Аттестационный лист по практике
ЗАДАНИЕ№19
на преддипломную практику
Специальность18.02.09 Переработка нефти и газа
студенту | Шленцовой Валентины Валерьевны | |
(фамилия, имя, отчество) | ||
группы | ЗН-417 | |
| ||
Тема: | Подбор методик по определению внешней удельной поверхности различных марок технического углерода.
|
СОДЕРЖАНИЕ ЗАДАНИЯ
Введение (востребованность продукта на рынке, направления улучшения эксплуатационных или экологических показателей, цель прохождения практики)
Технологическая часть
1.1 Описание базы практики
1.2 Теоретические основы получения продукта. Область применения
1.3 Характеристика качества сырья и готовой продукции
1.4 Технология получения продукта. Нормы технологического режима
1.5 Автоматизация технологического процесса
1.6 Техника безопасности в лаборатории
Графическая часть
1 лист | Технологическая схема получения технического углерода |
2 лист | (технологическая схема, блок-схема) Физико-химические свойства технического углерода П-245, N-550 |
3 лист | (график зависимости) |
(диаграмма)
|
|
Председатель ПЦК | Светикова С.В |
Руководитель практики | Тимохина К.В |
Дата выдачи задания | |
Сроки практики | 23.03.2021 – 19.04.2021 |
МИНИСТЕРСТВО НАУКИ И ВЫСШЕГО ОБРАЗОВАНИЯ РОССИЙСКОЙ ФЕДЕРАЦИИ СИБИРСКИЙ КАЗАЧИЙ ИНСТИТУТ ТЕХНОЛОГИЙ И УПРАВЛЕНИЯ (ФИЛИАЛ)
ФЕДЕРАЛЬНОГО ГОСУДАРСТВЕННОГО БЮДЖЕТНОГО ОБРАЗОВАТЕЛЬНОГО
УЧРЕЖДЕНИЯ ВЫСШЕГО ОБРАЗОВАНИЯ
«МОСКОВСКИЙ ГОСУДАРСТВЕННЫЙ УНИВЕРСИТЕТ ТЕХНОЛОГИЙ И
УПРАВЛЕНИЯ ИМЕНИ К.Г. РАЗУМОВСКОГО (ПЕРВЫЙ КАЗАЧИЙ УНИВЕРСИТЕТ)»
(СКИТУ (филиал) ФГБОУ ВО «МГУТУ им. К. Г. Разумовского (ПКУ)»)
О Т Ч Е Т
По преддипломной практике
Фамилия Шленцова
Имя, отчество Валентина Валерьевна
Курс _____4___ Группа____ЗН-417__________
Специальность 18.02.09 Переработка нефти и газа
Тимохина Ксения Владимировна
Руководитель от базы практики ___________________________________________________
Ф.и.о., должность)
М.П.
Омск 2021 г.
![]() |
СОДЕРЖАНИЕ |
ВВЕДЕНИЕ | 4 | |
1 | Технологическая часть | 6 |
1.1 | Описание базы практики | 6 |
1.2 1.3 | Теоретические основы получения продукта. Область применения. Характеристика качества сырья и готовой продукции. Применение готовой продукции. | 7 11 |
1.4 | Технология получения технического углерода. Нормы технологического режима. | 15 |
1.5 | Автоматизация технологического процесса | 17 |
1.6 | Техника безопасности в лаборатории | 21 |
|
|
ВЫВОДЫ 29
СПИСОК ИСТОЧНИКОВ 30
ВВЕДЕНИЕ
ООО «Омсктехуглерод» занимает одно из ведущих мест среди
предприятий Омска и Омской области. Он производит наибольшее количество марок технического углерода среди отечественных заводов и имеет качество продукции на уровне лучших зарубежных фирм.
На заводе внедрена комплексная система управления качеством
продукции.
Подтверждением высокого качества продукции ООО "Омский завод
технического углерода" является сертификат соответствия системы
менеджмента требованиям стандарта ГОСТ ISO/IEC 17025-2019 Общие требования к компетентности испытательных калибровочных лабораторий.
Стандартами ASTM определены важные целевые значения
характеристик техуглерода, таких как абсорбция дибутилфталата, удельная
внешняя поверхность, исследование экстрагируемых веществ, массовая доля
пыли и др., которые служат для контроля процесса производства. С помощью индекса пригодности Рр производится оценка процесса получения
техуглерода.
На предприятии проводится статистический анализ измерительных
систем контроля показателей качества техуглерода в процессе производства и в готовой продукции в соответствии с требованиями методики MSA.
На начальном этапе развития промышленности техуглерода было
замечено, что о полноте реакции образования частиц продукта можно судить
по насыщенности цвета растворителя после экстрагирования веществ,
содержащихся в образце.
Как и любой полидисперсный материал, техуглерод характеризуют по его удельной поверхности, которая геометрически связана с размером частиц. Чем меньше размер частиц, тем выше его удельная поверхность. Для практических целей удельную площадь поверхности определяют по объему
|
|
|
|
или массе молекул различных газов или поверхностно-активных веществ, адсорбируемых на поверхности одного грамма техуглерода. Чем больше того или иного вещества адсорбирует техуглерод, тем выше его удельная поверхность и соответственно меньше размер частиц.
Приоритетными направлениями в области качества являются:
1. Выпуск продукции в соответствии со спецификациями зарубежных потребителей и отечественными стандартами.
2. Внедрение новых технологических процессов для расширения ассортимента технического углерода.
3. Освоение специальных марок технического углерода для лакокрасочной, полиграфической, электротехнической промышленностей.
4. Улучшение транспортных свойств технического углерода.
5. Поиск новых установочных материалов
Достижение целей в области качества обеспечиваются следующим образом:
1. Обеспечение точности ведения технологического процесса.
2. Обеспечение стабильности сырьевых смесей.
3. Повышение уровня автоматизации процесса.
