Типовые технологические процессы изготовления, применяемое оборудование и оснастка.
Задачами технологического проектирования явл-ся определение условий изготовления изделий, определение типа производства, видов исходных заготовок, проектирование технологического маршрута обработки, выявление необходимых средств производства и порядка их применения , определение себестоимости и трудоёмкости изготовления изделий , определение исходных данных для календарного планирования, для организации технического контроля, определение состава рабочей силы.
Исходные данные для проектирования технологических процессов.
Исходные данные ( информация) для проектирования технологических процессов подразделяют согласно ГОСТ 14.301-83 на:
- базовые;
-руководящие;
-справочные.
Базовая информация включает данные , содержащиеся в конструкторской документации на изделие и программу выпуска:
-чертёж детали с техническими требованиями на изготовление;
-чертежи сборочных единиц , определяющих служебное назначение деталей и их отдельных поверхностей;
-условия работы деталей;
-объём выпуска;
-плановые сроки выпуска.
Руководящая информация предопределяет подчинённость принимаемых решений стандартам, учёт перспективных разработок.
Руководящая информация включает:
- стандарты, устанавливающие требования к технологическим процессам и методам управления ими;
-стандарты на оборудование и оснастку;
-документацию на действующие единичные, типовые и групповые технологические процессы;
|
|
-классификаторы технико-экономической информации;
-производственные инструкции;
-материалы по выбору технологических нормативов( режимов обработки, припусков, норм расхода материалов и др);
-документацию по охране труда.
К справочной информации относятся: опыт изготовления аналогичных изделий, методические материалы и нормативы, результаты научных исследований.
Справочная информация включает:
-данные , содержащиеся в технологической документации опытного производства;
-описание прогрессивных методов изготовления и ремонта;
-каталоги и паспорта, справочники;
-альбомы компоновок прогрессивных средств технологического оснащения ;
-планировки производственных участков;
-методические материалы по управлению технологическими процессами.
При проектировании технологических процессов для действующих предприятий должна учитываться общая производственная обстановка:
- наличие площадей;
-состав и степень загрузки оборудования;
-наличие технологической оснастки;
- обеспеченность предприятия квалифицированной рабочей силой и др.
Последовательность проектирования технологических процессов изготовления деталей машин.
|
|
Процесс технологического проектирования содержит ряд взаимосвязанных и выполняемых в определённой последовательности этапов. К ним относятся:
-анализ исходных данных;
-технологический контроль чертежа;
- определение типа и организационной формы производства;
-выбор вида исходной заготовки и метода её получения;
-выбор вида технологического процесса;
-разработка технологического кода детали на основе технологического классификатора;
-выбор технологических баз и схем базирования заготовки;
-выбор методов обработки поверхностей заготовки;
-проектирование маршрута обработки;
-разработка структуры операций;
-выбор средств технологического оснащения ( оборудования, приспособлений, режущих и измерительных инструментов);
-назначение и расчёт режимов обработки;
-назначение и расчёт припусков и операционных размеров;
-нормирование технологического процесса и определение квалификации работы;
-выбор средств механизации и автоматизации элементов технологического процесса и средств внутрицехового транспорта;
-составление планировки ( по необходимости) и разработка операций перемещения деталей и отходов;
|
|
-разработка мероприятий по обеспечению требований техники безопасности и производственной санитарии;
-комплексная технико-экономическая оценка технологического процесса;
-оформление технологической документации.
Трудоёмкость, станкоёмкость, производительность технологического процесса. Норма времени и норма выработки.
Трудоёмкость обработки представляет собой затраты времени на выполнение технологического процесса ( или его элементов) изготовления единицы продукции. Выраженная в человеко- часах она позволяет определить необходимое кол-во рабочих.
Станкоёмкость представляет собой кол-во станочного времени, затрачиваемого на выполнение технологического процесса или его элементов. Единицей измерения станкоёмкости явл-ся станко-час. Станкоёмкость служит для расчёта числа станков, необходимого для выполнения одной или нескольких операций обработки.
Производительность – кол-во продукции в штуках или других единицах, выпускаемой в единицу времени.
Технически обоснованной нормой времени называется регламентированное время выполнения технологической операции в определённых организационно- технических условиях, наиболее благоприятных для данного производства. Технически обоснованные нормы времени позволяют установить расценки , определить производительность оборудования, осуществить календарное планирование и т.д.
|
|
Технической нормой выработки называется величина , обратная норме времени выполнения операции. Выражается числом изделий , изготавливаемых на операции в единицу времени.
Технически обоснованную норму времени и техническую норму выработки устанавливают на каждую операцию.
