Процесс резания при сверлении.
Практическая работа № 4
Тема занятия: Сверление металла.
Цели занятия:
Дидактическая: Изучить теорию основных приемов сверления металла, ознакомиться с инструментом, приспособлениями и оборудованием используемым для сверления металла, способствовать овладению техникой резки металла. Рассчитать скорость резания по варианту задания. Дать ответы на контрольные вопросы.
Развивающая: развитие у студентов самостоятельность и инициативу при выполнении практической работы, развить мозговую деятельность при расчете скорости резания.
Воспитательная:воспитание у студентов бережного отношение к инструменту, оборудование и материалу, аккуратность и внимательность в работе, соблюдения требований охраны труда. Стремиться воспитать чувство гордости за избранную профессию.
Вид занятия: комбинированное.
Оборудование и материалы: учебники, справочники, карандаши, линейки, транспортир, тетрадь, циркуль, вычислительная техника, методические рекомендации, наглядные пособия.
Теоретические сведенья.
СВЕРЛЕНИЕ МЕТАЛЛА.
Сверление — основной способ получения глухих и сквозных цилиндрических отверстий в сплошном материале заготовки. В качестве инструмента при сверлении используется сверло, имеющее две главные режущие кромки. Для сверления используются сверлильные и токарные станки.
На сверлильных станках сверло совершает вращательное (главное движение) и продольное (движение подачи) вдоль оси отверстия, заготовка неподвижна (рисунок, позиция а).
|
|
При работе на токарных станках вращательное (главное движение) совершает обрабатываемая деталь, а поступательное движение вдоль оси отверстия (движение подачи) совершает сверло (рисунок, позиция б).
Диаметр просверленного отверстия можно увеличить сверлом большего диаметра. Такие операции называются рассверливанием (рисунок, позиция в).
При сверлении обеспечиваются сравнительно невысокая точность и качество поверхности. Для получения отверстий более высокой точности и чистоты поверхности после сверления на том же станке выполняются зенкерование и развертывание.
Рисунок 1. Работа сверла при сверлении.
Приемы сверления.
Перед сверлением необходимо разметить центр отверстие, накернив его. Для этого нужно установить острие кернера в предполагаемый центр отверстия и ударить по нему молотком. Кернение необходимо для исключения скольжения сверла в первый момент сверления. Если след от кернера не достаточно большой для удержания сверла большого диаметра, то следует расширить углубление сверлом маленького диаметра. Оптимальными для сверления большинства металлов являются малые и средние обороты - 500-1000 об/мин. Высокие обороты быстро нагревают сверло, вследствие чего может произойти его отжиг и разупрочнение. При сверлении не стоит слишком сильно давить на сверло, подача должна быть медленной и плавной.
|
|
Для создания лучших условий сверления желательно окунуть кончик сверла в машинное масло или капнуть им в место кернения. Масло в зоне сверления способствует лучшему охлаждению сверла и облегчает резание металла. Сверло, которым сверлят с использованием масла, меньше тупится, требует более редких заточек и дольше служит. В качестве охлаждающей жидкости используют также специальную эмульсию, мыльную воду, керосин.
При сквозном сверлении с большой подачей, на выходе отверстия образуется заусенец (грат), за который сверло цепляется режущими кромками. В результате может произойти резкая блокировка сверла и его перелом. Чтобы избежать образования грата, нужно заканчивать сверление отверстий в металле с малой подачей. Желательно также под просверливаемую деталь подложить деревянный брусок, который препятствует образованию заусенца. Брусок и заготовка должны быть плотно прижаты друг к другу. Чаще всего приходится осуществлять сверление стали, но нередко приходится сверлить и другие металлы, которые имеют свои особенности сверления. Алюминий, например, обволакивает сверло, затрудняя его проникновение вглубь и расширяя получаемое отверстие. Если требуется сверлить в алюминии точное отверстие (например, под резьбу), нужно обязательно применять охлаждающую жидкость и почаще извлекать сверло из отверстия для его очистки. Отверстия большого диаметра следует сверлить поэтапно. Сначала нужно просверлить деталь тонким сверлом, затем рассверлить отверстие до большего диаметра. Например, отверстие диаметром 12 мм лучше сверлить в два или три приема - последовательно сверлами 5, 10 и 12 мм.
