Технология и механизация животноводства
Министерство сельского хозяйства Российской Федерации Федеральное государственное бюджетное образовательное учреждение высшего образования
«Самарская государственная сельскохозяйственная академия»
Технология и механизация животноводства
Учебное пособие
Кинель 2018
ББК П072.0я73
УДК 631.171:636.0851(07)
Т38
Рецензенты:
канд. техн. наук, доцент, зав. кафедрой «Механизация технологических процессов в АПК» ФГБОУ ВО Пензенского ГАУ
А. В. Яшин;
канд. техн. наук, проф. кафедры «Тракторы и автомобили» ФГБОУ ВО Самарской ГСХА
Г. И. Болдашев
Авторский коллектив:
С. В. Денисов, А. С. Грецов, А. Л. Мишанин, Е. В. Янзина, Ю. А. Киров, С. А. Васильев
Т38 Технология и механизация животноводства : учебное посо- бие / С. В. Денисов, А. С. Грецов, А. Л. Мишанин [и др.]. – Кинель : РИО Самарской ГСХА, 2018. – 165 с.
ISBN 978-5-88575-552-8
Изложены основные требования к механизации поточно- технологических линий в животноводстве, освещены требования к машинам и оборудованию, применяемому в животноводстве, дан анализ конструкций и рабочих процессов этих машин.
Учебное пособие предназначено для бакалавров, обучающих- ся по направлениям подготовки 35.03.06 Агроинженерия,
44.03.04 Профессиональное обучение, 35.03.07 Технология произ- водства и переработки сельскохозяйственной продукции;
36.03.02 Зоотехния, а также для магистрантов, аспирантов и ра- ботников сельскохозяйственных предприятий.
|
|
ББК П072.0я73 УДК 631.171:636.0851(07)
ISBN 978-5-88575-552-8
© ФГБОУ ВО Самарская ГСХА, 2018
|
![]() |
ПРЕДИСЛОВИЕ
Государственной программой развития сельского хозяйства и регулирования рынков сельскохозяйственной продукции, сырья и продовольствия на 2013-2020 годы предусматривается увеличе- ние производства скота и птицы на убой до 14,07 млн т в живой
массе, потребления мяса на душу населения с 69,1 до 73,2 кг, про- изводства молока – до 38,2 млн т, экспорта мяса птицы – до
400 тыс. т, свинины – до 200 тыс. т, потребление молока и молоч- ных продуктов на душу населения(в пересчете на молоко)
с 247 до 259 кг. Достижение этих показателей возможно после осуществления мероприятий, направленных на техническую
и технологическую модернизацию сельского хозяйства.
Для свободного ориентирования во всем многообразии про- дукции, представленной на современном рынке, обучающиеся должны владеть знаниями по устройству и принципу действия как машин и оборудования, применяемого в животноводстве, в целом, так и отдельных их узлов и агрегатов. В связи с этим в пособии представлена информация по технологиям, применяемым в жи- вотноводстве, устройству и принципу действия машин и оборудо- вания, применяемого в процессе приготовления кормов.
|
|
Цель пособия – формирование у обучающихся навыков реше- ния профессиональных задач по эффективному использованию сельскохозяйственной техники и технологического оборудования для производства и первичной переработки продукции животно- водства на предприятиях различных организационно-правовых форм, а также по обеспечению высокой работоспособности и со- хранности машин, механизмов и технологического оборудования.
Представленный в пособии материал в соответствии с феде- ральным государственным образовательным стандартом высшего образования и требованиями к результатам освоения основной профессиональной образовательной программы по направлениям подготовки 35.03.06 Агроинженерия, 44.03.04 Профессиональное обучение, 35.03.07 Технология производства и переработки сель- скохозяйственной продукции; 36.03.02 Зоотехния способствует формированию профессиональных компетенций.
1. Животноводческие фермы и комплексы
|
|
Известно, что разнообразные виды животноводческой про- дукции получают на животноводческих фермах и комплексах.
Животноводческая ферма – это совокупность зданий и со- оружений основного и вспомогательного назначения, расположен- ных на одной территории и объединенных единым процессом производства конечной или промежуточной животноводческой продукции.
Животноводческий комплекс – это сельскохозяйственное предприятие, предназначенное для равномерного круглогодового производства высококачественной животноводческой продукции на основе применения промышленной технологии, научной орга- низации труда, высокого уровня концентрации и специализации производства на базе комплексной механизации, электрификации, автоматизации и поточной организации технологических процес- сов в животноводстве.
В состав комплекса наряду с основными животноводческими зданиями входят ветеринарно-санитарные и административно- бытовые помещения, хозяйственные постройки, сооружения для хранения и приготовления кормов, переработки навоза, водоза- борные сооружения, инженерные сети, подъездные пути.
В отличие от фермы комплексы проектируются и строятся по полному набору зданий и сооружений. Они должны давать наибольший удельный вес животноводческой продукции. В них применяется цеховая структура управления.
|
|
Животноводческие фермы и комплексы классифицируются по следующим признакам:
- по форме собственности: частная; государственная и их раз- новидности (коллективная, смешанная).
- по организационно-правовой форме: государственные и му- ниципальные унитарные предприятия; производственные коопера- тивы, колхозы, артели; открытые и закрытые акционерные обще- ства (ОАО и ЗАО); общества с ограниченной и с дополнительной ответственностью (ООО и ОДО); полные товарищества и товари- щества на вере.
- по источникам поступления кормов – на привозных кормах из государственных ресурсов и на кормах собственного производ- ства;
- по основной специализации: по производству молока, говя- дины, свинины, шерсти, яиц, и т.д.;
- по уровню специализации: с законченным технологическим циклом или специализированные на отдельных стадиях техноло- гического цикла;
- по размерам: мелкие, средние, крупные;
- по биологическому виду содержащихся животных: крупного рогатого скота, свиноводческие, птицеводческие, овцеводческие, звероводческие, кролиководческие, коневодческие и некоторые другие.
- по основному производственному направлению фермы и комплексы могут быть племенными и товарными.
Племенные фермы и комплексы занимаются совершенствова- нием существующих и выведением новых пород животных и пти- цы.
Товарные фермы и комплексы занимаются производством жи- вотноводческой продукции в виде продуктов питания или сырья для промышленности. Товарные фермы и комплексы в свою оче- редь могут быть с законченным производственным циклом, ре- продукторные, откормочные, молочные, молочно-откормочные.
Фермы и комплексы с законченным производственным цик- лом включают воспроизводство стада, выращивание молодняка, производство товарной продукции.
Репродукторные фермы и комплексы занимаются размноже- нием и выращиванием ценных пород животных, предназначенных для поставки на специализированные фермы и воспроизводства собственного маточного поголовья.
Откормочные, молочные, молочно-откормочные фермы
и комплексы занимаются производством соответствующего вида продукции (молока, мяса). Особенностью молочных ферм является то, что они, как правило, являются и репродукторными, так как продуктом их производства являются, кроме молока, еще и телята.
Птицеводческие фермы и комплексы различают:
- по биологическому виду птицы (куры, утки, индюки, гуси и т.п.);
- выращиванию различных возрастных групп (цыплята, брой- леры, взрослая птица);
- виду продукции (мясо, яйца).
Размеры животноводческих ферм формируются главным об- разом в зависимости от наличия кормов как собственного произ- водства, так и из госресурсов. Меньшее влияние оказывают нали- чие рабочей силы, средств механизации, энергообеспечения средств доставки готовой продукции к месту переработки и по- требления, возможностей для утилизации навоза и некоторые дру- гие.
Размеры ферм колеблются в зависимости от назначения, спе- циализации, концентрации, способа содержания и находятся в пределах, указанных в таблице 1.
Таблица 1
Размеры животноводческих комплексов
Специализация комплекса | Размеры комплекса по поголовью, тыс. гол. | |||
мелкие ср | едние крупн | ые | ||
КРС, в том числе: | - производство молока | 0 4 | 0 8-1 2 | 1 6-2 |
- выращивание ремонтного молодняка | 1,2 | 3 | 6-9 | |
- производство говядины при откорме | 3 | 5-6 | 10-12 | |
Свиноводческие предприятия, в том числе: | - с законченным производственным циклом | 3,6-12 | 24-25 | 108-216 |
- репродуктивные | 0,3 | 0,6 | 1,2 | |
- откормочные | 1-3 | 4-8 | 12-24 | |
Овцеводческие, в том числе: | - романовские | 2-3 | 6 | 9 |
- откормочные | 6-12 | 18-24 | 30-40 | |
Птицефабрики, в том числе: | - куры-несушки | 50 | 100-600 | 1000 |
- цыплята-бройлеры | 300 | 600 | 10000 |
Специализация производства выражается в обособлении от- раслей и производства с целью выпуска продукции одного вида.
При специализации эффективнее используются технологиче- ское оборудование, передовые технологии и наиболее современ- ные методы организации производства. В животноводстве разли- чают следующие формы специализации: отраслевая, внутриотрас- левая, хозяйственная, внутрихозяйственная и внутрифермерская.
Отраслевая (межотраслевая) специализация основана на раз- делении труда между животноводческими отраслями. Хозяйствен- ная специализация предусматривает разделение труда между от- дельными сельскохозяйственными предприятиями и ограничение видов продукции, производимой в каждом хозяйстве. Разделение
труда распространяется не только на отдельные виды продукции (предметная специализация), но и на отдельные фазы производ- ства, ранее выполняющиеся в одном хозяйстве, а нередко и на од- ной ферме. Наиболее широко стадийную специализацию приме- няют в скотоводстве. Здесь отдельные производственные фазы производства выделяют в самостоятельные производства, в связи с чем образуют хозяйства, специализированные на производстве молодняка, доращивании и откорме молодняка.
Внутрихозяйственная специализация – разделение труда меж- ду отдельными подразделениями внутрихозяйственного предприя- тия.
Различают три основные формы внутрихозяйственной специ- ализации: комплексная, предметная, стадийная.
При комплексной специализации в нескольких (например, в трех) отделениях хозяйства сочетаются производства молочного животноводства, кормовых культур, овцеводства.
Предметная специализация – производство в хозяйстве одно- временно молока, свинины, картофеля и овощей.
Стадийную применяют в животноводческих и птицеводче- ских хозяйствах.
Внутрифермерская специализация предусматривает разделе- ние труда внутри животноводческих ферм (комплексов) и выража- ется в размещении каждой половозрастной группы животных в отдельном здании или помещении.
1.1. Фермы и комплексы крупного рогатого скота
Фермы и комплексы крупного рогатого скота строят с учетом природно-климатических и экономических условий районов стра- ны, направления животноводства, специализации хозяйств, обес- печения кормовой базой, размера поголовья и систем содержания животных.
В скотоводстве животных классифицируют по следующим возрастным группам с учетом их физиологического состояния:
- быки-производители в возрасте 1,5 года и старше;
- коровы дойные и с телятами на подсосе, сухостойные (стельные), глубокостельные (последние две недели до отела) и новотельные (первые две недели после отела);
- нетели – стельные телки;
- телята молочных и комбинированных пород в возрасте до 20 дней (профилакторный период) и от 10 дней до 6 мес., а также телята мясных пород в возрасте до 8 мес.;
- молодняк молочных и комбинированных пород в возрасте от
4 до 18 мес. и мясных пород – до 18 мес.
На молочно-товарных фермах и комплексах применяют ком- плексную механизацию и частичную автоматизацию производ- ственных процессов. С этой целью создают поточно- технологические линии.
Под поточно-технологической линией (ПТЛ) подразумевают совокупность расположенных в определенной последовательности и взаимоувязанных по производительности машин, и оборудова- ния, обеспечивающих выполнение производственного процесса по поточно-прерывистому и цикличному графикам. Комплексная ме- ханизация – это уровень механизации, при котором машины и ме- ханизмы поточно выполняют все основные и вспомогательные производственные процессы. Под уровнем механизации подразу- мевают выраженное в процентах отношение числа животных, об- служиваемых машинами, к общему поголовью животных, имею- щихся в хозяйстве.
Размещение отдельных помещений фермы (комплекса) и тех- нологическая связь между ними должны быть такими, чтобы обес- печивались рациональная организация работ и правильное течение технологических процессов в зависимости от системы содержания скота и назначения зданий.
При стойловом (привязном) содержании скота применяют многорядное размещение стойл, причем каждые два ряда их объ- единяют общим кормовым или навозным проходом. В одном не- прерывном ряду допускается не более 50 стойл (рис. 1).
При беспривязном содержании скота (рис. 2) здания разгора- живают на секции для раздельного содержания групп животных с учетом продуктивности, периода лактации и физиологического состояния. В одном непрерывном ряду допускается не более
80 боксов.
Родильное отделение на молочной ферме (комплексе) должно быть разделено на две секции сплошной перегородкой; в одной из них предусматривают помещение для отела коров, в другой – про- филакторий для телят.
Рис. 1. План и поперечный разрез коровника на 200 коров привязного содержания:
1 – стойловое помещение; 2 – помещение для подстилки; 3 – фуражная;
4 – инвентарная; 5 – тамбуры; 6 – тамбур навозоудаления; 7 – вентиляционная камера; 8 – молочная
Помещения для отела оборудуют стойлами шириной 1,5 м для глубокостельных и 1,2 м для новотельных коров. В родильном от- делении устраивают денники для отела коров. Размеры денников 3×3 м, а их число составляет 4...5 % общего числа мест в родиль- ном отделении, или 1...1,5 % поголовья коров на ферме. В профи- лактории рядами размещают индивидуальные клетки для телят.
В одном помещении телятника устанавливают групповые клетки для телят в возрасте от 10 дней до 4 мес. и от 3 до 6 мес.
Рис. 2. План коровника для боксового содержания коров на 400 голов: I – помещение для животных; II – доильное отделение; III – вакуум-насосная; IV – комната механика; V – молочная; VI – помещение для хранения кормов; VII – моечная; VIII – компрессорная; IX – служебное и бытовое помещение;
X – бойлерная; 1 – транспортеры для уборки навоза; 2 – доильные установки типа
«Елочка»; 3 – проезд для механизированной раздачи кормов
При любой системе содержания на животноводческих пред- приятиях предусматривают выгульные площадки (табл. 2).
Таблица 2
Нормы площадей, выгульных площадок для одного животного, м2
Группы животных | Выгульная площадка | |
с твердым покрытием | без твердого покрытия | |
Коровы и нетели за 2...3 мес. до отела на молочных фермах | 8 | 15 |
Молодняк всех возрастов и нетели в возрасте до 6...7 мес. | 5 | 10 |
Молодняк и взрослый скот на откормочной площадке | 5 | 15...20 |
Телята в возрасте от 10 дней | 2 | 5 |
Коровы мясных пород с телятами в возрасте до 7...8 мес. | 8 | 18 |
При групповом содержании скота на одно животное преду- сматривают среднюю площадь помещения, м 2: для коровы – 4...5, молодняка – 2...3, телят до 3-месячного возраста – 1...2, телят в возрасте 3...6 мес. (в боксах) – 1,5, коров и нетелей в стой- ле – 1,7...2,3.
В случае привязного содержания каждое животное находится в отельном стойле, оборудованном привязью, кормушкой, автопо- илкой, средствами механизации раздачи кормов, удаления навоза и доения. Размеры стойла, м: ширина – 1...1,2, глубина –1,7...1,9. При мобильной системе раздачи кормов ширину кормового про- хода принимают равной 2,2...2,3 м. Ширина навозного прохода между стеной и рядом стойл должна быть 1,5 м (не менее), а меж- ду рядами стойл – 2 м (не менее).
При четырехрядном расположении стойл ширину здания ко- ровника принимают равной 18 м (использование стационарных кормораздатчиков) и 21 м (использование мобильных кормораз- датчиков). Коровники шириной 18 м строят, как правило, одно- пролетными без внутренних колонн. Помещения шириной 21 м строят одно- и трехпролетными (ширина крайних пролетов по 7,5 м, среднего – 6 м).
Коровники для беспривязного содержания скота проектируют и строят вместимостью до 400 голов. Помещения разгораживают перегородками на секции раздельного содержания различных
групп животных. В каждой секции предусматривают выход на вы- гульный или выгульно-кормовой двор. Животных содержат на глубокой, сменяемой один раз в год подстилке. При содержании скота без подстилки секции оборудуют индивидуальными бокса- ми.
Бокс – это место для отдыха животного, ограниченное с боков разделителями, а спереди – перегородкой или стеной (рис. 3).
К верхней части разделителей боксов крепят горизонтальные ограничители, которые располагают на уровне затылка коровы. Ширину бокса выбирают такой, чтобы корова не могла в нем по- вернуться, вследствие чего большая часть пола бокса не загрязня- ется навозом. Чтобы в бокс не попадали загрязнения с навозного прохода, места отдыха для коров устраивают на возвышении (15...20 см) и с небольшим уклоном в сторону навозного прохода.
![]() |
Рис. 3. Боксовое оборудование для беспривязного содержания коров:
а, б – боксы; 1 – боковой разделитель; 2 – деревянный настил или коврик;
3 – устройство выравнивания электрических потенциалов; 4 – фиксирующее устройство; 5 – кормушка, 6 – дельта-скрепер навозоуборочного транспортера; 7 – разделитель кормового стола, в – комбибокс: 1 – поилка; 2 – водопровод;
3 – хомутик; 4 – боковой разделитель; 5 – скоба; 6 – капроновый канатик;
7 – накладка, 8 – ограничитель у кормушки;
9 – труба для стока воды; 10 – трап
Боксы бывают двух видов: только для отдыха животных и комбинированные – для отдыха и кормления. Длина бокса 190...210 см, ширина – 100...110 см. Комбинированные боксы
устраивают только в том случае, когда животных кормят и содер- жат в одном помещении. Длина такого бокса 155...180 см. В пе- редней части любого бокса ставят ограждающую решетку. Комби- нированные боксы оборудуют поилками, в полу таких боксов предусматривают щели и навозные решетки. Ряды боксов распола- гают вдоль и поперек помещения.
Телятники строят, как правило, на 200 голов, совмещая их с родильным отделением. Телят в возрасте до 10...14 дней содержат в индивидуальных клетках изолированного профилактория, до
2 мес. – в групповых станках на 4...6 голов и старше 2 мес. в груп- повых станках на 10...15 голов. В групповых клетках для одного животного должна быть предусмотрена площадь 1,1...1,5 м2.
При интенсивной технологии производства говядины с пол- ным (завершенным) циклом предусматриваются выращивание, доращивание и откорм молодняка крупного рогатого скота в воз- расте от 15...20 дней до 15...18 мес. на специализированных фер- мах промышленного типа и комплексах, а также реализация госу- дарству животных массой 420...450 кг. На этих комплексах приме- няют пастбищное и безпастбищное содержание животных, как с выгулом, так и без выгула, а также содержание их на открытых площадках.
В технологии производства говядины сформировалось два основных направления получения мяса: от специализированных мясных пород и от животных молочных и мясомолочных пород.
Технологией предусмотрена непрерывность процесса выра- щивания и откорма молодняка по циклическому графику. Телят в возрасте от 10...20 дней до 3...4 мес. содержат безвыгульно и бес- привязно на щелевых полах или на привязи в боксах. Доращива- ние и откорм осуществляют в закрытых помещениях или на пло- щадках открытого или полуоткрытого типа. В закрытых помеще- ниях скот содержат на привязи или беспривязно на щелевых сплошных полах группами по 20...50 голов, а на площадках – по 100...200 голов.
На рисунке 4 показан комплекс по выращиванию 10 тыс. го- лов молодняка крупного рогатого скота в год.
Рис. 4. Комплекс по выращиванию и откорму 10 тыс. голов молодняка крупного рогатого скота в год (все размеры даны в метрах):
а – павильонная застройка; б – застройка укрупненными зданиями;
1 – телятники на 720 голов каждый (22×84 м); 2 – соединительные галереи; 3 – здание для приема телят; 4 – здания для молодняка на 720 голов каждый (22×84 м); 5 – кормоприготовительное помещение со складом комбикормов; 6 – санитарно-убойный пункт; 7 – котельная; 8 – здание для отгрузки скота;
9 – пункт технического обслуживания; 10 – ветеринарно-санитарный пропускник;
11 – телятники на 1000 голов каждый (84×96 м); 12 – автомобильные весы;
13 – сарай для сена; 14 – телятник на 4000 голов (84×96 м); 15 – здания для молодняка на 4000 голов каждое (84×120 м); 16 – блок для дезинфекции
транспортных средств (6×135 м); 17 – помещение для насосов (насосная);
18 – навозохранилище
Откормочные площадки (рис. 5) предназначены для откорма молодняка и выбракованного взрослого скота. Эти площадки стро- ят преимущественно в южных районах страны с расчетной
температурой наружного воздуха зимой не ниже -20 0С. Террито- рию площадки делят на зону содержания скота и зону хранения
и подготовки кормов. В зоне содержания животных устраивают навесы или легкие закрытые помещения вместимостью не более 250 голов с секциями для разных групп молодняка и выгульные площадки (загоны), оборудованные кормушками и поилками. Раз- меры навесов для молодняка строят из расчета 3 м 2 на одну голову при содержании животных на глубокой подстилке и 2 м 2 при со- держании их на решетчатых полах. При устройстве загонов с твердым покрытием для животного должна быть предусмотрена площадь 5 м2, без твердого покрытия – 15...20 м2.
![]() |
Рис. 5. Площадка для откорма молодняка (все размеры даны в метрах):
а – схема генерального плана; б – навес для кормушки;
1 – телятники на 400 голов каждый (18×86 м); 2 – площадка для грубых кормов;
3 – силосная траншея; 4 – кормоцех и склад концентрированных кормов;
5 – навесы для отдыха животных; 6 – навесы над кормушками; 7 – лечебные участки; 8 – пруды-отстойники (110×380 м).
В первый период откорма животных содержат под навесом, во второй – без навесов. Чтобы защитить животных от ветров
и снежных заносов, навесы закрывают с трех сторон сплошным ограждением из дерева или асбоцементных листов. Для этих же целей часть ограды (как правило, с северной стороны) делают в виде сплошных заборов высотой 2,7...3 м. Для отвода поверхност- ных вод площадки загонов выполняют с уклоном, благодаря чему вода стекает в пруды-отстойники, размещаемые за оградой терри- тории.
1.2. Свиноводческие фермы и комплексы
Существует следующая классификация свиней различных возрастных групп с учетом их физиологического состояния
и назначения:
- хряки – производители в возрасте 1,5 лет, проверяемые,
т. е. ремонтные (от времени первой случки до момента оценки их по массе потомства в возрасте 2 или 6 мес.), и пробники (предна- значены для выявления маток, приходящих в охоту);
- матки – холостые, т.е. неосемененные после отъема поросят, супоросные, т. е. осемененные (их делят на три группы: после осеменения до установления фактической супоросности, с уста- новленной супоросностью и тяжелосупоросные за 7...10 дней до опороса), и подсосные с поросятами в возрасте до 2 мес. (при ран- нем отъеме до 26...35 дней);
- поросята-сосуны – от рождения до 2 мес. (при раннем отъ- еме до 26...35 дней);
- поросята-отъемыши – после отъема от маток до возраста
3...4 мес.;
- ремонтный молодняк – хрячки и свинки в возрасте
4...11 мес., предназначенные для замены (ремонта) выбракованно- го взрослого поголовья;
- свиньи на откорме (откормочное поголовье) – молодняк в возрасте 3...8 мес. и взрослые свиньи (выбракованные матки
и хряки).
На комплексах промышленного типа всех маток после перво- го опороса (в возрасте 13 мес. и старше) формируют в группы в зависимости от физиологического состояния. На фермах племен- ных, репродукторных и с законченным производственным циклом
всех маток делят на проверяемых (от плодотворного осеменения до отъема поросят) и основных. Их также формируют в группы в зависимости от физиологического состояния и содержат в специа- лизированных зданиях или секциях.
Свиноводческие предприятия по назначению делят на пле- менные и товарные. Племенные предприятия предназначены для совершенствования пород и выращивания высокоценного молод- няка для товарных свиноводческих предприятий. Товарные свино- водческие фермы и комплексы промышленного типа служат для производства мяса и бывают специализированные (репродуктив- ные и откормочные) и с законченным производственным циклом (рис. 6). Репродуктивные предприятия выращивают поросят, пред- назначенных для откорма на специализированных откормочных фермах, комплексах промышленного типа и подсобных хозяй- ствах. На откормочных предприятиях с законченным производ- ственным циклом выращивают поросят, предназначенных для от- корма, и организуют откорм собственного молодняка на мясо.
![]() |
Рис. 6. Генеральный план свиноводческого комплекса на 12000 голов в год с законченным производственным циклом:
1 – свинарник для холостых и супоросных маток и ремонтного молодняка; 2 – свинарник для свиноматок; 3 –свинарники для проведения опоросов; 4 – свинарник для поросят-отъемышей; 5 – свинарники-откормочники;
6 – галереи подачи кормов; 7 – кормоцех с корнеплодохранилищем; 8 – блок служебных помещений; 9 – блок помещений ветпункта, санбойни и стационара; 10 – изолятор; 11 – хранилище травяной муки; 12 – силосохранилище;
13 – весовая; 14 – выгульный двор; 15 – котельная; 16 – дезбарьеры;
17 – площадка для корнеплодов
В свиноводстве применяют две системы содержания живот- ных: станочную и станочно-выгульную. Для всего поголовья сви- ней (кроме поросят-отъемышей) племенных ферм и репродукто- ров, а также для хряков-производителей, ремонтного молодняка, маток с установленной супоросностью и холостых (при групповом содержании) на товарных фермах и комплексах промышленного типа предусматривается, как правило, выгульная система содер- жания. При этом выгульные площадки размещают у продольных стен, а свинарник делят на секции. Размер секций зависит от пого- ловья свиней в группе (при групповом содержании) или численно- сти свиней, обслуживаемых одним работником (при содержании в индивидуальных станках).
Все остальное поголовье свиней, как правило, содержат без- выгульно. В южных районах страны допускается выгульное со- держание свиней на откорме. На комплексах промышленного типа допускается безвыгульное содержание свиней.
В зданиях свиней размещают в секциях, групповых или инди- видуальных станках. Хряков-производителей, маток тяжелосупо- росных, подсосных с поросятами-сосунами и осемененных до установления фактической супоросности содержат в индивиду- альных станках, маток с установленной супоросностью и холо- стых, ремонтный молодняк, поросят-отъемышей и свиней на от- корме – в групповых станках.
Для осуществления принципа «свободно – занято» и проведе- ния всех необходимых мероприятий по санитарной обработке и дезинфекции помещений, в которых происходят опоросы, свинар- ники для поросят-отъемышей и свинарники-откормочники следует разделять сплошными перегородками на изолированные секции.
Вместимость секций, зависящая от размеров технологического оборудования, должна быть (не более) 100 хряков; 300 голов ре- монтного молодняка; 400 холостых и супоросных маток; 60 маток, готовых к опоросу, на комплексах промышленного типа или
30 маток на племенных и товарных фермах; 600 поросят- отъемышей; 1200 свиней на откорме.
Здания и сооружения зоны хранения и приготовления кормов определяют с учетом принятого на предприятии типа кормления. Кормоцех размещают при въезде на территорию предприятия с наветренной стороны по отношению к остальным зданиям и со- оружениям. В непосредственной близости к кормоцеху или
в блоке с ним располагают склад концентрированных кормов и хранилище для корнеклубнеплодов, силоса и других кормов.
Вместимость сооружений для хранения и обработки навоза определяют с учетом нормативов выхода экскрементов от живот- ных, количества поступающей воды в каналы навозоудаления при уборке помещений, ее расхода на гидравлическую транспортиров- ку навоза. Навоз из станковых помещений удаляют главным обра- зом с помощью гидравлических систем – гидросмывных и само- течных. Навоз удаляется гидросмывом с площадок для дефекации и из навозных каналов, а далее по трубам направляется в сооруже- ния для обработки навозных стоков.
1.3. Птицеводческие предприятия
Домашняя птица бывает следующих видов: куры, индейки, утки, перепела, гуси. Птицу каждого вида делят на три основные категории: взрослая, ремонтный молодняк и молодняк, выращива- емый на мясо. В зависимости от производственного назначения различают птицу племенного стада (исходные линии, прароди- тельское и родительское стадо (птица всех видов)) и промышлен- ного стада (куры и перепела).
По производственному назначению различают ремонтный молодняк, выращиваемый для замены особей племенного и про- мышленного стада, и молодняк, выращиваемый на мясо.
По назначению различают следующие птицеводческие пред- приятия:
- товарные – яичного и мясного направления соответственно по производству яиц и мяса птицы; к ним относятся также птице- фабрики и фермы сельскохозяйственных предприятий (без птицы, родительского стада), функционирующие на основе технологиче- ской кооперации в составе объединений;
- с замкнутым циклом производства – птицефабрики и объ- единения;
- племенные – для совершенствования существующих и выве- дения новых специализированных пород и сочетающихся линий птицы, производства прародительских и родительских форм,
а также гибридов для снабжения ими товарных предприятий и ин- кубаторно-птицеводческих станций;
- специализированные – по выращиванию гибридных кур- молодок товарных хозяйств;
- инкубаторно-птицеводческие станции.
Размеры товарных предприятий (табл. 3) яичного направле- ния определяют по среднегодовому поголовью кур-несушек и са- мок перепелов промышленного стада и годовому производству пищевых яиц от них, а мясного направления – по числу сдаваемых в год бройлеров (цыплят, индюшат, утят, гусят, перепелят) и годо- вому производству мяса в живой массе; племенных – по числу по- садочных птицемест для взрослой птицы и выходу суточного пле- менного молодняка или инкубационных яиц в год для реализации; специализированных – по числу выращиваемых в год гибридных кур-молодок и по годовой их реализации; инкубаторно- птицеводческих станций – по числу яйцемест (куриных).
Таблица 3
Размеры товарных птицеводческих предприятий
Специализация предприятия | Поголовье птицы, тыс. голов | Годовое производство основной продукции | ||
млн яиц т | мяса | |||
Производство пищевых яиц | 50-600 | 127-153 | 125-150 | |
Производство мяса: | ||||
цыплят-бройлеров | при клеточном содержании | 250-6000 | 412,5-9900 | 387-5430 |
при напольном содержании | 250-6000 | 375-9000 | 387-5430 | |
утят-бройлеров | 125-1000 | 275-2200 | 275-2200 | |
индюшат-бройлеров | 50-250 | 625-3125 | 550-2750 | |
гусят-бройлеров | 100-250 | 400-1000 | 380-950 |
Птицеводческие предприятия следует отделять от жилой за- стройки санитарно-заградительными зонами. Расстояние от птице- водческой жилой застройки должно быть не менее 300 м; от пти- цеводческого предприятия размером 1-3 млн бройлеров в год или 100-400 тыс. кур-несушек и от племенного предприятия – не менее 1000 м; от птицеводческого предприятия размером более 400 тыс. кур-несушек или более 3 млн бройлеров в год – не менее 1200 м.
Помещения для выращивания молодняка и содержания взрос- лого поголовья птицы строят павильонного типа, как правило, од- ноэтажные (одно-, двухзальные). Эти помещения следует ком- плектовать партией птицы одного вывода. Многоэтажные и сбло- кированные птичники допускается проектировать для содержания
кур-несушек промышленного стада и выращивания цыплят- бройлеров только при соответствующем технико-экономическом обосновании. Возрастной диапазон птицы в таких птичниках дол- жен составлять не более 3...5 дней для бройлеров и 14 дней для кур-несушек. При павильонном содержании птицы (на глубокой подстилке, сетчатых и планчатых полах) с учетом заполненности и направления продуктивности установлены следующие нормы посадки ее на 1 м 2 площади пола: для кур – 3,5-5 голов, для инде- ек – 1-2, для уток – 2,3-3, для гусей – 1-1,2 для цесарок – 4-5 голов.
При клеточном содержании, например, кур площадь пола ба- тарей для одной особи составляет в среднем 0,05...0,1 м2.
С целью уменьшения опасности распространения заболеваний птиц, повышения эффективности профилактики и обеспечения ритмичной работы предприятия предусматривают строгое зониро- вание территории, а также ограничивают концентрацию поголовья в одной зоне. Как правило, выделяют следующие зоны: производ- ственного сектора, административно-хозяйственную, убоя и пере- работки птицы, склад, пометохранилище.
Птицеводческие здания в производственном секторе разме- щают по отдельным зонам и подзонам в зависимости от техноло- гического процесса и возраста птицы. Производственный сектор предприятия яичного и мясного направлений включает в себя сле- дующие основные зоны: родительского стада кур, ремонтного мо- лодняка родительского стада, инкубатория, промышленного стада, ремонтного молодняка промышленного стада.
Товарные предприятия яичного и мясного направлений раз- мером не более 300 тыс.кур-несушек, 3 млн бройлеров, 750 тыс. утят, 250 тыс. индюшат строят на одной площадке, предусматри- вая между отдельными зонами и подзонами расстояние (зоовете- ринарный разрыв) не менее 60 м. При строительстве более круп- ных птицефабрик различные технологические группы птиц, инку- баторий и цех убоя размещают на разных площадках в обособлен- ных зонах, зооветеринарные разрывы между которыми должны быть не менее 300 м.
Концентрация поголовья в соответствующих подзонах долж- на быть не более 350 тыс. голов промышленного стада, 50 тыс. кур родительского стада, 20 тыс. цыплят-бройлеров. Максимальная вместимость подзон (тыс. голов): для уток, гусей, индеек
родительского стада и их ремонтного молодняка – 20, для утят- бройлеров – 200, для гусят и индюшат-бройлеров – 100.
Допустимая вместимость (голов) отдельных секций птични- ков на товарных предприятиях при напольном содержании: кур промышленного стада – 2000, племенного – 300; индеек – 150, ин- дюков – 15; уток – 100; гусынь – 120; самцов гусей – 12; ремонт- ного молодняка кур промышленного стада – 2500, племенного – 1000; цыплят, выращиваемых на мясо (бройлеры, кур) – 500; мо- лодок индеек – 250; молодок гусей – 250; молодок уток промыш- ленного стада – 300, племенного – 100.
Максимальная вместимость птичников (тыс. голов) при кле- точном содержании кур промышленного стада – 150, ремонтного молодняка – 200, при напольном содержании ремонтного молод- няка – 20. Вместимость птичников (тыс. голов) для племенного стада кур при клеточном содержании – не более 16, при наполь- ном – не более 5. На птицеводческих предприятиях мясного направления взрослое поголовье, ремонтный молодняк кур- несушек и цыплят-бройлеров, выращиваемых на мясо, содержат на подстилке или в клеточных батареях (рис. 7, 8).
![]() |
Рис. 7. План птичника на 20 тыс. кур-несушек промышленного стада: 1 –залы для птицы; 2 – подсобные помещения; 3 – инвентарная, 4 – моечная; 5 – служебное помещение; 6 – яйцесклад; 7 – вентиляционная камера;
8 – коридоры и тамбуры
Рис. 8. План птичника для выращивания бройлеров на 22 тыс. голов
(все размеры даны в метрах):
1 – вентиляционная камера; 2 – подсобное помещение; 3 – помещение для птицы
При напольном содержании кур используются птичники шириной не менее 16 м. В этих птичниках можно содержать кур на глубокой под- стилке, планчатых или сетчатых полах.