Применяют три метода установления норм времени:
-на основе изучения фактических затрат рабочего времени наблюдением;
-расчёт по нормативам;
-расчёт по укрупнённым типовым нормам.
Первые два метода нормирования применяют в серийном и массовом производствах, третий – в единичном и мелкосерийном.
Структура технически обоснованной нормы времени.
Время, затрачиваемое на технологическую операцию изготовления единицы продукции , в общем случае складывается из двух частей:
t ш.к =t шт + tп.з , где
N
t ш.к - штучно-калькуляционное время ( представляет собой трудоёмкость изготовления на операции);
t шт- штучное время изготовления единицы продукции;
tп.з – подготовительно- заключительное время , затрачиваемое на партию изготавливаемой продукции;
n- кол-во единиц продукции ( например деталей) в партии.
Штучное время выражается формулой t ш.к = tо+tв+tт+t+орг+tп, где
tо - основное ( технологическое ) время;
tв – вспомогательное время;
tт – время технического обслуживания рабочего места;
tорг – время организационного обслуживания;
tп – время перерывов в работе.
В единичном производстве выпускаются изделия широкой номенклатуры с малыми объёмами выпуска. Изготовление изделий либо не повторяется , либо повторяется через неопределённые промежутки времени. На каждом рабочем месте за смену обрабатываются детали различных наименований.
В серийном производстве выпускаются изделия ограниченной номенклатуры, изготавливаемые периодически повторяющимися партиями со сравнительно большим объёмом выпуска. На рабочих местах выполняются несколько периодически повторяющихся операций. Различают мелкосерийное, среднесерийное и крупносерийное производство.
Серийное производство явл-ся основным типом машиностроительного производства. Примерно 75…80% всей продукции машиностроения страны изготавливаетяс на заводах серийного производства.( станки, прессы, текстильные машины, насосы и т.д). В серийном производстве заготовки обрабатывают партиями.
Производственная партия – это группа заготовок одного наименования и типоразмера, запускаемых в обработку одновременно или непрерывно в течение определённого интервала времени.
Кол-во деталей в партии (n) рассчитывается по формуле:
n =Na
Т
Где N – объём выпуска;
Т – кол-во рабочих дней в планируемом периоде выпуска;
а- периодичность запуска в днях.
Серия изделий –это общее кол-во изделий определённого наименования, типоразмера и исполнения , изготовляемых или ремонтируемых по неизменяемой конструкторской документации.
Интервал времени от начала до окончания производственного процесса изготовления или ремонта изделия называют производственным циклом.
В массовом производстве выпускаются изделия узкой номенклатуры с большим объёмом выпуска , непрерывно изготавливаемые в течение продолжительного времени. На каждом рабочем месте выполняется только одна закреплённая за ним операция. ( Производство автомобилей, тракторов, подшипников качения, швейные машинки и т.д).
При проектировании технологического процесса на конкретную деталь тип производства ориентировочно может быть определён по заданному объёму выпуска с помощью таблицы.
Тип производства. | Годовая программа выпуска деталей одного наименования, шт. | Годовая программа выпуска деталей одного наименования, шт. | Годовая программа выпуска деталей одного наименования, шт. |
Лёгкие до 20 кг. | Средние 20-300 кг. | Тяжёлые , свыше 300 кг. | |
Единичное | До 100 | До 10 | 1-5 |
Мелкосерийное | 101-500 | 11-200 | 6-100 |
Среднесерийное | 501-5000 | 201-1000 | 101-300 |
Крупносерийное | 5001-50000 | 1001-5000 | 301-1000 |
Массовое | Свыше 50000 | Свыше 5000 | Свыше 1000 |
Значения коэффициента:
К=1 – для массового производства;
К=2-10 – для крупносерийного производства;
К=10-20 – для среднесерийного производства;
К> 20 – для мелкосерийного производства.
После окончательной разработки технологических процессов для определённого участка или цеха на всю номенклатуру обрабатываемых деталей тип производства определяется по коэффициенту закрепления операций.
Выбор средств технологического оснащения.
К технологическому оборудованию относятся литейные машины, прессы, станки, печи, гальванические ванны, контрольные и испытательные стенды и т.д.
Выбор технологического оборудования ( станков) определяется:
- методом обработки;
-точностью и качеством обрабатываемой поверхности;
-габаритными размерами заготовок, размерами обработки и массой заготовок,;
-мощностью. Потребной на резание;
-экономически целесообразной производительностью и себестоимостью в соответствии с типом производства;
-возможностью уборки отходов и соблюдения правил экологии;
-возможностью приобретения и стоимостью станка;
-удобством и безопасностью работы.
