Метрологическая экспертиза и метрологическая проработка технической документации
Федеральное агентство железнодорожного транспорта
Федеральное государственное бюджетное образовательное учреждение
высшего образования
«ОМСКИЙ ГОСУДАРСТВЕННЫЙ УНИВЕРСИТЕТ ПУТЕЙ СООБЩЕНИЯ»
(ОмГУПС (ОмИИТ))
Кафедра «Технологии транспортного машиностроения
и ремонта подвижного состава»
ОТЧЕТ
по учебной
(слесарно-механической)
практике
Студентка гр. 19-з
___________И.И. Иванова
______________2021 г.
Руководитель практики:
доцент каф. ТТМ и РПС
___________М.И. Бисерикан
______________2021 г.
Омск 2021
Содержание
Введение. 3
1 Обработка плоских торцевых поверхностей и уступов. Резцы для обработки торцевых поверхностей и уступов. Контрольный и измерительный инструмент. 4
|
|
1.1 Основные теоретические положения. 4
1.1.1 Механическая обработка. 4
1.1.1.1 Виды механической обработки. 4
1.1.2 Торцевая поверхность. 5
1.1.3 Уступы.. 5
1.1.4 Классификация токарных резцов. 5
1.2 Резцы для обработки торцов и уступов. 6
1.2.1 Материалы и углы подрезных резцов. 7
1.2.2 Углы подрезного резца и их назначения. 8
1.2.3 Режимы резания. 10
1.2.3.1 Основные параметры.. 10
1.2.4 Направление подачи при подрезании торцов. 11
1.2.5 Системы ЧПУ (Числовое программное управление) 12
1.3 Инструменты, применяемыедля обработки плоских торцевых поверхностей и уступов. 14
1.3.1 Контрольно-измерительные инструменты.. 14
2 Метрологическая экспертиза и метрологическая проработка технической документации 16
2.1 Метрологическая экспертиза. 16
2.1.1 Фактическая цель формальной метрологической
экспертизы.. 17
2.1.2 Метрологический контроль. 17
2.1.3 Возможные формы организации метрологической экспертизы 18
2.2 Метрологическая проработка. 19
2.2.1 Различие понятий МЭ и МП.. 20
Заключение. 21
Библиографический список. 23
Введение
Прежде чем приступить к изучению вопросов отчёта, необходимо ознакомиться с основными понятиями, благодаря которым я сумею в общих чертах ознакомиться с профессиями токаря и слесаря (поскольку суть нашей практики заключается в изучении соответственного материала и работе на токарном и слесарном станках) и их профессиональными функциями. Изучить методы обработки поверхности детали, инструменты, которыми выполняется сама обработка и производится процесс измерения.
|
|
Цель практики: приобретение и совершенствование навыков слесарного и токарного дела, а также расширение некоторой области знаний, необходимой для дальнейшего развития и самореализации в профессиональной сфере.
В век современных технологий и инноваций колосальное значение в развитии большенстваотрослей промышленности, науки и экономики играет техника. Составляющие технического прибора – это взаимосвязанные детали, которые в свою очередь должны соответствовать первоначально заданым определённым требованиям. От качества изготовленных деталей, точности и соответствия её первоначальным критериям зависит качество работы прибора. Для того, чтобы предать детали вид, подобающий с идеальным (заданым первоначально), деталь необходимо обработать. Процесс обработки детали называется – металлообработка.
|
|
Металлообработка – технологический процесс изменения формы, размеров и качеств металлов и сплавов. Во время технологических процессов обработки металлов различными методами меняются форма и размер металла, а также могут меняться физико-механические свойства металлов.
Люди, занимающиеся процессом обработки материалов имеют свои профессиональные названия:
Токарь –рабочий-станочник, специалист по токарному делу– обработке резанием вращающихся заготовок или вращающегося режущего инструмента, по обработке дерева, металла
Принцип токарной обработки заключается в том, что инструмент, врезаясь своей режущей кромкой в поверхность изделия, зажимает его. Чтобы снять слой металла, соответствующий величине такого врезания, инструменту надо преодолеть силы сцепления в металле обрабатываемой детали.
Слесарь – специалист по ручной (без использования станков) обработке металлов, включая операции по сборке и разборке (ссылка) на производстве или в быту.