1.4. Овцеводческие фермы и комплексы
В овцеводстве животных сортируют на следующие основные технологические группы: бараны (производители, пробники), мат- ки (холостые, суягные, подсосные), ягнята, ремонтный молодняк, откормочное поголовье, валухи. Созданы специализированные предприятия для содержания овец одной половозрастной группы (маток, ремонтного молодняка и т. д.) и неспециализированные – для содержания овец разных половозрастных групп (табл. 4).
Таблица 4
Размеры животноводческих комплексов, тыс. голов
Назначение предприятия | Направление продуктивности | |||
тонкорунное и полутонко- рунное | шубно-шерстное и мясо-молочное | каракульское и мясо- сальное | ||
Специали- зированные: | маточные | 3; 6; 9 | 0 5; 1 2 | 3; 6; 9 |
ремонтного молодняка | 3; 6; 9 | 1; 2 | 3; 6; 9 | |
откорма молодняка и взрослого поголовья | 5; 10; 20 | 1; 2; 4 | 5; 10; 20 | |
Неспециализированные с законченным оборотом | 1,5; 3; 6; 9 | 1; 2; 3 | 1,5; 3; 6; 9 |
Овец одного пола и возраста объединяют в отары (группы) и содержат, как правило, в одном здании. В случае приотарного осеменения, зимнее и ранневесеннее ягнения проводят в овчарнях
с тепляками (утепленное помещение) и родильном отделении. Для проведения весеннего ягнения овчарни строят без тепляков или устраивают базы-навесы с тепляком.
Для проведения ягнения маток при цикличном осеменении отдельных групп строят специально оборудованные овчарни, раз- гороженные на секции (огарки) вместимостью по 15...30 голов каждая. Овец кормят и поят, как правило, на выгульной площадке, а в период ягнения – внутри помещения.
Состав и взаимное расположение на участке основных произ- водственных зданий и сооружений, а также объектов обслужива- ющего назначения определяют с учетом системы содержания овец, направления продуктивности, специализации и размера предприя- тия. На рисунке 9 показана овцеводческая ферма с законченным оборотом стада на 2500 голов мясо-шерстного направления.
В производственной зоне размещают баранник для содержа- ния баранов-производителей и баранов-пробников; овчарни для содержания маток или маток с ягнятами; овчарни для содержания и ягнения маток (оборудованные тепляком и родильным отделени- ем); овчарни для искусственного выращивания и откорма ягнят; овчарни для выращивания ремонтного молодняка; баз-навес для укрытия овец; пункт искусственного осеменения; пункт стрижки овец; пункт дойки овец.
Рис. 9. Овцеводческая ферма с законченным оборотом стада
на 2500 голов мясо-шерстного направления (все размеры даны в метрах): 1 – бригадный дом с санпропускником (7,5×12 м); 2 – пункт искусственного осеменения (18×28 м); 3 – овчарни на 500 маток каждая (12×81 м); 4 – овчарня на 500 голов ремонтного молодняка (12×33 м); 5 – траншея для хранения силоса; 6 – изолятор (9×12 м); 7 – амбулатория (9×9 м); 8 – резервуар для воды
вместимостью 100 м3
На овцеводческих предприятиях всех направлений продук- тивности при бараннике и овчарнях размещают выгульно- кормовые площадки из расчета 3 м 2 на одну голову для баранов- производителей, баранов-пробников и маток, 2 м 2 – для ремонтно- го молодняка и 1 м2 – для откормочного поголовья и валухов.
Овчарни проектируют, как правило, одноэтажными и прямо- угольными (в плане). Овец содержат в секциях, вместимость кото- рых для баранов-производителей должна быть не более 25 голов, баранов-пробников – 50 ягнят на искусственном выращивании в возрасте до 45 дней – 25, в возрасте старше 45 дней – 75, маток, ремонтного молодняка и откормочного поголовья – 250 голов.
В связи с тем, что по технологии предусмотрена постоянная перегруппировка отар, никаких стационарных перегородок, разде- ляющих помещения на секции, не делают.
Для зимнего ягнения маток в овчарне устраивают тепляк вместимостью 30 % общего поголовья маток. В тепляке
предусматривают секции, каждая из которых рассчитана на
8...12 маток с ягнятами, родильное отделение со специальной площадкой (из расчета 115 м 2 на 100 суягных маток), разделенной на секции по 1,8...2 м 2, и несколько рядов индивидуальных клеток площадью 1,2...1,4 м 2. Помещения для овец, как правило, строят шириной 12 или 18 м с несущим каркасом без промежуточных опор.
Контрольные вопросы
1. Какими показателями характеризуется общее состояние животновод- ства?
2. Что представляет из себя животноводческая ферма?
3. В чем отличие животноводческого комплекса от фермы?
4. Отличие ПЖК от комплекса совхоза или колхоза?
5. В чем сходство между животноводческим комплексом и промыш- ленным предприятием?
2. Технология производства молока и говядины
Скотоводство – одна из наиболее важных отраслей животно- водства, так как от крупного рогатого скота получают такие цен- ные продукты питания, как молоко и мясо, а также сырье для лег- кой промышленности. Шкура скота, являясь лучшим сырьем для кожевенно-обувной промышленности, по количеству и качеству занимает первое место среди шкур сельскохозяйственных живот- ных других видов.
Получаемые после убоя КРС побочные продукты используют в колбасном производстве, из крови вырабатывают кровяную му- ку, богатую белком, из костей – костную муку.
Мясо КРС имеет важное значение в питании населения.
В мясном балансе страны доля говядины и телятины составляет более 40%.
От КРС земледелие получает навоз – ценное органическое удобрение.
КРС как жвачные животные имеют сложный многокамерный желудок, состоящий из рубца, сетки, книжки и сычуга. В связи с этим КРС может потреблять и переваривать большое количество дешевого грубого корма (сено, солому, мякину, остатки овощных и других культур, богатых клетчаткой) и превращать его в высо- коценные продукты питания – мясо, молоко.
КРС сравнительно неприхотлив, его можно разводить в райо- нах с различными почвенно-климатическими условиями.
Различают молочную и мясную продуктивность КРС.
Молочная продуктивность – это количество молока, которое корова дает за определенный промежуток времени. Период, в те- чение которого корова дает молоко, называется лактацией, про- должительность периода лактации составляет 300…305 дней.
Молочная продуктивность коров колеблется в широких пре- делах и зависит от многих факторов, важнейшие значение из кото- рых имеют наследственность, условия содержания и кормления.
Потенциальные наследственные возможности животных мо- гут быть реализованы только при обеспечении полноценного
и обильного кормления и оптимальных условий содержания.
На молочную продуктивность влияют возраст коровы, возраст первого осеменения, сервис-период и сухостойный период.
Как правило, до 5…6 лактации удои коров повышаются, затем в
течение нескольких лет поддерживаются на одном уровне, а при- мерно с 8…9 лактации резко снижаются. Оптимальный возраст первого осеменения телок 17…18 месяцев.
Сервис-период – это время от отела до плодотворной случки или осеменения. Сервис-период должен быть равен 45…70 дням, но не более 80 дней. Сухостойный период – время от запуска ко- ровы до нового отела, продолжительность 45…60 дней.
Молочная продуктивность зависит также от живой массы жи- вотного.
Мясная продуктивность – это количество мяса, которое мож- но получить от одного животного. Мясную продуктивность коров можно оценить по таким показателям, как убойная масса и убой- ный выход. Убойная масса – это масса туши без шкуры, головы, внутренних органов и ног, отрубленных по запястные и скакатель- ные суставы. Отношение убойной массы к предубойной, выра- женное в процентах, называется убойным выходом.
Ценность мяса определяется в основном содержанием в нем полноценного белка и жира. В говядине содержится в среднем 17…21% белка и до 23% жира; энергетическая ценность говядины в зависимости от упитанности животного составляет
5…12,6 МДж. Уровень мясной продуктивности зависит в первую очередь от породных особенностей, массы животного и степени его откорма, а качество мяса – от породных особенностей, пола, возраста животного и его упитанности. Высокопитательное мясо получают при убое животных специализированных скороспелых мясных пород.
2.1. Системы и способы содержания КРС
В скотоводстве в основном применяют две системы содержа- ния КРС: привязную и беспривязную.
Привязное содержание получило наибольшее распростране- ние в нашей стране. Главное его преимущество – обеспечение хо- роших условий для индивидуального нормированного кормления и раздоя животных, что способствует повышению их продуктив- ности.
При этой системе каждая корова находится на привязи в стой- ле с отдельной кормушкой и автопоилкой. Над стойлом каждого животного висит табличка, где указаны номер коровы, кличка,
возраст и продуктивность за последнюю лактацию.
В случае привязного содержания коров необходимо выпус- кать на выгульные площадки или организовывать активный моци- он на прогонных дорожках.
Данная система содержания широко распространена в пле- менных хозяйствах, где необходимо обеспечивать индивидуальное нормированное кормление, раздой коров и тщательный уход за племенными животными.
Однако привязная система содержания имеет ряд недостатков.
В течение всего стойлового периода коровы большую часть времени проводят без движения в помещении.
Строительство помещений для привязного содержания обхо- дится очень дорого, так как требуются дополнительные затраты на строительство стойл, кормушек, поилок и т.д.
При привязном содержании велики затраты труда, связанные с доением, раздачей кормов, уборкой навоза, отвязыванием и при- вязыванием животных.
Беспривязное содержание животных предусматривает содер- жание животных группами, организовывая перемещение их в по- мещениях и на выгульных площадках. Существуют следующие способы содержания КРС: свободно-выгульный на глубокой под- стилке, беспривязно-боксовый и комбинированный.
Преимущества беспривязной системы – это благотворное вли- яние на физиологическое состояние и воспроизводительные спо- собности животных; снижение заболеваний пищеварительных ор- ганов, уменьшение стоимости строительства фермы; снижение затрат труда на выполнение разных технологических процессов; улучшение зоогигиенических условий для животных.
2.2. Технология производства молока на промышленных фермах и комплексах
Интенсивные технологии производства молока предусматри- вают:
- ускоренное повышение генетического потенциала разводи- мых пород скота на основе использовании голштинской и других специализированных молочных пород, пригодных к интенсивной технологии;
- использование быков-улучшателей;
- интенсивное выращивание ремонтных телок и формирова- ние животных молочного типа (важнейшее условие формирования высокой продуктивности молочного скота – оптимальная интен- сивность роста и развития телок на всех этапах выращивания.
В возрасте 6 мес. живая масса должна быть 150…170 кг, 12 мес. – 250…295 кг, при осеменении – 340…400 кг. Живая масса первоте- лок: 420…440 кг при молочной продуктивности (удое) 3000 кг, 450…470 кг при удое 4000 кг, 500…530 кг при удое 5000 кг;
- расширенный ремонт стада первотелками, оцененными по собственной высокой продуктивности;
- сбалансированное кормление коров и ремонтного молодняка с максимальным использованием грубых и сочных кормов (корм- ление должно обеспечивать получение планируемой массы телят по возрастным периодам. Так, чтобы достичь уровня молочной продуктивности 3000…5000 кг, рацион должен быть следующим:
- цельное молоко 275…350 кг;
- обезжиренное молоко 490 кг;
- концентраты 210 кг;
- сено 199…225 кг;
- силос 490…500 кг;
- сенаж 250…460 кг.
Сокращение цельного молока до 200 кг допустимо при усло- вии восполнения его полноценным стандартным заполнителем.
До 6-месячного возраста телятам все корма дают раздельно, начиная с возраста 6 мес. рекомендуется вводить в рацион макси- мальное количество грубых и сочных кормов, а летом пастбищных и зеленых;
- использование высокопродуктивных культурных пастбищ;
- применение на фермах прогрессивных способов содержания, комплексной механизации и рациональных технологических ре- шений;
- выполнение комплекса ветеринарно-профилактических ме- роприятий, обеспечивающих высокий уровень здоровья живот- ных;
- внедрение эффективных форм организации и оплаты труда;
- соблюдение технологической дисциплины, направленной на современное качественное осуществление всех производственных процессов.
Основа интенсивной технологии – поточно-цеховая система
производства молока и воспроизводства стада. Она предусматри- вает определенный порядок содержания, кормления животных
и выполнения зооветеринарных мероприятий на ферме с учетом физиологического состояния и продуктивности скота.
2.3. Технология производства говядины на промышленных фермах и комплексах
Преимущества промышленного способа производства говяди- ны – максимальная механизация и автоматизация производствен- ных процессов, использование биологически полноценных кормов с учетом возраста, живой массы и физиологического состояния животных, создание оптимальных зоогигиенических условий со- держания животных.
Индустриальной технологией производства говядины преду- сматривается непрерывность выращивания и откорма молодняка по циклическому графику. Также по графику на комплекс завозят телят. Согласно технологи телята поступают на комплекс через каждые 13 дней. Для этого отбирают хорошо развитых, некастри- рованных бычков в возрасте 10…20 дней средней живой массой 45 кг. Из телят формируют однородные по массе и возрасту груп- пы по 360 голов в каждой. Телят осматривают, моют дезинфици- руют и помещают в станки-сектора помещений первого периода.
Первый период разделен на две фазы. Первая фаза продолжи- тельностью 65 дней. При плановом суточном приросте 600 г быч- ки в конце фазы должны иметь живую массу 84 кг. В первую фазу выращивания животные получают за сутки 0,43 кг заменитель цельного молока (ЗЦМ), 0,69 кг комбикорма и 0,18 кг люцерново- го сена.
Вторая фаза первого периода имеет продолжительность
50 дней. Средний суточный прирост должен составлять 880 г, а в конце фазы живая масса должна быть 128 кг. Средний суточный рацион второй фазы состоит из 2 кг комбикорма и 0,61 кг люцер- нового сена или резки.
Второй период – третья фаза продолжительностью 227 дней. Живая масса в конце фазы должна быть 450 кг при среднем суточ- ном приросте 1165 г. Интенсивный откорм молодняка основывает- ся на неограниченном использовании смеси комбикормов в соче- тании с сенажом из люцерны. В этой фазе суточный рацион
состоит из 67 % концентратов и 33 % сенажа. Структура среднего суточного рациона 5,3 кг комбикорма и 8,4 кг сенажа из люцерны.
В помещениях создают нормальные зоогигиенические усло- вия с помощью систем отопления и вентиляции.
Контрольные вопросы
1. Почему скотоводство является основной и наиболее важной отрас- лью животноводства?
2. Какие питательные вещества содержатся в молоке коровы?
3. Какие породы КРС разводят в России?
4. Как получить молоко высокого качества?
5. Какие преимущества и недостатки характерны для привязной и бес- привязной систем содержания?
6. Чем вызвана необходимость применения поточно-цеховой системы в молочном скотоводстве?
7. Как осуществляется промышленная технология производства мяса и молока?
8. Что такое нагул?
9. Что такое откорм скота на откормочных площадках?
3. Технология производства свинины
3.1. Хозяйственно полезные признаки и биологические особенности свиней
Развитие свиней позволяет в сравнительно короткие сроки производить большое количество мяса. Одна свиноматка может принести 18…20 поросят в год, откармливая которых получают 1,5…2 т свинины при затрате 0,5…0,6 тыс. корм. ед. на 0,1 т про- дукции. Свинина составляет 35% общего производства мяса в стране.
Этому способствуют следующие биологические особенности свиней:
- высокая плодовитость (10…12 поросят за один опорос);
- короткий период супоросности (беременности) – 112…114 дней, благодаря чему можно получить два опороса в год;
- раннее половое и физиологическое созревание – половая зрелость у свиней наступает в 5…8 мес., а физиологическая – в 9…10 мес.;
- скороспелость – первый опорос у свиноматок происходит в возрасте 13…14 мес. При оптимальных условиях содержания
и кормления поросята быстро растут и к 2-месячному возрасту их живая масса достигает 16…20 кг, а к 6…7-месячному 100…110 кг, благодаря чему от каждой свиноматки можно получать ежегодно по 2 т свинины и более;
- высокий убойный выход – 75…85% в зависимости от степе- ни упитанности, возраста, пола и природных особенностей;
- всеядность – они хорошо поедают растительные и животные корма, а также отходы технических производств и предприятий общественного питания;
- высокая оплата корма – на 1 кг прироста молодняка затрачи- вают 3,5…4 корм. ед. (для сравнения: молодняку КРС требуется 7…8 корм. ед.).
Помимо мяса и жира от свиней получают много побочных продуктов (кожа, кишки, щетина, кровь и т.д.), используемых как сырье для дальнейшей переработки. Из свинины приготовляют ценные продукты (колбасы, окорока, корейку и т.д.). В отличие от мяса других животных свинина хорошо консервируется и выдер- живает длительное хранение без снижения качества.
Из анатомо-физиологических особенностей свиней по сравне- нию с другими животными следует отметить самое маленькое сердце по отношению к собственной массе и низкое процентное отношение массы крови к живой массе – 4,6% (у коровы это отно- шение равно 8%, у овцы 8,1 у курицы 8,6%). Свиньи по сравнению с другими животными имеют несовершенную систему терморегу- ляции. Подкожный жировой слой препятствует отдаче тепла,
а способность к потоотделению у свиней практически отсутствует, поэтому они плохо переносят высокую температуру окружающего воздуха при высокой влажности. Свиньи очень возбудимы и чув- ствительны к раздражителям, в условиях современной промыш- ленной технологии и при воздействии неблагоприятных факторов у них возникает стрессовое состояние.
3.2. Откорм свиней
Увеличение производства свинины в большой степени зави- сит от правильной организации и проведения откорма. Откорм – заключительная стадия всего производственного процесса в сви- новодстве. Главная цель откорма – получить максимальные при- росты живой массы при минимальных затратах труда, кормов
и финансовых средств. На откорм поступает сверхремонтный мо- лодняк в возрасте 3…4 месяца, проверяемые матки после отъема от них поросят и выбракованные животные. Основное условие успешного проведения откорма – создание прочной кормовой ба- зы и полноценное кормление. Следует всегда иметь в виду, что расходы на корма составляют до 70 % себестоимости свинины. Успех откорма также зависит от породных особенностей и типа свиней, их возраста и развития, правильности подбора групп, про- должительности откорма и условий содержания. При укомплекто- вании групп животных подбирают одного пола и возраста. Разница в живой массе молодняка должна быть не более 3…5 кг.
В практике хозяйств применяется откорм:
- мясной;
- беконный;
- до жирных кондиций.
Мясной откорм – основной вид откорма молодняка в нашей стране. Главная его цель – получение нежирной свинины в корот- кие сроки при минимальных затратах кормов и средств.
На мясной откорм ставят молодняк после доращивания в воз- расте 3…4 месяца, и продолжают откорм до 6,5…7 месяцев до до- стижения живой массы 95…110 кг. При интенсивном мясном откорме среднесуточный прирост живой массы достигает 600…650 г. При мясном откорме используют самые разнообраз- ные корма. На качество мяса и сала хорошо влияют концентриро- ванные корма (ячмень, рожь, просо), а также зернобобовые (горох, люпин и т.д.), богатые белками, имеющими высокую биологиче- скую ценность. Сочные корма в рационе представлены морковью, комбинированным силосом. Корма животного происхождении представлены мясокостной мукой, обезжиренным молоком, сыво- роткой, пахтой.
В летний период необходимо вводить в рацион молодую тра- ву бобовых растений (клевер, люцерна).
При кормлении свиней необходимо учитывать, что некоторые корма резко ухудшают качество продукции. Например, скармли- вание свиньям кукурузы и пшеничных отрубей в количестве более 40% от общего количества концентратов ухудшает качество сала и способствуют его усиленному отложению. Также при скармли- вании соевого жмыха сало становится мягким, использование рыбной муки придает мясу специфический вкус и запах, а также отрицательно влияет на консервирование.
Для успешного интенсивного мясного откорма свиньи долж- ны получать минеральные вещества, витамины, белковые добавки.
Средняя структура зимнего рациона должна быть следующей:
- концентрированные корма 60…70%;
- сочные 25…30%;
- травяная мука 5%.
Корма скармливают в виде кормовой смеси в полужидком ви-
де.
Беконный откорм является разновидностью мясного откорма.
При беконном откорме получают молодое, нежное, сочное мясо, пронизанное тонкими прослойками плотного зернистого жира. На беконный откорм ставят подсвинок не позднее 3-месчного возрас- та живой массой 25…30 кг следующих пород: ландрас, крупная белая и т.д., а также их помесь.
Для получения бекона высокого качества свиней откармлива- ют до возраста 6…6,5 месяцев для достижения живой массы 80…95 кг и толщины шпика 30 мм. Для беконного откорма
разработаны специальные сбалансированные комбикорма, обеспе- чивающие потребность животных в питательных веществах. По достижении животными массы 60 кг из их рациона необходимо исключить овес, сою, жмых и отруби поскольку они ухудшают качество бекона.
В первые месяцы откорма доля сочных и зеленых кормов в рационе должна быть больше, чем в конце откорма, когда содер- жание концентрированных кормов увеличивают до 75% общей питательности рациона. Откорм свиней до жирных кондиций, как правило, применяют к выбракованным хрякам и свиноматкам.
Цель данного откорма – получение большой живой массы при ис- пользовании наиболее дешевых объемистых кормов. Продолжи- тельность откорма 90…100 дней до толщины шпика 40…60 мм.
В первый период откорма стремятся получать высокие суточ- ные приросты, для чего используют наиболее дешевые объемные корма с небольшим содержанием протеина (комбинированный силос, картофель, тыква, пищевые отходы, травяная мука, концен- траты). В летний период из рациона исключают грубые корма, уменьшают дозу корнеплодов, вводят в рацион 6…8 кг зеленого корма и комбинированного силоса. В последний месяц откорма уменьшают дозу объемных кормов, а дозу концентрированных кормов увеличивают до 50% по питательности рациона. Среднесу- точный прирост живой массы при откорме до жирных кондиций достигает 700…1000 г при расходе кормов 6,5…8,5 корм. ед. на
1 кг прироста. Продукцию используют для получения сала, копче- ностей и в колбасном производстве.
Откорм свиней производят в специализированных помещени- ях – свинарниках-откормочниках. Эти помещения рассчитаны на содержание свиней группами по 15…20 голов в станке с примене- нием комплексной механизации всех технологических процессов.
3.3. Лагерное содержание и кормление свиней
При лагерном содержании свиней значительную часть про- дукции можно получить без капитальных затрат на строительство при эффективном использовании пастбищ. При пребывании на пастбище животные находятся в движении, что способствует раз- витию костяка и мускулатуры и закаляет организм животных.
Находясь на чистом воздухе улучшается физическое состояние
свиней, при этом повышается плодовитость и молочность свино- маток, улучшается рост и развитие молодняка, увеличиваются приросты живой массы, вследствие чего снижается себестоимость продукции. Данный способ содержания свиней широко применя- ется в южных районах страны.
Для лагеря выбирают сухой возвышенный участок, желатель- но возле проточных водоемов и кустарников или леса, где живот- ные могли бы, находится в жаркое время дня. К лагерю должны прилегать пастбища с хорошим травостоем.
Перед переводом в лагерь все поголовье осматривают, и в случае необходимости делают прививки.
При лагерном содержании широко распространено использо- вание пастбищ. Пастьба свиней сокращает затраты на уборку, транспортировку и раздачу кормов. Примерная суточная потреб- ность свиней в пастбище на одну голову в день следующая, м2: для хряков и маток – 5…10, подсосных маток с поросятами – 10…12, для молодняка старше 4 месяцев – 2,5…5.
Животных приучают к пастбищу постепенно, чтобы избежать расстройств пищеварения при переходе на зеленый корм и ожогов от солнечных лучей. В первые дни свиней выгоняют на пастбище на 20…25 мин, и постепенно увеличивают до 1 часа, после того как животное привыкает к пастбищному содержанию, время уве- личивают до 8 часов. Свиней пасут как правило 2 раза в день.
Следует иметь в виду, что пастьба животных не обеспечивает их потребности в питательных веществах, поэтому в рацион сви- ней вводят концентрированные корма, минеральные добавки,
а осенью и корнеплоды.
3.4. Промышленные свиноводческие комплексы. Поточная система производства свинины
При поточной системе производства свинины производствен- ный процесс должен быть непрерывным в течение года с ритмом 1…4 дня для комплексов на 25, 54, 108 тыс. свиней в год с ритмом, кратным 7 дням.
При поточной технологии объемы производства должны быть постоянные в течение всего периода эксплуатации предприятия.
Поточная система производства свинины позволяет повысить
эффективность использования маточного стада, помещений, обо- рудования, средств механизации, рабочей силы.
В зависимости от мощности предприятия различают четыре этапа технологического процесса:
- воспроизводство – осеменение маток, супоросный период, подготовка к осеменению ремонтных свиноматок;
- репродукция – получение поросят и лактация;
- доращивание – выращивание молодняка после отъема;
- откорм.
В основу поточной системы производства свинины заложено получение, выращивание и реализация крупных одновозрастных групп молодняка свиней через определенные промежутки време- ни.
Это обеспечивается:
- непрерывным ритмичным подбором однородных по числу и срокам осеменения групп свиноматок и получением одновоз- растных партий молодняка;
- формированием необходимого числа групп маток и свиней других возрастных групп;
- осеменением маток каждой группы в короткий, четко опре- деленный промежуток времени (ритм) без паузы;
- наличием специализированных помещений для каждого эта- па производственного процесса, разделенных на секции и исполь- зуемых по принципу «свободно – занято».
Для выращивания и откорма молодняка применяют одно-, двух- и трехфазную систему.
При однофазном содержании маток переводят в цех осемене- ния, а молодняк оставляют в этих же станках, доращивают и от- кармливают. Преимущества – исключаются стрессы, связанные с перемещением поросят, улучшается рост молодняка, уменьшаются затраты корма на 1 кг прироста. Недостатки – сложность проведе- ния дезинфекции, необходимы реконструируемые станки.
При двухфазной системе содержания поросят оставляют до передачи на откорм в тех же станках, где происходит опорос. Отъ- ем поросят проводят в 30 дней. В возрасте 3 месяцев поросят пе- реводят в цех откорма.
При трехфазном содержании поросят отнимают в возрасте 26, 30 и 42 дней и переводят в цех доращивания, а в возрасте 105…120 дней – в цех откорма.
Контрольные вопросы
1. Перечислите основные системы и способы содержания свиней.
2. Благодаря каким биологическим особенностям свиней можно быстро увеличить производство мяса?
3. Какие основные породы свиней разводят в России?
4. Как кормить и содержать супоросных и подсосных свиноматок?
5. Какие трудности существуют при выращивании поросят-сосунов и поросят-отъемышей?
6. Какие корма лучше использовать для мясного и беконного откорма?
7. Как уменьшить затраты на производство свинины в летний период?
8. Какие особенности у промышленного комплекса по откорму и выра- щиванию свиней?
9. Как осуществляется кормление свиней на промышленных комплек- сах?
10. Какие проблемы возникают при содержании свиней на промышлен- ных комплексах?
4. Технология производства овцеводческой продукции
4.1. Механизация кормопроизводства и кормления овец
Основным направлением в развитии овцеводства так же, как и в других отраслях животноводства, является интенсификация отрасли на базе специализации, концентрации, строительства крупных овцеводческих механизированных комплексов и ферм, внедрения передовой технологии и научной организации произ- водства.
В РФ уровень производства продукции овцеводства остается пока низким. Средний настриг шерсти составляет 2,2 кг на одну овцу, деловой выход ягнят на 100 маток – 74...79 голов, выход ба- ранины на одну матку – 20...22 кг в год. Отсюда и низкая произво- дительность труда.
Перед учеными и практиками-овцеводами стоит задача разра- ботать прогрессивную технологию по содержанию овец на ком- плексах промышленного типа, которая позволит обеспечить сни- жение затрат труда на производство 1 ц баранины до 10...12 ч
(в настоящее время 60...90 ч) и шерсти – 70 ч (300...400 ч). На мел- ких фермах добиться таких показателей невозможно.
С учетом направления и специализации хозяйств, климатиче- ских условий ведения овцеводства в настоящее время определи- лись основные системы содержания овец: круглогодовая стойло- вая, стойлово-пастбищная, пастбищно-стойловая и пастбищная.
Круглогодовая стойловая применяется в зонах интенсивного земледелия с хорошо развитым полевым кормопроизводством при отсутствии пастбищ. Овец содержат и кормят в помещениях и на выгульно-кормовых площадках, а летом – только на выгульно- кормовых площадках.
Стойлово-пастбищная – в условиях хорошо развитого поле- вого кормопроизводства с преобладанием продолжительного стойлового периода. Овец зимой содержат в овчарнях с выгульно- кормовыми площадками, а летом на пастбищах.
Пастбищно-стойловая – во всех зонах, где имеются зимние пастбища, заготавливается необходимое количество кормов для кормления маток в период ягнения и подкормки овец зимой и ран- ней весной. Пастбищный период преобладает.
Пастбищная – в районах с достаточным количеством паст- бищ, в том числе зимних.
Основой для повышения продуктивности и увеличения пого- ловья овец являются корма. Без наличия прочной кормовой базы невозможно успешно вести овцеводство.
В кормовую базу овцеводства входят выгульные угодья для подножного скармливания дикорастущих и сеяных трав, а также посевные площади под кормовые культуры для сена, сенажа, си- лоса, приготовления травяной муки, комбикормов и гранул.
Выгулы могут эффективно использоваться только в летний
и весенне-осенний периоды до наступления заморозков и возник- новения снежного покрова. В зимний период при содержании овец в отарах необходимо иметь достаточное количество сена, сенажа, силоса и других кормов.
Заготовка кормов впрок сейчас уже не сводится только к при- готовлению сена и силоса. На крупных овцеводческих комплексах, которые имеют большую концентрацию поголовья овец на не- большой территории, применяются и такие способы заготовки кормов, как сенажирование с применением химических консер- вантов, искусственная сушка травы, гранулирование. Приготовле- ние высококачественного комбикорма производится с добавлени- ем в измельченные зерновые концентраты различных кормовых добавок и премиксов, обеспечивающих сбалансированность их по питательности.
Заготовка различных зеленых кормов должна производиться в строгом соответствии с агротехническими сроками и зоотехниче- скими требованиями и с использованием передовых прогрессив- ных технологий. Это гарантирует заготовку высококачественных кормов.
В настоящее время скармливание заготовленных кормов ов- цам рекомендуется производить в составе кормосмесей, за исклю- чением сена, что позволяет составить полностью сбалансирован- ный по содержанию основных питательных веществ и витаминов рацион. Для приготовления кормовых смесей используется комби- кормовые цеха, в которых отсутствует только линия переработки корнеплодов. Для размещения комплекта оборудования строятся специальные кормоприготовительные цеха.
Содержание овец на крупных комплексах (5...10 тыс. голов) заключается в следующем. Животных содержат в моноблоках по
2,5 тыс. голов. Система содержания – пастбищно-стойловая с ис- пользованием долголетних культурных пастбищ, разбитых на загоны с изгородями и водопойными площадками. Для содержа- ния маток строят помещения, пригодные для ягнения и выращива- ния молодняка в любое время года. Для откормочного поголовья и содержания ремонтного молодняка и валухов строят открытые площадки, где летом откармливают молодняк и выбракованное поголовье, а зимой содержат ремонтный молодняк.
В помещениях, где содержатся матки с приплодом, необходи- мо поддерживать микроклимат в соответствии с зоотребованиями, который оказывает существенное влияние на продуктивность
и здоровье ягнят.
4.2. Механизация поения, раздачи корма и уборки навоза
В помещениях для содержания овец механизация поения, раз- дачи кормов, удаления навоза осуществляется теми же машинами, что и на других видах животноводческих ферм. Для поения овец и ягнят широко применяются бесклапанные поилки с емкостями для воды ГАО-4 на 25 л. Поилка обслуживает 324 головы в час. Ис- пользуется также комплект водопойного оборудования КВО-8 с электроподогревом воды, способный обслужить от 3 до
30 тыс. голов.
Для доставки воды и поения овец на пастбищах используется автопоилка передвижного типа ВУО-3, агрегатируемая с тракто- ром или автомобилем, способная обслужить до 1 тыс. голов.
Для доставки воды на пастбища используются водораздатчик унифицированный ВУ-3 с емкостью цистерны 3 м 3, транспортиру- емый трактором или автомобилем, автоцистерна АВВ-3,6 на базе автомобиля ГАЗ.
В овчарнях для ягнения и содержания овцематок с ягнятами раздача кормов осуществляется стационарными раздатчиками кормов с производительностью 6 и 5 т/ч соответственно.
На откормочных площадках, а также внутри помещений корм раздают мобильными кормораздатчиками.
Механизацию уборки навоза из овчарен и выгульных площа- док осуществляют скребковыми транспортерами ТСН-2Б, ТСН- 160, погрузчиками-бульдозерами ПБ-3,5 и погрузчиками фронтально-перекидными ПФП-1,2. Для резания и рыхления
уплотненного навоза применяют фрезы ФС-0,7 и унифицирован- ные фрезы ФЛУ-0,8 со сменными рабочими органами.
4.3. Механизация стрижки и купания овец
Основная цель овцеводства – получение шерсти. Обычно вы- ход шерсти в чистом волокне составляет 35...45% от массы гряз- ной натуральной шерсти. В зависимости от технологических свойств шерсть делят на однородную, получаемую от тонкорун- ных и полутонкорунных овец, и неоднородную, которую получают от овец грубошерстных и полугрубошерстных пород. Для произ- водства тонких камвольных тканей используется только однород- ная шерсть, имеющая одинаковые по толщине волокна
(23...50 мкм) и длиной 45...80 мм. Шерсть длиной 20...30 мм ис- пользуется для изготовления валяльных изделий и фетра.
Неоднородная шерсть состоит из грубых волокон (ости) диа- метром 40...120 мкм и переплетенных с ним и тонких волокон – пуха. Такая шерсть идет на изготовление грубого сукна, валенок, войлока.
Основное качество шерсти – крепость волокна – зависит от полноценности кормления животных.
Тонкорунных и полутонкорунных овец стригут один раз
в год – весной, грубошерстных и полугрубошерстных два раза –
весной и осенью, овец романовской породы стригут три раза в год – весной, летом и осенью.
В хозяйствах с большим поголовьем овец стригут в строгой последовательности. Первыми стригут овец с малоценной или за- грязненной шерстью, чтобы стригали восстановили утраченный навык стрижки, затем стригут маточное поголовье зимнего скота, затем молодняк рождения прошлого года, валухов (переярок), ма- ток весеннего скота и, наконец, баранов-производителей. Перед стрижкой овец в течение суток выдерживают без корма
и 10...12 часов без воды. На ночь их оставляют в помещении, что- бы шерсть не увлажнялась от дождя или росы (влажная шерсть в кипах саморазогревается и портится).
Стрижка овец – трудоемкая операция. При работе вручную ножницами опытный стригаль может остричь до 15...20 овец в день. Но при этом качество шерсти ухудшается из-за неравномер- ной длины волокон, возможны порезы кожи овец.
