СЕПАРАТОРИ з постійними магнітами
З ерноочисні та сортувальні МАШИНИ
Зерно що поступає на підприємство зазвичай містить різні домішки , які при зберіганні можуть викликати швидке його псування і знизити якість готового продукту. Тому на підприємствах зерно очищають від найбільш грубих домішок просіюванням і провітрюванням. Таке очищення називається первинною, і для її здійснення звичайно застосовують повітряно- ситові сепаратори. Зерно після первинного очищення направляється в зерносховище , де і зберігається до моменту переробки.
Для отримання солоду зерно перед замочуванням подверга ється вторинної , більш ретельному очищенню . При цьому із зернової маси видаляються що залишилися в ній сторонні домішки , а також биті зерна інших злаків. Після вторинного очищення зерно поділяють на сорти , що необхідно для рівномірного замочування і рощення його.
Зерно, призначене для використання в спиртовому виробництві, очищається тільки від грубих домішок , піску і пилу і не поділяється на сорти
Для вторинного очищення і сортування зерна застосовуються повітряно- ситовий сепаратор, магнітний сепаратор (вловлює металеві домішки ), трієри ( виділяють частинки , що відрізняються від основної маси зерна своєю довжиною ) і сортувальні сита.
Крім перерахованих машин в зерноочисному відділенні встановлено проміжні бункери для зберігання зерна і відходів , ваги для обліку кількості зерна, що переробляється і транспортери (стрічкові транспортери , шнеки , норії , самопливні труби і т. п.) , які з'єднують окремі машини в потокову лінію. На рис. 1-1 зображена апаратурно - технологічна схема очищення і сортування зерна солодового заводу.
|
|
При прийманні на зберігання зерно норією 1 подається в бункер 2 , з якого через автоматичні ваги 3 надходить у сепаратор 4 . Попередньо очищене зерно з сепаратора проходить через автоматичні ваги 5 в бункер 6 , звідки норією 1 і транспортером 13 розподіляється по силосах 14.
Для повторної очищення і сортування зерно з силосів 14 транспортером 15 подається на норії 1, які піднімають його в бункер 2. З бункера 2 зерно проходить через сепаратор 7, магнітний сепаратор 8, трієр 9, сортувальні сита 10, ваги 11 і потрапляє в бункери сортованого зерна 12, звідки норією 1 і транспортером 13 завантажується знову в силоси .
Рис. 1-1. Апаратурно-технологічна схема очищення і сортування зерна солодового заводу
ПРИНЦИПИ очищення і сортування ЗЕРНА
У масі зерна знаходяться домішки двох видів: бур ` і зернові. До смітної домішки відносяться різні частинки мінерального (грудки землі , пісок , пил , каміння і т. п. ) і органічного ( колоск , солома , полова , дрібне і попсоване зерно , насіння бур'янів і т. п. ) походження.
|
|
До зернової домішки відносяться зерна основної культури, що мають ті чи інші недоліки: биті , пророслі , запліснявілі , пошкоджені при сушці і т. д. Засмічені та зернові домішки володіють більшою гігроскопічністю , ніж доброякісне зерно , сприяють самозігріванню зернової маси , розвитку мікроорганізмів і шкідників комор . Тому щоб уникнути швидкого псування зерно після приймання має негайно піддаватися очищенню.
У зерновій масі нерідко містяться різні металеві домішки ( гайки , болти , цвяхи , обривки дроту , частинки окалини) , які викликають передчасний знос робочих органів машин і можуть стати причиною серйозних поломок .
Очищення зерна від домішок і поділ його на сорти заснована на різних фізичних властивостях зерна і частинок домішок. Для поділу зернової маси на фракції найчастіше використовують такі ознаки зерна : 1 ) лінійні розміри ; 2 ) аеродинамічні властивості; 3 ) феромагнітні властивості; 4 ) щільність частинок. Іноді враховують також стан поверхні частинок і деякі інші ознаки .
Принцип дії зерноочисних машин заснований на відділенні домішок від основної маси зерна але лінійним розмірам і аеродинамічним властивостям . Сортувальні машини поділяють очищене зерно по товщині , а трієри - по довжині частинок. Металеві частки витягуються з маси зерна магнітними апаратами. Під час мийки зерна частинки з малою щільністю спливають на поверхню води і видаляються з апарату в особливий збірник .
|
|
У табл. 1.1 наведені середні значення фізичних властивостей найважливіших зернових культур і домішок .