По технологическому назначению все металлорежущие станки подразделяются на девять групп. В каждой группе предусмотрены девять типов станков, отличающихся друг от друга технологическим назначением , расположением их главных рабочих органов ( например, вертикально-и горизонтально-фрезерные станки), степенью автоматизации ( полуавтомат или автомат).
По степени универсальности станки подразделяются на универсальные \. Специальные и специализированные.
По массе – на лёгкие ( до 1 т), нормальные ( до 10 т), крупные ( до 30 т), тяжёлые ( до 100т) и уникальные ( более 100т).
По точности – нормальной (Н) точности, повышенной (П), высокой (В), особо высокой (А), особо точные или прецизионные (С).
Оборудование должно подбираться не только с точки зрения обеспечения предъявляемых к нему технических требований, но и с точки зрения достижения наивысших экономических показателей проектируемой операции.
Выбор технологической оснастки.
Технологическая оснастка – орудия производства, дополняющие технологическое оборудование для выполнения определённой части технологического процесса.
К технологической оснастке относятся:
- приспособления;
-режущий инструмент;
-вспомогательный инструмент;
-контрольно- измерительный инструмент.
Приспособление ( станочное) – технологическая оснастка , предназначенная для закрепления заготовки на станке при выполнении технологической операции. Применение приспособлений расширяет технологические возможности металлорежущего оборудования.
Конструкции приспособлений с учётом стандартных и типовых решений для данного вида технологических операций определяются на основе:
- габаритных размеров изделий;
- вида заготовок;
-материала изделий;
-точности обработки , качества поверхности;
-конфигурации изделия;
-схем базирования и закрепления;
-характеристик оборудования;
- типа производства.
Различают следующие системы установочно- зажимных станочных приспособлений:
-неразборные специальные (НСП);
-универсально- наладочные (УНП);
-универсально- сборные (УСП);
-сборно-разборные (СРП);
-универсально- безналадочные (УБП);
-специализированные наладочные (СНП).
По возможности следует применять универсальные, переналаживаемые и быстродействующие приспособления. Применение специальных приспособлений должно быть экономически оправдано.
Выбор режущего инструмента.
Режущий инструмент выбирается с учётом :
-максимального применения нормализованного и стандартного инструмента;
-метода обработки;
-размеров обрабатываемых поверхностей и размеров станков;
-заданной точности обработки и качества поверхности;
-условий работы;
-промежуточных размеров и допусков на эти размеры;
-требуемой производительности;
-обрабатываемого материала;
-стойкости инструмента, его режущих свойств, жёсткости и прочности;
-стадии обработки ( черновая, чистовая, отделочная);
-стоимости инструмента;
- типа производства;
Размеры мерного режущего инструмента определяются исходя из промежуточных размеров обработки ( зенкеры, развёртки, протяжки и т.д), размеры других видов инструмента ( резцы, расточные борштанги и т.д) должны определяться из расчёта по прочности и жёсткости.
Выбор вспомогательного инструмента.
Вспомогательный инструмент выбирают по уже выбранному режущему инструменту. Вспомогательный инструмент должен иметь , с одной стороны, установочные поверхности и элементы крепления , соответствующие режущему инструменту, а с другой стороны – поверхности установки и элементы крепления, соответствующие посадочным местам станка. К вспомогательному инструменту относятся:
-для резцов –резцедержатели;
-для насадных фрез- оправки, концевых – цанговые патроны, переходные втулки;
-для осевого инструмента с коническим хвостовиком ( свёрла, зенкеры) – переходные втулки , с цилиндрическим хвостовиком – сверлильные патроны, в том числе быстросменные;
-для метчиков и плашек – специальные патроны;
-для расточных резцов – оправки и борштанги;
-для развёрток – оправки качающиеся.
Конструктивные особенности, служебное назначение и технические требования, предъявляемые к поршням, гильзам, шатунам двигателей. Материал и заготовки Типовые технологические процессы изготовления, применяемое оборудование и оснастка. Техническая и технологическая документация, применяемая при изготовлении деталей и агрегатов автотракторной техники
Дата добавления: 2022-01-22; просмотров: 13; Мы поможем в написании вашей работы! |
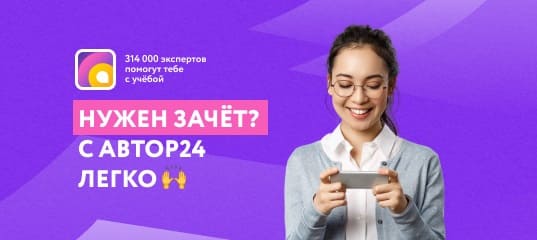
Мы поможем в написании ваших работ!