В настоящее время в России широко внедрена машинная стрижка – уровень механизации достиг 90%. При машинной стрижке, кроме увеличения производительности труда (до 60 овец в день), улучшается качество шерсти, на 8...13% увеличивается настриг шерсти за счет более низкого среза (на 200...300 г больше с одной овцы), снижается количество порезов кожи у овец, уменьшается количество сечки в руне.
Особенно важна роль механизированной стрижки овец в тон- корунном овцеводстве, где шерсть является основной продукцией.
Стрижка овец может производиться на столах, на специаль- ных столах-тележках с фиксацией ног животного и на полу. Суще- ствуют специальные прогрессивные приемы стрижки с минималь- ным количеством последовательных движений рук и операций
и отсутствия повторных проходов машинкой по одному и тому же месту.
Немаловажную роль при стрижке играет организация работ.
Стрижку всего поголовья необходимо закончить за 12...24 рабочих дня. В зависимости от количества поголовья организуют стригаль- ные пункты различной пропускной способности: на 12...24 ма- шинки. При этом пункты могут быть оборудованы в помещениях на базе кошар, передвижные, на скотопрогонных трассах.
Для механизации стрижки овец наибольшее распространение получили стригальные агрегаты ЭСА-12/200 на 12 стригальных машинок (рис. 10) с пропускной способностью 120 голов в час.
![]() |
Рис. 10. Стригальный агрегат ЭСА-12-200:
1 – машинка стригальная; 2 – электросеть низкого напряжения; 3 – крючки подвески машинки; 4 – преобразователь; 5 – кабель питания преобразователя; 6 – кабель питания заточного аппарата; 7 – заточной аппарат; 8 – провод заземления; 9 – штырь заземления
Применяется также стригальный агрегат ЭСА-6/200 на 6 ма- шинок с пропускной способностью 60 гол/ч. На каждом стригаль- ном пункте имеются точильные аппараты для заточки режущих пар стригальных машинок. Используются точильные аппараты ДАС-350, обеспечивающие заточку 30 пар в час, и ТА-1 такой же производительности. Для этой же цели служит комплект вспомо- гательного оборудования КВЗ-1 и разрабатываемый полуавтомат для заточки ножей ПЗН-60. Место слесаря-точильщика снабжается ванночками для режущих пар и приготовления наждачной смеси.
После стрижки полученную шерсть разбирают по сортам в за- висимости от ее качества. Для этого имеются столы для класси- ровки шерсти СКШ-200. Разобранную по сортам шерсть прессуют в кипы на гидравлических прессах, упаковывают в мешковину
и обвязывают проволокой.
Для стрижки и первичной обработки шерсти промышленность выпускает комплекты оборудования стригальных цехов.
Наибольшее распространение получили два типа цехов:
ВЦС-24/200 и комплект технологического оборудования КТО-24. Выносной стригальный цех ВЦС-24/200 представляет собой по- точную линию для комплексной механизации стрижки и первич- ной обработки шерсти в различных районах овцеводства. Его про- пускная способность 200 тыс. овец за сезон. Оборудование вклю- чает 24 стригальных машинки МСУ-200, входящих в состав агре- гата ЭСА-12/200, классировочный стол СКШ-200, гидравлический пресс ПГШ-1Б, точильный аппарат ТН-1, доводочный агрегат ДАС-350. В комплект включены транспортеры шерсти ТШ-0,5Б. Для привода стригальных машинок вырабатывается переменный ток частотой 200 с -1 и напряжением 36 В электростанцией СТН-12А (преобразователь частоты). Все оборудование размеща- ется под переносным укрытием УУП-500 размером 10×50 м, со- стоящим из сборного каркаса из труб, накрываемых брезентом.
Цех имеет три производственных (стрижки, обработки шерсти
и техобслуживания) и один бытовой участки, боксы для классиро- ванной шерсти БШ-16 и лабораторию для оценки качества шерсти с необходимыми приборами и оборудованием. Комплект техноло- гического оборудования КТО-24 аналогичен оборудованию
цеха ВЦС-24/200. После завершения стрижки каждая отара (800...1200 голов) проходит профилактическое купание, после чего ее направляют на летнее пастбище.
В овцеводческих хозяйствах проводится обязательная профи- лактическая обработка (купание) овец дезинфекционными раство- рами два раза в году: весной после стрижки и осенью перед поста- новкой на зимовку. Обработку проводят двумя способами:
- купанием животных в растворе;
- поверхностным опрыскиванием шерсти растворами.
Купание овец осуществляют в ваннах, а опрыскивание – в душевых установках. При купании овец обычно применяют эмульсию, приготовленную из 4 частей креолина, 1 части гек- сахлорана и 5 частей воды. Нагретый в бочке паром до 800 креолин тщательно перемешивается с гексахлораном до полного растворе- ния смеси, после чего добавляют воду.
Для приготовления рабочего раствора берут 2,5 части эмуль- сии на 97,5 части воды. Расход креолина на одну овцу в среднем 30 г. Температура раствора в пределах 25...300.
Промышленностью выпускаются стационарные установки для купания овец ОКВ, МКУ-1 и КУП-1, а также передвижные дезинфекционные установки ДУК-1 (смонтированная на шасси автомобиля ГАЗ) и ЛСД-3М (смонтированная на одноосном при- цепе) которые различаются по устройству и показателям работы.
Купочная установка стационарная с механическим окунанием овец ОКВ (рис. 11) предназначена для дезинфекционного купания поголовья на отгонных пастбищах с профилактической и лечебной целью. Механизированная купочная установка ОКВ состоит: из предварительного загона 1 с воротами; рабочего загона 2 с вы- пускными воротами, имеющего бетонированный пол и боковые бетонированные стенки с рельсовым путем; купочной ванны 13 вместимостью 20 м 3 с выпускными дверцами 6; двух отстойных площадок 4 с бетонированным полом, отстойниками 5 и выпуск- ными воротами; толкающей тележки 3; окунателя 12; смесителя 10; котла-парообразователя 8 с оборудованием 9 для сжигания жидкого топлива; насосной станции 7 с водопроводом; электроси- лового щита, канализационного устройства и рабочего инвентаря.
Установка МКУ-1 (рис. 12) состоит из загона 1, толкающей тележки 2 и рельсового пути 3, ванны для купания 11, рамы плат- формы 4, площадки для выкупанных овец 8, подъемной стенки ванны 10, насоса 12 и привода 13. Для приготовления эмульсии установка снабжена котлом 6 и смесителем 5.
Рис. 11. Конструктивно-технологическая схема установки ОКВ:
1 – загон для отары овец; 2, 4 – рабочий и отстойный загоны; 3 – толкающая тележка; 5 – отстойник; 6 – выпускные двери; 7 – насосная станция;
8 – котел-парообразователь; 9 – топливная аппаратура котла; 10 – смеситель;
11 – место оператора ванны; 12 – окунатель; 13 – ванна
![]() |
Рис. 12. Установка для купания овец МКУ-1:
1 – загон; 2 – толкающая тележка; 3 – рельсовый путь; 4 – рама погружной платформы, 5 – смеситель; 6 – парообразователь; 7 – отопительная система;
8 – площадка для выкупанных овец; 9 – люк для стока раствора; 10 – подъемная стенка; 11 – ванна для купания;12 – насос для откачки грязного раствора;
13 – привод платформы
Производственный процесс купания животных осуществляет- ся по следующей схеме. Оператор с помощью толкающей тележки подает на погружную платформу ванны 50...60 овец. Затем, поль- зуясь приводом, погружает платформу в ванну с раствором. Уста- новленная над платформой сетка позволяет погружать овец в рас- твор с головой в течение 2...3 сек, после чего платформу подни- мают на 15...20 см, и животные всплывают на поверхность. Вы- держав овец в растворе 2...3 мин, оператор поднимает платформу в исходное положение и выпускает овец на площадку для выкупан- ных животных. Производительность установки 700 овец в час, установку обслуживают три человека: механик-оператор, элек- трик-оператор и техник-ветеринар.
Установка КУП-1 имеет опрокидывающуюся платформу, с которой овцы падают в ванну с раствором гексахлорана, далее они через дверь ванны выплывают и выходят на площадку для стока жидкости. Раствор после купания 10...12 тыс. овец сливают, ванну чистят, а затем заливают водой. На следующий день вновь готовят раствор и заливают в ванну.
4.4. Механизация доения овец
Молоко овец по содержанию питательных веществ значи- тельно богаче коровьего. Если в коровьем молоке содержится 3...5% жира, то в овечьем – 6,5...7%. В овечьем молоке содержится 5% белков, около 4,5 молочного сахара, более 1 % минеральных веществ, т.е. в 1,5...2 раза больше, чем в коровьем молоке.
Молоко овец используют для переработки на брынзу и сыр, которые отличаются хорошими вкусовыми качествами и высокой питательностью.
Доят каракулевых овец в Казахстане и Средней Азии, овец других пород – в Дагестане, Закавказье, Молдавии и некоторых других районах.
Для доения овец созданы специальные доильные установки ДЗО-8, ДЗС-16, «Альфа-Лаваль», «SAC». Применение доильных установок позволяет значительно повысить производительность труда по сравнению с ручным доением.
Доильная установка ДЗО-8 предназначена для поточной ме- ханизированной дойки при пастбищном содержании овец. Она
может быть использована и как стационарная на овцеводческих фермах при стойлово-пастбищном содержании овец.
При доении на пастбище установка располагается на ровном месте, желательно в тени. Перед началом доения установку про- мывают в течение 1...2 минуты холодной водой.
Для доения овец загоняют в преддоильный загон партиями по 50...60 голов, откуда по трапу поочередно загоняют в клетки, уста- новленные на движущемся транспортере доильной установки.
Всего на транспортере имеется 20 клеток, движущихся по замкну- тому контуру в вертикальной плоскости. Овцы находятся
в 5...6 клетках верхней ветви транспортера.
Обслуживают установку 2 оператора. Первый надевает до- ильные стаканы на соски вымени овец, второй – производит меха- ническое додаивание, снимает доильные стаканы и по наклонному транспортеру возвращает доильный аппарат первому оператору.
Каждая овца выдаивается за время движения клетки от одного оператора до другого. Выдоенная овца выходит из клетки по наклонному трапу в загон для выдоенных овец.
После дойки всех овец доильные аппараты, бидоны и вся установка промываются.
Установка ДЗО-16 по устройству аналогична ДЗО-8, но имеет большую пропускную способность. Обе установки унифицирова- ны с доильной установкой ДА-100 для доения коров.
Для доения овец и коз используют установку «Альфа-Лаваль» с доением в ведра и молокопровод. Расположение молокопровода может быть вверху доильной установки и внизу. Нижнее располо- жение предпочтительнее, так как способствует поддержанию по- стоянного вакуума в доильной аппаратуре и молокопроводе, что обеспечивает быстрое выдаивание животных и предохраняет вымя от заболевания.
Система машин для механизации работ в овцеводстве преду- сматривает также машины и оборудование для забоя каракулевых ягнят и первичной обработки тушек, шкурок и сычуга.
Контрольные вопросы
1. Что входит в кормовую базу овцеводства и какие существуют спосо- бы заготовки кормов?
2. Какие типы машин используются для поения овец, раздачи корма и уборки навоза?
3. Какие доильные машины применяются для доения овец и в чем за- ключается технология их доения?
4. Какие агрегаты и установки применяются для стрижки и купания овец и в чем заключается технология их стрижки и купания?
5. Какие существуют системы содержания овец?
6. Назовите машины и оборудование, входящие в состав выносного стригального пункта ВСЦ-24/200.
7. Как часто следует купать овец?
8. Перечислите операции технологического процесса купания овец в установках ванного типа.
9. Какие купочные установки выпускаются промышленностью?
5. Технология производства птицеводческой продукции
5.1. Технология производства яиц кур
Технологический процесс производства яиц должен быть ор- ганизован таким образом, чтобы обеспечить максимальную про- дуктивность птицы и равномерное в течение года поступление продукции.
К основным принципам организации технологического про- цесса можно отнести:
- использование современных высокопродуктивных кроссов птицы;
- содержание птицы в безоконных птичниках, обеспечиваю- щих соблюдение необходимого микроклимата и светового режи- ма;
- круглогодовое производство яиц;
- многократное комплектование стада;
- работу по замкнутому или открытому циклу производства;
- применение новых ресурсосберегающих технологий.
Из технологических факторов, влияющих на продуктивность птицы, важны следующие: продолжительность светового дня
и интенсивность освещения, влажность и скорость движения воз- духа, температура окружающего воздуха, плотность посадки, фронт кормления и поения, численность поголовья сообщества.
Свет оказывает значительное воздействие на организм птицы: на газообмен, деятельность кроветворных органов, синтез витами- нов, содержание в крови кальция и фосфора, работу эндокринных желез, в том числе и половых. Он может тормозить или, наоборот, стимулировать развитие половых желез и их деятельность.
Наибольшее влияние на развитие половых органов оказывает продолжительность светового дня. Поэтому дополнительное освещение широко используют для стимулирования продуктивно- сти птицы. Однако удлиненный световой день способствует ран- нему половому созреванию птицы, что не всегда является положи- тельным. При раннем половом созревании птица несет мелкие яй- ца, снижается яйценоскость.
Постепенное сокращение светового дня в период выращива- ния птицы задерживает половое созревание, но способствует ее хорошему росту и высокой последующей продуктивности. При
более позднем начале яйцекладки куры дольше сохраняют ее на высоком уровне. При этом получают крупные яйца с крепкой скорлупой, характеризующиеся высокими инкубационными каче- ствами.
В связи с этим создают искусственный световой день, режим которого моделирует естественный световой день. Для растущего молодняка световой день постепенно уменьшают с 20-18 до 6-8 ч, а для несушек увеличивают до 15-18 ч к концу продуктивного пе- риода.
На физиологическое состояние птицы, ее продуктивность и поведенческие реакции оказывает влияние и интенсивность
освещения. Известно, что при излишней интенсивности освещения цыплята проявляют беспокойство и склонны к каннибализму.
Температура окружающего воздуха влияет на теплообмен в организме птицы, обмен веществ, газообмен и интенсивность окислительно-восстановительных процессов.
Существует зависимость между температурой воздуха в птичнике, температурой тела птицы и отдачей тепла во внешнюю среду. У птиц отсутствуют потовые железы, поэтому большая часть тепла теряется с водой, которая удаляется из организма при дыхании и с пометом. Курица массой 2,2 кг выделяет 7,48 г влаги и 17,6 ккал тепла в 1 ч.
Птица менее приспособлена к повышенным температурам, чем к пониженным. Увеличение температуры тела курицы на
2-3 0С по сравнению с нормой приводит к гибели.
Установлено, что при температуре воздуха в помещении выше 330С яйценоскость кур снижается на 18-20%, потребление корма на 15-20, а потребление воды увеличивается на 50-60%. Кроме то- го, уменьшается масса яиц и ухудшается их качество.
При низкой температуре усиливается обмен веществ в орга- низме и возрастает потребление корма, снижается яйценоскость и масса яиц, нарушается функциональная деятельность сердца
и легких, расстраивается регулирующая функция центральной нервной системы.
Для взрослых кур оптимальной считается температура возду- ха 16-180С. Для поддержания оптимальной температуры необхо- димо тщательно ее контролировать. Замеряют температуру в зоне размещения птицы не реже трех раз в сутки.
Наряду с температурой большое значение имеет влажность воздуха. Высокая влажность приводит к снижению переваримости питательных веществ корма, уменьшению содержания гемоглоби- на в крови. Поэтому пребывание птицы в помещениях с высокой влажностью воздуха и низкой температурой часто приводит к про- студным заболеваниям. При высокой влажности и температуре теплоотдача у птиц сильно затруднена, вследствие чего наступает перегрев организма и тепловой удар.
Воздух влажностью 50% считается сухим, вызывает раздра- жение слизистых оболочек дыхательных путей и глаз птицы, по- вышает хрупкость пера, усиливает потерю влаги организмом. Оп- тимальной влажностью воздуха при температуре 16-18 0С считают 60-70%.
Важнейшая составляющая микроклимата в птичнике – содер- жание в воздухе вредных газов, к которым относят диоксид угле- рода (С02), аммиак (NH3), сероводород (H2S). Они накапливаются в результате жизнедеятельности организма птицы и при разложении помета и подстилки.
Интенсивность газообмена у птицы значительно выше, чем у других животных, поэтому при дыхании выделяется значительное количество СО 2, которое зависит от вида, возраста и плотности посадки птицы. Повышенное содержание СО 2 в воздухе приводит к раздражению слизистых оболочек, общей слабости, вялости, уменьшению аппетита и, как следствие, снижению продуктивно- сти. Предельная концентрация диоксида углерода 0,25 %.
Аммиак образуется при разложении помета и мочи. Проникая в кровь, он снижает окислительные свойства гемоглобина, вызы- вая кислородное голодание птицы, что отрицательно действует на нервную систему. При низких температурах аммиак накапливается в нижних слоях воздуха. При повышенной влажности воздуха
(85-90%) испарение снижается и повышается его растворимость в воздухе, в результате чего газ распространяется по всему объему помещения. При совместном действии аммиака и водяных паров нарушается белковый обмен, уменьшается количество эритроци- тов и гемоглобина в крови, что приводит к анемии, а нередко и к гибели птицы. Предельная концентрация аммиака 15 мг/м3.
Сероводород – бесцветный газ с характерным запахом тухлых яиц. Он обладает самой большой токсичностью по сравнению с
другими газами, образующимися в птичниках. Даже в небольшой концентрации вызывает головокружение, сердцебиение, тошноту. Яд нервного действия. Вызывает смерть в результате наруше-
ния процессов дыхания. Действует на слизистую оболочку органов зрения и дыхания, на кожу, вызывая их раздражение. Поступая через легкие в кровь, сероводород нарушает деятельность элемен- тов крови, в первую очередь влияет на гемоглобин, вследствие че- го организм птицы испытывает кислородное голодание. Образует- ся сероводород при гниении белковых веществ помета и подстил- ки.
Предельно допустимая концентрация сероводорода 5 мг/м3.
При оценке чистоты воздуха в птичнике следует учитывать также его запыленность, особенно при содержании птицы на под- стилке. По происхождению пыль подразделяют на органическую и неорганическую. К первой относят пыль растительного (различ- ные виды муки, древесная) и животного происхождения (пух, во- лосы, шерсть); ко второй – пыль металлическую и минеральную.
Длительность нахождения пылевых частиц в воздухе птични- ков зависит от их размера и дисперсности. Особую опасность представляют частицы размером до 5 мкм, так как они свободно проникают в альвеолы легких и оседают в них. Пыль вредно дей- ствует на органы дыхания, слизистую оболочку глаз, состояние оперения. Предельно допустимая концентрация пыли в воздухе птичников 5-6 мг/м3.
Плотность посадки оказывает существенное влияние на про- дуктивные качества птицы и экономические показатели производ- ства. При увеличенной плотности посадки птица чаще болеет, снижаются ее жизнеспособность и сохранность. Оптимальная плотность посадки зависит от обеспеченности птицы кормами
и водой, соблюдения необходимого микроклимата, типа использу- емого оборудования и др.
Если птица обеспечена полноценными кормами, имеется до- статочное число кормушек и поилок, необходимое поступление свежего воздуха, то плотность посадки может быть увеличена.
При содержании птицы в клеточных батареях или на сетчатых полах применяют повышенную по сравнению с напольной систе- мой плотность посадки. Как правило, при содержании птицы в клетках плотность посадки выражают в сантиметрах квадратных,
приходящихся на 1 гол. (см 2/гол.), а при содержании на полу –
в головах на единицу площади пола (гол./м2).
Наряду с таким показателем, как плотность посадки, необхо- димо учитывать и величину сообщества, то есть численность по- головья в одной группе. Величина сообщества зависит от вида, пола и возраста птицы. Например, молодняк можно содержать большими сообществами, а взрослых самцов нет. Отмечено, что чем меньше птиц в одной группе, тем лучше растет молодняк
и выше продуктивность взрослого стада.
5.2. Выращивание ремонтного молодняка
Существует несколько систем выращивания ремонтного мо- лодняка: в клеточных батареях, на подстилке или сетчатых полах.
В России наибольшее распространение получило выращива- ние молодняка в клеточных батареях.
Для выращивания ремонтного молодняка яичных кур с суточ- ного до 120-дневного возраста применяют клеточное оборудова- ние такое как Carre-1600 (ООО «Энергогазсервис», г. Екатерин- бург), КП-35 (АО «Энергомера», г. Ставрополь) КВИ-1/4МШ (ОАО «ВИАСИМ», г. Санкт-Петербург), КБ-1600 (ООО «Уралсиб- агро», г. Тюмень), Урал («Уралтехномаш Плюс», г. Новоуральск), КБП-М (ОАО «ГОЗСА», г. Голицино), БМ («Липецкптицесер- вис»), оборудование копаний «Valli», «FACCO», «Tecno» (Италия), «Big Dutchman», «Specht», «Meller», «Hellmann»,
«Farmer Automatic» (Германия) и др.
Перед приемом (за 1-2 дня до поступления) суточных цыплят необходимо тщательно подготовить помещение. Птичник и обо- рудование моют, дезинфицируют и газируют, проверяют и нала- живают оборудование и механизмы, создают необходимую темпе- ратуру и влажность воздуха.
В первые дни у молодняка не развита терморегуляция, поэто- му создание оптимальной температуры – непременное условие, иначе неизбежны заболевания и повышенный отход.
Необходимо следить за температурой воздуха не только в по- мещении, но и в зоне нахождения птицы, то есть в клетках. Ее определяют не только по термометру, но и по поведению цыплят. Если им холодно, то они скучиваются и пищат; если жарко, то рассредоточиваются по всей клетке, раскрывают клюв, много
пьют. В ночное время цыплята находятся без движения и поэтому им требуется больше тепла, чем днем.
Температура корма и воды должна быть не ниже температуры окружающего воздуха. При поении птицы холодной водой часть энергии корма будет затрачена на ее согревание в желудке, кроме того, повышается вероятность простудных заболеваний.
В первые 3-5 дней цыплят содержат в клетках на «пеленках»: пол клетки застилают плотной бумагой в 5 слоев. Каждый день один слой убирают. Применение «пеленок» исключает травмы ла- пок, так как они не проваливаются через сетчатый пол клеток.
Очень важно сразу после посадки напоить цыплят. Это спо- собствует более полному выведению из организма мочевой кисло- ты, накопившейся в ходе эмбрионального развития. Кормить цып- лят можно только после того, как их напоили.
Поят цыплят из вакуумных поилок, добавляя в воду 7-8 % раствор глюкозы и аскорбиновую кислоту. Количество жидкости в поилке не должно превышать суточного потребления. Каждый день воду необходимо менять, а поддон поилки промывают, так как в нем накапливаются остатки корма. Одновременно с вакуум- ными заполняют водой и желобковые поилки. Они должны быть установлены таким образом, чтобы цыплята имели свободный до- ступ к воде.
Цыплятам дают только сухой корм – комбикорм в виде круп- ки (размером с пшено 2 мм), который насыпают в кормушки тон- ким слоем в 3 см, и одновременно (чтобы были видны отдельные крупинки) на «пеленки» в клетках. Чтобы у молодняка не было залипания клоаки, в первые 10 дней дают подсолнечное масло из расчета 0,1 г/гол. Со 2-7-го дня рекомендуется корм замешивать на свежем твороге до чуть влажного состояния и давать небольшими порциями по 5-6 раз в день.
С 15-го дня жизни цыплятам корм замешивают на обезжирен- ном молоке и вводят вареное яйцо (без скорлупы) из расчета
0,5 г/гол. в сутки.
Птичник или изолированный зал птичника должен заполнять- ся одновозрастной птицей (разница в возрасте не более 5 дней).
На выращивание принимают крепких, здоровых, подвижных цыплят не позднее 6 ч после выемки их из инкубатора. В связи с этим закладывают яйца в инкубатор с таким расчетом, чтобы вы- вод молодняка приходился на утренние часы. Перед инкубацией
проверяют полноценность яиц, затем их калибруют на яйцесорти- ровальных машинах по массе на 4-5 категорий с разницей 2-3 г. Более крупные яйца закладывают на инкубацию на несколько ча- сов раньше, так как они дольше прогреваются. Цель калибровки – получить равномерный вывод молодняка и одинаковых по массе цыплят.
Поступивший из инкубатора молодняк размещают в клетках, начиная с дальнего от входа конца клеточной батареи. В много- ярусных клеточных батареях суточных цыплят сажают в клетки сначала верхнего и среднего ярусов, а затем в 3-недельном воз- расте их рассаживают по всем ярусам.
Количество голов, помещаемое в одну клетку, зависит от кросса птицы, типа клеточного оборудования, рекомендуемой плотности посадки, фронта кормления и поения. Переуплотнение, а также недостаточный фронт кормления и поения приводят к ухудшению развития молодняка, снижению сохранности поголо- вья, а в дальнейшем к невысокой продуктивности.
В первые 2 нед. жизни молодняк кормят 5-6 раз, в 3 неделю – 4 раза, а затем 2 раза в сутки. Необходимо постоянно контролиро- вать потребление корма и воды и сравнивать их с нормативами.
Резкое отклонение этих показателей от нормы свидетельствует о нарушении режима выращивания или заболевании птицы.
Цыплят ежедневно осматривают. Обращают внимание на со- стояние оперения. Молодняк с сильно развитыми маховыми перь- ями (превышающими длину туловища) или плохо оперенный вы- браковывают. Птицу лучше осматривать после раздачи корма.
Слабые цыплята плохо подходят к кормушкам, у них тусклое взъерошенное оперение, учащенное дыхание, сонный вид, клоака часто загрязнена жидким пометом. Такой молодняк следует не- медленно выбраковывать из стада.
Огромное влияние на развитие курочек и их последующую продуктивность оказывают продолжительность светового дня и интенсивность освещения.
В настоящее время применяют как постоянное, так и преры- вистое освещение (периоды света чередуют с периодами темноты).
Чтобы создать равномерную освещенность на всех ярусах клеточной батареи, рекомендуется устанавливать на светильниках светорассеивающие плафоны. Светильники следует располагать на
одинаковом расстоянии друг от друга, лампы накаливания исполь- зовать только одинаковой мощности.
Для контроля за ростом и развитием молодняка выделяют не- сколько клеток из каждого яруса в начале, середине и конце кле- точной батареи. Молодняк, содержащийся в контрольных клетках, еженедельно взвешивают. На основании взвешиваний определяют однородность стада. Под однородностью понимают количество особей, выраженное в процентах, имеющих живую массу выше или ниже средней в пределах 10 % от массы всей взвешенной пти- цы. Например, стандарт живой массы в 11-недельном возрасте со- ставляет 1000 г. Однородной считается птица, имеющая живую массу в пределах от 900 до 1100 г. Из 100 взвешенных голов
15 имели массу или ниже 900 г, или выше 1100 г. Следовательно, однородность стада 85%.
Однородность в период выращивания молодняка должна быть не ниже 80%, а при переводе во взрослое стадо не менее 85 %.
В птицеводстве может наблюдаться такое явление, как канниба- лизм, то есть расклев птицей друг друга. Каннибализм существен- но ухудшает производственные и экономические показатели. Для его профилактики во взрослом стаде и уменьшения потерь вслед- ствие россыпи корма рекомендуется проводить обрезку клювов (дебикирование) в 6-10-недельном возрасте на специальном обо- рудовании.
При выращивании ремонтного молодняка особое внимание следует уделять петухам. Их тщательно отбирают по живой массе, развитию вторичных половых признаков, экстерьеру и качеству спермы.
В родительских стадах рекомендуется поэтапная система оценки и отбора петухов: первую оценку и отбор проводят при разделении цыплят по полу в инкубатории; вторую –
в 3-4-недельном возрасте при рассадке по ярусам клеточной бата- реи, отбирая лучших особей по экстерьеру, живой массе, развитию вторичных половых признаков; третью – в 9-10-недельном воз- расте; четвертую – в 16-17-недельном возрасте перед комплекто- ванием родительского стада.
Особое внимание обращают на экстерьер и живую массу сам- цов, которая должна быть в пределах стандарта кросса, на окраску и размер сережек, гребня и его состояние.
В некоторых птицеводческих хозяйствах делают обрезку гребня у петухов, так как при содержании их в клетках гребень часто травмируется, что приводит к стрессовому состоянию птицы и повышенной выбраковке. Эту операцию проводят в
5-6-недельном возрасте петухов после оценки и отбора их по вто- ричным половым признакам.
Отмечена положительная коррелятивная связь между разме- рами и развитием гребня в 5-6-недельном возрасте и воспроизво- дительными качествами петухов впоследствии. Чем раньше фор- мируется гребень, тем больших размеров достигнет он
в 22-недельном возрасте, тем лучше будут развиты семенники и выше качество спермы. Петухи, у которых вторичные половые признаки развиваются позже 5-6 нед. часто оказываются поздне- спелыми или стерильными.
Рекомендуется петушков и курочек с суточного возраста вы- ращивать раздельно. Петушков содержат или в отдельных пету- шатниках, или в специально переоборудованных для этих целей клеточных батареях.
При переводе птицы во взрослое стадо (в 110-120 дней) сна- чала в клетки помещают петухов, а затем кур. Отбирают самцов с хорошо развитыми вторичными половыми признаками и вырав- ненных по живой массе. В противном случае между самцами воз- никают драки, что приводит к каннибализму.
Половое соотношение петухов к курам при естественном спа- ривании 1:10. При искусственном осеменении нагрузка на петуха увеличивается до 40 кур.
Для искусственного осеменения петухов отбирают по эксте- рьеру и оценивают по качеству спермопродукции. Сперму полу- чают методом абдоминального массажа. Объем эякулята должен быть в пределах 0,4-0,9 мл, концентрация спермы не менее
4 млрд/мл, подвижность спермиев 8-9 баллов.
При совместном содержании в клетках петухи часто травми- руют кур когтями во время спаривания, что приводит к повышен- ному отходу и снижению яйценоскости. Поэтому рекомендуют обрезать когти у петухов или в суточном возрасте, или при пере- воде их во взрослое стадо.
5.3. Родительское стадо кур-несушек
Родительское стадо кур содержат на предприятиях- репродукторах и в отдельных случаях на птицефабриках с замкну- тым циклом производства. Основная цель при работе с родитель- скими стадами – получить максимальное количество ремонтного молодняка, идущего на ремонт промышленных стад.
Родительские формы (суточные цыплята или инкубационные яйца) завозят из репродукторов I порядка или племзаводов. Чис- ленность поголовья родительского стада зависит от мощности птицефабрики, размеров помещения, типа используемого обору- дования, яйценоскости птицы, инкубационных показателей яиц.
Размер родительского стада составляет от 8 до 15 % поголовья промышленных несушек.
Чтобы получать инкубационные яйца в течение года равно- мерно, применяют многократное комплектование родительского стада (от 4-до 12-кратного). Чем больше поголовье промышлен- ных несушек, тем больше размер родительского стада, тем чаще надо его комплектовать. Оптимальным считается 12-кратное ком- плектование.
Содержание кур родительского стада в клетках. В настоящее время родительские стада птицы яичных кроссов на птицефабри- ках содержат в основном в клеточных батареях. Наибольшее рас- пространение получили усовершенствованные отечественные комплекты клеточного оборудования КП-1Л (АО «Энергомера» г. Ставрополь), КВИ-3РН (ЗАО «ВИАСИМ», г. Санкт-Петербург), ТБР (Россия) и зарубежные комплекты клеточных батарей
«Big Dutchman», «Farmer Automatic» (Германия) и др.
Из цеха выращивания ремонтный молодняк переводят в
105-119-дневном возрасте. В этом возрасте птица, как правило, достигает половой зрелости. Птицу необходимо пересаживать до наступления яйцекладки. Перемещения в более старшем возрасте приводят к стрессу, задержке наступления яйцекладки и снижению продуктивности.
Одновременно с комплектованием стада проводят профилак- тические прививки. Курочек внимательно осматривают и отбира- ют по живой массе и экстерьеру. Для воспроизводства оставляют курочек и петушков с крепкими ногами, прямым килем, плотным оперением, блестящими глазами. За изменениями живой массы
следят по данным взвешивания птицы, находящейся в контроль- ных клетках.
За 10 ч до пересадки птицу прекращают кормить, но в воде не ограничивают. Каждый птичник укомплектовывают одновозраст- ной птицей с разницей в возрасте не более 5 дней. Продолжитель- ность процесса по пересадке ремонтного молодняка не должна превышать 5 дней.
При размещении молодняка в клетки следует строго соблю- дать плотность посадки.
Плотность посадки при содержании взрослой птицы, см 2/гол.: для петухов 750-800, кур родительского стада 650-750, кур про- мышленного стада 450-500; для кроссов с коричневой окраской оперения на 10-15 % ниже, чем для кроссов с белой окраской.
При комплектовании родительского стада петухов рекомен- дуют помещать в клетки на 2 дня раньше кур. Это позволяет пету- хам привыкнуть к новым условиям содержания и установить до- минирующее положение над курами. Подсадка петухов к уже раз- мещенным курам может привести к повышенной выбраковке пе- тухов и снижению оплодотворенности яиц. Половое соотношение в племенной сезон должно быть в пределах 1:9-11.
Переводимый в родительское стадо молодняк рекомендуется рассаживать с учетом его живой массы. В нижнем ярусе размеща- ют птицу со средней и нижесредней живой массой по стаду, в верхнем ярусе – со средней и вышесредней живой массой.
Важнейший фактор, влияющий на яичную продуктивность птицы, – световой режим. Разработано много вариантов световых режимов.
При первом варианте светового режима птицу кормят 4 раза в сутки: утром – сразу после включения света; днем – в 13 ч и 16 ч; вечером – за 1 ч до выключения света.
При втором варианте светового режима первый раз корма раздают сразу после включения света в птичнике (в 2 ч ночи), вто- рой раз – в 10 ч, третий – в 14 ч и четвертый раз за 2 ч до выклю- чения света. Второй вариант светового режима и кормления наиболее полно отвечает биологическим ритмам птицы: повыша- ется яйценоскость кур и оплодотворенность яиц.
При составлении графика комплектования родительского ста- да необходимо учитывать сохранность птицы, ее продуктивность, инкубационные качества яиц и показатели вывода молодняка.
Сохранность взрослой птицы обоих кроссов составляет 95-97 %, оплодотворенность яиц 93-94 %, вывод молодняка 78-79%.
Исходя из стандартных нормативов продуктивности роди- тельского стада кросса, определяют количество суточного молод- няка, получаемого от одной несушки, а, следовательно, и потреб- ность в поголовье родительского стада. Например,
к 30-недельному возрасту интенсивность яйцекладки составляет 90 %, или 27 яиц за месяц; пригодность яиц к инкубации (выход инкубационных яиц) – 90 %, или 24 яйца. Следовательно, при вы- воде молодняка 78 % от одной курицы получат 19 суточных цып- лят. Исходя из потребности в суточном молодняке, рассчитывают необходимое поголовье родительского стада.
