволяет предсказывать, какие структуры возникнут в стали при том или ином темпе ее охлаждения. Такое наложение представлено на Рис 1.1.11. Кривая V1 соответствует наиболее медленному охлаждению. При этом, как видно из рисунка, распад аустенита начинается при температуре около 700 град С (точка а1) и возникает пластинчатая структура с твердостью 150 НВ ( 1500 МПа). Кривая охлаждения V2 соответствует большей скорости, и распад аустенита ( точка а2) начинается при температуре около 650 град С, возникает структура ( сорбит) с меньшими по размеру пластинками и большей твердостью (200 НВ). V3 Аналогично, кривая охлаждения V3 приводит к структуре троостита (250НВ)
Рис 1.1.11. Наложение на диаграмму изотермического распада аустенита кривых охлаждения, схемы возникающих структур и примерная их твердость
При наиболее быстром охлаждении (V5) распада аустенита не происходит (С-кривая не пересекается), и при температуре около 200 град С (Мн) образуется мартенсит
На Рис1.1.11. обозначена так же критическая скорость охлаждения Vк, о которой говорилось ранее . Кривая охлаждения, соответствующая критической скорости, проходит касательно к кривой начала распада переохлажденного аустенита. Отсюда следует, что критическая скорость - это минимальная скорость охлаждения при закалке , при которой еще образуется структура чистого мартенсита. При скорости меньшей критической (V4) в структуре стали наряду с мартенситом появляются продукты диффузионного распада аустенита ( троостит, сорбит) .
Критическая скорость зависит от структуры стали ( например, укрупнение зерна приводит к понижению Vкр), но в наибольшей степени она зависит от химического состава стали: при легировании стали в большинстве случаев критическая скорость закалки существенно уменьшается . это обстоятельство позволяет производить охлаждение легированных сталей в масле, что дает возможность избежать появления больших закалочных напряжений. Для примера на рис.1.2.8 приведено схематическое сравнение кривых изотермического превращения аустенита ( С-_кривых) углеродистой (нелегированной) и легированной сталей. Из рисунка видно, что легирование приводит к сдвигу С-кривых вправо, что уменьшает критическую скорость закалки. Это важно для практики закалки, так как позволяет в легированных сталях получить мартенсит и высокую твердость при закалке в масло и уменьшить внутренние напряжения, возникающие при быстром охлаждении.
Рис 1.2.8. С – кривые углеродистой (а) и легированной (б) сталей: ΔТ1 и ΔТ2 – температуры переохлаждения аустенита к моменту начала перлитного превращения при нормализации
При больших скоростях охлаждения при закалке возникают большие внутренние напряжения, которые могут привести к короблению или растрескиванию деталей.
Причинами возникновения внутренних напряжений являются различие температур по сечению изделия при охлаждении и разновременное протекание фазовых превращений в разных участках изделия. О6разующиеся от этих причин напряжения соответственно называются термическими и фазовыми напряжениями.
Рис. .1.2.9. Схема деформации образца при термообработке:
а — начальная форма; б — деформация образца от фазовых напряжений; в — деформация образца от термических напряжений
Фазовые напряжения связаны с тем , что как уже говорилось, мартенсит обладает большим удельным объемом, чем аустенит и перлит.
Для уменьшения их напряжений применяют различные способы закалки представленные на рис 1.2.10. Во всех способах стремятся достичь высокой скорости охлаждения в диапазоне 650 – 300 град С ( она должна быть выше критической) и значительно снизить скорость охлаждения в диапазоне 300 – 200 градС, ( при образовании мартенсита)
Закалочные среды
Наиболее интенсивное охлаждение обеспечивает вода , так как при кипении воды поглощается большое количество тепла. Однако при интенсивном парообразовании вокруг закаливаемой детали может образоваться паровая «рубашка», что приведет к замедлению охлаждения. Поэтому в закалочных баках с помощью насосов организуется интенсивное движение закалочной среды для срыва этой рубашки.
Масло является более «мягким» охладителем, вызывающим меньшие напряжения при закалке. Различают масла по вязкости, температуре вспышки и другим параметрам.
Интенсивность охлаждения закалочной среды количественно оценивается параметром Н. Условно принято, что для спокойной воды Н = 1
Таблица 2.2.1
Интенсивности Н закалки в различных средах
Движение | Интенсивность Н закалки для сред : | |||
воздух | масло | вода | соленая вода | |
Отсутствует | 0,02 | 0,25 | 1,0 | 2,0 |
Среднее | 0,05 | 0,4 | 1,3 | 2,5 |
Сильное | 0,08 | 0,9 | 2,0 | 4,0 |
Наряду с водой и маслом в настоящее время широко применяются полимерные закалочные среды – это водные растворы некоторых полимеров. Такие среды отчасти компенсируют недостатки воды и масла.
