Химико-термическая обработка стали
Существуют различные способы воздействия на сталь с целью придания ей требуемых свойств. Один из комбинированных методов — химико-термическая обработка стали.
Общие принципы
Суть данной технологии состоит в преобразовании внешнего слоя материала насыщением. Химико-термическая обработка металлов и сплавов осуществляется путем выдерживания при нагреве обрабатываемых материалов в средах конкретного состава различного фазового состояния. То есть, это совмещение пластической деформации и температурного воздействия.
Это ведет к изменению параметров стали, в чем состоит цель химико-термической обработки. Таким образом, назначение данной технологии — улучшение твердости, износостойкости, коррозионной устойчивости. В сравнении с прочими технологиями химико-термическая обработка выгодно отличается тем, что при значительном росте прочности пластичность снижается не так сильно.
Основные ее параметры — температура и длительность выдержки.
Рассматриваемый процесс включает три этапа:
Интенсивность диффузии увеличивается в случае формирования растворов внедрения и снижается, если вместо них формируются растворы замещения.
Количество насыщающего элемента определяется притоком его атомов и скоростью диффузии.
На размер диффузионного слоя влияют температура и длительность выдержки. Данные параметры связаны прямой зависимостью. То есть с ростом концентрации насыщающего элемента возрастает толщина слоя, а повышение интенсивности теплового воздействия приводит к ускорению диффузии, следовательно, за тот же промежуток времени она распространится на большую глубину.
|
|
Большое значение для протекания процесса диффузии имеет растворимость в материале обрабатываемой детали насыщающего элемента. В данном случае играют роль пограничные слои. Это объясняется тем, что ввиду наличия у границ зерен множества кристаллических дефектов диффузия происходит более интенсивно. Особенно это проявляется в случае малой растворимости насыщающего элемента в материале. При хорошей растворимости это менее заметно. Кроме того, диффузия ускоряется при фазовых превращениях.
Классификация
Химико-термическая обработка стали подразделяется на основе фазового состояния среды насыщения на жидкую, твердую, газовую.
В первом случае диффузия происходит на фрагментах контакта поверхности предмета со средой. Ввиду низкой эффективности данный способ мало распространен. Твердую фазу обычно используют с целью создания жидких или газовых сред.
Химико-термическая операция в жидкости предполагает помещение предмета в расплав соли либо металла.
|
|
При газовом методе элемент насыщения формируют реакции диссоциации, диспропорционирования, обмена, восстановления. Наиболее часто в промышленности для создания газовой и активной газовой сред используют нагрев твердых. Удобнее всего проводить работы в чисто газовой среде ввиду быстрого прогрева, легкого регулирования состава, отсутствия необходимости повторного нагрева, возможности автоматизации и механизации.
Как видно, классификация по фазе среды не всегда отражает сущность процесса, поэтому была создана классификация на основе фазы источника насыщения. В соответствии с ней химико-термическая обработка стали подразделена на насыщение из твердой, паровой, жидкой, газовой сред.
Кроме того, химико-термическая технология подразделена по типу изменения состава стали на насыщение неметаллами, металлами, удаление элементов.
По температурному режиму ее классифицируют на высоко- и низкотемпературную. Во втором случае производят нагрев до аустенитного состояния, а в первом — выше и оканчивают отпуском.
Наконец, химико-термическая обработка деталей включает следующие методы, выделяемые на основе технологии выполнения: цементацию, азотирование, металлизацию, нитроцементацию.
|
|
Диффузионная металлизация
Это поверхностное насыщение стали металлами.
Возможно проведение в жидкой, твердой, газовой средах. Твердый метод предполагает использование порошков из ферросплавов. Жидкой средой служит расплав металла (алюминий, цинк и т. д.). Газовый метод предполагает использование хлористых металлических соединений.
Металлизация дает тонкий слой. Это объясняется малой интенсивностью диффузии металлов в сравнении с азотом и углеродом, так как вместо растворов внедрения они формируют растворы замещения.
Такая химико-термическая операция производится при 900 — 1200°С. Это дорогостоящий и длительный процесс.
Основное положительное качество — жаростойкость продуктов. Ввиду этого металлизацию применяют для производства предметов для эксплуатационных температур 1000 — 1200°С из углеродистых сталей.
По насыщающим элементам металлизацию подразделяют на алитирование (алюминием), хромирование, борирование, сицилирование (кремнием).