Таблица 1.1
показники | зернові культури | домішки | ||||||
ячмінь | пшениця | жито | овес | кукурудза | просо | кукіль | вівсюг | |
Середній розмір часток, мм | ||||||||
довжина | 7,0-14,6 | 4,2-8,6 | 5,0-10,0 | 8,0-16,6 | 5,5-13,5 | 1,8-3,2 | 4 | 15 |
ширина | 2,0-5,0 | 1,6-4,0 | 1,4-3,6 | 1,4-4,0 | 5,0-11,5 | 1,2-3,0 | 3 | 2,6 |
товщина | 1,4-4,5 | 1,5-3,8 | 1,2-3,5 | 1,2-3,6 | 2,5-8,0 | 1,0-2,2 | 2,5 | 2,2 |
Насипна щільність, кг/м3 | 650 | 750 | 720 | 550 | 750 | 720 | — | — |
щільність, кг/м3 | 1300 | 1360 | 1300 | 1250 | 1350 | 1000 | 1200 | — |
Коефіцієнт внутрішнього тертя (чорно по зерну) | 0,51 | 0,47 | 0,49 | 0,51 | 0,53 | 0,54 | — | — |
Коефіцієнт зовнішнього тертя зерна | ||||||||
по зерну | 0,40 | 0,40 | 0,40 | 0,45 | 0,35 | 0,40 | — | — |
по сталі | 0,37 | 0,37 | 0,37 | 0,37 | 0,37 | 0,34 | — | — |
по бетону | 0,43 | 0,40 | 0,42 | 0,45 | 0,42 | 0,34 | — | — |
|
|
СІТА
Багато зерноочисні та сортувальні машини мають в якості робочого органу рухомі сита. При просіюванні крізь сита зернова маса очищається від домішок , які відрізняються від зерен основної культури за розмірами. Крім того , зерно на ситах може бути розділене на сорти . Форма і розмір отворів у цьому випадку і визначають призначення сита.
Сита з круглими отворами поділяють зернову масу по ширині частинок , сита з довгастими отворами - по товщині частинок ( рис. 1-2) . Сита з квадратними отворами не забезпечують чіткого поділу зернової маси , так як частинки при цьому можуть розташовуватися як по стороні квадрата , так і за його діагоналі. Тому сита з круглими і квадратними отворами використовуються для очищення зерна від великих н дрібних домішок , сита з довгастими отворами - для сортування зерна. Кожне сито поділяє зернову масу на дві частини. Частина , що проходить крізь отвори , називається проходом , частина , що залишається на ситі і зсипають з нього через край , називається з ходом.
У зерноочисних і сортують машинах зазвичай працюють одночасно кілька сит з отворами різної величини і форми з тим , щоб розділити зернову масу відразу на кілька фракцій. За формою розрізняють сита плоскі і циліндричні ( барабанні ) ; плоскі сита застосовуються для очищення зерна і сухого солоду від домішок ; барабанні сита - для сортування зерна перед подачею у виробництво та очищення сухого солоду від паростків .
За способом виготовлення розрізняють сита штамповані ( пробивні ) н ткані . Для виготовлення штампованих сит застосовується тонка оцинкована або відпалений і травлена (так звана декапировать ) листова сталь ; ткані сита виготовляють із сталевого або латунного дроту або ж з шовкових або капронових ниток.
Розміри отворів і частота їх розташування на ситі впливають на продуктивність сита. Чим більше отворів припадає на одиницю площі , тим вище ймовірність потрапляння в них частинок зерна і, отже , тим вища продуктивність сита. Відношення суми площ отворів до загальної площі сита називається живим перетином сита або коефіцієнтом використання площі сита. Чим більше живий перетин сита , тим вище його продуктивність; однак при занадто великій частоті розташування отворі механічна міцність сита знижується. Тому для збереження міцності сита розмір перемички між сусідніми отворами повинен бути не менше діаметра круглого отвори або не менше ширини довгастого отвору .
Круглі отвори в ситі розташовують в кутах рівносторонніх трикутників (рис. 1-3) . Для розмітки центрів отворів достатньо прокреслити паралельні лінії уздовж аркуша , потім перетнути їх лініями під кутом 60 °. Відстані між лініями залежно від прийнятого кроку а вказані на рис. 1-3.
При розташуванні отворів по кутах квадратів на ситі між рядами отворів виходять смужки цілого листа , по яких зерно ковзає , не потрапляючи в отвори.
Довгасті отвори пробивають в шаховому порядку , прямими або похилими рядами. Найбільш доцільне розміщення - шаховий порядок. Розміри довгастих отворів в сортуючих ситах для ячменю приймаються наступними (у мм) : довжина 15-20 , ширина 2,2-2,5 і 2,8 .
