Режущее и пластифицирующее действие.
Введение
1.1. Значимость науки о резании металлов
Обработка резанием является основным технологическим способом изготовления деталей машин и механизмов. Трудоемкость механосборочного производства в большинстве отраслей машиностроения значительно превышает трудоемкость литейных, ковочных и штамповочных процессов, взятых вместе. Обработка резанием имеет достаточно высокую производительность и отличается высокой точностью. Нужно также учитывать универсальность и гибкость обработки резанием, обеспечивающие ее преимущество перед другими методами формообразования, особенно в индивидуальном и мелкосерийном производствах.
В настоящее время совершенствуется заготовительное производство, развиваются методы обработки без снятия стружки. Это приводит к уменьшению припусков под обработку резанием, изменяется качественный состав операций: уменьшается объем простых высокопроизводительных обдирочных операций и увеличивается объем сложных трудоемких финишных операций. Однако значительного сокращения объема обработки конструкционных материалов резанием не происходит по причине усложнения конструктивных форм деталей и ужесточения требований к точности и качеству их изготовления.
В авиационной промышленности широкое применение находят труднообрабатываемые конструкционные материалы (высокопрочные, жаростойкие и жаропрочные стали и сплавы), имеющие низкую обрабатываемость резанием, что также повышает трудозатраты при обработке. Совершенствование существующих и создание новых методов и практических приемов обработки металлов резанием невозможно без использования достижений науки о резании металлов, которая является базой для этой отрасли технологии машиностроения. При проектировании технологического процесса изготовления деталей необходимо оценить эффективность созданного процесса, показателями которой являются качество изготовляемых деталей, надежность функционирования процесса и его производительность и себестоимость.
|
|
Если не опираться на теоретические основы процесса резания металлов, то невозможно ни спроектировать научно обоснованный технологический процесс, ни дать оценку его эффективности. Производительность и себестоимость технологического процесса определяются временем, которое затрачивается на выполнение отдельных операций, и зависит от установленных на них режимов резания. Сознательное назначение режима резания невозможно без знания основных законов производительного резания, базирующихся на процессах, происходящих в зоне деформации и на контактных поверхностях инструмента.
|
|
Качество выпускаемых деталей определяется точностью их геометрических форм и шероховатостью обработанной поверхности. При определенной жесткости детали макрогеометрические погрешности формы зависят от величины и направления сил, действующих в процессе обработки. Таким образом, при точностных расчетах, базирующихся на жесткости технологической системы СПИД (станок — приспособление — инструмент — деталь), нужно уметь определять силы резания и знать, от чего зависят их величины и направления действия. Погрешности формы детали, вызванные разогреванием детали и инструмента, можно рассчитать, зная температуру детали и инструмента, для чего необходимо иметь сведения о тепловых явлениях, сопутствующих превращению срезаемого слоя в стружку. Надежность функционирования технологического процесса определяется возможными отказами по точности обработки и стойкости инструмента. Анализ возникновения отказов и установление путей их устранения возможны на основании изучения характера изнашивания инструментов и статистической теории их стойкости.
Проектирование металлорежущих инструментов начинается с выбора геометрических параметров: переднего и заднего углов, углов в плане, угла наклона винтовой канавки и т. д. Оптимальные величины указанных углов, при которых период стойкости инструмента максимален, определяются физическими процессами, происходящими на контактных поверхностях инструмента, без знания которых невозможно дать научно обоснованных рекомендаций по установлению численной величины оптимальных углов. Для повышения долговечности инструмента большое значение имеет правильный выбор инструментального материала в зависимости от рода обрабатываемого материала и условий работы. Поскольку износостойкость, пластическая и хрупкая прочности инструмента зависят от особенностей контактирования пары — материал инструмента и обрабатываемый материал и величины и распределения контактных напряжений, то выбор материала инструмента производят на основании изученных закономерностей контактных процессов. Для установления критерия затупления при эксплуатации инструментов и величины допустимого износа необходимо знать физическую природу и количественные закономерности изнашивания.
|
|
При проектировании металлорежущих станков задают диапазоны изменения подачи, числа оборотов шпинделя и эффективную мощность станка. Выбор этих параметров производят на основе рациональных режимов резания при одноинструментальной и многоинструментальной обработке. Расчеты на прочность, жесткость и долговечность отдельных деталей и узлов станка, на виброустойчивость станка осуществляют, используя силовые и динамические закономерности процесса резания. Эти закономерности также нужны при проектировании адаптивных систем.
|
|
1.2. Развитие науки о резании металлов
Первые экспериментальные исследования процесса резания металлов проведены во Франции. В 1848—1849 годах капитан французской артиллерии Кокилья проделал опыты по сверлению отверстий в орудийных стволах. Подача сверла осуществлялась с помощью груза. В опытах определялась работа, затрачиваемая на сверление.
В 1851 году Коквилхэт исследовал работу, необходимую для сверления отверстий в железе, бронзе, камне и других материалах. В 1862 году опыты Кокилья повторил капитан французской артиллерии Кларинваль на отличающихся по своим свойствам обрабатываемых материалах: чугуне, стали и бронзе. В 1864 году французский исследователь Джоссель сделал сообщение о влиянии геометрии резца на силу резания.
В конце 70-х годов 19-ого века интенсивно развиваются науки о строении и свойствах металлов. Так, в 1968 году Д.К.Чернов исследует строение металлов и закладывает основы металлургии, в том же году французский академик Треска публикует первые работы по пластической деформации металлов.
В 1780 году наш соотечественник Иван Августович Тиме (1838-1920), профессор Петербургского Горного Института, публикует труд «Сопротивление металлов и дерева резанию», в котором он «… впервые рассмотрел процесс деформации металла при стружкообразовании». Этот труд и считается началом науки о резании металлов, а его автор, Иван Августович Тиме — ее основоположником.
В 1893 году вышла в свет книга профессора Харьковского Технологического Института Константина Алексеевича Зворыкина(1861-1928) «Работа и усилие, необходимые для отделения металлических стружек». Эта работа явилась ценным вкладом в мировую техническую литературу и поставила К.А.Зворыкина в ряд крупнейших ученых- основоположников науки о резании металлов. За свое исследование, описанное в этой книге, К.А.Зворыкин был удостоен премии Русского технического общества. В своем исследовании для измерения усилий он впервые применил гидравлический динамометр. Методика изложенного исследования была настолько совершенна и тщательно продумана, что от современных исследований она отличается только технической оснащенностью. К.А.Зворыкиным была предложена схема сил, действующих на резец, в которой были учтены силы трения на передней и задней поверхностях. К.А.Зворыкин теоретически определил положение плоскости скалывания и высказал предположение, что в плоскости скалывания действуют нормальные силы, вызывающие силы трения между элементами стружки, препятствующие их движению. Значительная часть работы посвящена исследованию зависимости сил резания от толщины стружки.
В 1896 году опубликована работа преподавателя Михайловской артиллерийской академии, капитана А.А. Брикса «Резание металлов». В своей книге автор дал глубокий анализ работ отечественных и зарубежных исследователей, систематизировал понятия и уточнил терминологию, принятую в резании. Такие термины, как «режущее лезвие», «передняя грань», «задняя грань», «угол заострения», «задний угол», «передний угол» утвердились в науке о резании металлов и сохранились до наших дней.
В 1905-1910 годах – Н.Н. Савиным выполнены исследования влияния смазочно-охлаждающей жидкости на процесс резания и качество обработанной поверхности. Результаты исследования опубликованы в «Известиях СПБ Политехнического института» и в «Вестнике общества технологов» в 1910 году.
В 1914 году в «Известиях Донского политехнического института» была опубликована работа Б.Г. Соколова «О форме обдирочных резцов». В этой работе автор обращает внимание на то, что процесс образования стружки следует рассматривать в плоскости «схода стружки», которую в настоящее время мы называем главной секущей плоскостью.
Выдающейся работой после работ И.А. Тиме и К.А. Зворыкина была работа мастера механических мастерских Петроградского политехнического института Якова Григорьевича Усачева (1873-1941) «Явления, происходящие при резании металлов». Для изучения пластической деформации в зоне образования стружки Я.Г. Усачев впервые применил микроструктурный анализ корней стружек, позволивший увидеть плоскости скалывания и плоскости сдвигов внутри элементов стружки. При микроструктурном анализе корней стружек Я.Г. Усачев обратил внимание на явление образования нароста на передней поверхности резца, которое он охарактеризовал как явление приспособляемости металла к условиям резания и указал, что «…нарост образуется всегда, если форма резца не соответствует условиям наименьшего сопротивления резанию...».
Я.Г. Усачев был выдающимся экспериментатором и большим мастером своего дела, опубликованные им фотографии микроструктур корней стружек и нароста, удивляют исключительно высоким качеством их выполнения, собственноручно им изготовленные и применяемые в экспериментах резцы со встроенными полуискуственными термопарами, являют собой образцы ювелирного их исполнения.
Начало работам советского послереволюционного периода времени было положено Андреем Николаевичем Челюсткиным (1891-1926), преподавателем Ленинградской артиллерийской академии. За 7 лет своей научно-педагогической работы он опубликовал целый ряд сочинений, сыгравших большую роль в развитии отечественной науки о резании металлов.
Особое место среди его работ занимает сочинение «Влияние размеров стружки на усилие резания металлов».
В годы первой пятилетки 1928-1933 в нашей стране развернулось широкое строительство новых предприятий тяжелой индустрии и реконструкция существующих машиностроительных заводов. В этот период строятся такие гиганты нашей индустрии, как Горьковский Автозавод, Сталинградский, Харьковский и Челябинский тракторные заводы, авиационные заводы в Москве, Воронеже и в Горьком, Уралмаш, Ново-Краматорский завод тяжелого машиностроения и другие.
Резкое расширение парка металлорежущих станков и увеличение объема металлообработки потребовало создания научно-обоснованных руководящих материалов по рациональному использованию имеющихся мощностей, выбору оптимальных режимов резания и условий обработки.
Развитие массового производства требовало освоения высокопроизводительных методов обработки металлов с применением специализированных инструментов.
Эти задачи в целом потребовали расширения научно-исследовательских работ в металлообработке. Поэтому в 1936 году по инициативе Наркома тяжелой промышленности СССР Григория Константиновича Орджоникидзе была создана «Комиссия по резанию металлов» под председательством профессора МВТУ имени Н.Э.Баумана, Е.П. Надеинской. Членами комиссии стали А.И. Каширин, В.А. Кривоухов, И.М. Беспрозванный и С.Д. Тишин. На основании работ, выполненных под руководством комиссии, впервые в мировой практике металлообработки разработаны справочные материалы по режимам резания всех применявшихся в то время конструкционных материалов и всех видов обработки всеми видами инструмента.
Эти материалы были положены в основу государственных нормативов по режимам резания.
В результате работ Комиссии были прочно заложены основы Советской школы резания металлов. Впервые в мировой практике созданы нормативно-справочные материалы по резанию металлов.
В период Великой Отечественной Войны проведены широкие исследования, направленные на определение режимов резания максимальной производительности.
Послевоенный период характеризуется глубокими исследованиями накопившихся за время войны узких вопросов по теории резания металлов.
Результаты исследований опубликованы авторами:
1945 г. — В.А. Кривоуховым «Деформирование поверхностных слоев металла в процессе резания».
1946 г. — И.М. Беспрозванным «Физические основы теории резания металлов».
1949 г. — С.Ф. Глебовым «Механизм пластической деформации при резании металлов».
1950 г. — А.И. Исаевым «Процесс образования поверхностного слоя при обработке металлов резанием».
1953 и 1958 г. — опубликованы две монографии М.И. Клушина «Резание металлов».
По вопросам тепловых явлений и износа режущего инструмента опубликованы работы:
1946 г. — А.М. Даниеляна «Износ инструмента и тепловые явления при резании металлов».
1949 г. — Б.И. Костецкого «Стойкость режущего инструмента».
1949 г. — М.П. Левицкого «Проблема стойкости резцов».
Наряду с теоретическими исследованиями в послевоенный период решаются и новые практические задачи. В этот период осваивается производство новых мощных турбин, атомных реакторов, реактивных двигателей. Детали этих устройств, работающие в условиях действия высоких температур и давлений, изготавливаются из специальных жаропрочных, нержавеющих, эрозионно-стойких и тугоплавких материалов и сплавов, которые трудно поддаются механической обработке. Работы послевоенного периода и были направлены на определение оптимальных условий обработки таких материалов. В 1947 году интенсивно внедряется скоростное резание твердосплавными инструментами.
Современное состояние науки о резании металлов характеризуется глубокими исследованиями физико-химических явлений в зоне резания, исследуются процессы взаимодействия обрабатываемого материала и инструмента, новые инструментальные материалы, исследуется сверхскоростное резание.
Повышение быстроходности и надежности машин потребовало повышения точности обработки и улучшения качества обработанной поверхности. В связи с этим расширились работы по исследованию размерной стойкости инструмента, большое число работ посвящено исследованию внутренних напряжений в поверхностном слое обрабатываемой детали и исследованию влияния различных технологических факторов на усталостную прочность обрабатываемых деталей.
Необходимо отметить, что в настоящее время обнаруживается несоответствие возможностей металлургической промышленности и металлообработки. Металлургическая промышленность может поставлять нашей промышленности материалы высочайшей прочности, обрабатывать которые обработчики еще не научились и обработка их стоит непомерно дорого. И в этом направлении ведутся исследовательские работы.
2. Общие сведения о резании металлов
2.1. Резание как технологический способ обработки
Сущность технологии изготовления деталей машин состоит в последовательном использовании различных технологических способов воздействия на обрабатываемую заготовку с целью придания ей заданной формы и размеров требуемой точности. Одним из таких способов является механическая обработка заготовок резанием. Она осуществляется металлорежущим инструментом и ведется на металлорежущих станках.
Обработка металлов резанием основана на срезании лезвийным или абразивным режущим инструментом с поверхностей заготовки слоя материала для получения необходимой геометрической формы, точности размеров, взаиморасположения и шероховатости поверхностей детали. Слой материала, срезаемый с заготовки, называют припуском. Припуск может удаляться одновременно с нескольких поверхностей заготовки или последовательно друг за другом с каждой обрабатываемой поверхности. В ряде случаев припуск может быть настолько большим, что его срезают не сразу, а за несколько проходов. После срезания с заготовки всего припуска, оставленного на обработку, заготовка прекращает свое существование и превращается в готовую деталь.
Металл, удаляемый в процессе резания с заготовки, подвергается пластическому деформированию и разрушению. В результате этого материал припуска, отделенный от обрабатываемой заготовки, приобретает характерную форму и в таком виде его принято называть стружкой. Срезанная с заготовки стружка является побочным продуктом — отходом обработки металлов резанием. Пластическое деформирование и разрушение материала припуска с превращением его в стружку протекает при резании в специфических условиях. Это предопределяет и специфические закономерности процесса, отражаемые функциональными зависимостями, справедливыми только для обработки металлов резанием. Таким образом, характерным признаком обработки металлов резанием является стружка. Все способы и виды обработки металлов, основанные на срезании припуска и превращении его в стружку, составляют разновидности, определяемые термином «резание металлов». Все разновидности резания подчиняются общим закономерностям. Способы разделения металлов на части, при которых стружка не образуется, например разрезка ножницами, к обработке резанием не относится. Условия деформирования обрабатываемого металла и образования новых поверхностей при разрезке ножницами не подчиняются закономерностям теории резания металлов.
2.2.Элементы резания
Рабочий процесс резания возможен только при непрерывном относительном перемещении обрабатываемой заготовки и лезвий режущего инструмента. Для осуществления процесса резания необходимо и достаточно иметь одно взаимное перемещение детали и инструмента. Однако для обработки поверхности одного взаимного перемещения, как правило, недостаточно. В этом случае бывает необходимо иметь два или более, взаимосвязанных движений обрабатываемой детали и инструмента. Совокупность нескольких движений инструмента и обрабатываемой детали и обеспечивает получение поверхности требуемой формы. Кинематика станков основана на пользовании механизмов, сообщающим исполнительным органам станка только два простейших движения – вращательное и поступательное. Сочетания и количественные соотношения этих двух движений определяют все известные виды обработки металлов резанием. В зависимости от числа и характера сочетаемых движений принципиальные кинематические схемы могут быть разделены на восемь групп:
1) одно прямолинейное движение (строгание);
2) два прямолинейных движения;
3) одно вращательное движение;
4) одно вращательное и одно прямолинейное движения (точение, сверление, зенкерование, развертывание);
5) два вращательных движения;
6) два прямолинейных и одно вращательное движения;
7) два вращательных и одно прямолинейное движения;
8) три вращательных движения.