|
|
Для сверления глухих отверстий на многих сверлильных станках имеются механизмы автоматической подачи с лимбами, которые и определяют ход сверла на нужную глубину. Если же ваш станок не оснащен таким механизмом или вы сверлите ручной дрелью, то можно использовать сверло со втулочным упором;
— если вам нужно просверлить неполное отверстие, расположенное у края детали, то наложите на деталь пластину из такого же материала, весь пакет укрепите в тисках и просверлите отверстие. Пластина затем снимается;
— когда необходимо просверлить отверстие в полой детали (например, в трубе), отверстие предварительно забивают деревянной пробкой. Если труба большого диаметра, а отверстие требуется сквозное, то приходится сверлить с двух сторон.
|
|
— получить ступенчатые отверстия можно двумя способами. Первый: сначала сверлится отверстие наименьшего диаметра, затем (на нужную глубину) — отверстие большего диаметра и последним просверливается отверстие наибольшего диаметра; второй способ — с точностью до наоборот: сначала на нужную глубину сверлят отверстие наибольшего диаметра, затем — меньшего, и в конце — наименьшего диаметра;
— если нужно просверлить отверстие на криволинейной плоскости или плоскости, расположенной под углом, то сначала следует сделать (выпилить, вырубить) площадку, перпендикулярную к оси будущего отверстия, накернить центр, а затем сверлить отверстие;
— при сверлении деталей имеющих большую толщину (при глубоком сверлении), когда глубина отверстия более пяти диаметров сверла, его нужно периодически вынимать из отверстия и удалять стружку, иначе инструмент может заклинить.
Сверло состоит из трёх элементов:
- Кромки врезаются в дно отверстия и снимают с него тонкую стружку.
- Спиральная нарезка выталкивает стружку из отверстия.
- Хвостовик предназначен для крепления сверла в патроне инструмента.
Конструкция спирального сверла по металлу
О режущих кромках стоит рассказать более подробно. Это два скоса на остром конце сверла, которые сходятся в вершине — самой выступающей точке передней части, образуя перемычку. Угол, под которым сходятся кромки, называют главным углом при вершине, его величина стандартизирована для различных материалов и режимов обработки:
· Твёрдая сталь и нержавейка: 135–140°
· Конструкционная сталь: 135°
· Алюминий, бронза, латунь: 115–120°
· Медь: 100°
· Чугун: 120° задний угол и 90° угол заточки кромки
Рекомендуемые углы заточки сверла по металлу
Каждая кромка также имеет собственный угол заточки порядка 20–35°, определяющий её остроту. Этот угол, называемый задним, обеспечивает касание сверла к металлу только по линии кромок, при этом за ними остаётся свободное пространство. Такая форма необходима для более лёгкого снятия и выброса стружки. У некоторых свёрл кромка заточена под более тупым углом, вплоть до прямого. Такие режущие кромки хорошо справляются с обработкой хрупких металлов, например, чугуна, латуни и бронзы.
Углы сверла
Угол при вершине 2φ=118° и угол наклона винтовой канавки ω=27°.
· Угол при вершине 2φ — угол между главными режущими кромками сверла. С уменьшением 2φ увеличивается длина режущей кромки сверла, что приводит к улучшению условий теплоотвода, и, таким образом, к повышению стойкости сверла. Но при малом 2φ снижается прочность сверла, поэтому его значение зависит от обрабатываемого материала. Для мягких металлов 2φ=80…90°. Для сталей и чугунов 2φ=116…118°. Для очень твёрдых металлов 2φ=130…140°.
· Угол наклона винтовой канавки ω — угол между осью сверла и касательной к винтовой линии ленточки. Чем больше наклон канавок, тем лучше отводится стружка, но меньше жёсткость сверла и прочность режущих кромок, так как на длине рабочей части сверла увеличивается объём канавки. Значение угла наклона зависит от обрабатываемого материала и диаметра сверла (чем меньше диаметр, тем меньше ω).
· Передний угол γ определяется в плоскости, перпендикулярной режущей кромке, причём его значение меняется. Наибольшее значение он имеет у наружной поверхности сверла, наименьшее — у поперечной кромки.
