ГЛАВА2. Технологическая часть
СОДЕРЖАНИЕ
ВВЕДЕНИЕ…………………………………………………………………… | 3 |
Глава 1. Высокооктановый компонент автомобильных бензинов, пропан-пропиленовая, бутан-бутиленовая фракция..................................... | 4 |
1.1. Характеристика производимой продукции.............................................. | 4 |
1.2. Физические и химические свойства…...................................................... | 6 |
ГЛАВА2. Технологическая часть...................................................... | 11 |
2.1.Описание химико-технологического процесса......................................... | 11 |
2.2. Описание технологической схемы............................................................ | 13 |
ЗАКЛЮЧЕНИЕ……………….………………………………………………. | 0 |
СПИСОК ИСПОЛЬЗОВАННЫХ ИСТОЧНИКОВ ………………………... | 0 |
ВВЕДЕНИЕ
Установка каталитического крекинга флюид (ККФ) в псевдоожиженном слое катализатора предназначена для получения высокооктанового компонента автомобильных бензинов за счет процесса каталитического крекинга тяжелого нефтяного сырья – смеси вакуумных газойлей (в том числе прямогонных и/или гидроочищенных).
Проектная мощность установки каталитического крекинга по вакуумному газойлю – сырью секции реактора-регенератора составляет:
· суточная ………………………………….. 3000 т/сут
· годовая ……………………………… 1095 тыс. т/год
Часовая производительность установки определена из расчета 8760 часов непрерывной работы в год.
|
|
Диапазон устойчивой работы установки составляет 60-120 % от расчетной производительности.
Межремонтный пробег для установки каталитического крекинга составляет 4 года, в том числе с ежегодной остановкой на техническое обслуживание на 14 суток.
Основными продуктами комбинированной установки каталитического крекинга в соответствии с базовым проектом являются:
· бензин каталитического крекинга (ККФ);
· пропан-пропиленовая фракция;
· бутан-бутиленовая фракция;
Цель: изучение производства высокооктанового компонента автомобильных бензинов, пропан-пропиленовой, бутан-бутиленовая фракции.
Для достижения поставленной цели были определены следующие задачи:
1. Рассмотреть физические и химические свойства получаемых продуктов;
2. Изучить стадии производства высокооктанового компонента автомобильных бензинов, пропан-пропиленовой, бутан-бутиленовой фракции и технологическую схему установка каталитического крекинга флюид (ККФ)
Глава 1. Высокооктановый компонент автомобильных бензинов , пропан-пропиленовая, бутан-бутиленовая фракция
1.1 Характеристика производимой продукции
Таблица 1.1 характеристикаготовой продукции
|
|
Наименование продукции | Национальный стандарт, технические условия, регламент или методика на подготовку сырья, стандарт организации | Показатели, обязательные для проверки | Регламентируемые показатели | Область применения |
Бензин каталитического крекинга ККФ | СТО05766575-N099 401.205-2016 | 1. Плотность при 15 °С, кг/м3 | Не нормируется, определение обязательно | Направляется на установку гидроочистки |
2. Октановое число по моторному методу | Не нормируется, определение обязательно | |||
3. Октановое число по исследовательскому методу | Не нормируется, определение обязательно | |||
4. Массовая доля серы, мг/кг, не более | 1740 | |||
5. Фракционный состав: Температура начала кипения, ˚С Температура конца кипения, ˚С, не выше | Не нормируется, определение обязательно 215 | |||
6. Массовая доля углеводородов, % 6.1 – ароматических - парафиновых - нафтеновых 6.2 – олефиновых, не более | Не нормируется, определение обязательно 30,0 |
Продолжение таблицы1.1
Фракция пропан-пропиленовая | СТО 05766575-N099 403.108-2016 | 1.Плотность при 15 °С, кг/м3 при 20 °С, кг | Не нормируется, определение обязательно | Направляется в парк | ||
2. Массовая доля компонентов - сумма углеводородов С1+С2 - сумма углеводородов С3, не менее - сумма углеводородов С4и выше | ГОСТ 10679-76 или МИ Т008/04.67-2013 Не нормируется, определение обязательно 98 Не нормируется, определение обязательно | |||||
