Основные этапы проектирования технологических процессов механической
ПМ 01. «Разработка технологических процессов изготовления деталей машин»
МДК 01. 01 Технологические процессы изготовления деталей машин
Тема 1.1 Технологическое оборудование и оснастка машиностроительных производств.
Виды технологической оснастки
Типовые конструкции различных видов технологической оснастки: станочные, сборочные, контрольные приспособления, вспомогательные приспособления .
Захватные устройства промышленных роботов. |
Методы автоматизации проектирования технологической оснастки
Технологичность конструкции изделия
Базирование. Базы в машиностроении
Основы проектирования технологических процессов механической обработки
|
|
и организационно-технического уровня производства.
1. ВИДЫ ТЕХНОЛОГИЧЕСКИХ ПРОЦЕССОВ
1.1. Классификация и определение видов технологических процессов.
1.1.1. Технологические процессы классифицируют на основные виды по следующим
признакам:
- форма организации технологического процесса, определяемая числом охватываемых
предметов производства или их конструктивных элементов;
- освоенность технологического процесса того или иного вида, определяемого формой его
организации, в конкретных производственных условиях.
1.1.2. В зависимости от формы организации технологического процесса различают три его
вида:
- единичный;
- типовой;
- групповой.
Определение указанных видов технологических процессов - по ГОСТ 3.1109-82.
1.1.3. В зависимости от освоенности производством различают два вида технологического
процесса: рабочий и перспективный.
Рабочим технологическим процессом называется процесс изготовления одного или
нескольких изделий в соответствии с требованиями принятой для данных условий
производства рабочей технологической документации.
1.2. Единичные технологические процессы.
1.2.1. Единичный технологический процесс разрабатывают только на уровне предприятия
|
|
и применяют для изготовления или ремонта одного конкретного предмета производства.
Разработка рабочих технологических процессов осуществляется в соответствии с
требованиями ГОСТ 3.1001-74.
1.2.2. Единичный технологический процесс разрабатывают на основе имеющихся
типового и группового технологических процессов изготовления изделий, относящихся к
определенной классификационной группе, или единичном технологического процесса
изготовления аналогичного изделия.
1.2.3. При определении степени детализации содержания документации единичного
рабочего технологического процесса следует исходить из того, что рабочий технологический
процесс должен обеспечивать возможность изготовления предмета производства в полном
соответствии с рабочей конструкторской документацией на изделие.
1.2.4. Рабочий технологический процесс должен обеспечивать: реализацию значений
базовых показателей технологичности конструкций изготовляемого изделия; соблюдение
правил техники безопасности и промышленной санитарии, изложенных в системе
стандартов безопасности труда (ССБТ), стандартах на типовые технологические процессы,
инструкциях и других нормативных документах по технике безопасности и промышленной
|
|
санитарии.
1.2.5. Единичный перспективный технологический процесс разрабатывают на конкретное
изделие серийного или массовом производства, если технически и экономически целесообразно внедрить содержащиеся в этом процессе решения не с момента запуска
изделия в производство, а лишь с определенной серии изделия или этапа производства после
произведения запланированного на перспективу комплекса мероприятий (по реконструкции,
переоснащению производства и т.п.).
Рис. 1. Принципиальная схема классификации технологических процессов
1.3. Групповые технологические процессы.
1.3.1. Групповой технологический процесс разрабатывается с целью экономически
целесообразного применения методов и средств крупносерийного и массового производства
в условиях единичного, мелкосерийного и серийного производства.
1.3.2. Обязательным этапом, предшествующим разработке групповых процессов, является
группирование предметов производства по технологическому подобию с учетом основных
факторов организации производства.
Группирование предметов производства следует осуществлять на основе их
классификации и результатов комплексного анализа:
|
|
- состава и программ выпуска изделий;
- существующей структуры производственных подразделений;
- технико-экономических показателей производства.
1.3.3. Групповой технологический процесс охватывает комплексы групповых
технологических операций, выполняемых на специализированных рабочих местах в
последовательности технологического маршрута изготовления определенной группы
изделий.
1.3.4. Групповую технологическую операцию следует разрабатывать для выполнения
технологически однородных работ при изготовлении группы изделий на
специализированном рабочем месте при условии возможности подналадки средств
технологическом оснащения. Ее можно создавать и применять как составную часть
группового технологического процесса и отдельную групповую операцию.
При разработке групповой технологической операции предусматривают достаточную
величину суммарной трудоемкости технологически однородных работ для обеспечения
непрерывной загрузки средств технологического оснащения без их полной переналадки в
течение экономически целесообразного периода. Допускается только частичная подналадка
средств технологического оснащения.
Групповые технологические операции осуществляют с учетом специализации рабочих
мест путем: - применения высокопроизводительных специализированных средств технологического
оснащения взамен универсальных;
- применения высокопроизводительных универсально-переналаживаемых средств
технологического оснащения;
- целевой модернизации оборудования;
- целевой наладки оборудования.
1.3.5. Основой разработки группового технологического процесса и выбора общих
средств технологического оснащения для совместной обработки группы изделий служит
комплексное изделие.
При разработке комплексного изделия следует учитывать, что его конструкция должна
содержать основные подлежащие обработке элементы всех изделий группы.
Комплексное изделие может быть:
- одним из изделий группы;
- реально существующим, но отсутствующим в группе;
- искусственно созданным (условным).
При значительном разнообразии конструкций сочетающихся поверхностей деталей,
затрудняющих искусственное создание комплексного изделия, его заменяют двумя или
несколькими характерными деталями группы.
1.3.6. Групповые технологические процессы и операции разрабатывают для всех типов
производства только на уровне предприятия.
1.3.7. Групповой перспективный технологический процесс разрабатывают в случаях,
когда для экономически обоснованного повышения уровня использования метода групповой
обработки на предприятии требуется провести большой комплекс подготовительных
мероприятий по переоснащению действующего производства.
1.4. Типовые технологические процессы.
1.4.1. Типовой технологический процесс должен быть рациональным в конкретных
производственных условиях, характеризоваться единством содержания и
последовательности большинства технологических операций для группы изделий,
обладающих общими конструктивными признаками. Разрабатывают его на основе анализа
множества действующих и возможных технологических процессов на типовые
представители групп изделий.
1.4.2. Типизация технологических процессов базируется на классификации объектов
производства, должна обеспечивать устранение многообразия технологических процессов
обоснованным сведением их к ограниченному числу типов и служить базой для разработки
стандартов на типовые технологические процессы.
Классификация объектов производства заключается в разделении их по признакам,
содержащимся в конструкторской документации, на отдельные группировки, для которых
возможна разработка общих технологических процессов или операций.
1.4.3. Типизация технологических процессов осуществляется на уровнях предприятия или
отрасли.
На отраслевом уровне выполняется разработка типовых технологических процессов
соответственно межотраслевого и внутриотраслевого применения.
На уровне предприятия производится разработка и применение типовых технологических
процессов для перспективной номенклатуры однотипных объектов производства.
1.4.4. Разработка типовых технологических процессов на каждом уровне базируется на
внедрении научно-технических достижений и передового опыта промышленности в области
технологии машиностроения и рациональном использовании материальных и трудовых
ресурсов производства с учетом конкретных производственных условий.
1.4.5. Типовой перспективный технологический процесс разрабатывают на группу
изделий, обладающих общими показателями функционального назначения (например, на совокупность моделей, образующих вид изделия, и т.п.) или общими технологическими
признаками (например, общность метода обработки, единство средств технологического
оснащения и т.д.), если технически и экономически целесообразно внедрить этот процесс
лишь с определенной модели или этапа производства изделий после необходимого
технического и организационного перевооружения производства.
2. РАЗРАБОТКА И ПРИМЕНЕНИЕ ТЕХНОЛОГИЧЕСКИХ ПРОЦЕССОВ
2.1. Основные требования к разработке технологических процессов.
2.1.1. Технологический процесс разрабатывается для изготовления нового или
модернизуемого изделия и совершенствования действующего технологического процесса в
соответствии с достижениями науки и техники.
2.1.2. Разрабатываемый технологический процесс должен быть прогрессивным и
обеспечивать повышение производительности труда и качества изделий, сокращение
трудовых и материальных затрат на его реализацию, уменьшение вредных воздействий на
окружающую среду.
Прогрессивность технологического процесса оценивается по показателям, установленным
системой аттестации технологических процессов в отрасли и на предприятии.
2.1.3. Технологический процесс должен соответствовать требованиям техники
безопасности и промышленной санитарии, изложенным в системе стандартов безопасности
труда (ССБТ), стандартах на типовые и групповые технологические процессы, инструкциях
и других нормативных документах по технике безопасности и промышленной санитарии.
2.1.4. Документы на технологические процессы всех видов следует оформлять в
соответствии с требованиями стандартов Единой системы технологической документации
(ЕСТД).
2.1.5. Разработка рабочих технологических процессов проводится для изготовления или
ремонта изделий, конструкции которых отработаны на технологичность.
