Расчет цикла простого производственного процесса.
Логистика производства
Лекция 3
Организация производственных процессов во времени
Формирование производственного цикла изделия необходимо для обеспечения рационального взаимодействия всех элементов производственного процесса и упорядочения выполняемых работ во времени и в пространстве.
Производственным циклом называется комплекс определенным образом организованных во времени основных, вспомогательных и обслуживающих процессов, необходимых для изготовления определенного вида продукции.Понятие о производственном цикле применимо не только к процессу изготовления машин, но и к процессам проектирования, испытания изделий, вспомогательным и обслуживающим процессам. Важнейшей характеристикой производственного цикла является его длительность.
Длительность производственного цикла — это календарный период времени, в течение которого материал, заготовка или другой обрабатываемый предмет проходит все операции производственного процесса или определенной его части и превращается в готовую продукцию. Длительность производственного цикла чаще всего выражается в календарных днях, а при малой трудоемкости изделий – в часах. Структура производственного цикла включает время рабочего периода и время перерывов. В течение рабочего периода выполняются собственно технологические операции и работы подготовительно-заключительного характера. К рабочему периоду относятся также продолжительность контрольных и транспортных операций и время естественных процессов. Время перерывов обусловлено режимом труда, межоперационным пролеживанием деталей и недостатками в организации труда и производства.
|
|
Время межоперационного пролеживания определяется перерывами партионности, ожидания и комплектования. Перерывы партионности возникают при изготовлении изделий партиями и обусловлены тем, что обработанные изделия пролеживают, пока партия не пройдет через данную операцию. При этом исходят из того, что производственной партией называется группа изделий одного и того же наименования и типоразмера, запускаемых в производство в течение определенного времени при одном и том же подготовительно-заключительном периоде. Перерывы ожидания вызываются несогласованной длительностью двух смежных операций технологического процесса, а перерывы комплектования — необходимостью ожидания того времени, когда будут изготовлены все заготовки, детали или сборочные единицы, входящие в один комплект изделий. Перерывы комплектования возникают при переходе от одной стадии производственного процесса к другой.
|
|
В наиболее общем виде длительность производственного цикла Тц выражается формулой
Тц = Тт + Тп-з+ Те + Тк + Ттр + Тмо +Тпер , (1)
где: Тт — время технологических операций; Тп-з — время работ подготовительно-заключительного характера; Те — время естественных процессов; Тк — время контрольных операций; Ттр — время транспортирования предметов труда; Тмо— время межоперационного пролеживания (внутрисменные перерывы); Тпер - время перерывов, обусловленных режимом труда.
Межоперационные перерывы или время межоперационного пролеживания возникает из-за дискретности процесса производства, связанного с разностью производительности оборудования, вследствие которой детали, полуфабрикаты пролеживают либо в ожидании освобождения оборудования либо время пролеживания связано с регламентными перерывами.
Время межоперационного пролеживания Тмо в машиностроении достаточно велико, так что это время может быть использовано для выполнения контрольных , транспортных и операций складирования.
Регламентированные перерывы – это выходные дни, обеденные перерывы, нерабочие смены.
Нерегламентированные перерывы связаны с организационно-техническими неполадками, аварийным простоем оборудования и другими нештатными ситуациями. Нерегламентированные перерывы учитываются при определении фактической длительности цикла.
|
|
Структура производственного цикла включает в себя выполнение основных, вспомогательных операций и перерывы (рис. ).
![]() ![]() ![]() ![]() ![]() ![]() ![]()
![]() ![]() ![]() ![]() ![]() ![]() ![]() ![]() ![]() ![]() ![]() ![]() ![]() ![]() ![]()
![]() ![]() ![]() ![]() ![]() ![]()
![]() | ||||||||||
Рис.3.1 |
Длительность технологических операций и подготовительно-заключительных работ в совокупности образует операционный цикл Тц оп.
Операционный цикл — это продолжительность законченной части технологического процесса, выполняемой на одном рабочем месте.