Слесарной обработкой металлов называется ручная обработка режущим инструментом, производимая для придания деталям необходимой формы и размеров или для пригонки одной детали к другой с определенным допуском.
|
|
1 Обработка плоских торцевых поверхностей и уступов. Резцы для обработки торцевых поверхностей и уступов. Контрольный и измерительный инструмент
1.1 Основные теоретические положения
1.1.1Механическая обработка
Механическая обработка – обработка изделий из стали и других материалов с помощью механического воздействия с применением резца, сверла, фрезы и другого режущего инструмента. Сам процесс обработки осуществляется на металлорежущих станках, в установленном порядке согласно технологическому процессу.
1.1.1.1Виды механической обработки
Обработка резанием осуществляется на металлорежущих станках путём внедрения инструмента в тело заготовки с последующим выделением стружки и образованием новой поверхности.
Виды резания:
–наружные цилиндрические поверхности – точение, шлифование, притирка, обкатывание, суперфиниширование;
–внутренние цилиндрические поверхности – растачивание, сверление, зенкерование, развертывание, протягивание, шлифование, притирка, хонингование, долбление;
– плоскости – строгание, фрезерование, шлифование.
При обработке резанием механическая обработка также разделяется по чистоте обработанной поверхности:
– черновая обработка;
– получерновая обработка;
– чистовая обработка;
– получистовая обработка;
– суперфиниширование;
– обработка методом пластической деформации.
Осуществляется под силовым воздействием внешней силы, при этом меняется форма, конфигурация, размеры, физико-механические свойства детали. Это процессы: ковка, штамповка, прессование, накатывание резьбы.
Обработка методом деформирующего резания основана на совмещении процессов резания и пластического деформирования подрезанного слоя. Используется для получения поверхностей с регулярным макрорельефом (теплообменных, фильтрующих), для восстановления размеров изношенных поверхностей трения.
Электрофизическая обработка основана на использовании специфических явлений электрического тока: искра (электроэрозионная обработка), электрохимия (электрохимическая обработка), дуга (электрическая дуговая сварка).
1.1.2Торцевая поверхность
В случае использования отогнутого подрезного резца подача осуществляется поперечно для деталей, закреплённых в патроне, или со стороны задней бабки при закреплении в центрах. Расположение резца при этом должно быть строго по центру. Опускание его ниже приведёт к невозможности обработки части детали, а выше – наверняка закончится для резца плачевно.
Чистота обработки достигается стандартным путём – несколькими проходами (как правило, достаточным количеством является два – черновой» и «чистовой», хотя нередко и использование финальной шлифовки). При этом обработка торцов и уступов использует определённую терминологию. Так, толщину удаляемого слоя металла при каждом проходе называют глубиной резки, а длину поперечного перемещения, осуществляемую за один оборот – подачей.
1.1.3Уступы
Отличием их обработки от торцевой является использование не обычных, а упорных проходных резцов, используемых в первую очередь для однопроходной обработки уступов небольшого размера (до 5-6 мм). Подача при этом осуществляется продольно, а при последующей зачистке – поперечно, с отведением резца. При крупных серийных партиях частым явлением служит использование ограничивающих неподвижных упоров, а для мелких партий или единичных деталей – так называемый метод пробных проходов.
1.1.4Классификация токарных резцов
На токарных станках выполняют много видов обработки, что привело к созданию большого количества резцов по назначению и конструкции. Типы токарных резцов в основном подразделяют по следующим признакам: виду обработки, характеру обработки, форме головки, направлению подачи, способу изготовления и роду материала режущей части.На рисунке 1.1 приведены типы резцов по виду обработки.
На рисунке 1 приведены типы резцов по виду обработки. Проходные резцы 1,2 и 3 служат для обтачивания гладких цилиндрических и конических поверхностей. Подрезной резец 4 работает с поперечной подачей при обточке плоских торцовых поверхностей. Расточные резцы 5 и 6 применяется при растачивании сквозных отверстий, а расточной упорный резец 12 – для растачивания глухих отверстий. Отрезной резец 10 применяется для разрезания заготовки и для протачивания кольцевых канавок. Для нарезания резьбы применяют резьбовые резцы 10, 12, а для обточки фасонных поверхностей – резец 11.
1,2,3 – проходные резцы; 4 – подрезной резец; 5 – широкий проходной резец; 6 – расточной резец; 7 – расточной упорный; 8 – отрезной резец; 9 – резьбовой резец
Рисунок 1.1 – Основные типы токарных резцов
По характеру обработки резцы подразделяют на черновые (обдирочные) 2, чистовые 5 и для тонкого точения. По форме головки: прямые 1,3, отогнутые 2, оттянутые 10 и изогнутые.