Требования к качеству продукции предъявляются в соответствии с ГОСТ ISO/IEC 17025-2019
Контроль качества готовой продукции и поступающего сырья осуществляет лаборатория контроля и качества, в состав которой входит 4 сектора:
· сектор испытания техуглерода в резине;
· аналитический сектор;
· санитарно-промышленная лаборатория;
· сектор технического контроля.
1. Технологическая часть
1.1 Описание базы практики
1.1 Описание базы практики
Одним из видов нефтехимической переработки является производство теического углерода из продуктов нефти. В настоящее время изготовление технического углерода является востребованным, так как данная продукция в дальнейшем используется, как усиливающий компонент в производстве резин и пластических масс. Остальное количество находит применение в качестве черного пигмента; замедлителя «старения» пластмасс; компонента, придающего пластмассам специальные свойства: (электропроводные, антистатические, способность поглощать ультрафиолетовое излучение, излучение радаров).
В городе Омске производством технического углерода в промышленных масштабах занимается предприятия ООО «Омсктехуглерод» - крупнейшее по мощности предприятие отрасли в России. Производство крупнотоннажное, автоматизированное, непрерывного действия, модульного типа. Производственная мощность превышает 220 тысяч тонн технического углерода в год, что делает завод самым крупным в мире. Технический углерод получают в реакторе в результате термоокислительного пиролиза углеводородов.
Благодаря высокому и стабильному качеству продукта предприятие успешно конкурирует как с отечественными, так и с зарубежными производителями. 35% продукции крупными партиями поставляется в Германию, Италию, Францию, Венгрию, Турцию, Польшу, США, Канаду. Номенклатура и ассортимент выпускаемой продукции постоянно обновляется.
Предприятие состоит из трех основных цехов по производству технического углерода, вспомогательных цехов, лаборатории контроля качества, котельные, ТЭЦ, железнодорожные магистрали.
1.2 Теоретические основы получения продукта. Область применения
Технический углерод – сыпучее вещество чёрного цвета, продукт неполного сгорания или термического разложения углеводородного сырья.
Промышленные способы получения технического углерода основаны на разложении углеводородного сырья под действием высокой температуры. Образование технического углерода в одних случаях происходит в пламени горения сырья при ограниченном доступе воздуха. Некоторые виды технического углерода получают, извлекая его из продуктов синтеза различных углеводородов (синтез ацетилена из метана).
Процесс получения техуглерода принято обозначать рядом терминов – процесс неполного сгорания углеводородов, процесс термоокислительного крекинга углеводородов, процесс термоокислительного пиролиза углеводородов. Наибольшеераспространение получило последнее определение. Под всеми этими терминами понимается процесс сжигания углеводородов в контролируемых условиях при недостатке окислителя (воздуха). При этом часть сырья сгорает, а выделившееся в процессе горения тепло расходуется на разложение оставшегося сырья.
Реакция термического разложения углеводородов может быть выражена уравнением: CnHm↔nC+m/2H2 , углерод при этом выделяется виде твердой фазы.
Печной способ получения технического углерода характеризуется проведением реакции термоокислительного пиролиза (разложения) в строго контролируемых условиях в специальных реакторах. Этот способ получил название печной потому, что первые реактора имели большие размеры, большой объем огнеупорной футеровки и больше походили на металлургические печи.
В общепринятом понятии реактором называется герметичный аппарат, предназначенный для проведения химических реакций. Реактор имеет полностью закрытый газонепроницаемый металлический корпус. Герметичность корпуса – основное условие, обеспечивающее направленное регулирование всех потоков (сырья, газа, воздуха, воды). Так как процессы получения печного техуглерода осуществляются при высоких температурах, реактор футеруется огнеупорами, выдерживающими температуру до 1900оС.
Реактор имеет три зоны:
- зона горения,
- зона реакции,
- зона закалки.
В зоне горения сжигается природный газ и часть сырья, выделяется тепло для разложения углеводородного сырья, в зоне реакции происходит непосредственно сама реакция, и в зоне закалки прекращается реакция пиролиза за счет подачи туда воды, которая охлаждает углеродогазовую смесь.
Реактора подразделяются: по исполнению на вертикальные и горизонтальные, по производительности по сырью на РС 50/5000, РС 105/3500. В зависимости от активности выпускаемого техуглерода реактора имеют различные конструкции, также отличаются размерами камер, схемы подачи сырья, у реакторов для получения активных марок также имеется камера предзакалки. В реакторах соблюдается различный температурный режим, так у реакторов для активных марок температура в камере горения достигает 1700-1900 оС, для малоактивных 1300-1600 оС.
Основным параметром, влияющим на выход техуглерода из сырья, является температура в зоне горения реактора. Чем выше температура газов в зоне горения, тем меньше требуется дополнительного тепла на проведение пиролиза сырья. Поэтому для уменьшения потерь тепла в окружающую среду применяют футеровку.
В качестве футеровки применяют:
§ огнеупорный кирпич;
§ шамот;
§ корунд;
§ мулитокорунд.
Толщина футеровки должна быть такой, чтобы температура корпуса была не более 90 оС. Сырье вводят в реактор в виде капель, образованных при распылении его форсунками пневматического действия.
В реакторе происходит одновременно несколько различных процессов:
- сгорание вспомогательного горючего или части сырья для получения тепла, необходимого для термического разложения углеводородов;
- испарение капель сырья;
- частичное неполное сгорание сырья с образованием вследствие недостатка кислорода окиси углеводорода и паров воды;
- термическое разложение углеводородов сырья с получением сажи и формированием сажевых частиц;
- взаимодействие между полученной сажей и газообразными продуктами процесса.
В мире разработано множество марок технического углерода. Чтобы различить или унифицировать предлагаемые на рынке типы технического углерода их подразделяют по следующим первичным признакам:
§ по виду процесса (печной, диффузионный, термический);
§ по виду сырья (жидкое или газовое);
§ по свойствам.
Удельная внешняя поверхность – это адсорбция ЦТАБ (цетилтриметиламмоний бромид), м2/г. Это объясняется тем, что молекулы ЦТАБ имеют большие размеры и не проникают в поры частиц, а с кислородосодержащими группами, находящимися на поверхности техуглерода, не вступают в реакцию. Принято считать, что метод ЦТАБ с достаточной точностью характеризует поверхность техуглерода доступную для молекул каучука.
