Измельчение зерна в вальцовых станках
ЛЕКЦИЯ №12
Измельчение
1. Классификация способов измельчения
2. Теория измельчения (дробления) твердых тел
3. Измельчение зерна в вальцовых станках
4. Измельчение зерна в машинах ударно истирочного действия.
5. Технологическая эффективность процесса измельчения.
6. Расчет машин для измельчения сырья.
1.Классификация способов измельчения
Измельчение –процесс разделения твердых тел под действием механических сил.
Если уменьшить размеры кусков без придания определенных форм,то процесс измельчения называется дроблением;
Если же одновременно с уменьшением размеров кусков ни придается определенная форма, процесс измельчения называется резанием.
По характеру применяемых усилий, способы измельчения могут быть классифицированы как измельчение при помощи удара, сжатия (раздавливания),раскалывания, истирания, разрыва ,изгиба, сдвига.
Выбор того или иного типа (принципа) воздействия определяется размерами и механическими свойствами измельчаемых материалов, а также конечными задачами процесса.
Различают измельчение крупное, среднее, мелкое и тонкое, а также коллоидный размол табл.1.
Табл.1 Зависимость размеров кусков измельчаемого материала от типа дробления.
Тип измельчения | Размер кусков материалов, мм | |
Поступающих на измельчение | После измельчения | |
Крупное | 1000-200 | 250-40 |
Среднее | 250-25 | 40-10 |
Мелкое | 50-25 | 10-1 |
Тонкое | 25-3 | 1-0,4 |
Коллоидный размол | 0,2-0,1 | 0,001 |
Такое разделение, хотя и условное лежит в основе классифицировании измельчающих машин на следующие основные группы: Щековые, или челюстные ,измельчители, раздавливают куски материала между неподвижной щекой 1 и подвижной 3,катающиеся на оси 2,(для известкового камня, строительных материалов).
|
|
![]() | Конусные измельчители (дробилки) работают по принципу раздавливание материала между двумя конусами. Наружный конус 1 неподвижен, внутренний 2 вращается. |
![]() | Вальцовые измельчители (дробилки) работают при непрерывном нажатии и стирании(для среднего, тонкого, и мелкого измельчения) |
![]() | Ударные (молотковые) измельчители (дробилки) работают по принципу удара и истирание(для не слишком твердых тел) |
![]() | Шаровые и стержневые мельницы работают при непрерывном нажатии и истирании, а если валок зубчатый, материал дробится путем раскалывания (для мелкого и тонкого помола) |
|
|
![]() | Вибрационные измельчители- производят измельчение вследствие круговых колебаний корпуса мельницы. При этом шары, находящиеся в мельнице, многократно взаимодействуют с материалом и измельчают его(для тонкого и сверх тонкого измельчения) |
Мельницы с вращающимися частями
![]() | ![]() | ![]() |
Одной из важных проблем измельчения является получение конечного продукта, возможно более однородного по гранулометрическому составу. Это обусловлено необходимостью стабилизации показателя качества продукции ,а также требованиям снижения удельной энергоемкости ее получения.
2.Теория измельчения(дробления)твердых тел.
Существуют две основные гипотезы дробления и разрушения твердых тел:
Объемная –предложенная В.Л.Кирпичевым
Поверхностная- выдвинутая Риттингером.
Согласно объемной теории, работа разрушения прямо пропорциональна объему дробимого тела т.е А=V*Hм
где V объем деформируемого тела см³, Нм постоянная величина для данного тела т.е свойства тела.
Сдругой стороны, из теории упругости известно, что абсолютная величина работы деформации (кг*см): А=δ²· V /2 E где δ - напряжение, ктс/см2;Е - модуль упругости при линейной деформации, кгс/см2. Таким образом, объемная теория учитывает упругие и пластические деформации, происходящие в теле при его разрушении. Согласно поверхностной теории, работа разрушения прямо пропорциональна величине образовавшейся при деформации поверхности, так как она затрачивается на разрыв связей между частицами материала, т.е.А= H s ·∆ S Нs - некоторая постоянная, характерная для данного тела и пропорциональная свободной поверхностной энергии; ·∆ S -приращение поверхности.
|
|
П.А. Ребиндер предложил объединить эти две гепотизы в один общий закон. В общем виде он может быть выражен так: А= V *Нм+ ∆ S * Hs
Из уравнения видно, что работа измельчения складывается из двух частей. Первая из них, - это работа, расходуемая на упругую и пластическую деформацию тела. В момент разрушения часть этой работы превращается в тепло. Величина этой части работы зависит от разрушающего напряжения и модуля упругости. Вторая часть - это работа, расходуемая на образование! новых поверхностей.
