ОСТАТОЧНЫЕ НАПРЯЖЕНИЯ, СТРУКТУРНЫЕ И ФАЗОВЫЕ ПРЕВРАЩЕНИЯ
ОБЩИЕ СВЕДЕНИЯ О ПОВЕРХНОСТИ ДЕТАЛЕЙ И ЕЁ ГЕОМЕТИИ
В технике под поверхностью детали понимают наружный слой, который по строению и другим физическим свойствам отличается от внутренних слоев. Комплекс свойств, приобретаемых поверхностью детали в результате ее обработки, характеризуется обобщенным понятием «качество поверхности».
Качество поверхности определяется геометрией поверхности, как границей тела, так и физико-химическими свойствами, обусловленными процессом ее образования при обработке детали. Качество поверхности деталей машин влияет на сопротивление усталости, износостойкость, коррозионную и эрозионную стойкость и связано с такими свойствами сопряжений, как прочность посадок с натягом и плотность подвижных и неподвижных соединений.
Всякое реальное тело имеет отклонения от идеальной геометрической формы, именуемые погрешностями. Погрешности обработанной поверхности можно подразделить на три категории: 1) макрогеометрические отклонения, 2) волнистость поверхности, 3) шероховатость поверхности.
Макрогеометрическими отклонениями называют отклонения формы поверхности от заданной. Так, детали с боковой поверхностью кругового цилиндра могут иметь следующие погрешности (рис. 3.3): отклонения контура от окружности (овальность /а/, огранка /б/); отклонения от прямолинейности образующих при прямолинейности оси цилиндра (бочкообразность /в/); отклонения от прямолинейности образующих (конусность /г/); криволинейности оси /д/. Величина и характер этих отклонений могут быть определены путем измерения диаметра детали в различных поперечных сечениях по длине, а в данном поперечном сечении – в различных направлениях.
|
|
Возникновение макрогеометрических погрешностей поверхности происходит в основном из-за низкой точности станка, на котором происходит обработка, погрешностей установки заготовок, силовых и температурных деформаций системы станок – заготовка – инструмент и износа инструмента в процессе обработки детали.
Рис. 3.3. Макрогеометрические отклонения поверхности цилиндрической детали при токарной обработке
Волнистость поверхности – совокупность более или менее регулярно чередующихся возвышений и впадин с шагом волны, значительно превышающим ее высоту (рис. 3.3).
![]() |
Волнистость в направлении главного движения при резании называют продольной, а в перпендикулярном направлении – поперечной.
Волнистость поверхности образуется в результате неравномерности подачи при точении и шлифовании, неплоскостности направляющих и вынужденных колебаний системы станок – изделие – инструмент, возникающих из-за неравномерности силы резания, наличия неуравновешенных масс и т.д. Другими причинами могут быть копирование волнистости режущего инструмента, искажение формы шлифовального круга и неравномерный износ его, а также погрешности движения инструмента или изделия. От шероховатости волнистость поверхности отличается значительно большим шагом: при чистовой обработке он не менее 0,25 мм, при грубой – превышает 8 мм. Достаточно часто высота волны при чистовом точении и цилиндрическом шлифовании доходит до 15 мкм при шаге до 14 мм.
|
|
Шероховатость поверхности –совокупность неровностей поверхности с относительно малыми шагами на базовой длине.
Реальная поверхность не является гладкой, то есть она содержит выступы и впадины с относительно малым расстоянием между ними – микронеровности, которые образуют рельеф поверхности детали. Контур сечения реальной поверхности плоскостью, перпендикулярной соответствующей идеальной геометрической поверхности, образует профиль, характеризующий микрогеометрию поверхности изделия. Графическое изображение реального профиля по данным измерений шероховатости называют профилограммой шероховатости. Так как через данную точку геометрической поверхности можно провести бесчисленное множество нормальных сечений, то шероховатость поверхности следует связывать с тем или иным направлением.
|
|
Шероховатость обработанной поверхности в направлении главного движения при резании называют продольной, а в направлении подачи – поперечной шероховатостью. Преобладающее направление следов механической обработки поверхности или следов трения называют направлением неровностей.