3. Массовая доля суммы сероводорода и меркаптановой серы, %, не более | 0,0040 | |||||
4. Массовая доля воды, %, не более | 0,10 | |||||
Фракция бутан-бутиленовая
| СТО 05766575-N099 403.109-2016 | 1.Плотность при 15 °С, кг/м3 при 20 °С, кг | Не нормируется, определение обязательно | Направляется в парк | ||
2. Массовая доля компонентов - сумма углеводородов С1+С2 - сумма углеводородов С3, не менее - сумма углеводородов С4и выше | ГОСТ 10679-76 или МИ Т008/04.67-2013 Не нормируется, определение обязательно 95 Не нормируется, определение обязательно | |||||
3. Массовая доля суммы сероводорода и меркаптановой серы, %, не более | 0,0250 | |||||
4. Массовая доля воды, %, не более | 0,10 |
1.2 Физические и химические свойства
Бензин - топлива, выкипающие в интервале температур 28-215°С и предназначенные для применения в двигателях внутреннего сгорания с принудительным воспламенением.
В зависимости от назначения бензины разделяются на автомобильные и авиационные. [3]
|
|
Основными показателями бензина являются детонационная стойкость, давление насыщенных паров, фракционный состав, химическая стабильность и др. Ужесточение в последние годы экологических требований к качеству нефтяных топлив ограничило содержание в бензинах ароматических углеводородов и сернистых соединений. [1]
Детонационная стойкость
Детонация возникает в том случае, если скорость распространения пламени в двигателе достигает 1500-2500 м/с, вместо обычных 20- 30 м/с. В результате резкого перепада давления возникает детонационная волна, которая нарушает режим работы двигателя, что приводит к перерасходу топлива, уменьшению мощности, перегреву двигателя, к прогару поршней и выхлопных клапанов.
Октановое число - условный показатель, характеризующий стойкость бензинов к детонации и численно соответствующий детонационной стойкости модельной смеси изооктана и н-гептана.
Октановое число изооктана принято за 100 пунктов, а н-гептана - за 0. Для автомобильных бензинов (кроме А-76) октановое число измеряется двумя методами: моторным и исследовательским. Октановое число определяется на специальных установках путем сравнения характеристик горения испытуемого топлива и эталонных смесей изооктана с н-гептаном. Испытания проводят в двух режимах:
· жестком (частота вращения коленчатого вала 900 об/мин, температура всасываемой смеси 149°С, переменный угол опережения зажигания);
· мягком (600 об/мин, температура всасываемого воздуха 52°С, угол опережения зажигания 13 град.). [10]
Получают соответственно моторное (ОЧМ) и исследовательское октановые числа (ОЧИ). Разность между ОЧМ и ОЧИ называется чувствительностью и характеризует степень пригодности бензина к разным условиям работы двигателя. Считают, что ОЧИ лучше характеризует бензины при движении автомобиля в городских условиях, а ОЧМ - в условиях высоких нагрузок и скоростей при форсированном режиме работы двигателя. Среднее арифметическое между ОЧМ и ОЧИ называют октановым индексом и приравнивают к дорожному октановому числу, которое нормируется стандартами некоторых стран (например, США) и указывается на бензоколонках как характеристика продаваемого топлива. [15]
При производстве бензинов смешением фракций различных процессов важное значение имеют так называемые октановые числа смешения (ОЧС), которые отличаются от расчетных значений. Октановые числа смешения зависят от природы нефтепродукта, его содержания в смеси и ряда других факторов. У парафиновых углеводородов ОЧС выше действительных на 4 единицы, у ароматических зависимость более сложная. Различие может быть существенным и превышать 20 пунктов. Октановое число смешения важно также учитывать при добавлении в топливо оксигенатов. [9]
Фракционный состав
Фракционный состав бензинов характеризует испаряемость топлива, от которой зависит запуск двигателя, распределение топлива по цилиндрам двигателя, полнота сгорания, экономичность двигателя. Испаряемость определяется температурой перегонки 10, 50 и 90% (об.) выкипания фракций бензина.