Технологический процесс должен обеспечивать реализацию значений базовых
показателей технологичности конструкций изготовляемого или ремонтируемого изделия.
2.1.6. Единичный технологический процесс разрабатывают на основе имеющегося
типового или группового технологического процесса.
При отсутствии типового или группового технологического процесса изготовления
изделия, относящегося к определенной классификационной группе, технологический
процесс создается на основе использования ранее принятых прогрессивных решений,
содержащихся в действующих единичных технологических процессах изготовления
аналогичных изделий.
2.1.7. Объекты производства, на которые разрабатывают перспективные технологические
процессы, и стадии разработки конструкторской документации, после завершения которых
целесообразно разрабатывать перспективный технологический процесс, устанавливают с
учетом специфики разрабатываемого изделия (например, конструкция изделия требует
применения новых физических способов воздействия, новых требований к материалам и т.п.)
и наличия исходной информации, достаточной для разработки этого процесса в заданные
сроки.
2.1.8. При организации производства нового изделия перспективные технологические
процессы разрабатывают после завершения стадий эскизного или технического проектов
разработки конструкторской документации на изделие. В технически обоснованных случаях
их разрабатывают после завершения стадии разработки рабочей документации опытного
образца (партии).
Принципиальная схема взаимосвязи разработки перспективного технологического
процесса со стадиями разработки изделия приведена на рис. 2. На схеме приняты следующие условные обозначения: ТКИ - технологичность конструкции изделия; ТТП - типовой
технологический процесс; СТО - стандартное технологическое оснащение.
2.1.9. Разработка перспективных технологических процессов должна быть основана на
результатах проведения научно-исследовательских, опытно-технологических, опытно-
конструкторских работ, прогнозирования новых методов обработки, разработки и
исследования перспективных технологических возможностей предприятий, анализа опыта
применения новых методов и средств технологического оснащения другими предприятиями
промышленности.
2.2. Исходная информация для разработки технологических процессов.
2.2.1. Исходную информацию для разработки технологических процессов подразделяют
на базовую, руководящую и справочную.
2.2.2. Базовая информация включает данные, содержащиеся в конструкторской
документации на изделие, и программу выпуска этого изделия.
2.2.3. Руководящая информация включает данные, содержащиеся в следующих
документах: стандартах и руководящих материалах, устанавливающих требования к технологическим
процессам и методам управления ими, а также стандартах на оборудование и оснастку;
программах и планах повышения технического уровня производства и совершенствования
его организации;
документации на перспективные технологические процессы;
документации на действующие единичные, типовые и групповые технологические
процессы;
классификаторах технико-экономической информации;
производственных инструкциях;
материалах по выбору технологических нормативов (режимов обработки, припусков,
норм расхода материалов и др.);
документации по технике безопасности и промышленной санитарии.
2.2.4. Справочная информация включает данные, содержащиеся в следующих документах:
технологической документации опытного производства;
описаниях прогрессивных методов обработки;
каталогах, паспортах, справочниках, альбомах компоновок прогрессивных средств
технологического оснащения;
методических материалах по типовым методам расчета производительности, точности и
стабильности технологических процессов;
планировках производственных участков;
методических материалах по управлению технологическими процессами;
2.3. Этапы разработки технологических процессов.
2.3.1. В общем случае разработка единичных, групповых и типовых технологических
процессов (ЕТП, ГТП, ТТП) состоит из этапов, приведенных в табл. 1.
2.3.2. Необходимость каждого этапа, состав задач и последовательность их решения
определяются в зависимости от видов и типа производства и готовности предприятия к
освоению технологического процесса.
Основные этапы проектирования технологических процессов механической
Обработки
1 ТЕХНОЛОГИЯ ИЗГОТОВЛЕНИЯ ВАЛОВ
1.1 Характеристика валов
В технологии машиностроения в понятие валы принято включать собственно валы, оси, пальцы, штоки, колонны и дру-
гие подобные детали машин, образованные наружными поверхностями вращения при значительном преобладании длины
над диаметром. Конструктивное разнообразие валов вызывается различным сочетанием цилиндрических, конических, а так-
же зубчатых (шлицевых), резьбовых поверхностей. Валы могут иметь шпоночные пазы, лыски, осевые и радиальные отвер-
стия (рис. 1).
Рис. 1 Классификация валов
Технологические задачи
Технологические задачи формулируют в соответствии с рекомендациями и охватывают требованиям к точности детали
по всем ее параметрам (рис. 2).
Точность размеров. Точными поверхностями валов являются, как правило, его опорные шейки, поверхности под дета-
ли, передающие крутящий момент. Обычно они выполняются по 6...7-му квалитетам.
Точность формы. Наиболее точно регламентируется форма в продольном и поперечном сечениях у опорных шеек под
подшипники качения. Отклонения от круглости и профиля в продольном сечении не должны превышать 0,25...0,5 допуска на
диаметр в зависимости от типа и класса точности подшипника.
Точность взаимного расположения поверхностей. Для большинства валов главным является обеспечение соосности ра-
бочих поверхностей, а также перпендикулярности рабочих торцов базовым поверхностям. Как правило, эти величины выби-
раются по V – VII степеням точности.
Рис. 2 Эскиз вала с типовыми техническими требованиями
Качество поверхностного слоя. Шероховатость базовых поверхностей обычно составляет Rа = 3,2...0,4 мкм, рабочих
торцов Rа = 3,2...1,6 мкм, остальных несоответственных поверхностей Rа = 12,5...6,3 мкм. Валы могут быть сырыми и тер-
мообработанными. Твердость поверхностных слоев, способ термообработки могут быть весьма разнообразными в зависимо-
сти от конструктивного назначения валов. Если значение твердости не превышает НВ 200...230, то заготовки подвергают
нормализации, отжигу или термически не обрабатывают. Для увеличения износостойкости валов повышают твердость их
рабочих поверхностей. Часто это достигается поверхностной закалкой токами высокой частоты, обеспечивающей твердость
НRС 48...55. Поверхности валов из малоуглеродистых марок стали подвергают цементации на глубину 0,7...1,5 мм с после-
дующей закалкой и отпуском. Таким способом можно достичь твердости НRС 55...60.
Так, например, для вала, представленного на рис. 3, технологические задачи формулируются следующим образом:
− точность размеров основных поверхностей находится в пределах 6...8-го квалитетов, а размеры с неуказанными от-
клонениями выполняются по 14-му квалитету;
Рис. 3 Эскиз вала
− точность формы регламентируется для опорных шеек допусками круглости и профиля в продольном сечении – 0,006
мм, а у остальных поверхностей погрешности формы не должны превышать определенной части поля допуска на соответст-
вующий размер (например, для нормальной геометрической точности 60 % от поля допуска);
− точность взаимного расположения задается допусками радиального и торцового биений (соответственно 0,02 мм и
0,016 мм) относительно базы;
− шероховатость сопрягаемых цилиндрических поверхностей ограничивается значениями Rа = 0,8 мкм, а торцовых –
Rа = 1,6 мкм; шероховатость несопрягаемых поверхностей – Rа = 6,3 мкм; шлицевый участок подвергается термообработке
ТВЧ НRС 50...55.
Некоторые требования к технологичности валов
К технологичности валов предъявляются некоторые специфические требования.
1 Перепады диаметров ступенчатых валов должны быть минимальными. Это позволяет уменьшить объем механиче-
ской обработки при их изготовлении и сократить отходы металла. По этой причине конструкция вала с канавками и пружин-
ными кольцами технологичнее конструкции вала с буртами.
2 Длины ступеней валов желательно проектировать равными или кратными длине короткой ступени, если токарная об-
работка валов будет осуществляться на многорезцовых станках. Такая конструкция позволяет упростить настройку резцов и со-
кратить их холостые перемещения.
3 Шлицевые и резьбовые участки валов желательно конструировать открытыми или заканчивать канавками для выхо-
да инструмента. Канавки на валу необходимо задавать одной ширины, что позволит прорезать их одним резцом.
4 Валы должны иметь центровые отверстия. Запись в технических требованиях о недопустимости центровых отвер-
стий резко снижает технологичность вала. В таких случаях следует заметно удлинять заготовку для нанесения временных
центров, которые срезают в конце обработки.
1.2 Материалы и заготовки валов
Валы, в основном, изготовляют из конструкционных и легированных сталей, к которым предъявляются требования вы-
сокой прочности, хорошей обрабатываемости, малой чувствительности к концентрации напряжений, а также повышенной
износостойкости. Этим требованиям, в определенной степени, отвечают стали марок 35, 40, 45, 40Г, 40ХН и др. Достаточно
редко валы отливают из чугуна.