В качестве охлаждающих сред в ряде случаев используются расплавы щелочей ( температуры 250 -300 град С) и солей ( температуры 500 – 600 град С)
Рис 1.2.10 Кривые охлаждения для различных способов закалки, нанесенные на диаграмму изотермического распада аустенита: 1- непрерывная закалка в одном охладителе; 2 — прерывистая закалка в двух средах; 3—ступенчатая закалка; 4 — изотермическая закалка
Закалка в одном охладителе - наиболее простой и распространенный способ. Деталь, нагретую до температуры закалки, погружают в закалочную жидкость, где она находится до полного охлаждения. Этот способ используют при закалке несложных деталей, изготовленных из углеродистых и легированных сталей. Детали из углеродистых сталей охлаждаются в воде; а детали из легированных сталей - в масле. Можно использовать такой способ и при механизированной закалке, когда детали автоматически поступают из агрегата в закалочную жидкость.
Для высокоуглеродистых сталей такой способ закалки неприемлем, так как в процессе закалки создаются большие внутренние напряжения. Высокоуглеродистые стали закаливают с подстуживанием, т. е. нагретую деталь перед охлаждением некоторое время выдерживают на воздухе. Это уменьшает внутренние напряжения в деталях и гарантирует их от образования трещин.
- закалка в двух средах (прерывистая закалка) (2). Этот метод заключается в предварительном охлаждении детали в более резком охладителе (например, в воде) до температуры около 300 градС. и последующим охлаждением в более мягкой среде (например, в масле).Прерывистая закалка в двух средах обеспечивает приближение к оптимальному режиму охлаждения 1. Недостатком прерывистой закалки является трудность установления момента переноса изделия из одной среды в другую для различных изделий, имеющих, как правило, различную толщину по сечению.
-.ступенчатая закалка (3). При этом способе деталь после нагрева переносят в среду с температурой несколько выше температуры точки Мн выдерживают в ней для выравнивания температуры по всему сечению и дальнейшее охлаждение осуществляют на воздухе.
- изотермическая закалка (5). Отличием этого вида закалки от ступенчатой является длительность выдержки выше температуры точки Мн в нижней части области промежуточного превращения. Время выдержки должно быть достаточно для превращения аустенита в бейнит. Такая структура обеспечивает высокую прочность, пластичность и вязкость стали, т. е. высокую конструктивную прочность. Вместе с этим значительно снижается деформация изделий вследствие ликвидации термических напряжений. фазовые (структурные) напряжения также уменьшаются в связи с тем, что превращение аустенита в бейнит происходит постепенно в течение длительного времени. Поэтому для легированных сталей изотермическая закалка находит довольно широкое применение.
Для охлаждения при изотермической закалке обычно используются расплавленные соли и щелочи разного состава. Охлаждение в расплавах щелочей (если нагрев под закалку производить в хлористых солях) позволяет получить чистую поверхность после термообработки. Такой способ закалки называется светлой закалкой.
2.2.3 Обработка стали холодом.
Высокоуглеродистые ( как и многие легированные) стали имеют температуру точки Мк ниже О °С ( см. рис 1.1.12). Поэтому после закалки в структуре стали наряду с мартенситом наблюдается в большом количестве остаточный аустенит, который снижает твердость и ряд других свойств стали. Для устранения остаточного аустенита проводят дополнительное охлаждение детали в области отрицательных температур до температуры несколько ниже температуры точки Мк стали. Обычно для этого используется сухой лед.
Такая обработка называется обработкой стали холодом. Обработку холодом необходимо проводить сразу после закалки, иначе аустенит стабилизируется и эффект обработки будет незначителен. Увеличение твердости после обработки холодом обычно составляет 1...4 НRС. После обработки холодом дают низкий отпуск.
Дата добавления: 2022-06-11; просмотров: 109; Мы поможем в написании вашей работы! |
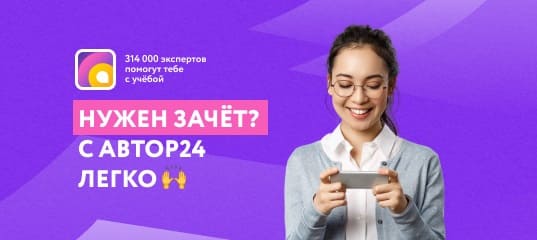
Мы поможем в написании ваших работ!