|
|
Применительно к дроблению зерна необходимо отметить следующее: при грубом и среднем дроблении величина \/*Нм намного превышает второе слагаемое ( ∆ S *Н s ), которое можно не учитывать. Следовательно, работа будет расходоваться на дробление (деформацию) тела При тонком измельчении работа дробления\/*Нм (деформации) незначительна. Более развернуто обобщенный закон измельчения для «идеальных» твердых тел описывают так:
A = K + n * +Kz*∆S*a
где К - энергия, расходуемая на процессы деформации и образование продуктов;
п - число циклов деформации частиц измельчаемого продукта;
а - разрушающее напряжение измельчаемого продукта;
V - объем разрушаемого продукта;
Е. - модуль упругости измельчаемого продукта;
Кz - энергия, расходуемая на образование 1 см2 новой поверхности для данного продукта;
∆s - вновь образованная поверхность; а - безразмерный множитель, характеризующий для машины данной конструкции процесс образования новой поверхности и тип измельчения (крупное, среднее, мелкое, тонкое, коллоидное).
Анализ обобщенного закона измельчения показывает, что для уменьшения затрат энергии на процессы деформации и образование продуктов следует:
-уменьшать величину К, т.е. уменьшать упругие деформации;
-уменьшать число п циклов деформации частиц разрушаемого продукта; -снижать разрушающие напряжения а измельчаемого продукта, что в определенной степени достигается процессами подготовки зерна к помолу (например, кондиционированием);
- размалывать продукт до крупности, диктуемой технологией производства, так как слишком бопьшое измельчение ведет к увеличению вновь образованной поверхности и безразмерного множителя, следовательно, к дополнительным затратам энергии.
Помимо влажности ( рис.6) на процесс дробления оказывают влияние физико - механические свойства зерна, в т.ч. стекловидность и температура (рис.7)
( рис.6)
Принципиальные кривые разрушения зерна различной влажности при сжатии:W1<W2<W3
Рис.7 Изменение расхода энергии на единицу вновь образованной поверхности в зависимости от температуры зерна.
Измельчение зерна в вальцовых станках
В вальцовых станках -рабочими органами вальцового станка являются два горизонтально расположенных цилиндрических вальца (сплошные или пустотелые) с рифленой или шероховатой поверхностью и вращающихся с разными окружными скоростями навстречу друг другу.
Что бы продукт попал между вальцами в их зазор между диаметром валков(вальцов) и размером частиц продукта должно быть определенное соотношение.
Рассмотрим случай, когда вальцы имеют гладкую поверхность и одинаковую частоту вращения рис.8
На валах со стороны частицы «А»действующая сила «Р»обусловленная его массой;
Со стороны вальца действует такая же сила «Р».
Вертикальная слагаемая этой силы Рsinα вытаскивая кусок сверху, так же сила действует со стороны вальца.
Следовательно ,вытаскивающее силы будут равны 2*Рsinα
Рис 8.Схема работы вальцовой дробилки. Сила трения 2fP,а ee вертикальная проекция 2fPcosα где,f коэффициент трения. Эта сила (2fPcosα) направляет вниз и увлекает частицы в щель между вальцами.
Чтобы частицы были затянуты вниз вальцами, должно быть соблюдено условие 2Р*sinα<2fPcosα или tgα <f,на рис.8 видно, что величина α зависит от диаметра вальца Д, размера d частицы A и ширины шнеков «в». С достаточной для протекающих целей точностью можно принять, что Dmin= где у угол трения измельчаемого продукта (12-21º)для чyгуна f коэффициент трения(0,231-0,284).Для размола зерна кроме гладких вальцов, применяются шероховатые и рифленые вальцы.
4. Измельчение зерна и других продуктов в машинах ударно - истирочного действия.
На мукомольных заводах для интенсификации процесса измельчения при хлебопекарных помолах зерна, в качестве дополнительных измельчающих машин после вальцевых станков, широко используют машины ударно-истирающего (деташеры, вымольные машины).
Рабочим органом деташера является горизонтально расположенный бичевой протер, вращающийся внутри цилиндрического корпуса. Измельчение продуктов происходит в результате многократных ударов, трение частиц о бичи и обичайку.
Рабочим органом вымольной машины служат вращающиеся бичевые роторы и горизонтальный ситовой полуцилиндр. В этих машинах ударное воздействие сочетается с просеиванием частиц.
Кроме этих машин на мукомольных заводах применяют молотковые дробилки для измельчения отходов, а на комбикормовых заводах для измельчения компонентов комбикорма.