Методы расчета длительности производственного цикла. Необходимо различать производственный цикл отдельных деталей и цикл изготовления сборочной единицы или изделия в целом. Длительность цикла Тц рассчитывается для изготовления одной детали, партии деталей отдельного узла или партии узлов, но нельзя рассчитать Тц изготовления изделия в целом. Длительность цикла изготовления изделия или партии изделий устанавливается путем разработки цикловых графиков на типовые изделия. Производственный цикл детали обычно называют простым, а изделия или сборочной единицы — сложным. Цикл может быть однооперационным и многооперационным. Длительность цикла многооперационного процесса зависит от способа передачи деталей с операции на операцию. Существуют три вида движения предметов труда в процессе их изготовления: последовательный, параллельный и параллельно-последовательный.
|
|
При последовательном виде движения вся партия деталей передается на последующую операцию после окончания обработки всей партии на предыдущей операции. Достоинствами этого метода является отсутствие перерывов в работе оборудования и рабочего на каждой операции, возможность их высокой загрузки в течение смены. Но производственный цикл при такой организации работ является наибольшим, что отрицательно сказывается на технико − экономических показателях деятельности цеха, предприятия.
При параллельном виде движения детали передаются на следующую операцию транспортной партией сразу после окончания ее обработки на предыдущей операции. В этом случае обеспечивается наиболее короткий цикл. Но возможности применения параллельного вида движения ограничены, так как обязательным условием его реализации является равенство или кратность продолжительности выполнения операций. В противном случае неизбежны перерывы в работе оборудования и рабочих.
При параллельно-последовательном виде движения деталей с операции на операцию они передаются транспортными партиями или поштучно. При этом происходит частичное совмещение времени выполнения смежных операций, а вся партия обрабатывается на каждой операции без перерывов. Рабочие и оборудование работают без перерывов. Производственный цикл длительнее по сравнению с параллельным, но короче, чем при последовательном движении предметов труда.
Расчет цикла простого производственного процесса.
При наличии на операции нескольких работающих станков операционный цикл ( напомним, что это продолжительность обработки партии на одной (данной) операции процесса) определится следующим образом:
Тц.посл = n , (2)
где n — количество деталей в производственной партии, шт.; — норма времени на выполнение каждой операции, мин;
− количество рабочих мест, занятых изготовлением партии деталей на каждой операции.
Операционный производственный цикл партии деталей при последовательном виде движения рассчитывается следующим образом:
Тц.посл = n , (3)
где m — число операций технологического процесса. Схема последовательного вида движения представлена на рис. 10.4, а. По данным, приведенным на схеме, можно рассчитать операционный цикл партии, состоящей из четырех деталей, обрабатываемых на четырех операциях ( =1):
Тц.посл = 4·( +
+
+
) = 4·(2 + 1,5 + 2,5 +1) = 28 мин.
Номера операций |
| |||||||||||
1 |
![]() ![]() ![]() ![]() | |||||||||||
2 |
![]() | |||||||||||
3 |
![]() ![]() ![]() ![]() ![]() ![]() ![]() | |||||||||||
4 |
![]() ![]() ![]()
| |||||||||||
![]() | ![]() | ![]() | ![]() | |||||||||
Минуты | 4 | 8 | 12 | 16 | 20 | 24 | 28 | 32 | ||||
Рис. 10.4, а. График производственного цикла при последовательном движении партий деталей |
Технологический цикл пропорционален размеру партии и трудоемкости операции. При этом имеют место существенные перерывы партионности. Поэтому такая организация движения предметов труда целесообразна при небольших партиях изделий и при невысокой трудоемкости операций. Как правило, это свойственно мелкосерийному и единичному производству. В организационном отношении такой вид движения предмета труда имеет некоторые преимущества так как партии изделий не дробятся и в производстве невелико число планово-учетных единиц. При значительных партиях образующиеся длительные циклы приводят к отрицательным экономическим последствиям. Поэтому в серийных, крупносерийных и массовых производствах этот вид организации движения предметов труда неприменим.