В технических требованиях на изготовление валов, прежде всего, указывается твердость материала или необходимость
соответствующей термической обработки. Если значение твердости не превышает НВ 200...230, то заготовки подвергают
нормализации, отжигу или термически не обрабатывают. Для увеличения износостойкости валов повышают твердость их
рабочих поверхностей. Часто это достигается поверхностной закалкой токами высокой частоты, обеспечивающей твердость
HRС 48...55. Поверхности валов из малоуглеродистых марок стали подвергают цементации на глубину 0,7...1,5 мм с после-
дующей закалкой и отпуском. Таким способом можно достичь твердости НRС 55... 60.
Производительность механической обработки валов во многом зависит от вида заготовки, ее материалов, размера и
конфигурации, а также от характера производства. Заготовки получают отрезкой от горячекатаных или холодно-тянутых
нормальных прутков и непосредственно подвергают механической обработке.
Прокат круглого сечения поступает на машиностроительные заводы в виде многометровых прутков, из которых в заго-
товительных цехах нарезаются заготовки необходимой длины.
В наибольшей мере указанным требованиям отвечают отрезные круглопильные станки, применяемые в серийном и
массовом производствах. В качестве режущего инструмента в них применяются пильные диски, оснащенные сегментами из
быстрорежущей стали. Таким диском можно разрезать прокат диаметром до 240 мм или пакет прутков меньшего диаметра.
Торцы заготовок после отрезки имеют шероховатость Rа = 25 мкм.
В мелкосерийном и единичном производствах применяются более простые, но менее производительные отрезные но-
жовочные станки. Тонкие ножовочные полотна дают узкий пропил, но вследствие малой жесткости не обеспечивают высо-
кой перпендикулярности торцов заготовок.
Резка прутков и труб из высокотвердых, закаленных сталей наиболее эффективна на абразивно-отрезных станках, ос-
нащенных тонкими, толщиной 3...6 мм абразивными кругами на бакелитовой или вулканитовой связках. Благодаря высокой
скорости вращения, достигающей 80 м/с, круги быстро разрезают пруток, образуя ровный срез с шероховатостью Rа =
3,1...6,3 мкм. Во избежание пережога торцов зона резания обильно поливается охлаждающей жидкостью.
Рис. 4 Схема правильно-рихтовочного устройства станка:
1 – пруток; 2 – ролик
В сравнении с перечисленными другие методы резки применяются реже. К ним относятся резка на токарно-отрезных
станках отрезными резцами, на фрезерных станках прорезными фрезами, резка фрикционными пилами. Фрикционная пила
представляет собой тонкий стальной диск, которому сообщается скорость вращения выше 100 м/с. В месте контакта с заго-
товкой выделяющаяся вследствие трения теплота расплавляет металл прутка, что обеспечивает высокую производитель-
ность процесса. Однако оплавление торцов заготовок снижает их качество. К наиболее производительным методам относят-
ся рубка прутков на прессах и резка ножницами. Существенным недостатком этих методов, ограничивающим их применение,
является смятие концов заготовок.
На машиностроительные заводы прокат поступает с заметными отклонениями от прямолинейности оси. Для устранения
кривизны прутки перед резкой подвергают правке. Для этой цели служат правильно-калибровочные станки. Нарезанные за-
готовки перед началом обработки, а иногда и в процессе дальнейшей обработки также приходится подвергать правке. Такую
правку обычно проводят на прессах.
Заготовки такого вида применяют в основном в мелкосерийном и единичном производстве, а также при изготовлении
валов с небольшим количеством ступеней и незначительными перепадами их диаметров.
В производстве с более значительным масштабом выпуска, а также при изготовлении валов более сложной конфигура-
ции с большим количеством ступеней, значительно различающихся по диаметру, заготовки целесообразно получать методом
пластической деформации. Эти методы (ковка, штамповка, периодический прокат, обжатие на ротационно-ковочных маши-
нах, электровысадка) позволяют получать заготовки, по форме и размерам наиболее близкие к готовой детали (рис. 5), что
значительно повышает производительность механической обработки и снижает металлоемкость изделия.
Рис. 5 Заготовки, полученные методами:
а – штамповкой в штампах; б – штамповкой на горизонтально-ковочной
машине; в – поперечно-винтовой прокаткой
Выбор наиболее рационального способа получения заготовки в каждом отдельном случае определяется комплексно с
учетом технико-экономической целесообразности. С увеличением масштабов выпуска особое значение приобретают эффек-
тивность использования металлов и сокращение трудоемкости механической обработки. Поэтому в крупносерийном и мас-
совом производстве преобладают методы получения заготовок с коэффициентом использования металлов от 0,7 и выше (от-
ношение массы детали к норме расхода металла), доходящим в отдельных случаях до 0,95. Полые валы целесообразно изго-
тавливать из труб.
Детали, имеющие поверхности вращения (цилиндрические, наружные, фасонные, цилиндрические внутренние и др.)
обрабатывают на различных станках: токарной группы (токарно-винторезные, токарно-карусельные, токарно-револьверные,
одношпиндельные и многошпиндельные полуавтоматы и автоматы, станки для тонкого точения и др.); шлифовальной груп-
пы (круглошлифовальные, бесцентрово-шлифовальные, притирочные, полировальные и т.п.). Станки этих групп применяют
как обычные, так и с числовым программным управлением (ЧПУ).
Наиболее распространенным методом обработки цилиндрических наружных поверхностей является точение резцом
(резцами).
При установке и обработке длинных заготовок валов, осей, стержней и т. п. в качестве дополнительной опоры, повы-
шающей жесткость технологической системы, применяют люнеты (подвижные и неподвижные).
Для точения цилиндрических поверхностей и поверхностей, прилегающих к ним и ограничивающих их длину (торцы,
уступы, канавки, радиусы и т.п.), применяют проходные, подрезные (прямые и отогнутые), отрезные, канавочные и другие
резцы с напайными пластинами из быстрорежущей стали или твердых сплавов и композиционных материалов.
При токарной обработке различают:
а) черновое точение (или обдирочное) – с точностью обработки IТ13... IТ12 с шероховатостью поверхности до Rа = 6,3
мкм;
б) получистовое точение – IТ12...IТ11 и шероховатость до Rа = 1,6 мкм;
в) чистовое точение – IТ10...IТ8 и шероховатость до Rа = 0,4 мкм.
При черновом обтачивании, как и при любой черновой обработке снимают до 70 % припуска. При этом назначаются
максимально возможные глубина резания t и подача S.
На черновых операциях повышения производительности обработки добиваются увеличением глубины резания (умень-
шением числа рабочих ходов), а также подачи.
На чистовых операциях подача ограничивается заданной шероховатостью поверхности, поэтому сокращение основного
времени возможно за счет увеличения скорости резания. На универсальных токарно-карусельных станках обрабатывают
заготовки деталей типа тел вращения разнообразной формы диаметром до 10 000 мм.
Токарно-многорезцовые станки рассчитаны (как и револьверные) на повышение производительности труда путем со-
вмещения переходов операций и автоматического получения операционных размеров. Эти станки предназначены для обра-
ботки (в патроне или в центрах) заготовок деталей типа ступенчатых валов, блоков шестерен, валов-шестерен, фланцев;
шкивов и т.п. в условиях среднесерийного и крупносерийного производства.
Токарные многорезцовые станки и копировальные полуавтоматы имеют два суппорта, работают в полуавтоматическом
цикле. Они, как правило, одношпиндельные с горизонтальной и вертикальной компоновками. Обычно на многорезцовых
станках обрабатывают заготовки диаметром до 500 мм, длиной до 1500 мм.
Настройка резцов (рис. 16) производится так, чтобы обработка всех участков вала заканчивалась одновременно.
Основное время рассчитывают для резца, который обтачивает наиболее длинную поверхность (или в совокупности по
двум и более поверхностям, образующим общую длину обработки).
К методам чистовой обработки относятся: тонкое точение и различные методы шлифования. Они, как правило, позво-
ляют обеспечить требуемые точность размеров, формы, взаимного расположения и, в большинстве случаев, качество по-
верхностного слоя.
Тонкое точение применяется, главным образом, для отделки деталей из цветных металлов и сплавов (бронза, латунь,
алюминиевые сплавы и другие) и отчасти для деталей из чугуна и закаленных сталей (НRС 45...60). Объясняется это тем, что
шлифование цветных металлов и сплавов значительно труднее, чем стали и чугуна, вследствие быстрого засаливания кругов.
Кроме того, имеются некоторые детали, шлифование которых не допускается из-за возможного шаржирования поверхности.
Тонкое точение обеспечивает получение наружных цилиндрических поверхностей вращения правильной геометриче-
ской формы с точным пространственным расположением осей и является высокопроизводительным методом.
При тонком точении используются алмазные резцы или резцы, оснащенные твердым сплавом (ТЗОК4, синтетические
сверхтвердые материалы типа оксидная керамика ВОК60 и оксидно-нитридная керамика "кортинит" гексанит-Р, эльбор-Р).