Клетки желательно оборудовать гнездами, насестами и кор- мушками для подкормки петухов. Это очень важно, так как петухи подходят к корму позже кур и при ограниченном кормлении полу- чают меньше питательных веществ, чем требуется. Клеточные ба- тареи рекомендуется располагать яйцесборными лентами друг к другу.
Следует учитывать, что почти 90 % кур сносят яйцо до 12 ч
дня.
Поэтому собирать яйца следует чаще в первой половине дня,
но не менее 4 раз в день.
Содержание кур родительского стада на полу. Оборудование для напольного содержания кур родительского стада включает в себя: кормораздаточные линии; системы поения; системы, обеспе- чивающие поддержание микроклимата в птичнике; насесты, гнез- да, линии сбора яиц.
Птичник разделен на секции по 1000-2000 кур в каждой. Плотность посадки 4-5 гол./м 2 площади пола. Фронт кормле-
ния 10 см, фронт поения 3 см/гол.
Гнезда устанавливают из расчета 5 кур на одно гнездо. Недо- статок гнезд приводит к загрязнению и повреждению скорлупы яиц.
Следует регулярно следить за чистотой подстилки.
В качестве подстилки применяют древесные опилки, стружку, резаную солому, дробленые стержни початков кукурузы, лузгу семян подсолнечника, сфагновый торф. Расход подстилки за пери- од содержания несушек 8-10 кг/гол. Подстилку первоначально
насыпают слоем 5-10 см, а затем по мере ее загрязнения подсыпа- ют новую.
Принудительная линька кур. С помощью принудительной линьки можно увеличить срок использования родительского стада, исключить затраты на выращивание ремонтного молодняка. Яйце- носкость кур во второй период продуктивности снижается, но при- годность яиц к инкубации возрастает.
Принудительную, или искусственную, линьку проводят после
52 нед. первого продуктивного периода в течение 50-55 дней.
Вызывают линьку воздействием на птицу каких-либо стресс факторов, заключающихся чаще всего в резком изменении корм- ления, поения, светового режима.
Перелинявшей считается несушка, полностью сменившая пе- ро и восстановившая нормальную величину и окраску гребня.
Во второй период продуктивности высокая яйценоскость со- храняется на протяжении 5-6 мес.
Петухов искусственной линьке, как правило, не подвергают, так как они сильнее, чем куры, реагируют на стрессы. Поэтому к переярым курам рекомендуют подсаживать молодых петухов.
5.4. Промышленное стадо кур-несушек
Птичники для содержания промышленного стада кур должны быть оснащены техническими средствами для создания и регули- рования микроклимата и комплектами серийно выпускаемого оте- чественного или импортного оборудования, обеспечивающего комплексную механизацию основных технологических процессов. Оборудование используют в соответствии с инструкцией по экс- плуатации, прилагаемой заводом-изготовителем.
Полы в птичниках должны быть с твердым покрытием, как правило, бетонированные, стойкие к воздействию сточной жидко- сти и дезинфицирующих веществ.
Для равномерного производства товарных яиц промышленное стадо несушек в течение года комплектуют многократно по гра- фику через определенные промежутки времени. Количество пар- тий цыплят в год и молодок в каждой партии хозяйство устанавли- вает с учетом объема производства и вместимости помещений, предназначенных для содержания несушек, что отражается в тех- нологическом графике.
Для комплектования промышленного стада кур используют гибридных молодок не старше 17-недельного возраста, получен- ных от высокопродуктивных кроссов, живая масса и экстерьер ко- торых соответствует нормативам, установленным для данного кросса.
При размещении их сортируют так же, как и цыплят: молод- няк живой массой ниже средней по стаду помещают в нижний ярус; средней массой – в средний; выше средней – в верхний ярус.
Каждый зал должен быть заполнен одновозрастными молод- ками (допускается разница в возрасте кур в птичнике павильонно- го типа не более 5 дней, а в многоэтажных и сблокированных – не более 15).
Для периодического контроля живой массы несушек данной партии выделяют группу кур из части клеточной батареи, метят их ножными кольцами и взвешивают в 17-, 20- и 22- недельном воз- расте и далее раз в месяц на протяжении всего продуктивного пе- риода не менее 100 голов от одной партии из различных зон по- мещения. Это позволяет регулировать кормление птицы в зависи- мости от ее состояния, возраста и продуктивности. В возрасте
150 дней молодок переводят в группу взрослых кур. В акте пере- вода указывают дату вывода молодняка, кросс, линию, живую массу кур, процент яйценоскости и среднюю массу яиц в день пе- ревода. Кур промышленного стада используют в течение 52 недель продуктивности. Яйценоскость на среднюю несушку должна быть не ниже 230 яиц, сохранность поголовья – 95%, зоотехническая браковка не более 25%. Сбор яиц проводят 4...5 раз в день в чи- стую продезинфицированную тару. Первый сбор яиц проводят пе- ред утренней раздачей кормов.
В период эксплуатации кур подсаживать к ним других вместо выбывших не допускается.
Норма удельной площади подножной решетки для кур должна быть не менее 400 см/гол.
Фронт кормления должен составлять не менее 7 см на голову при свободном допуске к корму и не менее 10 см при ограничен- ном кормлении; фронт поения при использовании желобковых по- илок с проточной водой – 2 см, при использовании ниппельных и микрочашечных поилок – один ниппель или одна микрочашечка на 4...5 голов. Моют поилки не реже одного раза в сутки. Уровень воды в желобковых поилках должен быть 1,5-2 см.
Раздачу корма и уборку помета производят при выключенном свете.
Опыт птицеводческих предприятий показывает, что при этом яйценоскость кур повышается на 1,5…4%, расход корма на 10 шт. яиц уменьшается на 4…8%, расход воды сокращается на 45…60%, а электроэнергии на освещение – в 3 раза, себестоимость яиц сни- жается на 7…14%. При этом отмечается определенное улучшение качества продукции.
Уборку помета в клеточных батареях производят не реже
2 раз в сутки.
С увеличением возраста птицу периодически (в зависимости от уровня яйценоскости) внимательно просматривают в клетках и отбраковывают плохих несушек. Кур, продуктивность которых вызывает сомнение, вынимают из клетки и осматривают (по при- знакам хороших и плохих несушек).
Для каждого вида и возраста птицы, а также способа ее со- держания должно применяться соответствующее оборудование, позволяющее механизировать и автоматизировать все трудоемкие операции при строгом соблюдении условий конкретного техноло- гического процесса.
5.5. Механизация содержания промышленного стада кур-несушек
Кур-несушек промышленного стада содержат на специализи- рованных предприятиях в типовых птичниках.
Помещения для кур-несушек делают безоконными. Это поз- воляет строго соблюдать рекомендуемые световые режимы.
Полы в птичнике бетонированные, так как этот материал устойчив к агрессивным средам (помет, дезинфицирующие сред- ства).
Выбор оборудования, обеспечивающего поддержание опти- мального микроклимата, зависит от поголовья птицы, системы со- держания, а также от климатических условий зоны расположения птицефабрики.
При производстве пищевых яиц на птицефабриках, птицесов- хозах и птицефермах применяются два способа содержания кур- несушек – напольное и клеточное.
Напольный способ содержания преобладает в племенных хо- зяйствах и на мелких совхозных и колхозных фермах. Наибольшее применение в последние годы нашел клеточный способ.
Клеточное содержание дает возможность разместить кур- несушек в 3…4 раза больше, чем при напольном и снизить расход корма на 10…15%, благодаря ограниченному движению.
Содержание кур-несушек на полу. При напольном содержании кур используются широкогабаритные птичники. В этих птичниках содержат кур на глубокой подстилке, планчатых или сетчатых по- лах.
Кормление птицы осуществляется из бункерных самокорму- шек АСК. Корм из наружного бункера БСК-10 шнеком подается в бункеры-дозаторы цепочно-шайбового кормораздатчика КЦБ, ко- торый разносит его по кормушкам.
Поение производится из весовых чашечных поилок АПЧ-1,5. Поилки, кормушки и гнезда для кладки яиц установлены на план- чатом настиле. Сбор яиц из гнезд производится ленточным транс- портером.
Помет, проваливающийся под настил, убирается скребками и подается в поперечный транспортер.
Комплекты унифицированы между собой и отличаются толь- ко количеством оборудования и его компоновкой.
Управление всеми электродвигателями осуществляется стан- цией в соответствии с программой, заложенной в реле времени.
Отличительной чертой содержания промышленного стада кур-несушек является повсеместный переход на многоярусные клеточные батареи с повышенными показателями использования полезного объема птичников, их комплексной механизацией и ав- томатизацией процессов.
Механизация клеточного содержания кур-несушек. Для со- держания несушек применяют, как правило, групповые клетки, соединенные в клеточные батареи. Самый распространенный тип клетки для несушек – клетка площадью 0,5 м2, рассчитанная на 5-6 несушек яйценоских пород. Для содержания промышленного ста- да кур-несушек используют отечественные и зарубежные ком- плекты оборудования: КП-12ЛМ, КП-112ЛМ (АО «Энергомера», г. Ставрополь), КВИ-4Н, КВИ-4НШ (ЗАО «ВИАСМ», г. Санкт- Петербург), БН-4НШ (АО «Липецкптицесервис»), «Big Dutchman», «Specht» (Германия) и др.
В двухрядных четырехъярусных клеточных батареях механи- зирован процесс раздачи корма (влажность до 30%) с применени- ем навесного бункерного кормораздатчика. Использована желоб- ковая система поения. Для уборки помета с шиферных (армиро- ванное стекло) настилов каждого яруса смонтирована канатно- скребковая установка. Сбор яиц выполняют одновременно с раз- дачей корма.
Во всех серийных клеточных батареях для содержания про- мышленного стада кур-несушек система раздачи корма не рассчи- тана на проведение режимного кормления, обеспечивающего по- лучение продукции с минимальными затратами кормовых средств.
5.6. Механизация обработки продуктов птицеводства
Птицеводческие хозяйства, как правило, имеют прямые тор- говые связи с магазинами и отвозят им свою продукцию, минуя перерабатывающие предприятия. Поэтому обработка яиц и птицы производится непосредственно в хозяйствах.
Механизация обработки яиц. Яйца в птичниках собираются с помощью различного типа транспортеров и привозятся на яй- цесклад. Загрязненные яйца подаются на яйцемоечную машину (рис. 13). В машинах М-4М, ЯМ-3000М, ЯМУ, Роса 16-6, Спрут-05 они моются с помощью воды и капроновых щеток и высушивают- ся вентилятором, подающим горячий воздух.
![]() | ![]() | ||
а б
Рис. 13. Яйцемоечная машина:
а – ЯМУ-Ф-10А; б – ЯМ5-05
Оператор укладывает загрязненные яйца на загрузочные лотки, установленные под небольшим углом. По ним яйца скатываются к обрезиненному шнеку. Над лотком установлен
увлажнитель-патрубок с отверстиями для замочки яиц. При вра- щении шнека с частотой 28 мин -1 яйца передвигаются между направляющими. Расположенные над шнеками капроновые щетки, вращаются с частотой 570 мин -1, очищают яйца. В конце машины установлены электронагреватели для сушки яиц. Со шнеков яйца попадают на разгрузочный транспортер и с него на транспортер, подающий их к сортировальной машине.
Следует отметить, что общая установленная мощность элек- тропотребителей яйцемоечной машины ЯМУ составляет 36,1 кВт (электрокалориферы СФСА-25/0, 5ТЦ-М2/1 – 25 кВт, трубчатые электронагреватели 10,5 кВт и электродвигатель мощностью
0,6 кВт).
Машины для сортировки яиц ЯС-1, МСЯ-1М и ЯСМ. Машина ЯС-1 (рис. 14) предназначена для сортировки яиц по массе, марки- ровки их с указанием категории и даты. На корпусе машины уста- новлены: накопитель, подающий транспортер с загрузочным сто- лом и овоскопом, весовой механизм, механизмы маркировки, при- вода и приборы управления. На овоскопе отбирают (вручную) не- кондиционные яйца.
![]() |
Рис. 14. Яйцесортировочная машина ЯС-1:
1 – раздаточный механизм, 2 – весовой механизм; 3 – овоскоп; 4 – подающий транспортер; 5 – ограждение стола
Более производительная машина (рис. 15) МСЯ-1М, по суще- ству, включает две установки, подобные ЯС-1, имеет аналогичные сборочные единицы и выполняет те же операции, но с разделени- ем яиц на пять категорий (вместо трех). Сортировочные столы приставлены к корпусу машины с обеих сторон, и яйца на сорти- ровку идут двумя потоками.
![]() |
Рис. 15. Яйцесортировочная машина МСЯ-1:
1, 6 – сортировочные столы, 2 – транспортер отсортированных яиц; 3 – весовые механизмы; 4 – овоскоп; 5 – стол для несортированных яиц
Машина ЯСМ-2 выполняет автоматическую сортировку и маркировку яиц с производительностью, равной производительно- сти МСЯ-1М (до 9000 яиц/ч), но при этом число обслуживающего персонала сокращено на 33%. Сортированные яйца укладываются в картонные литые или бугорчатые прокладки по 30 штук. Про- кладки с яйцами укладываются по 360 штук в картонные коробки.
Тара, предназначенная для хранения яиц, не должна иметь по- сторонних запахов. В помещении для хранения яиц должна под- держиваться температура 8…120С. Транспортировка яиц произво- дится в специальных автомашинах рефрижераторах.
Механизация убоя и обработки птицы. На крупных птице- фабриках устанавливаются специальные механизированные
и автоматизированные линии для убоя и обработки птицы. Перья после обработки сдаются на пухово-перовые фабрики.
На птицеперерабатывающих предприятиях и в убойных цехах птицефабрик и других птицеводческих хозяйств применяются сле- дующие конвейерные линии:
- линия убоя и переработки бройлеров В2-ФЦЛ (3000 гол./ч);
- линия убоя и переработки бройлеров К7-ФЦЛ-1,5
(1500 гол./ч);
- линия убоя и переработки кур и цыплят Б2-ФЦЛ-1,5
(1500 гол./ч);
- линия убоя и переработки кур и цыплят В2-ФЦЛ-0,5
(500 гол./ч);
- унифицированные линии убоя и переработки кур, цыплят, бройлеров:
- К7-ФОЛ (2000 гол./ч);
- К7-ФОК (1000 гол./ч);
- К7-ФЦЛ-0,5 (500 гол./ч);
- линия убоя и переработки уток и утят В2-ФУЛ (2000 гол./ч);
- линия убоя и переработки кур, цыплят и уток К.7-Ф02-Л
(2000 гол./ч кур и цыплят, или 1300 гол./ч уток);
- линия убоя и переработки кур, цыплят и уток В2-Ф02-К
(1000 голов/ч кур и цыплят, или 650 голов/ч уток);
- линия убоя и переработки птицы (в санитарных целях) В2-ФЦЛ-0,5С (500 гол./ч);
- линия убоя и переработки индюшат В2-ФИЛ (1000 гол./ч);
- автоматизированная линия конструкции ВНИИПП для обра- ботки птицы (3000 гол./ч бройлеров, кур и цыплят, или 2000 гол./ч уток);
- линия убоя и переработки бройлеров В2-ФЦЛ-6
(6000 гол./ч).
Технологический процесс обработки птицы включает следу- ющие операции: прием и навешивание птицы на конвейер; глуше- ние птицы; убой и обескровливание; ослабление удерживаемости оперения (обработка горячей водой); удаление оперения; полупо- трошение и потрошение тушек; туалет и формовку тушек; сорти- ровку и маркировку тушек; упаковку тушек и маркировку ящиков, фасовку тушек; холодильную обработку мяса; транспортировку мяса.
Птицу в передвижных тележках доставляют на приемную площадку отделения. Тележки устанавливают над приемным ко- нусным бункером, находящимся над ленточным транспортером. Птицу выгружают на ленточный транспортер при помощи вы- движных полов тележек, начиная с нижнего яруса. Из тележек птица попадает на движущуюся ленту транспортера, которая про- ходит в отделение, где птицу с приемного неподвижного лотка навешивают на конвейер обработки.
Аппарат для электрооглушения РЗ-ФЭО –универсальный (рис. 16). Прямоугольный корпус аппарата выполнен из винипла- ста. В корпусе размещены электроды: одна нижняя контактная пластина, передвигающаяся по вертикали, и неподвижный верх- ний электрод в виде прутка. Верхний электрод смещен относи- тельно оси аппарата так, чтобы подвеска отклонялась от своей вертикальной оси на 20-25 мм, что необходимо для лучшего кон- такта. Голова птицы касается электродов нижней контактной пла- стины, и электрическая цепь замыкается. Аппарат подключается к сети переменного тока 220 В.
![]() |
Рис. 16. Аппарат для электрооглушения птицы:
1 – стойка; 2 – ванна; 3 – углубление для стока воды; 4 – направляющая;
5 – щитки; 6 – резервуар ванны; 7 – каркас подвесного конвейера;
8 – направляющая каретки; 9 – лебедка; 10 – электрический блок; 11 – каретка
После оглушения птицы конвейером подают к месту убоя машиной В2-ФЦЛ-6/4 и обескровливания над желобом В2-ФЦЛ/3. Последний состоит из 9 отдельных секций. Первая секция имеет щиты из органического стекла (это позволяет наблюдать за наполнением нерабочей части секции кровью), а последняя осна- щена патрубком для стока крови.
Аппарат для тепловой обработки тушек К-7-ФЦЛ-6/5-01
(300 гол./ ч) состоит из двух секций, соединенных между собой. Над ванной конвейер делает четыре витка. Горячая вода 3 центро- бежными насосами нагнетается в боковые водораспределители коробчатой формы, снабженные с внутренней стороны заслонка- ми, при помощи которых регулируется каскад воды, орошающий тушки.
Машина для удаления оперения с тушек птицы (рис. 17) со- стоит из рамы и двух симметрично расположенных корпусов. В каждом корпусе смонтированы дисковые рабочие ряды.
![]() |
Рис. 17. Дисковый автомат для снятия оперения с тушек птицы 1 – корпус; 2 – опора; 3 – дисковый ряд; 4 – шкив; 5 – клиновой ремень; 6 – подшипниковый узел диска; 7 – перосъемный диск с пальцами
На концах валиков закреплены рабочие диски, оснащенные резиновыми рифлеными пальцами. Тушки птицы, закрепленные в подвесках пространственного конвейера, продвигаются вдоль ра- бочих рядов, и пальцы удаляют оперение со всей поверхности ту- шек, орошаемых теплой водой. Удаленное перо подается водой в гидрожелоб.
Машина для отрезания ног (В2-ФЦЛ-6/9) состоит из рамы, ножей и пилы. В верхней части машины расположены дисковые ножи, плоский нож, дисковая пила, приводные, натяжные и откло- няющие звездочки цепей с пластинами и направляющая с водораз- брызгивающим устройством.
Тушки после отделения от них ног падают в наклонный лоток, с которого попадают на ленточный транспортер, подающий тушки к месту навешивания на конвейер потрошения. Ножки продвига- ются подвесками ко второй движущейся цепи и стационарной направляющей и поступают к дисковым пилам, при помощи кото- рых их разрезают на две части.
Линия потрошения состоит из пространственного подвесного конвейера; ленточного транспортера; рабочего места ветеринарно- санитарного эксперта; системы желобов; двух машин для разреза- ния и мойки желудков; двух машин для снятия кутикулы с желуд- ков кур, цыплят и бройлеров; двух аппаратов для удаления легких и почек; трех охладителей субпродуктов; машины для отделения голов; бильно-моечной машины.
Контрольные вопросы
1. Какова технология производства яиц?
2. Как комплектуется промышленное стадо кур-несушек?
3. Расскажите о механизации содержания промышленного стада кур- несушек на полу.
4. Какое оборудование относится к общецеховому назначению?
5. Какими параметрами характеризуется микроклимат в птичниках?
6. Каковы граничные пределы параметров микроклимата в птичниках и какова периодичность их контроля в птичниках?
7. Какова технология обработки яиц?
8. Дайте характеристику яйцемоечным и сортировочным машинам.
9. Расскажите о технологии и механизации убоя и обработки птицы.
6. Механизированные технологические процессы
6.1. Классификация технологических процессов
Животноводство по своей организационно-экономической структуре близко подходит к промышленному производству: круглогодовой производственный процесс, строгая ритмичность в работе, определенный распорядок дня на ферме или комплексе, постоянный штат обслуживающего персонала, стационарное обо- рудование, электричество как основной вид энергии. Однако, не- смотря на ряд общих черт с комплексом промышленного типа, между ними имеются существенные различия.
Если промышленное предприятие представляет собой за- мкнутую динамическую инженерно-техническую систему «чело- век – машина» с детерминированной обратной связью, то живот- новодческий комплекс (ферма) является биотехнической системой
«человек – машина – животное» с независимым активно действу- ющим биологическим звеном. Такая система значительно услож- нена тем, что включает в себя животных, которые в процессе про- дуцирования подчинены своим внутренним физиологическим и биохимическим законам. Этими законами человек еще не научил- ся управлять так полно и оперативно, как того требуют условия промышленного производства, построенного на основе законов физики, механики и математики. Человек-оператор – ведущее зве- но в системе «человек – машина – животное». Алгоритмы управ- ления в такой системе, как правило, носят вероятностный харак- тер. Эффективность работы системы в целом зависит прежде всего от того, насколько оптимальны связи и взаимодействия между её звеньями. На рисунке 18 представлена структурно-техноло- гическая схема процесса производства продуктов животноводства. В животноводстве человек может воздействовать на кормовое сы- рье только лишь через животное (в отличие от фабрично- заводского производства), которое в данном производстве выпол- няет одновременно две функции, будучи одновременно предметом труда (выращивание, откорм) и средством труда (продуцирование молока, живой массы, мяса). Это отличие имеет принципиальное значение и дает основание условно разделить технологию произ- водства продуктов животноводства на две части – зооинженерную (биологическую) и инженерно-техническую (машинную).
Рис. 18. Структурно-технологическая схема процесса производства продуктов животноводства
Это отличие имеет принципиальное значение и дает основа- ние условно разделить технологию производства продуктов жи- вотноводства на две части – зооинженерную (биологическую) и инженерно-техническую (машинную).
Таким образом, производственный процесс – это сложная си- стема, включающая в себя ряд подсистем, расположенных на раз- ных уровнях. Примем следующие обозначения: О – оператор,
М – машина, Ж – животное, С –среда, М т – материал.
Подсистемы первого уровня – биотехническая О - М - Ж
С
и две технические
О - М - М т ,
С
О - М - М т
[С ]
– представляют со-
бой совокупности технологических процессов, отличающихся между собой силой связи с внешней средой и наличием или отсут- ствием в своем составе биологического звена – животного.
По силе влияния на продуктивность животных (птицы) маши- ны и оборудование, применяемые на фермах, делят на две основ- ные группы: первая – машины, непосредственно связанные с об- служиванием животных (доильные установки, кормораздатчики, стригальные агрегаты и др.), вторая – машины, непосредственно не связанные с обслуживанием животных (кормозаготовительные и кормоприготовительные машины, оборудование для первичной обработки молока и др.).
Поданным Г. М. Кукта, в технике, используемой на животно- водческих фермах и комплексах, машины и оборудование первой
группы составляют более 60%. Первая подсистема О - М - Ж
С
первого уровня – биотехническая – сильно связана с внешней сре- дой. Она включает в себя такие технологические процессы, как доение коров, стрижка овец, поение, раздача кормов, уборка наво- за, создание микроклимата, санитарно-гигиеническое обслужива- ние и др.
Технологические процессы, на протекание которых сильное влияние оказывает взаимодействие со средой, выделены во вторую
подсистему
О - М - М т . При эксплуатации оборудования требу-
С
ется строго учитывать как вредное влияние среды на технику, так
и отрицательное воздействие некоторых технологических процес- сов на окружающую среду.
В подсистемах [С] – означает, что внешняя среда оказывает незначительное влияние на оборудование технологических про- цессов. Подсистемы второго уровня отображают структуру и связи внутри отдельных технологических процессов, а также состав
и характер рабочих операций.
Любой технологический процесс – это совокупность последо- вательных операций, в процессе выполнения которых материал меняет свое место, свойство, качество. Он включает операции тех- нологические, транспортные и вспомогательные (контроль каче- ства, взвешивание, мойка, дезинфекция и т.п.).
При поточной организации производства продукт, получен- ный в результате работы предыдущей машины, является исходным материалом для последующей машины. Операции на всех рабочих местах выполняются в промежутке времени, равном или кратном ритму потока, при непрерывном движении обрабатываемого мате- риала.
Схема поточной линии в простейшем случае имеет вид це- почки, в каждое звено которой поступает поток подачи и выходит из него поток расхода (рис. 19). Если между некоторыми звеньями устанавливают промежуточные регулирующие емкости (бункера- накопители и т.п.), то совокупность звеньев, расположенных меж- ду двумя промежуточными емкостями, составляет участок данной поточной линии.
![]() |
Рис. 19. Схемы поточных линий:
а – с жёсткой связью; б – с гибкой связью; в –с полу гибкой связью; г – со сходящимися потоками; д – с параллельным соединением
Построение технологического процесса начинают с определе- ния основной операции и далее состава и последовательности опе- раций, которые включаются в ту или иную линию, изображаемую в виде технологической схемы.
6.2. Рабочие и функциональные схемы технологических процессов
Поточные линии создаются на основе заранее отработанных технологических процессов для каждого типа производства. По- точно-технологические линии (ПТЛ) в зависимости от назначения могут быть изображены в различных схемах: технологических (операционных), конструктивно-технологических, структурных или информационных (кибернетических).
Технологическая схема представляет собой краткое описание порядка и последовательности выполнения отдельных операций ПТЛ без указания типа и марки машины, осуществляющей ту или иную операцию. Иногда такая схема представляется перечислени- ем операций, связанных друг с другом стрелками. Например, тех- нология обработки корнеплодов может быть представлена такой схемой: мойка – измельчение – дозирование – смешивание – выда- ча готовой продукции в транспортные средства.
На рисунке 20 показана технологическая схема производства молока, включающая основные поточно-технологические линии, типичные для молочной фермы. Состав и последовательность опе- раций выбирают с учетом зоотехнических требований к качеству конечных продуктов, новейших достижений науки и техники,
а также передового отечественного и зарубежного опыта.
Конструктивно-технологическая схема отражает конкретный состав машин, включенных в ПТЛ, и представляется в техниче- ской документации, отображающей технологические процессы, (рис. 21).
Структурные схемы ПТЛ (рис. 22) отражают внутреннюю структуру производственных потоков, соподчиненность отдель- ных элементов, участков или секций, показывают направление по- токов, а также управляющих воздействий и команд, наличие и ме- сторасположение регулирующих емкостей и резервирующих средств.
Рис. 20. Технологическая схема производства молока на ферме
![]() |
Рис. 21. Конструктивно-технологическая схема уборки навоза
От правильности выбора структуры ПТЛ зависят прежде все- го надежность работы всей линии и ее технико-экономические по- казатели.
Любая ПТЛ состоит из определенных структурных элементов: машин, транспортирующих и грузоподъемных механизмов, участ- ков или секций, а также регулирующих и запасных емкостей.
Наличие тех или иных элементов, их взаимосвязь между собой
и материальным потоком определяют характер функционирования поточной линии как системы массового обслуживания.
В качестве примера рассмотрим структуру и опыт работы ПТЛ приготовления жидких кормов в кормоцехе на репродуктор- ной ферме, имеющей следующие технологические участки: дози- рования и загрузки комбикормов и травяной муки в расходные бункеры, выгрузки комбикормов и травяной муки в смесители, смешивания, выдачи и транспортирования готовых кормов в сви- нарники (рис. 22). Имеется также линия приема и загрузки комби- кормов и травяной муки в силосы (хранилища).
![]() |
Рис. 22. Структурная схема поточной линии приготовления жидких кормов на репродукторной свиноферме:
1 – кормовой загрузчик; 2 – приемный бункер;
3, 5, 6, 9, 10, 11, 12, 17, 19 – транспортеры; 4 – нория; 7 – хранилище; 8 – дозатор;
13, 15, 16, 24 – бункеры; 14, 18 – весы; 20 – насос; 21 – смеситель; 22 – котлы;
23 – кормопроводы; 24 – бункеры-накопители
Комбикорма и травяная мука доставляются транспортом, по- даются загрузчиком 1 в приемный бункер 2, затем транспортерами 3, 5, 6 и норией 4 направляются в силоса общей емкостью
1200 м3.
При приготовлении кормов травяная мука и комбикорма вы- гружаются из силоса дозаторами 8, транспортерами 9, 10, 11, 12 и норией 4, подаются на весы 14, после чего загружаются в рас- ходные бункера 15, 16.
Из этих бункеров транспортерами 17, 19 комбикорма и травя- ная мука подаются в смесительное отделение, где они смешивают- ся с водой лопастными смесителями 21 периодического действия.
Влажность приготовленного корма должна составлять 82...84%.
Вода подается насосом 20.
Приготовленная кормовая смесь сливается в продувочные котлы 22, а затем кормопроводом 23 под давлением подается в бункеры-накопители 24, находящиеся в свинарниках.
6.3. Технические средства для осуществления технологических процессов
Технологическое оборудование ферм и комплексов можно условно разделить на следующие группы: машины, аппараты, ме- ханизмы, агрегаты и установки.
Любая технологическая (рабочая) машина представляет собой совокупность трех механизмов: двигателя (источника энергии), передаточного механизма (трансмиссии) и исполнительного меха- низма (рабочего органа).
Механизм – это последовательное соединение звеньев, слу- жащих для преобразования одного вида движения в другой вид. Например, храповой механизм служит для преобразования враща- тельного движения в поступательное.
Двигатель служит источником энергии (механической, тепло- вой, гравитационной, электрической и др.) или энергетическим средством машины. В животноводстве преобладают электрические асинхронные двигатели с короткозамкнутым ротором.
Передаточный механизм (трансмиссия) служит для передачи энергии.
Исполнительный механизм преобразует движения (энергию), осуществляемые рабочими органами машины. Иногда эти функ- ции выполняют рабочие органы, возможно и совмещение или за- мещение воздействий на объект.
К примеру, возьмем доильную машину. Она включает элек- трический двигатель, вакуумный насос, вакуумпровод и доильный аппарат. В ней электрический двигатель – энергетическое сред- ство, вакуумный насос – источник энергии, вакуум-провод транс- миссия, стакан доильного аппарата – рабочий орган исполнитель- ного механизма.
Аппараты – доильный аппарат, пастеризатор, режущий аппа- рат осуществляют непосредственное воздействие (силовое,
тепловое, гравитационное, электрическое и др.) на обрабатывае- мые объекты.
Агрегат объединяет в себе несколько различных машин, устройств, механизмов и аппаратов, например, электростригаль- ный агрегат ЭСА-12/200, агрегат ОГМ-1,5 для гранулирования травяной муки.
Комплект оборудования – это набор машин, предназначенный для комплексной механизации одного или нескольких технологи- ческих процессов, например, комплекты оборудования ОЦК-4, ОЦК-8 для комбикормовых цехов, КОРК-15 – комплект оборудо- вания для приготовления рассыпных кормосмесей.
Установка представляет собой совокупность механизмов, ма- шин, агрегатов и аппаратов. Она, как правило, монтируется на фундаменте и отвечает определенному назначению. Например, доильная установка УДА-8А «Тандем», УДА-16А «Елочка», теп- лохолодильная установка ТХУ-37, купочная установка ОКВ для дезинфекционной обработки овец и др.
Контрольные вопросы
1. На основании чего все машины и оборудование в животноводстве делятся на две группы?
2. Дать определение технологического процесса.
3. В виде каких схем можно изобразить любую поточно- технологическую линию?
4. Какие технические средства имеются в животноводстве для осу- ществления технологических процессов?
5. Что понимается под системой машин для животноводства?
6. Каковы пути совершенствования системы машин?
7. Каков уровень комплексной механизации в животноводстве?
7. Машины и оборудование для приготовления кормов и кормовых смесей
7.1. Виды кормов, применяемых в животноводстве, и их характеристики
Решающая роль в развитии животноводства принадлежит сбалансированной кормовой базе, организации полноценного кормления животных, обеспеченности их высококачественными кормами. Корма, производимые в хозяйствах и выпускаемые про- мышленностью, значительно различаются по своему назначению, составу и питательности, физическим и технологическим свой- ствам (рис. 23).
Для удобства планирования кормовой базы и рационального использования кормов их объединяют в группы, близкие по ос- новным показателям (исходному сырью, технологии приготовле- ния, питательным и кормовым достоинствам, физиологическому воздействию на организм). Для практических целей наиболее удобно такое их деление: растительные корма (рис. 24), побочные продукты промышленности и пищевые отходы, корма животного и микробного происхождения, комбикорма, белково-витаминные добавки (БВД), заменитель цельного молока (ЗЦМ), небелковые азотистые соединения, минеральные и витаминные добавки.
![]() |
Рис. 23. Классификация кормов
Рис. 24. Классификация растительных кормов
Зеленые корма. В эту группу входят травы естественных и ис- кусственных лугов и пастбищ, сеяные злаковые и бобовые культу- ры, ботва корнеклубнеплодов и бахчевых, гидропонный корм.
Отличительная особенность зеленых кормов – высокая влаж- ность (70-83%). Сухое вещество их отличается высоким содержа- нием протеина, минеральных веществ и витаминов. Оно содержит 13-25% сырого протеина, 4-5% сырого жира, 15-18% клетчатки, до
45% БЭВ и 8-11% сырой золы.
По содержанию энергии (1,0-1,2 МДж обменной энергии) и переваримого протеина (120-220 г/кг) сухое вещество зеленых кормов близко к растительным концентратам, но превосходит их по биологической ценности протеина и содержанию витаминов. В процессе вегетации растений их питательная ценность меняется: снижается содержание протеина, каротина и повышается клетчат- ки, вследствие чего снижается переваримость и энергетическая ценность.
Питательная ценность зеленых кормов зависит от ботаниче- ского состава трав, условий и места их произрастания, агротехни- ки выращивания, цикла (времени) стравливания пастбищ.
Грубые корма естественной и искусственной сушки. К ним относятся сено естественных и сеяных трав, сенная мука, травяная мука, резка из искусственно высушенных трав, сенаж, все виды соломы, мякина (полова), шелуха, веточный корм, хвойная мука.
Основным показателем, характеризующим эту группу кормов, является высокое содержание клетчатки: в сене – 18-32%, в соломе – до 42, в мякине – 25-35, в травяной муке и резке – 15-28, в сенаже – 13-16%.
Питательность разных видов кормов этой группы зависит как от содержания в них клетчатки, так и от ботанического состава растений, фазы скашивания трав, технологии приготовления кор- ма. В различных видах сена содержится в 1 кг 5,5-8,0 МДж ОЭ
и 30-80 г переваримого протеина, в сенаже, соответственно, 3,5-5,0
и 45-105 г; в соломе – 3,7-6,9 и 5-35 г; в травяной муке – 7,3-8,6
и 80-150 г.
Грубые корма – хорошие источники углеводов, протеина, ви- таминов и минеральных веществ. Для жвачных животных эти корма служат наполнителем рациона, создают определенный объ- ем и структуру кормовой смеси, оказывают положительное влия- ние на пищеварение.