Йодное число – зависит от поверхности техуглерода, функциональных групп и пористости. Более пористый техуглерод поглощает больше йода. Не разложившиеся углеводороды на поверхности техуглерода понижают йодное число, г/кг.
Структурность – абсорбция дибутилфталата образца внутри частицы технического углерода, см3/100г. Для характеристики степени разветвленности агрегатов техуглерода используют термин «структурность». Чем больше частиц в агрегате и чем больше степень их разветвления, тем выше структурность техуглерода. Структурность оценивают по объему пустот в агрегатах. Для этого используют абсорбенты — дибутилфталат (ДБФ) или парафиновое масло, которые заполняют пустоты в разветвлениях агрегатов. Чем больше техуглерод абсорбирует масла или дибутилфталата, тем выше структурность техуглерода.
Область применения технического углерода в зависит от его марки: N550 применяется для изготовления корпуса и камеры шин, резинотехнических изделий, уплотнителей, шлангов; N220 входит в состав особо ответственной, протекторной резины при производстве шин для грузовых и легковых автомобилей, рекомендуется для использования при производстве конвейерных лент и других резинотехнических изделий (где требуется повышенная износостойкость), N339 применяется для изготовления протекторов шин, резинотехнических изделий, конвейерных лент.
1.3 Характеристика качества сырья и готовой продукции. Применение готовой продукции.
Для производства технического углерода используются жидкое сырье – нефтяное и коксохимическое.
Желательными компонентами сырья является ароматические углеводороды.
Чаще всего используются виды нефтяного сырья такие, как тяжелый каталитический газойль, термический газойль, экстракты масляного производства и тяжелые смолы пиролиза.
К разновидностям коксохимического сырья относят антраценовые фракции и антраценовое масло. Каменноугольные фракции в отличие от нефтяных характеризуются высоким содержанием ароматических углеводородов без боковых цепей. На производстве для характеристики ароматизированости сырья используют величину как индекс корреляции.
Индекс корреляции зависит от плотности вещества и его показателя преломления.
Содержание серы в сырье нормируется при производстве. Сера распределяется между техническим углеродом и отходящим газом. До 40% серы переходит в технический углерод в химически связанном состоянии, а часть серы содержится в отходящих газах.
Асфальтосмолистые вещества неблагоприятно влияют на качество технического углерода, они с трудом испаряются и являются причиной образования кокса в реакторе. Наличие асфальтосмолистых веществ характеризуют величиной - коксуемость, измеряемой в процентах (%). Лучшие марки сырья имеют коксуемость в пределах 2%.
Содержание механических примесей в сырье так же не должно превышать нормы. Они представляют собой частицы кокса, песка, катализаторной пыли. Механические примеси удаляют методом фильтрования, так как они загрязняют сырье. Содержание их в сырье строго нормируется.
Технический углерод малодисперсный и полидисперсный продукт. Форма частиц близка к сферической. Частицы технического углерода способны срастаться в агрегаты. По химическим свойствам технический углерод не растворим в воде, не взаимодействует с кислотами и щелочами. Устойчив к воздействию высоких температур. Основными показателями качества технического углерода являются: удельная внешняя поверхность, адсорбционная удельная поверхность, зольность.
Основным потребителем технического углерода является шинная промышленность. При добавлении технический углерода в резиновую смесь, значительно возрастает механическая прочность сопротивления разрыву, поэтому технический углерод называют усилителем резиновых смесей. Усиливающее свойство будет зависеть главным образом от дисперсности.технический углерод добавляют в дорожный битум, так как он смягчает действие солнечного света. Также технический углерод используют в полиграфии, лакокрасках.
Путем обработки технического углерода получают углеродный материал, который имеет более упорядоченное строение и используется как носитель катализатора, гемосорбент, а также технический углерод используется для очистки питьевой воды от железа.
В основном техуглерод является важнейшим компонентом резины. Для производства резиновых технических изделий применяют технический углерод, обладающий высокой износостойкостью, стойкостью к агрессивным средам.
Постоянно растущие требования к качеству изделий из резины обуславливают необходимость повышения качества сырья, в том числе и технического углерода. Усиливающее действие технического углерода возрастают с увеличением дисперсности и структурности.
В РФ применяются две классификации технического углерода по ГОСТ 7885 86 и стандарту американского общества испытания материалов ASTM D1765. В соответствии с классификацией по ГОСТ установлены 10 марок технического
углерода. В зависимости от способа получения (печной, канальный, термичес-
ский) маркам присвоены буквенные индексы «П», «К», «Т». Следующий за буквенным цифровой индекс характеризует средний размер частиц техуглерода в целых десятках нанометров. Два последних цифровых индекса выбирались при утверждении марки. В основе классификации по стандарту ASTM D1765 лежит способность некоторых марок техуглерода изменять скорость вулканизации резиновых смесей. В зависимости от чего маркам присвоены буквенные индексы «N» (с нормальной скоростью вулканизации) и «S» (с замедленной скоростью вулканизации, от англ. «slow» — медленный). Следующий за буквенным цифровой индекс — номер группы марок по средней удельной поверхности. Два последних цифровых индекса выбирались при утверждении марки. Стандартом описаны (по состоянию на 2006 год) 43 марки техуглерода, из которых индекс «S» имеют 2.
