Энергетический баланс предприятия
Расходная часть | Приходная часть |
Потребность во всех видах энергии и топлива основного ивспомогательного производства | Производственные ресурсы собственных генерирующих установок по получению топлива различных видов и марок |
Потребность в энергии и топливе на отопление, вентиляцию, освещение, хозяйственно-бытовые и непроизводственные нужды | Регламентация режимов работы собственных генерирующих установок и распределения нагрузки между агрегатами |
Нормальные (допускаемые) величины потерь энергии в сетяхпромышленного предприятия | Величина покрытия потребности в энергии за счет собственного производства, использование вторичных энергоресурсов и ресурсов со стороны |
Объектами второго направления являются материальные ресурсы, которыми обеспечивается обслуживание и ремонт оборудования, используемого в производственных подразделениях энергетического хозяйства промышленного предприятия. В свою очередь, оборудование входит составной частью в производственные единицы подразделений энергетического хозяйства. Как правило, производственные единицы подразделения энергетического хозяйства состоят из следующих производственных единиц:
• электросиловое подразделение — понизительные подстанции, мотор-генераторные установки зарядных станций, электродвигатели высокого напряжения (для генераторов высокой частоты), трансформаторные установки (трансформаторы дуговых печей);
|
|
• теплосиловое подразделение — заводские котельные, тепловая сеть завода, компрессорные установки и воздушная сеть завода, система водоснабжения, мазутоперекачивающие установки;
• газовое подразделение — газовые вводы или заводская газогенераторная станция, кислородная станция, газовые сети;
• электромеханическое подразделение — дефектовочная группа, обмоточная мастерская с сушильно-пропиточным отделением, слесарно-механическое и сборочное отделение;
• слаботочное подразделение — автоматическая телефонная станция, коммутаторные установки, передающие и приемные установки, зарядные станции, аккумуляторное хозяйство электрокарного парка.
Организация обслуживания и ремонта оборудования энергетического хозяйства, создание нормативной базы и последующий расчет потребности в материальных ресурсах (материалах, полуфабрикатах, готовых и комплектующих изделиях), необходимых для обслуживания и ремонта, основываются на принципах и методах организации, нормирования и планирования, используемых в ремонтном хозяйстве с учетом специфических особенностей оборудования энергетического хозяйства. В частности, система планово-предупредительного ремонта и обслуживания оборудования, применяемого в энергетическом хозяйстве, базируется на оптимальном соотношении между надежностью работы оборудования и расходами на его обслуживание и ремонт.
|
|
Инструментальное хозяйство предприятия призвано обеспечивать бесперебойное снабжение производственных подразделений и рабочих мест промышленного предприятия высококачественной технологической оснасткой в необходимом количестве и ассортименте при минимальных затратах на ее приобретение или изготовление, хранение и эксплуатацию.
Промышленные предприятия используют широкую номенклатуру технологической оснастки — режущий, мерительный и вспомогательный инструмент; различные штампы и модели; станочные и слесарные приспособления; пресс-формы различных конфигураций. При этом затраты на технологическую оснастку, например, в себе стоимости машиностроительной продукции достигают 8—15%.
Планирование потребности в технологической оснастке включает в себя определение ее расхода при выполнении производственной программы и объемов запасов, необходимых для обеспечения нормального снабжения производственных подразделений предприятия и рабочих мест. В свою очередь, планирование потребности в технологической оснастке основано на определении номенклатуры оснастки — составлении каталога технологической оснастки.
|
|
Основой для расчета потребности в каждом виде оснастки являются производственная программа, нормы расхода и нормы ее запасов. Нормирование расхода технологической оснастки осуществляется различными методами в зависимости от особенностей эксплуатации данного вида инструмента и типа производства. В массовом и серийном производстве используются подетальные нормы расхода, в условиях единичного и мелкосерийного производства — укрупненные нормы.
Расчет норм расхода, например, режущего инструмента в условиях массового и серийного производства производится по каждому типоразмеру — норма устанавливается на определенное количество деталей — операций, узлов и изделий в зависимости от величины производственной программы по данному изделию:
Н= (1000 · tн ) / (tм · 60 · (1 − ау /100)) (38)
где Н — норма расхода режущего инструмента на 1000 деталей, шт.;
tн — время работы данного инструмента при обработке деталей, мин;
|
|
tм— машинное время работы данного инструмента до полного его износа, ч;
ау — процент случайной убыли.