Сочные корма. К ним относятся силос, корнеплоды, клубне- плоды, сочные плоды бахчевых и листовых культур, овощи. Отли- чаются высоким содержанием воды (до 90%), являются хорошими источниками легкоусвояемых углеводов (кроме силоса), обладают молокогонными свойствами, оказывают положительное влияние на процессы пищеварения, повышают эффективность использова- ния питательных веществ рациона.
Энергетическая питательность этих кормов в связи с высоким содержанием влаги невысокая – 1,2-3,5 МДж ОЭ. Мало в них так- же протеина и клетчатки. Однако как диетические и молокогонные корма они незаменимы в рационах молодняка и лактирующих ко- ров (особенно корнеплоды).
Зерно, семена и продукты их переработки являются, главным образом, источниками энергии и протеина. В 1 кг этих кормов со- держится 7,8-13,0 МДж ОЭ и от 80 до 400 г переваримого протеи- на. По содержанию основных питательных веществ зерновые
корма делят на богатые углеводами (зерна и семена злаковых), бо- гатые протеином (зерна и семена бобовых) и богатые жиром (се- мена масличных растений). К этой группе кормов относятся про- дукты переработки зерна и семян, мукомольные отходы, зерновые отходы, дерть, зародыши.
Зерна злаковых культур являются основным компонентом для приготовления кормовых концентратных смесей. В среднем в них содержится около 120 г сырого протеина, в том числе около 75% переваримого.
Протеин зерна злаковых имеет низкую биологическую цен- ность. Во всех кормах этого вида сырья лимитирующей аминокис- лотой является лизин. Поэтому, заменяя один вид зерна другим, невозможно существенно повысить качество протеина кормовой смеси или комбикорма.
Зерно злаковых культур содержит от 2 до 5% сырого жира, отличается низким содержанием кальция (0,12-0,01%) и относи- тельно высоким фосфора (0,24-0,47%). Около двух третей массы зерна приходится на крахмал, который переваривается на 95%. Высокая концентрация легкопереваримых углеводов обеспечивает высокую питательность зерна злаковых.
В среднем в зерне злаковых содержится около 6% сырой клетчатки, но в отдельных его видах этот показатель сильно варь- ирует (от 2,2% в кукурузе и до 10% в овсе). Различия в содержа- нии клетчатки существенно влияют на количество усвояемой энергии и, следовательно, на кормовую ценность зерна. Общая тенденция заключается в том, что количество клетчатки и усвояе- мой энергии в зерне коррелируют отрицательно.
Основными углеводистыми зернофуражными культурами яв- ляются: ячмень, кукуруза, овес, пшеница, рожь, просо, сорго.
Ячмень содержит в среднем в 1 кг: 10,5-11,0 МДж ОЭ, 80-85 г переваримого протеина, 22 г жира, 49 г клетчатки, 4,1 г лизина, 3,6 г метионина+цистина. Он отличный диетический корм для всех видов и групп животных и важнейший зерновой компонент комбикормов.
Кукуруза является наиболее высокоэнергетическим кормом из всех зерновых злаков. В 1 кг ее зерна содержится 12,2 МДж ОЭ, 70-75 г переваримого протеина, 40-45 г жира, 38-45 г клетчатки, 2,1-2,8 г лизина и 1,8-2,0 г метионина+цистина. Особенно ценно как источник энергии зерно кукурузы в рационах птицы.
Овес – ценный диетический корм для всех видов и групп жи- вотных. В 1 кг овса – 9,5-10,5 МДж ОЭ, 75-80 г переваримого про- теина, 40 г жира, 95-100 г клетчатки, 3,6 лизина, 3,2 г метиони- на+цистина.
Пшеница. Как правило, на кормовые цели используют зерно с пониженными хлебопекарными свойствами, засоренное другими видами зерна и щуплое. В 1 кг пшеницы в среднем содержится 10,7-10,8 МДж ОЭ, 13,5% сырого протеина, 0,37% сырой клетчат- ки, около 2% жира, 0,06% кальция и 0,4% фосфора. Зерно пшени- цы в комбикормах используют в дробленом виде или в виде муки грубого помола. Пшеница тонкого помола во рту у животных пре- вращается в клейкую массу, которая, попадая в желудок, может приводить к нарушению пищеварения. Причем, свежеубранная пшеница более опасна в этом отношении, чем хранившаяся в тече- ние определенного времени. В составе комбикормов пшеницу це- лесообразно использовать в смеси с другими видами зерна.
Рожь. По химическому составу ее зерно сходно с зерном пшеницы, но имеет более низкие вкусовые качества. Рожь, даже слегка пораженная спорыньей, опасна для животных. Этот гриб содержит смесь алкалоидов, которые могут вызывать у беремен- ных животных аборты и нарушение пищеварения у растущих жи- вотных. Поэтому такое зерно нельзя вводить в комбикорма для свиноматок, хряков-производителей, поросят-сосунов и отъемы- шей. В комбикормах для откармливаемых свиней его должно быть не более 10% по массе.
Просо. По питательной ценности зерно этой культуры при- ближается к питательности овса. В нем содержится около 9.0 МДж ОЭ, 11 % сырого протеина, около 4% жира и до 9% сырой клет- чатки.
Сорго имеет более высокую питательную ценность. В его зерне несколько меньше протеина и больше жира, чем в ячмене. По энергетической питательности эти виды зерна практически не отличаются. Зерно сорго мелкое и очень твердое. Это следует учи- тывать при его измельчении, поскольку в условиях дробления, одинаковых для других видов зерна, значительная часть сорго мо- жет остаться не размолотой и практически не будет использована животными.
Зерно бобовых – горох, соя, вика, чечевица, люпин – по хими- ческому составу существенно отличается от зерна злаковых.
Кормовая ценность зерна бобовых определяется высоким содер- жанием в нем биологически полноценного протеина. По сравне- нию со злаковыми, в зерне бобовых в 2-3 раза больше сырого про- теина и в 3-5 раз лизина – основной лимитирующей аминокислоты при кормлении свиней и птицы.
Горох – отличный компонент комбикормов для свиней и пти- цы. В 1 кг его содержится около 220 г сырого протеина и около 15 г лизина. По биологической ценности протеин гороха прибли- жается к протеину соевого шрота или мясной муки, по энергетиче- ской ценности он немного уступает зерну злаковых. В 1 кг гороха содержится более 11,0 МДж ОЭ. Углеводы в горохе представлены в основном крахмалом, клетчатки в нем около 5%.
Использование гороха в комбикормах и кормовых смесях для маток, растущих откармливаемых свиней и в качестве единствен- ного белкового компонента (15-25% по весу) позволяет получать среднесуточные приросты 580-630 г. В комбикорма для крупного рогатого скота вводят до 10% гороха.
Соя – самая ценная кормовая бобовая культура. Бобы сои – наиболее полноценные из всех растительных кормов. Они содер- жат 33% сырого протеина. В 1 кг зерна сои содержится 31,9 г ли- зина. Белок сои по этому показателю близок к животным белкам, вследствие чего соя – превосходный компонент комбикормов для свиней и птицы. Однако в сырых бобах сои находятся антипита- тельные вещества (ингибитор трипсина, гемагглютинин, липокси- даза и др.), ухудшающие использование протеина и оказывающие неблагоприятное влияние на организм моногастричных животных и птицы. Поэтому использовать зерно сои для этих животных сле- дует только после его тепловой обработки, прожаривания, авто- клавирования, экструзии и др. Содержащиеся в сое антипитатель- ные вещества термолабильны и при тепловой обработке разруша- ются. При использовании сои в кормлении жвачных необходимо иметь в виду, что ее нельзя вводить в комбикорма, предназначен- ные для скармливания в составе рационов с добавками карбамида, например, при скармливании силоса, обогащенного мочевиной, поскольку в зерне сои содержится фермент уреаза, способствую- щий ускоренному расщеплению мочевины с образованием аммиа- ка.
Зерна сои содержат до 17% жира, поэтому энергетическая ценность их высокая – 14-15 МДж в 1 кг.
Побочные продукты промышленности (пищевой, бродильной, сахарной, крахмальной, маслоэкстракционной, спиртовой, лесной, бумажной). В эту группу включены кормовые средства, получае- мые как побочные продукты от переработки сырья промышленно- стью. Питательная ценность 1 кг этих кормов колеблется в значи- тельных пределах – от 1,13 (пищевые отходы, свежий жом, мезга) до 12,9 МДж (жмыхи, шроты, меласса) и от 8-10 г (жом, мезга и др.) до 350-400 г (жмыхи, шроты) переваримого протеина.
Наибольший удельный вес в кормовом балансе занимают отходы свеклосахарного производства (жом, меласса), спиртового (барда) и маслоэкстракционного (жмыхи, шроты).
Жом широко используют при откорме крупного рогатого ско- та как в свежем, так и в силосованном виде. В 1 кг свежего жома содержится 1,13 МДж ОЭ, 6 г переваримого протеина, 2,5 г сахара, 3 г жира, 33 г клетчатки.
Меласса – источник легкоусвояемых углеводов (сахара).
В 1 кг ее содержится 9,4 МДж ОЭ, 500-550 г сахара.
Барда зерновая – корм, получаемый как продукт переработки зерна при производстве спирта. В 1 кг барды содержится
0,9-1,2 МДж ОЭ, 20-30 г (200-300 г в 1 кг сухого вещества) пере- варимого протеина, 5-9 г сырого жира, 7-11 г клетчатки. Барда – ценный корм для откорма крупного рогатого скота.
Отруби (пшеничные, ржаные) являются побочным продуктом переработки зерна. Состав их зависит от состава исходного про- дукта помола. Они богаты пленками зерна с приставшими к ним частицами эндосперма. В них 8-10% сырой клетчатки, вследствие чего их энергетическая ценность по сравнению с зерном значи- тельно ниже (около 9,0 МДж ОЭ в 1 кг), 15% – сырого протеина и 3,5-4% жира. В 1 кг содержится 5,5-7,8 г лизина. Отруби – богатый источник фосфора, хотя значительная часть его находится в труд- но усвояемой форме в составе фитина, оказывающего послабляю- щее действие на желудочно-кишечный тракт животных.
Корма животного и микробного происхождения. Для этой группы кормов характерно высокое содержание полноценного протеина (в 1 кг сухого вещества от 280 до 800 г переваримого протеина).
Наибольшее значение в кормлении животных имеют молоко и молочные продукты, отходы от переработки животных и рыбы (мясная, мясокостная и рыбная мука).
Молоко и отходы от его переработки – незаменимые про- дукты для питания молодняка. Обрат, пахту, сыворотку использу- ют как в натуральном виде, так и в составе жидких и сухих ЗЦМ.
Отходы мясной промышленности (мясная, мясокостная и кровяная мука) содержат от 30 до 80% протеина, отличающегося высокой биологической ценностью. В 1 кг протеина мясной и мя- сокостной муки до 40-60 г лизина и 20-25 г метионина+цистина.
Рыбная мука обладает высокой биологической ценностью протеина, определяемой его аминокислотным составом. В 1 кг рыбной муки содержится 9,9-14,5 МДж ОЭ, до 650 г переваримого протеина, 45-55 г лизина, 25-30 г метионина+цистина. Она пред- ставляет исключительную ценность для балансирования рационов свиней и птицы по критическим аминокислотам.
Из кормов микробного синтеза наиболее ценны дрожжи и бактериальные продукты, выращиваемые на отходах нефти (БВК), спиртах (эприн) и др. Эти корма занимают промежуточное поло- жение между кормами животного и растительного происхождения.
Комбикорма, БВД, ЗЦМ представляют собой смеси заводско- го изготовления, состоящие из многих компонентов, специально подобранных с целью сбалансирования кормового рациона по недостающим элементам питания и энергии, а также для частич- ной или полной замены цельного молока при выращивании мо- лодняка. Рецепты комбикормов и БВД составляют с учетом зо- нальных особенностей кормовой базы, структуры рационов и типа кормления животных. Небелковые азотистые соединения (карба- мид, аммонийные соли, синтетические аминокислоты), минераль- ные и витаминные препараты (микроэлементы, макроэлементы, витамины, премиксы) используют в качестве добавок к рационам для балансирования их по недостающим элементам питания или частичной замены кормового протеина.
7.2. Зоотехнические требования к кормам и к обработке кормов
К кормам предъявляются повышенные требования по соот- ношению и концентрации, прежде всего основных питательных веществ (протеин, углеводы, жир). Независимо от вида кормов и их назначения все они должны отвечать следующим основным требованиям:
- содержать максимальное количество легкоусвояемых, уни- кальных для данного корма и ценных для животных питательных веществ;
- содержать минимальное количество вредных и ядовитых веществ, оказывающих пагубное воздействие на состояние здоро- вья животных, усвоение питательных веществ и качество продук- ции;
- иметь привлекательный внешний вид, соответствовать цвету и запаху, характерным для данного корма, без признаков порчи;
- отличаться хорошей поедаемостью;
- обладать способностью длительного хранения в консервиро- ванном или натуральном виде.
Зоотехнические требования сводятся к тому, чтобы обеспе- чить животное в течение суток необходимым количеством кормов, которые полностью удовлетворяли бы его потребность в пита- тельных веществах. При несоблюдении норм кормления рацион может быть перенасыщен одним типом корма и иметь нехватку других. Учеными доказано, что необходима комплектность усвоя- емых веществ по всем элементам при одновременном и равномер- ном поступлении их в кровь. Неравномерное и несвоевременное усвоение основных элементов питания ведет к снижению их ис- пользования.
Подготовка отдельных кормов и смесей должна удовлетво- рять следующим требованиям:
Грубые корма – солому и другие грубостебельчатые корма –
измельчают на резку 10-50 мм с расщеплением волокон.
Корнеклубнеплоды очищают от загрязнений, измельчают и смешивают с другими кормами. Остаточная загрязненность не должна превышать 3%. Размеры частиц измельченных корне- клубнеплодов не должны превышать 3-15 мм.
Силос и сенаж в составе кормосмесей должны иметь длину частиц не более 30 мм. Измельчают силос, как в кормоцехе, так и при заборе погрузчиком измельчителем из хранилища.
Концентрированные корма должны поступать в кормоцех в готовом виде (в виде комбикормов или обогащенных смесей кон- центрированных кормов) с комбикормовых заводов или комби- кормовых цехов хозяйства и вводиться в кормосмесь в натураль- ном или увлажненном виде.
Травяную муку вводят в кормосмесь вместе с концентратами. Оборудование для хранения и дозирования травяной муки в смесь должно быть унифицировано с оборудованием для комбикормов.
Питательные растворы – мелассовый и другие – приготавли- вают в кормоцехе в соответствии с зоотехническими требования- ми на растворы и питательные добавки, сдабривающие корма и балансирующие питательные кормосмеси. Все компоненты необ- ходимо дозировано подавать на непрерывное смешивание в пото- ке. Погрешность в дозировании грубых кормов, силоса, корне- клубнеплодов в готовой кормосмеси допускается не более ±15%, а концентрированных кормов ±5% от заданного рациона. Однород- ность кормосмеси, скармливаемой животным, должна быть не ме- нее 80 %, а при вводе в кормосмесь карбамида не менее 90 %.
Влажность кормосмеси должна составлять не более 15 %.
7.3. Способы и схемы подготовки кормов к скармливанию
Различают следующие способы приготовления кормов: меха- нические, химические, тепловые, биологические.
К механическим способам относятся измельчение, плющение, дозирование, смешивание, уплотнение и т.д. Некоторые механиче- ские способы, кроме всего прочего, обеспечивают лучшие условия и для других операций приготовления и раздачи кормов. Напри- мер, измельчение компонентов создает условия для их хорошего смешивания, а уплотнение позволяет облегчить их транспортиров- ку, хранение и раздачу.
Химические способы заключаются в воздействии на некото- рые виды кормов химическими веществами (соляной кислотой, известковым молоком, щелочью, аммиаком и т.д.). Чаще всего этим способом обрабатывают солому с целью расщепления клет- чатки и увеличения ее переваримости.
Тепловые способы сводятся к воздействию на корм тепла (за-
паривание, поджаривание, сушка, заваривание (горячей водой). При этом убивается плесень, если она есть на корме.
Биологические способы основаны на воздействии на корм различных микроорганизмов (дрожжевание, осолаживание и т.д.).
Технологические процессы приготовления кормов отличают- ся большим разнообразием, что обусловливается природно- климатическими зонами содержания животных, особенностями
местности, наличием вблизи ферм предприятий по переработке сельскохозяйственной продукции, структурой посевных площа- дей, технологией содержания животных и другими факторами.
Различают следующие типы рационов кормления крупного рогатого скота: сенной, силосный, концентратный, силосно- сенной, силосно-корнеплодный, силосно-жомовый, силосно- сенажный, силосно-сенажно-концентратный с долей концентриро- ванных кормов до 30-35% питательности рациона.
Для свиней применяют следующие типы кормления: концен- тратно-корнеплодный и концентратно-картофельный с содержани- ем концентрированных кормов в рационах до 60-75% питательно- сти, концентратный.
Для овец применяют сено-силосно-концентратный тип корм- ления с содержанием концентратов до 25-35% по питательности. Для этих животных сено-концентратную часть весьма желательно скармливать в виде гранул.
Главным критерием экономической эффективности рационов являются наименьшая трудоемкость и себестоимость производства кормов, наибольший выход с 1 га кормовых угодий питательных веществ, полноценность кормов.
В связи с большим разнообразием рационов каждый из видов кормов обрабатывают по многим схемам.
Грубые корма (солому и грубостебельное сено) готовят по следующим схемам:
1) измельчение – дозирование – смешивание с другими ком- понентами;
2) измельчение – дозирование – запаривание – смешивание;
3) измельчение – дозирование – биологическая или химиче- ская обработка – смешивание.
Корнеклубнеплоды готовят по схемам:
1) мойка – измельчение – дозирование – смешивание;
2) мойка – запаривание – разминание – дозирование – смеши- вание;
3) мойка – измельчение – дозирование – дрожжевание – сме- шивание;
Первую схему применяют на фермах крупного рогатого скота, вторую – на свинофермах, третью на фермах всех видов.
Зерновые корма готовят, используя следующие схемы:
1) очистка – измельчение – дозирование – смешивание;
2) очистка – измельчение – осолаживание (дрожжевание) –
дозирование – смешивание;
3) очистка – измельчение –дозирование – смешивание – прес- сование;
4) очистка – проращивание;
5) очистка – измельчение – смешивание с мочевиной – экс- трузия;
6) очистка – микронизация.
Эти схемы служат для выбора технологии и оборудования кормоцехов.
7.4. Машины и оборудование для подготовки кормов к скармливанию
7.4.1. Машины и оборудование для измельчения грубых кормов
Для измельчения скирдованную солому загружают фуражи- ром (ФН-1,2/5,1; ФН-1,4) в транспортные средства техническая характеристика приведена в таблице 5.
Фуражир навесной ФН-1,4А (рис. 25) предназначен для из- мельчения и погрузки соломы и сена из скирд в прицеп с сетчатой крышей. Представляет собой навешиваемую на трактор машину, состоящую из пневмопривода с измельчающим аппаратом, венти- лятора с редуктором и выбросной трубы. Фуражир работает
в 2-х режимах:
- низкие обороты барабана, уменьшенное количество штиф- тов, высокая производительность;
- высокие обороты барабана, увеличенное количество штиф- тов, высокая степень измельчения.
Рис. 25. Фуражир навесной ФН-1,4А
Таблица 5
Техническая характеристика фуражиров
Показатели | ФН-1,2/5,1 Ф | Н-1,4А |
Агрегатируется с трактором | МТЗ-80/82 | |
Производительность, т/ч | 3,0 | 3,0-7,0 |
Количество обслуживающего персонала, чел. | 1 | 1 |
Высота подъема измельчающего аппарата, м | 5 5 | 5 1 |
Масса, кг | 2200 | 1350 |
Рабочий процесс фуражира протекает в такой после- довательности. Трактор с навешенной машиной и поднятым аппа- ратом подъезжает к торцу скирды или хранилища. После включе- ния вала отбора мощности (ВОМ) измельчающий аппарат с пнев- мопроводом опускается, постепенно отрезая погружаемый корм.
Нужно следить за тем, чтобы барабан забирал корм на рассто- янии не более ширины обоих барабанов. Отделенный корм всасы- вается воздушным потоком и подается через дефлектор в транс- портное средство.
Режим работы устанавливается регулятором гидросистемы. Перед началом работы измельчающий аппарат принудительно поднимается в исходное (верхнее) положение, при заборе массы он опускается под действием собственного веса. Скорость опуска- ния устанавливается положением шпинделя регулятора гидроси- стемы. При его вкручивании (по часовой стрелке) она увеличива- ется.
Для измельчения грубых кормов (рулонов или тюков соломы и сена), а также сырого и уплотненного материала в рулонах и блоках применяют большую группу машин с молотковыми и штифтовыми рабочими органами: ИГК-30Б, ИРТ-80, ИРТ-165, ИРМА-15 и ИГК-Ф-4, ИРК-145, ИРК-180, ИСС-180; ИР-1,8, ИР-8, ИР-88, ИГК-5М, РИК-88, ИРР-1М, ИСН-1,8.
Измельчители ИГК-30Б, ИГК-Ф-4 и ИУ-Ф-10 относятся к ос- новной группе машин для измельчения грубых кормов. Измельча- ющие аппараты ИГК-30Б и ИГК-Ф-4 штифтового типа полностью унифицированы и обеспечивают высокое качество измельчения. Рабочий орган аппарата выполнен в виде ротора-диска с закреп- ленными на нем клиновидными штифтами в три ряда, противоре- жущая часть (неподвижный диск) несет на себе два ряда штифтов, расположенных концентрично и входящих в промежутки
между штифтами ротора. При работе солома, проходя между
неподвижными и подвижными штифтами измельчающего устрой- ства, разрывается и расщепляется вдоль и поперек волокон.
Техническая характеристика измельчителей представлена в таблице 6.
Таблица 6
Техническая характеристика измельчителей
Показатели ИГК-30Б | ИГК-Ф-4 ИУ-Ф | -10 | ||
1 | 2 | 3 | 4 | |
Производитель- ность при измель- чении, т/ч | соломы | 0 8 | 2 5 | 4 0 |
зеленой массы | 3 0 | - | 5 0- 10 0 | |
зерна | - | - | 5 0 | |
Мощность привода, кВт | 30,0 | 46,1 | 37,0 | |
Измельчающий аппарат ш | тифтовый | штифтовый к | омбини рованный | |
Диаметр ротора, мм | 1000 | 1000 | 1000 | |
Длина ротора, мм | 82 | 82 | 82 | |
Количество штифтов, шт.: на неподвижном диске на роторе (подвижном диске) | 66 100 | 66 100 | 4 ножа 24 молотка | |
Частота вращения, мин-1 | 1124 | 1300 | 1300 | |
Габариты, мм | длина | 3325 | 3000 | 3500 |
ширина | 1350 | 2500 | 1500 | |
высота | 3500 | 3400 | 3500 | |
Масса кг | 1320 | 1223 | 1200 |
Измельчитель грубых кормов ИГК-30Б предназначен для из- мельчения соломы, сена, сухих кукурузных стеблей и других гру- бых кормов с расщеплением их вдоль волокон; применяется на фермах КРС.
ИГК-30Б имеет большую производительность, измельчает со- лому повышенной влажности (до 30%) и обеспечивает высокое качество измельчения. Измельчитель выпускается в двух исполне- ниях: навесной на трактор BELARUS-80.1 – ИГК-30Б-1 и стацио- нарный с приводом от электродвигателя – ИГК-30Б-2 – в кормоце- хах и на кормоприготовительных площадках.
ИГК-30Б-2 (рис. 26) состоит из рамы 15, питателя, приемной камеры 6, измельчающего аппарата, дефлектора 8 с механизмом поворота и направляющим козырьком 9, электродвигателя 14, со- единительной муфты 13, привода и шкафа управления.
Рис. 26. Технологическая схема измельчителя ИГК-30Б-2:
1 – диск неподвижный; 2 – окно; 3, 4 – транспортеры; 5 – лопасть ротора;
6 – приемная камера; 7 – лопасть; 8 – дефлектор; 9 – козырек; 10 – штифты;
11 – диск неподвижный; 12 – ротор; 13 – муфта; 14 – электродвигатель; 15 – рама
Питатель состоит из нижнего горизонтального 3 и верхнего уплотняющего 4 транспортеров, загружающих корм в машину. Верхний транспортер может качаться относительно оси ведущего вала. Привод питателя – от вала ротора через клиноременную пе- редачу, червячный редуктор, цепные передачи и ведущий вал транспортера. Отключает питатель кулачковая муфта на промежу- точном валу. В приемную камеру 6 корм подается питателем. На корпусе приемной камеры находится отсекатель, препятствующий накоплению в ней влажной соломы. В цилиндрической части ка- меры есть люк для осмотра и очистки приемной камеры, в нижней части – отражатель и окно 2 для удаления тяжелых посторонних включений.
Измельчающий аппарат состоит из ротора 12, подвижного 11 и неподвижного 1 дисков, лопастей 7, отсекателя и привода. В со- став измельчающего аппарата входит измельчающая камера, со- стоящая из стенок и обечайки. На обечайке имеются четыре люка.
К передней стенке приварен фланец, к которому крепится привод. К задней стенке с помощью прижимов крепится непо- движный диск 1. Штифты 10 в поперечном сечении имеют клино- видную форму и установлены заостренной гранью вперед по ходу движения, что обеспечивает интенсивное рубящее действие.
Принцип измельчения соломы штифтами в дисковом измель- чителе ИГК-30Б (излом, разрыв, перетирание при окружающей скорости штифтов 42-48 м/с) основан на использовании свойств ломкости и хрупкости сухих стеблей. Посторонние примеси из соломы удаляются в промежутках шириной 200-300 мм между транспортером 3 и камерой измельчения. Поступающая солома втягивается в камеру измельчения воздушным потоком, создавае- мым штифтовым диском, а более тяжелые включения попадают в указанный промежуток.
Солома при повышенной влажности теряет свойство хрупко- сти, стебли ее не ломаются, трудно поддаются разрыву и перети- ранию, поэтому работа штифтового измельчителя ИГК-30Б за- труднена: стебли зависают на штифтах и тормозят диск, падает производительность с 3 до 0,8 т/ч, а энергоемкость процесса воз- растает с 7,2 до 16 кВт∙ч/т. Недостатками машины являются руч- ная загрузка (необходимо 3-5 чел.) и ограниченность расстояния пневмоподачи готового корма (3,5 м), что недостаточно для транс- портировки к местам переработки в кормоцехе.
Технологический процесс. При работе измельчителя корм за- гружается на питатель вручную, а при использовании его в линии кормоцехов для приготовления грубых кормов загрузка обеспечи- вается кормораздатчиком КТУ-10А с электроприводом или други- ми бункерами-дозаторами. Величина подачи корма контролирует- ся по загрузке электродвигателя. Максимальное отклонение стрел- ки амперметра не должно превышать 35 А (на шкале отмечено красной чертой).
Корм подается питателем в приемную камеру, где происходит частичное отделение тяжелых примесей, которые выпадают из этой камеры в пространство между питателем и измельчающей камерой. Далее примеси выносятся поперечным конвейером. В измельчающей камере корм, попадая между неподвижными штиф- тами дискового ротора, измельчается и подается воздушным пото- ком в транспортное средство или на площадку. Благодаря регулируемому козырьку и механизму поворота дефлектора,
измельченный корм равномерно распределяется в кузове транс- портного средства.
Включается и выключается измельчитель с помощью кнопоч- ной станции, контроль осуществляется специальными лампочка- ми.
Регулировки:
1. Изменением длины тяги регулируют подачу рычага вклю- чения питателя так, чтобы при его вертикальном положении по- движная кулачковая полумуфта привода включалась в торцевую шайбу промежуточного вала.
2. Необходимо отрегулировать натяжение: подающих транс- портеров регулировочными болтами, при этом стрела провисания нижнего транспортера – 1-20 мм, верхнего – 5-10 мм (неравномер- ное натяжение правой и левой сторон транспортера не допускает- ся); приводных цепей – звездочками, в итоге стрела провисания длинной цепи составляет 10-15 мм, короткой цепи – 8-10 мм; кли- ноременной передачи – натяжным шкивом; натяжение троса регу- лируется так, чтобы при верхнем положении козырька трос не провисал и не имел изгибов.
3. Настройка измельчителя на работу зависит от влажности грубых кормов. При измельчении кормов влажностью более 18% уменьшают подачу их на загрузчик-питатель. Если влажность бо- лее 20%, снижают скорость питателя путем перестановки звездо- чек: на первичный вал редуктора устанавливают звездочку z=15 зубьев, на промежуточный – z=20.
В комплект измельчителя ИГК-30Б входит 25 лопастей, кото- рые устанавливают при измельчении влажной соломы и снимают при обработке сухой. На роторе лопасти размещают так, чтобы число штифтов между соседними лопастями было одинаковым с обеих сторон: по внешнему ряду – 19, внутреннему – 9. Стержни штифтов, к которым крепятся лопасти, должны выступать за гра- ницы гаек (с пружинными шайбами) не менее чем на одну нитку резьбы.
Измельчитель ИГК-Ф-4 (рис. 27) применяется для измельче- ния грубых кормов и зерна кукурузы в технологических линиях кормоцехов, а также на малых, семейных фермах и в зонах отгон- ного животноводства.
Рис. 27. Измельчитель грубых кормов ИГК-Ф-4-1:
1 – питатель; 2 – приемная камера; 3 – переходник; 4 – рама; 5 – двигатель;
6 – измельчающая камера; 7 – дефлектор; 8 – козырек; 9 – рычаг включения
Выпускается в трех исполнениях: ИГК-Ф-4 с приводом от электродвигателя и механизированной загрузкой питателями- дозаторами ПЗМ-1,5М или БДК-Ф-70 и др.; ИГК-Ф-4-1 – с ручной загрузкой и приводом от электродвигателя для малых ферм; ИГК- Ф-4-2 – с ручной загрузкой и приводом от ВОМ трактора для ма- лых ферм. ИГК-Ф-4-1 любого исполнения состоит из питателя 1, приемной камеры 2 и переходника 3, измельчающей камеры 6, по- перечного конвейера для удаления тяжелых включений соломы, выгрузного поворотного дефлектора 7, рамы 4, электродвигателя 5, шкафа управления и карданной передачи (для привода от ВОМ трактора). При использовании измельчителя без питателя последний можно заменить бункером-дозатором или
питателем-дозатором стебельчатых кормов, трубопроводом, цик- лоном и цепной передачей.
Измельчитель кормов ИУ-Ф-10 предназначен для измельче- ния соломы, сена, початков кукурузы, зерна и других кормов и погрузки корма в транспортное средство или в емкость для накоп- ления. Может использоваться как отдельно, так и в составе техно- логических линий кормоцехов. Состоит из питателя, измельчаю- щей камеры, дефлектора и шкафа управления.
Питатель цепочно-планчатый состоит из рамы, ведущего и натяжного валов, натяжных болтов, полотна транспортера, натяж- ной звездочки. Звездочка свободно подвешена на оси заслонки.
Вращение вала питателя – от вала привода ротора через клиноре- менную передачу, червячный редуктор, промежуточный вал и пе- редачи. Для отключения питателя установлена кулачковая муфта с рычагом.
Промежуточный вал установлен на двух шарикоподшипнико- вых узлах, которые закреплены на раме измельчителя. Каждый из узлов состоит из корпуса, крышки, манжеты, подшипника. На валу установлена звездочка и кулачковая муфта, состоящая из полу- муфты и звездочки-полумуфты.
Измельчающий аппарат состоит из камеры с крышкой, внутри которой установлено решето и дека, а на консольном валу смонти- рован ротор. Измельчитель укомплектован сменными рабочими органами: решетами с отверстиями различного диаметра (для пе- реработки зерна и кукурузы) и декой – для измельчения стебельча- тых кормов. Мелкое измельчение сухих стебельчатых кормов обеспечивается установкой решет. Деку с дефлектором (без цик- лона) монтируют для измельчения крупных кормов, зеленой массы и силоса, одновременного измельчения грубых кормов и корне- клубнеплодов, для получения кормосмесей. Решета 30 и 50 мм (без циклона) используют при измельчении грубых кормов влажно- стью до 15%; 10, 16, 21, 30 и 50 мм (с циклоном) – кукурузы влаж- ностью до 40%; решета 4 и 5 мм с циклоном и бункером для зерна применяют при измельчении зерна влажностью до 15%. Чтобы уменьшить распыление при приготовлении комбикорма, на роторе снимают четыре лопатки. Решето с диагональными отверстиями и циклоном используют при переработке початков кукурузы влаж- ностью до 15%. Решета 16 и 21 мм с циклоном устанавливают при
измельчении грубых сухих кормов (влажностью до 15%) для их мелкого размола.
Ротор состоит из диска, на котором закреплены лопатки, ножи и молотки.
Измельчающая камера состоит из рамы и крышки. Внутри корпуса камеры установлено решето или дека, а на консольном валу смонтирован ротор. Вал ротора клиноременной передачей приводится от вала электродвигателя. На крышке измельчающей камеры закреплены восемь ножей-противорезов. К крышке через переходник присоединен питатель.
Рама питателя состоит из сварного швеллерного основания, корпуса, обечайки, грузовой скобы для погрузочных работ, угол- ков для крепления питателя и рычага переключения. На передней стенке корпуса крепится редуктор, на задней стенке с помощью прижимов закреплены решета (рис. 28) и крышка.
Выгрузное устройство состоит из переходника, шарнира, де- флектора и циклона. Переходник крепится к корпусу рамы из- мельчителя. К фланцу переходника шарнирно осью крепится вто- рой фланец, который вместе с вращающейся на нем обоймой и прижимом составляет механизм поворота. В прижиме установлен регулировочный болт. Поворотом верхней части выгрузного устройства относительно второго фланца дефлектор устанавлива- ют в транспортное положение.
Выгрузной дефлектор состоит из поворотного козырька, кор- пуса, рычага, кольца и троса. Рычаг управления поворотным ко- зырьком включает ручку, рычаг, пружину, кольцо, собачку и стяжки. Угол поворота козырька фиксируется зацеплением собач- ки и сектора. При установке на дефлектор циклона козырьки сни- мают.
Электрооборудование включает электродвигатель, шкаф управления и кабели. На двери шкафа управления установлены: сигнальные лампы, посты управления («Пуск», «Стоп», «Измель- читель», аварийная кнопка «Стоп»), предохранитель для защиты электрических цепей ящика управления от токов короткого замы- кания, индикатор нагрузки для визуального контроля тока нагруз- ки электродвигателя, сирена для предпусковой сигнализации.
Электрооборудование обеспечивает: управление электродвигате- лем (пуск плавный, с переключением обмоток электродвигателя со
«звезды» на «треугольник»); световую сигнализацию наличия
напряжения в шкафу управления; контроль загрузки измельчителя; защиту от перегрузок и коротких замыканий; блокировку электро- двигателя при замене рабочих органов измельчителя.