Таблица 1.2-Характеристика сырья, готовой продукции
Наименование | ГОСТ, ТУ, СТП, ASTM | Показатели по ГОСТ, ТУ, СТП | Допустимые пределы |
Газойль каталитический | ТУ 38.301-19-87-97 | Плотность пpи 15°С, г/см3, не менее | 1,013 |
Вязкость кинематическая пpи 50°С, мм2/с, не более | 50,0 | ||
Коксуемость, %, не более | 9,0 | ||
Массовая доля воды, %, не более | 0,2 | ||
Индекс коppеляции, не менее | 102,0 | ||
Смола пиролизная тяжелая | ТУ 38.1021256-89 | Плотность пpи 20°С, г/см3, не менее | 1,04 |
Вязкость кинематическая пpи 50°С, мм2/с, не более | 25,0 | ||
Коксуемость, %, не более | 12,0 | ||
Массовая доля воды, %, не более | 0,3 | ||
Массовая доля механических примесей, %, не более | 0,01 | ||
Индекс коppеляции, не менее | 125,0 | ||
Массовая доля иона натрия, %, не более | 0,005 | ||
Массовая доля иона калия, %, не более | 0,0005 | ||
Темпеpатуpа отгона 3 % объема, °С, не ниже | 180.0 |
Продолжение таблицы 1.2
Наименование | ГОСТ, ТУ, СТП, ASTM | Показатели по ГОСТ, ТУ, СТП | Допустимые пределы |
Антраценовая фракция | ГОСТ111-26-88 | Плотность при 200С,кг/см3 не менее | 1120 |
Коксуемость ,% не более | 2,0 | ||
Массовая доля воды ,% не более | 1,0 | ||
Технический углерод марки N330 | ASTM | Удельная внешняя поверхность, м2/г | 78 |
Йодное число, г/кг | 121±5 | ||
Вода предочищенная |
СТП 015016-94 | Эквивалентная жесткость, мг/л, не более | 7,5-9,5 |
Механические примеси, мг/л не более | 10,0 | ||
Гидроокись калия |
ГОСТ 24363 – 80 | Массовая доля (КОН), %, не менее | 84,5 |
Рассыпчатость,% | 100 | ||
Технический лигносульфонат |
ТУ 2455-028-00279580-2004 | Массовая доля сухих веществ, %, не менее | 50 |
Массовая доля золы к массе сухих веществ, %, не более | 27,0 | ||
Плотность, кг/м3, не менее | 1280 | ||
Вязкость условная, с не менее | 4,5 |
N330 - Высокодисперсный усиливающий техуглерод, размер частиц 28- 36 нм. Обеспечивает высокий предел прочности при растяжении и хорошее сопротивление истиранию.
Применение: 1. Брекер и боковины шин. Массивные шины, каркас рукава, конвейерные ленты, резинотехнические изделия
1.4 Технология получения технического углерода. Нормы технологического режима.
В головную часть реактора РС тремя потоками в зону горения подается природный газ 28 и воздух низкого давления 3а. При сгорании образуется поток раскаленного дымового газа, который поступает в зону реакции. В этот поток четырьмя форсунками подается сырье 32. Происходит его термическое разложение. Температура в зоне реакции может быть 1500-2000˚С, время реакции 0,01-0,06 секунд. Для прекращения реакции в реактор подают воду химически очищенную. Сначала в зону предзакалки двенадцатью форсунками, а затем четырьмя форсунками в зону закалки.
Температура в зоне закалки понижается до 750-850˚С, из реактора поток углеводородгазовая смесь УГС поступает в подогреватель воздуха ПВ, где за счет подогрева воздуха низкого и высокого давления, УГС охлаждается до температуры 500-550˚С.
Дальше УГС поступает в газоохладитель ГО, а затем в водяной холодильник Х1. Температура после газоохладителя не должна превышать 270˚С, так же это связано с термической устойчивостью рукавов. Далее УГС попадает в циклон Ц1, где улавливается основная часть технического углерода. Уловленный техуглерод через инерционную ловушку ИЛ1 поступает в микроизмельчитель МИ, где очищается от примесей (грит, окалина) механически. Отходящий газ с циклона Ц1 поступает в рукавный фильтр ФР1. Техуглерод из фильтра ФР1 поступает в циклон Ц1. Из микроизмельчителя МИ1 поступает в систему газотранспорта турбовоздуходувки ТВ2 откуда попадает в циклон газотранспорта ЦГ.
Из цикла газотранспорта ЦГ техуглерод шлюзовым питателем подается в уплотнитель сажи УС. Газы из циклона газотранспорта ЦГ поступает в циклон аспирации ЦА.
Из уплотнителя сажи УС техуглерод поступает в смеситель-гранулятор СГ, куда подается раствор лигносульфанатов. Гранулированныйтехуглерод поступает в барабанную сушилку БСК. Высушенный техуглерод из сушилки
поступает на элеватор Э, откуда проходит классификатор К2 и поступает в бункер готовой продукции БГС. Запыленный воздух из элеватора и классификатора турбовоздуходувкой ТВ12 поступает на фильтр аспирации ФР2. Очищенный воздух поступает в атмосферу, а уловленный техуглерод на циклон аспирации ЦА.
Воздух с частицами техуглерода с сушилки поступает вместе с газом из циклона доулавливания ЦД в фильтр доулавливания ФР3. Техуглерод из ФР3 поступает в циклон доулавливания ЦД.
Готовый техуглерод из бункера ссыпается в вагоны-хоппера ВХ.
Для производства определенных марок техуглерода необходимо поддерживать технологический режим. К показателям режима относятся температура футеровки, температура реакционной смеси, давление воздуха, давление природного газа, расход сырья, расход природного газа, расход воздуха.