Количественно шероховатость можно оценить по тем или иным показателям. ГОСТ 2789-73 предусматривает шесть параметров, характеризующих шероховатость поверхности: три высотных – Ra, Rz и R max, два шаговых – S и S m и относительная опорная длина профиля t p.
Средним арифметическим отклонением профиля Ra называют среднее арифметическое абсолютных значений отклонений профиля в пределах базовой длины l (рис. 3.4):
или
.
На профилограмме положение средней линии профиля определяют так, чтобы площади F по обе стороны от нее до контура профиля были равны, т.е. чтобы
или
.
Относительная однородность микронеровностей поверхности детали позволяет судить о шероховатости в данном направлении по результатам обследования участка сравнительно небольшой длины. Длину базовой линии, используемую для выделения неровностей, характеризующих шероховатость поверхности, называют базовой длиной l .
|
|
Высота неровностей профиля по десяти точкам Rz представляет собой сумму средних абсолютных значений высот пяти наибольших выступов профиля и глубин пяти наибольших впадин профиля в пределах базовой длины (см. рис. 3.4):
,
где ypi – высота i-го наибольшего выступа профиля; yui – глубина i-й наибольшей впадины профиля.
Наибольшая высота неровностей профиля R max является полной высотой профиля, т.е. расстоянием между линией выступов профиля и линией впадин профиля в пределах базовой длины. Главными показателями шероховатости поверхности являются Ra и Rz. В ГОСТ 2789-73 можно найти другие показатели: S, S m и t p .
Профилограммы обработанной поверхности, как правило, имеют пилообразную форму; это является результатом того, что вертикальное увеличение во много раз больше горизонтального (например, 40 000 и 400 соответственно). Иногда создается представление, что при трении обработанные поверхности зацепляются своими зубцами. В действительности профиль поверхности выглядит иначе (рис. 3.5).
Отдельные неровности имеют пологую форму. Угол между плоскостью основания выступа профиля и касательной к его боковой поверхности составляет при доводке 1 – 3°, при шлифовании 10° и при точении 20°. Самые гладкие металлические поверхности имеют неровности высотой порядка 100 межатомных расстояний.
ОСТАТОЧНЫЕ НАПРЯЖЕНИЯ, СТРУКТУРНЫЕ И ФАЗОВЫЕ ПРЕВРАЩЕНИЯ
Остаточными называют напряжения, существующие в теле при отсутствии внешних силовых воздействий на него. Наличие этих напряжений обусловлено неравномерностью температуры по объему тела, образованием во время нагрева или охлаждения новых структур с иной плотностью, наличием включений и др. Остаточные напряжения образуют равновесную систему. В зависимости от объема, который охватывается этой системой, различают собственные напряжения трех родов. Напряжения первого рода уравновешиваются в крупных объемах, соизмеримых с размерами детали; напряжения второго рода (микронапряжения) уравновешиваются в пределах одного или нескольких кристаллических зерен; напряжения третьего рода – субмикроскопические искажения кристаллической решетки. Напряжения второго и третьего родов не имеют ориентировки относительно осей детали.
Пластическая деформация вызывает уменьшение плотности металла или, что то же, увеличение его удельного объема. Пластически деформированный при резании слой не может свободно увеличиваться в объеме (этому препятствует недеформированный металл изделия), поэтому в наружном слое проявляются напряжения сжатия, а в остальной части – напряжения растяжения.
Это рассуждение предполагает, что деформируемый слой не находится даже частично в состоянии ползучести. В зависимости от температуры металл может быть в упругом и пластичном состояниях. В состоянии ползучести металла силы упругости не проявляются, и деформация протекает без стремления материала к восстановлению формы.
За температуру рекристаллизации (t p ) , то есть перехода из упругого состояния металла в пластическое, можно принять 450°С для углеродистых сталей и 550°С для легированных.