В свою очередь, время работы инструмента до полного его износа определяется следующей формуле:
tм = (1 + И сд. / И сп..) tст. (39)
где И сд. — допустимая величина стачивания режущих граней инструмента, мм;
И сп— величина стачивания лимитирующей режущей грани за одну переточку, мм; tст. — оптимальная стойкость инструмента между переточками, мин.
В условиях единичного и мелкосерийного производства нормы расхода рассчитываются укрупненным методом, например методом средней оснащенности станка. Этот метод предусматривает предварительную группировку оборудования, позволяющую значительно упростить технику расчетов, снизить их трудоемкость и сохранить требуемую точность. Расчет в этом случае производится для группы однотипных инструментов по следующей формуле:
И но. = (1000 · Км. ш · КП) / (tм · (1 − а /100)) (40)
где И но. — норма расхода данной группы режущего инструмента на 1000 часов работы оборудования, шт.;
Км. ш — коэффициент, характеризующий отношение машинного времени к штучному для данной группы оборудования;
КП — коэффициент, характеризующий удельную применяемость данного инструмента.
Норма расхода измерительного инструмента универсального типа определяется экспериментальным путем исходя из среднего срока его службы в регламентируемых эксплуатационных условиях. Аналогично нормируется расход вспомогательного инструмента и различных приспособлений, в том числе слесарно-монтажного инструмента. Годовой расход инструмента определяется на основе соотношения между годовым объемом работ (количество изделий, деталей, часов эксплуатации оборудования) и соответствующей нормой расхода инструмента.
Потребность предприятия в технологической оснастке удовлетворяется по двум направлениям — ее приобретение по кооперации, изготовление на собственных производственных мощностях. Естественно, что стандартная типовая технологическая оснастка производится на специализированных инструментальных предприятиях и поставляется промышленным предприятиям. Одновременно часть оснастки изготавливается в инструментальных цехах предприятия и предназначена для собственных нужд.
Инструментальные цехи, например, машиностроительных предприятий классифицируются по типу производства, характеру выпускаемой продукции, уровню специализации и масштабу производства:
• инструментальные цехи универсального типа, изготовляющие нормализованный инструмент методом серийного производства и специальную оснастку — мелкими сериями (крупные машиностроительные предприятия);
• универсальные цехи мелкосерийного производства (в составе мелких и средних машиностроительных предприятий);
• инструментальные цехи, специализированные на производстве определенной группы технологической оснастки (штампы для горячей и холодной штамповки), которые обычно организуются на крупных промышленных предприятиях наряду с универсальными инструментальными цехами.
Основные производственные участки инструментальных цехов промышленных предприятий специализируются как по признаку однородности технологических операций (механический, слесарный, сварочный, термический участки), что характерно для незначительных масштабов производства, так и по предметному признаку (участок резцов, приспособлений, штампов). Производственная программа инструментального цеха строится на основе расчета производственной мощности отдельных производственных участков.
Изготовление технологической оснастки требует определенных объемов (в том числе и запасов) разнообразной номенклатуры материальных ресурсов, потребность в которых рассчитывается на основе норм расхода основных и вспомогательных материалов, полуфабрикатов, готовых и комплектующих изделий, плана производства оснастки и заказов на ее изготовление. Данная потребность входит составной частью в общую потребность предприятия (включая основное производство) в материальных ресурсах.
Одновременно часть отработанной технологической оснастки подлежит восстановлению и ремонту. Что касается восстановления оснастки, то на практике используется несколько его разновидностей: восстановление оснастки по первоначальному ее назначению; изменение геометрических параметров на другие, меньшие размеры; использование деталей и узлов отработанной оснастки в качестве полуфабрикатов при изготовлении новой оснастки.
Ремонт сложных видов технологической оснастки организуется аналогично ремонту основного оборудования. Штампы, приспособления, пресс-формы и другие виды сложной оснастки классифицируются по группам сложности ремонта (по аналогии с группами сложности ремонта оборудования), и для них разрабатываются соответствующие нормативы планово-предупредительного ремонта. При этом организация ремонта технологической оснастки предполагает наличие соответствующей номенклатуры и объемов запасных частей, заготовок, деталей и узлов.