Рис. 1-2. Сита з круглими і продовгуватими отворами
Рис. 1-3. Розташування круглих отворів в штампованому ситі
Живе перетин тканих дротяних сит зазвичай значно більше живого перетину штампованих сит ; крім того , ткані сита більш міцні і зносостійкі . Однак штамповані сита набули більшого поширення завдяки тому , що в них можуть бути виконані отвори будь-якої форми .
Рух зерен по нерухомому ситу можливо тільки в тому випадку , якщо воно нахилене до горизонту під кутом α, великим кута тертя зерен про сито.
Щоб підвищити продуктивність плоских сит , їх встановлюють під малим кутом до горизонту (α = 6 - 14 °), а рух зерна здійснюється за допомогою коливання сит. Ситовий корпус підвішують за допомогою плоских сталевих пластин до станини машини і приводять його в коливальний рух допомогою шатунно - кривошипного механізму . Залежно від взаємного положення приводу і ситового корпусу розрізняють такі кінематичні схеми :
1 ) похиле сито з горизонтальними коливаннями ;
2 ) горизонтальне сито з коливаннями в похилій площині;
3 ) похиле сито з коливаннями в похилій площині.
Похилі сита з горизонтальними коливаннями застосовуються найбільш часто. Частка зерна , що лежить на похилому ситі , яке робить коливання в горизонтальній площині , знаходиться під дією сил тяжіння , інерції і тертя ( рис. 1-4).
Коли кривошип знаходиться в I або IV квадранті , прискорення сита має напрямок зліва направо . Дія сили інерції протилежно напрямку прискорення і в даному випадку прагне зрушити частку зерна вгору по похилій площині сита ( рис. 1-4 , α).
При положенні кривошипа в II або III квадранті прискорення сита направлено справа наліво , а сила інерції - зліва направо і прагне зрушити частку зерна вниз по похилій площині сита ( рис. 1-4 , б).
Рис. 1-4. Рух зерна по похилому ситу
Циліндричні сита встановлюються під невеликим кутом до горизонту і наводяться в обертальний рух . При повільному обертанні сита на частку зерна діє тільки сила тяжіння , при швидкому - виникає ще і відцентрова сила.
Частка зерна в обертовому циліндричному ситі (рис. 1-5) притискається до поверхні сита нормальної складової А сили тяжіння G і відцентровою силою С.
Під дією сили тертя Т частка зерна буде перемішатися разом з ситом до тих нір , поки сила В ( друга складова сили G) не стане рівною силі тертя Т.
Рис. 1-5. рух зерна
в циліндричному ситі
При нормальній роботі частота обертання циліндричного сита повинна бути значно менше граничної ; чим більше частота обертання сита , тим вище піднімається зерно і тим більше швидкість зворотного ковзання. При великій же швидкості ковзання зерно не встигає провалюватися через отвори в ситі .
Циліндричні сита встановлюють послідовно по ходу переміщення зерна. Для поділу ячменю на три сорти використовують сита з довгастими отворами шириною 2,2 і 2,5мм; при діленні ячменю на чотири сорти застосовують сита з отворами шириною 2,2 ; 2,5 і 2,8мм. Проходом крізь перші сито (ширина отворів 2,2мм) йдуть самі щуплі зерна; крізь другий сито - зерна середньої величини ( II сорт ); нарешті, найбільш великі і важкі зерна (I гатунок) йдуть сходом з цих сит.,
Чіткість розподілу зерна за сортами тим більше, чим триваліший зерно знаходиться в зіткненні з сортуючої поверхнею і чим інтенсивніше воно при цьому перемішується. Обидва ці фактори залежать від розмірів , кута нахилу і окружної швидкості барабанного сита. Граничний нахил циліндра становить 0,1м на 1м довжини; нормальна окружна швидкість сита 0,7-1,2м / с.
Навантаження на 1м2 сита в годину становить ( в кг ): при очищенні зерна від великих домішок 500-600 ; при очищенні зерна від дрібних домішок 200-300 ; при сортування зерна 150-200.
Машина з барабанним ситом для сортування ячменю на три сорти зображена на рис. 1-6. Сортируемое зерно безперервним струменем подається через приймальний отвір 2 всередину барабанного сита 1. Під барабаном знаходяться два шнека 5, призначені для відводу з машини кормового ячменю і ячменю II сорту. Кожен шнек частково перекритий клапанами 4 уникнення змішування розсортувати зерна. Велике зерно I сорту йде сходом в нижньому кінці барабанного сита. Від застрявшіхв отворах зерен сита очищаються щітками 3. У процесі інтенсивного перемішування зерна в машині виділяється багато пилу, для видалення якої необхідна аспірація з розрахунку 150-200м3 повітря на кожну тонну зерна.