Тонкое точение характеризуется незначительной глубиной резания (t = 0,05...0,2 мм), малыми подачами (S = 0,02...0,2
мм/об) и высокими скоростями резания (v = 120….1000 м/мин). Точность размеров IТ5...IТ6; Rа = 0,8...0,4 мкм.
Подготовка поверхности под тонкое точение сводится к чистовой обработке с точностью IТ8...IТ9. Весь припуск снима-
ется за один рабочий ход. Применяются станки особо высокой точности, жесткости и виброустойчивости. На этих станках
не следует выполнять другие операции.
Шлифование
Шлифование наружных поверхностей деталей типа тел вращения производят на круглошлифовальных, торцекруглош-
лифовальных станках, бесцентрово-шлифовальных полуавтоматах и автоматах как высокой, так и особо высокой точности.
Шлифование – основной метод чистовой обработки наружных цилиндрических поверхностей. Шейки валов шлифуют в
две операции: предварительное и чистовое шлифование. После чистового шлифования точность размера IТ6, а шерохова-
тость Rа = 1,6...0,4 мкм.
Как правило, все наружные цилиндрические поверхности с точностью выше IТ8 и шероховатостью Rа = 1,6...0,4 мкм
подвергают после чистового точения шлифованию.
При обработке на круглошлифовальных и торцекруглошлифовальных станках заготовки устанавливают в центрах, па-
троне, цанге или в специальном приспособлении.
Заготовке сообщается вращение с окружной скоростью v зг = 10...50 м/мин; она зависит от диаметра обработки заготов-
ки. Окружная скорость шлифовального круга (скорость резания) v = 30...60 м/с. Подача S и глубина резания t варьируются в
зависимости от способов шлифования. Различают следующие разновидности шлифования: продольное (с продольным дви-
жением подачи) и врезное (с поперечным движением подачи).
Поперечная подача на глубину шлифования осуществляется шлифовальным кругом в конце каждого двойного хода за-
готовки или круга и принимается в зависимости от материала, заготовки, круга и вида обработки S = 0,005…0,05 мм/об. В
конце обработки последние продольные проходы выполняют без поперечной подачи, так называемое выхаживание.
Шлифование с продольной подачей применяют при обработке цилиндрических заготовок значительной длины.
Врезное шлифование применяют для обработки поверхностей, длина которых не превышает ширину шлифовального
круга. Его преимущество – большая производительность и простота наладки, однако, оно уступает продольному шлифова-
нию по достигаемому качеству поверхности. Врезное шлифование широко применяют в массовом и крупносерийном произ-
водстве (рис. 17, б). Рекомендуемые скорости резания v = 50...60 м/с; радиальная (поперечная) подача при окончательном
шлифовании S = 0,001...0,005 мм/об.
Разновидностью шлифования с продольным движением подачи является глубинное шлифование. Оно характеризуется
большой глубиной резания (0,1...0,3 мм) и малой скоростью резания. При этом способе шлифования меньше, чем при врез-
ном, сказывается влияние погрешности формы исходной заготовки и колебания припуска при обработке. Поэтому глубинное
шлифование (рис. 17, б) применяют для обработки заготовок без предварительной лезвийной обработки и, как правило, сни-
мают припуск за один рабочий ход. Производительность труда повышается в 1,2 – 1,3 раза по сравнению с продольным
шлифованием. При значительном объеме производства применяют бесцентровое шлифование, которое более производи-
тельно, чем в центрах.
На бесцентрово-шлифовальных полуавтоматах и автоматах можно шлифовать заготовки деталей типа тел вращения с
цилиндрическими, коническими и фасонными поверхностями. Применяют два метода шлифования: проходное (способ про-
дольного движения подачи, рис. 13, а) и врезное (способ поперечного движения подачи, рис. 18, б). При проходном шлифо-
вании за несколько рабочих ходов можно достигнуть точности по 6-му квалитету и Rа = 0,2 мкм.
Врезным шлифованием (рис. 18, б) обрабатывают заготовки круглых деталей с уступами, а также заготовки, имеющие
форму конуса. При этом методе оси кругов параллельны или ведущий круг устанавливается под малым углом (α = 0,2...0,5°),
а осевому перемещению обрабатываемой заготовки препятствует установленный упор.
По аналогии с врезным шлифованием находит применение обработка не шлифовальными кругами, а шлифовальной
лентой, закрепляемой на ведущем и ведомом шкивах. Обрабатываемую заготовку также устанавливают на нож.
1.5 Методы повышения качества поверхностного слоя деталей
К методом повышения качества поверхности относятся различные методы упрочнения и отделочная обработка. Их ос-
новной задачей является обеспечение заданного качества поверхностного слоя, которое характеризуется его физико-
механическими свойствами и микрогеометрией.
Известно, что состояние поверхностного слоя валов и других деталей оказывает существенное влияние на эксплуатаци-
онные свойства машин. Специальной обработкой можно придать поверхностным слоям деталей машин особые физико-
механические свойства. Для этой цели в машиностроении применяют ряд методов. Все эти методы могут быть классифици-
рованы следующим образом:
− методы поверхностной термической обработки [обычная закалка, закалка токами высокой частоты (ТВЧ)];
− химико-термические методы (цементация, азотирование, планирование);
− диффузионная металлизация (диффузионное алитирование, хромирование, силицирование и др.);
− покрытие поверхностей твердыми сплавами и металлами (покрытие литыми и порошкообразными сплавами);
− металлизация поверхностей (распыление расплавленным металлом);
− поверхностно-пластическое деформирование.
Закалка поверхностная – нагревание электротоком или газовым пламенем поверхности изделия. Сердцевина изделия
после охлаждения остается незакаленной. Закалкой получается твердая износоустойчивая поверхность при сохранении прочной и
вязкой сердцевины. Кроме того, поверхностная закалка может осуществляться с помощью лазерного луча.
Цементация – насыщение поверхностного слоя стали углеродом при нагревании ее в твердом, газообразном или жид-
ком карбюризаторе, выдержка и последующее охлаждение. Детали после цементации подвергаются закалке для достижения
высокой твердости поверхностного слоя и сохранения пластичной сердцевины.
Азотирование – насыщение поверхностного слоя стали азотом при нагревании в газообразном аммиаке (температура
не ниже 450 °С), выдержка при этой температуре и последующее охлаждение. Повышается твердость, износоустойчивость и
антикоррозийные свойства.
Цианированне – одновременное насыщение поверхностного слоя стали углеродом и азотом. При этом повышаются
твердость, износостойкость.
Для придания стали специальных физических и химических свойств (жаростойкости, антикоррозийных свойств и др.)
применяют диффузионную металлизацию. Она заключается в нагревании стальной поверхности, контактирующей с метал-
лосодержащей средой, до высокой температуры, насыщении поверхности алюминием (алитирование), хромом (диффузион-
ное хромирование), кремнием (силицирование) и другими металлами, выдержке и последующем охлаждении.
Покрытие поверхностей твердыми сплавами и металлами, а также металлизацию (напыление) применяют для повы-
шения износостойкости поверхностей.
При использовании в качестве присадочного материала порошков возможны следующие методы напыления – плазмен-
ное напыление, с применением лазеров и др.
Поверхностно-пластическое деформирование (ППД) – один из наиболее простых и эффективных технологических
путей повышения работоспособности и надежности изделий машиностроения. В результате ППД повышаются твердость и
прочность поверхностного слоя, формируются благоприятные остаточные напряжения, уменьшается параметр шероховато-
сти Rа, увеличиваются радиусы закругления вершин, относительная опорная длина профиля и т.п.
Формирование поверхностного слоя с заданными свойствами должно обеспечиваться технологией упрочнения.
Основные способы поверхностного пластического деформирования, достигаемая точность и шероховатость поверх-
ностей показаны в табл. 7.
Наиболее широко применяют способы обкатывания и раскатывания шариковыми и роликовыми обкатниками наруж-
ных и внутренних цилиндрических, плоских и фасонных поверхностей. Цилиндрические наружные, внутренние, фасонные
поверхности обрабатываются, как правило, на токарных, револьверных, сверлильных и других станках; плоские поверхности
– на строгальных, фрезерных станках. Примеры обкатывания и раскатывания поверхностей роликами приведены на рис. 19.
Обычно этими способами обрабатывают достаточно жесткие детали из стали, чугуна и цветных сплавов.
звуковое упрочнение и др.
Отделочная обработка. На этапе отделочной обработки обеспечиваются повы-
шенные требования к шероховатости поверхности. При этом могут повышаться в не-
большой степени точность размеров и формы обрабатываемых поверхностей. К методам
отделочной обработки относятся доводка, притирка, суперфиниширование, полирование и
пр.
Абразивная доводка является окончательным методом обработки заготовок де-
талей типа тел вращения, обеспечивающим малые отклонения размеров, отклонение
формы обрабатываемых поверхностей и Rа = 0,16…0,01 мкм. Этот метод характеризу-
ется одновременным протеканием механических, химических и физико-химических
процессов. Доводку выполняют с помощью ручных притиров или на специальных дово-
дочных станках(рис. 22).