Средняя температура поверхностного слоя стали при шлифовании составляет 300 – 400°С, у самой поверхности 800 – 850°С. Температуры того же порядка развиваются при скоростном точении. Нагрев поверхностного слоя металла при обработке обусловливает образование в нем температурных напряжений. Допустим, что в процессе обработки цилиндрической детали слой 1 (рис. 3.6) находится в состоянии ползучести. В этом слое внутренние напряжения отсутствуют, а если до того существовали остаточные напряжения, то они снимаются. В слое 2 с температурой ниже t p, но выше нормальной t н возникают напряжения сжатия, а в слое 3 – напряжения растяжения. Напряжения эти временные. Как только наружный слой охладится до температуры t p, он станет упругим. Встречая сопротивление сокращению, он оказывается растянутым в окружном направлении. В слое 2 сжимающие напряжения возрастают. При дальнейшем охлаждении до полного выравнивания температуры по глубине металла напряжения растяжения в слое 1 возрастают, а в слоях 2 и 3 устанавливается система уравновешивающих напряжений сжатия. По характеру остаточные температурные напряжения, равно как и обусловленные пластической деформацией, являются напряжениями первого рода. Однако из-за неодинакового тепловыделения на смежных участках обрабатываемой поверхности и различной степени пластической деформации возникают также остаточные напряжения второго рода.
Итак, при обработке металла в его наружном слое под влиянием пластической деформации при отсутствии ползучести развиваются остаточные напряжения сжатия, тепловой же эффект от резания приводит к напряжениям растяжения. Так как оба фактора действуют совместно, то знак остаточного напряжения в наружном слое зависит от того, какой из факторов превалирует. Разумеется, если температура на обрабатываемой поверхности менее t p, то температурные напряжения являются временными, после выравнивания температуры они исчезают.
Пластическая деформация, в том числе и при резании металлов, обусловливает изменение микроструктуры. Беспорядочно расположенные в исходной структуре металла кристаллические зерна при пластической деформации приобретают однородную ориентацию (текстуру). Более глубокие изменения возможны при обработке металлов, воспринимающих закалку. Так как каждой структурной составляющей свойствен присущий ей удельный объем, то фазовые и структурные превращения наряду с пластической деформацией являются источником остаточных напряжений.
Местные фазовые и структурные превращения поверхностного слоя шлифуемой детали известны под названием шлифовочных прижогов. Они образуются вследствие интенсивного (почти мгновенного) тепловыделения на небольшом участке поверхностного слоя. При шлифовальном круге нормальной твердости, нормальном режиме шлифования и достаточном охлаждении прижоги возникают из-за вибрации круга (циклические прижоги), неправильной установки детали на центрах и т.п. В области прижогов образуются остаточные напряжения. Прижоги являются структурными концентраторами напряжения, понижающими как сопротивление усталости, так и износостойкость.
Фазовые и структурные превращения при обработке инструментом возможны только для металлов с метастабильной структурой.
В случае холодной пластической деформации металла повышаются его твердость и предел прочности при одновременном снижении относительного удлинения и относительного поперечного сужения при растяжении. Это явление называют упрочнением металла или наклепом.
При резании металлов протекают два противодействующих друг другу процесса: упрочнение в результате действия сил резания, которое тем выше, чем больше давление резания, и разупрочнение – снятие наклепа за счет повышающейся температуры резания. Степень наклепа и толщина наклепанного слоя при прочих равных условиях зависят от режима резания.
Дата добавления: 2022-01-22; просмотров: 27; Мы поможем в написании вашей работы! |
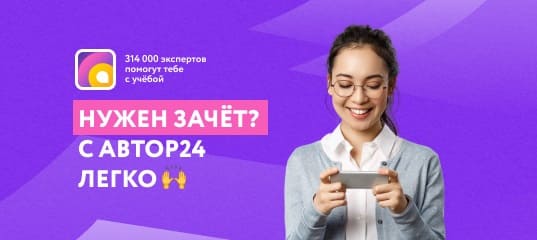
Мы поможем в написании ваших работ!