По направлению подачи их подразделяют на правые и левые. Правые работают с подачей справа налево, а левые – слева направо. По способу изготовления резцы бывают целые, с приваренной встык головкой, с припаянной пластинкой, с механическим креплением режущей пластинки. По применяемому материалу резцы бывают из быстрорежущей стали, с пластинками из твердого сплава или минералокерамики, с кристаллами алмазов.
1.2Резцы для обработки торцов и уступов
Обработка торцов деталей производится подрезными резцами (рисунок 1.2). Подрезной торцовый резец (рисунок 1.2а) пригоден лишь для обработки открытых поверхностей, например торца детали, закрепленной в патроне без поддержки задним центром. Он не пригоден для обработки торцов валов и других деталей, поддерживаемых задним центром. Подрезным резцом, изображенным на рисунке1.2 б, можно обрабатывать торцы валов и других деталей, установленных в центрах, уступы и многие другие поверхности. Недостаток такого резца: он хуже поглощает теплоту резания.
Раньше чем вершина такого резца приблизится к центру обрабатываемой поверхности, правый конец его главной режущей кромки упрется в центр. Достоинство рассматриваемого резца — массивность его головки, хорошо поглощающей теплоту резания.
Рисунок1.2 –Подрезные резцы
При обработке деталей, закрепленных без поддержки задним центром, торцовые поверхности их, обращенные к задней бабке, можно обтачивать проходными и чистовыми резцами, устанавливая их в резцедержателе параллельно линии центров станка.
Подрезные резцы бывают правые и левые. Правыми резцами пользуются для обработки торцовых поверхностей. Уступы, обращенные к задней бабке, обрабатывают правыми, а к передней бабке – левыми подрезными резцами.
1.2.1Материалы и углы подрезных резцов
Подрезные резцы изготовляются с пластинками из быстрорежущих сталей и из твердых сплавов, применяемых для проходных резцов. Форма передней поверхности подрезных резцов, как и проходных, может быть радиусной с фаской, плоской с фаской и плоской.
Прежде чем выбрать подрезной резец для обработки, нужно определиться с некоторыми особенностями: Во-первых, необходимо учесть материал режущей пластины инструмента. Резец должен быть более жестким, чем сама заготовка. Во-вторых, нужно учесть геометрию и конструкцию резца. Эти два параметры повлияют на дальнейший выбор значений подачи и скорости резания, а также на его стойкость, т. е. продолжительность непрерывной работы до того момента, пока режущие кромки не затупятся.
1.2.2Углы подрезного резца и их назначения
На рисунке 1.3 показана главная секущая плоскость. Передняя поверхность направлена вниз от главной режущей кромки, передний угол γ в этом случае считается положительным.
Рисунок 1.3 – Главная секущая плоскость резца
Для определения углов резца установлены следующие плоскости:
1)Плоскость резания– плоскость, касательная к поверхности резания и проходящая через главную режущую кромку.
2) Основная плоскость– плоскость, параллельная направлениям подач (продольной и поперечной).
3) Главная секущая плоскость – плоскость, перпендикулярная проекции главной режущей кромки на основную плоскость.
4) Вспомогательная секущая плоскость– плоскость, перпендикулярная проекции вспомогательной режущей кромки на основную плоскость.
Главные углы измеряются в главной секущей плоскости. Сумма углов α+β+γ=90°.
Главный задний угол α – угол между главной задней поверхностью резца и плоскостью резания. Служит для уменьшения трения между задней поверхностью резца и деталью. С увеличением заднего угла шероховатость обработанной поверхности уменьшается, но при большом заднем угле резец может сломаться. Следовательно чем мягче металл, тем больше должен быть угол.
Угол заострения β – угол между передней и главной задней поверхностью резца. Влияет на прочность резца, которая повышается с увеличением угла.
Главный передний угол γ – угол между передней поверхностью резца и плоскостью, перпендикулярной плоскости резания, проведённой через главную режущую кромку. Служит для уменьшения деформации срезаемого слоя. С увеличением переднего угла облегчается врезание резца в металл, уменьшается сила резания и расход мощности. Резцы с отрицательным γ применяют для обдирочных работ с ударной нагрузкой. Преимущество таких резцов на обдирочных работах заключается в том, что удары воспринимаются не режущей кромкой, а всей передней поверхностью.