Наибольшее распространение получили первая и четвертая кинематические схемы.
При этом движение с наибольшей скоростью называется главным движением (Dг) или движением резания, а все остальные движения являются вспомогательными и называются движениями подачи (Ds) (рисунок 1). Движение подачи необходимо при осуществлении главного движения для обеспечения врезания лезвий инструмента в материал заготовки и отделения срезаемого слоя в виде стружки по всей обрабатываемой поверхности. Суммарное движение режущего инструмента относительно заготовки, включающее главное движение и движение подачи, называется результирующим движением резания (De).
Рисунок 1 – Движения и поверхности при резании
В процессе срезания припуска на заготовке различают характерные поверхности (рисунок 1):
· обрабатываемую – поверхность, срезаемую в результате снятия припуска;
· обработанную – поверхность, образующуюся на заготовке в результате снятия припуска;
· поверхность резания – промежуточную поверхность, временно существующую в процессе резания между обрабатываемой и обработанной поверхностями.
Интенсивность процесса резания определяется напряженностью режима резания. Режим резания характеризуют три параметра:
- глубина резания t;
- подача s;
- скорость резания v.
Элементы режима резания: глубина подача и скорость, обозначаются строчными (малыми) буквами латинского алфавита.
Глубиной резания называется толщина слоя обрабатываемого материала, срезаемого за один проход инструмента.
Подачей называется величина перемещения инструмента или обрабатываемого изделия в единицу времени или величина этого перемещения, отнесенная к величине главного движения.
Скоростью резания называется скорость перемещения поверхности резания относительно режущей кромки инструмента. Скорость резания может сообщаться как режущему инструменту, так и обрабатываемой заготовке. Скорость резания можно представить как путь, пройденный режущим инструментом в единицу времени в направлении главного движения по поверхности резания.
Величина подачи и глубины резания определяют размер площади поперечного сечения срезаемого слоя (сечения среза) (рисунок 2). Процесс пластической деформации срезаемого слоя и напряженность процесса резания наиболее полно оценивается не величиной площади поперечного сечения среза, а величинами ширины и толщины поперечного сечения срезаемого слоя (рисунок 2).
Толщиной срезаемого слоя (среза) a1 называется расстояние между двумя последовательными положениями поверхности резания.
Шириной срезаемого слоя b1 называется расстояние между обрабатываемой и обработанной поверхностями, измеренное по поверхности резания.
Рисунок 2 – Сечение срезаемого слоя
Форма поперечного сечения среза зависит от формы режущей кромки инструмента и от расположения ее относительно направления движения подачи. При резании инструментом с прямолинейной режущей кромкой толщина среза а1 постоянна на всей ширине среза, а при резании инструментом с криволинейной режущей кромкой толщина среза неодинакова в разных точках по ширине среза.
При постоянных значениях подачи s и глубины резания t ширина среза b и толщина среза a изменяются в зависимости от угла j:
2.3. Конструктивные элементы режущего инструмента
Для того, чтобы режущий инструмент мог осуществлять процесс резания, его режущая часть должна быть очерчена определенными поверхностями. Рассмотрим их на примере наиболее распространенного режущего инструмента – резца.
Токарные резцы (рисунок 3) и металлорежущие инструменты всех других видов имеют присоединительную часть (участок l2) в виде державки или корпуса, а также режущую часть (головку) (участок l1), с помощью которой осуществляется процесс срезания стружки.
Режущая часть состоит из одного или нескольких конструктивно обособленных режущих элементов (зубьев), которые могут работать одновременно или последовательно, непрерывно или с перерывами, вступая в работу друг за другом.
Каждый режущий элемент имеет переднюю поверхность и одну или несколько задних поверхностей, из которых одна называется главной задней поверхностью, а остальные — вспомогательными задними поверхностями.
Передней поверхностью 1 (рисунок 3) называется поверхность, по которой сходит образующаяся в процессе резания стружка.
Главная задняя поверхность 2 – поверхность, обращенная к поверхности резания.
Вспомогательная задняя поверхность 3 (рисунок 3) – это поверхность, обращенная к обработанной поверхности. Передняя и задняя поверхности ограничивают материальное тело каждого элемента режущей части инструмента.
Передняя и главная задняя поверхности, взаимно пересекаясь, образуют главную режущую кромку 4. Вспомогательная режущая кромка 5 образована пересечением передней и вспомогательной задней поверхности.
Точка пересечения главной и вспомогательной режущих кромок носит название вершины режущей части 6.
Рисунок 3 – Конструктивные элементы режущей части резца
Положение передних и задних поверхностей, главных и вспомогательных режущих кромок, образующих режущие элементы (зубья), координируется относительно корпуса инструмента системой угловых размеров, называемых геометрическими параметрами. Конкретные числовые значения геометрических параметров проставляются на рабочих чертежах инструментов таким образом, чтобы по ним можно было, во-первых, изготовить режущие элементы (зубья) заданной формы и, во-вторых, проверить точность изготовления всех углов универсальными или специальными контрольно-измерительными инструментами и приборами.
2.4. Геометрические параметры режущей части инструмента
Для определения геометрических параметров режущих инструментов устанавливают три координатных плоскости: основную, рабочую и плоскость резания.
Основная плоскость P v – координатная плоскость, проходящая перпендикулярно направлению главного движения (вектору скорости резания). Для случая токарной обработки она параллельна продольной и поперечной подачам и параллельна опорной поверхности (основанию) призматической зажимной части резца.
Плоскостью резания P n называется координатная плоскость, проходящая через главную режущую кромку перпендикулярно основной плоскости.
Рабочая плоскость Ps. – плоскость, проходящая через главную режущую кромку перпендикулярно основной плоскости и параллельно направлению движения подачи
Геометрические параметры режущего инструмента рассматриваются в плане, то есть в проекции на основную плоскость, и в секущих плоскостях: главной секущей плоскости, нормальной секущей плоскости, в рабочей плоскости и в других вспомогательных секущих плоскостях.
Нормальной секущей плоскостью Pn называется секущая плоскость, проходящая перпендикулярно (нормально) режущей кромке в рассматриваемой точке.
Главной секущей плоскостью Р t называется координатная плоскость, перпендикулярная линии пересечения основной плоскости с плоскостью резания и проходящая через главную режущую кромку.
Для определения геометрических параметров режущей части инструментов используют прямоугольные системы координат трех видов:
· инструментальную систему координат (ИСК) – прямоугольную систему координат, определяемую по отношению к основной плоскости (установочной базе);
· статическую систему координат (ССК) – прямоугольную систему координат с началом в рассматриваемой точке режущей кромки, ориентированную относительно плоскости резания;
· кинематическую систему координат (КСК) – прямоугольную систему координат с началом в рассматриваемой точке режущей кромки, ориентированную относительно направления скорости результирующего движения резания.
Геометрические параметры (углы) режущего инструмента рассматриваются в этих системах координат. В статической – как геометрические параметры твердого тела – неподвижного предмета, в кинематической – как углы работающего инструмента в процессе резания.
Рассмотрим геометрические параметры, присущие режущим элементам различных инструментов, в статической системе координат на примере проходного токарного резца (рисунок 4).
Главным углом в плане j называется угол, измеряемый в опорной плоскости между проекцией на нее вектора скорости подачи и проекцией главной режущей кромки.
Вспомогательным углом в плане j1 называется угол, измеряемый в опорной плоскости между проекцией на нее вспомогательной режущей кромки и линией, на которой лежит вектор скорости подачи.
Угол при вершине резца в плане e - угол между главной и вспомогательной режущими кромками:
.
Рисунок 4 – Геометрические параметры режущей части резца в статической системе координат
Главная режущая кромка может быть параллельна или наклонена под некоторым углом к опорной плоскости.
Угол наклона главной режущей кромки l измеряется между главной режущей кромкой и горизонтальной плоскостью, проходящей через вершину режущей части.
Углы j и l , однозначно определяют положение в пространстве главной режущей кромки. В свою очередь, она, как линия, принадлежащая передней и главной задней поверхностям, определяет положение их в пространстве. Чтобы полностью задать положение передней и главной задней поверхностей на чертежах токарных резцов, необходимо для каждой из них задать еще по одному угловому параметру. Для передней поверхности — это передний угол g, а для главной задней поверхности — главный задний угол a.
Передний угол g и главный задний угол a измеряются в сечении режущей части резца вертикальной главной секущей плоскостью, перпендикулярной проекции главной режущей кромки на опорную плоскость.
Передний угол g измеряется в главной секущей плоскости между линиями пересечения ее с передней поверхностью и горизонтальной плоскостью.
Главный задний угол a измеряется в главной секущей плоскости между линиями пересечения ее с главной задней поверхностью и вертикальной плоскостью.
Положение передней поверхности относительно главной задней поверхности определяет форму клина режущей части и может быть охарактеризовано углом заострения b (рисунок 4), который измеряется в главной секущей плоскости между линиями пересечения ее с передней и главной задней поверхностями.
Таким образом, согласно данным выше определениям, a + b + g = 90°, а при заданных a и g угол заострения b = 90° - (a + g).
Положение передней поверхности и угол j1 (рисунок 4) однозначно определяют положение вспомогательной режущей кромки. Для полного определения положения вспомогательной задней поверхности используют вспомогательный задний угол a1, лежащий в сечении режущей части резца вспомогательной секущей плоскостью, перпендикулярной проекции вспомогательной режущей кромки на горизонтальную координатную плоскость.
Вспомогательный задний угол a1 измеряется во вспомогательной секущей плоскости между линиями пересечения ее вспомогательной задней поверхностью и вертикальной плоскостью.
Кроме рассмотрения углов резца в статической системе координат как углов какого-то геометрического тела (или углов резца в статике) следует рассматривать углы резца в движении, в кинематической системе координат. В результате сложения главного движения с движением подачи при резании изменяется величина углов режущего инструмента, приданных ему при заточке.
Углы в статической системе координат называются статическими углами, углы в кинематической системе координат – кинематическими. Величина кинематических углов отличается от величины статических на величину кинематического угла скорости резания h, угла между векторами скорости резания v и скорости результирующего движения vе. (рисунок 5).
При резании задний угол уменьшается, а передний увеличивается на величину угла скорости резания:
Величина этого кинематического угла легко определяется из схемы на рисунке 6, где резец условно показан в контакте с разверткой обрабатываемой торцевой поверхности на цилиндрической заготовке. Здесь видно, что:
где d – диаметр обрабатываемой поверхности, мм; s – величина подачи, мм/об.
Рисунок 5 – Связь между статическими и динамическими углами резца
Рисунок 6 – Определение угла скорости резания
3. Стружкообразование при резании
3.1. Физическая сущность процесса стружкообразования
Процессы резания по своей физической сущности являются процессами с протеканием упругих и пластических деформаций в снимаемом припуске и поверхностном слое заготовки.
Согласно теории элементного стружкообразования стружка представляется в виде элементов стружки. При этом каждый элемент стружки образуется в 2 этапа
1) Под сжимающим воздействием резца металл снимаемого припуска начинает пластически течь и заплывает на переднюю поверхность инструмента (рисунок 7, а).
2) При дальнейшем сжатии металла касательные напряжения начинают концентрироваться вблизи некоторой плоскости АВ (рисунок 7, б). Когда максимальные напряжения превысят предел прочности металла на срез, происходит мгновенный пластический сдвиг элементов металла вдоль плоскости АВ (рисунок 7, б).
а
б
АВ – условная плоскость сдвига,
b1 – угол наклона этой плоскости к вектору скорости резания
Рисунок 7 – Процесс образования стружки
Все последующие элементы стружки образуются также. Данная теория стружкообразования является общепризнанной в России и за рубежом. Она находит подтверждение в типах стружки, которые образуются при резании (элементная, суставчатая (гофрированная), сливная, циклическая).
Процесс образования стружки согласно рассматриваемой теории характеризуют следующие параметры.
1. Угол наклона условной плоскости сдвига (угол сдвига):
, (формула профессора Зворыкина),
где g - передний угол режущего инструмента,
h - угол трения стружки о переднюю поверхность инструмента (рисунок 8).
Рисунок 8 – Определения угла трения
На переднюю поверхность инструмента при резании действуют сила трения F и нормальная сила N. Эти силы определяют силу стружкообразования R (рисунок 8). Силы Rz и Ry являются, соответственно горизонтальной (тангенциальной) и вертикальной (радиальной) составляющими силы R . Так как сила сдвига Rc является проекцией равнодействующей силы R на условную плоскость сдвига АВ, то угол между силами Rz и Rc равен углу наклона условной плоскости сдвига b1.
. Из теории сопротивления материалов известно, что сила сжатия образца вызывает его разрушение по плоскости максимальных напряжений т—т, расположенной под углом 45° к линии ее действия (рисунок 9).
Рисунок 9 – Схема разрушения
Сила стружкообразования R при резании также вызывает значительное сжатие и упруго-пластическое деформирование металла снимаемого припуска с последующим пластическим сдвигом (разрушение) образующихся элементов стружки. Следовательно, можно в первом приближении принять допущение о том, что сила R всегда должна составлять
с условной плоскостью сдвига АВ (с силой Rc ) угол, равный 45°;
с силой Rz угол (45° – b1);
силой F угол (90° – g) – (45° – b1) = 45° + (b1 – g).
Из рисунка 8 видно, что
.
В тоже время сила трения F может быть определена через коэффициент трения m и нормальную силу N:
.
Следовательно:
.
2. Длина плоскости сдвига:
.
3. Площадь плоскости сдвига:
.
Поскольку , получим
.
Данная формула показывает, что площадь плоскости сдвига тем больше, чем больше значения подачи и глубины резания и чем меньше угол наклона условной плоскости сдвига.
4. Сила сдвига отдельных элементов стружки R с .
Она определяется произведением сопротивления материала пластическому сдвигу tр на площадь плоскости сдвига:
.
5. Скорость деформации металла при резании.
Она определяется скоростью резания:
, м/мин,
где D – диаметр обрабатываемой поверхности,
n – частота вращения заготовки, об/мин.
3.2. Классификация стружек
Срезаемые стружки имеют различные вид и форму, зависящие от химического состава, структурного состояния и механических свойств обрабатываемых металлов, толщины срезаемого слоя, значения переднего угла инструмента, скорости резания и прочих менее влияющих факторов. И. А. Тиме разделил все виды стружки по внешнему виду и строению на три основных типа.
1. Стружка скалывания.
Стружки, состоящие из пластически деформированных и взаимно сдвинутых элементов, достаточно прочно соединенных по плоскостям скалывания называются стружками скалывания. Стружки скалывания образуются при обработке сталей пониженной пластичности и при больших толщинах срезаемого слоя. Образование стружки скалывания происходит также при средних значениях используемых в производственных условиях передних углов и скоростей резания. Внешний вид стружки скалывания показан на рисунке 10. На рисунке 11 представлена микрофотография корня стружки скалывания в главной секущей плоскости. В технической литературе, изданной в более позднее время, встречается также название элементная стружка. С изменением условий резания стружка скалывания может перейти в сливную и наоборот.
![]() | ![]() |
Сливная стружка.
При резании пластичных металлов с большими скоростями резания резцами с большими передними углами и при срезании слоя металла средних и малых толщин пластическая деформация протекает более равномерно и связанные с ней внутренние напряжения тоже распределяются более равномерно по всему деформируемому объему. Следовательно, отсутствуют условия для периодически повторяющихся через равные интервалы рабочего пути резца нарастаний напряжений, приводящих к образованию стружки скалывания. Материал срезаемого слоя подвергается равномерной пластической деформации на всем пути рабочего движения резца. Срезаемая стружка имеет вид непрерывной ленты, на верхней и обеих боковых сторонах которой видны следы пластической деформации в виде мелких заостренных выступов. Стружки такого типа называются сливными (рисунки 12, 13).