Таблица 1.3 – Технологический режим процесса
Наименование аппаратов и показателей режима | Единицы измерения | Допустимые пределы |
Расход сырья в реактор | кг/ч | 4200 – 4800 |
Расход воздуха низкого давления | м3/ч | 18000 – 23000 |
Расход природного газа в реактор | м3/ч | 700 – 1000 |
Расход предочищенной воды | кг/ч | 4000 – 8000 |
Температура подогрева воздуха низкого давления | оС | не менее 50 |
Температура футеровки в зоне горения реактора | оС | 1820 – 1860 |
Температура реакционной смеси реакции | оС | 1500 – 1680 |
Температура углеродогазовой смеси в зоне закалки реактора | оС | 820 -850 |
Давление сырья перед форсунками реактора | МПа | 0,8 - 1,6 |
Давление природного газа перед отсечным клапаном | МПа | 0,3 - 0,45 |
Давление природного газа после регулирующего клапана | МПа | 0,06 - 0,3 |
Давление природного газа перед горелкой реактора | МПа | 0,06 - 0,3 |
Давление природного газа перед диафрагмой | МПа | 0,3 – 0,45 |
Давление предочищенной воды | МПа | 0,8 |
Температура газов перед ФР1 | 0С | 260-280 |
Температура газов после ФР1 | 0С | 220-260 |
Давление газов перед ФР 1 | МПа | 2,5 |
Температура газов перед ФР3 | 0С | 140-240 |
Температура газов после ФР 3 | 0С | 130-200 |
Давление перед ФР 3 | МПа | н/б 2,5 |
Температура газов перед ФР 2 | 0С | 30-100 |
Температура газов на продувку ФР 2 | 0С | 180-250 |
Давление перед ФР 2 | МПа | н/б 2,5 |
1.5 Автоматизация технологического процесса
Автоматизированная система управления (АСУ) – комплекс программных и технических средств выполняющих функцию непрерывного сбора информации о процессе от датчиков, ее обработки, визуализации и формирования управляющих воздействий (регулирующих, сигнализирующих, блокирующих) в соответствии с заданными моделями управления с привлечением оператора или без него. Обеспечение соблюдения технологических параметров в полной мере зависит от системы управления. Новая модульная система управления Allen-Bradley, позволяет обеспечить оптимальное управление всем технологическим процессом, формирует задачи автоматического управления, а так же создает наилучшие условия эксплуатации оборудования что, в свою очередь, позволит снизить затраты на его техническое обслуживание и ремонт. Процесс сушки технического углерода ведется при использовании комбинированной системы управления. Система управления Allen-Bradley и контроллеры SLC-500 широко используются.
Все данные о процессе представляются двумя типами сигналов: аналоговыми и дискретными. Определяют наличие сигналов постоянным напряжением 10-30В. В АСУ ТП применяют сигналы напряжением 24 В. Модули имеют гальваническую развязку каналов, способны осуществлять контроль целости кабельной линии. Все сведения о настройках модуля сохраняются во временном процессоре.
Система выполняет следующие функции:
1.Автоматическое регулирование следующих технологических параметров:
- температура углеродогазовой смеси в зоне основной закалки реактора, изменением расхода предочищенной воды при помощи регулирующего клапана (поз. 8-4);
- температура углеродогазовой смеси в зоне предварительной закалки реактора изменением расхода предочищенной воды в эту зону, регулирующий
клапан (поз. 6-4);
- температура углеродогазовой смеси в зоне горения с коррекцией по расходу природного газа регулирующим клапаном (поз. 2-4);
- расход сырья на реактор с автоматической поправкой по значениям плотности сырьевой смеси регулирующим клапаном (поз. 10-4);
- расход воздуха низкого давления в реактор регулирующим клапаном (поз. 13-4);
- расход воздуха высокого давления в реактор на распыление сырьевой смеси регулирующим клапаном (15-4);
- расход хлорида калия в реактор регулирующим клапаном (11-4).
2. Контроль осуществляется всех входных, выходных, и регулирующих параметров:
- температура футеровки в зоне горения реактора (поз. 3-1);
- температура углеродогазовой смеси в зоне реакции реактора (поз. 4-1);
- температура углеродогазовой смеси в зоне предварительной закалки реактора (поз. 5-1);
- температура углеродогазовой смеси в зоне основной закалки реактора (поз. 7-1);
- температура углеродогазовой смеси перед воздухоподогревателем ПВ-235 (поз. 22-1);
- температура углеродогазовой смеси после воздухоподогревателя ПВ-235 (поз. 23-1);
- температура подогрева ВНД, подаваемого на горение (поз. 21-1);
- давление природного газа перед отсечным клапаном (поз. 15-1);
- давление природного газа после регулирующего клапана (поз. 16-1);
- давление природного газа перед горелкой (поз. 17-1);
- давление воздуха высокого давления на распыление сырья (поз. 24-1);
- давление сырья перед форсунками реактора (поз. 18-1);
- давление предочищенной воды перед форсунками зоны предварительной закалки реактора (поз. 19-1);
- давление предочищенной воды перед форсунками зоны основной закалки реактора (поз. 20-1);
- перепад давления в реакторе (поз. 12-1);
- расход природного газа в реактор (поз. 2-1);
- расход ВНД в реактор (поз. 13-1);
- расход сырья на реактор (поз. 10-1);
- расход предочищенной воды в зону предварительной закалки реактора (поз. 6-1);
- расход предочищенной воды в зону основной закалки реактора (поз. 8-1).
3.При выходе за допустимую границу измерения технологических параметров предусмотрена световая и звуковая сигнализация:
- при увеличении температуры футеровки в зоне горения реактора выше установленного значения;
- при увеличении температуры углеродогазовой смеси в зоне реакции реактора выше установленного значения;
- при увеличении температуры углеродогазовой смеси в зоне предварительной закалки реактора выше установленного значения;
- при увеличении температуры углеродогазовой смеси в зоне основной закалки реактора выше установленного значения;
- при уменьшении давления природного газа после регулирующего клапана ниже установленного значения;
- при увеличении давления природного газа после регулирующего клапана выше установленного значения;
- при уменьшении давления воздуха высокого давления;
- при увеличении перепада давления в реакторе;
- при уменьшении расхода природного газа в реактор ниже установленного значения;
- при уменьшении расхода воздуха на горение в реактор ниже установленного значения;
- при уменьшении расхода воздуха на распыление сырья в реактор ниже установленного значения;
- при уменьшении расхода сырья, на реактор ниже установленного значения.