Рис. 1-6. Циліндрична сортуюча машина
Технічна характеристика машини з барабанним ситом продуктивністю 2000кг / год при сортування ячменю наведена в літературі [ 1 , с. 17 ] .
Машина з барабанним ситом має великі габаритні розміри при відносно малій продуктивності; пояснюється це тим, що лише 1/4-1/6 загальної поверхні барабанного сита одночасно перебуває в роботі. Перевагами машини є хороше перемішування зерна , плавність роботи і простота приводу.
Повітряно-ситові сепаратори
Для очищення від легких домішок (пилу , полови , часток стебел , остюків і т. п. ) крізь потік зерна продувають струмінь повітря . Легкі частинки захоплюються струменем повітря і виносяться із зернової маси.
З'ясуємо , за яких умов легкі частинки будуть виділятися з потоку зерна. Всяка матеріальна частка , що знаходиться в повітряному струмені , що піднімається у вертикальній трубі , відчуває дію двох сил : сили тяжіння G і сили опору повітря R. Якщо G > R , то частка падає вниз назустріч струмені повітря ; якщо R> G , частка піднімається струменем повітря вгору ; при G = R частинка витає в повітрі. Швидкість повітря , при якій частка перебуває в подібному стані , називається швидкістю витання . Швидкість витання частинок різних злаків і домішок залежить від аеродинамічних властивостей цих частинок : їх форми , маси, стану поверхні і т. д. Швидкість витання легких домішок значно менше швидкості витання повновагих частинок зерна. Тому , продуваючи потік зерна струменем повітря зі швидкістю , меншою швидкості витання частинок зерна , можна очистити зерно від легких домішок.
Швидкість витання найважливіших хлібних злаків (пшениці , жита , ячменю ) залежно від натури зерна коливається від 8,5 до 11,5 м / с , для кукурудзи вона досягає 13 м / с. Коефіцієнт опору для цих же злаків дорівнює приблизно 0,20-0,22 .
Швидкість руху повітря в аспіраційних каналах зерноочисних машин для попереднього очищення зерна від легких домішок приймають рівною 6-7 м / с , для вторинного очищення зерна 7 - 8 м / с. При вторинному очищенні поряд із зазначеними домішками додатково виділяються також легковагі зерна основної культури .
Найбільш поширеною зерноочисної машиною , заснованої на поділі зернової суміші по аеродинамічних властивостях , є повітряно - ситовий сепаратор ( рис. 1-7) . Основними робочими органами сепаратора є плоскі коливні сита і вентилятор . Сита виділяють домішки , що відрізняються від основної маси зерна за розмірами ; вентилятор продуває зерно струменями повітря для видалення легких домішок.
На станині 1 за допомогою плоских пружних сталевих пластин 3 підвішений ситовий корпус 2 . Ексцентриковий вал 19 і шатун 20 призводять ситовий корпус в зворотно- поступальний рух . У верхній частині сепаратора знаходиться приймальня коробка 11 з шнеком 12 , який розподіляє зерно по всій ширині машини. Під шнеком маються засувки 13, що регулюють кількість зерна , що надходить на сита. Осадові камери 6 служать для уловлювання легких домішок з повітря, що подається вентиляторами 9 ( зазвичай встановлюють два вентилятори - по одному з кожного боку сепаратора ) .
рис . 1-7 . Повітряно- ситовий сепаратор
Швидкість руху повітря в аспіраційних каналах 5 і 10 , а також в осадових камерах 6 регулюється клапанами 7 і шиберами 8 , що встановлюються в різних положеннях , зазначених на схемі пунктиром . У нижній частині кожної осадової камери шарнірно підвішені клапани 4 , які завдяки розрідженню, створюваному вентилятором , щільно притискаються до стінок камер. У міру накопичення легких домішок на дні камер клапани під дією маси домішок відкриваються і пропускають їх в похилі лотки 16 , укріплені на ситова корпусі. Сита в ситова корпусі знімні. Очищення сит проводиться інерційним щітковим механізмом 18 .
Зерно , яке надходить до приймальні коробку 11 , рівномірно розподіляється по ширині машини шнеком 12 і засувками 13 і тонким потоком тече вниз по аспіраційного каналу 10 , в якому воно провітрюється струменем повітря . Зерно , очищене від легких домішок , зсипається на коливний ситовий корпус 2 . Па ситах 14 і 15 відокремлюються грубі і великі домішки , на ситі 17 - дрібні домішки. Очищене зерно сходом йде з сита 17 в аспіраційний канал 5 , де знову провітрюється.