§ Температура выкипания 10 % (об.) бензина характеризует пусковые свойства. При температуре ниже предельных значений в системе питания двигателя могут образовываться паровые пробки, а при более высоких температурах запуск двигателя затруднен. В США пусковые свойства бензина характеризуют количеством топлива, выкипающего до 70 °С.
§ Температура выкипания 50% (об.) бензина характеризует скорость перехода двигателя с одного режима работы на другой и равномерность распределения бензиновых фракций по цилиндрам.
§ Температура выкипания 90% (об.) фракций и конца кипения влияет на полноту сгорания топлива и его расход, а также на нагарообразование в камере сгорания в цилиндре двигателя.
В ГОСТ Р 51105-97, который действует с 01.01.99 г., фракционный состав бензина определяется при температуре выкипания 70, 100 и 180°С (по аналогии с требованиями к бензинам в США). [12]
Давление насыщенных паров
Давление насыщенных паров дает дополнительное представление об испаряемости бензина, а также о возможности образования газовых пробок в системе питания двигателя. Чем выше давление насыщенных паров бензина, тем выше его испаряемость.
Бензины, предназначенные для применения в летних условиях, имеют более низкое давление паров. Чтобы обеспечить необходимые пусковые свойства товарного бензина, в его состав включают, как правило, до 30% (об.) легких компонентов (фракция НК - 62°С, изомеризата, алкилата и др.). Требуемое давление насыщенных паров обеспечивается также добавлением бутана. В летних бензинах обычно содержится 2- 3% (об.) бутана, в зимних - до 5-8% (об.). [8]
Химическая стабильность
В процессе хранения, транспортирования и применения бензинов возможны изменения в их химическом составе, обусловленные реакциями окисления и полимеризации. Окисление приводит к понижению октанового числа бензина и повышению его склонности к нагарообразованию. Для оценки химической стабильности бензинов используют показатели содержания фактических смол, индукционного периода окисления. Высокой химической стабильностью обладают компоненты, не содержащие алкенов, - прямогонные бензины, бензины каталитического риформинга, алкилаты и изомеризаты. В бензинах коксования, термического и каталитического крекинга, напротив, содержатся в достаточном количестве алкены, которые легко окисляются с образованием смол. Для повышения химической стабильности к топливам, содержащим компоненты вторичного происхождения, добавляют антиокислительные присадки: n-оксидифениламин, ионол (2,6-ди-трет-бутил-n-крезол), антиокислитель ФЧ-16, древесносмоляной антиокислитель и др. [2]
Содержание сернистых и ароматических соединений
Активные сернистые соединения, содержащиеся в бензинах (сероводород, низшие меркаптаны) вызывают сильную коррозию топливной системы и транспортных емкостей; полнота очистки бензинов от этих веществ контролируется анализом на медной пластинке. Неактивные сернистые соединения (тиофены, тетрагидротиофены, сульфиды, дисульфиды, высшие меркаптаны) коррозии не вызывают, однако при их сгорании образуются оксиды серы (SO2, SO3), под действием которых происходит быстрый коррозионный износ деталей двигателя, снижается мощность, ухудшается экологическая обстановка. [6]
Наибольшую опасность для людей представляют ароматические углеводороды, особенно бензол и полициклические ароматические углеводороды. Токсическое действие бензола объясняется возможностью его окисления в организме. В связи с этим в последних нормативных документах ограничено допустимое содержание серы, бензола и ароматических соединений в бензинах.