В единичном производстве, при ремонте притирку производят на токарном
станке притиром в виде втулки, сделанной по размеру притираемой детали, с одной
стороны втулка разрезана (рис. 22, а)
Втулку смазывают доводочной пастой или тонким слоем мелкого корундового
порошка.
Деталь при доводке смазывают жидким машинным маслом или керосином.
Припуск на доводку составляет 5...20 мкм на диаметр. Скорость вращения заго-
товки
v 32 = 10….20 м/мин.
В крупносерийном и массовом производстве процесс механизирован и иногда
называется лаппингование.
Притирка осуществляется между двумя чугунными (свинцовыми, медными)
притирами (рис. 22, б).
Диски вращаются в разные стороны. Детали закладываются в сепаратор, закреп-
ленный на кривошипе. Достижимая точность процесса – IТ6, Ra = 0,05...0,025 мкм.
Суперфиниширование – отделочная обработка различных поверхностей дета-
лей, в том числе цилиндрических, абразивными брусками (рис. 23). В результате су-
перфиниширования шероховатость поверхности снижается до Ra = 0,1...0,012 мкм,
увеличивается относительная опорная длина профиля поверхности с 20 до 90 %. Су-
щественного изменения размеров и макрогеометрии поверхности не наблюдается.
Обработка производится мелкозернистыми (зернистость не ниже 320) брусками с
добавлением смазочного вещества (смесь керосина с маслом) при небольшой скоро-
сти (до 2,5 м/с) и с весьма малыми давлениями инструмента на поверхность детали
(0,1...0,3 МПа – для заготовок деталей из стали; 0,1...0,2 МПа – для заготовок деталей
из чугуна и 0,05...0,1 МПа – для заготовок деталей из цветных металлов).
В простейших схемах обработки на различных станках общего назначения
осуществляются следующие движения: вращение заготовки (окружная скорость
0,05...2,5 м/с); возвратно-поступательное движение (колебание инструмента или заготовки – ход 2...6 мм, число двойных
ходов 200...1000 в 1 мин); перемещение инструмента вдоль поверхности заготовки. Толщина снимаемого слоя металла
0,005...0,02 мм.
Полирование предназначено для уменьшения параметров шероховатости поверхности без устранения отклонений раз-
меров и формы деталей. При окончательном полировании достигается (при малых давлениях резания 0,03...0,2 МПа) пара-
метр шероховатости – Ra = 0,1...0,012 мкм. Абразивными инструментами являются эластичные круги (войлок, ткань, кожа и
т.п.), покрытые полировальными пастами, шлифовальные шкурки и свободные абразивы (обработка мелких заготовок в ба-
рабанах и виброконтейнерах.
Сквозные шпоночные пазы валов можно обрабатывать на строгальных станках. Пазы на длинных валах, например, на
ходовом вале токарного станка, строгают на продольно-строгальном станке. Пазы на коротких валах строгают на поперечно-
строгальном станке – преимущественно в единичном и мелкосерийном производствах.
Рис. 26 Протягивание шпоночного паза в отверстии
Шпоночные пазы под сегментные шпонки изготовляются фрезерованием с помощью дисковых фрез (см. рис. 25, г).
Шпоночные пазы в отверстиях втулок зубчатых колес, шкивов и других деталей, надевающихся на вал со шпонкой, об-
рабатываются в единичном и мелкосерийном производствах на долбежных станках, а в крупносерийном и массовом – на
протяжных станках. На рис. 26 показано протягивание шпоночного паза в заготовке зубчатого колеса на горизонтально-
протяжном станке. Заготовка 1 насаживается на направляющий палец 4, внутри которого имеется паз для направления про-
тяжки 2. Когда канавка протягивается за 2-3 рабочих хода, то под протяжку помещают подкладку 3.
Шлицевые соединения широко применяются в машиностроении (станкостроении, автомобиле- и тракторостроении и
других отраслях) для неподвижных и подвижных посадок.
Различают шлицевые соединения прямоугольного, эвольвентного и треугольного профиля.
В наиболее часто используемых шлицевых соединениях прямоугольного профиля сопряженные детали центрируются
тремя способами (рис. 27):
− центрированием втулки (или зубчатого колеса) по наружному диаметру шлицевых выступов вала по (D);
− центрированием втулки (или зубчатого колеса) по внутреннему диаметру (шлицев вала (т.е. по дну впадины) по (d);
− центрированием втулки (или зубчатого колеса) по боковым сторонам (В) шлицев.
Центрирование по D наиболее технологично, но его использование ограничивается в основном неподвижными шлице-
выми соединениями, не требующими повышенной твердости. Центрирование по d применяется в тех случаях, когда элемен-
ты шлицевого соединения используются для подвижных сопряжений, подвергнутых закалке.
Рис. 27 Виды центрирования шлицевых соединений
Центрирование по d применимо в случае передачи больших крутящих моментов с реверсированием вращения.
Технологический процесс изготовления шлицев валов зависит от того, какой принят способ центрирования вала и втул-
ки, т.е. термообрабатываются или нет поверхности шлицев.
Приведем в качестве примера маршруты обработки шлицев на валах, соответственно не подвергаемых и подвергаемых
термообработке:
− черновая токарная обработка, чистовая токарная обработка и шлифование цилиндрических поверхностей под наре-
зание шлицев, нарезание шлицев, снятие заусенцев и промывка;
− черновая токарная обработка, чистовая токарная обработка, нарезание шлицев с припуском под шлифование, фрезе-
рование канавок для выхода круга при шлифовании центрирующей поверхности внутреннего диаметра (если на первой опе-
рации применяется фреза без усиков), термическая обработка, шлифование поверхностей шлицев, снятие заусенцев и про-
мывка.
Шлицы на валах и других деталях изготовляются различными способами, к числу которых относятся: фрезерование,
строгание (шлицестрогание), протягивание (шлицепротягивание), накатывание (шлиценакатывание), шлифованием.
Фрезерование шлицев на валах небольших диаметров (до 100 мм) обычно фрезеруют за один рабочий ход, больших
диаметров – за два рабочих хода. Черновое фрезерование шлицев, в особенности больших диаметров, иногда производится
фрезами на горизонтально-фрезерных станках, имеющих делительные механизмы (рис. 28, а, б, в).
Фрезеровать шлицы можно способом, изображенным на рис. 28, в, позволяющим применять более дешевые фрезы, чем
фреза, изображенная на рис. 28, а.
Более производительным способом является одновременное фрезерование двух шлицевых канавок двумя дисковыми
фрезами специального профиля (рис. 28, в).
Чистовое фрезерование шлицев дисковыми фрезами производится только в случае отсутствия специального станка или
инструмента, так как оно не дает достаточной точности по шагу и ширине шлицев.
Более точное фрезерование шлицев производится методом обкатки при помощи шлицевой червячной фрезы (рис. 28, г).
Фреза, помимо вращательного движения, имеет продольное перемещение вдоль оси нарезаемого вала. Этот способ является
наиболее точным и наиболее производительным.
l Рис. 28 Способы фрезерования шлицев
Окончательная обработка шлицев по методу обкатки производится чистовым фрезерованием червячными шлицевыми
фрезами высокого класса точности (АА и А).
При центрировании втулки (или зубчатого колеса) по внутреннему диаметру шлицев вала как червячная, так и дисковая
фреза должна иметь "усики", вырезающие канавки у основания шлица, чтобы не было заедания во внутренних углах; эти
канавки необходимы также при шлифовании по боковым сторонам и внутреннему диаметру.
Шлицестрогание реализуется, как правило, на специальных станках-полуавтоматах, которые могут работать как от-
дельно, так и будучи встроенными в автоматическую линию. Этим методом чаще всего обрабатываются сквозные шлицы
или шлицы, у которых предусмотрен выход для резцов.
Шлицестрогание обеспечивает шероховатость поверхности Rа = 3,2...0,8 мкм.
Шлицепротягивание обеспечивает шероховатость поверхности Rа = 1,6...0,8 мкм.
Шлифование шлицев осуществляется следующим образом.
При центрировании шлицевых валов по наружному диаметру шлифуют только наружную цилиндрическую поверх-
ность вала на обычных круглошлифовальных станках; шлифование впадины (т.е. по внутреннему диаметру шлицев вала) и
боковых сторон шлицев не осуществляется.
При центрировании шлицевых валов по внутреннему диаметру шлицев фрезерование последних дает точность обра-
ботки по внутреннему диаметру до 0,05...0,06 мм, что не всегда является достаточным для точной посадки.
Если шлицевые валы после чернового фрезерования прошли термическую обработку в виде улучшения или закалки, то
после этого они не могут быть профрезерованы начисто; их необходимо шлифовать по поверхностям впадины (т.е. по внут-
реннему диаметру) и боковых сторон шлицев. Наиболее производителен способ шлифования фасонным кругом (рис. 29), но
при таком способе шлифовальный круг изнашивается неравномерно ввиду неодинаковой толщины снимаемого слоя у боко-
вых сторон и впадины вала, поэтому требуется частая правка круга. Несмотря на это, данный способ широко распространен
в машиностроении.