Описаний сепаратор одинарний , із зворотно -поступальним рухом ситового корпусу. Існують також сепаратори з двома ситова корпусами і з круговим поступальним рухом сит. Продуктивність сепараторів залежить від якості очищення зерна. При первинному очищенні зерна , виробленої відразу після приймання від заготівельних організацій , відокремлюють найбільш грубі домішки. Вторинна очистка зерна проводиться перед переробкою його на солод і призначена для більш повного виділення домішок. Тому при вторинному очищенні в сепаратор подають зерна приблизно в 3-4 рази менше. На продуктивність сепаратора також впливають вид зерна, що переробляється , його насипна щільність ( табл. 1.2).
Таблиця 1.2
Показники | Пшениця | Жито | Ячмінь | Овес | Кукурудза | Просо |
Насипна щільність, г/м5 | 750 | 720 | 650 | 500 | 700 | 700 |
Коефіцієнт для розрахунку продуктивності сепаратора | 1,0 | 0,9 | 0,8 | 0,7 | 1,0 | 0,75 |
Технічна характеристика повітряно- ситових сепараторів наведена в літературі [ 1 , с. 20 ] .
При зворотно- поступальних рухах ситових корпусів , що забезпечують переміщення зернової маси по ситам , виникають сили інерції , які діють по лінії руху корпусів. Сили інерції через станину машини передаються міжповерхових перекриттів та іншим частинам будівлі і можуть призвести до небезпечних коливань останніх. Тому ситові корпусу потрібно врівноважити . Урівноваження досягається спільною роботою двох ситових корпусів на одному приводі або особливою конструкцією приводу.
Найбільш поширеним способом врівноваження ситових корпусів з кривошипно -шатунним приводним механізмом є урівноваження допомогою обертового вантажу
Балансуючий механізм , зміцнюваний безпосередньо на ситова корпусі , призводить в коливальний рух ситовий корпус і врівноважує виникають у ньому інерційні сили . Повний урівноваження досягається у сит , що здійснюють круговий поступальний рух і мають балансирний привід ( рис. 1-8) . Подвійний ситовий корпус 3 підвішений за допомогою тросів 4 до стельової рамі. Приводний механізм складається з веретена 6 і балансирной осі 1 з регульованими вантажами 7 .
Приводний механізм укріплений на стельової підвісці 5 . Балансирная вісь зміщена від осі веретена (ексцентриситет r = 45мм) і при обертанні в підшипнику 2 змушує здвоєний ситовий корпус здійснювати круговий поступальний рух . Вантажі 7 врівноважують інерційні сили корпусу.
Рис. 1-8. Подвійний сепаратор з круговим рухом ситових корпусів
Сучасні повітряно- ситові сепаратори ( аспіратори ) діють за аналогічним принципом , але з поділом виконуваних машиною операцій на дві частини:
відсів більш грубих і більш тонких частинок за допомогою комплекту вібраційних сит ;
видалення легких часток з використанням окремої розширювальної камери з рециркуляцією більшої частини використовуваного повітря .
Прикладом сучасного аспіратора може служити сепаратор «Классіфайер» (Classifier) фірми Бюлер (Biihler) (м. Брауншвейг, Німеччина) (рис. 2.6).
Як і всі аспіратори , цей сепаратор оснащений двома ситами для відділення більш грубих і більш тонких домішок, але, природно, розрахований на більш високу продуктивність (до 24 т/год). Привід розташований в центрі ваги ящика у вигляді двох ексцентрикових електродвигунів, що обертаються синхронно і в протифазі; завдяки цьому компенсується бічна вібрація, яка перетворюється в зворотно - поступальні рухи. У що знаходиться на виході з аспіраційного каналу продукті можуть відділятися легкі частинки, які потім очищаються від пилу в центральній аспіраційноїної установці.
|
а-впуск ячменю, b-випуск очищеного ячменю, з-підключення до пристрою для видалення пилу, d - видалення грубих домішок, е - випуск дрібних домішок (пісок і т. п.)
1 - станина, 2 - приймальна камера; 3 - поділ продукту; 4 - розподільний клапан; 5 - головне сито; 6 - сито для піску; 7 - ситовий ящик; 8 - аспіраційний канал
Рис. 2.6. Сепаратор «Классіфайер»:
Для знепилювання повітря в сучасних установках використовують аспіратори з повітряною циркуляцією (рис. 2.7).
За допомогою ексцентрикового мотора (1) дно ємності (2) періодично відкривається і пропускає рівномірний регульований потік ячменю , який відразу ж підхоплюється повітрям , легкі частинки піднімаються вгору , а ячмінь падає вниз. Потік подводимого повітря може регулюватися (5). У верхній частині аспіратора обсяг простору більше, і завдяки зниженню швидкості потоку легкі частинки падають вниз і видаляються через клапанний затвор (8).