V. Технологическая эффективность процесса измельчения.
Критерием эффективности измельчения любых твердых тел, в том числе и зерна является степень измельчения (i) удельная энергоемкость процесса.
Степень измельчения (i) характеризует изменения соотношения вновь образованной площади (Sк) в результате изменения первоначальной площади (Sп) измельчаемого материала i = S к/ Sn
В мукомольной промышленности степень измельчения (i) составляет 20:50.
В комбикормовой промышленности 300:500.
Число частиц в отдельных фракциях может быть по формуле: n 1= G 1/( d ³* p )
Где G1 массовый выход,d-средний размер частиц, р- плотность продукта
В качестве критерия оценки степени измельчения компонентов комбикормов применяют показатель, называемый модулем крупности размола, который определяют по выражению: М= 0,5 *Ро+1.5Р1+2.5Р2+3,5*Р3
100
где Ро- масса прохода через сито с отверстиями Ø 1мм выраженная в % к массе всего образца.Р1 масса остатка на сите с отверстиями Ø 1мм выраженная в % к массе всего образца.Р2 масса остатка на сите с отверстиями Ø 2мм выраженная в % к массе всего образца.Р3 масса остатка на сите с отверстиями Ø 3мм выраженная в % к массе всего образца.
Общую массу образца определяют, как сумму Р0+Р1+Р2+Р3.
В качестве показателя удельной энергоемкости можно использовать величину работы (кг*м),затраченной на образование единицы новой поверхности[(кг*м)/м² ∆А=А(Sk-Sн),где А работа,затраченная на измельчение продута с начальной обшей поверхностью (Sн) и конечной поверхностью измельченных частиц(Sк).
6.Расчет машин для измельчения раздавливанием
Валковые машины
Производительность Q(кг/с)двухвалковой машины можно определить по формуле: Q=π DLвnpм=0.052DLbnpм
60
Где D Ø валка,м
L-рабочая длина валка,м
В- зазор между валками
n-частота вращения валков об/мин
р-насыпная плотность продукта,кг/м³
м-коэффициент заполнения продуктом зазора между валками(м=0,2+0,8)
Для двух валковой дробилки рекомендуемое соотношение l/d=2:3,для мельниц 2,5:4.
Минимальный Ø валка можно определить для горизонтального и вертикального вальцового станка: Dmin>60S1k -1
K
S1-первоначальный размер измельчаемого материала,мм
К-степень измельчения
Частота вращения валков,мин¯¹: n =616 1 или n =275,5
р S1D р S1D
Мощность измельчения на вальцах
N=Мпр*2*π*n
Где Мпр(Н*М) т(с¯¹)
Приведенный момент Мпр РDEα
Где р(мпа);D(м)
Среднее давление в зоне измельчения
Р= ld∫ р xdh ; Рх= Pm ах( nл)
Dk-δ nx
ЛЕКЦИЯ 13
Шелушение.
1.Общие сведения
2.Методы шелушения зерна
3.Оценка технологической эффективности процесса шелушение зерна.
4.Расчет машины для снятия оболочек семян.
Общие сведения.
Шелушение зерна, т.е. отделение наружных оболочек (цветковых у проса, овса, ячменя, риса, плодовых у гречихи, плодовых и частично семенных у пшеницы и кукурузы, семенных у гороха), является одной из основных операций в технологии крупяных продуктов. Чтобы получить наибольшую эффективность шелушения, необходимо вполне определенное воздействие рабочих органов машины на зерно, вызывающее в оболочках такую деформацию, при которой они отделяются от ядра при минимальном повреждении последнего и с наименьшей затратой энергии.
В комбикормовом производстве зерно пленчатых культур шелушат в случае выработки некоторых комбикормов, в состав которых входит шелушенное зерно (например, для цыплят, поросят - отъемышей и т.д.).
Методы шелушения зерна.
Для шелушения зерна применяют много типов шелушильных машин, принципы действия большинства из которых можно свести к трем основным способам воздействия рабочих органов на зерно: сжатием и сдвигом; многократным и однократным ударом; трением об абразивную и другие твердые поверхности.
Классификация методов шелушения крупяных культур и виды применяемого оборудования в зависимости от связи пленок с ядром и его прочности приведены в табл.1.
Шелушение зерна сжатием и сдвигом заключается в воздействии на зерно двух рабочих поверхностей, расстояние между которыми меньше размера зерна. Обязательным условием является движение одной поверхности относительно другой. Это возможно в случае, когда одна поверхность подвижна, а другая нет, или когда движутся обе поверхности, но с разной скоростью.