4.Аварийная блокировка работы реактора обеспечивает закрытие отсечных клапанов: на трубопроводе подачи природного газа в реактор (позиция 1-3), на трубопроводе подачи сырья в реактор (позиция 10-6), на трубопроводе подачи в реактор воздуха низкого давления (позиция 13-6), на трубопроводе подачи в реактор воздуха высокого давления (позиция 14-6), на трубопроводе подачи в поток сырья хлорида калия (позиция 11-6) и открытие отсечного клапана (позиция 5-3) на трубопроводе подачи предочищенной воды в форсунки зоны основной закалки реактора, при выходе за допустимую границу измерения следующих технологических параметров:
- при увеличении температуры углеродогазовой смеси в зоне основной
закалки реактора выше установленного значения;
- при увеличении давления природного газа после регулирующего клапана выше установленного значения;
- при уменьшении расхода воздуха на горение в реактор ниже установленного значения;
- при уменьшении расхода сырья, на реактор ниже установленного значения.
1.6 Техника безопасности в лаборатории
Исследование по теме «анализ методов по определению удельной внешней поверхности технического углерода» выполнялись в лаборатории контроля качества.
Общие правила техники безопасности
Вход в помещение лаборатории посторонним лицам, непосредственно не связанным с работой в лаборатории, воспрещается.
Ответственным за соблюдение правил пожарной безопасности по лаборатории в целом является начальник лаборатории. В каждом отдельном помещении лаборатории ответственным является сотрудник, назначенный по распоряжению начальника лаборатории; на вывешенном аншлаге должна быть указана фамилия ответственного за соблюдение правил пожарной безопасности.
К работе в химических лабораториях и на опытных установках допускаются лица, прошедшие инструктаж и обучение безопасным методам работы согласно инструкции "О порядке прохождения инструктажа и обучения безопасным приемам и методам работы на ООО «Омсктехуглерод" (ИТБ-СК-00.001-02).
Лаборант химического анализа может быть подвержен воздействию следующих опасных и вредных факторов: отравлению, термическим и химическим ожогам, поражению электрическим током.
Таблица 1.3 – Характеристика пожаро-взрывоопасных и токсических свойств сырья, полупродуктов, готовой продукции и отходов производства
Наименование | Температура вспышки оС | Темп-ра самовосп-ламенения, оС | Пределы воспламе-нения об.% | пдк | Класс опас- ности | Описание свойств | ||
Сырье и реагенты | ||||||||
Антраце-новая фракция | 140 | 554 | 133 | 165 | 0,1 | 2 | Вызывает раздроженислиз.обол. | |
Продолжение таблицы 1.3
Наиме- нование | Темпера- тура вспышки, оС | Темп-ра самовосп-ламенения, оС | Пределы воспламе-нения об.% | Пдк г/м3 | Класс опас- ности | Описание свойств | |
Смола пиролиза | Не ниже 75 | не ниже 400 | 80 | 140 | 50 | 4 | Раздражают слиз.оболочки вызывает головокружение,головную боль. |
Лигно-сульфо-натытехнические | Пожаро- и взрывобезопасны | 6 | 4 | Пары диокси-да серы, при повыш.температуре(180°С и более),могут раздражать глаза и дыхат. пути | |||
Калий хлористый | Пожаро- и взрывобезопасны | 5 | 3 | Попадая на кожные раны, ухудшает заживление | |||
Продукция | |||||||
Технический углерод N339 |
Пожароопасный | 0,05 | 2 | Вызывает механическое раздрожениеглаз,дыхательных путей , сухость кожи | |||
Характеристика пожаро-взрывоопасных и токсических свойств сырья, полупродуктов, готовой продукции и отходов производства
Таблица – 6 Взрывопожарная и пожарная опасность, санитарная характеристика производственных зданий помещений, зон и наружных установок
Наименование производственных зданий, помещений, наружных установок | Категория взрывопожарной и пожарной опасности помещений и зданий по НПБ 105-03 | Классификация взрывоопасных зон внутри и вне помещений для выбора и установки электрооборудования по ПУЭ | Группа производственных процессов по санитарной характеристике по СНиП 2.09.04-87 | ||
Класс взрывоопасной зоны | Категория и группа взрывоопасных смесей | Наименование веществ, определяющих категорию и группу взрывоопасных смесей | |||
Отделение получения техуглерода (реакторное отделение) | Г | Пожароопасная зона, класс П-II | Категория IIА, группа Т1 | Пары углеводородов, техуглерод, окись углерода | Выделение вредной пыли, выделение тепла, группа 3-б |
Отделение улавливания. Отметка 0,0 м, 6,0 м, 15,2 м | Б | Взрывоопасная зона, класс В-1б | Категория IIА, группа Т1 | Пыль техуглерода, окись углерода | Выделение вредной пыли, группа 1-в |
Отделение обработки | Г | Пожароопасная зона, класс П-II | Категория IIА, группа Т1 | Пыль техуглерода, природный газ | Выделение вредной пыли, группа 1-в |
Отделение упаковки, склад готовой продукции | В | Пожароопасная зона, класс П-II | Категория IIА, группа Т1 | Пыль техуглерода | Выделение вредной пыли, группа 1-в |
Настоящая инструкция предусматривает основные требования по организации и безопасному проведению лабораторных работ: с химреактивами, с сырьем для производства техуглерода, концентрированными кислотами, едкими щелочами, стеклянной химической посудой, ЛВЖ и ГЖ, электроприборами, техуглеродом и т.д.
Работа с вредными и ядовитыми веществами.
В каждом помещении лаборатории разрешается хранить запас легковоспламеняющихся и горючих жидкостей и газов, не превышающий суточной потребности каждого вида вещества.
ЛВЖ и ГЖ необходимо хранить в специальном помещении (кладовой) в специальных металлических ящиках, стенки и дно которых выложены асбестом.
На рабочем месте ЛВЖ и ГЖ должны находиться в количествах, необходимых для работы.
ЛВЖ и ГЖ следует доставлять в лабораторию в плотно закрытой посуде, помещенной в специальный металлический ящик с ручками.
Категорически запрещается сливать в канализацию горючие жидкости и ядовитые вещества без их предварительной нейтрализации и обезвреживания.
В помещении лаборатории категорически запрещается мыть пол, столы и другое оборудование бензином, керосином и другими органическими растворителями.
Нельзя оставлять на рабочем месте промасленные тряпки и бумагу.