Використане повітря знову підводиться по повітряному каналу і знову застосовується в циклі видалення домішок. Близько 10% отодімого повітря направляється в центральну аспірацію, і тому при подачі зерна виникає знижений тиск і з системи відводиться пил.
|
1 - ексцентриковий електродвигун; 2 - дно ємності з регульованою налаштуванням (башмак живильника), 3 - ємність живильника; 4 - переставляється стінка каналу; 5 - пристрій для перестановки підйомного каналу; 6 - регулювання повітря за допомогою дросельного клапана; 7 - розширювальна камера; 8 - клапанний затвор
А - впуск неочищеного ячменю; В - випуск очищеного ячменю; С - випуск легких відходів; D - відведення аспіраційного повітря з пилоподібними відходами до циклону
Рис. 2.7. Аспіратор з повітряною циркуляцією
Трієрів
Домішки, які від зерен основної культури довжиною , відокремити на ситах неможливо. Для цієї мети використовують трієри . Робочим органом трієра є циліндр або диск з осередками , які обирають короткі частинки.
За призначенням розрізняють трієри для виділення з основної маси зерна половинчастих зерен і кулястих домішок (куколя тощо) і трієри для відділення зерен основної культури (пшениці , ячменю і т. п.) від довгих зерен вівса і вівсюга . Трієри першого виду називаються куколеотборнікамі . трієри другого виду - овсюгоотборнікамі .
Осередки робочої поверхні куколеотборніка вибирають з маси зерна кулясті домішки і половинчасті зерна, кількість яких не перевищує 5%; осередку овсюгоотборніка, навпаки, вибирають основну складову частину - пшеницю, жито чи ячмінь, кількість якої звичайно дорівнює 95% обсягу зернової маси. Природно, при рівних розмірах продуктивність куколеотборніка набагато більше , ніж овсюгоотборннка .
Залежно від призначення діаметр осередків трієра різний: для виділення половинчастих зерен ячменю, кулястих зерен куколю та інших насіння 6,25-6,5мм; для виділення пшениці 8,5; для виділення ячменю з вівса 9.5-10мм.
Циліндрові і дискові трієри
Робочим органом циліндричного трієра (рис. 1-9) є циліндр, на внутрішній поверхні якого є осередки. При обертанні циліндра зерна заповнюють осередку і піднімаються на деяку висоту; довгі частинки, що не укладаються в осередках повністю, випадають з них при малому куті підйому і повертаються в зернову масу; короткі частинки, цілком укладаються в осередках , утримуються У них і випадають в лоток, знаходиться усередині циліндра. З лотка короткі частки віддаляються шнеком .
Частота обертання циліндричних трієрів обмежується так само, як і частота циліндричних сит , дією відцентрової сили, яка за певної граничної частоті обертання утримує частинки зерна в комірці і повністю припиняє поділ зернової суміші.
Рис 1-9. Схема циліндричного трієра
У трієрах зернова маса внаслідок енергійного перемішування набуває велику рухливість. Тому циліндри трієрів немає потреби встановлювати похило; переміщення зерна вздовж горизонтального циліндра відбувається в них під дією підпору зерна, що надходить в трієр. Для створення підпору зерна приймальний кінець циліндра закривають кільцевої діафрагмою.
На рис. 1-10 зображений циліндричний трієр . Ніздрюватий циліндр 3 і шнек 2 в ньому жорстко пов'язані між собою і обертаються одночасно. Лоток 1 вільно підвішений на валу 5; допомогою черв'яка 10 і черв'ячного сектора 9 цей лоток може бути встановлений під потрібним кутом. Положення лотка фіксується маховичком 12 на направляючої 11. Зерно надходить в циліндр через приймальню коробку 6 . Короткі частинки, вибрані з загальної маси зерна осередками трієра , направляються в лоток 1 і шнеком 2 виводяться з машини по каналу 8; довгі частинки сходять наприкінці циліндра через отвір 7 . У верхній частині трієра є отвір 4 для аспірації.
Рис. 1-10. циліндричний трієр
Іноді трієри забезпечуються ворушилка (рис. 1-11), яка відкидає очищуване зерно назустріч руху циліндра. Цим досягається краще використання комірчастої поверхні, завдяки чому продуктивність трієра різко зростає.