Пропилен (пропен), C3H6 – органическое вещество класса алкенов. Пропилен имеет двойную углерод-углеродную связь и поэтому относится к ненасыщенным или непредельным углеводородам.
Пропилен – бесцветный газ, без вкуса, со слабым запахом. Пропилен – бесцветный газ, без вкуса, со слабым запахом.Пожаро- и взрывоопасен. Плохо растворяется в воде. Зато хорошо растворяется в углеводородах. Пропилен по токсикологической характеристике относится к веществам 4-го класса опасности (малоопасным веществам) по ГОСТ 12.1.007, но оказывает вредное воздействие на человека более сильным, чем этилен (этен). [7]
Цвет без цвета
Запах со слабым запахом
Вкус без вкуса
Агрегатное состояние (при 20 °C и атмосферном давлении 1 атм.) газ
Плотность (при 20 °C и атмосферном давлении 1 атм.), кг/м31,184
Плотность (при 0 °C и атмосферном давлении 1 атм.), кг/м31,9149
Температура плавления 185,25 °C
Температура кипения 47,6 °C
Температура вспышки 107,8°C
Температура самовоспламенения 410°C
Критическая температура 91,4°C
Критическое давление 4,6 МПа
Взрывоопасные концентрации смеси газа с воздухом, % объёмныхот 2,3 до 11,1
Удельная теплота сгорания, МДж/кг 45,694
Молярная масса, г/моль 42,08
Бута́н (C4H10) — органическое соединение, углеводород класса алканов. В химии название используется в основном для обозначения н-бутана. Такое же название имеет смесь н-бутана и его изомера изобутана CH(CH3)3. Название происходит от корня «бут-» (французское название масляной кислоты — acide butyrique, от древне греческого (βούτῡρον, масло) и суффикса «-ан» (принадлежность к алканам). Вдыхание бутана вызывает дисфункцию лёгочно-дыхательного аппарата. Содержится в природном газе, образуется при крекинге нефтепродуктов, при разделении попутного нефтяного газа, «жирного» природного газа. Как представитель углеводородных газов пожаро- и взрывоопасен, малотоксичен, имеет специфический характерный запах, обладает наркотическими свойствами. По степени воздействия на организм газ относится к веществам 4-го класса опасности (малоопасные) по ГОСТ 12.1.007-76. Вредно воздействует на нервную систему. [14]
Бутан — бесцветный горючий газ, со специфическим запахом, при нормальном давлении легко сжижаем от −0,5 °C, замерзает при −138 °C; при повышенном давлении и обычной температуре — легколетучая жидкость. Критическая температура +152 °C, критическое давление 3,797 МПа.
Растворимость в воде — 6,1 мг в 100 мл (для н-бутана, при 20 °C), значительно лучше растворяется в органических растворителях). Может образовывать азеотропную смесь с водой при температуре около 100 °C и давлении 10 атм. [11]
Плотность жидкой фазы — 580 кг/м³
Плотность газовой фазы при нормальных условиях — 2,703 кг/м³.
Теплота сгорания 45,8 МДж/кг (2657 кДж/моль
ГЛАВА2. Технологическая часть
2.1 Описание химико-технологического процесса
Основным процессом комплекса является каталитический крекинг – процесс каталитического деструктивного превращения тяжелых нефтяных фракций в более легкие, за счет контакта испарившегося сырья с циркулирующим твердым катализатором.
Процесс каталитического крекинга осуществляют в системах с непрерывно циркулирующим катализатором, который последовательно проходит через зоны каталитического крекинга сырья, десорбции адсорбированных углеводородов, окислительной регенерации. [3]
В данном комплексе используется процесс каталитического крекинга в псевдоожиженном слое циркулирующего микросферического катализатора.
Одним из важных преимуществ процесса каталитического крекинга в псевдоожиженном слое является способность катализатора легко перетекать между реактором и регенератором. В установках каталитического крекинга газовая фаза реактора представлена парами углеводородов и водяным паром, в регенераторе псевдоожижающей средой являются воздух и газы сгорания.