Запрещается сушить что-либо на батареях, трубах парового отопления, работать с ЛВЖ и ГЖ над трубами парового отопления.
Все работы с ЛВЖ, ГЖ, а также работы, связанные с выделением ядовитых и токсичных веществ и огне-взрывоопасных паров и газов, должны производиться только в вытяжных шкафах при работающей вентиляции выключенных горелках и электронагревательных приборах.
Категорически запрещается нагревать на открытом огне, а также на электронагревательных приборах, не предназначенных для этого, сосуды, содержащие огнеопасные и низкокипящие жидкости.
В случае разлива огнеопасных жидкостей или при утечке горючих газов необходимо немедленно потушить все горелки, принять меры к выявлению и устранению причин утечки. Разлитые жидкости засыпать песком, собрать совком в металлическое ведро и вынести за пределы лаборатории в подземный резервуар участка подготовки сырья.
Залитые места промыть водой, а помещение в обязательном порядке проветрить.
Категорически запрещается хранить в лаборатории сжиженные газы и низкокипящие жидкости с температурой кипения ниже 50°С, за исключением баллонов со сжиженными газами непосредственно используемых для выполнения круглосуточных анализов.
Работа с электрооборудованием
Прежде чем приступать к работе с использованием электрооборудования проверить заземлено ли оно, а электрошнуры на наличие видимых повреждений. При обнаружении повреждений или дефектов оборудования - немедленно поставить в известность инженера вашего сектора. Нельзя оставлять без присмотра работающие электроустановки, нагревательные приборы, газовые горелки.
При пользовании электронагревательными приборами запрещается:
- устанавливать приборы на сгораемой подставке;
- использовать временную электропроводку к нагревательным приборам;
- оставлять без присмотра включенные в сеть приборы;
- применять электроприборы сразу же после воздействия химических веществ или воды;
- применение открытых плиток в вытяжных шкафах;
- держать горючие материалы вблизи включенных электронагревательных приборов.
При обработке резиновых смесей на вальцах :
- работать с включенной вытяжной вентиляцией;
- после пуска вальцев и в процессе работы загрузку каучука и резины выполнять со стороны переднего валка справа;
- равномерность зазора между валками проверяется путем выреза кусочков резины с обеих сторон валка и сравнения их толщины;
- во время работы поддерживать чистоту и порядок рабочего места;
- нельзя производить чистку вальцев, ремонт или устранение неполадок на ходу;
- в случае обнаружения в процессе работы нехарактерных для работы шума или стука, вальцы следует остановить и сообщить об этом инженеру или слесарю;
- в случае попадания в резину посторонних предметов следует остановить вальцы аварийником и убрать эти предметы;
- нельзя извлекать посторонние предметы из резины при работе вальцев;
- при переходе резины на задний валок нужно подрезать смесь со стороны заднего валка, спустив ее на противень, и произвести загрузку смеси на вальцы со стороны переднего валка;
- нельзя наклоняться над валками для передачи резины с заднего валка на передний;
- при подрезании, срезке резины следить, чтобы левая рука была выше правой, во избежание пореза ее соскользнувшим ножом;
- закатывать подрезанную резину в рулон нужно только ладонью, при этом ладонь должна находиться сверху резины;
- нельзя производить уборку и чистку вальцев во время их работы;
Также запрещается:
- допускать к вальцам посторонних лиц и оставлять их без присмотра;
- облокачиваться или класть какие-либо предметы на ограждения и ходовую часть вальцев;
- приближать руки близко к сходу валков при загрузке вальцев каучуком;
- при срезании резины с вальцев или подрезании ее опираться свободной рукой о стрелы, станину или валок;
- работать с перекошенным зазором между валками;
- работать одному на вальцах, изолированных от места общей работы.
В целях предупреждения загорания резин нужно следить, чтобы оборудование не перегревалось, было исправно заземление.
Вальцовщику резиновых смесей необходимо во время работы на прессе выполнять следующие требования безопасности:
- загрузку пресса производить с помощью подъемного стола;
- во время загрузки пресса стоять в устойчивом положении;
- нельзя оставлять работающий пресс без присмотра.
Рабочим, работающим на прессах, запрещается:
- допускать к прессам посторонних лиц;
- работать на прессах с неисправным заземлением;
- работать на прессах с неисправным аварийным выключателем;
- ставить на подъемный стол посторонние предметы;
- без отключения пресса от электросети производить его ремонт, чистку и обтирку
- включать пресс без прессформ (при работе с планками для принудительного разъема прессформ);
- работать на прессе при давлении в гидросистеме свыше 20 МПа (200 кгс/см2);
- опираться руками на ограждение подъемного стола при его опускании.
Противопожарные мероприятия
К средствам пожаротушения в ЛКК относятся:
- внутренние пожарные краны;
- углекислотные огнетушители;
- порошковые огнетушители;
- асбестовое одеяло, песок и пр.
Персональная ответственность за сохранность противопожарного инвентаря возлагается на лиц, ответственных за противопожарное состояние помещений лаборатории.
В случае пожара позвонить по телефону 5-44, 5-12 и начать тушение имеющимися в лаборатории средствами пожаротушения.
При возникновении аварийных ситуаций (возникновение загорания, пожара) немедленно сообщить начальнику сектора испытаний техуглерода в резине (в вечернее время - диспетчеру завода) и приступить к ликвидации аварийной ситуации подручными средствами пожаротушения.
Уметь оказывать первую доврачебную помощь при переломах костей, поражении электрическим током, ожогах, отравлениях.
При необходимости сообщить в здравпункт по тел. 5-57.
Характеристика токсичных свойств веществ
• сырье для производства технического углерода - горючие вещества, нерастворимые в воде с характерным специфическим запахом, воспламеняющиеся при нагревании при контакте с открытым пламенем. Обладают токсическими свойствами, опасны при вдыхании, попадании на кожу и слизистые оболочки; класс опасности 4, ПДК - 300 мг/м3
• газ пропан - токсичен, обладает удушающими свойствами, при концентрации в воздухе рабочей зоны более 10% вызывает кислородное голодание (удушье), при концентрации более 20% - смерть;
• органические растворители (бензин, толуол, ацетон) на организм человека действуют как слабые наркотики, вызывая головную боль, головокружение, тошноту, сердцебиение, расстройство равновесия, а также сухость кожи.