Шлифовать шлицы можно в две отдельные операции (рис. 29, б); в первой шлифуют только впадины (по внутреннему
диаметру), а во второй – боковые стороны шлицев. Для уменьшения износа шлифовального круга после каждого хода стола
вал поворачивается, и, таким образом, шлифовальной круг обрабатывает впадины постепенно, одну за другой.
Для объединения двух операций шлифования в одну применяются станки, на которых шлицы шлифуются одновремен-
но тремя кругами: один шлифует впадину, а два других – боковые поверхности шлицев (рис. 29, в).
В машиностроительном производстве применяют цилиндрические резьбы – крепежные и ходовые, а также конические
резьбы.
в – тремя кругами
Основной крепежной резьбой является метрическая резьба треугольного профиля с углом профиля 60°.
Ходовые резьбы бывают с прямоугольным и трапецеидальным профилем; последние бывают однозаходные и многоза-
ходные.
Резьба может быть наружная (на наружной поверхности детали) и внутренняя (на внутренней поверхности детали).
Наружную резьбу можно изготовлять различными инструментами: резцами, гребенками, плашками, самораскрываю-
щимися резьбонарезными головками, дисковыми и групповыми фрезами, шлифовальными кругами, накатным инструмен-
том.
Для изготовления внутренней резьбы применяют: резцы, метчики, раздвижные метчики, групповые фрезы, накатные
ролики.
Тот или иной метод нарезания резьбы применяется в зависимости от профиля резьбы, характера и типа материала изде-
лия, объема производственной программы и требуемой точности.
Основные способы формообразования резьбовых поверхностей с указанием границ степеней точности резьбы и пара-
метров шероховатости приведены в табл. 8.
Нарезание резьб осуществляется на резьбонарезных и резьбофрезерных станках и полуавтоматах, гайконарезных авто-
матах, резьбонакатных, резьбошлифовальных, токарных и других станках.
Нарезание резьбы резцами и резьбовыми гребенками. Наружную и внутреннюю резьбы можно обработать на токар-
ных станках. Это малопроизводительный процесс, так как обработка осуществляется за несколько рабочих ходов и требует
высокой квалификации рабочего. Достоинством метода является универсальность оборудования, инструмента и возмож-
ность получить резьбу высокой точности. На токарных станках нарезают точные резьбы на ответственных деталях, а также
нестандартные резьбы и резьбы большого диаметра. Для повышения точности резьбы осуществляют как черновые, так и
чистовые рабочие ходы разными резцами. Различают два способа нарезания треугольной резьбы: 1) радиальное движение
подачи; 2) движение подачи вдоль одной из сторон профиля.
б – расположение зубьев резьбовой гребенки; в – набором резцов
Для скоростного нарезания резьбы применяют резцы, оснащенные твердым сплавом, а также наборы резцов (рис. 30).
Гребенки, подобно резцам, бывают плоские, призматические и круглые и отличаются от резцов тем, что режут одно-
временно несколькими режущими кромками. Для разделения работы резания концы зубьев гребенки стачиваются от одного
края гребенки к другому, так что глубина резания постепенно увеличивается.
г – с трехрезцовой головкой; д – трехрезцовая пластина
Токарные станки применяются для нарезания резьбы преимущественно для:
− нарезания резьбы на поверхностях, предварительно обработанных на токарном же станке, благодаря чему обеспечи-
вается правильное положение резьб относительно других поверхностей;
− нарезания очень точных длинных винтов (в этом случае токарный станок, работающий одним резцом, имеет пре-
имущество перед всеми другими методами, в том числе и перед фрезерованием;
− при выполнении работ, подходящих для резьбофрезерного станка, когда его нет или объем партии мал;
− нарезания резьб большого диаметра, нестандартного профиля или шага, а также вообще во всех случаях, когда при-
обретение подходящих плашек и метчиков не оправдывается объемом производства;
− нарезания прямоугольных резьб, чистовое фрезерование которых невозможно, а применение плашек и метчиков хо-
тя и возможно, но затруднительно, особенно при обработке крупных заготовок.
Резьбу после нарезания резцом иногда калибруют точными плашками (часто вручную).
Таким образом, нарезание резьбы на токарном станке применяется преимущественно в единичном и мелкосерийном
производствах, а в крупносерийном и массовом производствах – главным образом, для нарезания длинных или точных
резьб.
В крупносерийном и массовом производствах используется нарезание резьбы вращающимися резцами так называе-
мым вихревым методом. При этом заготовка закрепляется в центрах токарно-винторезного станка или в патроне. В про-
цессе работы она медленно вращается. В специальной головке, установленной на суппорте станка, закрепляется резец. Го-
ловка, вращающаяся с большой скоростью от специального привода, расположена эксцентрично относительно оси наре-
заемой резьбы. Таким образом, при вращении головки, резец, закрепленный в ней, описывает окружность, диаметр кото-
рой больше наружного диаметра резьбы .
Нарезание резьбы метчиками, плашками и самораскрывающимися резьбона-
резными головками производится на различных станках.
Внутренние резьбы нарезают обычно машинными метчиками на резьбона-
резных, сверлильных, револьверных, а также на агрегатных станках, полуавто-
матах и автоматах в зависимости от масштаба производства.
В массовом и крупносерийном производстве получили широкое распростра-
нение метчики сборной конструкции (резьбонарезные головки).
Основной недостаток всех типов плашек – это необходимость свинчивания
их по окончанию резания, что снижает производительность и несколько ухудшает качество резьбы.
Плашками нарезают резьбу как вручную, так и на различных станках токарной, сверлильной, резьбонарезной групп.
Круглые плашки (рис. 33, а) устанавливают на станках в специальных патронах и закрепляют тремя-четырьмя винтами. На-
резание плашками – малопроизводительный процесс.
Фрезерование резьбы широко распространено в серийном и массовом производствах и применяется для нарезания на-
ружных и внутренних резьб на резьбофрезерных станках (рис. 34). Оно осуществляется двумя основными способами: диско-
вой фрезой (рис. 34, а) и групповой (гребенчатой) фрезой (рис. 34, б).
Нарезание дисковой фрезой применяют при нарезании резьб с большим шагом (Р) и круглым профилем и главным об-
разом для предварительного нарезания трапецеидальных резьб за один, два или три рабочих хода. При нарезании фреза вра-
щается и совершает поступательное движение вдоль оси заготовки, причем перемещение за один оборот заготовки должно
точно соответствовать шагу резьбы.
Гребенчатая резьбовая фреза представляет собой набор нескольких дисковых резьбовых фрез. Полное нарезание проис-
ходит за 1,2 оборота заготовки (0,2 оборота необходимы для полного врезания и перекрытия места врезания).
Фрезерование дисковой фрезой часто применяют как черновую обработку перед нарезанием резьбы резцом.
Фрезерование гребенчатой фрезой – применяется для получения коротких резьб с мелким шагом. Длина фрезы обычно
принимается на 2...5 мм больше длины фрезеруемой детали. Групповая фреза устанавливается параллельно оси детали, а не
под углом, как дисковая фреза. Нарезание резьбы с большим углом подъема гребенчатой фрезой затруднительно.
Фрезерование резьбы является одним из наиболее производительных методов обработки резьбы.
Шлифование резьб выполняют чаще всего после термической обработки заготовок. Резьбошлифование может быть на-
ружным и внутренним, осуществляется на различных резьбошлифовальных станках. Существуют следующие способы шли-
фования резьбы: однопрофильным кругом; многопрофильным кругом с продольным движением подачи; врезное; широким
многопрофильным кругом.
2 ТЕХНОЛОГИЯ ИЗГОТОВЛЕНИЯ ВТУЛОК
2.1 Характеристика втулок
К деталям класса втулок относятся втулки, гильзы, стаканы, вкладыши, т.е. детали, образованные наружными и внут-
ренними поверхностями вращения, имеющие общую прямолинейную ось.
Некоторые основные виды подшипниковых втулок, представленные на рис. 37, служат как опоры вращающихся валов.
Наиболее часто применяют втулки с L/D ≥ 3.
Технологические задачи. Отличительной технологической задачей является обеспечение концентричности наружных
поверхностей с отверстием и перпендикулярности торцов к оси отверстия.
Точность размеров. Диаметры наружных поверхностей выполняют по h6, h7; отверстия по Н7, реже по Н8, для ответст-
венных сопряжении по Н6.
Точность формы. В большинстве случаев особые требования к точности формы поверхностей не предъявляются, т.е.
погрешность формы не должна превышать определенной части поля допуска на размер.