В условиях каталитического крекинга при температуре 490¸550 °С, и давлении 1¸3 кг/см2, на цеолитсодержащем катализаторе протекает большое число реакций, среди которых определяющее влияние на результаты процесса оказывают реакции разрыва углерод–углеродной связи, перераспределения водорода, ароматизации, изомеризации, разрыва и перегруппировки углеводородных колец, конденсации, полимеризации и коксообразования.
Скорость реакций крекинга и выход продуктов существенно меняются в зависимости от качества сырья, свойств катализатора, технологического режима, конструктивных особенностей реакционных аппаратов.
Результатом расщепления крупных молекул углеводородов на более мелкие в процессе каталитического крекинга является отложение на катализаторе нелетучего углеродного вещества – кокса. [1]
Коксообразование является одной из основных причин дезактивации катализатора. Для восстановления активности катализатора осуществляют выжиг кокса воздухом в регенераторе. Не являясь целевым продуктом крекинга, кокс, тем не менее, в определенных количествах необходим для поддержания теплового баланса в системе.
Целью регенерации является повторная активация отработанного катализатора. Регенератор служит для удаления (выжига) кокса с поверхности твердых частиц и для передачи тепла циркулирующему катализатору, так как его окисление в регенераторе протекает с выделением теплоты. Эта теплота компенсирует поглощение энергии в процессе крекинга.
Циркуляция катализатора характеризуется массовым соотношением расходов катализатора и сырья, подаваемых в реактор. Снижение кратности циркуляции катализатора приводит к увеличению содержания кокса на отработанном катализаторе, которое не должно превышать 1 % масс. При большом количестве кокса затрудняется регенерация катализатора и снижается ее эффективность. Повышение кратности циркуляции катализатора замедляет падение его активности и соответственно повышается конверсия сырья. Для сохранения выхода бензина и его октанового числа требуется постоянная, равномерная подпитка катализатора. [5]
Основным сырьем каталитического крекинга являются вакуумные дистилляты нефтей, имеющих конец кипения до 560 °С.
Важнейшими характеристиками сырья, влияющими на показатели каталитического крекинга, являются фракционный состав, групповой углеводородный состав, содержание смол и асфальтенов, сернистых и азотистых соединений, металлов, коксуемость.
Качество продуктов каталитического крекинга изменяется ввесьма широких пределах в зависимости от типа сырья, характеристик катализатора, технологического режима и т.д.
Продукты реактора каталитического крекинга представляют собой смесь углеводородных газов, паров легких, средних и тяжелых дистиллятов, сероводорода и водяного пара. Их разделение на отдельные фракции происходит в секции фракционирования.
Продукты регенератора – газы регенерации или дымовые газы содержат катализаторную пыль и соединения серы, образующиеся при сгорании отложившегося на катализаторе кокса, выводятся из регенератора и поступают в котел утилизатор.
Котел-утилизатор предназначен для получения пара высокого давления за счет тепла горячих газов регенерации.
Для снижения выбросов окислов азота в атмосферу в котле-утилизаторе предусмотрен блок DeNOx.
Горячие дымовые газы после котла-утилизатора, содержащие сернистые газы и катализаторную пыль проходят очистку в электрофильтре и выбрасываются в дымовую трубу. [3]
2.2. Описание технологической схемы
После нагрева фракции вакуумного газойля в сырьевых теплообменниках, сырье из секции 1200 подается в реактор Р-1101, либо, при пуске и остановке установки, а также при аварии, направляется по пусковому байпасу реактора в линию подачи сырья к емкости смешения Е-1201. Переключение направления потока осуществляется при помощи сблокированных клапанов-отсекателей UV11102 и UV11107.