Технологический процесс. На базе измельчителя ИУ-Ф-10 раз- работаны три основные технологические линии для измельчения грубых кормов с загрузкой вручную или механическим способом (рис. 28, а, б), измельчения зерна, початков кукурузы (рис. 28, в).
а
![]() |
б
в
Рис. 28. Схемы технологических линий с измельчителем ИУ-Ф-10: а, б – измельчители грубых кормов с загрузкой соответственно вручную и грейферным погрузчиком; в – измельчение початков и зерна кукурузы
повышенной влажности; 1 – тележка 2ПТС-4; 2 – измельчитель кормов ИУ-Ф-10; 3 – питатель КТУ-10А с приставкой КТУ-40.000; 4 – помещение-накопитель кормов; 5 – погрузчик типа ПЭ-0,8; 6 – емкость-накопитель корма;
7 – трубопровод с циклоном; 8 – питатель-дозатор
Во всех случаях технологический процесс измельчения оди- наков и протекает следующим образом. Корм равномерным слоем загружается на питатель и подается в измельчающую камеру. Пи- татель включается и выключается рычагом муфты включения. Из- мельченный корм через дефлектор поступает в транспортное сред- ство или емкость для хранения. При переработке фуражного зерна
на дефлектор вместо козырька устанавливают циклон, в котором воздух отделяется от корма. Работой измельчителя управляют при помощи шкафа управления.
Регулировки:
1. Степень измельчения зерна и грубых кормов в муку регу- лируют сменой решет.
2. Подача корма в измельчающий аппарат регулируют изме- нением скорости питателя путем перестановки звездочек на при- воде.
Подготовка к работе. Для начала работы измельчителя
ИУ-Ф-10 включают рубильник, рукоятку выключателя «Сеть» устанавливают в положение «Вкл.», при этом загорается сигналь- ная лампочка. Повернув от себя рычаг, выключают муфту питате- ля и устанавливают дефлектор и его козырек в нужное положение. Затем нажимают «Пуск» на шкафу управления – загорается сиг- нальная сирена, которая через 8 секунд автоматически отключает- ся, после чего сразу включается электродвигатель привода измель- чителя. В течение не более 12 секунд после его разгона происхо- дит переключение пускателей, и электродвигатель начинает рабо- тать в установившемся режиме, его нагрузка контролируется по индикатору. Перемещением рычага на себя включают питатель и загружают равномерным слоем корма, при отклонении стрелки на 70 А питатель выключают и включают снова только тогда, когда стрелка амперметра покажет 65 А. По окончании измельчения корма выключают питатель и лишь после того, как измельчающая камера станет пустой, выключают электродвигатель привода
и очищают от остатков корма все внутренние и наружные поверх- ности машины.
При необходимости срочной остановки измельчителя (появ- ление стуков, вибраций и т.д.) кнопкой «Стоп» отключают элек- тродвигатель и рычагом выключают питатель, устанавливают ру- коятку автоматического выключателя в положение «Выключено». При переезде на небольшие расстояния, а также в местах с низко расположенными электропроводами, дефлектор устанавливают в транспортное положение, соединив его болтом и пружинной шай- бой с питателем.
Измельчитель ИР-8 предназначен для измельчения грубых кормов (рулонов или тюков соломы и сена), а также сырого и уплотнённого материала в рулонах и блоках. Измельчённая масса
может, как раздаваться в кормушки и на кормовой стол, так и ис- пользоваться для приготовления и разбрасывания подстилки для КРС в животноводческих помещениях. Для самозагрузки рулона- ми или тюками используется управляемый гидравликой задний откидной приёмный борт. Машину можно также загружать с по- мощью фронтального погрузчика. Основной рабочий орган – ба- рабан-измельчитель, расположенный в передней части камеры, с помощью установленных на нём ножей (лезвий), обеспечивает из- мельчение материала. Разгрузочное устройство имеет возмож- ность с помощью гидравлики изменять высоту и дальность выбро- са измельчённого материала. Измельчитель агрегатируется с оте- чественными тракторами тягового класса 1,4 или с зарубежными тракторами, имеющими мощность двигателя не менее 55 кВт, не- зависимый ВОМ с 540 об/мин. Обслуживает тракторист.
7.4.2.Машины и оборудование для измельчения зерновых кормов
Из известных способов механического воздействия на зерно с целью его разрушения, таких как удар, сжатие, сдвиг, резание, ис- тирание и т.д., наиболее широкое применение в практике кормо- приготовления нашли удар и сжатие.
Однако в большинстве оборудования этим видам деформации сопутствуют другие. Например, в молотковой дробилке наряду с измельчением ударом присутствует истирание, в вальцовом риф- леном станке к сжатию присоединяется сдвиг и т.д. В одних слу- чаях это явление желательное, в других – нет, поскольку способ- ствует переизмельчению.
Выбор способа измельчения определяется рядом факторов, в числе которых вид корма, физико-механические свойства измель- чаемого зерна, требования технологии подготовки кормов, зоотех- нические требования к корму для различных видов животных.
Свойства измельчаемого материала, определяющие эффек- тивность его измельчения, зависят от температуры и влажности. При сухих методах измельчения влажность оказывает отрицатель- ное влияние, в том числе из-за налипания измельченного продукта на рабочие поверхности.
Дробление свободным ударом используется в молотковых дробилках (рис. 29).
Кроме разрушения от ударов по зерну молотками, продукт дополнительно измельчается при ударах о стенки камеры, которые выполняют рифлеными. Измельченные частицы просеиваются че- рез сменное решето, размер отверстий в котором определяет мо- дуль помола.
Молотковые дробилки позволяют измельчать фуражное зерно влажностью до 18-20%. Однако при использовании их для приго- товления сенной или травяной муки влажность исходной резки не должна превышать 10-12%.
В основе принципа действия ударно-центробежных измельчи- телей лежит разгон зерна под действием центробежных сил с по- следующим ударом о движущуюся или неподвижную преграду.
Указанные измельчители отличает малая энерго- и металлоем- кость. Однако они весьма чувствительны к попаданию в полость измельчителя посторонних предметов, а также к повышению влажности исходного зерна.
Молотковая дробилка
Ударно- центробежный измельчитель
Вальцовый станок
Плющилка Измельчитель
ИЛС-5
Вид воздействия рабочих органов на зерно
Удар
и истирание
Удар Сжатие, сдвиг и срез
Сжатие Резание
Рис. 29. Рабочие органы, применяемые для измельчения зерна
Работа вальцовых станков основана на сжатии, сдвиге и срезе материала. При вращении пары вальцов их рифленые поверхности затягивают материал в рабочий зазор между собой и разрушают его. Вальцы в паре вращаются с различной частотой, что позволяет разрушать материал деформацией сдвига и препятствует залипанию рифлей. Качество измельчения регулируют, изменяя
зазор в вальцовой паре и соотношение окружных скоростей валь- цов.
Вальцовые станки работают при влажности зерна 15-16%.
При более сухом зерне увеличивается выход мучнистой фракции. На более влажном зерне показатели вальцовых станков резко сни- жаются: залипают вальцы, уменьшается производительность, воз- растают энергозатраты.
Плющение зерна проводят на плющилках в рабочем зазоре между двумя гладкими вальцами, вращающимися с одинаковой рабочей скоростью. В некоторых конструкциях плющилок привод от двигателя устроен на один валец, а второй вращается свободно. Регулируют процесс плющения изменением расстояния между вальцами.
Плющению подвергается зерно в фазе восковой спелости или прошедшее влаготепловую обработку, при этом его влажность существенно превышает равновесную. Полученные хлопья или должны быть сразу скормлены, или, в случае хранения, обработа- ны консервантами.
Молотковые дробилки выпускаются различными сериями с производительностью от 0,1 до 5,0 т/ч.
В кормоцехах и кормоприготовительных отделениях ферм целесообразно применять универсальные молотковые дробилки ДКМ-5, КДУ-2А, КДМ-2, ДКУ-1, ДБ-5 и др.
Рассмотрим конструкции наиболее известных и проверенных практикой молотковых дробилок.
Универсальная дробилка кормов КДУ-2А предназначена для измельчения зерна, сочных кормов, минеральных добавок и при- готовления сенной муки. Она может использоваться для приготов- ления смеси из 2-3 компонентов с введением жидких добавок.
Дробилка состоит (рис. 30) из дробильного аппарата 1, венти- лятора 2, загрузочного бункера 3, циклона 6 со шлюзовым затво- ром 5 и двухпатрубковым раструбом 4, нагнетательного 7 и отво- дящего 8 трубопроводов, фильтра 9, режущего аппарата 12, пита- ющего механизм и системы электрооборудования. Все узлы смон- тированы на раме 16.
Дробильный аппарат состоит из чугунного корпуса 4, бокови- ны 3, откидной крышки, двух рифленых дек, сменного решета и дробильного барабана (рис. 31).
Рис. 30. Универсальная дробилка кормов КДУ-2А:
1 – дробильный аппарат; 2 – вентилятор; 3 – загрузочный бункер;
4 – рукав выгрузки; 5 – шлюзовой затвор; 6 – циклон; 7 – кормовой трубопровод;
8 – воздушный трубопровод; 9 – фильтрованный рукав;
10 – амперметр-индикатор; 11 – червячный редуктор; 12 – барабан ножевой;
13 – рычаг включения; 14, 17 – подающий и прессующий транспортеры;
15 – электродвигатель; 16 – рама; 18 – редуктор
Верхнее скошенное окно корпуса сообщает дробильную ка- меру с режущим аппаратом. Откидная крышка крепится к корпусу двумя откидными замками. К нижнему окну крышки замками при- соединен всасывающий патрубок вентилятора. При измельчении сухих кормов в крышке устанавливается решето, при измельчении сочных – выбросная горловина. При этом крышка верхнего окна открывается. Деки крепятся болтами к внутренней поверхности корпуса.
Дробильный барабан состоит из восьми дисков 6 (рис. 31), за- крепленных на валу шпонкой 11. Расстояние между дисками за- фиксировано распорными втулками 10. Через отверстия дисков проходят шесть пальцев9, на которых установлены молотки 7. На каждом пальце – по пятнадцать молотков. Расстояние между мо- лотками отрегулировано распорными втулками 8.
Загрузочный бункер выполнен из листовой стали и имеет в нижней части заслонку, которая регулирует поступление сыпучих кормов в дробильную камеру.
Циклон отделяет муку от воздуха. Он состоит из цилиндриче- ской и корпусной частей. Снизу к нему прикреплен шлюзовой за- твор. Сверху находится цилиндрический патрубок с улиткообраз- ным выбросным кожухом.
Рис. 31. Молотковый барабан КДУ-2А с вентилятором:
1 – шкив; 2 – двухрядный сферический подшипник; 3 – боковина; 4 – корпус;
5 – дека; 6 – диск; 7 – молоток; 8, 10 – распорные втулки; 9 – палец; 11 – шпонка;
12 – кожух вентилятора; 13 – ротор; 14 – всасывающий патрубок
Шлюзовой затвор предназначен для вывода муки из нижней части циклона. Он препятствует выходу воздушного потока из циклона. Шлюзовой затвор состоит из чугунного корпуса, боковин и ротора с прорезиненными лопастями. Привод ротора от главного вала осуществляется клиноременной передачей, червячным редук- тором и гибкой муфтой. Снизу шлюзового затвора закреплен двухпатрубковый раструб с перекидной заслонкой и мешкодержа- телями.
Пневмоприводы 7 и 8 соединяют циклон с вентилятором
и через полотняной фильтр 9 – с подводящим воздушным патруб- ком (рис. 30).
Режущий аппарат измельчает сочные и грубые корма. Состо- ит из ножевого барабана 12, противорежущей пластины и рамы (рис. 30). Режущий барабан имеет три ножа, закрепленных на двух фигурных дисках, и вал. Зазор между ножами и противорежущей
пластиной регулируется перемещением ножей на дисках упорны- ми болтами. На одном конце вала закреплен шкив с фрикционной предохранительной муфтой, на другом – звездочка (Z = 15) для привода редуктора питающего механизма.
Противорежущая пластина крепится на раме винтами. На пла- стине имеется планка для регулирования минимального зазора с транспортерной лентой для предотвращения затягивания корма.
Верхнее окно камеры измельчающего аппарата соединено с загру- зочным бункером 1, нижнее – с подводящим воздушным патруб- ком, имеющим продольную щель для направления воздушного потока в дробильную камеру. Загрузочный бункер шарнирно за- креплен над верхним окном камеры режущего аппарата. На задней стенке верхнего окна закреплен магнитный сепаратор 6. Поступ- ление зерна в дробильную камеру регулируют заслонкой с рычаж- ным механизмом и зажимом.
Питающий механизм (рис. 30) состоит из транспортеров 14 и 17 и редуктора 18. Наклонный прессующий транспортер 17 состо- ит из рамки, цепочно-планчатой ленты, ведомого и ведущего ва- лов. Рамка включает две боковины и коробкообразную лыжу, со- единенные стяжными винтами. Цепочно-планчатая лента – это две втулочно-роликовые цепи с наклепанными на них металлическими планками. На ведомом валу прессующего транспортера закрепле- ны две звездочки и ролик, опоры подшипников закреплены на рамке. На ведущем валу имеется три звездочки: две из них предна- значены для привода ленты, а третья – для привода ведущего вала. Опоры вала шарнирно установлены в обоймах вертикальных сте- нок кожуха. На выступающих концах опор крепятся рычаги, со- единенные пружинами с рамой машины. Этим достигается при- жимание наклонного транспортера вниз. Нижнее положение транспортера ограничивается упорными пластинами на стенках кожуха.
Питающий транспортер состоит из рамы, прорезиненной лен- ты, ведомого и ведущего валов, на которых закреплены ролики.
Ведомый вал может перемещаться в направляющих рамы болтами, чем достигается натяжение или ослабление ленты.
Редуктор обеспечивает включение транспортеров в работу, отключение или обратный ход. Привод редуктора осуществляется цепной передачей от вала режущего барабана.
Для обеспечения легкого запуска дробилка комплектуется ав- томатической пусковой фрикционной муфтой центробежного ти- па, встроенной в шкив электродвигателя.
Технологический процесс, выполняемый дробилкой КДУ-2А, следует рассматривать как трехэтапный: дробление сыпучих зер- новых кормов в муку; измельчение грубых кормов в муку; измель- чение сочных кормов (зеленой травы, силоса, корнеклубнеплодов) в пастообразную массу.
При дроблении сыпучих зерновых кормов (рис. 32) клиновые ремни привода режущего барабана снимают.
![]() |
Рис. 32. Технологическая схема работы дробилки КДУ-2А при измельчении зерна:
1 – приемный бункер; 2 – барабан ножевой; 3 – молоток; 4 – вентилятор;
5 – решето; 6 – магнитный сепаратор; 7 – заслонка; 8 – раструб; 9 – шлюзовой затвор; 10 – циклон; 11 – фильтрующий рукав
В заднюю крышку дробильной камеры устанавливают смен- ное решето 5. Нижнее окно крышки соединяют сменным всасыва- ющим патрубком с вентилятором 4. Включают дробилку в работу и регулируют заслонкой 7 зернового бункера 1 степень загрузки.
Амперметр-индикатор должен показывать 55-60 А. Зерно, проходя по наклонному днищу горловины, очищается магнитным сепара- тором 6 от стальных предметов и попадает в дробильную камеру. Под действием ударов молотков 3 оно частично разрушается. Не- разрушенные частицы отбрасываются на деки и решета, где окон- чательно измельчаются. Частицы, по размеру меньшие или равные отверстию решета, попадают в зарешетную полость крышки дро- бильной камеры, из которой потоком воздуха по всасывающему патрубку, вентилятору 4 и нагнетательному пневмопроводу пере- мещаются в циклон 10. В циклоне происходит отделение муки от воздуха. Мука через шлюзовой затвор 9 и раструб 8 поступает в тару, а воздух уходит через отводящий пневмопровод, фильтр 11 и приемный воздушный патрубок – снова в дробильную камеру.
Часть воздуха через фильтр выходит наружу. Этим создается не- которое разрежение при выходе в дробильную камеру, благодаря чему устраняется распыливание измельченного корма через не- плотности дробильной камеры. Мучная пыль, осевшая в фильтре, по мере накопления снова попадает в дробильную камеру.
При измельчении грубых кормов в работу включается режу- щий аппарат. Горловина приемного бункера перекрывается за- слонкой. На время запуска электродвигателя необходимо отклю- чить питающий механизм, для чего рычаг 13 устанавливают в среднее положение (рис. 30). После запуска электродвигателя включают питающий механизм, для чего рычаг 13 устанавливают в крайнее заднее положение. На питающий транспортер 14 корм загружают равномерным слоем. Прессующий транспортер 17 уплотняет его. Частицы, отрезанные ножами, отбрасываются на скатную доску и поступают в дробильную камеру. Дробится и транспортируется грубый корм как зерно. При измельчении гру- бых кормов в заднюю крышку дробильной камеры устанавливают сменное решето с отверстиями 10 мм.
При измельчении сочных кормов машину переоборудуют для работы по прямоточному циклу: отсоединяют всасывающий па- трубок от крышки дробильной камеры и вентилятора. На входе вентилятора ставят оградительную сетку. Заменяют сменное ре- шето вставной выбросной горловиной и открывают верхнее окно в крышке дробильной камеры. Снаружи под окном устанавливают отражательный козырек-дефлектор. В этом случае дробилка рабо- тает со сквозным проходом кормов от транспортера через ножевой
аппарат, дробильную камеру, вставную выбросную горловину и верхнее окно в крышке дробильной камеры.
Воздушный поток, создаваемый вентилятором, проходя через циклон, отводящий пневмопровод, фильтр, приемный воздушный патрубок, дробильную камеру и выбросную горловину, препят- ствует залипанию корма на стенках последней.
Регулировки:
1. Требуемая степень измельчения продукта обеспечивается с помощью сменных решет с отверстиями 4; 6; 8 и 10 мм.
2. Подачу зерна из приемного бункера в дробильную камеру регулируют открытием и закрытием поворотной заслонки. Сте- пень загрузки дробилки контролируется по показаниям ампермет- ра-индикатора (55-60 А).
3. Зазор между ножами и противорежущей пластиной регули- руется перемещением ножей упорными винтами. Предварительно ослабляются крепежные болты. Зазор должен составлять не более 1 мм.
4. Зазор между планкой противорежущей пластины и лентой горизонтального транспортера устанавливают минимальным за счет перемещения самой пластины.
5. Уплотнение массы прессующим транспортером регулируют натяжением пружины так, чтобы прессующий материал не выдер- гивался при работе.
6. Длину резки изменяют заменой звездочек (Z = 13 и Z = 15)
на валу ножевого барабана.
7. Молотки на новые рабочие грани переставляют при их из- носе более 3 мм.
8. Предельный износ режущей кромки ножей 10-12 мм, про- тиворежущей пластины – до 5 мм.
Дробилка безрешетная ДБ-5-1 (ДБ-5-2) предназначена для из- мельчения фуражного зерна нормальной и повышенной влажно- сти, но не выше 17%. Она укомплектована (рис. 33) дробильным аппаратом 2, загрузочным 1 и выгрузным 4 шнеками и шкафом управления 6.
Дробилка ДБ-5-2 отличается от ДБ-5-1 укороченным загру- зочным шнеком и не комплектуется выгрузным шнеком.
Дробилка ДБ-5 (рис. 34) состоит из ротора 9, корпуса 11, при- емного бункера 8, разделительной камеры 2, рамы 10, фильтра 1, шнека для выгрузки измельченного продукта, электродвигателя
14, магнитных сепараторов 15, механизма управления заслонкой бункера-дозатора 20 и дек 22.
![]() |
Рис. 33. Общий вид комплекта оборудования дробилки безрешетной ДБ-5-1:
1 – шнек загрузочный; 2 – дробилка; 3 – подставка; 4 – шнек выгрузной;
5 – рукав; 6 – шкаф управления
Ротор дробилки (рис. 35) состоит из вала 4 с набором дисков 3 и шарнирно качающихся на осях 2 молотков 1. Между дисками 3 установлены распорные втулки 5. Расстояние между молотками на осях 2 обеспечивается распорными втулками 8 и шплинтами. Мо- лотки на осях собраны пакетами, разница пакетов по массе не должна превышать 10 г.
Вал ротора вращается в сферических двухрядных роликовых подшипниках 6, которые установлены в корпусах 7, прикреплен- ных к раме дробилки.
Ротор дробилки размещается на корпусе 11 (рис. 32), на кото- ром установлены разделительная камера 2 и приемный бункер 8. Корпус вместе с ротором образуют дробильную камеру. Внутрен- няя поверхность корпуса выложена ребристыми деками 22, кото- рые опираются на секторы и прижимаются к ним болтами. Для обслуживания дробильной камеры в корпусе предусмотрена от- кидная крышка 12. Для предотвращения случайного включения дробилки в работу при открытой крышке, на ней установлен ко- нечный включатель. Бункер 8 имеет загрузочное и смотровое окна
18. В нижней части бункера установлены электропривод 19 за- слонки для автоматического регулирования подачи зерна в дро- бильную камеру и рычаг 17 для ручного управления заслонкой.
На наклонной стенке бункера для улавливания металлических предметов закреплена батарея постоянных магнитов 15.
![]() |
Рис. 34. Дробилка ДБ-5:
1 – фильтр; 2 – камера разделительная; 3 – кормопровод; 4 – рычаг управления заслонкой; 5 – клиноременная передача; 6 – скоба; 7 – рамка; 8 – бункер;
9 – ротор; 10 – рама; 11 – корпус; 12 – крыша откидная; 13 – втулочно-пальцевая муфта со шкивом; 14 – электродвигатель; 15 – магнитный сепаратор; 16 – зажим; 17 – рычаг; 18 – загрузочное и смотровое окно; 19 – электропривод заслонки бункера-дозатора; 20 – кожух; 21 – шкив привода шнека для выгрузки измельченного зерна; 22 – дека; 23 – рычаг управления удлиняющим козырьком
Загрузка бункера осуществляется загрузочным шнеком, кото- рый управляется с помощью датчиков нижнего и верхнего уров- ней. Как только нижний датчик освободится от зерна, подается сигнал на включение шнека. Зерно загружается в бункер 8 и при
его наполнении срабатывает датчик верхнего уровня, подающий сигнал на отключение загрузочного шнека.
![]() |
Рис. 35. Ротор:
1 – молоток; 2 – ось; 3 – диск; 4 – вал; 5 – втулка; 6 – двухрядный роликоподшипник; 7 – корпус; 8 – распорная втулка; 9 – муфта
На бункере смонтированы автоматический регулятор подачи зерна в дробильную камеру и привод загрузочной заслонки.
Привод состоит из электродвигателя РД-0,9, зубчатой переда- чи вала, на котором закреплена заслонка. Дополнительно на этом валу установлена электромагнитная муфта, которая при отключе- нии напряжения электрической сети дает возможность загрузоч- ной заслонке мгновенно под действием собственной массы пере- крывать поступление зерна в дробилку. Блок питания электропри- вода заслонки расположен в шкафу управления.
Основными узлами механизма управления загрузочной за- слонкой являются: выпрямительный мост КЦ402В, реле промежу- точное РПУ-0-962, реле времени пневматическое РВП-72-32, блок включателей, взаимодействующих с реле.
Камера разделительная 2 (рис. 34) предназначена для сепари- рования измельченных частиц по размерам и направления на до- измельчение крупной фракции в дробильную камеру. На верхней части разделительной камеры с помощью четырех откидных болтов крепится тканевый фильтр 1 для частичного сброса
циркулирующего в дробилке воздуха. В нижней части камеры 2 установлен шнек для выгрузки готового продукта и подачи его на выгрузной шнек.
В шкафу управления размещена основная и вспомогательная аппаратура управления дробилкой. На передней панели шкафа управления находится амперметр-индикатор, показывающий за- грузку электродвигателя привода дробилки, переключатель режи- мов работы, кнопки включения работы шнеков, тумблер включе- ния аппарата загрузки дробилки.
На правой стенке шкафа управления находится сетевой вы- ключатель, на передней – сирена, сигнализирующая об окончании подачи зерна в дробилку.
Внутри шкафа установлен автоматический регулятор, пред- ставляющий собой электронный блок, который управляет приво- дом заслонки загрузочного бункера. Он автоматически поддержи- вает такое положение заслонки, при котором количество поступа- ющего зерна создает номинальную загрузку электродвигателя дробилки. Система электрооборудования обеспечивает привод дробилки, защиту, управление и автоматический контроль степени загрузки электродвигателя.
Технологический процесс работы. Зерно загрузочным шнеком подается в приемный бункер 2 (рис. 36). Двигаясь по наклонному днищу бункера, зерно очищается от механических примесей маг- нитным сепаратором 18 и после очистки попадает в дробильную камеру 3. После сигнала автоматического регулятора заслонка 19 поднимается или опускается, поддерживая определенную толщину слоя зерна, поступающего в дробильную камеру на измельчение. Измельчение происходит за счет воздействия на зерно вращающе- гося ротора.
При ударном воздействии шарнирно подвешенных молотков и дек зерно измельчается за неполный оборот ротора и выносится за пределы дробильной камеры.
Измельченный материал транспортируется из дробильной ка- меры в кормопровод 4 за счет швыркового эффекта ротора и воз- душного потока, создаваемого им. Воздушный поток усиливается благодаря вихревой камере, установленной в корпусе дробилки.
Смесь измельченного материала и воздуха по кормопроводу по- ступает в разделительную камеру 6.
Рис. 36. Технологическая схема работы дробилки ДБ-5:
1 – шнек загрузочный; 2 – бункер; 3 – камера дробильная; 4 – кормопровод;
5 – воздушная камера; 6 – разделительная камера; 7 – возвратный канал;
8 – заслонка; 9 – сепаратор; 10 – шнек дробилки; 11 – козырек; 12 – воздушный рециркуляционный канал; 13 – фильтр; 14 – выгрузной шнек; 15 – датчики верхнего и нижнего уровней; 16 – питающий шнек; 17 – электродвигатели загрузочного и выгрузного шнеков; 18 – магнитный сепаратор; 19 – заслонка
В разделительной камере измельченные фракции зерна про- ходят через сепаратор 9 на выгрузной шнек 10. Здесь же происхо- дит отделение муки от воздуха. Кроме того, в разделительной ка- мере 6 предусмотрены два регулировочных механизма: заслонка 8 и удлиняющий козырек 11. Положение заслонки 8 устанавливают нижним рычагом 23, с помощью которого регулируют качество измельчения зерна. Козырек 11 используют для регулирования качества измельчения овса и зерна повышенной влажности. Козы- рек рычагом 4 устанавливают на необходимую степень измельче- ния.
Измельченный продукт (мука) шнеком 10 (рис. 36) подается в выгрузной шнек 14, который транспортирует его в склад, мешко- тару или непосредственно в транспортные средства. В дробилке ДБ-5-2 готовый продукт поступает в приемное устройство комби- кормового агрегата.
Недоизмельченная фракция по возвратному каналу 7 попадает в дробильную камеру. В зависимости от положения заслонок 8 и 19 задается масса подаваемой на возврат фракции.
Если заслонки находятся в крайнем правом положении (стрелка указателей заслонок в левом положении), то все фракции по возвратному каналу 7 поступают на доизмельчение (мелкий помол). При среднем положении заслонок только часть материала возвращается на доизмельчение (средний помол), а в крайнем ле- вом положении заслонок все фракции поступают на выгрузку (крупный помол).
Допускается работа дробилки ДБ-5 в ручном режиме. При этом необходимо постоянно следить за показаниями амперметра на шкафу управления (стрелка амперметра должна находиться на отметке 60 А). Заслонка бункера-дозатора поворачивается рыча- гом 17, а стопорится зажимом 16 (рис. 32).
Регулировки:
1. Степень измельчения регулируется положением заслонок 8 и 19 (рис. 36), управляемых рычагами 4 и 23 (рис. 34). Рычаги устанавливают в такой последовательности: отвинчивают махови- чок зажимного устройства, закрепленного на стенке разделитель- ной камеры, переводя каждый рычаг в положение «помол», кон- тролируемое стрелкой, и завинчивают маховичок, фиксируя тре- буемое положение регулировочного устройства.
2. Для обеспечения требуемого качества измельчения необхо- димо отрегулировать зазор между молотками и деками (не более 2,5 мм). Зазор устанавливают следующим образом: ослабляют болты крепления секторов с деками; вращением эксцентриков сек- торы приближают до упора в диски ротора, затем эксцентрики по- ворачивают против часовой стрелки на 15-20 0 и затягивают болты крепления секторов.
3. Подачу зерна в дробильную камеру устанавливают вруч- ную рычагом 17 или автоматически регулятором (рис. 34). Нагруз- ку двигателя в первом случае регулируют по показанию ампер- метра на шкафу управления. Автоматический регулятор выдержи- вает положение заслонки, соответствующее номинальной нагрузке электродвигателя (55-57 А). Если зерно не поступает в дробилку, то конечный выключатель автоматически включает звуковой сиг- нал, установленный на крышке электропривода заслонки.
4. По мере износа рабочих граней молотков их переставляют на новые грани или заменяют. Наработка на одну грань составляет примерно 250 т зерна. При замене износившихся комплектов мо- лотков новыми необходимо проверить, чтобы разность массы мо- лотков, расположенных на осях ротора, не превышала 10 г.
Вальцовые станки предназначены для сухого измельчения зерна и получения круп и муки. Оптимальная влажность исходно- го материала 15-16%. Вальцовые станки могут заменять молотко- вые дробилки, однако часто дают переизмельченный продукт.
Применение вальцовых станков распространено в хозяйствах Юга России (Краснодарский, Ставропольские края и т.д.), но воз- можно использование в других зонах страны.
Рабочие органы вальцового станка представляют два горизон- тально расположенных цилиндрических вальца с рифленой или микрошероховатой поверхностью, вращающихся с разными ско- ростями навстречу друг другу. Продукт при этом затягивается в зазор между вальцами, испытывая сжатие, сдвиг и срез. Это, в ко- нечном счете, и ведет к разрушению.
Величина зазора между вальцами изменяется от 0,03 до 1,5 мм и является регулируемым параметром измельчения. Даже малое его изменение приводит к существенному изменению в процессе измельчения.
При эксплуатации станка зазор приходится регулировать, по- скольку сам валец изнашивается, а физико-механические свойства зерна изменяются от партии к партии.
Окружные скорости вальцов неодинаковы. Быстровращаю- щийся валец обгоняет частицу в зоне измельчения и обрабатывает ее своими рифлями, а частица, обгоняя медленновращающийся валец, измельчается о его рифли.
Установлено, что оптимальной, с точки зрения качества из- мельчения и энергетики процесса, является скорость быстровра- щающегося вальца 5-6 м/с.
Плющилки содержат вальцы одинаковых диаметров, которые вращаются с одинаковой окружной скоростью и подвергают зерно деформации чистого сжатия. Превращение зерна в хлопья увели- чивает его поверхность, что ведет к увеличению усвояемости кор- ма. Однако не только в этом положительные стороны плющения.
По существу следует рассматривать две технологии плюще-
ния.
Первая из них предполагает влаготепловую обработку зерна, приводящую к желатинизации крахмала. При этом предполагается гидротермическая обработка исходного сухого зерна водой или паром, при которой его влажность повышается.
С увеличением влажности зерна до 25-30% усилие на его раз- давление уменьшается в несколько раз. Однако при этом возника- ет нежелательное явление, связанное с прилипанием расплющен- ного зерна к рабочей поверхности валков, которые приходится оснащать чистиками.
При влажности зерна более 24-26% на нем много поверхност- ной влаги, что ведет к уменьшению коэффициентов трения и ухудшению захвата зерна валками.
Влажное зерно после сжатия способно к некоторому восста- новлению толщины (явление обратной ползучести). Хлопья запаренного ячменя, например, увеличивают свою толщину
в 2,0-2,1 раза (по отношению к зазору между вальцами). Толщина хлопьев после охлаждения должна быть в пределах 0,8-1,0 мм.
По различным данным, по сравнению с дроблением на молот- ковых дробилках плющение позволяет уменьшить удельный рас- ход зерна в рационах на 6-12%. Не следует, однако, забывать, что повышение эффективности использования корма достигается в этом случае возрастанием затрат тепловой и механической энер- гии на его переработку.
Вторая технология использования плющения обусловлена за- готовкой консервированного плющенного зерна, убранного в пе- риод молочно-восковой спелости (влажность 30-35%).
Консервирование плющенного зерна имеет следующие досто- инства по сравнению с другими способами заготовки кормов:
- питательная ценность зерновых в период молочно-восковой спелости наивысшая, поэтому с 1 га площади заготавливают на 10% больше питательных веществ;
- урожай собирают на 2-3 недели раньше обычных сроков, что важно для регионов с неустойчивым климатом;
- исключаются сушка зерна и его предварительная очистка.
Плющение зерна может осуществляться как прямо в поле так и возле хранилища или внутри его. Обработка консервантами про- водится прямо в хранилище. Хранят обработанное зерно в герме- тичных траншеях с облицовкой стен и верха полиэтиленовой пленкой.
Полученный таким способом корм готов к употреблению, имеет высокую питательную ценность, хорошо поедается и усваи- вается всеми видами животных, в том числе молодняком. Эффект от его использования примерно такой же, как от пророщенного плющенного зерна.
Указанную технологию активно продвигает в России финская фирма MURSKA. Отечественные разработки оборудования име- ются в опытно-конструкторском бюро СибНИПТИЖ.
В качестве примера рассмотрим устройство агрегата ПЗ-3А для приготовления хлопьев из зерна. Он предназначен для перера- ботки в хлопья различных видов фуражного зерна и зерносмесей путем гидротермической обработки и плющения. Влажность пере- рабатываемого зерна для злаковых до 18%, для кукурузы – до 25%.
Применяется в линиях переработки фуражного зерна кормо- приготовительных цехов, может использоваться как отдельная зерноперерабатывающая машина на откормочных и молочных фермах, имеющих в качестве источников парообразования котлы Д-721 или КВ-300М.
Агрегат для приготовления хлопьев из зерна ПЗ-3А обеспечи- вает его влаготепловую обработку и плющение. Состоит из плю- щилки 4 (рис. 37), пропаривателя 5, загрузочного 1 и выгрузного 8 шнеков, эжектора 3, шкафа управления и системы вентиляции.
Плющилка состоит из рамы, неподвижного и подвижного вальцов, механизмов перемещения и регулировки зазора между ними и ме- ханизма отсчета, показывающего зазор между вальцами. Вальцы приводятся во вращение индивидуальными электродвигателями через клиноременную передачу. Подвижный валец перемещается в рабочее положение поворотом рычага механизма перемещения.
Пропариватель предназначен для влаготепловой обработки зерна и состоит из дозатора, нижнего и верхнего корпусов, пред- ставляющих собой емкость, соединенную болтами, эжектора, сме- сительной камеры и двух паропроводов для подачи зерна в ем- кость пропаривателя и возврата отработанного пара в эжектор.
Технологический процесс протекает следующим образом.
Зерно из завальной ямы шнеками загрузки 1 и 2 подается в эжек- тор 3, где его подхватывает струя пара и перемещает в пропарива- тель 5.