Угол резания δ=α+β.
Вспомогательные углы измеряются во вспомогательной секущей плоскости.
Вспомогательный задний угол α1 – угол между вспомогательной задней поверхностью резца и плоскостью, проходящей через его вспомогательную режущую кромку перпендикулярно основной плоскости.
Вспомогательный передний угол γ1 – угол между передней поверхностью резца и плоскостью, перпендикулярной плоскости резания, проведённой через вспомогательную режущую кромку
Вспомогательный угол заострения β1 – угол между передней и вспомогательной задней плоскостью резца.
Вспомогательный угол резания δ1=α1+β1.
Углы в плане измеряются в основной плоскости. Сумма углов φ+φ1+ε=180°.
Главный угол в плане φ – угол между проекцией главной режущей кромки резца на основную плоскость и направлением его подачи. Влияет на стойкость резца и скорость резания. Чем меньше φ, тем выше его стойкость и допускаемая скорость резания. Однако при этом возрастает радиальная сила резания, что может привести к нежелательным вибрациям.
Вспомогательный угол в плане φ1 – угол между проекцией вспомогательной режущей кромки резца на основную плоскость и направлением его подачи. Влияет на чистоту обработанной поверхности. С уменьшением φ1 улучшается чистота поверхности, но возрастает сила трения.
Угол при вершине в плане ε – угол между проекциями главной и вспомогательной режущей кромкой резца на основную плоскость. Влияет на прочность резца, которая повышается с увеличением угла.
Угол наклона главной режущей кромки измеряется в плоскости, проходящей через главную режущую кромку перпендикулярно к основной плоскости.
Угол наклона главной режущей кромки λ – угол между главной режущей кромкой и плоскостью, проведенной через вершину резца параллельно основной плоскости. Влияет на направление схода стружки.
Углы резца в процессе резания
При смещении резца относительно оси детали, а также при наличии движения подачи плоскость резания поворачивается, в связи с чем значения углов меняются.
Если вершину резца установить выше или ниже оси детали, то плоскость резания отклонится от вертикального положения на угол τ. При наружном точении с установкой резца выше оси детали действительный передний угол γсмещ увеличивается, а αсмещуменьшается на угол τ. При внутреннем точении углы изменяются в обратном направлении.
При продольной подаче в результате вращательного движения детали и поступательного движения резца стружка срезается по винтовой поверхности. Плоскость резания при этом отклоняется от своего положения в статике на угол μ. Чем больше величина подачи, тем больше отклонение. Передний угол в кинематике γкин увеличивается, а αкин уменьшается на угол μ. При поперечной подаче поверхность резания будет представлять собой спираль, а задний угол будет уменьшаться с приближением резца к оси детали.
Действительную величину углов резца в главной секущей плоскости с учётом установки резца и кинематики процесса можно определить:
γд=γ+μ±τ(1)
αд=α-μ±τ(2)
На действительные углы резца влияет также износ передней и задней поверхностей резца.
1.2.3Режимы резания
Режимы резания при токарной обработке определяют на основании ряда технических показателей, среди которых самые значимые – это подача инструмента и частота вращения детали, закрепленной в шпинделе станка. Правильный выбор и применение режимов обработки гарантируют не только геометрическую точность и экономичность изготовления, но и сохранность детали, инструмента и оборудования, а также безопасность станочника.
1.2.3.1Основные параметры
Одна из главных задач технологической подготовки производства при токарных работах – это определение рациональных режимов резания. При их расчете должны учитываться особенности обрабатываемого изделия и возможности станочного парка, а также наличие соответствующего инструмента, приспособлений и оснастки. Компоновка узлов и агрегатов токарного станка позволяет реализовать два определяющих вида движения, которые формируют заданную конфигурацию поверхностей детали: вращение заготовки (главное движение) и перемещение резца вглубь и вдоль поверхности детали (подача). Поэтому основными технологическими параметрами для токарного оборудования являются:
– глубина резания t;
– подача и обороты шпинделя S;
– скорость резания V.
Элементы режима резанья и геометрия срезаемого слоя представлены на рисунке 1.4.
Рисунок 1.4 – Элементы режима резания и геометрия срезаемого слоя
Существует взаимовлияние режимов резания и основных элементов производственной экономики. Среди них самые значимые – это:
– производительность оборудования;
– качественные показатели производства;
– стоимость выпускаемых изделий;
– износ оборудования;
– стойкость инструмента;
– безопасность труда.