Точность взаимного расположения:
− концентричность наружных поверхностей относительно внутренних поверхностей 0,015...0,075 мм;
− разностенность не более 0,03...0,15 мм;
− перпендикулярность торцовых поверхностей к оси отверстия 0,2 мм на радиусе 100 мм, при осевой загрузке на тор-
цы отклонения от перпендикулярности не должны превышать 0,02...0,03 мм.
Качество поверхностного слоя. Шероховатость внутренних и наружных поверхностей вращения соответствует Ra
=1,6...3,2 мкм, торцов Ra = 1,6...6,3 мкм, а при осевой нагрузке Ra = 1,6...3,2 мкм. Для увеличения срока службы твердость
исполнительных поверхностей втулок выполняется НRС 40...60.
В качестве материалов для втулок служат: сталь, латунь, бронза, серый и ковкий антифрикционный чугун, специальные
сплавы, металлокерамика, пластмассы.
Заготовками для втулок с диаметром отверстия до 20 мм служат калиброванные или горячекатаные прутки, а также ли-
тые стержни. При диаметре отверстия больше 20 мм применяются цельнотянутые трубы или полые заготовки, отлитые в
песчаные или металлические формы, используют также центробежное литье и литье под давлением. Заготовкой для рас-
сматриваемой детали является штамповка, полученная на горизонтально-ковочной машине. Задача обеспечения концен-
тричности наружных поверхностей относительно отверстия и перпендикулярности торцовых поверхностей к оси отверстия
может быть решена обработкой:
− наружных поверхностей, отверстий и торцов за один установ;
− всех поверхностей за два установа или за две операции с базированием при окончательной обработке по наружной
поверхности (обработка от вала);
− всех поверхностей за два установа или за две операции с базированием при окончательной обработке наружной по-
верхности по отверстию (обработка от отверстия).
При обработке за один установ рекомендуется следующий технологический маршрут обработки втулки:
− подрезка торца у прутка, подача прутка до упора, зацентровка торца под сверление, сверление отверстия и обтачи-
вание наружной поверхности, растачивание или зенкерование отверстия и обтачивание наружной поверхности со снятием
фасок на свободном торце, предварительное развертывание, окончательное развертывание, отрезка. Эта первая операция
выполняется на токарно-револьверном станке, одношпиндельном или многошпиндельном токарном автомате;
− снятие фасок с противоположного торца втулки на вертикально-сверлильном или токарном станке;
− сверление смазочного отверстия;
− нарезание смазочных канавок на специальном станке. При обработке втулки из трубы вместо сверления производят
зенкерование или растачивание отверстия, далее технологический маршрут сохраняется.
При обработке втулки с базированием по внутренней поверхности рекомендуется следующий технологический маршрут об-
работки втулки: − зенкерование отверстия втулки и снятие фаски в отверстии на вертикально-сверлильном станке (технологическая
база – наружная поверхность);
− протягивание отверстия на горизонтально-протяжном станке со сферической самоустанавливающейся шайбой, ко-
торую применяют, потому что торец не обработан;
− предварительное обтачивание наружной поверхности (в зависимости от точности заготовки), подрезка торцов и сня-
тие наружных (а часто и внутренних фасок на токарно-многорезцовом полуавтомате). Базирование осуществляется по внут-
ренней поверхности на разжимную оправку;
− чистовое обтачивание наружной поверхности, чистовая подрезка торца.
При выборе метода базирования следует отдавать предпочтение базированию по отверстию, которое имеет ряд пре-
имуществ:
− при обработке на жесткой или разжимной оправке погрешность установки отсутствует или значительно меньше, чем
при обработке в патроне с креплением заготовки по наружной поверхности;
− более простое, точное и дешевое центрирующее устройство, чем патрон;
− при использовании оправки может быть достигнута высокая степень концентрации обработки.
2.2 Методы обработки внутренних цилиндрических поверхностей
Внутренние цилиндрические, поверхности (отверстия) встречаются у большинства деталей классов 71...76 как тел вра-
щения, так и не тел вращения.
Отверстия в заготовительных цехах получают достаточно просто, начиная с диаметра 25...40 мм.
Обработка отверстий в деталях различных типов производится путем сверления, зенкерования, фрезерования на стан-
ках с ЧПУ, растачивания резцами, развертывания, шлифования (внутреннего), протягивания, хонингования, раскатывания
шариками и роликами, продавливания, притирки, полирования, суперфиниширования.
Обработка отверстий со снятием стружки производится лезвийным и абразивным инструментом.
К лезвийным инструментам относятся: сверла, зенкеры, развертки, расточные резцы и протяжки. Разновидности и ха-
рактеристики этих инструментов приведены в справочниках [1, 2].
Обработку отверстий лезвийным инструментом производят на станках следующих групп: сверлильной (вертикально-
сверлильные, радиально-сверлильные); расточной (горизонтально-расточные, горизонтальные и вертикальные отделочно-
расточные координатно-расточные); протяжной группы (горизонтальные и вертикальные полуавтоматы), как обычного ис-
полнения, так и с ЧПУ.
Кроме того, отверстия обрабатываются практически на всех станках, полуавтоматах и автоматах токарной группы.
Сверлением получают отверстия в сплошном материале (рис. 38). Для неглубоких отверстий используются стандарт-
ные сверла диаметром 0,30...80 мм.
д – ружейным с внутренним отводом СОЖ
Существуют два метода сверления:
1) вращается сверло (станки сверлильно-расточных групп);
2) вращается заготовка (станки токарной группы).
Обработку отверстий диаметром до 25...40 мм осуществляют спиральными сверлами за один переход (рис. 38, а), при
обработке отверстий больших диаметров (до 80 мм) – за два и более перехода сверлением и рассверливанием или другими
методами. Для сверления отверстий диаметром свыше 80 мм применяют сверла или сверлильные головки специальных кон-
струкций.
На многих корпусных деталях, фланцах, крышках и т.п. имеются небольшие отверстия (для крепежных болтов, шпилек
и т.п.), точность и шероховатость которых определяется точностью, достигаемой сверлением. Такие отверстия обрабатыва-
ют на станках с применением кондукторов. При этом достигаемая точность диаметральных размеров – IT11...IТ10.
При обработке глубоких отверстий (L/D > 10) трудно обеспечить направленность оси отверстия относительно ее внут-
ренней цилиндрической поверхности. Чем больше длина отверстия, тем больше увод инструмента. Для борьбы с уводом
сверла или искривлением оси отверстия применяются следующие способы:
− применение малых подач, тщательная заточка сверла;
− применение предварительного засверливания (зацентровки);
− сверление с направлением спирального сверла с помощью кондукторной втулки;
− сверление вращающейся заготовки при невращающемся или вращающемся сверле. Это самый радикальный способ
устранения увода сверла, так как создаются условия для самоцентрирования сверла;
− сверление специальными сверлами при вращающейся или неподвижной заготовке.
К специальным сверлам относятся:
− полукруглые (рис. 38, б) – разновидность ружейных сверл одностороннего резания, которые применяются для обра-
ботки заготовок из материалов, дающих хрупкую стружку (латунь, бронза, чугун);
− ружейные – одностороннего резания с внешним отводом СОЖ (рис. 38, в) и внутренним отводом (эжекторные) (рис.
38, д) с пластинами из твердого сплава (припаянными или неперетачиваемыми с механическим креплением), предназ-
наченные для высокопроизводительного сверления;
− трепанирующие (кольцевые) сверла (рис. 38, г) для сверления отверстий диаметром 80 мм и более, длиной до 50 мм;
Они вырезают в сплошном металле кольцевую поверхность, а остающуюся после такого сверления внутреннюю часть в
форме цилиндра можно использовать как заготовку для изготовления других деталей.
Зенкерование отверстий – предварительная обработка литых, штампованных или просверленных отверстий под по-
следующее развертывание, растачивание или протягивание. При обработке отверстий по 13...11-му квалитету зенкерование
может быть окончательной операцией. Зенкерованием обрабатывают цилиндрические углубления (под головки винтов, гнезд
под клапаны и др.), торцовые и другие поверхности.
Режущим инструментом при зенкеровании является зенкер. Зенкеры изготовляют цельными с числом зубьев 3...8 и бо-
лее, диаметром 3...40 мм; насадными диаметром 32...100 мм и сборными регулируемыми диаметром 40...120 мм.
Зенкерование является производительным методом: повышает точность предварительно обработанных отверстий, час-
тично исправляет искривление оси после сверления. Для повышения точности обработки используют приспособления с кон-
дукторными втулками. Зенкерованием обрабатывают сквозные и глухие отверстия.
Зенкеры исправляют, но не устраняют полностью оси отверстия, достигаемая шероховатость Rа = 12,5...6,3 мкм.
Развертывание отверстий – чистовая обработка отверстий с точностью до 7-го квалитета. Развертыванием обрабаты-
вают отверстия тех же диаметров, что и при зенкеровании. Развертки рассчитаны на снятие малого припуска. Они отличают-
ся от зенкеров большим числом (6...14) зубьев. Развертыванием достигается высокая точность диаметральных размеров и
формы, а также малая шероховатость поверхности. Следует отметить, что обработанное отверстие получается несколько
большего диаметра, чем диаметр самой развертки. Такая разбивка может составлять 0,005...0,08 мм.