Рис. 37. Схема технологического процесса агрегата ПЗ-3А:
1 – загрузочный шнек; 2 – шнек эжектора; 3 – эжектор; 4 – плющилка;
5 – пропариватель; 6 – дозатор; 7 – шнек плющилки; 8 – шнек выгрузной;
I – зерно; II – хлопья; III – пар
Обработанное зерно дозатором направляется на вальцы плю- щилки 4, а готовые хлопья эвакуируются выгрузными шнеками 7 и 8. Пропариватель работает при температуре пара 90-110 0С и давлении 0,05-0,07 МПа. Расход пара составляет350 кг/ч. Конеч- ный продукт представляет собой хлопья влажностью 14-20% и толщиной 0,77-1,2 мм; время хранения их не более 5-6 ч.
7.4.3.Машины и оборудование для измельчения сочных кормов
Для приготовления сочных кормов используют корнеклуб- немойки, корнерезки, измельчители корнеклубнеплодов и кормо- приготовительные агрегаты.
Камни, частицы грязи от кормовой массы отделяют специаль- ные устройства различного конструктивного исполнения. Наибо- лее эффективно этот процесс протекает в воде, где камни, имею- щие удельную массу значительно большую, чем у корнеклубне- плодов, оседают на дно ванны, а продукт выводится из устройства.
Корнеклубнемойки по конструкции рабочих органов делятся на кулачковые, барабанные, дисковые и шнековые (рис. 38). Раз- личают машины периодического и непрерывного действия, вода в них служит для удаления в осадок отдельных частиц грязи.
![]() |
Рис. 38. Схемы корнеклубнемоек и корнерезок: корнеклубнемойки: а – кулачковая; б – барабанная; в – дисковая; г – шнековая; корнерезки: д – дисковая; е – дисковая с вертикальным валом; ж – барабанная;
з – с неподвижными ножами
Корнерезки и измельчители корнеплодов (рис. 38) по принци- пу действия делятся на машины с режущими (рубящими) рабочи- ми органами, ударного действия (штифтовые или молотковые)
и комбинированные (рубящие и ударные). Ножи при резке корне- клубнеплодов подвержены быстрому износу в результате абразив- ного воздействия земли и песка, находящихся на поверхности из- мельчаемого продукта.
Рабочими органами ударного действия служат жестко или шарнирно закрепленные штифты, молотки или фрезы. Они более стойки к абразивному износу, однако измельчают корнеплоды со значительным выделением сока, что увеличивает потери пита- тельных веществ в процессе приготовления кормов.
При надлежащем конструировании режущие рабочие органы имеют некоторые преимущества по удельным энергозатратам
и получению продукта заданного гранулометрического состава.
В настоящее время для обработки корнеклубнеплодов кроме отдельных используются комбинированные машины и агрегаты, которые выполняют две технологические операции и более, обес- печивая поточность и высокое качества приготовления кормов.
Измельчитель кормов ИКВ-5А «Волгарь-5» (рис. 39) состоит из подающего 8 и уплотняющего 3транспортеров, аппаратов пер- вичного 2 и вторичного 10 резания, натяжного устройства подаю- щего транспортера 9, натяжных звездочек 5, 6, 7 и автомата от-
ключения 11.
Рис. 39. Измельчитель кормов ИКВ-5В «Волгарь-5»:
1 – шнек; 2 – аппарат первичного резания; 3 – уплотняющий транспортер;
4 – скоба управления; 5, 6, 7 – натяжные звездочки; 8 – подающий транспортер; 9 – натяжное устройство подающего транспортера; 10 – аппарат вторичного резания; 11 – автомат отключения
Подаваемый из кормоприемника-питателя корм располагается (или укладывается вручную) ровным слоем на подающем транс- портере 8, уплотняется натяжным транспортером 3, а затем направляется в аппарат первичного резания. Ножевой барабан 2 предварительно измельчает массу до размеров частиц резки
20-80 мм. Спиральные ножи барабана в сечении имеют
Г-образную форму, их лезвия описывают окружность диаметром
450 мм.
На барабане установлено 6 ножей с углом заточки 35 040' и уг- лом подъема винтовой линии 70 0. Угол заточки противорежущей пластины 750. Зазор между лезвием ножей и противорежущей пла- стиной устанавливают в пределах 0,5-1 мм. Измельченный режу- щим барабаном корм падает на шнек 1 и направляется им в аппа- рат вторичного резания, состоящий из девяти подвижных и девяти неподвижных ножей. Этот аппарат измельчает корм до фракции размером 2-10 мм. Готовый корм выбрасывается через нижнее ок- но в корпусе измельчителя на транспортер, расположенный в при- ямке.
Аппарат вторичного резания устроен следующим образом. В желобе по всей ширине корпуса измельчителя расположен шнек диаметром 440 мм, имеющий на концах консольные валы. На кон- сольный вал со шпоночной канавкой со стороны выхода продукта надета втулка с шлицевой наружной поверхностью. На шлицован- ную часть этой втулки надеты чередующиеся подвижные (со шли- цами) и неподвижные (без шлиц) ножи. Последние своими наруж- ными концами закреплены на неподвижных планках на корпусе.
Таким образом, многоножевой дисковый режущий аппарат щелевого типа осуществляет двухопорное резание ножами с
П-образной режущей кромкой и углами заточки, равными 90 0. Этот аппарат более энергоемкий по сравнению с соломосилосо- резкой, но он позволяет получить тонкое измельчение и более рав- номерный гранулометрический состав частиц.
ИКВ-5В «Волгарь-5» может работать по трем технологиче- ским схемам – измельчение корма для крупного рогатого скота, для свиней и для птицы. При измельчении грубых и сочных кор- мов для крупного рогатого скота в работу включают только аппа- рат первичного резания. Необходимую крупность частиц для сви- ней и птицы достигают путем изменения угла установки лезвия первого подвижного ножа аппарата вторичного резания
относительно конца витка шнека. При измельчении корма для птицы этот угол должен быть 9 0 (по направлению вращения но- жей), а для свиней – 54 0 (против направления вращения). Все по- следующие ножи располагают по спирали через 72 0 против направления вращения ножей.
Измельчитель-камнеуловитель-мойка ИКМ-Ф-10 (рис. 40) предназначен для очистки корнеклубнеплодов от камней, их мой- ки и измельчения на частицы размером до 10 мм (для свиней) или ломтики толщиной до 15 мм (для крупного рогатого скота). Из- мельчитель агрегатируется с транспортерами-питателями
![]() |
ТК-5 или ТК-5Б, а также может быть использован как самостоя- тельная машина при установке в утепленных помещениях, обору- дованных водопроводом и простейшей системой канализации.
Рис. 40. Схема измельчителя корнеклубнеплодов ИКМ-Ф-10:
1 – рама; 2 – транспортер; 3, 7, 11 – электродвигатели; 4 – вентиль;
5 – душевое устройство; 6 – кожух; 8 – выбрасыватель; 9 – крышка измельчающего аппарата; 10 – измельчающий аппарат; 12 – шнек мойки; 13 – ванна; 14 – диск-крылач; 15 – люк
Измельчитель ИКМ-Ф-10 имеет три рабочих органа: моечный шнек; измельчающий аппарат дискового типа; транспортер, при- водимый в работу от мотора-редуктора.
Рабочий процесс протекает следующим образом. Ванну за- полняют водой до уровня, который поддерживается сливным па- трубком на кожухе выгрузного транспортера. Корнеклубнеплоды транспортером-питателем подают в моечную ванну, где их отмы- вают вихревыми потоками воды, создаваемыми крылачом, и осво- бождают от камней. Далее корнеклубнеплоды поступают на шнек и вторично отмываются от грязи встречным потоком воды в шне- ке, затем по откидному направляющему кожуху отбрасываются в камеру измельчения. Измельчающий аппарат состоит из литого корпуса и двух дисков. На верхнем диске закреплены два горизон- тальных ножа, а на нижнем –четыре вертикальных. Оба диска установлены на валу электродвигателя. Переходник (коробка), со- единяющий шнек с измельчителем, имеет крышку, которая в слу- чае забивания измельчителя кормом отклоняется и предохраняет шнек от поломок.
Степень измельчения регулируют изменением частоты вра- щения режущих дисков. С этой целью измельчитель оборудован сменными шкивами.
7.4.4. Машины и оборудование для дозирования кормов
При приготовлении кормовых смесей одним из важнейших технологических процессов является дозирование, к которому предъявляют особые требования.
Дозирование – это процесс отмеривания материала с заданной точностью, т.е. с погрешностью, не выходящей за установленные требования.
Неточное дозирование компонентов снижает кормовую
и биологическую питательную ценность кормовых смесей, а избы- ток дорогостоящих компонентов приводит к удорожанию продук- ции и нарушению баланса питательных веществ, а в некоторых случаях – к заболеванию животных. Особо строгую точность предусматривают при дозировании белково-витаминных и мине- ральных добавок, так как несоответствие норм их выдачи может привести даже к гибели животных.
Допустимые отклонения по массе при дозировании кормов для крупного рогатого скота, свиней и овец составляют: грубого корма, силоса, зеленой массы ±10%; корнеплодов, плодов бахче- вых культур ±15%; комбикорма и концентрированных кормов
±5%; кормовых дрожжей ±2,5%; минеральных добавок ±5%.
В практике кормоприготовления применяют массовое (весо- вое) и объемное дозирование, каждое из которых может быть пор- ционным (дискретным) или непрерывным.
Для дискретного объемного дозирования характерно перио- дическое повторение цикла выпуска дозы материала, как правило, в порционный смеситель. В большинстве случаев дозаторы данно- го типа применяются при подготовке влажных кормовых смесей, хотя известны варианты их использования и для дозирования ин- гредиентов комбикормов. Дозаторы этого типа просты по устрой- ству, но далеко не всегда отвечают указанным требованиям.
Порционное массовое дозирование основано на отмеривании дозы определенной массы. Дозирование по массе проводят раз- личными методами и на весах различной конструкции, исходя из мощности предприятия, особенностей технологического процесса и ассортимента вырабатываемой продукции. Дозаторы такого типа дают высокую точность дозирования, их устройство не сложно, но множество операций, связанных с загрузкой, взвешиванием, до- грузкой, выгрузкой сводят на нет все преимущества данного обо- рудования. Массовое дозирование не всегда дает при требуемой точности необходимую производительность, поэтому очень часто применяют комбинированные весы, на которых первоначально производят грубое взвешивание, а затем досыпку. К недостаткам весовых дозаторов следует отнести также удары механизмов в процессе работы, большую занимаемую площадь, сложность об- служивания. По этой причине весовое дозирование не нашло ши- рокого применения в условиях кормоцехов хозяйств, хотя на больших современных комбикормовых заводах дозированию по массе отдают предпочтение.
При порционном дозировании порцию смеси составляют из компонентов, которые в необходимых количествах подготавлива- ют или одновременно при помощи индивидуальных дозаторов, или в одном дозаторе поочередно каждый компонент. Подготов- ленные компоненты поступают в сборные бункеры или непосред- ственно в смеситель, который перемешивает полученную порцию
смеси в течение определенного времени.
Для массового непрерывного дозирования пока не разработа- но точного и надежного оборудования.
При использовании дозирования по массе компонентов ком- бикормов следует учитывать следующие обстоятельства. Влаж- ность наружного воздуха колеблется от 60 до 90 %. Поскольку приготовление комбикормов в хозяйствах производится в неотап- ливаемых помещениях, то равновесная влажность зерновых ком- понентов, следуя изменению влажности воздуха, может принимать значения от 12 до 20 %. Относительное изменение сухого веще- ства в кормах может при этом достигать 10 %. Поэтому, если бу- дем дозировать ингредиенты по массе даже с нулевой погрешно- стью, то животному сухого вещества будет доставаться то больше, то меньше. Это сводит на нет основное преимущество дозирова- ния по массе – малую погрешность.
Объемное непрерывное дозирование менее требовательно к состоянию компонентов и при использовании соответствующего оборудования позволяет приготавливать кормовые смеси с задан- ным качеством. В связи с этим его широко применяют в кормоце- хах.
При непрерывном дозировании все компоненты подают одно- временно непрерывными потоками в соотношениях, соответству- ющих рецептам комбикорма или составу смеси в смеситель, где происходит также непрерывное перемешивание.
Основными факторами, отрицательно влияющими на процесс дозирования, являются:
- самосортирование компонентов при поступлении в наддоза- торные бункеры;
- забивание рабочих органов крупногабаритными включения-
ми;
- различная степень уплотнения кормов в бункерах, зависящая
от высоты заполнения;
- повышенная влажность компонентов, способствующая сле- живанию, комкованию и сводообразованию;
- наличие в днищах и стенках наддозаторных бункеров вы- ступов и других препятствий, тормозящих свободный выход про- дуктов.
Некоторые компоненты обладают достаточной сыпучестью, относительно стабильно сохраняют постоянную объемную массу,
хорошо заполняют рабочие полости дозатора, не вызывают за- труднений при истечении из бункеров, не слеживаются и не обра- зуют сводов. К этим кормам относятся зерновые культуры (кроме овса). К продуктам, не обладающим этими свойствами, относятся дерть, травяная и мясокостная мука, отруби, сырье минерального происхождения т.д.
Большие затруднения возникают при дозировании мела и со- ли. Мел при влажности 12% налипает на рабочие поверхности оборудования, образуя скомкавшиеся частицы, не выходит из от- верстий бункеров. Соль при влажности 6% теряет сыпучесть и при продолжительном нахождении в бункере слеживается.
Физико-механические свойства кормов в зависимости от вре- мени хранения изменяются, в частности ухудшается сыпучесть.
Длительное хранение кормов часто приводит к их отвердева- нию. Связывающими (цементирующими) веществами являются белковые (мучнистые), минеральные и различные липкие матери- алы. Степень цементации частиц зависит от вида кормов, их спо- собности, при определенных условиях, к комкованию. В емкост- ном устройстве повышенные давление и температура в при- сутствии влаги способствуют ускорению процесса цементации частиц.
Для сохранения сыпучести влажность комбикормов при хра- нении до 30 суток не должна превышать 13%, а при более дли- тельных сроках хранения (до 60 суток) – 11,5%.
Жесткая связь между частицами комбикормов, а также их компонентов приобретается с увеличением времени хранения при нормальной влажности 13% или несколько выше ее и проявляется в увеличении сил сцепления между частицами, приобретении вяз- кости и цементации (образуются комки различной величины).
С увеличением срока хранения начальное сопротивление сдвигу у всех компонентов комбикормов, за исключением зерно- вых и дробленого жмыха, увеличивается.
Такие компоненты комбикормов, как микроэлементы, соли и их смеси, могут отвердевать, подвергаясь колебаниям температу- ры, даже при хранении в воздухонепроницаемых мешках или ем- костях. Повышение температуры вызывает дополнительное рас- творение соли, которая кристаллизуется с образованием твердых мостиков между частицами при последующем понижении темпе- ратуры. На процесс дозирования больше всего влияют такие
свойства, как сопротивление сдвигу, коэффициент внешнего и внутреннего трения и сцепление частиц, которые проявляются в большей степени с повышением влажности продукта.
К дозирующим устройствам объемного типа предъявляют следующие требования:
- регулирование расхода в заданных пределах;
- точность и устойчивость питания, необходимые для обеспе- чения постоянства заданного расхода в пределах допустимых от- клонений;
- возможность работы с различными материалами;
- простота устройства, малая металло- и энергоемкость;
- удобство обслуживания, герметичность и высокая надеж- ность;
- быстрота настройки и регулировки в зависимости от вида корма и нормы дозирования.
При объемном дозировании применяют барабанные, тарель- чатые и шнековые дозаторы, реже – вибрационные. Продукты до- зируют по двум схемам: ширине (толщине) потока продукта и скорости движения. Дозатор ДП-1 барабанного типа предназначен для дозирования сыпучих продуктов. Поэтому его устанавливают не только на комбикормовых, но и на мукомольных и крупяных предприятиях. Особенностью конструкции этого дозатора
(рис. 41) является то, что в стальном корпусе на валу закреплен барабан 1, который составлен из отдельных звездочек 3, между которыми установлены диски 2, разделяющие его на четыре сек- ции, Секции смещены относительно друг друга на 10 0 по винтовой линии. Такое расположение звездочек позволяет равномерно и непрерывно подавать компоненты при их дозировании.
![]() |
Рис. 41. Схема рабочего органа барабанного дозатора ДП-1:
1 – барабан; 2 – дозирующий диск; 3 – звездочки
В зависимости от физических свойств компонентов применя- ют звездочки различной формы: А – для зерновых; Б – для мучни- стых; В – для трудносыпучих; Г – для компонентов, входящих в рецепты в небольших количествах. Над барабаном установлен скребок для выравнивания поступающего продукта.
Технологическая схема подачи продукта в дозатор барабанно- го типа следующая. Компоненты поступают в приемную часть до- затора, где при помощи побудителя равномерно заполняют ячейки барабана. Вращаясь, продукт высыпается из них и выводится из дозатора.
Основной рабочий орган тарельчатого дозатора – вращаю- щийся горизонтальный диск 4, с которого компоненты сбрасыва- ются неподвижным скребком 2 (рис. 42). Компоненты на диск 4 поступают из приемного бункера 5 и распределяются по диску в виде усеченного конуса. Размеры конуса регулируют манжетой 1.
![]() |
Рис. 42. Схема тарельчатого дозатора:
1 – манжета; 2 – скребок; 3 – вал; 4 – диск; 5 – приемный бункер
Тарельчатый дозатор ДТ предназначен для дозирования соли, мела и других компонентов комбикормов. При дозировании соли и мела следует учитывать состояние этих компонентов по влажно- сти. В тарельчатых дозаторах можно дозировать мел влажностью не более 6-8 %, а соль влажностью 3-4 %. Для дозирования труд- носыпучих компонентов применяют дозатор ДДТ.
Малый тарельчатый дозатор МТД-3А предназначен для объ- емного дозирования минеральных компонентов комбикормов и
обогатительных смесей. Особенностью этого дозатора является то, что в верхней части его установлены вертикальный шнек и воро- шитель, которые не допускают слеживания дозируемых компонен- тов и обеспечивают равномерную подачу продукта на тарелку до- затора.
Шнековый дозатор применяют для дозирования и подачи зер- новых, мелкокусковых и мучнистых компонентов. Благодаря ва- риатору скорости, который установлен в приводном устройстве, регулирует производительность дозатора, изменяя скорость вра- щения шнека 2 (рис. 43).
![]() |
Рис. 43. Схема шнекового дозатора:
1 – приемный бункер; 2 – шнек
Подобного вида дозаторы (шнековые, тарельчатые) могут до- зировать также измельченные корнеплоды.
Наиболее трудно дозировать силос, сено, измельченные гру- бые корма (не измельченные вообще не поддаются дозированию).
В качестве питателей-дозаторов для накопления и дозирован- ной подачи стебельчатых материалов в технологических линиях кормоприготовления широко применяют цепочно-планчатые пи- татели с битерными устройствами различного конструктивного исполнения (рис. 44). Они различаются между собой рабочими органами подающих конвейерных устройств, конструкцией бите- ров, их количеством и расположением, углом наклона питателей к горизонту и приемной частью.
Технологический процесс дозированной подачи стебельчатых и других связных кормов происходит следующим образом. Нахо- дящийся в бункере питателя-дозатора монолит кормового матери- ала подается цепочно-планчатым конвейером к счесывающему устройству, состоящему из битеров. Штифты вращающихся бите- ров счесывают соприкасающийся с ними материал и выгружают на поперечный конвейер или подают непосредственно в техноло- гическую линию сбора и смешивания компонентов приго- товляемого корма.
![]() |
Рис. 44. Функциональная схема питателей-дозаторов стебельчатых кормов:
а – горизонтальный с вертикальным расположением битеров; б – наклонный с горизонтальным расположением битеров; в – ступенчатый со счесывающим планчатым конвейером
В любом случае пропускная способность битерной системы должна несколько превышать пропускную способность питателя, обеспечивающего подачу кормов к битерам. При этом условии система обеспечивает дозированную выдачу связных кормовых материалов с допустимыми отклонениями. Для повышения точно- сти дозирования стебельчатых кормов нередко применяют двух- стадийную систему, состоящую из питателей-дозаторов битерного типа и выравнивающего устройства, которое обеспечивает
сглаживание поступающего от питателя кормового потока и авто- матическое управление его работой.
Скорость движения конвейера регулируют храповым меха- низмом или вариатором. Особенностью рассматриваемых устройств является зависимость подачи дозируемого корма от за- полнения емкости накопителя. В начальный период работы, когда кормовая масса еще не сформировалась у битеров и режим их ра- боты не стабилизировался, темп подачи материала значительно отстает от нормы. При установившемся режиме количество вы- данного корма в единицу времени и точность дозирования соот- ветствуют расчетным показателям. По мере уменьшения объема кормовой массы в бункере начинается сдвиг, а затем обрушение верхних слоев массы. Количество выдаваемого корма при этом резко уменьшается и составляет 60-70% нормы установленной вы- дачи.
Для избежание нарушения нормы выдачи дозируемых кормов, особенно в условиях их непрерывного дозирования и смешивания постоянно следят за уровнем кормов в накопительном бункере и дополняют его по мере опорожнения или оснащают питатели-до- заторы дополнительными устройствами, обеспечивающими ста- бильность геометрической формы обрабатываемого битерами мо- нолита кормового материала.
Равномерность выдачи связана с битерами, конструктивные и кинематические параметры которых влияют на количество захва- тываемого каждой гребенкой корма и формирование выгружаемо- го валка массы на сборном или выгрузном конвейере. Поэтому определяют оптимальную, увязанную с подачей продольного кон- вейера, частоту вращения битеров и другие параметры, исходя из постоянства скорости продольного конвейера.
Массовые (весовые) дозаторы позволяют с большей, чем объ- емные, точностью (в условиях постоянного микроклимата) состав- лять рецепты смесей с погрешностью в пределах ±0,1-1%, и по- этому применение их обязательно в линиях приготовления преми- ксов, белково-витаминных добавок и комбикормов повышенного качества с введением компонентов, составляющих менее 3% сме- си. Применение массовых дозаторов в комбикормовой промыш- ленности, как правило, сочетается с порционным смешиванием компонентов и автоматизацией управления линиями. По кон- струкции весовые дозаторы аналогичны (рис. 45), отличаются
лишь количеством питателей и грузоподъемностью ковша. Систе- ма управления весами приводится в действие пневматикой. Давле- ние воздуха 0,4 МПа, расход 0,4 м3/ч.
![]() |
Рис. 45. Автоматический многокомпонентный дозатор серии ДК:
1 – циферблатный указатель; 2 – люк для питателя; 3 – питатель; 4 – рычажная система; 5 – ковш весов; 6 – конечный выключатель; 7 – брезентовые рукава; 8 – днище; 9 – пневматический цилиндр управления секторными заслонками днища; 10 – электропневматический клапан; 11 – станина
Каждый отдельный компонент в соответствии с заданным ре- цептом подается на весы винтовыми питателями, которые имеют индивидуальный привод от скоростных электродвигателей. Пита- тели переключают для последовательной подачи компонентов с бункеров автоматически, после получения порции заданной мас- сы. При этом в конце подачи каждой порции винтовой конвейер переключается на сниженное число оборотов для более осторож- ной досыпки. Взвешенная порция также автоматически выгружа- ется с ковша весов в смеситель либо в приемный накопительный бункер. После этого начинается новый цикл взвешивания.
Дозирование по массе компонентов в линиях приготовления влажных кормовых смесей на животноводческих фермах приме- няют по двум технологическим схемам:
- последовательное взвешивание каждого компонента с вы- грузкой его в накопительный бункер, соответствующий емкости кузова мобильного кормораздатчика-смесителя;
- последовательное взвешивание и загрузка компонентов в порционный смеситель, установленный на механических или тен- зометрических весах (в данном случае бункер смесителя является и накопительным).
Указанные системы дозирования позволяют также автомати- зировать управление технологическим процессом приготовления смесей.
Массовое непрерывное дозирование, как уже указывалось, пока затруднено из-за отсутствия надежных и простых по кон- струкции весовых дозаторов непрерывного действия. Имеющиеся системы уступают порционным по точности и экономическим по- казателям. Учитывая, что само непрерывное дозирование позволя- ет значительно повысить производительность всего комплекта оборудования при приготовлении различных кормовых смесей, целесообразен поиск более совершенных устройств для обеспече- ния измерения массы потоков, управления ее дифференциальным и интегральным значениями с погрешностью, не превышающей погрешности порционных дозаторов. В этой связи представляют интерес безынерционные акустические расходомеры.
7.4.5. Машины и оборудование для смешивания кормов
Завершающей операцией приготовления кормовых смесей яв- ляется смешивание компонентов в специальных устройствах – смесителях порционного или непрерывного действия.
С зоотехнической точки зрения важно не только ввести в со- став кормосмеси предусмотренные рационом компоненты в требу- емом соотношении, но и необходимо, чтобы все они были равно- мерно распределены во всем объеме смеси. Однородность смеси обеспечивает одинаковую питательную ценность корма во всех частях его объема. Использование для кормления животных неод- нородных по своему составу смесей значительно снижает их про- дуктивное действие. Особенно важно распределять в массе кор- мосмеси компоненты, вводимые в небольших количествах и име- ющие высокую кормовую ценность или биологическую
активность: комбикорма, БВД, премиксы, витамины, микроэле- менты, лекарственные препараты и др.
Однородность имеет большое значение, поскольку суточный рацион, а особенно разовая дача корма животным, в частности птице, очень мала.
В отдельных случаях она исчисляется несколькими десятками граммов. И в этом небольшом количестве корма должны быть все вещества, предусмотренные рационом комбикормов, БВД, преми- ксов и т.д.
Равномерность распределения компонентов обеспечивается их смешиванием.
Цель смешивания – превращение некоторого перечня компо- нентов в кормосмесь с определенными свойствами. Иначе говоря, смешивание – совокупность процессов направленного формирова- ния однородных по составу, плотности и физико-механическим свойствам систем из набора требуемых компонентов.
Иногда операцию смешивания совмещают с основным или дополнительным измельчением компонентов. В частности, хоро- шим смешивающим эффектом обладают молотковые дробилки, и это свойство успешно используется при производстве комбикор- мов. При приготовлении влажных кормосмесей применяют из- мельчители-смесители с ножевыми рабочими органами.
В зависимости от вида и способа содержания животных или птиц, принятого типа кормления, а также наличия кормов в хозяй- стве кормовые смеси готовят разной консистенции:
- сухие (комбикорма и кормосмеси) – влажность W=13-15%;
- влажные рассыпные – W=45-70%;
- жидкие (текучие) W=75-85%.
Все эти смеси получают путем механического перемешивания до однородной массы. Поэтому качество смешивания определяет- ся степенью однородности смеси. Ее минимум устанавливают зоо- технические требования:
- для свиней – 85%;
- для птицы – 90%;
- для крупного рогатого скота – 80% (с вводом карбамида –
90%);
- комбикормов собственного производства – 90-95%.
Перемешивание кормовой массы иногда проводят для пере- распределения влаги, тепла и растворения некоторых добавок.
В смесителях происходит взаимное перемещение частиц раз- личных компонентов, причем в идеальном случае может быть по- лучена смесь, в любой точке которой соотношение компонентов соответствует заданному (рис. 46).
![]() | ![]() | ![]() |
а б в
Рис. 46. Стадии смешивания двух компонентов:
а – исходное состояние; б – статистическое распределение компонентов в процессе смешивания; в – идеально перемешанная смесь (практически не осуществима)
Такое идеальное распределение возможно в смеси, где компо- ненты состоят из сферических частиц одинаковых свойств и раз- меров, и при отсутствии гравитации. Естественно, что в кормах этого не может быть, т. к. смесь компонентов состоит из частиц разных размеров, которые обладают различными физико- химическими свойствами. Поэтому на процесс их перемещения влияет огромное число факторов, а в малых объемах смешиваемо- го продукта возможно бесконечное разнообразие взаимного рас- положения частиц. Поэтому соотношение компонентов в любой точке смеси – случайная величина.
Исходя из этого, современные методы оценки качества кор- мовых смесей, степени их однородности основаны на методах ста- тистического анализа. Большое число компонентов создает систе- му со многими случайными величинами, законы которой очень сложны. Для оценки качества смеси обычно выделяют компонен- ты, содержание которых в смеси должно быть сравнительно не- большим, т. к. наиболее сложно равномерно распределить в смеси именно такие компоненты. Желательно, чтобы физические свой- ства их в наибольшей степени отличались от свойств других ком- понентов и, самое главное, чтобы метод их определения был до- статочно прост и надежен.
При периодическом смешивании в смеситель обычно поступа- ет набор компонентов, причем они предварительно почти не сме- шаны друг с другом. В процессе смешивания происходит:
- перемещение группы смежных частиц из одного места смеси в другое внедрением или скольжением слоев;
- постепенное перераспределение частиц различных компо- нентов через вновь образованные границы их раздела;
- сосредоточение частиц, имеющих близкие размеры, форму, массу в разных местах смесителя под действием сил тяжести (гравитационных сил).
В первом и во втором случаях частицы при смешивании рав- номерно распределяются в смеси, последний, третий процесс пре- пятствует равномерному распределению частиц. Все три процесса в смесителе протекают одновременно, но их роль в разные перио- ды смешивания неодинакова.
В начале процесса качество смеси улучшается в основном в результате перемещения частиц из одного места смеси в другое внедрением или скольжением слоев. Скорость процесса смешива- ния практически не зависит от физико-механических свойств ком- понентов, т. к. процесс идет на уровне больших объемов. Наиболее важную роль в это время играет конструкция смесителя, придаю- щая смеси определенный характер движения. В этот период
(т. е. в начале смешивания) частицы не успевают сосредоточиться в разных местах смесителя, т. к. в перемещаемых объемах компо- ненты относительно друг друга неподвижны.
Постепенно в процессе смешивания происходит перераспре- деление частиц. В этой фазе на эффективность смешивания начи- нают влиять плотность, форма и характер поверхности частиц, гранулометрический состав, влажность компонента, его сыпу- честь. Чем ближе по своим свойствам компоненты, тем эффектив- нее процесс их смешивания. Число компонентов также имеет зна- чение для процесса смешивания: при большом числе компонентов доля каждого из них уменьшается, а продолжительность процесса увеличивается.
Распределить равномерно компоненты с высокой дисперсно- стью легче, т. к. в единице объема содержится большее количество частиц. При этом вступает в силу процесс сосредоточения частиц, залипания их в различных частях смесителя. Чем больше различие в физико-механических свойствах смешиваемых компонентов, тем этот процесс продолжительнее.
Выбор конструкции смесителя зависит от свойств смешивае- мых компонентов. При перемешивании сыпучих компонентов
широко используют гравитационные силы, под воздействием ко- торых они пересыпаются и перемешиваются. Для трудно сыпучих компонентов и для смешивания сыпучих компонентов с жидкими гравитационных сил недостаточно, приходится перемещать мате- риал шнеками, лопатками и т. д.
При непрерывном смешивании поступление компонентов, их смешивание и выдача готовой смеси происходят непрерывно. Ка- чество готовой смеси, получаемой в этих смесителях, зависит не только от их конструкции, но и от равномерности дозирования компонентов.
Существующие дозаторы не могут обеспечить строго посто- янного количества подаваемого компонента в любую единицу времени, его обычно подают пульсирующими потоками. Поэтому смеситель не только должен хорошо перемешивать компоненты, но и сглаживать пульсацию их подачи. Выбор смесителя зависит от качества работы дозаторов. Если дозаторы подают компоненты равномерно или пульсация их подачи существенного влияния на качество смеси не оказывает, в этом случае можно выбрать смеси- тель, в котором компоненты перемещаются вдоль его оси без про- дольного перемещения частиц.
Если дозаторы подают компоненты неравномерно, необходи- мо применять смесители, способные частично или полностью сглаживать пульсации. В таких случаях кроме поперечного, долж- но обязательно быть и продольное перемещение, создаваемое обычно лопастями, которые способны перемещать компоненты как в направлении движения, так и частично обратно.
Особенно трудно получить кормосмеси, включающие силос, солому, сенаж, корнеклубнеплоды, комбикорм или дерть, которые существенно различаются по физико-механическим свойствам.
При чисто механическом смешивании создать кормосмесь требуе- мой однородности 80-90% весьма проблематично. В. И. Передня считает, что для кормов с включением длинноволокнистых ком- понентов качественная кормосмесь может быть получена только за счет срезающего смешивания и растирания порции слоя, что до- стигается дополнительным измельчением компонентов во время смешивания.
Смесители, применяемые в животноводстве, отличаются большим разнообразием. Это объясняется необходимостью приго- товления кормовых смесей с различными физико-механическими
свойствами компонентов: гранулометрическим составом, плотно- стью, формой частиц, влажностью, консистенцией и т.д. Смеши- вание кормов часто сопровождается тепловыми процессами и до- полнительным измельчением.
Применяемые в настоящее время смесители для подготовки кормовых смесей можно классифицировать следующим образом:
- по влажности (физическому состоянию) готовящейся сме- си – смесители для сыпучих, влажных и жидких кормов;
- по характеру протекающего процесса смешивания – смеси- тели периодического и непрерывного действия;
- по способу воздействия на смесь – смесители гравитацион- ные, центробежные, с механическим воздействием рабочих орга- нов;
- по конструктивному признаку – смесители с перемешиваю- щими устройствами, с быстроходными роторами, вибрационные;
- по совокупности выполняемых операций – смесители, сме- сители-запарники, смесители-измельчители, смесители- раздатчики, смесители-измельчители-раздатчики кормов.
По характеру процесса различают смесители порционного (периодического) и непрерывного действия. В зависимости от ви- да смешиваемых кормов смесители могут быть предназначены для приготовления сухих сыпучих (комбикормов), рассыпных влаж- ных и жидких (консистентных) кормов. По организации рабочего процесса все смесители делятся на две большие группы: с враща- ющейся камерой и с неподвижной камерой (или транспортирую- щие). В кормоприготовлении смесители с вращающейся камерой не получили распространения.
Ко второй группе относятся мешалочные смесители. По кон- струкции рабочих органов (мешалок) применяют смесители: для сыпучих кормов – шнековые, лопастные и ленточные; для жид- ких – турбинные, пропеллерные и лопастные; для рассыпных влажных (стебельных) кормов – шнековые и лопастные (рис. 47).
В зависимости от частоты вращения мешалок смесители делят на тихоходные и быстроходные.
Мешалочные смесители по числу мешалок делят на одно- и двухвальные.
Рассмотрим наиболее типичные рабочие органы кормосмеси- телей с неподвижной камерой.
Для приготовления комбикормов в хозяйствах применяют главным образом шнековые смесители – вертикальные, горизон- тальные, наклонные или планетарные.
![]() |
Рис. 47. Типы мешалок (по С. В. Мельникову):
1, 2, 3 – шнековые; 4, 5 – лопастные; 6, 7, 8 – ленточные;
9, 10, 11, 12 – турбинные; 13, 14, 15, 16 – пропеллерные
Для приготовления влажных кормовых смесей из стебельных кормов и корнеклубнеплодов до последнего времени применялись преимущественно тихоходные, горизонтальные одно- или двух- вальные лопастные смесители порционного действия.