Рисунок 12 – Сливная стружка (схема)
Рисунок 13 – Микрофотография корня сливной стружки, полученного при резании стали 40Х
Рисунки 11 и 13 показывают, что в стружке скалывания четко видны ее отдельные элементы, а в сливной стружке отдельные элементы трудно различимы
Стружки скалывания и сливные формируются при резании относительно пластичных материалов — сталей, латуней, алюминиевых сплавов. Скользя по передней поверхности инструмента, стружки изгибаются и образуют винтовые витки большего или меньшего диаметра. При резании хрупких металлов, таких, как чугуны и бронзы, образование стружек скалывания и сливных практически не наблюдается.
Стружка надлома.
Хрупкие металлы под действием силы, развиваемой лезвием резца, надламываются и разрушаются, образуя мелкие осколки самых разнообразных форм и размеров, полностью отделенные друг от друга.
При обработке хрупких металлов резец, внедряясь в металл, не сдвигает его, а сжимает, и вырывает сжатый надломленный элемент, образуя мелкие осколки самых разнообразных форм и размеров, полностью отделенные друг от друга. Только в благоприятных спокойных условиях резания они могут на некоторое время сохранить взаимно упорядоченное положение благодаря механическому сцеплению неровностей. При слабом силовом воздействии это механическое сцепление легко нарушается и стружка, имевшая вид, схожий со сливной стружкой, рассыпается на отдельные кусочки. Стружки такого типа называются стружками надлома и внешний вид их показан на рисунке 14. Разрушение идет по поверхности, произвольно охватывающей напряженную зону, поэтому обработанная поверхность получается неровной.
Рисунок 14 – Стружка надлома (схема)
Стружку скалывания и сливную стружку иногда называют стружками сдвига, т.к. их образование связано с напряжениями сдвига. Стружку надлома иногда называют стружкой отрыва, т.к. ее образование связано с растягивающими напряжениями.
Тип стружки во многом зависит от рода и механических свойств обрабатываемого материала. При резании пластичных материалов возможно образование стружки скалывания и сливной стружки. По мере увеличения твердости и прочности обрабатываемого материала сливная стружка переходит в стружку скалывания. При обработке хрупких материалов образуется или стружка скалывания (чаще), или стружка надлома (реже). С повышением твердости материала, например чугуна, стружка скалывания переходит в стружку надлома.
Из геометрических параметров инструмента наиболее сильно на тип стружки влияют передний угол g и угол наклона главного лезвия l. При обработке пластичных материалов влияние данных углов принципиально одинаково: по мере их увеличения стружка скалывания переходит в сливную. При резании хрупких материалов при больших передних углах может образовываться стружка надлома, которая по мере уменьшения переднего угла переходит в стружку надлома. При увеличении угла наклона главного лезвия стружка постепенно превращается в стружку скалывания.
На тип стружки оказывают влияние подача (толщина срезаемого слоя) и скорость резания. Глубина резания (ширина срезаемого слоя) на тип стружки практически не влияет. Увеличение подачи (толщины срезаемого слоя) приводит при резании пластичных материалов к последовательному переходу от сливной стружки к стружки скалывания. При резании хрупких материалов с увеличением подачи стружка скалывания переходит в стружку надлома.
Наиболее сложно на тип стружки влияет скорость резания. При резании большинства углеродистых и легированных конструкционных сталей, если исключить зону скоростей резания, при которых образуется нарост, по мере увеличения скорости резания стружка из стружки скалывания постепенно превращается в сливную. Однако при обработке некоторых жаропрочных сталей и сплавов, титановых сплавов повышение скорости резания, наоборот, превращает сливную стружку в стружку скалывания. Повышение скорости резания при обработке хрупких материалов сопровождается переходом стружки надлома в стружку скалывания с уменьшением размеров отдельных элементов и упрочнением связи между ними.
3.3. Усадка стружки
В результате пластических деформаций всего срезаемого слоя припуска обычно оказывается, что длина срезанной стружки короче пути, пройденного резцом. Это явление профессор И. А. Тиме назвал усадкой стружки. При укорочении стружки размеры ее поперечного сечения изменяются по сравнению с размерами поперечного сечения срезаемого слоя металла. Толщина стружки оказывается больше толщины срезаемого слоя, а ширина стружки не изменяется, лишь на прирезцовой ее стороне имеет место уширение тонкого прирезцового слоя. Этим уширением в большинстве случаев можно пренебречь, поскольку оно не распространяется на всю толщину стружки. Чем больше деформация срезаемого слоя, тем больше отличается длинна стружки от длины пути, пройденного резцом (рисунок 15).
Рисунок 15 – Усадка стружки
Количественно усадка оценивается следующими величинами:
1. Коэффициентом продольной (линейной) усадки (коэффициент усадки или укорочение):
.
2. Коэффициентом поперечной усадки (утолщение):
.
3. Коэффициентом усадки по ширине (уширение):
.
Данные коэффициенты отражают величину пластической деформации, имевшей место при резании.
Объем стружки равен объему срезаемого слоя, поэтому . Отсюда
, следовательно:
.
Величина коэффициента усадки стружки зависит от свойств обрабатываемого материала, геометрии режущего лезвия инструмента, свойств внешней среды, в которой осуществляется резание, и других факторов. Из элементов режима резания менее всего на величину коэффициента усадки, влияет глубина резания, сильнее – подача и наиболее сильно скорость резания.
Определим зависимость угла плоскости сдвига b 1 от коэффициента поперечной усадки K а и переднего угла g (рисунок 16).
AD ^ BE, BF ^ AF, a стр || BF, AD || a1
Рисунок 16 – Схема к определению угла плоскости сдвига
Из прямоугольного DFBA имеем
.
Отсюда
.
,
Отсюда
.
Это уравнение получило название уравнение Тиме.
3.4. Относительный сдвиг при резании
Усадка стружки является лишь приближенной характеристикой пластических деформаций при резании. Это подтверждает тот факт, что при Ka = 1 в металле снимаемого припуска (стружке) видны следы глубоких пластических деформаций (обнаруживаются металлографическими методами).
Поэтому в теории резания введена характеристика с названием относительный сдвиг, определяемая по формуле:
.
При Ka = 1 , а при g = 0 e = 2.
Это свидетельствует о том, что относительный сдвиг – более точная характеристика пластических деформаций при резании.
4. Наростообразование при резании
Резанию большинства конструкционных материалов при определенных условиях сопутствует явление, называемое наростообразованием.
При резании металлов срезаемый слой в результате пластического деформирования приобретает повышенную физическую активность и, будучи плотно прижатым силами нормального давления к передней поверхности режущего инструмента, схватывается (сваривается) с ней, образуя тело нароста. Схватыванию обрабатываемого материала с материалом инструмента способствуют высокая температура в зоне резания и то обстоятельство, что при резании в контакт вступают вновь образованные, физико-химически чистые, свободные от каких-либо пленок поверхности. Первоначально на поверхности контакта стружки с передней поверхностью происходят точечные контакты с образованием налипов на передней поверхности. С течением времени число таких налипов растет и они покрывают площадь контакта сплошной тонкой пленкой из обрабатываемого материала, которая называется первослоем. Поскольку этот первослой обладает абсолютным сродством с обрабатываемым материалом, схватывания между ними происходят чаще и интенсивнее с образованием более крупных наслоений. Схватывание и наслаивание микрообъемов обрабатываемого металла на переднюю поверхность инструмента приводит к образованию на ней слоя упрочненного микролегированного материала, прочно соединенного с инструментом. Процессы периодического cхватывания и последовательного наслаивания упрочненного материала стружки повторяются многократно, в результате на передней поверхности образуется новое довольно крупное тело, называемое наростом.
Таким образом, под наростом понимают клиновидную, более или менее неподвижную область материала обрабатываемой заготовки, расположенную у лезвия инструмента перед его передней поверхностью (рисунок 17).
Тело нароста состоит из:
1) сильно деформированных частиц обрабатываемого материала;
2) продуктов износа инструмента;
3) окислов элементов металлов, возникших под действием кислорода воздуха и СОТС.
Форму и размер нароста можно охарактеризовать тремя основными параметрами: высотой hн, шириной подошвы lн, и углом gн.(рисунок 17).
Рисунок 17 – Нарост и его параметры
Из представленной на рисунке 18 фотографии хорошо видно ярко выраженное слоистое строение нароста. Форма нароста зависит от свойств обрабатываемого материала, элементов режима резания и других конкретных условий обработки. Нарост состоит из основания и вершины. Вершина является неустойчивой частью нароста, она, по мере увеличения высоты нароста, разрушается и уносится из зоны стружкообразования, сходящей по ней стружкой (как это видно на рисунке 18) или поверхностью резания обрабатываемой заготовки.
Рисунок 18 – Строение нароста
Нарост не является полностью стабильным телом. Высота нароста растет до тех пор, пока его прочность становится недостаточной для восприятия нагрузки со стороны стружки, и нарост разрушается. Обычно нарост разрушается не весь, а только его верхняя, менее прочная область. Одна часть разрушенного нароста уносится стружкой, а другая – поверхностью резания. После разрушения нарост вновь возрастает до предельной для данных условия резания высоты, затем опять разрушается и т.д. Частота возникновений и срывов нароста растет с увеличением скорости резания и при v = 40…60 м/мин составляет 3000…4000 циклов в минуту.
Из параметров режима резания на интенсивность образования, размеры и форму нароста наиболее сильно влияет скорость резания. На очень малых скоростях резания нарост не удерживается на передней поверхности инструмента, из-за мелко-элементной сыпучей стружки с увеличением скорости интенсивность образования нароста возрастает лишь до какого-то значения скорости, после которого интенсивность его образования и размеры начинают уменьшаться.
На рисунке 19 представлены корни стружки, полученные, при точении стали 45 с разными скоростями резания.
Рисунок 19 – Корни стружки с наростом, полученные при точении стали 45. Скорость резания: а. — 13, б. — 28 и в. — 55 м/мин
Здесь видно, что скорость резания сильно влияет на размеры и форму нароста. Нарост наибольшей высоты образуется на скорости 13 м/мин. На скорости 28 м/мин. образуется нарост меньшей высоты и другой формы. На сравнительно большой скорости резания 55 м/мин. нароста уже почти нет. Можно предположить, что на такой скорости температура в зоне резания выше температуры «отдыха» обрабатываемого материала, под влиянием которой материал нароста разупрочняется и не может противостоять истирающему действию обрабатываемого материала.
Все материалы можно разделить на материалы:
1) не склонные к наростообразованию (медь, латунь, бронза, олово, свинец, большинство титановых сплавов, белый чугун, закаленные стали, легированные стали с большим содержанием хрома и никеля);
2) склонные к наростообразованию (конструкционные, углеродистые и большинство легированных сталей, серый чугун, алюминий, силумин).
Если материал склонен к наростообразованию, то размеры нароста возрастают при уменьшении твердости и повышении пластичности материала.
Поскольку нарост образуется из сильно деформированного металла, твердость которого намного больше твердости исходного обрабатываемого, то и нарост в целом имеет высокую твердость, в 2...3 раза превосходящую твердость обрабатываемого материала. Наличие высокой твердости позволяет наросту успешно противостоять воздействию стружки и выполнять работу самого режущего инструмента. Он служит продолжением инструмента и принимает на себя его функции.
Нарост на режущем инструменте образуется не всегда, а только в тех случаях, когда условия резания благоприятствуют этому. Необходимыми условиями существования нароста являются следующие:
1. Обрабатываемый материал должен обладать способностью упрочняться при пластическом деформировании.
2. Температура в зоне резания должна быть ниже той температуры, при которой происходит разупрочнение материала нароста.
3. Должна образовываться сливная стружка. При образовании стружек скалывания нарост не удерживается на передней поверхности вследствие прерывистости процесса резания.
4. Коэффициент трения в зоне контакта обрабатываемого материала с передней поверхностью должен быть больше единицы.
Если условия для существования нароста вполне подходящие, нарост образуется и существенно влияет на параметры процесса резания и состояние обработанной поверхности (рисунок 17). Образование нароста изменяет фактическую геометрию инструмента, передний угол увеличивается и становится больше переднего угла, приданного инструменту при его заточке (gн > g). Процесс резания происходит легче. Поверхность нароста, обращенная к стружке, становится продолжением передней поверхности инструмента. Изменение фактического угла резания вызывает изменение характера процесса образования стружки.
В случае свешивания вершины нароста над задней поверхностью инструмента изменяется фактическая толщина среза. Фактически толщина среза . Сказанное, иллюстрируется представленной на рисунке 17 схемой зоны резания с наростом и представленной на рисунке 19 фотографией нароста, полученного при резании коррозионностойкой стали 12Х18Н10Т. На ней случайно, но очень удачно запечатлен момент разрушения вершины нароста, которая уносится из зоны образования стружки с поверхностью резания.
А – часть вершины нароста на поверхности резания,
b1д – угол скалывания до разрушения нароста,
b1п – угол скалывания после разрушения нароста.
Рисунок 20 – Корень стружки с разрушающимся наростом.
Здесь надо обратить внимание на изменение положения плоскости скалывания. Вслед за разрушением нароста уменьшается угол скалывания b1 и увеличивается толщина образующейся стружки. Нарост представляет собой тело твердое, но неустойчивое, он периодически разрушается, и фактическая толщина среза постоянно меняется вслед за изменением размера нароста. По этой причине обработанная поверхность получается неровной, со следами надиров и вырывов. Располагаясь на передней поверхности и свешиваясь над задней поверхностью, нарост закрывает главную режущую кромку и предохраняет ее от разрушения.
В некоторых случаях нарост бывает настолько устойчив, что в течение всего периода резания исключает контакт стружки с передней поверхностью инструмента. Так на рисунке 21 представлены фотографии быстрорежущего проходного упорного резца с наростом и после его удаления.
Рисунок 21 – Фотографии проходного упорного резца со стороны главной задней поверхности (вверху ) и со стороны передней поверхности (внизу), с наростом (слева ) и после его удаления (справа )
После удаления нароста на передней поверхности резца «под наростом» обнаружились следы доводки передней поверхности порошком карбида бора.
Эти следы в виде мелких царапин стертые за пределами нароста, свидетельствуют о том, что нарост надежно защищал переднюю поверхность от действия стружки в течении всего времени резания.
Нарост имеет некоторые положительные особенности:
1) защищает режущую кромку от износа;
2) снижает силы резания за счет уменьшения угла резания dн < d.
Однако, в целом, данное явление является сильно отрицательным, т.к.
1) ухудшается шероховатость поверхности (все получистовые и чистовые операции необходимо выполнять без нароста);
2) образование нароста является трудно управляемым явлением
Для борьбы с наростообразованием при резании необходимо выполнять следующие мероприятия:
1. Увеличивать скорость резания и подачу до достижения температуры в зоне резания порядка 550…600 0С.
2. Увеличивать передний угол g
3. Применять СОТС с большими проникающими и смазывающими способностями с целью уменьшения трения на передней поверхности инструмента и торможения металла.
4. Применять режущие инструменты с износостойкими покрытиями, уменьшающими трение.
5. Применять доводку инструмента алмазными кругами для твердосплавных инструментов и эльборовыми кругами – для быстрорежущего.
5. ТРение и контактные явления в зоне резания
Основными особенностями трения при резании являются:
· различное физико-механическое состояние контактирующих поверхностей;
· интенсивное схватывание обрабатываемого и инструментального материалов;
· сложный характер распределения нормальных напряжений на контактных площадках;
· малая продолжительность контакта инструмента со стружкой и деталью при постоянном обновлении зоны контакта.
На передней l и задней D контактных поверхностях имеют место явления трения стружки о переднюю поверхность инструмента и обработанной поверхности по задней поверхности инструмента (рисунок 22).
Рисунок 22 – Зоны трения
На контактных участках АС = l и AD = D присутствуют участки пластических контактов АM = l0 и AN = D0 и участки упругих контактов MC = l – l0 и ND = D – D0.
На участках пластических контактов происходят адгезионные явления (явления «слипания» двух разнородных материалов). На этих участках коэффициенты трения велики и могут превышать 1 (закон Кулона о трении здесь не работает).
На участках упругих контактов закон Кулона выполняется, т.к. здесь происходит чисто внешнее трение стружки о резец, и m <1.