Рис. 1-11. Трієр з Ворушилки
Технічна характеристика циліндричних трієрів наведена в літературі [1, с.25]
Дискових ТРИЕР
У дискового трієра (рис. 1-16) під щитками 1 уздовж всього корпусу встановлений шнек 2, призначений для відділення із загальної маси коротких частинок, що потрапляють в неї при незадовільному дії якого-небудь диска. Для цього необхідно тільки відкрити кришку шнека проти даного диска. Па валу трієра можна послідовно поставити диски для відбору куколя , вівса та ін Частота обертання дискового трієра не обмежується умовою, обов'язковим для циліндричних трієрів; в останніх гранична частота обертання є такий, при якій відцентрова сила, що діє на одне зерно, досягає маси цього зерна. У дисковому трієрі ця гранична частота може бути перевершена.
У дисковому трієрі робочими елементами є литі чавунні диски з карманообразние осередками на бічних поверхнях (рис. 1-17 ) . Осередки залежно від того , для якого зерна призначений трієр , мають різну форму і ухил у напрямку обертання. На рис. 1-18 зображена типова форма осередків дискового трієра . Спиці диска мають форму вигнутих лопатей. На горизонтальний вал насаджують від 16 до 27 дисків. Вал з дисками ( ротор) обертається в циліндричному корпусі , заповненому зерном.
Роботу дискового трієра можна простежити по рис. 1-19 . Осередки диска , занурені в зернову масу (зона 1 ) , при обертанні ротора зачерпують зерно. Довгі частки випадають в зоні 2 і приєднуються до всієї маси зерна; короткі частки випадають в зоні 3 та по щитку 2 видаляються з машини. При обертанні ротора вигнуті спиці дисків 1 подібно шнеку пересувають зерно від одного диска до іншого в осьовому напрямку через всю машину ; потім зерно в очищеному вигляді виводиться назовні шнеком 3 .
Дискові трієри мають високу продуктивність і компактну форму , завдяки чому можлива установка двох одночасно працюючих дискових трієрів (рис. 1-20). Верхній трієр являє собою куколеотборннк , нижній - овсюгоотборнік .
Рис . 1-20 . Установка двох одночасно працюючих дискових трієрів
До недоліків дискових трієрів слід віднести швидку зношуваність дисків внаслідок стирання їх поверхні в шарі зерна; наявність піску в зерні і збирається па дні машини ( при недогляді може швидко вивести машину на ладу) ; лущення зерна , також обумовлене тертям дисків
Для аспірації дискового трієра необхідно видаляти до 4м3 повітря на хвилину.
Технічна характеристика дискових трієрів дана в [1, с. 28]
Магнітні сепаратори
У зерні , що надходить у виробництво , нерідко містяться різні металеві предмети: цвяхи , гайки , болтики , шматочки сталі і чавуну. Найбільш великі з них відокремлюються із зерна на ситах сепаратора ; дрібніші , за розмірами наближаються до зерна , проходять крізь сито разом з зерном. При подальшій обробці зерна шматочки металу , що потрапляють на робочі органи машин , прискорюють їх знос , а часом викликають поломки.
Сита сепараторів , робочі поверхні трієрів , сортувальні сита , росткоотбівние машини , солодополіровочние машини , дробарки для солоду і транспортери зношуються набагато швидше за наявності в зерні металевих домішок. Ці домішки видаляються магнітами , що встановлюються по шляху руху зерна самопливом , зазвичай відразу після сепаратора . Для магнітної сепарації зерно, що містить металеві домішки , пропускають тонким струменем поблизу магнітів.
СЕПАРАТОРИ з постійними магнітами
Постійні магніти для сепараторів виготовляють з металів або їх сплавів, що володіють високими магнітними властивостями: магнітною проникністю , магнітною індукцією , коерцитивної силою. Магнітні сталі містять один або кілька легуючих компонентів: хром, вольфрам, кобальт, молібден. Останнім , час постійні магніти стали виготовляти з безуглеродістих сплавів на основі заліза. Подібні сплави мають високу залишковою індукцією і коерцитивної силою, але мають істотні недоліки: крихкість і погану оброблюваність різанням.
У магнітних сепараторах використовують обидва полюси магніту , для чого йому надають дугоподібну форму.
Простий магнітний апарат (рис. 1-21) складається з підковоподібних постійних магнітів 3, вставлених в корпус 4 і закріплених на ньому стрижнем 2. Полюси магніту встановлюють під кутом 45° до горизонту. Заслінка 1 призначена для регулювання кількості проходить зерна.
Металеві частки видаляють з поверхні магніту механічно або вручну. Магнітний апарат з ручним очищенням вимагає систематичного спостереження і своєчасне видалення металевих домішок. Якщо полюси магнітів замикаються великою кількістю металевих частинок, то робота апарату припиняється.