Шелушение многократным и однократным ударом заключается в том, что зерно, под хваченное бичами или лопастями крыльчатки, направляется многократно или однократно к от ражательной поверхности.
Шелушение зерна трением об абразивную и другие твердые поверхности. Наиболее целесообразно для зерна, оболочки которого прочно срослись с ядром. Под воздействием длительного движения абразивной поверхности о зерно постепенно соскабливается пленка с зерновки. По такому принципу работает шелушильно-шлифовальная машина А 1-ЗШН-3(шлифуют -ячмень,горох,пшеницу,кукурузу)
Таблица 1 Классификация методов шелушения.
3.Оценка технологической эффективности процесса шелушения зерна
Процесс шелушения должен обеспечить возможно более полное отделение оболочек у зерен, поступивших в шелушильные машины. Однако полного отделения пленок у всех зерен ни одна шелушильная машина практически не обеспечивает. Кроме того, при шелушении большинства крупяных культур желательно сохранить целыми как можно больше ядер. Поэтому эффективность шелушения зерна можно оценивать как количественным, так и качественным показателями.
Количественно эффективность шелушения может быть оценена так называемым коэффициентом шелушения (%)
Еш = Н1-Н2 *100
Н1
где Н1, - содержание нешелушенных зерен в продукте, поступившем в машину, %;
Н2 - содержание нешелушенных зерен в продукте, выходящем из машины, %.
Качественную характеристику процесса шелушения может дать так называемый коэффициент цельности ядра
К 2 - К 1 __к _
E ц я= (К 2 - К 1+(d2-d 1) +m 2 -m 1) =К+ d + m
где К1, d2, m2т, - соответственно количество целого ядра, дробленого и мучки в продукте, поступившем на шелушение, %;
К2, d2, m2 - соответственно количество целого ядра, дробленого и мучки в продукте, выходящем из машины; %;
К, d, m- соответственно прирост количества целого ядра, дробленого и мучки в процессе шелушения, %.
Увеличение выхода дробленого ядра и мучки снижает коэффициент цельности ядра.
Комплексная оценка эффективности шелушения может быть представлена произведением коэффициента шелушения и коэффициента цельности ядра E ш+ E уя
4. Расчет бичевой сименнорушки.
При обрушивании семян подсолнечника в бичевой семеннорушкеудельная работа разрушения семенной оболочки Дж/кг по формуле:
Ас=185,4+20 w
Где w влажность семян %
Скорость (м/с)при которой семенадолжны ударятся о неподвижную деку:
V=1,41 Ас
Частота вращения бичевого барабана семенорушки:
N=27 Ас =19.1v,
D
где D- бичевого барабана,м
Зависимость между конструктивными размерами бичевой семенорушки(ограничение которое учитывают)
Z ≥2 ,22 D 2 g Н ,
B cosα Ас
где Z число бичей на барабане, α угол наклона бича к радиусу,Н-высота с которой падают семена на бич,g- ускорение свободного падения.
Производительность семенорушки, кг/с
Q=lg ,
где l- длина бича,м,п. Удельная нагрузка на 1 м длины бича,для семенорушки (0,6-0,7 кг/мс)
Мощность необходимая для разрушения ячменной оболочки.
N1=QAc ,
1000
Мощность необходимая на преодоление сопротивление воздуха
N ²= VH ,
1000 η
где V=Уπ Dlan =0,021 Dl А n
У- коэфициент неупорядочности = 0,4
Н=π²Ψр D ² n ²=1,78¯³* D ² n ²,
3600
где Ψ- коэффициет напора 0,5
N=27 Ас
D
η- 0,4- аэродинамический КПД,тогда N2=3,07*10¯³QaAc
где А- ширина выходной точки бичевой семенорушки,м(0,08)
Мощность необходимая для преодоления трения семян о деку.
N3=0,2*10¯³*QAc*в*fo,
где: в- угол обхвата барабана декой(1,9)
fo- коэффициент внутреннего трения рушанки (0,9)
Дата добавления: 2022-06-11; просмотров: 29; Мы поможем в написании вашей работы! |
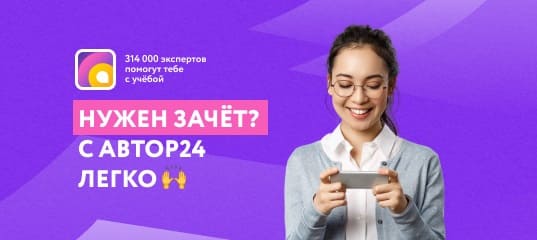
Мы поможем в написании ваших работ!