Применение заменителей цельного молока для телят связано с необходимостью готовить жидкие кормовые смеси в виде
эмульсий. Применение жидкого кормления в свиноводстве требует приготовления суспензий. Приготовление кормовых дрожжей свя- зано с аэрированием биомассы для насыщения жидкой фазы кис- лородом.
Жидкие компоненты смешивают, как правило, механическим способом в аппаратах с мешалками. Но в ряде случаев применяют циркуляцию насосом или пневматическое перемешивание (барбо- таж). Для механического способа применяют тихоходные лопаст- ные мешалки или быстроходные – турбинные и пропеллерные.
Лопастные мешалки используют для перемешивания в малых объ- емах жидкостей большой вязкости, пропеллерные – для жидкостей малой вязкости. Турбинные мешалки допускают широкий диапа- зон вязкостей.
Для приготовления влажных кормовых смесей из стебельных кормов и корнеклубнеплодов применяют одно- или двухвальные смесители порционного действия. Промышленность выпускает двухвальные унифицированные смесители нескольких типоразме- ров, согласованных между собой по технологической схеме и ос- новным конструктивным параметрам. Смеситель С-12 является базовой моделью. Цифра после буквы в марке смесителя ука- зывает на полезную вместимость корпуса (м3).
Для небольших свиноводческих ферм и индивидуальных хо- зяйств выпускаются одновальные смесители ЗС-Ф-1, ЗС-Ф-2, СКО-Ф-3 и СКО-Ф-6, предназначенные для запаривания и приго- товления кормосмесей из концентрированных и зеленых кормов, а также пищевых отходов (используют пар низкого давления
до 0,07 МПа).
Наряду с этим промышленность выпускает варочные котлы- смесители ВК-1 и ВКС-ЗМ. Они имеют теплоизоляцию и отлича- ются более высокой степенью герметизации, что позволяет варить в них каши и супы для молодняка (ВК-1) и стерилизовать пищевые отходы (ВКС-ЗМ).
Варочный котел-смеситель ВКС-ЗМ имеет одновальную ло- пастную мешалку и рассчитан на работу с острым паром.
Смеситель С-12 предназначен для приготовления сырых и за- паренных кормовых смесей. Он выпускается в двух модификаци- ях: 1) для использования в поточных линиях кормоцехов типа КЦС без пускозащитной аппаратуры (она входит в строительную
часть кормоцеха); 2) с полным комплектом пускозащитной аппара- туры для применения в кормоцехах других типов.
Смеситель состоит из корпуса 1 (рис. 48), парораспределителя 2 с кранами, двух лопастных мешалок 3, выгрузного шнека 4, вы- грузной горловины 5, крышек 7 и системы управления 6 задвиж- кой и включением шнека. Мешалки и шнек приводятся в движение от привода 8.
Рис. 48. Смеситель С-12:
1 – корпус; 2 – парораспределитель; 3 – лопастная мешалка;
4 – выгрузной шнек; 5 – выгрузная горловина с клиновой задвижкой; 6 – система управления; 7 – крышка; 8 – привод
Корпус смесителя вместе с рамой и двумя поперечными кронштейнами является базовым узлом, на котором устанавлива- ют все механизмы, и одновременно емкостью для приготовления
кормов. Между торцевыми стенками корпуса вварены три трубы, служащие для подачи воды и растворов.
Внутри корпуса установлены две лопастные мешалки. Каждая состоит из вала с 8 лопастями и подшипниковых блоков, за- крепленных на торцевых стенках корпуса. Лопасти установлены на валу по винтовой линии под углом 45 0 и крепятся стремянками. Лопасти правой мешалки, если смотреть со стороны привода, пе- ремешивают и направляют корм в сторону приводной станции, а лопасти левой мешалки – в сторону выгрузной горловины, что обеспечивает хорошее перемешивание корма.
В нижней части смесителя расположен шнек диаметром 320 мм и шагом 250 мм, подающий перемешанную массу к вы- грузному патрубку.
Сверху корпус С-12 герметически закрыт крышками. В одной из них имеется люк с шиберной задвижкой и тягой, а в другой – смотровой люк. Сбоку крышки на кронштейне установлен конеч- ный выключатель, который отключает механизм смесителя при открытии крышки.
Система подачи пара в смеситель состоит из коллектора с ма- нометром и двух распределительных труб, которые пятью муфто- выми кранами каждая соединяются с паропроводящими патрубка- ми. Подачу пара регулируют при помощи переключателя. Чтобы корм не попадал в распределительные трубы, краны после оконча- ния запаривания должны быть закрыты.
Первыми в смеситель подают корма, которые необходимо за- паривать. Измельченные грубые корма загружают с одновремен- ным увлажнением. Мешалки включают не позднее, чем при за- полнении 1/3 технологического объема и продолжают загрузку. При этом коэффициент заполнения емкости смесителя не должен превышать 0,6...0,7 для густых смесей с включением соломы
и 0,8 – для кормов влажностью более 70 %. Затем плотно закры- вают крышки люков, открывают вентиль на паропроводе и муфто- вые краны на распределительных трубах. Давление подаваемого пара и температуру смеси контролируют по манометру и термо- метру. В среднем время запаривания в смесителе С-12 составляет 1-3 ч. По окончании запаривания необходимо перекрыть муфто- вые краны и вентили на паропроводе и в течение 40-60 мин вы- держать корм для разваривания. После этого доливают воду для охлаждения корма и загружают другие компоненты. При
приготовлении кормосмесей без запаривания все компоненты, входящие в смесь, можно подавать одновременно. Перемешивают корма 10 мин, а при обогащении их карбамидными и другими хи- мическими растворами – 15 мин.
Измельчитель-смеситель кормов ИСК-10 (рис. 49) предназна- чен для измельчения и смешивания корма. Машина состоит из но- жевого ротора 5, приемной I, рабочей II и выгрузной III камер, расположенных одна над другой, бункера 11, выгрузного транс- портера, пакетов противорезов, зубчатых дек 3, электродвигателя 7 и клиноременной передачи 9, снабженной натяжным роликом.
![]() |
Для введения в обрабатываемую массу жидких добавок преду- смотрено по две форсунки 4 на приемной и на выгрузной камерах. Приемная и рабочая камеры соединены откидными креплениями. В стенках рабочей камеры имеется шесть окон, в которых уста- навливают пакеты ножей-противорезов и зубчатые деки. Окна за- крывают с наружной стороны кожухами 12.
Рис. 49. Измельчитель-смеситель ИСК-10:
1 – рама; 2 – швырялка; 3 – зубчатая дека; 4 – форсунка; 5 – ротор;
6 – нож противореза; 7 – электродвигатель; 8 – шибер; 9 – клиноременный привод; 10 – натяжной ролик; 11 – бункер выгрузного транспортера; 12 – кожух; 13 – основание; 14 – вал; I – приемная камера; II – камера измельчения
и смешивания; III – выгрузная камера
На рабочем органе-роторе размещены ярусами ножи измель- чителя, выполняющие также роль смесителей, и молотки.
В нижней части ротора, расположенной в выгрузной камере, нахо- дится двухлопастная швырялка. Ножи и молотки размещены в па- зах между фланцами, установленными на шлицах головки ротора при помощи специальных болтов и пальцев.
Пакет ножей-противорезов собран на валу 14, установленном шарнирно на основании 13, прикрепляемом болтами к корпусу рабочей камеры. Основание и кронштейн вала соединены пружи- ной, под воздействием которой ножи-противорезы входят в рабо- чую камеру через прорези в пластине и удерживаются ею в рабо- чем положении. При попадании в камеру посторонних включений шарнирно-пружинное крепление противорезов позволяет им от- клоняться без поломки и пропускать твердые предметы.
При работе измельчителя-смесителя корма загружаются в ка- меру 1 и попадают в зону взаимодействия ножей 6 верхнего яруса с режущими элементами ротора 5, где частично измельчаются. За- тем частицы кормов увлекаются на гладкий участок внутренней поверхности камеры и под действием силы тяжести по спирали несколько перемещаются вниз. На пути своего движения частицы кормов встречаются зубчатые деки 3, и их скорость уменьшается.
Ножи следующего яруса, являясь более длинными, осуществ- ляют дополнительное измельчение и дальнейшее продвижение частиц кормов. Благодаря этому одна часть измельченных кормов приобретает скорость большую, чем другая, что способствует про- никновению одних частиц кормов в массу других и эффективному их смешиванию. При выходе на гладкий участок внутренней по- верхности камеры измельченные частицы кормов опять переме- щаются вниз, встречая на своем пути зубчатые грани ножей 3 и режущих элементов нижнего яруса 4, взаимодействующих между собой. В этом месте происходит окончательное измельчение ча- стиц кормов вдоль волокон.
В процессе измельчения режущие элементы под действием силы резания постоянно колеблются, поворачиваясь на валу 14, автоматически выбирая оптимальные углы резания и обеспечивая равномерный износ режущих частей измельчителя-смесителя. При попадании в камеру 1 твердых посторонних предметов режущие элементы 6 отклоняются на большую величину, выходя за преде- лы внутренней поверхности камеры, обеспечивают свободное прохождение твердых предметов, предотвращая поломку режущих частей и их заклинивание. В машину подают на смешивание
предварительно измельченные компоненты, причем перед этим снимают диаметрально расположенные пластины с противорезами и устанавливают деки. При необходимости доизмельчения компо- нентов смеси оставляют на месте три пакета противорезов и три зубчатые деки, чередуя их в окнах рабочей камеры. При измельче- нии одного вида корма или нескольких компонентов, подлежащих измельчению и смешиванию, в окнах устанавливают все шесть пакетов противорезов. Производительность машины, работающей на смешивании, может доходить до 25 т/ч, на смешивании с ча- стичным доизмельчением – до 15 т/ч, на измельчении, например, соломы – до 3-4 т/ч при длине резки до 30 мм и 4-8 т/ч при длине резки до 50 мм. Степень измельчения регулируют, изменяя число ножей на роторе, число противорезов и время нахождения продук- та в рабочей камере (при помощи кольцевого шибера, установлен- ного над швырялкой).
Машина обеспечивает смешивание силоса, соломы, корнепло- дов и комбикорма со степенью равномерности 80-90%; установ- ленная мощность двигателя 39,2 кВт; частота вращения ротора
17 с-1; габариты машины 1600×1090×1150 мм; масса с выгрузным транспортером 2200 кг. Обслуживает измельчитель-смеситель один рабочий.
Рассмотрим в качестве примера оборудование для приготов- ления мелассы – смеситель мелассы СМ-1,7 (рис. 50).
Он является комплексной установкой для приготовления вод- ного раствора мелассы с карбамидом, который добавляется в жом и грубые корма на фермах крупного рогатого скота. Смеситель состоит из комплекта технологического оборудования, в который входят смеситель, цистерна для приема и хранения расходного за- паса мелассы, приемная воронка для слива мелассы из транспорт- ных средств, фильтр, насос, трубопроводы, арматура и элек- трооборудование.
Смеситель представляет собой металлическую емкость ци- линдрической формы с одновальной мешалкой. На нем располо- жены патрубки для подключения трубопроводов горячей воды, мелассы, отбора готового раствора и горловина с крышкой для доступа в смеситель и загрузки карбамида. Количество раствора в смесителе контролируют по указателю уровня.
Рис. 50. Смеситель CM-1,7:
1, 5 – электродвигатели; 2, 7 – редукторы; 3 – смеситель; 4 – трубопровод
мелассы; 6, 9 – трубопроводы питания насоса; 8 – емкость; 10 –трубопроводы перекачки мелассы и раствора; 11 – трубопровод выдачи раствора; 12 – шланг; 13 – специальный болт; 14 – воронка; 15, 21 – колена; 16 – фильтр мелассы;
17 – шестеренный насос; 18 – трубопровод очищенной мелассы; 19 – рычаг;
20 – кран; 22 – рама; 23 – электрошкаф
Цистерна мелассы оборудована внутри радиаторной батареей для подогрева и разжижения мелассы. Заполнение цистерны кон- тролируют по указателю уровня.
Приемную воронку устанавливают снаружи здания в месте, удобном для приема. Воронка имеет два корпуса, между которыми расположены паровая рубашка для подогрева корпуса и фильтр грубой очистки мелассы.Фильтр тонкой очистки состоит из двой- ного корпуса для подогрева паром, фильтрующей сетки и крышки с резиновой прокладкой.
Мелассу и готовый раствор перекачивает насос НШП-20-59. Он имеет собственный электродвигатель, смонтированный на од- ной плите с насосом. Для подогрева рабочей камеры насоса и его сальников при засахаривании предусмотрен подвод пара через резьбовые отверстия в крышках.
7.4.6. Предприятия по приготовлению кормовых смесей
(кормоцехи)
Кормообрабатывающие предприятия в сельскохозяйственном производстве по свойствам приготавливаемых кормов делятся на две группы (рис. 51). Предприятия группы I (заводы, цехи, агрега- ты) предназначены для подготовки в рассыпном, гранулированном или брикетированном виде сухих кормов, пригодных для длитель- ного хранения (комбикорма, кормовых добавок, травяной муки, полнорационных кормосмесей). Предприятия группы II (цехи) го- товят влажные кормосмеси непосредственно перед скармливанием животным.
![]() |
Рис. 51. Классификация кормообрабатывающих предприятий в сельскохозяйственном производстве (по В. И. Земскову)
Работа технологических линий кормоцехов первой группы не согласовывается с распорядком дня животноводческой фермы или комплекса. Кормосмеси, приготовленные в таких кормоцехах, должны иметь все ингредиенты, предусмотренные рецептом. От- клонения от принятой технологии не допускаются. Работа техно- логических линий кормоцехов второй группы согласовывается с распорядком дня животноводческой фермы или комплекса. Кор- мосмеси в своем составе могут иметь разное количество ингреди- ентов в соответствии с зоотехническими нормами кормления жи- вотных, поэтому отказ одной из технологических линий не всегда приводит к прекращению выпуска готовой продукции.
Кормоприготовительные цехи второй группы различаются по виду обслуживаемых животных (для ферм и комплексов крупного рогатого скота, свиноводческих ферм и др.), они также могут быть универсальными.
На фермах и комплексах крупного рогатого скота для подго- товки влажных полнорационных кормосмесей применяют кормо- цехи с использованием соломы, прошедшей термическую обра- ботку, и без такой обработки. Первый тип кормоцехов отличается более сложным схемно-конструктивным исполнением: в комплек- те машин и оборудования имеются агрегаты или установки для термохимической обработки соломы, например смесители С-12 и др. Технология подготовки кормов в таких кормоцехах позволяет полнее использовать возможности механизации для увеличения производства животноводческой продукции. Кормоцехи свино- водческих ферм и комплексов по технологическим признакам также делятся на два типа: для подготовки влажных или жидких кормосмесей из кормов собственного производства и для подго- товки жидких кормосмесей с использованием пищевых отходов. В первом случае в зависимости от типа кормления (концентратно- корнеплодный или концентратно-картофельный) кормоцехи име- ют незначительно отличающиеся наборы машин.
В соответствии с номенклатурой, разработанной Гипрони- сельхозом, для удовлетворения потребности в кормах молочных ферм и комплексов требуются кормоцехи четырех размерных групп, для свиноводческих – семи. Из множества разработанных проектов кормоцехов для приготовления влажных кормосмесей рассмотрим в качестве примера комплект оборудования КОРК-5, оборудование которого выпускается серийно.
Для приготовления влажных кормосмесей, в состав которых входят солома (россыпью, в рулонах, в тюках), сенаж или силос, корнеклубнеплоды, концентраты, химические растворы и другие добавки, предназначен комплект оборудования KOPK-5. Его мож- но использовать на молочных фермах с поголовьем 200-400 коров и откормочных фермах до 1000 голов крупного рогатого скота.
Вариант КОРК-5-1 для откормочных ферм не имеет линии корнеклубнеплодов.
Комплект оборудования КОРК-5 имеет 5 технологических линий: грубых кормов (сено, солома, силос или сенаж) 1
(рис. 52 а), корнеклубнеплодов 5, концентрированных кормов 2,
жидких кормовых добавок 4 и смешивания кормов 3.
Грубые корма самосвальным транспортом загружают в при- емный лоток питателя-дозатора 9 (рис. 52, б), где они разрыхляют- ся, дозируются битерами, подаются на сборный транспортер 11 и в измельчитель-смеситель 12, затем в пневмошвырялку 1 и по пнев- мопроводу 2 – в циклон бункера-дозатора 8. В освободившийся от сухих грубых кормов питатель-дозатор 9 загружают силос или се- наж.
Концентрированные корма загрузчиком ЗСК-10 (или другим) подаются в бункер-дозатор10.
Корнеклубнеплоды с самосвальных транспортных средств вы- гружаются в приемный бункер 7 скребкового транспортера, про- ходят через измельчитель-камнеуловитель 6, промываются, из- мельчаются, поступают в бункер-дозатор 5 и скребковым транс- портером 4 подаются на сборный транспортер 11.
Жидкие кормовые добавки от оборудования 3 подаются в приемную камеру измельчителя-смесителя 12.
Комплектом КОРК-5 управляют с пульта управления. При включении пневмошвырялки, измельчителя-смесителя ИСК-3А-1 и сборного транспортера на последний подаются измельченные грубые корма, силос или сенаж, концентрированные корма, из- мельченные корнеклубнеплоды.
Многослойная масса одновременно с жидкими добавками направляется на смешивание в измельчитель-смеситель ИСК-ЗА-1, откуда при помощи пневмошвырялки через перекидной клапан выгружается в кормораздатчик.
Комплект оборудования КОРК-5 имеет номинальную произ- водительность 5 т/ч, установленную мощность 106,7 кВт и массу 13,3 т.
![]() |
Рис. 52. Комплект оборудования рассыпных кормосмесей КОРК-5:
а – общий вид: 1 – линия грубых кормов; 2 – линия концентрированных кормов;
3 – линия смешивания; 4 – линия жидких кормовых добавок;
5 – линия корнеклубнеплодов; б – технологическая схема: 1 – пневмошвырялка; 2 – пневмопровод; 3 – оборудование жидких кормовых добавок; 4 – транспортер ТС-40; 5 – бункер-дозатор корнеклубнеплодов КОРК-15.03.01;
6 – измельчитель-камнеуловитель ИКМ-Ф-10; 7 – приемный бункер ПБ-15; 8 – бункер-дозатор грубых кормов; 9 – питатель-дозатор ПДК-Ф-3-2;
10 – бункер-дозатор концкормов; 11 – сборный транспортер ТС-40М;
12 – измельчитель-смеситель ИСК-3А-1
Комплекты оборудования кормоцехов типа КЦС предназна- чены для механизированного приготовления запаренных или сы- рых кормовых смесей влажностью 60-80 %.
Разработано несколько модификаций кормоцехов типа КЦС. Комплекты оборудования кормоцехов КЦС-10/1000
и КЦС-200/ 2000 используют на смешанных свинофермах соответ- ственно на 100 и 200 свиноматок со шлейфом 1000 и 2000 голов на откорме, а КЦС-2000, КЦС-3000 и КЦС-6000 («Маяк-6») – на от- кормочных фермах с поголовьем соответственно 2000, 3000
и 6000 свиней.
Все унифицированные кормоцехи аналогичны базовому
КЦС-6000 («Маяк-6»), включают в себя пять поточных технологи- ческих линий: концентрированных кормов, силоса и зеленой мас- сы; травяной муки; корнеклубнеплодов; приготовления и выдачи готовых смесей.
Линия концентрированных кормов предназначена для приема, хранения и дозированной загрузки концентрированных кормов в смеситель. Она состоит из приемного бункера вместимостью 15 м 3 и питателя 1 (рис. 53). Концентраты по мере необходимости пода- ются питателем в сборный загрузочный шнек ШЗС-40М и далее – в запарник-смеситель С-12. Дозирование кормов определяют про- должительностью работы питателя 1. Линия силоса и зеленой мас- сы включает в себя измельчитель кормов 3, загрузочный скребко- вый транспортер 2 и загрузочный шнек 8. Подача линии 5-10 т/ч.
Линия приготовления травяной муки содержит универсаль- ную дробилку КДУ-2, питатель ПСМ-10 и транспортер ТС-40С. Сено подают в дробилку 5 вручную. Сенная мука воздушным по- током, создаваемым вентилятором дробилки, подается в циклон и через шлюзовой затвор поступает в бункер питателя 4. Из него она высыпается на транспортер 2, который направляет ее в шнек 8 или непосредственно в запарник-смеситель 9. Производительность ли- нии 1,5 т/ч.
В линию подготовки корнеклубнеплодов входят приемный бункер вместимостью 9 м 3, который расположен на уровне пола, скребковый транспортер ТК-5Б со шнеком и мойка-измельчитель ИКМ-5. Корнеклубнеплоды доставляют самосвалом к цеху и вы- гружают в приемный бункер, из которого они подаются выгруз- ным шнеком и наклонным скребковым транспортером 6 в мойку- измельчитель 7. Здесь они отмываются от почвы, измельчаются
и подаются в сборный загрузочный шнек 8 или непосредственно в запарник-смеситель 9. Подача линии на свекле составляет 3-4 т/ч, на картофеле – 1-2 т/ч.
![]() |
Рис. 53. Технологическая схема кормоприготовительного цеха КЦС-6000 («Маяк-6»):
1 – питатель концентрированных кормов ПК-6; 2 – транспортер ТС-40С,
3 – измельчитель «Волгарь-5»; 4 – питатель сенной муки ПСМ-10; 5 – дробилка КДУ-2, 6 – транспортер корнеклубнеплодов ТК-5Б; 7 – мойка-измельчитель кормов ИКМ-5; 8 – шнек ШЗС-40М, 9 – запарник-смеситель С-12; 10 – шнек ШВС-40; 11 – выгрузной транспортер ТС-40М, А – концентрированные корма; Б – зеленая масса; В – сено; Г – корнеклубнеплоды,
Д – готовая кормосмесь
Линия приготовления и выдачи готового корма включает в себя загрузочный сборный шнек ШЗС-40М, два запарника- смесителя вместимостью по 12 м 3 (КЦС-6000, КЦС-3000) или за- парник С-12 и варочный котел ВК-1 (КЦС-200/2000), или запар- ник-смеситель С-7 и варочный котел ВК-1 (КЦС-100/1000), вы- грузной сборный шнек ШВС-40; транспортер готового корма ТС-40М.
Со всех технологических линий корнеклубнеплоды, концен- трированные и зеленые корма, травяная мука поступают в загру- зочный сборный шнек 8, который находится над запарником- смесителем, и поочередно их загружают. Одновременно с загруз- кой смесителя корм перемешивается вращающимися мешалками.
Приготовленные корма из запарников-смесителей подаются в вы- грузной транспортер 11 для загрузки в кормораздатчик или другое транспортное средство.
Производство комбикормов непосредственно в коллективных или фермерских хозяйствах позволяет экономить на транспортных расходах, избежать потерь зерна при перевозках, в нужной мере использовать собственное сырье. Если при этом еще использовать покупные белково-витаминые добавки (БВД), то можно получить комбикорм высокого качества, в полной мере отвечающий физио- логическим потребностям крупного рогатого скота, свиней, овец и других сельскохозяйственных животных.
Себестоимость комбикормов собственного производства
в 2-3 раза ниже, чем стоимость покупных комбикормов, произве- денных на крупных комбикормовых заводах.
Известны три схемы (рис. 54) построения технологического процесса:
1. Последовательно-параллельная подготовка всех компонен- тов и одноразовое дозирование (классический способ).
Зерновые компоненты после очистки измельчаются раздельно (за каждой дробилкой закрепляют зерновые культуры, сходные по своим технологическим показателям) и размещаются в над доза- торных бункерах. Дозирование компонентов осуществляется мно- гокомпонентными весовыми дозаторами с использованием порци- онных смесителей, или батареей объемных дозаторов при не- прерывном смешивании (рис. 54, а).
Классические схемы из-за многочисленных параллельных технологических линий насыщены основным, вспомогательным и транспортным оборудованием, работа которого требует больших затрат энергии.
2. Формирование предварительных смесей зернового сырья с повторным дозированием.
Зерновые материалы измельчают одновременно (после пред- варительного дозирования и смешивания) и размещают эту смесь в одном наддозаторном бункере. Затем ее и другие компоненты дозируют при помощи многокомпонентных весовых дозаторов в смеситель порционного действия (рис. 54, б).
1 7
З е р н о в ы е
О т р у б и
Ж мМ ые хл
С о П лр ье м и к с
6
5
3
Р а с с ы п н о й к о м б и к о р
2 4 а
7
З е р н о в ы е
О т р у б и
Ж мМ ые хл
С о П лр ье м и к с
9
6
5
Р а с с ы п н о й к о м б и к о р
1 8 2 3
1
4
б
6 4
З е р н о в ы е
Ж мМ ые х л
О т р у б и
С о л
ь П р е м и к с
Р а с с ы п н о й к о м б и к о р м
2 10 8
в
Рис. 54. Технологические схемы производства комбикормов:
а – классическая схема с последовательно-параллельной подготовкой компонентов, б – классическая схема с формированием предварительной смеси, в – прямоточная схема
Такая схема позволяет значительно увеличить производитель- ность дробилок и снизить удельный расход электроэнергии, одна- ко она не лишена недостатков ранее рассмотренного варианта.
3. Прямоточный метод.
Все компоненты обрабатываются в потоке вплоть до выпуска готовой продукции. Зерновые материалы дозируют при помощи многокомпонентного дозатора непрерывного действия с последу- ющим их измельчением и смешиванием в дробилке. Полученная зерновая смесь и другие компоненты подаются в прямоточный шнек-смеситель (рис. 54, в), где происходит окончательное сме- шивание, и получение комбикорма.
Такая схема позволяет в полной мере использовать принцип поточности и, следовательно, достичь высокой производительно- сти, а также сократить количество используемого оборудования и снизить удельный расход электроэнергии.
Контрольные вопросы
1. Перечислите основные зоотехнические требования к приготовлению кормов.
2. Что называется измельчением и какие рабочие органы имеют маши- ны для измельчения грубых кормов?
3. Опишите устройство измельчителя грубых кормов и принцип дей- ствия штифтового дискового измельчителя.
4. Как предотвратить снижение производительности измельчителя при высокой влажности корма?
5. Какие конструктивные изменения имеют измельчители ИКМ-Ф-10 и ИКУ-Ф-10 по сравнению с ИКМ-5?
6. Как регулируют размер получаемых частиц при измельчении корне- клубнеплодов на машинах типа ИКМ?
7. Опишите устройство и рабочий процесс измельчителя кормов маши- ны ИКВ-5А «Волгарь-5».
8. Как регулируют степень измельчения кормов на измельчителе ИКВ-5А «Волгарь-5»?
9. Объясните принцип действия молотковых дробилок.
10. Расскажите о назначении и рабочем процессе безрешетной дробил- ки зерна ДБ-5.
РЕКОМЕНДУЕМАЯ ЛИТЕРАТУРА
1. Трухачев, В. И. Техника и технологии в животноводстве : учеб. пособие / В. И. Трухачев, И. В. Атанов, И. В. Капустин, Д. И. Грицай. – СПб. : Лань, 2016. – 380 с.
2. Федоренко, И. Я. Ресурсосберегающие технологии и оборудо- вание в животноводстве : учеб. пособие / И. Я. Федоренко,
В. В. Садов. – СПб. : Лань, 2012. – 304 с.
3. Федоренко, В. Ф. Инновационные технологии, процессы
и оборудование для интенсивного разведения сельскохозяйствен- ной птицы / В. Ф. Федоренко, Н. П. Мишуров, Т. Н. Кузьмина
[и др.]. – М. : ФГБНУ «Росинформагротех», 2017. – 100 с.
4. Федоренко, В.Ф. Инновационные технологии, процессы и обо- рудование для интенсивного разведения свиней / В. Ф. Федорен- ко, Н. П. Мишуров, Т. Н. Кузьмина [и др.]. – М. : ФГБНУ «Росин- формагротех», 2017. – 128 с.
5. Фролов, В. Ю. Комплексная механизация свиноводства и пти- цеводства : учеб. пособие / В. Ю. Фролов, В. П. Коваленко,
Д. П. Сысоев. – СПб. : Лань, 2016. – 176 с.
6. Фролов, В. Ю. Машины и технологии в молочном животно- водстве : учеб. пособие / В. Ю. Фролов, Д. П. Сысоев, С. М. Сидо- ренко. – СПб. : Лань, 2017. – 308 с.
7. Хазанов, Е. Е. Технология и механизация молочного животно- водства : учеб. пособие / Е. Е. Хазанов, В. В. Гордеев, В. Е. Хаза- нов. – СПб. : Лань, 2016. – 352 с.
АЛФАВИТНО-ПРЕДМЕТНЫЙ УКАЗАТЕЛЬ
Агрегат 45, 80, 122
Аппарат 45, 49, 71, 72, 81, 95,
97, 101, 104, 107, 109, 112, 126,
128
Беспривязное содержание скота
8, 11, 29
Бокс 12, 13, 30, 46
Грубые корма 36, 85, 154
Дека 101, 102, 109, 115
Дозатор 129, 153
Дозирование 80, 128, 132 Дробилка безрешетная ДБ-5 113 Дробильный аппарат 107
Животноводческая ферма 4
Животноводческий комплекс 4,
74
Зеленые корма 84 Измельчитель грубых кормов ИГК-30Б 95, 96, 98, 99
Измельчитель ИГК-Ф-4 95, 100
Измельчитель ИКМ-Ф-10 127,
128
Измельчитель ИР-8 104
Измельчитель кормов ИКВ-5А
«Волгарь-5» 125
Комбикорма, БВД, ЗЦМ 90
Комплект оборудования 82, 153,
154, 155
Концентрированные корма 35,
91, 154
Корма животного и микробного происхождения 83, 89
Кормоцех 18, 152, 156
Коровник 11
Массовое дозирование 129
Механизм 81
Молотковая дробилка 106
Молоток106, 109, 111 Небелковые азотистые соедине- ния 83, 90
Объемное дозирование 129
Овчарня 25, 40, 42
Отара 41, 45
Питающий механизм 110, 112
Плющилка 106, 122
Поточно-технологическая линия
8
Привязное содержание 28
Продуктивность молочная 28
Продуктивность мясная 28
Племенная ферма 5
Птичник 20, 21, 55, 61, 62
Режущий аппарат 81, 109, 112,
126
Репродукторная ферма 5
Решето 101, 102, 106, 108, 111,
112
Ротор 102, 114, 116, 148
Свиноводческое предприятие 17 Система содержания овец 40 Смеситель 145, 146, 150, 151,
156, 157, 158
Смешивание 78, 139, 142, 149,
150, 154, 160
Сочные корма 35, 85 Стойловое (привязное) содер- жание скота 8, 28
Телятник 13
Технологический процесс 51,
70, 77, 98, 103, 111, 117, 122, 135
Товарная ферма 5 Универсальная дробилка кормов КДУ-2А 107, 108
Установка 46, 48, 49, 89 Фермы и комплексы крупного рогатого скота 7
Фуражир 94
Шлюзовой затвор 108, 109, 112,
156
ОГЛАВЛЕНИЕ
Предисловие................................................................................ 3
1. Животноводческие фермы и комплексы................................. 4
1.1. Фермы и комплексы крупного рогатого скота............... 7
1.2. Свиноводческие фермы и комплексы............................. 16
1.3. Птицеводческие предприятия......................................... 19
1.4. Овцеводческие фермы и комплексы............................... 23
2. Технология производства молока и говядины...................... 27
2.1. Системы и способы содержания КРС............................. 28
2.2. Технология производства молока на промышленных фермах и комплексах 29
2.3. Технология производства говядины на промышленных фермах и комплексах 31
3. Технология производства свинины........................................ 33
3.1. Хозяйственно полезные признаки и биологические осо- бенности свиней 33
3.2. Откорм свиней................................................................. 34
3.3. Лагерное содержание и кормление свиней.................... 36
3.4. Промышленные свиноводческие комплексы. Поточная система производства свинины 37
4. Технология производства овцеводческой продукции........... 40
4.1. Механизация кормопроизводства и кормления овец.... 40
4.2. Механизация поения раздачи корма и уборки навоза.. 42
4.3. Механизация стрижки и купания овец............................ 43
4.4. Механизация доения овец............................................... 48
5. Технология производства птицеводческой продукции......... 51
5.1. Технология производства яиц кур.................................. 51
5.2. Выращивание ремонтного молодняка........................... 55
5.3. Родительское стадо кур-несушек................................... 60
5.4. Промышленное стадо кур-несушек............................... 63
5.5. Механизация содержания промышленного стада кур- несушек 65
5.6. Механизация обработки продуктов птицеводства........ 67
6. Механизированные технологические процессы.................... 74
6.1. Классификация технологических процессов................. 74
6.2. Рабочие и функциональные схемы технологических процессов 78
6.3. Технические средства для осуществления технологиче-81
ских процессов……………………………………………………..
7. Машины и оборудование для приготовления кормов и кор- мовых смесей 83
7.1. Виды кормов, применяемых в животноводстве и их ха- рактеристики 83
7.2. Зоотехнические требования к кормам и к обработке кормов 90
7.3. Способы и схемы подготовки кормов к скармливанию 92
7.4. Машины и оборудование для подготовки кормов
к скармливанию......................................................................... 94
7.4.1. Машины и оборудование для измельчения грубых кормов 94
7.4.2. Машины и оборудование для измельчения зерновых кормов 105
7.4.3. Машины и оборудование для измельчения сочных кормов 123
7.4.4. Машины и оборудование для дозирования кормов... 128
7.4.5. Машины и оборудование для смешивания кормов.... 138
7.4.6. Предприятия по приготовлению кормовых смесей
(кормоцехи)............................................................................... 152
Рекомендуемая литература....................................................... 161
Алфавитно-предметный указатель........................................... 162
Учебное издание
Денисов Сергей Владимирович Грецов Алексей Сергеевич Мишанин Александр Леонидович Янзина Елена Владимировна Киров Юрий Александрович Васильев Сергей Александрович
Технология и механизация животноводства
Учебное пособие
Подписано в печать 21.12.2018. Формат 60×84 1/16
Усл. печ. л. 9,59, печ. л. 10,31.
Тираж 100. Заказ №365.
Отпечатано с готового оригиналмакета в редакционноиздательском отделе ФГБОУ ВО Самарской ГСХА
![]() |
|
Дата добавления: 2022-01-22; просмотров: 36; Мы поможем в написании вашей работы! |
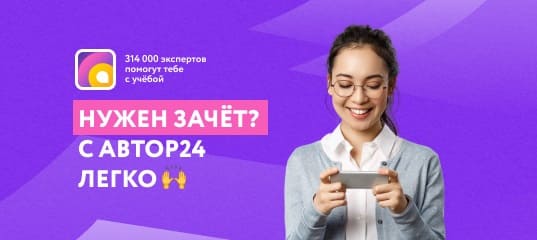
Мы поможем в написании ваших работ!