С учетом всех межоперационные перерывов (пролеживания), транспортных, складских, контрольных операций и естественных процессов (например сушки после окрашивания), рассчитывают производственный цикл:
Тц.посл = n +
+ Te , (3)
где – длительность i-го межоперационного перерыва, Te – длительность естественных процессов.
Можно рассчитать длительность производственного цикла в днях:
Тц.посл = n +
+
+
, (3)
где – подготовительно-заключительное время, s – количество смен, q – продолжительность смены. Тe в этой формуле, очевидно, берется в часах.
Чтобы сократить длительность цикла и достичь непрерывности производственного процесса применяется параллельно-последовательный вид движения предметов труда. Сущность его заключается в разделении всей обрабатываемой партии на транспортные (передаточные) партии p. Подбор транспортных партий позволяет добиться непрерывности выполнения операций над партиями деталей и обеспечивает возможность максимальной загрузки оборудования и рабочих.
| |||
| |||
1 |
![]() ![]() ![]()
![]() ![]()
![]() ![]() ![]() ![]() ![]() ![]() ![]() ![]() ![]() ![]() ![]() ![]() ![]() ![]() ![]() ![]() ![]() ![]() ![]() ![]() ![]() ![]() ![]() | ![]() ![]() ![]() ![]() ![]() ![]() |
![]() ![]() ![]() ![]() ![]() ![]()
![]() ![]() ![]() ![]() ![]() ![]() ![]() ![]() ![]() ![]() ![]() | ||||||||||||||||
![]() | ![]() | ||||||||||||||||||
Рис. 5 Варианты парных сочетаний операций |
При параллельно-последовательном виде движения происходит частичное совмещение во времени выполнения смежных операций. Существует два вида сочетания смежных операций во времени: а) если время выполнения последующей операции больше времени выполнения предыдущей операции и б) если время выполнения последующей операции меньше времени выполнения предыдущей. Возможен и вариант, когда времена выполнения операций равны.
Первые два случая изображены на рис. 5.
В первом варианте максимальное сочетание операций можно получить, передавая первую транспортную (передаточную) партию (p) на последующую операцию сразу же после окончания работы над ней на предыдущей. Все последующие транспортные партии будут пролеживать между этими операциями, ожидая освобождения следующего рабочего места (i+1), при этом обеспечивается непрерывная работа на всех рабочих местах. Во втором варианте для обеспечения непрерывной работы на последующей операции (i+1) необходимо ориентироваться на последнюю транспортную партию, определяя возможное время работы над ней на этой (i+1) операции. Чтобы обеспечить непрерывную загрузку рабочих мест операции (i+1), к этому времени необходимо закончить работу над всеми предшествующими транспортными партиями, осуществляя ее без перерывов. То есть необходимо следовать правилу, при котором если ti > ti+1 , то согласования проводят по последней детали комплекта, а если ti < ti+1 – то по начальной.
При этом сокращение технологического цикла на величину τ достигается за счет частичного запараллеливания работ на смежных операциях. Эта экономия может быть рассчитана по наиболее короткой из двух смежных операций:
а) при <
τ = Тпосл − Тпп , Тпосл = n (t1/c1) + n (t2/c2); Тпп = p (t1/c1) + n (t2/c2). Подставив эти значения в формулу для τ нетрудно получить: τа = (n – p) (t1/c1);
б) при >
τ = Тпосл − Тпп , Тпосл = n (t1/c1) + n (t2/c2); Тпп = n (t1/c1) + p (t2/c2), и τа = (n – p) (t2/c2).
В том и в другом случае индексы при t/c соответствуют операции с более коротким циклом, следовательно, это соотношение имеет место для каждой пары смежных операционных циклов, т. е. τ = (n – p) (t/c)кор.