Таким образом, на разных точках контактных участков имеют место различные коэффициенты трения. Поэтому в теории резания введены понятия средних коэффициентов трения:
m - средний коэффициент трения стружки о резец;
m1 – средний коэффициент трения на задней поверхности.
Коэффициент трения m можно определить следующим образом:
(см. выше). Отсюда
.
Следовательно
Но . Поэтому
Для коэффициента трения на задней поверхности можно использовать упрощенную формулу:
.
Ширина площадки контакта по передней поверхности инструмента зависит от переднего угла g, толщины срезаемого слоя а, коэффициента утолщения стружки Ka, скорости резания и других факторов.
Соответственно на коэффициент трения оказывают влияние физико-механические и теплофизические свойства обрабатываемого материала, передний угол g, толщина срезаемого слоя а, скорость резания v и применяемая СОЖ.
Для трущейся пары стружка – передняя поверхность инструмента средний коэффициент трения обусловливается склонностью к адгезионному взаимодействию инструментального и обрабатываемого материалов. Возникновение связей между стружкой и инструментом определяется их способностью образовывать между собой химические соединения и твердые растворы. Чем сильнее эти связи, возникающие в результате сил адгезии между стружкой и инструментом, тем больше средний коэффициент трения. С повышением механических свойств обрабатываемого материала средний коэффициент трения уменьшается, однако при этом возрастают средние нормальные и касательные напряжения. Если температура резания изменяется мало, средний коэффициент трения остается практически неизменным.
На контактных поверхностях инструмент — стружка под действием кислорода воздуха образуются оксидные пленки, препятствующие схватыванию материалов и уменьшающие средний коэффициент трения. Самый большой средний коэффициент трения отмечается для быстрорежущих сталей, далее (в порядке его уменьшения) следуют однокарбидные и двухкарбидные твердые сплавы.
Большое влияние на средний коэффициент трения оказывает СОЖ, особенно с хорошим смазочным действием. В случае применения таких СОЖ значения g и а практически не влияют на средний коэффициент трения. Если же резание ведется без СОЖ, то при увеличении переднего угла и толщины срезаемого слоя уменьшается средний коэффициент трения, так как увеличивается среднее нормальное контактное напряжение на передней поверхности инструмента.
Рассматривая влияние различных факторов на средний коэффициент трения при резании, необходимо помнить, что он ни по величине, ни по физическому смыслу, ни по закономерностям изменения не совпадает с коэффициентом внешнего трения, определяемым по закону трения Амонтона—Кулона, и не является константой трущихся пар.
Такое специфическое изменение коэффициента трения при резании связано с двоякой природой трения на передней поверхности, где существуют два участка трения (зона пластического и зона упругого контакта). Поэтому нельзя средний коэффициент трения отождествлять ни с коэффициентом трения при пластическом течении материала, ни с коэффициентом внешнего трения.
6. Взаимосвязь явлений в процессе резания
Условия резания по-разному влияют на деформационные и контактные процессы в зоне резания. Это влияние может быть непосредственным или косвенным. Например, изменение g приводит к увеличению или уменьшению средних контактных нормальных напряжений на передней поверхности инструмента, что вызывает изменение среднего коэффициента и угла трения. Последнее оказывает влияние на угол действия, изменение которого вызывает изменение угла сдвига и работы стружкообразования.
Параметры процесса резания делятся на внутренние и внешние: к внутренним относятся угол действия, температура на передней поверхности инструмента, действительный передний угол с учетом нароста, ширина площадки контакта, средний коэффициент трения и др.; к внешним — физико-механические свойства обрабатываемого и инструментальных материалов, геометрические параметры инструмента, параметры режима резания и свойства СОЖ.
Непосредственное и наиболее сильное влияние на процесс резания оказывают угол действия, передний угол инструмента, скорость резания и свойства обрабатываемого материала. Влияние остальных факторов на процесс резания косвенное, из них наибольшее оказывает толщина срезаемого слоя.
Непосредственное влияние на процесс стружкообразования при прямоугольном резании оказывают только четыре фактора: угол действия, передний угол инструмента, скорость резания и свойства обрабатываемого материала. Все остальные факторы влияют косвенно. Рассмотрим влияние некоторых факторов, действующих наиболее сильно.
6.1. Влияние угла действия
Под углом действия yпонимают угол между плоскостью сдвига и передней поверхностью режущего инструмента.
Важнейшей характеристикой процесса стружкообразования является угол сдвига b, от величины которого зависят коэффициент усадки стружки, относительный сдвиг и работа стружкообразования. Все то, что увеличивает угол сдвига, уменьшает степень деформации срезаемого слоя и работу стружкообразования.
При увеличении угла действия угол сдвига уменьшается, что приводит к увеличению степени деформации срезаемого слоя и работы стружкообразования. Ухудшение условий стружкообразования связано с изменением напряженного и деформированного состояния зоны стружкообразования. При увеличении угла y вектор R силы стружкообразования поворачивается против часовой стрелки, что приводит к повороту в том же направлении осей главных напряжений и соответствующему уменьшению угла сдвига.
6.2. Влияние переднего угла g
Непосредственное влияние переднего угла на процесс стружкообразования заключается в изменении направления схода стружки в пространстве. При уменьшении переднего угла увеличивается угол между векторами скоростей резания v и стружки v с и частицы срезаемого слоя при превращении его в стружку сильнее изменяют направление своего движения. При этом изменяется направление движения срезаемого слоя (рисунок 23), уменьшается угол сдвига и увеличивается степень деформации срезаемого слоя.
Рисунок 23 – Влияние переднего угла на процесс стружкообразования
При обработке металлов без образования нароста косвенное влияние переднего угла инструмента на процесс формирования стружки связано только с изменением угла действия вследствие изменения ориентации передней поверхности и среднего коэффициента трения. С уменьшением g угол действия увеличивается вследствие изменения положения передней поверхности и уменьшается из-за уменьшения среднего коэффициента трения. Первое воздействие является преобладающим.
При обработке с образованием нароста влияние g на процесс формирования стружки менее ощутимо, поскольку, чем меньше передний угол инструмента, тем больше высота нароста и больше действительный передний угол.
6.3 Влияние скорости резания v
Непосредственное влияние скорости резания на процесс стружкообразования выражается в изменении угла сдвига. Угол сдвига растет при увеличении скорости резания, что связано с запаздыванием процесса пластической деформации.
Косвенное влияние скорости резания на процесс стружкообразования проявляется в ее влиянии на угол действия за счет изменения среднего коэффициента трения, а если материал обрабатываемой детали склонен к наростообразованию, то и за счет изменения фактического переднего угла. Изменение среднего коэффициента трения при изменении скорости резания связано как с влиянием ее на средние нормальные контактные напряжения, так и с изменением температуры на передней поверхности, влияющей на сопротивление сдвигу в контактном слое стружки. При резании материалов, не склонных к наростообразованию, увеличение скорости резания непрерывно улучшает процесс стружкообразования, уменьшая относительный сдвиг и удельную работу стружкообразования. При резании материалов, склонных к наростообразованию, влияние скорости резания усложняется. Только при скоростях резания, при которых температура резания становится больше 600°С, увеличение скорости резания непрерывно улучшает все показатели стружкообразования.
6.4 Влияние механических свойств материала обрабатываемой детали
Непосредственное влияние на процесс стружкообразования механических свойств материала обрабатываемой детали заключается в увеличении угла сдвига с повышением сопротивления сдвигу материала в зоне стружкообразования при постоянных переднем угле, и угле действия. Соответственно этому уменьшается степень деформации срезаемого слоя.
Если нарост при резании отсутствует, то косвенное влияние свойств обрабатываемого материала на процесс стружкообразования проявляется в изменении угла действия вследствие изменения среднего коэффициента трения. При постоянной температуре на передней поверхности средний коэффициент трения для различных обрабатываемых материалов изменяется сравнительно мало, так как при увеличении сопротивления материала пластической деформации одновременно возрастают как касательные, так и формальные контактные напряжения. При постоянной скорости резания с увеличением сопротивления материала пластическим деформациям средний коэффициент трения уменьшается, что уменьшает коэффициент усадки стружки и относительный сдвиг. При наличии нароста косвенное влияние свойств обрабатываемого материала на процесс стружкообразования дополняется их влиянием через изменение фактического переднего угла.
7. Силы и работа резания
7.1. Основные случаи резания
Процесс пластической деформации срезаемого слоя и образования стружки рассмотренных ранее параметров характеризуется еще и степенью осложненности условий, в которых совершается образования стружки. По этому признаку различают два случая резания: свободное и несвободное (осложненное).
1.Свободное резание. Происходит в случае, когда в резании участвует одна прямолинейная режущая кромка. Деформированное состояние срезаемого слоя при этом является плоским. Пример свободного резания указан на рисунке 24,.а. В этом случае деформация совершается в плоскостях, параллельных друг другу, и все элементарные объемы срезаемого слоя могут свободно перемещаться в параллельных направлениях.
Свободное резание может осуществляться также при строгании прямых гребешков на плоской поверхности призматической заготовки или при точении с поперечной подачей буртика на цилиндрическом образце (заготовке). Длинна прямолинейной режущей кромки инструмента в обоих этих случаях должна быть больше ширины гребешков или буртика на ширину перекрытия режущего лезвия. Свободное резание обычно производится при выполнение каких-либо экспериментов в различных исследованиях. Это делается для того, чтобы исключить влияние осложненного деформирования срезаемого слоя на исследуемое явление. Получить хороший корень стружки для изучения, например, пластической деформации срезаемого слоя или образования нароста, можно только при свободном резании, при котором все явления в зоне резания совершаются в семействе параллельных плоскостей, поэтому одинаковы в каждой из них.
а б
Рисунок 24 – Свободное (а) и несвободное резание (б).
2. Несвободное (осложненное) резание (рисунок 24, б). Характеризуется тем, что отдельные объемы срезаемого слоя на разных участках режущей кромки перемещаются в разных направлениях, что создает условия сложного деформирования и затрудняет образование стружки.
При несвободном резании отдельные элементарные объемы срезаемого слоя перемещаются в разных направлениях и поэтому в разных точках зоны резания одни и те же явления совершаются по-разному, с разной степенью интенсивности. Картина состояния материала в зоне резания в одной секущей плоскости не является типичной для всех других секущих плоскостей и не повторяет картины состояния материала в других секущих плоскостях.
7.2. Система сил при свободном резании
Силы резания, возникающие на передней поверхности инструмента и в плоскости сдвига были рассмотрены ранее в разделе «физическая сущность процесса стружкообразования» (рисунок 8).
Рассмотрим систему сил, возникающих при свободном резании (рисунок 25, а). На переднюю поверхность резца давит стружка с силой Rп, которая является равнодействующей нормальной силы Nп и силы трения стружки о переднюю поверхность Fп, т. е.
Рисунок 25 – Схема сил, действующих при свободном резании
В то же время на заднюю поверхность резца вблизи режущей кромки действует нормальная сила упругого противодействия обрабатываемого материала Nз и сила трения о заднюю поверхность инструмента F3. Они дают результирующую силу Rз. Так как задний угол a мал, а при наличии площадки износа на некотором участке задней поверхности он равен нулю, в расчетной схеме принимаем направление сил Fз и Nз, как показано на рисунке 25, а, т.е. направление Fз противоположно вектору скорости резания v. Для осуществления процесса резания или сохранения равновесия резца к нему извне должна быть приложена сила, равная по величине и противоположная по направлению силе (рисунок 25, б).
Разложим силу R, приложенную к резцу, на две составляющие (рисунок 25, в):
1) Р z в направлении главного движения резания (назовем ее главной силой);
2) Ру в направлении, совпадающем с осью резца (назовем ее радиальной силой резания).
Спроектируем действующие силы на направление осей у и z:
Силы, действующие на передней и задней поверхностях инструмента, а также вдоль осей у и z , можно рассчитать теоретически на основе теорий пластичности, упругости и др. Теоретические уравнения, однако, сложны и не совсем точны; в них используются коэффициенты, которые характеризуют свойства обрабатываемого материала и численные значения которых неизвестны. Поэтому на практике силы резания определяют экспериментальным путем.
7.3. Система сил при несвободном резании
При несвободном резании на режущий инструмент действует пространственная система сил. Режущий инструмент находится в контакте с обрабатываемым материалом по трем рабочим поверхностям его режущей части: по передней, главной задней и вспомогательной задней поверхности. Поскольку эти поверхности инструмента расположены под разными углами друг к другу, то и действующие на этих поверхностях нормальные и касательные силы в пространстве располагаются не параллельно друг к другу, не в параллельных, как при свободном резании, плоскостях. Природа сил, естественно, та же, что и при свободном резании, это силы нормального давления и касательные силы трения. Схема сил при несвободном резании представлена на рисунке 26.
Рисунок 26 – Схема сил при несвободном резании
В условиях несвободного резания равнодействующую силу сопротивления резанию R раскладывают на три составляющие:
Pz — главную (тангенциальную) силу резания, которая действует в направлении скорости главного движения;
Py — радиальную силу, направленную в вершине лезвия по радиусу траектории главного вращательного движения резания;
Рх — осевую силу, действующую параллельно оси главного вращательного движения резания, т. е. силу подачи.
По Pz производят расчеты прочности и жесткости резца, а также необходимой мощности на осуществление процесса резания.
Сила Py вызывает механические деформации технологической системы СПИД (рисунок 27). Деформация может быть определена:
Рисунок 27 – Прогиб детали
, м
где j – жесткость технологической системы (Н/м).
Чем больше величина жесткости системы, тем меньше прогиб y и меньше погрешность обработки. Поэтому сила Py определяет точность обработки. Данную силу необходимо уменьшать, а жесткость системы увеличивать.
Сила Ру также используется при определении прочности и жесткости отдельных деталей станка.
Прочность и жесткость механизма подачи станка рассчитывают по силе Рх.
Установлено, что при точении конструкционных сталей и чугунов резцом с геометрическими параметрами j = 45°, g = 15°, l = 0° наблюдается следующее соотношение сил резания:
Ру = (0,4 ... 0,5)Р z;
Рх = (0,3 ... 0,4) Р z,
а при точении жаропрочных сталей сила Ру может быть больше, чем Рг.
Это же соотношение наблюдается и при точении практически всех материалов с малыми сечениями среза. С увеличением угла j и с уменьшением переднего угла g отношение Py / Pz уменьшается, a Рх/Рг увеличивается. Кроме того, относительные значения Рх и Ру возрастают с увеличением износа резца, особенно при его затуплении по задней поверхности.
Равнодействующая R является диагональю параллелепипеда. Следовательно:
.
7.4. Работа и мощность резания
В общем случае работа резания (Дж):
,
где Р z – сила резания, действующая в направлении скорости резания, Н;
L – путь, проходимый режущим инструментом, м.
Полная работа резания затрачивается
· на пластическую деформацию срезаемого слоя припуска Wпл.деф.,
· на упругую деформацию, которая всегда предшествует пластической деформации Wупр.деф,
· на преодоление сил трения на передней и задней поверхностях Wтр,
· на образование новой поверхности (она называется работой диспергирования-разделения) Wдиспрег.:
Работа диспергирования и работа на упругую деформацию составляют менее 1% всей работы и потому ими можно пренебречь, а вся работа резания практически расходуется на пластическую деформацию, на преодоление трения на передней и задней поверхностях:
Реакция тангенциальной силы Pz создает момент сопротивления резанию, называемый крутящим моментом резания (заготовки):
, Н×м,
где D – диаметр обрабатываемой поверхности, м.
Для осуществления процесса резания необходимо, чтобы крутящий момент, развиваемый станком при определенном числе оборотов его шпинделя Мст, был больше крутящего момента резания:
.
Мощность, непосредственно затрачиваемая на осуществление процесса резания, называется эффективной мощностью. Она не включает затраты мощности на преодоление сил трения в механизмах станках. Эффективная мощность складывается из мощностей Nez и Nex, затрачиваемых на преодоление сил Pz и Px соответственно, т.е.
.
При применяемых режимах резания, даже в случае равенства составляющих Pz и Px, мощность Nex во много раз меньше Nez. Поэтому эффективную мощность рассчитывают только по тангенциальной силе резания:
, Вт,
где Р z – тангенциальная составляющая силы резания, Н;
v – скорость резания, м/с.