· Задний угол α определяется в плоскости, параллельной оси сверла. Его значения так же, как и переднего угла, изменяются. Только наибольшее значение он имеет у поперечной кромки, а наименьшее — у наружной поверхности сверла.
· Угол наклона поперечной кромки ψ расположен между проекциями главной и поперечной режущих кромок на плоскость, перпендикулярную оси сверла. У стандартных свёрл ψ=50…55°.
Переменные значения углов γ и α создают неодинаковые условия резания в различных точках режущей кромки.
Процесс резания при сверлении.
В процессе сверления, под влиянием силы резания, режущие поверхности сверла сжимают прилегающие к ним частицы металла и когда давление, создаваемое сверлом превышает силы сцепления частиц металла, происходит отделение и образование элементов стружки.
При сверлении вязких металлов (сталь, медь, алюминий и др.) отдельные элементы стружки, плотно сцепляясь между собой, образуют непрерывную стружку, завивающуюся в спираль, такая стружка называется – сливной. Если обрабатываемый металл хрупок( чугун, бронза) то отдельные элементы стружки надламываются и отделяются друг от друга. Такая стружка, состоящая из отдельных разобщенных между собой элементов, неправильной формы, носит название стружки надлома.
В процессе сверления различаются следующие элементы резания: скорость резания, глубина резания, подача, толщина и ширина стружки. Главное рабочее движения сверла (вращательное) характеризуется скоростью резания.
Скорость резания – это путь, проходимый в направлении главного движения наиболее удаленной от оси инструмента точкой режущей кромки в единицу времени. Принято скорость резания обозначать латинской буквой ὐ и измерять в метрах в минуту. Если известны число оборотов сверла и его диаметр, нетрудно определить скорость резания. Она подсчитывается по общеизвестной формуле:
м/мин.
Где D – диаметр инструмента в мм;
n- число оборотов сверла в минуту;
π- постоянное число, равное 3,14.
Порядок выполнения работы
- Выбрать вариант задания из таблици1.
Таблица 1
№№ | D | n |
1 | 10 | 200 |
2 | 12 | 300 |
3 | 14 | 400 |
4 | 16 | 500 |
5 | 18 | 250 |
6 | 20 | 350 |
7 | 8 | 180 |
8 | 6 | 160 |
9 | 11 | 260 |
10 | 13 | 230 |
- Рассчитать скорость резания по формуле:
м/мин.
- Расчет записать в тетрадь для выполнения практических работ, письменно ответить на контрольные работы.
Пример выполнения работы.
Задано: D=9мм., n=250об/мин. Рассчитать скорость резания.
=
= 7,065 об/мин.
Контрольные вопросы.
1. Дать определение, что такое сверление металла?
2. Дать определение , что такое развертывание металла?
3. Классификация сверл и их виды?
4. Какие элементы сверла вы знаете?
5. Порядок заточки сверла, угол заточки для металла?
6. Какие приспособления для ручного сверления вы знаете?
7. Какие приспособления для механизированного сверления вы знаете?
8. Какие сверлильные станки вы знаете?
9. Устройство сверлильного станка?
- Способы крепления деталей для сверления?
Использованная литература.
1. Макиенко . Н.И. Общий курс слесарного дела: учебник для студ. учреждений сред. проф. образования –М.Высшая школа 1989г.
2. Черпаков Б.И., Вереина Л.И. Технологическое оборудование машиностроительного производства. – М.: Издательский центр «Академия», 2005.-416с.
3. Черпаков Б. И. Технологическая оснастка: учебник для студ. учреждений сред. проф. образования. – М.: Издательский центр «Академия», 2007. 288 с.
Дата добавления: 2021-12-10; просмотров: 25; Мы поможем в написании вашей работы! |
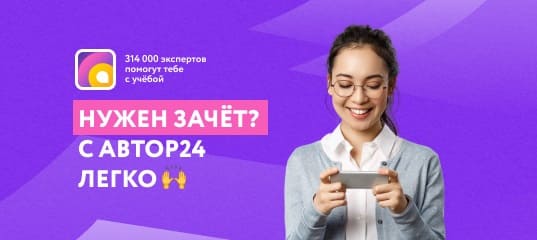
Мы поможем в написании ваших работ!