• хлороформ, четыреххлористый углерод - наркотики, действующие токсически на обмен веществ и внутренние органы, в особенности на печень;
• фенол - обладает токсическими свойствами, оказывает раздражающее
• действие на кожные покровы, угнетает мыслительные процессы;
• едкие щелочи - вызывают ожоги при попадании на кожу и слизистые оболочки;
• концентрированные кислоты - вызывают раздражение и ожоги слизистых оболочек верхних дыхательных путей, поражают легкие. При попадании на кожу образуются глубокие ожоги, плохо поддающиеся лечению.
ВЫВОДЫ
Освоены требования техники безопасности и охраны труда на ООО «Техуглерод». Изучены нормы технологического режима работы оборудования.
Отражены способы контроля и регулирования технологических параметров, описание средств автоматизации.
СПИСОК ИСТОЧНИКОВ
Основные источники
1.Кирсанов, Ю.Г.Анализ нефти и нефтепродуктов: учебно-методическое пособие / Ю.Г.Кирсанов, М.Г.Шишов, Е.И.Коняева; Под ред. О.Белоусова. - 2-е изд., стер. - М.:Флинта, Изд-во Урал.ун-та, 2017. - 88 с [Электронный ресурс]. http://znanium.com/bookrea d2.php?book=947691
2.Рябов, В. Д. Химия нефти и газа: учеб.пособие / В.Д. Рябов. — 2-е изд., испр. и доп. — М.: ФОРУМ; ИНФРА-М, 2017. — 335 с. [Электронный ресурс].- Режим доступа: http://znanium.com/bookrea d2.php?book=546691
Методические:
1. Светикова С.В. Комплект учебно-методических указания по проведению практических занятий по междисциплинарному курсу «Обеспечение технологии нефти и газа», для специальности 18.02.09 Переработка нефти и газа, 2017 . [Электронный ресурс]
указаний к практическим занятиям/С.В.Светикова.- Омск, 2014
2.Светикова С.В. Управление технологическим процессом: ведение технологии производства технического углерода: методические указания для выполнения практических работ/ С.В.Светикова.- Омск, 2013.
Дополнительные:
1. Вержичинская, С.В. Химия и технология нефти и газа: учеб.пособие для СПО/ С.В. Вержичинская, Н.Г.Дигуров, С.А.Синицын.- 2-е изд., испр. и доп.- М.: Форум, 2012.- 400с., ил.
2.Ивановский, В.И. Технический углерод. Процессы и аппараты: учеб.пособие/ В.И.Ивановский.- Омск: Техуглерод, 2004.- 228 с., ил.
3. Капустин, В.М. Технология переработки нефти. Ч.2: Деструктивные процессы: учеб.пособие для вузов/ В.М.Капустин, А.А.Гуреев.- М.: КолосС, 2008.- 334 с.
4.Орлов, В.Ю. Производство и использование технического углерода для резин/В.Ю.Орлов, А.М.Комаров, Л.А.Ляпина.- Ярославль, Изд-во А.Рутман, 2002.- 512 с.: ил.
5. Основные процессы и аппараты химической технологии: пособие по проектированию/ под ред. Ю.И.Дытнерского.- 4-е изд., стереотип.- М.: Альянс, 2008.- 496 с.
6. Романков, П.Г. Методы расчета процессов и аппаратов химической технологии (примеры и задачи): учеб.пособие для вузов/ П.Г.Романков, В.Ф.Фролов, О.М.Флисюк.- СПб.: Химиздат, 2010.- 544 с.: ил.
7.Рябов, В.Д. Химия нефти и газа: учеб.пособие/ В.Д.Рябов.- М.: Форум, 2009.- 334 с.
8. Технология переработки нефти: учеб.пособие для вузов. Ч.1/ под ред. О.Ф.Глаголевой, В.М.Капустина.- М.: Химия, 2007
9.Нефтепереработка и нефтехимия: науч.–информационный сборник/учредитель ОАО «ЦНИИТЭнефтехим».- М.: ОАО «ЦНИИТЭнефтехим».
10. Потехин, В.М. Основы теории химических процессов технологии органических веществ и нефтепереработки: учебник для вузов/ В.М.Потехин, В.В.Потехин.- СПб.: Химиздат, 2007.- 944 с., ил.
Нормативно - техническая литература
ГОСТ Р 51313-2013 - Стандарты на нефтепродукты
Периодические издания (по выбору)
«Химия и технология топлив и масел»
Интернет – ресурсы
1. Ахметов С.А Технология глубокой переработки нефти. - СПб: Недра. 2006.URL: http://www.gaschemistry.ru (дата обращения 15.11.2020).
2. Баннов П.Г. Процессы переработки нефти. - /ЦНИИТЭНефтехим: сетевой журнал.2006. www.infanata.org/...pererabotki_nefti_i_gaza.html (дата обращения 02.10.2020).
Аттестационный лист по практике
Ф.И.О.____Шленцовой Валентины Валерьевны
Обучающегося на__4_ курсе специальности 18.02.09 Переработка нефти и газа
Успешно прошел _________________________________ практику в объеме __________ часов
с 23.03.2021 – 19.04.2021г. На предприятии ООО «Техуглерод»
(Название предприятия)
Дата добавления: 2021-12-10; просмотров: 31; Мы поможем в написании вашей работы! |
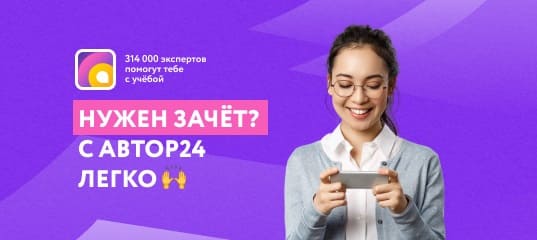
Мы поможем в написании ваших работ!