Учитывая к.п.д. кинематических цепей главного привода станка h, получим формулу для определения мощность электродвигателя главного привода:
, Вт.
7.5. Измерение сил в процессе резания
Наиболее часто силы резания определяют на основе непосредственного измерения с помощью специальных приборов. Существует большое количество таких приборов, называемых динамометрами. Деформации упругих элементов динамометра непосредственно или с использованием связанных с ними явлений служат основой для измерения сил резания. Независимо от конструкции динамометры состоят из следующих основных частей:
1) первичного измерительного преобразователя, воспринимающего нагрузку;
2) регистрирующего устройства;
3) вспомогательных звеньев, связывающих их друг с другом.
Динамометры подразделяются на гидравлические, механические, электрические.
Гидравлические динамометры в настоящее время не находят применения по причине большой инерционности рычажно-поршневой системы, из-за чего показания отстают от быстропротекающих процессов и искажают картину изменения сил резания во времени и по величине, а также из-за малой чувствительности.
Принцип работы механических динамометров (рисунок 28) основан на том, что под действием сил резания на резец 9резцедержатель 8вследствие деформации упругих стенок 1 корпуса 5перемещается. Эти перемещения через сухари 4и ножки индикаторов 2,6фиксируются индикаторами 3и 7.
Механические динамометры просты по конструкции, но имеют те же недостатки, что и гидравлические, и поэтому получили ограниченное распространение.
Рисунок 28 – Схема механического динамометра
Электрические динамометры являются наиболее чувствительными приборами, так как они мало инерционны и позволяют с помощью осциллографа производить запись быстропротекающих процессов за тысячные и стотысячные доли секунды. Такие динамометры преобразуют механическое воздействие сил резания в легко измеряемые электрические величины.
Электрические преобразователи подразделяются на емкостные, или конденсаторные; индуктивные; тензометрические.
В емкостных преобразователях (рисунок 29) под действием силы резания перемещается упругая пластина конденсатора, изменяя воздушный зазор Dh, а следовательно, и емкость конденсатора. Изменение емкости при помощи высокочастотного устройства приводит к колебанию силы тока, регистрируемой с помощью гальванометра или осциллографа.
Рисунок 29 – Емкостной преобразователь
Индуктивные преобразователи (рисунок 30) основаны на изменении индуктивности токонесущего контура, а следовательно, и силы тока в обмотке в зависимости от воздушного зазора Dh между ферромагнитными телами. Изменение силы резания соответственно влияет на регистрируемый ток.
Рисунок 30 – Индуктивный преобразователь
Проволочные, или тензометрические, первичные преобразователи представляют собой несколько витков очень тонкой проволоки, изготовляемой из специального сплава, которая изменяет электрическое сопротивление при деформации преобразователя. Витки или решетку из такой проволоки помещают между двумя склеенными бумажными полосками и наклеивают на элемент 6(державку) (рисунок 31). Под влиянием сил резания элемент 6и приклеенная к нему проволока 5упруго деформируются. Это вызывает изменение силы тока в электрической цепи, которая увеличивается усилителем 2и измеряется регистрирующим прибором 1. Чтобы не было искажений в показаниях приборов при измерении сил резания из-за непостоянства напряжения в сети, в электрическую цепь необходимо включать стабилизатор напряжения 3, устанавливаемый между регистрирующим прибором и источником питания 4.
Рисунок 31 – Схема измерения сил резания с использованием тензометрических преобразователей
В зависимости от того, сколько составляющих сил резания можно измерить динамометром, они называются одно-, двух- или трехкомпонентными.
Наиболее широкое распространение среди электрических динамометров получил универсальный динамометр СУРП (старое название УДМ; выпускаются модификации СУРП-100, СУРП-600 и СУРП-1200) конструкции Всесоюзного научно-исследовательского инструментального института (ВНИИ). Он позволяет измерять составляющие силы резания при точении, фрезеровании, шлифовании, осевую силу и крутящий момент при сверлении, зенкеровании, развертывании, нарезании резьбы метчиком и рассчитан на максимальное значение Р z , равное 1, или 12 кН.
Динамометры не позволяют определить непосредственно силы резания; их показания соответствуют деформациям, пропорциональным действующей силе. Поэтому перед работой необходимо протарировать динамометр. Тарирование заключается в том, что динамометр нагружают в направлении сил резания сначала возрастающими, а затем убывающими силами, которые известны. Показания динамометра, соответствующие определенным силам, регистрируются. На основании этих данных по средней линии нагрузки и разгрузки строят тарировочный график, которым в дальнейшем пользуются при расшифровке показаний динамометра.
7.7. Влияние различных факторов на силу резания
7.7.1. Влияние ширины и толщины среза
Толщина среза а1и ширина b1не в одинаковой степени влияют на силу резания. Сила резания возрастает пропорционально b 1 , но отстает от увеличения а1.
Отставание роста силы резания от увеличения толщины среза можно объяснить следующим: с увеличением толщины среза нагрузка на единицу длины режущего лезвия возрастает. В связи с этим увеличивается температура резания, что приводит к уменьшению сил трения, усадки стружки и снижению сопротивления обрабатываемого материала пластическому деформированию. Пластические деформации и напряжения распределяются по толщине стружки неравномерно. Они значительно больше в слоях, прилегающих к передней поверхности лезвия инструмента. Поэтому увеличение толщины среза приводит к относительному уменьшению слоя с максимальными деформациями. Кроме того, сила трения Fзпо задней поверхности лезвия как одна из слагаемых при расчете сил резания с изменением толщины среза остается неизменной или изменяется очень мало.
Таким образом, при сохранении площади поперечного сечения среза постоянной, силы резания уменьшаются по мере уменьшения ширины и одновременно увеличения толщины среза.
7.7.2. Влияние механических свойств обрабатываемого металла
При снятии стружки металл не только срезается, но и претерпевает сильную пластическую деформацию. Большое влияние на силы резания оказывают силы трения стружки и обрабатываемого материала соответственно о переднюю и заднюю поверхности лезвия инструмента. Однако необходимо учитывать, что в процессе обработки металл в зоне резания сильно разогревается. Значит, его свойства могут отличаться от свойств, которые характерны для него при статических испытаниях. Поэтому нет точной и однозначной зависимости между силой Р z и временным сопротивлением обрабатываемого материала, а также его твердостью и другими механическими характеристиками. Установлено, что силы резания растут при увеличении предела прочности s в , твердости, пластичности и вязкости обрабатываемого материала.
7.7.3. Влияние механических свойств инструментального материала
Это влияние может быть вызвано только различием в силах трения (коэффициентах трения) между обрабатываемым и инструментальным материалами. Внутри групп быстрорежущих сталей и вольфрамокобальтовых твердых сплавов коэффициенты трения и укорочения стружки не отличаются, а следовательно, сила Pz не изменяется.
При обработке инструментами, оснащенными вольфрамотитановыми твердыми сплавами, Р z уменьшается с увеличением содержания карбидов титана TiC. Для сравнения отметим, что если при обработке инструментом из быстрорежущей стали принять Р z = 1, для тех же условий работы инструмента, оснащенного твердыми сплавами группы ВК, Р z =1, а группы ТК Р z = 0,9...0,95.
7.7.4. Влияние режимов резания
Ранее считалось, что скорость резания практически не влияет на его силу. Объясняется это проведением работ в сравнительно узком диапазоне скоростей, а также недостаточной чувствительностью используемых при этом динамометров. В настоящее время известно, как изменяется сила резания в широком диапазоне скоростей.
Прежде всего необходимо отметить полную идентичность зависимостей тангенциальной составляющей силы резания Pz и коэффициента линейной усадки стружки Kl от скорости резания. В тех областях скоростей резания, где уменьшается коэффициент укорочения стружки, снижается сила резания, и наоборот. (рисунок 32).
Рисунок 32 – Зависимость сил резания от скорости резания и переднего угла при обработке стали 40Х с а1 = 0,2 мм; b 1 = 4 мм
Однако, это не случайное совпадение, а закономерность. Возрастание значения Kl свидетельствует об уменьшении угла сдвига b1 и соответственно об увеличении поверхности, по которой происходит сдвиг. При этом повышается степень деформации металла, т. е. происходит его упрочнение, а значит, возрастают напряжения, при которых происходит сдвиг. Увеличение напряжения и площади сдвига приведет к росту силы резания. Кроме того, сила резания и коэффициент укорочения зависят от коэффициента трения при деформировании срезаемого слоя.
Сложный характер кривых Р z = f ( v ) объясняется появлением нароста на передней поверхности лезвия инструмента. Минимальные значения силы на кривых Pz = f ( v ) соответствуют максимально возможному наросту. При малой скорости резания, когда нарост не образуется, сила резания велика. В диапазоне скоростей, где имеется максимальное наростообразование, сила резания и укорочение стружки уменьшаются, так как с увеличением размеров нароста возрастает действительный передний угол инструмента. По мере дальнейшего повышения скорости резания высота нароста, а следовательно, и действительный передний угол уменьшаются. Одновременно с этим возрастают коэффициент укорочения стружки и силы резания.
Как уже отмечалось, работа на очень высоких скоростях резания приводит к значительному повышению температуры резания, в результате чего уменьшается коэффициент трения, а следовательно, и Р z .
Минимумы и максимумы кривых Р z = f ( v ) тем рельефнее, чем меньше передний угол. Объясняется это тем, что больший нарост может образоваться (и образование его интенсивнее) при меньших передних углах инструмента.
При обработке чугуна образуется меньший нарост, поэтому зависимость Р z = f ( v ) имеет вид плавной кривой (рисунок 33).
Рисунок 33 –Кривая зависимости Р z = f ( v ) при обработке чугуна
Аналогично выглядят зависимости Р z = f ( v ) для материалов, не склонных к наростообразованию — меди, жаропрочных и нержавеющих сталей и сплавов, титановых сплавов.
Глубина резания t и подача S увеличивают силы, т.к. увеличивается сечение среза и сила сдвига отдельных элементов стружки: .
7.7.5. Влияние геометрических параметров режущей части инструмента
1) Влияние переднего g и заднего a углов.
При увеличении переднего угла g облегчается врезание зубьев инструмента в деталь, улучшается сход стружки, уменьшается деформация обрабатываемого металла и снижается коэффициент укорочения стружки, а, следовательно, уменьшается Р z.
Влияние заднего угла a на силу резания устанавливается, исходя из способности металла упруго восстанавливаться. С уменьшением угла a увеличивается контакт задней поверхности инструмента с обрабатываемой деталью, что приводит к росту сил трения и резания. Этому способствует то обстоятельство, что после прохождения режущего лезвия металл упруго восстанавливается, образуя дополнительную площадку контакта инструмент— деталь. Чем больше a, тем меньше длина контакта, а, следовательно, и Р z.
Таким образом, интенсивность влияния a на силы резания невелика. С увеличением заднего угла a от 20 до 10° Pz уменьшается на 6 %, а Ру – на 17 %. При дальнейшем увеличении a силы резания остаются почти постоянными.
2) Влияние главного угла в плане j..
С увеличением j при неизменных режимных параметрах увеличивается толщина среза и уменьшается его ширина
. Соответственно уменьшается величина усадки стружки, снижаются и силы Pz и Py. Сила Px с увеличением угла j возрастает, что связано с изменением соотношения сил, действующих в горизонтальной плоскости: при увеличении угла j равнодействующая сила R отклоняется в сторону оси заготовки, увеличивая тем самым Px.
3) Влияние радиуса при вершине r.
С увеличением r при неизменных s и t растет ширина и уменьшается толщина среза. Кроме того, это приводит к увеличению деформации срезаемого металла и уменьшению вспомогательного переднего угла g 1 . Это вызывает увеличение сил Pz и Py и уменьшение Px .
7.7.6. Влияние СОТС
В целом, СОТС, проникая на контактные площадки, действует как смазка и снижает силы Pz, Py и Px .
8. Вибрации технологической системы станок-приспособление-инструмент-заготовка
В процессе резания в элементах технологической системы могут возникать колебания, называемые вибрациями.
Технологическая системав общем случае представляет совокупность функционально взаимосвязанных средств технологического оснащения, предметов производства и исполнителей, предназначенная для выполнения того или иного технологического процесса или операции.
Технологическая система СПИЗ может служить для обработки конкретной поверхности детали или, как одна из многих подсистем, входить в общую систему для обработки детали, а в дальнейшем — сборки машины.
Обязательным условием получения высокой точности и низкой шероховатости обработанной поверхности является устойчивость движения при резании. Для этого система СПИЗ должна быть выиброустойчивой и не допускать существенных колебаний.
Практика показала, что при различных условиях обработки могут появляться колебания детали, оборудования и инструмента различной частоты. Чаще всего деталь имеет низкочастотные колебания, а инструмент — высокочастотные. При возникновении вибраций снижается качество обработанной поверхности и период стойкости инструмента.
В ходе работы станка возникает 4 вида колебаний.
1. Вынужденные колебания возникают вследствие наличия в системе внешней периодической силы, вызывающей колебательный процесс с частотой, равной частоте возмущающей силы. Причиной появления возмущающей силы могут быть силы, обусловленные процессом резания (прерывистость процесса резания, неравномерность припуска, оставленного на обработку), а также силы, возникающие технологической системы вне зоны резания (дисбаланс вращающихся частей станка, детали и инструмента, дефекты зубчатых и ременных передач станка, передача колебаний станку от других работающих поблизости станков и т. д.). Для устранения этих колебаний достаточно ликвидировать причины их возникновения.
2. Параметрические колебания возникают при наличии какого-либо переменного параметра, создающего эффект, аналогичный действию переменной силы. Обычно таким параметром является переменная жесткость узла или детали. Например, наличие шпоночной канавки на валу или переменная жесткость подшипников качения приводит к тому, что при вращении прогибы вала периодически изменяются, хотя внешняя сила постоянна. Параметрические колебания вследствие переменной жесткости по своему характеру близки к вынужденным.
3. Релаксационные (прерывистые) колебания возникают при медленных перемещениях узлов станочной системы. Рассмотрим механизм их появления (рисунок 34).
а
б
Рисунок 34 – Схема возникновения релаксационных колебаний (а)и изменение скорости перемещения узла станка во времени (б)
При малой равномерной скорости перемещения v0 ведущего звена 1 сначала происходит деформация передаточного звена 2без движения ведомого звена 3, пока не будет преодолена сила сопротивления F 0 . Как только начнется движение, сила трения резко падает, так как она меньше, чем сила трения покоя. При этом ведомое звено под действием потенциальной энергии передаточного звена получит перемещение с переменной скоростью v и остановится. Далее циклы скачков повторяются. Релаксационные колебания, приводя к неустойчивому перемещению узлов, могут вызвать значительные динамические нагрузки на узлы станка и режущий инструмент, а также погрешности при обработке деталей.
4. Автоколебания (самовозбуждающиеся колебания) являются наиболее характерной формой колебаний. Они возникают при всех известных видах обработки. Любое случайное возмущение (толчок), каких много в реальной системе резания (это вход или выход режущих лезвий из контакта с деталью, неравномерность припуска, неоднородность свойств обрабатываемого материала, радиальное биение заготовки или инструмента и др.), приводит к возникновению собственных затухающих колебаний системы. Эти колебания всегда сопровождаются изменением среза (обычно только толщины среза а1) и скорости резания v или скорости скольжения стружки по передней поверхности инструмента. Изменение а и v вызывает соответствующее изменение силы резания и ее составляющих. В определенных условиях возникшие колебания могут перейти в незатухающие автоколебания. Энергию для их поддержания создает переменная сила резания.
В реальной упругой системе в процессе резания может существовать много причин, вызывающих автоколебательный процесс. Наиболее существенное влияние имеют первичные механизмы возмущения автоколебаний, вызванные координатной связью системы станок — приспособление— инструмент — деталь (СПИД), имеющей несколько степеней свободы, с процессом резания, и специфической зависимостью силы резания от его скорости. Вибрации нарастают до тех пор, пока не устанавливаются стабильные автоколебания с частотой, определяемой свойствами системы СПИД.