Первая химико-термическая технология придает материалу стойкость к окалине коррозии, однако на поверхности после нее остается алюминий. Алитирование возможно в порошковых смесях либо в расплаве при меньшей температуре. Второй способ быстрее, дешевле и проще.
|
|
Хромирование тоже увеличивает стойкость к коррозии и окалине, а также к воздействию кислот и т. д. У высоко- и среднеуглеродистых сталей оно также улучшает износостойкость и твердость. Данная химико-термическая операция в основном производится в порошковых смесях, иногда в вакууме.
Основное назначение борирования состоит в улучшении стойкости к абразивному износу. Распространена электролизная технология с применением расплавов боросодержащих солей. Существует и безэлектролизный метод, предполагающий использование хлористых солей с ферробором или карбидом бора.
Сицилирование увеличивает стойкость к коррозии в соленой воде и кислотах, к износу и окалине некоторых металлов.
Науглероживание (цементация)
Это насыщение поверхности стальных предметов углеродом. Данная операция улучшает твердость, износостойкость, а также выносливость поверхности материала. Нижележащие слои остаются вязкими.
Данная химико-термическая технология подходит для предметов из низкоуглеродистых сталей (0,25%), подверженных контактному износу и переменным нагрузкам.
Предварительно необходима механическая обработка. Не цементируемые участки покрывают слоем меди либо обмазками.
Температурный режим определяется содержанием углерода в стали. Чем оно ниже, тем больше температура. Для адсорбирования углерода и диффузии в любом случае она должна составлять 900 — 950°С и выше.
Таким образом, путем насыщения поверхности стальных деталей углеродом достигают концентрации данного элемента в верхнем слое 0,8 — 1%. Большие значения ведут к повышению хрупкости.
Цементацию осуществляют в среде, называемой карбюризатором. На основе ее фазы технологию подразделяют на газовую, вакуумную, пастами, в твердой среде, ионную.
При первом способе применяют каменноугольный полукокс, древесный уголь, торфяной кокс. С целью ускорения используют активизаторы и повышают температуру. По завершении материал нормализуют. Ввиду длительности и малой производительности данная химико-термическая технология используется в мелкосерийном выпуске.
Вторая технология предполагает использование суспензий, обмазок либо шликеров.
Газовую среду наиболее часто применяют при цементации ввиду скорости, простоты, возможности автоматизации, механизации и достижения конкретной концентрации углерода. В таком случае используют метан, бензол или керосин.
Более совершенный способ — вакуумная цементация. Это двухступенчатый процесс при пониженном давлении. От прочих методов отличается скоростью, равномерностью и светлой поверхностью слоя, отсутствием внутреннего окисления, лучшими условиями производства, мобильностью оборудования.
Ионный метод подразумевает катодное распыление.
Цементация — промежуточная химико-термическая операция. Далее осуществляют закалку и отпуск, определяющие свойства материала, такие как износостойкость, выносливость при контакте и изгибе, твердость. Главный недостаток — длительность.
Азотирование
Данным термином называют насыщение материала азотом. Этот процесс производят в аммиаке при 480 — 650°С.
С легирующими данный элемент формирует нитриды, характеризующиеся дисперсностью, температурной устойчивостью и твердостью.
Такая технология химико-термической обработки увеличивает твердость, стойкость к коррозии и износу.
Необходима предварительная механическая и термическая обработка для придания окончательных размеров. Не азотируемые фрагменты покрывают оловом либо жидким стеклом.
Обычно используют температурный интервал от 500 до 520°С. Это дает за 24 — 90 ч. 0,5 мм слой. Толщина определяется длительностью, составом материала, температурой.
Азотирование приводит к увеличению обрабатываемых деталей вследствие возрастания объема верхнего слоя. Величина роста напрямую определяется его толщиной и температурным режимом.
При жидком способе применяют цианосодержащие, реже бесцианитные и нейтральные соли. Ионная химико-термическая операция отличается повышенной скоростью.
Азотирование подразделяют по целевым свойствам: им достигается или улучшение устойчивости к коррозии, либо повышение стойкости к износу и твердости.
Дата добавления: 2021-12-10; просмотров: 26; Мы поможем в написании вашей работы! |
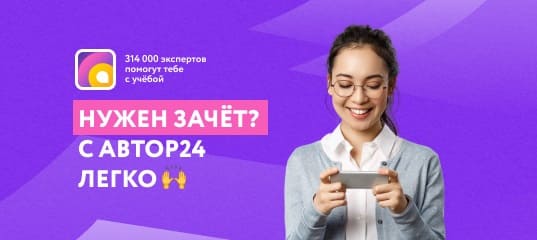
Мы поможем в написании ваших работ!