1.2.4Направление подачи при подрезании торцов
При обтачивании торцовых поверхностей резцом по рисунку1.2 б существенное значение имеет направление подачи.
Если подача резца направлена от центра (рисунок1.5 а) по стрелке А, то под действием давления резания резец будет отходить несколько в сторону от обрабатываемой поверхности (по стрелке А1). Получившиеся при этом недостатки в обработке поверхности будут устранены при чистовом подрезании, когда сила резания, а следовательно, и отжим резца незначительны. Если же подача резца производится к центру детали (рисунок 1.5 б), т. е. по стрелке В, то под действием силы резания резец отжимается по стрелке В1, затягивается в материал и обрабатываемая поверхность получает недостатки, часто не устранимые чистовым подрезанием.
При чистовом обтачивании торцовых поверхностей, особенно больших диаметров, вследствие износа резца они получаются вогнутыми, если подача производилась от центра к наружной поверхности, и выпуклыми – при обратном направлении подачи. Если обрабатываемая поверхность является опорной, то при установке и закреплении детали она займет правильное положение, когда эта поверхность вогнутая, и наклонное (неправильное), – когда она выпуклая.
а) – направленной от центра обрабатываемой детали;
б) – направленной к центру обрабатываемой детали
Рисунок 1.5 – Обтачивание торцовых поверхностей при подаче
От приведенного выше правила о выборе направления подачи как при черновом, так и при чистовом обтачивании торцовых поверхностей приходится иногда отказываться ввиду затруднений, возникающих при измерении длины детали, и когда приходится определять положение обрабатываемого торца относительно других ее поверхностей.
1.2.5Системы ЧПУ (Числовое программное управление)
Важнейшую роль в металлообработке играет и компьютерное управление станками – без которого обработка торцов и уступов никогда бы не достигла нынешней скорости, точности и практически нулевого присутствия не вынужденного брака. Учитывая технологические особенности токарных процессов, системы управления ими включают в себя следующие основные составляющие:
– позиционное управление – отвечающее за череду точных перемещений как резцов, так и деталей в заданные позиции;
– контурное управление – следящее за траекториями;
– адаптивное управление – корректирующее процесс обработки при изменяющихся условиях.
К плоским торцовым поверхностям и уступам предъявляются следующие основные требования: плоскостность, т. е. отсутствие выпуклости или вогнутости; перпендикулярность к оси; параллельность плоскостей уступов или торцов между собой. Перед обработкой торцовых плоскостей заготовки закрепляют теми же способами, что и при обработке наружных цилиндрических поверхностей.
Для подрезания торцов и уступов применяют резцы: проходной прямой, проходной отогнутый, проходной упорный, а также специальный подрезной (торцовый).
Невысокие уступы подрезают проходным упорным резцом при продольной Додаче, причем подрезание уступа обычно совмещают с обтачиванием наружной поверхности. Режущая кромка резца в этом случае должна располагаться перпендикулярно оси заготовки, что контролируют угольником. Торец подрезают упорным резцом при поперечной подаче с установкой режущей кромки под небольшим углом (5–10 ) к торцовой поверхности. Если при подрезании торца проходным упорным резцом приходится срезать большой припуск, то подача в направлении к центру вызывает отжимающую силу (черная стрелка), углубляющую резец в торец, в результате чего торец может» получиться вогнутым. Чтобы этого не произошло, срезают большую часть припуска несколькими проходами с продольной подачей, а чистовой проход выполняют поперечной подачей от центра.
На рисунке1.6 показаны методы подрезания торца заготовки при закреплении ее в патроне с поджимом задним центром. Для обеспечения подрезания центрирование выполняют с дополнительной фаской или применяют специальный срезанный опорный неподвижный центр.
Торцы и уступы обрабатывают подрезными, проходными отогнутыми или проходными упорными резцами. Подрезной резец (рисунок 1.1) предназначен для обработки наружных торцовых поверхностей. При подрезании торца подача резца осуществляется перпендикулярно оси обрабатываемой детали. Подрезной резец, позволяет обрабатывать различные торцовые и другие поверхности с продольной и поперечной подачами. Подрезные резцы изготовляют с пластинами из быстрорежущих сталей и твердых сплавов. Главный задний угол α=10-15 градусов, передний угол γ выбирают в зависимости от обрабатываемого материала. Проходным отогнутым резцом, рисунок - в) можно выполнять подрезку торца при поперечной подаче S2 и обтачивание при продольной подаче S1 резца. Проходным упорным резцом, рисунок - г) можно подрезать торцы и обтачивать уступы при продольной подаче S1. Резцы для подрезания торцов должны устанавливаться точно по оси детали, иначе на торце детали остается выступ. При большом диаметре торцовой поверхности припуск снимают с поперечной подачей в несколько проходов.