В зависимости от положения осей жесткости системы СПИД возможно три состояния технологической системы — устойчивый процесс резания, автоколебательные процессы при резании и подрывание. Последнее является следствием апериодической неустойчивости динамической системы станка. В этом случае в результате случайного толчка возникает нарастающее в одном направлении отклонение инструмента. Он все глубже врезается в металл, и в конечном итоге происходит поломка инструмента или обрабатываемой детали.
Физическая модель возникновения и развития установившейся формы автоколебаний при резании лезвийным инструментом может быть следующей:
1) любые случайные толчки выводят из равновесия упругую систему СПИД и приводят к изменению толщины среза;
2) отставание изменения силы резания от изменения толщины среза (В диапазоне режимов резания, в котором работают быстрорежущие и твердосплавные инструменты, оно находится в пределах 3—5 мкс.) переводит возникшие собственные затухающие колебания в незатухающие автоколебания, где поддерживающую их энергию создает изменяющаяся синхронно, но сдвинутая по фазе сила резания;
3) возникающие на поверхности резания вибрационные следы, начиная со второго оборота детали при точении или с работы второго зуба многолезвийного инструмента, будут при каждом колебании передавать в систему дополнительную энергию;
4) через определенный промежуток времени наступает равновесие между энергией возбуждения, поступающей в систему, и энергией, рассеиваемой при колебаниях, и устанавливается определенный уровень автоколебаний.
Однако ни в реальных процессах, ни при моделировании на ЭВМ никогда не наблюдаются установившиеся автоколебания в полном смысле этого слова. Автоколебания, как правило, происходят с периодическим изменением амплитуд.
На амплитуду колебаний оказывает влияние ряд факторов.
1) Увеличение толщины срезаемого слоя или подачи уменьшает амплитуду колебаний, а ширины срезаемого слоя или глубины резания — увеличивают ее (рисунок 35).
2) Влияние скорости резания на амплитуду колебаний имеет экстремальный характер (рисунок 36). Максимальная амплитуда зависит от рода обрабатываемого материала и условий работы.
3) Интенсивность вибраций зависит от переднего угла инструмента. При отрицательных его значениях амплитуда колебаний резко возрастает. Чем меньше g , тем больше зона скоростей, при которых возникают вибрации (рисунок 36).
4) Уменьшение заднего угла инструмента до 3° и ниже приводит к снижению амплитуды колебаний, а если он больше 8... 10°, то на интенсивность колебаний он не оказывает существенного влияния.
5) С изменением угла j изменяется толщина и ширина срезаемого слоя, и в соответствии с этим — амплитуда колебаний. С увеличением j амплитуда колебаний уменьшается (рисунок 37), поскольку при этом уменьшается b 1 и увеличивается а1.
6) Частота автоколебаний не зависит ни от угла в плане, ни от толщины среза.
1 – b1 = 6 мм, 2 – b1 = 4,7 мм, 3 – b1 = 3,7 мм
Рисунок 35 – Влияние толщины a1 срезаемого слоя на амплитуду А колебаний при точении
1 – g = -100; 2 – g = -50; 3 – g = 00; 4 – g = 100; 5 – g = 300;
Рисунок 36 – Влияние скорости резания v и переднего угла резца g на амплитуду А колебаний при точении
Рисунок 37 – Влияние главного угла в плане j на амплитуду колебаний при точении
Автоколебательный процесс оказывает существенное влияние на протекание процесса резания. В частности, интенсивность изнашивания и период стойкости инструмента существенно зависят от амплитуды колебаний, в то время как влияние частоты на эти параметры значительно меньше.
Серьезной проблемой является борьба с вибрациями при резании. Для устранения их необходимо:
1) повышать виброустойчивость и динамические характеристики металлорежущих станков и их узлов. Проблема ликвидации вибраций, становится особенно важной при проектировании приводов главного движения и движения подачи станков с ЧПУ. Это вызвано спецификой такого рода оборудования, где управляющий сигнал должен обеспечивать крайне малое перемещение исполнительного механизма. Чувствительность к сигналу в настоящее время приближается к 1 мкм и менее. Возникновение колебаний, особенно релаксационных, нарушает взаимодействие управляющего и исполнительного элементов, что нарушает структурный принцип ЧПУ и является недопустимым;
2) разрабатывать применительно к конкретным технологическим операциям специальные виброгасящие устройства различных принципов действия — ударного, фрикционного, гидравлического и др. Применение виброгасителей существенно снижает интенсивность автоколебаний при точении, растачивании, развертывании, фрезеровании;
3) разрабатывать виброустойчивые конструкции режущего и вспомогательного инструментов и оснастки, выбирать виброустойчивые диапазоны режимов резания. Эти работы приобретают особое значение в связи с возрастающим использованием многооперационных станков с ЧПУ и гибких производственных модулей;
4) исследовать и разрабатывать методы и средства управления уровнем интенсивности автоколебаний в целях повышения периода стойкости инструмента, производительности и качества обработки;
5) контролировать техническое состояние оборудования.
9. Тепловые явления в процессе резания
Технологическая система может функционировать только при подводе к ней энергии. В процессе выполнения операций энергия полностью или частично преобразуется из одного вида в другой, например, механическая – в тепловую. При этом источники тепловой энергии по отношению к тому или иному компоненту системы или подсистемы могут быть внешними или внутренними. Чтобы управлять тепловыми процессами, необходимо знать, каким образом и по каким закономерностям происходит теплообмен в технологической системе.
9.1. Основные источники тепловыделения в зоне резания
В процессе резания тепловые явления играют важную роль. Именно они определяют температуру в зоне резания, которая оказывает прямое влияние на характер образования стружки, нарост, усадку стружки, силы резания и микроструктуру поверхностного слоя. Еще более существенно воздействует температура резания q на интенсивность затупления инструмента и период его стойкости.
Выделение теплоты при снятии стружки объясняется тем, что в теплоту преобразуется механическая работа, затраченная на срезание стружки (см. выше):
где Wдеф – работа, затрачиваемая на упругую и пластическую деформации срезаемого слоя;
Wтр.пер.пов. и Wтр.задн..пов – работа, затрачиваемая на преодоление сил трения по передней и задней поверхностям соответственно.
Таким образом, при резании существуют три основных источника тепла (рисунок 38):
1) внутреннее трение между частицами срезаемого слоя в результате его деформации при образовании стружки (Qдеф);
2) трение стружки о переднюю поверхность инструмента (Qтр.пер.пов.);
3) трение поверхности резания и обработанной поверхности по задним поверхностям инструмента (Qтр.задн.пов.).
Рисунок 38 – Источники образования тепла в зоне резания.
Наиболее интенсивно выделение тепла происходит в области стружкообразования, прилегающей к плоскости сдвига. В этой области теплота выделяется в результате двух одновременно протекающих процессов: во-первых, в результате пластической деформации сдвига элементов образующейся стружки по плоскости сдвига; во-вторых, в результате пластической деформации сжатия и частично пластической деформации смятия тонкого слоя металла примыкающего к плоскости сдвига со стороны срезаемого слоя припуска.
Общее количество выделяющегося при резании тепла равно сумме тепла, выделившегося во всех перечисленных выше источниках:
Qобщ = Qдеф + Qтр.пер.пов. + Qтр.задн.пов.
Тепло, образующееся в процессе резания, не аккумулируется в местах его образования, а распространяется от точек с более высокой температурой к точкам с низкой температурой. Из зоны резания тепло уносится со стружкой (Qс), передается в деталь (Qд) и инструмент (Qи), и распространяется в окружающую среду (Qо.с). Тепловой баланс процесса резания может быть выражен уравнением:
Qдеф + Qтр.пер.пов. + Qтр.задн.пов. = Qс + Qд + Qи + Qо.с.
Соотношение количества тепла, отводимого со стружкой в деталь, в инструмент и окружающую среду, зависит от физико-механических свойств обрабатываемого материала, режима резания, геометрии режущего инструмента и внешних условий, в которых осуществляется резание.
В начале обработки температура в зоне резания растет до какого-то определенного значения и устанавливается постоянной, соответствующей стационарному тепловому режиму, при котором выделение тепла равняется отводу его по перечисленным направлениям. Для практических целей наибольший интерес представляет температура рабочей части инструмента и обрабатываемой заготовки. Тепло, переходящее в заготовку, увеличивает ее температуру и вызывает температурное изменение ее размеров и коробление, подчас являющееся причинами брака.
Теплота, переходящая в инструмент, при всей своей относительной незначительности, концентрируясь в малых объемах материала инструмента, вызывает сильный разогрев его в этих объемах и снижение режущих свойств и износоустойчивости инструмента. С увеличением скорости резания доля тепла, переходящего в инструмент, уменьшается, но абсолютное его количество возрастает и температура в зоне резания увеличивается до значений, близких к температуре красностойкости металла инструмента.
Практически в теплоту переходит вся работа резания (больше, чем 99,5%). Поэтому, зная количество теплоты, выделяемой в процессе резания и распространяемой между стружкой, обрабатываемой деталью, инструментом и средой, можно записать уравнение баланса тепловой и механической энергии при резании
,
где Qc, Qи, Qд, Qoc — количество теплоты, переходящее соответственно в стружку, инструмент, деталь и окружающую среду.
Эксперименты показывают, что при работе с небольшой скоростью резания (до 30...40 м/мин) относительное количество теплоты составляет: Qc » 60...70%; Qи » 3%;. Qд » 30… 40%; Qо.с. » 1 … 2%. Установлено, что чем ниже теплопроводность обрабатываемого материала, тем больше теплоты уходит в инструмент. По мере увеличения скорости резания значительно растет относительное количество теплоты, уходящей в стружку. Использование технологических сред позволяет значительно повысить Qo.c в общем тепловом балансе. В зависимости от условий подвода среды соответственно уменьшаются Qc, Qи, и Qд.
9.2. Температурное поле резца
Совокупность мгновенных значений температуры в различных точках зоны резания называется температурным полем. Температурное поле дает наиболее яркую и полную картину температурной обстановки в зоне резания.
Наибольшее количество теплоты концентрируется в тонких слоях стружки, прилегающих к передней поверхности. Здесь температура намного превышает температуру в зоне сдвига. По мере удаления от передней поверхности резца температура слоев стружки резко падает. В прирезцовом слое максимальная температура наблюдается в середине длины площадки контакта. От этой области температура убывает как по направлению к режущей кромке, так и по направлению к точке отрыва стружки от передней поверхности. Температура обрабатываемого материала, лежащего ниже поверхности резания, значительно меньше температур в стружке и на площади сдвига.
Режущий клин также нагревается неравномерно. Сильнее всего разогрет участок передней поверхности, расположенный в середине длины площадки контакта, тогда как у вершины уровень температур меньше. По мере удаления от передней поверхности температура в режущем клине изменяется гораздо менее значительно, чем температура стружки.
Уровень и распределение температур в значительной степени определяется теплофизическими характеристиками обрабатываемого и инструментального материалов. Так, при повышении коэффициента теплопроводности инструментального материала температуры на передней поверхности уменьшаются, а на задней — увеличиваются. При повышении коэффициента теплопроводности обрабатываемого материала температуры снижаются. При работе с малыми сечениями среза интенсифицируется тепловой поток со стороны задней поверхности, и температура на задней поверхности существенно возрастает.
В тех случаях, когда нет необходимости в изучении законов распределения температур на контактных площадках или в теле инструмента и детали, наиболее удобным показателем тепловой напряженности процесса резания является средняя температура резания на всей поверхности контакта инструмента со стружкой и деталью.
9.3. Методы измерения температур в зоне резания
Калометрический метод заключается в том, что стружка собирается в калориметре с водой. Зная количество воды в калориметре, массу стружки и ее теплоемкость, можно определить среднюю температуру стружки по разности температуры воды в калориметре до, и после резания:
,
где qстр – средняя температура стружки;
qсм –температура смеси воды и стружки в калориметре;
mв – масса воды в калориметре;
qв – температура воды в калориметре до добавления стружки;
mстр –масса стружки;
сстр –теплоемкость стружки.
Есть также калориметры, в которые погружают деталь и инструмент.
Метод термокрасок заключается в том, что на контактные площадки инструмента наносятся специальные составы, изменяющие свой цвет под действием температур.
Термоэлектрический метод заключается в том что если нагреть место спая двух проводников из различных металлов, оставляя при этом свободными концы при более низкой температуре, на последних возникает термоЭДС, которая зависит от разности температур спая и более холодных концов проводников. Замыкая цепь через вольтметр, можно измерить термоЭДС. Такая цепь называется термоэлектрической. Этот метод является наиболее распространенным и имеет следующие разновидности.
Метод искусственной термопары заключается в том, что в инструменте просверливается отверстие малого диаметра, не доходящее до какой-либо точки передней или задней поверхности примерно на 0,2...0,5 мм. В это отверстие вставляется изолированная термопара (рисунок 39). Температура в точке соприкосновения термопары и инструмента регистрируется включенным в цепь термопары гальванометром.
Рисунок 39 – Схема измерения температуры резания методом искусственной термопары
Этот метод дает возможность определить температуру различных точек на передней и задней поверхностях инструмента и на поверхности стружки, т. е. найти температурное поле.
Недостатками классической схемы искусственной термопары является сложность устройства и невозможность определить наивысшую температуру, так как измерение температуры фактически производится не на поверхности контакта резца и стружки, а на некотором удалении от них.
Метод скользящей (бегущей) термопары. Позволяет получить более точные значения температуры по сравнению с предыдущим методом. Суть этого метода заключается в том, что в заготовку заделываются термопары, которые при перерезании их режущим лезвием инструмента образуют слой термопары, скользящий (бегущий) по передней и задней поверхностям (рисунок 40). Концы термопар через передающую систему подключают к осциллографу. Это позволяет записать распределение температур по длине контакта.
Рисунок 40 – Схема метода «бегущей термопары»
Метод естественной термопары. Элементами термопары служат деталь и инструмент, которые, будучи разнородными металлами, в процессе резания имеют сильно нагретый контакт, являющийся спаем этой термопары (рисунок 41). Концы инструмента и детали имеют значительно более низкую температуру.
1 – обрабатываемая заготовка, 2 – резец, 3 – изоляция, 4 – милливольтметр
Рисунок 41 – Схема метода естественной термопары
Для устранения дополнительных паразитных термопар, возникающих в местах стыка деталей станка с заготовкой, резец и заготовку изолируют от станка. При исследованиях, не требующих высокой точности, установка может быть значительно упрощена. Деталь не изолируют от станка, считая, что роль возникающей дополнительно термопары ничтожна из-за слабого разогревания заднего центра по сравнению с резцом. В связи с этим провод, ранее присоединяемый к детали, можно присоединить к любой точке станка.
Естественные термопары могут также применяться для измерения средних температур на каждой из контактных площадок в отдельности и для изучения закона распределения температур на поверхности соприкосновения стружки с инструментом.
Естественная термопара измеряет некоторую среднюю температуру, тогда как на площадках контакта в процессе резания развивается различная температура в разных точках контакта. Отношение этой средней температуры к наивысшей непостоянно.
Метод бесконтактного измерения температур представляет собой регистрацию теплового излучения отдельных участков детали или инструмента в процессе обработки. Он может быть основан на разных принципах. Например, так называемый фотоэлектрический метод состоит в том, что тепловое излучение с участка нагретой поверхности собирается с помощью линз и направляется на фотосопротивление. Под действием теплового излучения в фотоэлементе возникает ток, который повышается усилителем и регистрируется измерительным устройством. Также существуют системы, основанные на регистрации инфракрасных лучей, исходящих из зоны резания.
9.4. Влияние различных факторов на температуру резания
Многочисленные исследования зависимости температуры от различных факторов показывают, что температура в зоне резания зависит от физико-механических свойств обрабатываемого материала, режима резания, геометрии режущего инструмента и многих других условий. Наибольшее влияние на температуру в зоне резания оказывает скорость резания, в меньшей степени влияет подача, а влияние глубины резания почти не обнаруживается. Из геометрических параметров режущей части инструмента наиболее сильно на температуру резания влияют передний угол, главный угол в плане и радиус закругления при вершине, сопряжения главной и вспомогательной режущих кромок на вершине режущего лезвия инструмента.
Влияние скорости резания. С увеличением скорости резания возрастает количество теплоты, выделяющейся в зоне резания, а также температура нагрева детали, стружки и инструмента. Однако рост температуры в зоне резания отстает от роста скорости резания. Это отставание особенно усиливается в зоне высоких скоростей, что видно на отдельных участках кривой, представленных на рисунке 42.