Для получения отверстий 7 квалитета применяют двукратное развертывание; IТ6 – трехкратное, под окончательное раз-
вертывание припуск оставляют 0,05 мм и менее.
Для разверток из твердых сплавов рекомендуются следующие режимы: для чугуна – V = 7...20 м/мин; S = 2...7 мм/об; t =
0,15 мм, в качестве СОЖ используется керосин (достигаемая точность размеров IТ6; шероховатость Ra = 1,6 мкм); для стали
– V = 4…10 м/мин; S = 2...4 мм/об; t = 0,1…0,15 мм (при использовании СОЖ по точности достигаются те же результаты, что
и при обработке чугунных заготовок).
Развертки обычно не применяют для развертывания больших по диаметру, коротких, глухих и прерывистых отверстий.
В настоящее время имеется целый ряд приемов и методов, повышающих производительность труда при обработке от-
верстий:
− применение комбинированных режущих инструментов (рис. 39);
− применение специальных приспособлений (кондукторов) и многошпиндельных
сверлильных головок на сверлильных, расточных и агрегатных станках.
Фаски в отверстиях обрабатываются зенковками (рис. 40, а). Цилиндрические уг-
лубления и торцевые поверхности под головки болтов и гаек выполняются на сверлиль-
ных станках цековками в виде насадных головок с четырьмя зубьями (рис. 40, б) или в
виде специальных пластин (рис. 40, в) с направляющей цапфой, служащей для получения
соосности с обработанными отверстиями.
Растачивание основных отверстий (определяющих конструкцию детали) произво-
дится на: горизонтально-расточных, координатно-расточных, радиально-сверлильных,
карусельных и агрегатных станках, многоцелевых обрабатывающих центрах, а также в
некоторых случаях и на токарных станках.
Существуют два основных способа растачивания: растачивание, при котором вращается заготовка (на станках токарной
группы), и растачивание, при котором вращается инструмент (на станках расточной группы)
Типичными для токарных станков операциями являются растачивание одиночного отверстия и растачивание соосных
отверстий универсальным методом и резцом (резцами).
Типичными для расточных станков операциями являются растачивание одиночного отверстия, соосных отверстий и
растачивание отверстий с параллельными осями.
Протягивание отверстий применяют в массовом, крупносерийном и серийном производствах. Протягивание является
одним из прогрессивных способов обработки металлов резанием, как в отношении производительности, так и достигаемых
точности и шероховатости. По сравнению с развертыванием, например, протягивание производительнее в 8 – 9 раз и выше.
Протягивание осуществляется многолезвийным инструментом протяжкой, которая протягивается через обрабатываемое
отверстие (рис. 41). Внутренним протягиванием обрабатывают различные отверстия: круглые (цилиндрические), щлицевые,
многогранные и др.
заготовка; 4 – протяжка
При протягивании на протяжных станках заготовку устанавливают на жесткой (рис. 41, а) или шаровой опоре (рис. 41,
б), если торец детали не перпендикулярен оси отверстия.
Для протягивания применяют горизонтальные и вертикальные протяжные станки-полуавтоматы.
Горизонтальные протяжные полуавтоматы применяются для внутреннего протягивания. Вертикальные полуавтоматы
используют как для внутреннего, так и наружного протягивания; они занимают в 2 – 3 раза меньше площади, чем горизон-
тальные.
Припуск под протягивание при обработке цилиндрических отверстий составляет 0,5…1,5 мм на диаметр отверстия.
Прошиванием называют аналогичную протягиванию обработку более коротким инструментом – прошивкой. При прошива-
нии инструмент испытывает напряжения сжатия, а при протягивании – растяжения, поэтому прошивку выполняют относи-
тельно небольшой длины (250...400 мм).
Для обработки отверстий применяют внутреннее шлифование, хонингование, притирку.
Внутреннее шлифование применяют для окончательной обработки отверстий скаленных деталей или в тех случаях, ко-
гда невозможно применить другие, более производительные методы обработки. Оно осуществляется на внутришлифоваль-
ных станках и бесцентрово-внутришлифовальных автоматах. Отверстия обрабатывают на проход и методом врезания (ко-
роткие отверстия).
Внутреннее шлифование имеет свои технологические особенности. Диаметр абразивного круга выбирают наибольший,
допустимый диаметром обрабатываемого отверстия d кр = (0,8…0,9) d отв . Высоту (ширину) круга принимают в зависимости
от длины обрабатываемого отверстия l кр = 0,8 l дет .
Чистовым шлифованием обеспечивается точность размеров отверстий IT6...IT7; шероховатость поверхности Ra =
0,8...3,2 мкм. При длительном выхаживании достигается Ra = 0,4 мкм.
Для внутреннего шлифования рекомендуются следующие режимы:
− для чугуна – V кр = 20...30 м/сек;
− для стали – V кр = 30...45 м/сек;
− V заг = (0,015…0,03) V кр ;
− S пр = (0,2...0,3) b – чистовое шлифование;
− S пр = (0,6...0,8) b – черновое шлифование.
Припуски на шлифование отверстий зависят от диаметра отверстия и его длины и рекомендуются 0,07…0,25 мм для
диаметра до 30 мм; 0,18…0,75 для диаметра до 250 мм. Наиболее распространенным методом является шлифование на про-
ход с продольным движением подачи. Это шлифование обеспечивает точность размеров, формы и, при соответствующем
базировании, точность взаимного расположения обработанных поверхностей.
Различают три основных вида внутреннего шлифования (рис. 42): во вращающейся заготовке; в неподвижной заготовке
(планетарное); бесцентровое.
Шлифование отверстия во вращающейся заготовке (рис. 42, а) осуществляется так же, как шлифование наружных по-
верхностей тел вращения.
Для шлифования торца детали после шлифования отверстия в ней целесообразно пользоваться станками, имеющими
помимо круга для шлифования отверстия круг для шлифования торца . Это обеспечивает соблюдение строгой пер-
пендикулярности торцовой поверхности и оси отверстия за счет обработки за один установ.
Шлифование отверстия в неподвижной заготовке применяют при обработке отверстий в крупных заготовках, которые
трудно вращать .
Хонингование является одним из методов отделочной обработки отверстий. Процесс осуществляется с помощью хо-
нинговальных головок (хонов) со вставными абразивными брусками. Хонингование выполняется на специальных станках,
которые подразделяют на две группы: вертикально-хонинговальные и горизонтально-хонинговальные.
Хонинговальная головка совершает совмещенное движение: вращательное и возвратно-поступательное при постоянном
давлении абразивных брусков на обрабатываемую поверхность в среде смазочно-охлаждающей жидкости .
заготовки; l п – перебег брусков; l х – длина рабочего хода брусков
В процессе хонингования абразивные бруски удаляют слой металла толщиной 0,3...0,5 мкм за один двойной рабочий
ход при общем припуске 0,01...0,07 мм для стали и 0,02...0,20 мм для чугуна. При этом снимаются как микронеровности, ос-
тавшиеся после предыдущей операции, так и некоторая часть основного металла, что позволяет устранять конусообразность,
овальность, бочкообразность.
Предварительная обработка отверстий под хонингование может быть выполнена растачиванием, зенкерованием, раз-
вертыванием или шлифованием и должна обеспечивать точность обработки не ниже, чем по 7...8-му квалитету и Rа =
6,3...3,2 мкм.
Притирка (доводка внутренних поверхностей). Этот метод аналогичен притирке наружных цилиндрических поверхно-
стей. Притирка и хонингование, в отличие от внутреннего шлифования, не исправляют погрешностей расположения, так как
обрабатывающий инструмент базируется по обрабатываемой поверхности.
К деталям класса "диски" относятся детали, образованные наружными и внутренними поверхностями вращения,
имеющими одну общую прямолинейную ось при отношении длины цилиндрической части к наружному диаметру менее 0,5.
Например: шкивы, фланцы, крышки подшипников, кольца, поршни гидро- и пневмоприводов и т.п. Технологические задачи
– аналогичные классу втулок: достижение концентричности внутренних и наружных цилиндрических поверхностей и пер-
пендикулярность торцов к оси детали.
Дата добавления: 2022-01-22; просмотров: 39; Мы поможем в написании вашей работы! |
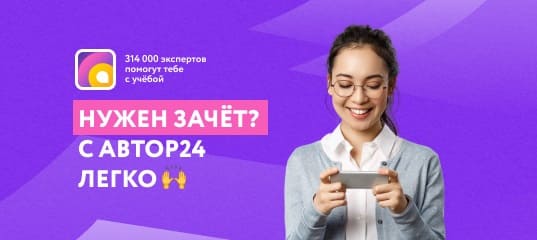
Мы поможем в написании ваших работ!