Ремонт технологической оснастки организуется или по типовой технологии (наиболее экономичный метод), или по индивидуальной. Одновременно ремонт может осуществляться как децентрализованно в производственных подразделениях предприятия, имеющих ремонтную базу, так и централизованно — в инструментальных цехах. Целесообразность того или иного способа проведения ремонта технологической оснастки в каждом отдельном случае должна быть обоснована экономическими расчетами.
Организация эксплуатации технологической оснастки включает в себя: организацию получения, хранения, выдачи и учета движения оснастки; организацию заточки и ремонта инструмента; организацию контроля и надзора за состоянием технологической оснастки и соблюдение правил ее эксплуатации (использование оснастки строго по назначению, соблюдение режимов обработки, использование исправной оснастки).
Технический контроль представляет собой проверку соблюдения технических требований, предъявляемых к качеству продукции на всех стадиях ее изготовления. Объектами технического контроля на промышленных предприятиях являются материальные ресурсы, поступающие на предприятие от поставщиков, продукция предприятия как в готовом виде, так и на всех стадиях ее производства, технологически процессы, орудия труда, технологическая дисциплина и общая культура производства. В зависимости от конкретных задач, стоящих перед техническим контролем, используются различные виды и методы контроля (рис. 11).
![]() | |||
![]() |
Рис. 11. Виды и методы технического контроля
Сущность отдельных видов контроля заключается в следующем: приемочный контроль осуществляется при поступлении материальных ресурсов от поставщиков и в производстве продукции с целью выявления и изоляции брака; профилактически контроль имеет целью предупреждение появления брака в процессе производства продукции; комплексный контроль решает одновременно задачи приемки ипрофилактики; специальный контроль преследует решение специфических производственных задач — оценку уровня качества продукции в производственных подразделениях предприятия, оценку качества продукции в эксплуатации.
В свою очередь, используемые методы технического контроля ставят перед собой следующие задачи: контроль наладки имеет целью проверку соблюдения установлениях требований к качеству продукции в начале выполнения той или иной операции; летучий контроль состоит в периодических и эпизодических проверках качества продукции непосредственно на рабочих местах; статистический контроль представляет собой особую группу методов, базирующихся на экономическом обосновании режимов технологических процессов и четкой их регламентации; выборочная проверка предусматривает контроль части продукции — представителя из совокупности или партии промежуточной или готовой продукции; сплошная проверка предусматривает полный контроль продукции.
В зависимости от особенностей контролируемых параметров различают: контроль геометрических форм и размеров; контроль внешнего вида продукции и документации (состояние упаковки и консервации, наличие и правильность маркировки, правильность оформления технической документации); контроль физико-механических, химических и других свойств материалов и полуфабрикатов; контроль внутреннего состояния продукции (раковины, внутренние трещины); контроль технологических свойств, определяющих пригодность материалов и полуфабрикатов для дальнейшей обработки (штампуемость, свариваемость); контрольно-сдаточные испытания в соответствующих условиях (при режимах нормальной эксплуатации, повышенных режимах); контроль за соблюдением технологической дисциплины.
Каждая из указанных выше разновидностей технического контроля отличается характером применяемых средств, методов и режимов контроля. В свою очередь, контрольные операции различаются в зависимости от стадий производственного процесса, на которых осуществляется технический контроль, в зависимости от степени охвата контролем технологических операций, а также в зависимости от места выполнения контрольных операций. Укрупненная классификация разновидностей контрольных операций представлена в табл. 11.
Таблица 11
Дата добавления: 2022-01-22; просмотров: 18; Мы поможем в написании вашей работы! |
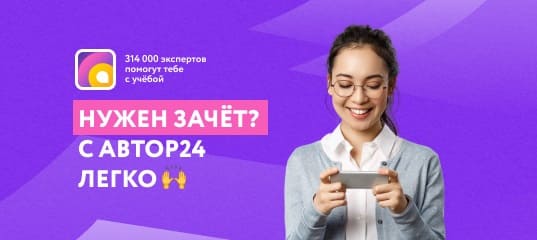
Мы поможем в написании ваших работ!