Схема параллельно-последовательного вида движения приведена на рис. 10.4, в. Цикл при параллельно-последовательном движении предметов труда меньше, чем при последовательном вследствие наличия параллельности протекания каждой пары смежных операционных циклов на сумму всех имеющихся τi , т. е. на . Таким образом формула для длины технологического цикла при параллельно - последовательном движении предметов труда будет выглядеть следующим образом:
Тц.пп = n − (n – p)
)кор.. (6)
Производственный цикл можно рассчитать по формуле:
Тц.пп = n − (n – p)
)кор.+
+ Te , (7)
а производственный цикл в днях:
Тц.пп = n − (n – p)
)кор.+
+
. (8)
Номера операций |
| |||||||||||||
![]() |
![]() ![]() ![]() | |||||||||||||
![]() |
![]() ![]() ![]() ![]() ![]() ![]() ![]() ![]() ![]() ![]() | |||||||||||||
3 |
| |||||||||||||
4 |
![]() ![]() ![]() ![]() ![]() ![]() ![]() ![]() ![]() ![]() | |||||||||||||
![]() | ![]() | |||||||||||||
Минуты | 4 | 8 | 12 | 16 | 20 | 24 | 28 | 32 | ||||||
Рис. 10.4, а. График производственного цикла при параллельно-последовательном движении партий деталей |
Для примера, приведенного на рис. 10.4 технологический цикл, вычисленный по формуле (6), выглядит так:
Тц.пп = 28 – (4 – 1)( 1,5 + 1,5 +1) = 28– 12 = 16мин.
Как видно из рисунка, графически получается та же величина.
При такой организации движения предметов труда не достигается полной непрерывности, так как детали пролеживают в ожидании обработки. Параллельно-последовательный вид движения имеет более короткий цикл, но приводит к увеличению числа учетно-плановых единиц, к более высокому темпу работы транспортных средств. Его целесообразно применять при больших партиях и большой трудоемкости изделий, что свойственно крупносерийному производству.
Параллельный вид движения предметов труда в производстве характеризуется тем, что небольшие передаточные партии или отдельные штуки передаются с предыдущей операции на последующую немедленно по окончании их обработки на предыдущей (вне зависимости от длительности смежных операционных циклов). При этом партия разделяется на небольшие передаточные (транспортные) партии p или даже отдельные штуки, которые имеют независимое от всей партии движение в процессе обработки (рис. 5).
Номера операций |
| |||||||||||||
![]() ![]() ![]() |
| |||||||||||||
![]() ![]() |
| |||||||||||||
3 |
![]() ![]() ![]() ![]() ![]() ![]() ![]() ![]() ![]() ![]() ![]() | |||||||||||||
4 |
![]() ![]() ![]() ![]() ![]() ![]() ![]() | |||||||||||||
![]() | ![]() | ![]() | ![]() | |||||||||||
Минуты | 4 | 8 | 12 | 16 | 20 | 24 | 28 | 32 | ||||||
Рис. 5График производственного цикла при параллельном движении партий деталей |
Технологический цикл при параллельном виде движения изделий рассчитывается по формуле:
Тц (пар) = p + (n – p)(
)max. , (8)
где p – размер передаточной партии, ( max — время выполнения операции, самой продолжительной в технологическом процессе, мин.
Эта формула легко получается из примера, приведенного на рис.5. В самом деле Тц (пар) легко вычислить:
Тц (пар) = pt1/c1 + pt2/c2 + nt3/c3 + pt4/c4 = p − pt3/c3 + nt3/c3 =
= p + (n− p) t3/c3. (9)
Здесь использован тот факт, что p = pt1/c1 + pt2/c2 + pt3/c3 + pt4/c4, а в левой части (9) слагаемого pt3/c3 нет, значит его необходимо вычесть из правой части, чтобы соблюдалось равенство. Заметим, что t3/c3 есть не что иное, как (
max.
Производственный цикл для параллельного движения предметов труда будет выглядеть следующим образом:
Тц (пар) = p + (n− p) (
max .+
+
. (9)
При параллельном движении предметов труда партии или отдельные штуки в процессе обработки не пролеживают, однако рабочие места загружены не полностью. Таким образом, в этом случае имеет место параллельность, наиболее короткий цикл, но так же, как и ранее, не достигается непрерывность.