Рисунок 1.6 – Методы подрезания торца заготовки при закреплении ее в патроне с поджимом задним центром
Уступы более 2-3 мм подрезают проходными резцами в несколько приемов. Сначала уступ образуется при продольной подаче S1 резца, а затем подрезается при поперечной подаче S2.
1.3Инструменты, применяемыедля обработки плоских торцевых поверхностей и уступов
1.3.1 Контрольно-измерительные инструменты
При выполнении слесарно-сборочных работ, для контроля используют следующие измерительные средства:
– инструменты общего назначения (метры, линейки, угольники, рулетки);
– инструменты повышенной точности (штангенинструмент, микрометрический инструмент, индикаторный инструмент, калибры и скобы);
– особо точные меры;
– специальные инструменты (шаблоны, контрольные оправки);
– измерительные приборы и приспособления;
– средства автоматического контроля (контрольно-измерительные машины (КИМ) и контрольно-сортировочные автоматы (КСА)).
Применение нужного инструмента зависит от типа производства и особенностей конструкции изделия.
Сейчас наиболее широко применяют инструменты повышенной точности и общего назначения. Для изменения линейных размеров применяют линейки, рулетки, штангенциркули, штангенглубиномеры, штангенрейсмусы, микрометры, глубиномеры микрометрические, нутромеры микрометрические, индикаторные глубиномеры, измерительные головки высокой точности, оптические и пневматические приборы.
Метрологическая экспертиза и метрологическая проработка технической документации
2.1 Метрологическая экспертиза
Метрологическая экспертиза технической документации – это анализ и оценка технических решений в части метрологического обеспечения (технических решений по выбору измеряемых параметров, установлению требований к точности измерений, выбору методов и средств измерений, их метрологическому обслуживанию).
Метрологическая экспертиза – часть комплекса работ по метрологическому обеспечению и может являться частью технической экспертизы конструкторской, технологической и проектной документации.
Общая цель метрологической экспертизы – обеспечение эффективности метрологического обеспечения, выполнение общих и конкретных требований к метрологическому обеспечению наиболее рациональными методами и средствами.
Конкретные цели метрологической экспертизы определяются назначением и содержанием экспертируемой технической документации. Например, конкретной целью метрологической экспертизы чертежей простейших деталей может быть обеспечение достоверности измерительного контроля с оптимальными значениями вероятностей брака контроля 1-го и 2-го рода.
В ранее действовавшем нормативном документе МИ 1325 – 86 «Методические указания. ГСИ. Метрологическая экспертиза конструкторской и технологической документации. Основные положения и задачи» определение было несколько иным: метрологическая экспертиза – анализ и оценка технических решений по выбору параметров, подлежащих измерению, установлению норм точности измерений и обеспечению методами и средствами измерений процессов разработки, изготовления, испытания и применения продукции.
Сопоставление определений показывает, что в новом НД упор сделан на метрологическое обеспечение, что не совсем корректно. Хотя результаты метрологической экспертизы могут быть использованы для организации метрологического обеспечения, экспертиза и метрологическое обеспечение – два разных вида работ. Метрологическое обеспечение – значительно более широкое понятие, по необходимости включающее в себя метрологическую экспертизу множества объектов (изделий, технологических процессов, процессов измерительного контроля, поверки средств измерений и др.).
Дата добавления: 2021-12-10; просмотров: 33; Мы поможем в написании вашей работы! |
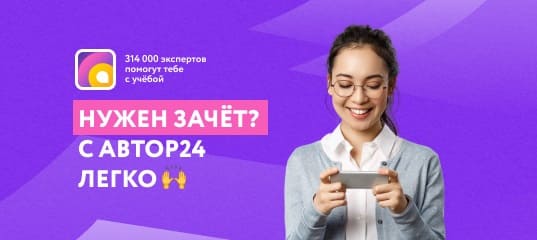
Мы поможем в написании ваших работ!