Рисунок 42 – Зависимость температуры от скорости резания
С увеличением скорости резания v растет мощность резания N = Pzv и, следовательно, количество выделяемой теплоты. Но непосредственно в резец переходит очень небольшое ее количество, а основное — уносится стружкой. Поэтому, хотя с увеличением скорости резания v температура резания повышается, этот рост все время замедляется. Кроме того, допущение о том, что N = Pzv изменяется пропорционально v , не совсем правильно, так как по мере увеличения v сила резания Рг уменьшается. Унос теплоты стружкой тоже растет с повышением скорости резания, и поэтому нет прямой зависимости изменения температуры резания q от изменения v .
Влияние физико-механических свойств обрабатываемого материала. На силы резания, а, следовательно, на работу резания и количество выделяющейся теплоты, а также на условия теплоотвода оказывают влияние физико-механические свойства обрабатываемого материала. На температуру резания они влияют так же, как и на силу резания Р z , т. е. имеется тенденция к увеличению q с повышением прочности, твердости и пластичности обрабатываемого материала. Большое воздействие на температуру резания оказывает теплопроводность обрабатываемого материала и характер его микроструктуры. Чем выше теплопроводность обрабатываемого материала, тем ниже q , так как отвод теплоты от места ее выделения в стружку и в деталь более интенсивен. Кроме того, при обработке сталей со структурой зернистого перлита сила и температура резания значительно выше, чем при обработке сталей со структурой пластинчатого перлита. Это объясняется тем, что пластичность структуры зернистого перлита гораздо выше, чем у пластинчатого перлита.
В настоящее время довольно широко применяются жаропрочные, нержавеющие и другие труднообрабатываемые стали с высоким содержанием таких легирующих элементов, как Cr, Ni, W, Mn и т. д. Эти стали имеют аустенитную структуру и отличаются низкой теплопроводностью. При обработке таких сталей температура резания значительно выше, чем при обработке обычных сталей перлитного класса. Еще меньше теплопроводность титановых сплавов, а поэтому q при обработке их очень высокая.
Влияние элементов сечения среза. С увеличением ширины среза b1прямо пропорционально растет сила, работа резания и количество выделяющейся теплоты. Во столько же раз увеличивается и длина активной части режущей кромки (рисунок 43), а соответственно и отвод теплоты. Поэтому с увеличением b1температура резания изменяется незначительно.
Рисунок 43 – Длина активной части режущей кромки резца при различной ширине среза
В зависимости от толщины срезаемого слоя а1сила Р z увеличивается примерно в степени 0,75. Также увеличивается работа резания и количество выделяемой теплоты. Одновременно растет, хотя и в меньшей степени, площадь контакта стружки с передней поверхностью резца. Это несколько улучшает условия отвода теплоты, поэтому увеличение температуры отстает от роста толщины среза.
Влияние геометрических параметров инструмента. С изменением переднего угла g инструмента изменяются условия подвода и отвода теплоты, а, следовательно, и температуры резания. С увеличением g уменьшается сила, а, следовательно, и работа резания, а также количество выделившейся теплоты. Однако при этом ухудшаются условия ее отвода, так как уменьшается угол заострения b. Поэтому существует некоторый оптимальный угол g , при котором уменьшаются силы резания и количество выделившейся теплоты. С увеличением g выше оптимального уменьшается угол заострения b, ухудшаются условия теплоотвода, растет температура резания (рисунок 44). Аналогично влияет на температуру также задний угол a.
С уменьшением главного угла в плане j увеличивается угол при вершине e, что приводит к возрастанию угла заострения b, а значит и массы головки резца, и улучшению теплоотвода, а, следовательно, к уменьшению q, и наоборот (рисунок 45).
Рисунок 44 – Зависимость температуры резания от переднего угла инструмента
Рисунок 45 – Зависимость температуры резания от главного угла инструмента в плане
10. Износ и стойкость режущих инструментов
Режущий инструмент в процессе резания воздействует на обрабатываемый материал и вызывает образование стружки и формирование новой поверхности, однако сам при этом подвергается воздействию со стороны обрабатываемого материала и интенсивно изнашивается. Режущие инструменты работают в чрезвычайно тяжелых условиях действия громадных давлений на поверхностях контакта и высокой температуры, в условиях трения чистых, вновь образованных ювенильных (чистых) поверхностей. По этим причинам интенсивность изнашивания режущих инструментов в тысячи и десятки тысяч раз превосходит интенсивность изнашивания трущихся деталей машин. Например, износ шеек коленчатых валов двигателей внутреннего сгорания, до предельно допустимой величины происходит после пути трения 106 … 109 метров, а износ режущих инструментов до установленной нормативной величины износа, наблюдается уже после пути трения всего лишь 103 … 104 метров. Путь трения при резании легко определяется умножением скорости резания (м/мин) на величину стойкости (мин). Так, например, при скорости резания 100 м/мин и нормативной стойкости 30 мин, путь, пройденный режущим инструментом по поверхности резания, составит: 3×103 метров, что подтверждает сказанное выше сравнение интенсивности изнашивания трущихся деталей машин и режущих инструментов.
В результате изнашивания режущее лезвие инструмента теряет свою первоначальную форму и, как следствие, режущую способность. Для восстановления режущей способности инструмента производится затачивание его рабочих поверхностей. В процессе затачивания инструмента с его рабочей части срезаются довольно большие слои дорогостоящего инструментального материала. Кроме того, на смену затупившегося инструмента затрачивается время, которое увеличивает продолжительность операции механической обработки, а следовательно и ее стоимость; срезаемый при затачивании абразивным инструментом дорогостоящий инструментальный материал переводится в шлам и безвозвратно теряется. В целом все это существенно удорожает механическую обработку и ограничивает ее эффективность. Поэтому, задача уменьшения интенсивности изнашивания режущих инструментов и увеличения срока его службы была и остается одной из главных задач металлообработки.
10.1. Причины износа инструмента
Рабочие поверхности режущего инструмента изнашиваются как от механического воздействия на него обрабатываемого материала, так и в результате молекулярно-термических процессов происходящих в зоне резания на поверхностях контакта инструмента с обрабатываемым материалом. Инструмент может подвергаться различным по своей природе, видам изнашивания: абразивному, адгезионному, химическому, диффузионному, электроэрозионному и другим. В процессе резания все эти виды изнашивания могут иметь место, но в зависимости от конкретных условий один из них является доминирующим, определяющим интенсивность изнашивания и стойкость режущего инструмента.
1. Абразивное изнашивание. Механизм абразивного изнашивания заключается в том, что твердые включения обрабатываемого материала, внедряясь в контактные поверхности инструмента, царапают их как микроскопические резцы, вызывая износ. Абразивное действие оказывают частицы нароста, карбиды, интерметаллиды, оксиды и другие включения высокой твердости.
Особенно это проявляется, когда твердость инструментального материала в процессе резания падает, а обрабатываемый материал упрочняется.
При резании в химически активных средах, например в четыреххлористом углероде, абразивное действие может возрастать вследствие разупрочнения поверхностных слоев инструментального материала, вступившего в химические реакции со средой. Такие слои легче поддаются разрушению абразивными частицами, а изнашивание получило название абразивно-химического.
2. Адгезионное изнашивание. Возникает за счет молекулярного взаимодействия инструментального и обрабатываемого материалов на участках пластического контакта. Если силы молекулярного сцепления двух разнородных материалов (силы адгезии) превышают силы молекулярного сцепления частиц однородного материала (силы когезии), то происходит вырыв частиц инструментального материала. Продукты износа уносятся из зоны резания стружкой и поверхностью резания. Разрушение может проходить как в объеме инструментального материала, так и по объему менее прочного обрабатываемого материала. В этом случае образовавшийся на поверхности инструмента налип вызывает осложнение перемещения стружки, дополнительное ее деформирование и локальное повышение температуры, которое приводит к ослаблению сил металлической связи инструментального материала.
Высокие давления в зоне контакта увеличивают его истинную площадь. Сам процесс непрерывного перемещения стружки и обрабатываемого металла вдоль поверхностей инструмента способствует образованию сильных металлических связей, при этом разрушаются слои поверхностных оксидов и других адсорбированных пленок. Поэтому явления адгезии при резании проявляются наиболее четко.
Однако процесс резания, способствуя возникновению адгезии, в то же время непрерывно разрушает возникающие мостики схватывания вследствие перемещения инструмента, стружки и детали друг относительно друга. Образование и разрушение мостиков производится непрерывно, и на контактирующих участках действуют циклические нагрузки. В результате усталостных явлений происходит разрушение под поверхностью контакта, в том числе и в инструментальном материале. Установлено, что размеры вырванных частиц зависят не от твердости или прочности инструментального или обрабатываемого материала, а от их соотношения в контакте.
Интенсивность адгезионного изнашивания сильно зависит от температуры резания (рисунок 45). При определенных температурах имеется максимум износа. Причем, чем прочнее обрабатываемый материал, тем больше максимальный износ и тем при большей температуре он наблюдается. При дальнейшем повышении температуры происходит резкое снижение адгезионного износа по причине смягчения мостиков схватывания.
3. Диффузионное изнашивание. Протекает на атомном уровне за счет диффузии атомов химических элементов инструментального материала в стружку и в заготовку (прямая или активная диффузия). От заготовки к стружке идет встречная диффузия атомов химических элементов (обратная или реактивная диффузия).
Обе (прямая и обратная) диффузии сильно изменяют химический состав поверхности инструментальной пластины, снижая прочность поверхностного слоя. Таким образом, на пластине образуется дефектный слой, который легко удаляется сходящей стружкой.
Рисунок 45 – Зависимость интенсивности адгезионного износа от температуры резания
Увеличение температуры приводит к резкому увеличению интенсивности диффузии.
4. Химическое изнашивание. Кислород воздуха и СОТС окисляет поверхность инструментальной пластины, возникают пленки из окислов, которые быстро удаляются стружкой и поверхностью резания.
5. Электроэрозионное изнашивание. Происходит в результате действия электрического тока, образующегося под влиянием термоэлектродвижущей силы (ТЭДС). В связи с тем, что инструмент и обрабатываемый материал контактируют в отдельных точках с разной температурой, в каждой точке действует ТЭДС разной величины. В результате в зоне резания образуется сложная система электрических цепей (контуров), при разрыве которых происходит перенос капли одного из материалов на поверхность другого в зависимости от знака заряда поверхности. При переносе капли обрабатываемого материала на поверхность инструмента она приваривается к поверхности инструмента и образует порог, который выламывается вместе с объемом инструментального материала. Кроме того, твердая затвердевшая капля проволакиваясь между обрабатываемым материалом и инструментом царапает поверхность последнего и усиливает абразивное изнашивание. Такой механизм изнашивания, надо полагать, значительно усиливает изнашивание твердосплавных инструментов, работающих при больших скоростях резания, при которых в зоне резания развиваются ТЭДС до нескольких десятков милливольт, а температура находится в пределах 1000 . Твердая частица в этом случае легко выскабливает размягченную и выдавленную на поверхность кобальтовую связку, недостаток которой ослабляет соединение твердых карбидных зерен твердого сплава. Выкрашивание их приводит к лавинообразному развитию изнашивания инструмента.
10.2. Характер износа режущих инструментов.
Первые признаки изнашивания режущих лезвий обнаруживаются уже в начале резания. При осмотре режущих лезвий с помощью микроскопа заметны микровыкрашивания на режущих кромках и в местах их сопряжения, возрастание радиусов округления кромок, появление вдоль главной режущей кромки узкой светлой полоски. Эта полоска и является признаком начала изнашивания. В процессе работы инструмента увеличиваются размеры площадок износа. В зависимости от условий резания эти площадки могут образовываться на разных участках лезвий инструмента.
Инструмент изнашивается как по передней, так и по задней поверхностям. На передней поверхности образуется лунка износа, а на задней – фаска износа (рисунок 46).
Износ режущего инструмента только по задней поверхности наблюдается при обработке хрупких материалов, при резании которых образуется стружка надлома, не представляющая собой сплошного прочного тела. Износ по задней поверхности является также превалирующим в случае резания с малыми толщинами среза, при малых значениях задних углов и при обработке сталей и сплавов, обладающих ярко выраженным упругим последствием и сильным обработочным упрочнением.
hз – фаска износа по задней поверхности;
lл – длина лунки износа;
hл – глубина лунки износа;
fл – расстояние между фаской износа и передней границей лунки износа
Рисунок 46 – Параметры износа режущего инструмента
Износ режущего инструмента только по передней поверхностипроисходитв случае обработки вязких металлов с большими сечениями среза, когда образуется устойчивый нарост, исключающий контакт задней поверхности с обрабатываемым материалом. В большинстве же случаев практики резания металлов инструмент изнашивается как по передней, так и по обеим задним поверхностям.
Наиболее характерными видами износа по передней и задней поверхностям являются следующие.
1. Равновеликий износ задней поверхности (рисунок 47)
Рисунок 47 – Равновеликий износ задней поверхности инструмента
2. Неравномерный износ задней поверхности (рисунок 48)
Рисунок 48 – Неравномерный износ задней поверхности инструмента
3. Местный износ задней поверхности (рисунок 49).
Рисунок 49 – Местный износ задней поверхности инструмента
4. Износ вершины резца (рисунок 50)
Рисунок 50 – Износ вершины резца
5. Комбинированный износ (рисунок 51)
Рисунок 51 – Комбинированный износ
6. Лунка на передней поверхности (рисунок 52)
Рисунок 52 – Лунка на передней поверхности
Изнашивание передней поверхности происходит, как правило, на некотором удалении от главной режущей кромки. Образующаяся лунка с течением времени работы резца углубляется и незначительно расширяется в сторону от режущей кромки. Износ инструмента полностью характеризуется указанными ниже параметрами.
10.3. Критерии затупления и стойкость режущего инструмента
Критерий отказа инструмента, характеризуемый максимально допустимым значением износа режущего лезвия, после достижения которого наступает его отказ, называется критерием затупления.
Критерии зависят от характера обработки и обрабатываемого материала. Например, о возрастании изнашивания инструмента можно судить по быстрому росту сил резания. Такой критерий затупления называется силовым.
Если к выполняемой операции не предъявляются высокие требования точности и шероховатости обработанной поверхности, целесообразно доводить инструмент до такой степени износа, при которой полный период его стойкости наибольший. Такой критерий затупления называется оптимальным.
Полный период стойкости инструмента
где Т — период стойкости инструмента, соответствующий данному износу;
k — количество переточек, допустимых инструментом при данном износе.
Размеры площадки износа инструмента могут ограничиваться требованиями обеспечения необходимого качества или точности обработанной поверхности. Такие критерии называются технологическими.
С увеличением времени работы инструмента нарастает его износ hз, причем кривая износа имеет следующий принципиальный характер (рисунок 53).
На кривой износа существуют три зоны.
I) Зона приработки. Износ растет быстро за счет стирания дефектного слоя на инструментальной пластине, возникшего при заточке инструмента.
II) Зона нормального износа. Темпы износа сохраняются постоянными. Эта зона составляет основной срок эксплуатации режущего инструмента.
III) Зона катастрофического износа. В точке D передняя граница лунки износа встречается с фаской износа.
Рисунок 53 – Кривая износа
В этой связи рекомендуется эксплуатировать инструмент до точки С, определяя допустимый износ инструмента . Этот допустимый износ определяется указанными выше критериями затупления.
Время работы инструмента до достижения предельно допустимого износа называют стойкостью инструмента Т.
10.4. Количественные параметры износа режущего инструмента
Для анализа вопросов, связанных с работой инструмента в автоматизированном производстве, важное значение имеет его размерная стойкость, под которой понимают способность инструмента обеспечивать получение деталей с определенной точностью. Например, при точении износ задней поверхности резца сопровождается увеличением диаметра обработанной детали на удвоенный радиальный износ hp (будет конус)(рисунок 54):
.
Рисунок 54 – Изменение размеров обработанной детали при радиальном износе инструмента
Для резца с острозаточенной вершиной значения h р можно найти по формуле
.
Экспериментально его можно определить с помощью микроскопов или датчиков положения вершины инструмента.