Фракция вакуумного газойля подается в реактор Р-1101 через кольцевой коллектор, откуда поступает в шесть специальных устройств ввода, в которых смешивается с распыляющим водяным паром среднего давления.
Расход распыляющего пара регулируется контуром FIRCA11010 с помощью регулирующего клапана FV11010, установленного на линии подачи пара в реактор. Предусмотрена сигнализация минимального и максимального расхода пара. [3]
В пусковом режиме поток пара среднего давления подается в реактор по линии байпаса регулирующего клапана FV11010.
Расход фракции вакуумного газойля в каждое из шести устройств ввода замеряется приборами FIRA11103, FIRA11104, FIRA11105, FIRA11106, FIRA11107, FIRA11108. Предусмотрена сигнализация минимального расхода фракции вакуумного газойляпри значении 13 м3/ч.
Кроме того, предусмотрена отдельная сигнализация XA11509, которая срабатывает, если расход подачи сырья на любой штуцер реактора отклоняется более чем на 30% от своего среднего значения.
Давление в каждом из шести устройств ввода сырья контролируется приборами PIR11515, PIR11516, PIR11517, PIR11518, PIR11519, PIR11520.
Расход распыляющего пара в каждое из шести устройств ввода замеряется приборами FIRA11109, FIRA11110, FIRA11111, FIRA11112, FIRA11113, FIRA11114. Предусмотрена сигнализация минимального расхода пара при значении 0,17 т/ч. [15]
Давление в каждом из шести устройств ввода пара контролируется приборами PIR11521, PIR11522, PIR11523, PIR11524, PIR11525, PIR11526.
Предусмотрена подача дополнительного количества пара враспределитель сырьяреактора по трубопроводу 50 MS-1111-CB7, на котором установлен через клапан-отсекательUV11106, управляемый по сигналам системы ПАЗ UC11100. Для ограничения расхода и плавного ввода пара в каждую из шести линий подачи сырья, на линиях подачи пара установлены дроссельные шайбы.
Температура в зоне ввода сырья замеряется приборами TIRA11524 и TIRA11525. Предусмотрена сигнализация минимального значения температуры.
Кроме того, в нижней части подъемной камеры реактора Р-1101 предусмотрено устройство ввода бензина висбрекинга.
Подача бензинависбрекинга осуществляется по трубопроводу 50 P11-1102-NE5, на котором установлен клапан-отсекатель UV11101,управляемый по сигналам системы ПАЗ UC11100. Расход поступающейбензина с установки висбрекинга контролируется прибором FQIRA11115 с функцией расходомера материального баланса. Предусмотрена сигнализация минимального расхода бензина висбрекинга. [6]
Давление бензина висбрекинга на входе в реактор контролируется прибором PIR11575.
Для равномерного распределения в устройство ввода бензина висбрекинга предусмотрена подача пара среднего давления. Подача пара среднего давления регулируется контуром FIRCA11009 при помощи клапана FV11009, установленного на линии подачи пара в распределительное устройство. Предусмотрена сигнализация минимального расхода пара.
Устройство ввода бензина висбрекинга может использоваться для подачи в нижнюю часть лифт-реактора до 3000 т/сутки вакуумного газойля. Для этого предусмотрен трубопровод 50 P01-1115-NE5 соединяющий линию ввода сырья и бензина висбрекинга в реактор. [1]
В нижней части лифт-реактора предусмотрена резервная линия аварийной подачи пара среднего давления, которая объединена с линией подачи воздуха, использующейся для разогрева аппарата во время пуска.На линии подачи пара среднего давления установлен клапан-отсекательUV11105, управляемый по сигналам системы ПАЗ UC11100. Через две минуты после полного открытия клапана UV11105выходной сигнал контура регулирования HIC11510 устанавливается на 50 % и далее происходит возврат клапана-отсекателя UV11105 в исходное положение.
Действия системы ПАЗ UC11100 указаны в разделе …. настоящего Регламента.