Постійні магніти слід оберігати від нагрівання і ударів, так як при цьому вони втрачають силу тяжіння . На час тривалих зупинок полюси магніту рекомендується замикати пластинками з м'якої сталі.
Рис. 1-21. Сепаратор з постійними магнітами
Технічна характеристика магнітних сепараторів з постійними дугоподібними магнітами і ручний очищенням наведена в [ 1 , с. 30 ]
ЕЛЕКТРОМАГНІТНІ СЕПАРАТОРИ
Основний недолік сепараторів з постійними магнітами - їх обмежена сила тяжіння , слабшає з часом.
У електромагнітах щільність магнітного потоку залежить тільки від сили струму, що живить котушки. Тому електромагніти можуть володіти потужним магнітним полем. Відомо багато конструкцій електромагнітних сепараторів.
Розглянемо барабанний електромагнітний сепаратор , що володіє великою пропускною здатністю і надійністю дії . Поверхня барабана очищається безперервно і автоматично.
Електромагнітний барабанний сепаратор ( рис. 1-22) складається з ряду нерухомих сердечників , намагнічувалося струмом, що протікає в котушках . Навколо електромагніта 1 обертається барабан 2 з немагнітного матеріалу (алюмінію, латуні). З воронки 3 на обертовий барабан потрапляє зерно; сталеві частинки притягуються до поверхні барабана і утримуються на ній, поки не вийдуть з магнітного поля.
Рис. 1-22. Електромагнітний барабанний сепаратор
Технічна характеристика електромагнітних барабанних сепараторів наведена в [1, с. 31].
МАШИНИ ДЛЯ ДРОБЛЕННЯ ЗЕРНА
Молоткова дробарка
При безперервному разваривании зерно подрібнюють на молоткових дробарках , руйнування зерна в них відбувається в результаті ударів сталевих молотків по зерну , ударів частинок про кожух дробарки і шляхом стирання їх про штамповане сито. Зерно , подрібнене до часток певного розміру , проходить через сито і видаляється з дробарки. Найбільшого поширення в спиртової промисловості отримали молотковідробарки ДМ і ДДМ .
Основним робочим органом дробарки ДМ ( рис. II - 1 ) є ротор 12; між дисками 3 ротора на стержнях 2 вільно підвішені молотки 5, виготовлені зі сталі товщиною 1,5-2мм. У корпусі встановлено сменяемое сито 4 (діаметр отворів у ситі становить 3,5 і 8мм) , яке закріплюється сталевими стрічками 11 . Подача зерна в дробарку проводиться з приймального бункера 8 інерційним живильником 9. Привід живильника здійснюється від електродвигуна 1 за допомогою ексцентрикового вала 7. Зерно з приймального бункера потрапляє на площину 10 з регульованим нахилом, проходить над магнітним сепаратором 6 і надходить у дробарку. Продуктивність дробарки становить 20 т / год, потужність електродвигуна 22 кВт , частота обертання ротора 2940 об / хв . Поряд з дробаркою ХМ застосовують дробарки ДДР .
Рис. II-1. Молоткова дробарка ДМ
Для тонкого подрібнення зерна ведуться розробки нових дискових дробарок типу дезінтегратора (обидва диска обертаються ) або дисмембратор (обертається один диск). Дезінтегратор (рис. II - 2) складається з кожуха 3, робочих дисків 4, на торцевих поверхнях яких розташовані по концентрич -ським окружностям пальці 2. Привід дисків проводиться за допомогою шківів 1 , при цьому диски обертаються в протилежних напрямках. У міру віддалення від центру відстань між пальцями, розташованими на одній окружності , зменшується. Підлягає подрібненню матеріал потрапляє в зазор між обертовими в протилежному напрямку дисками. Просуваючись від центру до периферії дисків, зерно багаторазово вдаряється об пальці і руйнується. При цьому інтенсивність руйнування наростає, оскільки крок між пальцями зменшується, а окружна швидкість їх зростає. Подрібнене зерно викидається в кожух дезінтегратора і спускається вниз, до вихідного отвору .
Рис. II-2. дезінтегратор
Дата добавления: 2022-01-22; просмотров: 15; Мы поможем в написании вашей работы! |
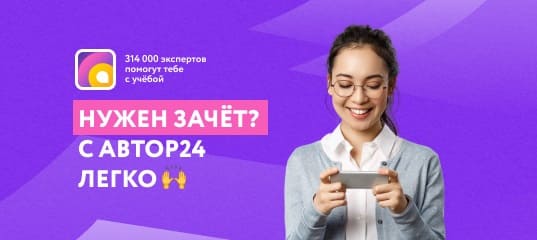
Мы поможем в написании ваших работ!