При неупорядоченных по производительности операций технологических процессах параллельный вид движения деталей сопряжен с простоями оборудования, что весьма ограничивает использование такого вида организации движения предметов труда. Он допустим лишь в порядке исключения, при острой дефицитности отдельных деталей или сборочных единиц. Как видно на рис. 5, непрерывно загружено оборудование только на главной операции, т. е. имеющей самый большой операционный цикл. На остальных операциях оборудование простаивает. Поэтому параллельный вид движения партий нецелесообразно применять в процессах, имеющих операционные циклы различной продолжительности, так как при этом потери окажутся весьма значительными. Следует либо спроектировать процесс так, чтобы выровнять операционные циклы, либо перейти на менее уплотненный по времени, но с лучшим использованием оборудования параллельно-последовательный вид движения партий. Тем более, что если при этом операционные циклы следуют в порядке монотонно-убывающей или монотонно-возрастающей функции, то циклы технологических процессов при параллельном и параллельно-последовательном видах движения предметов труда будут иметь равную продолжительность.
В процессах, имеющих одинаковую производительность по всем операциям технологического процесса, т. е. при Топ = const, достигается полная непрерывность движения предмета труда, работы оборудования и рабочих. Такой вариант процессов ложится в основу организации непрерывно-поточного производства и цикл его определяют, исходя из ритма поточной линии r и числа рабочих мест с Тпот = ; или при партионной подаче Тпот =
.
Продолжительность вспомогательных (транспортных, контрольных) операций, в зависимости от организации их выполнения, не всегда включается в норматив производственного цикла, так как она полностью или частично может быть перекрыта временем технологического цикла или временем перерывов в обработке. Но при сложных погрузочно-разгрузочных работах или неперекрываемых контрольных (стендовые испытания) и транспортных (пульсирующий конвейер) операциях и других это время включается в производственный цикл. Межоперационные перерывы обычно рассчитывают через нормативы заделов, затем корректируют по статистическим данным и устанавливают общую их величину для группы технологически родственных деталей (по детали-представителю), а затем усредняют эту величину в расчете на одну операцию в процессе, т. е. tмо = Тмо/m, где Тмо — суммарные межоперационные перерывы в процессе, Тмо= ; m — число основных операций в процессе. С учетом введенного значения Тмо формулы для производственных циклов для последовательного, параллельно-последовательного и параллельного движения предметов труда будут выглядеть так:
Тц.посл = n +
+
+
;
Тц.пп = n − (n – p)
)кор.+
+
;
Тц (пар) = p + (n− p) (
max .+
+
. (11)
![]()
![]() ![]() ![]() ![]() ![]() ![]() ![]() ![]() ![]() ![]() ![]() ![]() ![]() |
![]() ![]() ![]() ![]() ![]()
![]() ![]() ![]() ![]() ![]() | ||||||||||||||||||||||||||||||||||
![]() ![]() ![]() ![]() ![]() ![]() ![]() ![]() ![]() ![]() ![]()
![]() ![]() ![]() | |||||||||||||||||||||||||||||||||||
Рис. 6 Элементы операционных перерывов |
Наличие межоперационных перерывов необходимо учитывать в графиках движения предметов труда и в производственном цикле (рис. 6).
Перерывы, связанные с режимом работы производства, обычно учитывают путем перевода цикла, рассчитанного в рабочем времени, в календарное время, соблюдая при этом размерность всех слагаемых цикла.
Дата добавления: 2022-01-22; просмотров: 50; Мы поможем в написании вашей работы! |
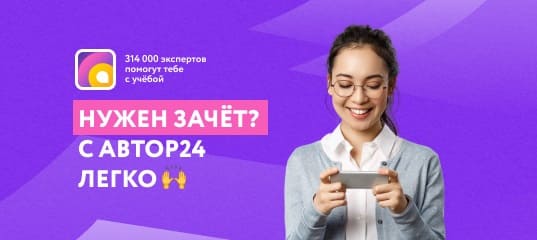
Мы поможем в написании ваших работ!