Расход аварийной подачи пара среднего давления контролируется прибором FIRA11116. Предусмотрена сигнализация минимального расхода пара.
При обнаружении в процессе эксплуатации установки высоких потерь катализатора из реактора, вводят в работу гидроциклон кубового продукта Ф-1201. Тяжелый остаток с частицами катализатора направляется обратно в реактор Р-1101, ввод которого расположен выше ввода основного сырья (фракции вакуумного газойля). На лини возврата тяжелого остатка в реактор установлен клапан-отсекатель UV11103, управляемый по сигналам системы ПАЗ UC11100.Предусмотрена подача распыляющего водяного пара среднего давления в устройство ввода тяжелого остатка в реактор. [3]
Между вводами тяжелого остатка главной фракционирующей колонны и сырья каталитического крекинга предусмотрена линия подачи котловой воды. На линии подачи воды установлен пневматический клапан-отсекательUV11100, управляемый по сигналам системы ПАЗ UC11100. Расход воды регулируется контуром FIRC11012 с помощь регулирующего клапана FV11012, установленного на линии подачи котловой воды в реактор.
Кроме того, предусмотрена подача пара среднего давления в трубопровод котловой воды перед реактором Р-1101.
При контакте сырья с регенерированным катализатором, сырье быстро испаряется, и смесь катализатора и паров движется восходящим потоком в лифт-реакторе, где происходит процесс крекинга. Пары сырья уносят катализатор вверх по лифт-реактору и далее направляются для отделения от катализатора в первичный циклон грубого отделения Ф-1101. После прохождения через циклон Ф-1101 пары продуктов реакций каталитического крекинга объединяются с водяным паром и потоком паров продуктов из секции отпарки катализатора и направляются для извлечения унесенного катализатора во вторичные циклоны Ф-1102/А-С, а отделенный катализатор ссыпается в стриппинг реактора Р-1102. [12]
Пары продуктов крекинга после прохождения через вторичные циклоны Ф-1102/А-С направляются в главную фракционирующую колонну К-1201. На линии выхода газов реакции предусмотрен контроль температуры при помощи прибора TIR11535, сигнал от которого поступает на переключатель HS11504.
Перепад давления между линией подачи газов реакции в секцию фракционирования и стриппингом реактора Р-1102 контролируется прибором PDIR11590. Предусмотрена продувка импульсной линии топливным газом или, при пуске, азотом высокого давления (специальный узел типа "DG").
Перепад давления между линией подачи газов реакции в секцию фракционирования и главной фракционирующей колонной К-1201 контролируется прибором PDIR11591.
Для снижения уровня шума при пуске реактора Р-1101 на трубопроводе вывода газов реакции из стриппинга реактора Р-1102устанавлен глушитель З-1116. [10]
ЗАКЛЮЧЕНИЕ
Целевым назначением процесса каталитического крекинга является получение высококачественного бензина с октановым числом (в чистом виде) 90-92 по исследовательскому методу. При каталитическом крекинге образуется значительное количество газа, богатого бутан-бутиленовой фракцией (сырье для производства высокооктанового компонента бензина - алкилата). Установки каталитического крекинга являются также поставщиком сырья для химической промышленности: из газойлей каталитического крекинга получают сажевое сырье и нафталин; тяжелый газойль может служить сырьем для производства высококачественного игольчатого кокса.
Дата добавления: 2021-12-10; просмотров: 110; Мы поможем в написании вашей работы! |
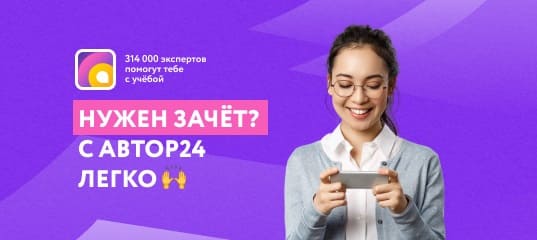
Мы поможем в написании ваших работ!