Размерную стойкость инструментов можно характеризовать продолжительностью их работы без подналадки или замены, количеством обработанных деталей, длиной пути резания, площадью обработанной поверхности и объемом снятого металла. Все перечисленные характеристики являются частными и в общем случае не пригодны для выбора оптимальных условий ведения автоматических процессов обработки резанием, поскольку не учитывают уровни скорости резания и допустимого затупления. Например, по периоду стойкости нельзя судить о размерной стойкости сравниваемых инструментов, если последние работали при различных скоростях резания и подачах и были доведены до разной степени затупления.
Более объективными можно считать такие показатели износа, как:
1) относительный радиальный линейный износ (мкм/м):
;
2) скорость размерного износа (мкм/мин):
;
3) относительный радиальный поверхностный износ :
;
4) относительный радиальный объемный износ :
,
где hp, hp.н– соответственно предельный радиальный износ и начальный радиальный износ (после периода приработки) (мкм);
L, Lн –пути резания и приработки (м);
Т, Тн– периоды размерной стойкости и приработки (мин);
Sо.п– площадь обработанной поверхности (мм2);
Vc.м– объем снятого металла (мм3).
11. Формирование качества поверхностного слоя деталей
В современном машиностроении к выпускаемой продукции предъявляются высокие требования. Эксплуатационные показатели отдельных деталей, образующих механизмы и узлы машин, зависят не только от вида материала, но и от того, как и по какому технологическому процессу они изготовлены.
Под качеством поверхности детали понимают свойства ее поверхностного слоя, которые формируются в результате воздействия на поверхность одного или нескольких последовательно применяемых технологических методов обработки. Качество поверхностей деталей определяется геометрическими и физико-механическими характеристиками поверхностного слоя. Классификация показателей качества поверхностей деталей приведена на рисунке 55.
Рисунок 55 – Классификация показателей качества поверхностей деталей.
Шероховатость поверхности представляет совокупность неровностей с относительно малыми шагами, образующих ее рельеф в пределах базовой длины.
Микронеровности формируются в результате взаимодействия обрабатываемой поверхности с элементами режущего инструмента или обрабатывающих сред.
Волнистость представляет совокупность периодически повторяющихся неровностей на поверхности детали.
Причиной появления волнистости является недостаточная жесткость и колебания в ячейках технологической станочной системы. При изучении микрорельефа поверхности (шероховатости) отношение шага к высоте неровностей не превышает 50, а макрорельефа (волнистости) — отношение шага волны к ее высоте значительно больше: 50…1000.
Физико-механические свойства поверхностного слоя. Тонкий поверхностный слой деталей машин имеет иные механические, физические, химические свойства и напряженное состояние, чем в глубинной части металла. Глубина поверхностного слоя в зависимости от вида обработки находится в пределах от нескольких десятитысячных до сотых и десятых долей миллиметра, оказывая большое влияние на работоспособность деталей машин. Отличие свойств тонких поверхностных слоев от свойств сердцевины обусловлено наличием свободной поверхностной энергии и большой адсорбционной активностью поверхности; суммой механических, тепловых и физико-химических воздействий на поверхность металла при обработке резанием.
11.1. Механизм возникновения шероховатости
Все причины образования шероховатости обработанной поверхности можно разбить на три группы, связанные:
1) с положением режущих кромок инструмента относительно обработанной поверхности;
2) упругой и пластической деформацией обрабатываемого материала;
3) возникновением вибраций в технологической станочной системе.
Образование неровностей обработанной поверхности в первом приближении можно представить как след рабочего движения режущей кромки (или кромок) инструмента в поверхностном слое металла (рисунок 56). Назовем такой профиль регулярным. На образование регулярного профиля шероховатости влияет геометрия режущего инструмента, в частности главный и вспомогательный углы в плане j и j1, радиус вершины резца r и подача s.
Рисунок 56 – Схема образования шероховатости поверхности
Исходя из геометрических соотношений расчетная высота неровностей для резца с незакругленной вершиной
.
Для резца, вершина которого закруглена радиусом r (при s > r), используется эмпирическая зависимость
.
Из приведенных формул следует, что чем больше s, j и j1 и меньше r , тем высота неровностей больше, и наоборот. Указанную шероховатость называют поперечной (ее измеряют в направлении подачи). Одновременно образуется и продольная шероховатость, измеряемая вдоль главного движения инструмента (или детали). Обычно поперечная шероховатость больше продольной, и поэтому она сильнее влияет на эксплуатационные свойства обработанных поверхностей.
В реальном процессе обработки металлов резанием впереди резца и под обработанной поверхностью образуется определенная зона пластической деформации. Это вносит существенные искажения в регулярный профиль поверхности (рисунок 57), так как пластически деформированный металл в отдельных местах как бы наволакивается, а также вырываются отдельные кусочки металла. Поэтому чем меньше поверхностная пластическая деформация, тем ближе фактический профиль подходит к регулярному.
1 – регулярный профиль
2 – искаженный (действительный) профиль
Рисунок 57 – Искажение профиля
Исходя из изложенного, реальное значение Rz в общем виде может быть выражено уравнением
,
где Rz pacч — расчетная величина гребешков;
DRz — приращение высоты неровностей.
где DRz пл — приращение высоты неровностей в результате пластического течения металла в направлении вершины остаточного гребешка;
DRz упр — приращение, вызванное упругим восстановлением поверхностного слоя;
DRzз — приращение, вызванное трением задней поверхности инструмента об обработанную поверхность.
При затуплении режущего инструмента шероховатость обработанной поверхности возрастает:
при точении на 50...60 %,
фрезеровании цилиндрическими фрезами на 100...115%,
фрезеровании торцовыми фрезами на 35...45%,
сверлении на 30...40 %,
развертывании на 20...30 %.
Это объясняется увеличением пластической деформации металла поверхностного слоя.
Уменьшить пластическую деформацию, а следовательно, и искажения регулярного профиля поверхности можно увеличением переднего угла, а также скорости резания, проведением соответствующей термической обработки металла (например, нормализации или улучшения), применением СОЖ и т. д.
Как уже отмечалось, влияние скорости резания на высоту микронеровностей проявляется по-разному, в зависимости от того, склонен или нет обрабатываемый материал к наростообразованию (рисунок 58).
Рисунок 58 – Типовые зависимости шероховатости обработанной поверхности от скорости резания и подачи
В широком диапазоне скоростей и подач уровень шероховатости может неоднократно изменяться. Это обусловлено одновременным протеканием таких процессов, как наростообразование, изменение направления тепловых потоков, изнашивание контактных площадок инструмента, массоперенос, разрушение режущих кромок инструмента и др. Однако существует такое оптимальное их сочетание, при котором высота микронеровностей оказывается минимальной. Сложный характер зависимости шероховатости от подачи можно объяснить тем, что при уменьшении последней уменьшается и толщина среза. Радиус округления режущей кромки оказывается соизмеримым с толщиной среза, и процесс стружкообразования в таких условиях становится неустойчивым, вследствие чего возрастают силы трения на задней поверхности и высота микронеровностей.
Зависимость шероховатости от износа инструмента также неоднозначна. Если при относительно больших толщинах среза изнашивание приводит к росту шероховатости обработанной поверхности, при тонких процессах она в определенном диапазоне значений h з может несколько уменьшаться. Это, очевидно, вызывается своего рода «естественной оптимизацией» геометрических параметров инструмента по мере изнашивания его режущих кромок.
Для различных видов обработки резанием при одних и тех же режимах шероховатость поверхности получается различной в зависимости от свойств материала обрабатываемых деталей. При обработке более твердых материалов высота микронеровностей получается меньшей, чем при обработке мягких. Вязкие и пластичные материалы более склонны к пластическим деформациям и при обработке резанием дают более грубые поверхности. Недостаточная жесткость в ячейках технологической системы и возникающие вибрации вызывают перемещение лезвия режущего инструмента относительно поверхности обрабатываемой детали, что ведет к увеличению шероховатости.
11.2. Формирование физико-механических свойств поверхностного слоя металла
11.2.1. Упрочнение (наклеп) поверхностного слоя
В процессе резания металлов зерна в поверхностном слое вытягиваются в направлении действия силы резания. Кристаллиты в основном ориентируются по кристаллографическим направлениям. Подобная ориентировка мелких зерен, вытянутых по направлению деформации, называется текстурой.
При пластической деформации происходит возникновение и концентрация дислокаций (нарушение в отдельных местах правильного строения кристаллической решетки) около линий сдвигов. Поскольку дислокации окружены полями упругих напряжений, для последующих деформаций потребуется значительно большее усилие, чем в недеформированном металле. Это связано с необходимостью преодоления сопротивления полей напряжений. Следовательно, при резании пластическая деформация вызывает наклеп поверхности, за счет чего последняя упрочняется, повышается ее микротвердость и снижается пластичность.
При наклепе наблюдается снижение электропроводности, теплопроводности и плотности металла, что объясняется увеличением количества дислокаций и вакансий в наклепанном металле. В общем случае с увеличением сил резания и продолжительности их воздействия возрастает пластическая деформация поверхностного слоя металла, а следовательно, увеличивается степень его упрочнения N и глубина распространения наклепа hc . Так, например, они возрастают с увеличением подачи и уменьшаются с ростом скорости резания (рисунок 59).
Рисунок 59 – Зависимость степени N и глубины hc наклепа от подачи и скорости резания
Установлено, что возможности упрочнения металла за счет его наклепа ограничены, и при чрезмерном пластическом деформировании может образоваться «перенаклеп» металла, что приводит к его разупрочнению. Разупрочнение происходит при исчерпании зернами металла возможности упрочняться. При этом наблюдается его разрыхление, появление трещин, отслаивание и т. д.
Наклеп в поверхностном слое приводит металл в структурно-неустойчивое состояние, вызванное неодинаковым распределением внутренних напряжений между отдельными зернами и даже целыми участками металла. В этих условиях возникает явление отдыха, т. е. стремление металла к возвращению в первоначальное, ненаклепанное состояние, чему способствует упругая деформация наклепанного металла, а также повышенная температура в зоне резания. При комнатной температуре отдых наклепанного металла протекает довольно медленно, однако уже при небольшом нагреве процесс ускоряется. При этом даже незначительные перемещения атомов могут снять искажения кристаллической решетки. Например, для снятия искажений атомной кристаллической решетки железа достаточно нагреть его до 200...300 °С, после чего механические свойства железа частично восстанавливаются.
При данных температуре и упрочнении, чем дольше металл подвергается отдыху, тем полнее происходит восстановление свойств, которые металл имел до пластической деформации, т. е. тем полнее его отдых.
При обработке металлов резанием одновременно действуют значительные силы резания, создающие наклеп, и температура, вызывающая разупрочнение металла. Конечное состояние поверхностного слоя определяется соотношением процессов упрочнения и разупрочнения, зависящих от преобладания в зоне резания силового или теплового фактора. В связи с этим всякое изменение режимов резания, вызывающее увеличение усилий резания и степени пластической деформации, ведет к повышению степени наклепа. Увеличение продолжительности их воздействия на поверхностный слой приводит к увеличению глубины распространения наклепа.
Изменение режимов, приводящее к увеличению количества теплоты в зоне резания и увеличивающее продолжительность теплового воздействия, усиливает интенсивность отдыха, снимающего наклеп поверхностного слоя. Влияние указанных явлений на конечное состояние поверхности отмечено, в частности, при точении порошковых материалов после их химико-термической обработки. Микротвердость в этом случае возрастает в зоне низких скоростей вследствие вибраций и в зоне высоких — вследствие вторичной закалки.
11.2.2. Остаточные напряжения в поверхностном слое
Остаточными напряжениями называют напряжения в поверхностном слое деталей, которые существуют при отсутствии каких-либо внешних воздействий, например температурных или силовых.
Можно предложить следующую схему формирования остаточных напряжений в ходе лезвийной обработки. Вследствие трения задней поверхности инструмента об обработанную поверхность в поверхностных слоях последней возникает пластическая, а ниже — упругая деформация растяжения. По мере движения режущего клина и снятия нагрузки упругорастянутые слои стремятся возвратиться в исходное состояние, но этому препятствуют пластически деформированные слои. В результате внутренние области оказываются частично растянутыми, а в поверхностных слоях возникнут остаточные напряжения сжатия.
Остаточные напряжения могут возникнуть в связи с локальным нагревом поверхности обрабатываемой детали. Под действием теплового фактора поверхностные слои стремятся удлиниться, но этому препятствуют более холодные, расположенные в глубине металла, и в поверхностном слое возникают напряжения сжатия. При охлаждении наблюдается обратная картина с образованием растягивающих напряжений. Результирующую эпюру напряжений следует рассматривать как результат одновременного действия силового и теплового фактора.
При обработке резанием металлов, склонных к фазовым превращениям, нагрев в зоне резания может вызывать структурные превращения, связанные, как известно, с объемными изменениями кристаллической решетки металла. Поэтому в слоях со структурой, имеющей больший удельный объем, развиваются напряжения сжатия, а в слоях со структурой меньшего удельного объема — остаточные напряжения растяжения.
В зависимости от вида и режимов обработки в зоне резания возникают различные количество теплоты и напряженность силового поля, в результате чего изменяются уровень и знак остаточных напряжений в поверхностном слое (рисунок 60). При увеличении скорости резания растягивающие остаточные напряжения растут, но глубина их залегания уменьшается. С ростом подачи увеличиваются растягивающие напряжения, но при этом несколько больше и глубина их залегания. При переходе от положительных передних углов к отрицательным растягивающие напряжения резко уменьшаются, но одновременно увеличивается глубина их залегания. Поэтому остаточные напряжения зависят от конкретных условий процесса обработки. Последние должны быть такими, чтобы обеспечить благоприятные остаточные напряжения, повышающие эксплуатационные характеристики деталей.
Рисунок 60 – Характер влияния условий резания на тангенциальные остаточные напряжения и глубину их залегания
12. Смазочно-охлаждающие технологические среды (СОТС) при обработке конструкционных материалов
12.1. Общие требования к СОТС
Применение при обработке резанием смазочно-охлаж-дающих технологических сред (СОТС) повышает период стойкости режущего инструмента, уменьшает силы резания, улучшает качество обработанной поверхности детали, а следовательно, и ее эксплуатационные характеристики. Применение технологических сред — одно из основных направлений интенсификации процесса механической обработки различных материалов.
Все виды СОТС, несмотря на конкретные области их применения, должны удовлетворять следующим требованиям :
1)не снижать эксплуатационные характеристики деталей, изготовленных при их применении, прежде всего коррозионную стойкость и прочность;
2) быть устойчивыми при эксплуатации и хранении;
3) не воспламеняться при температурах, сопровождающих процесс резания;
4) не оказывать аллергического, дерматического или иного вредного воздействия на организм человека;
5) не выделять в процессе эксплуатации пену, дым, клейкие вещества, не смешиваться с машинными маслами;
6) не оказывать окрашивающего или коррозионного действия на узлы и механизмы станка.
12.2. Действие технологической среды в процессе резания
Смазочное действие.
Цель применения СОТС — снижение интенсивности изнашивания режущего инструмента, улучшение качества обработанной поверхности и повышение производительности труда. Достичь этого можно направленным воздействием на элементарные физико-механические и механохимические процессы, протекающие при резании металлов.
В результате смазочного действия технологической среды уменьшаются схватывание, фрикционный нагрев и силы трения при перемещении стружки и обрабатываемого металла по передней и задней поверхностям инструмента. В зависимости от свойств обрабатываемого и инструментального материалов СОТС могут уменьшать или увеличивать схватывание между ними, изменять длину контакта стружки с передней поверхностью и силы резания. Соответственно улучшаются или ухудшаются такие параметры обработки, как период стойкости инструмента, производительность процесса, качество обработанной поверхности и др.
Смазочное действие СОТС осуществляется в значительной степени за счет уменьшения реакционной способности образуемых в процессе резания ювенильных (новых, химически чистых) поверхностей. Эти поверхности характеризуются высокой физической и химической активностью, высокими коэффициентами трения. При отсутствии смазочной пленки наличие ювенильных поверхностей вызывает значительную адгезию, т. е. сцепление поверхностей контактирующих металлов. Вследствие этого резко возрастают силы трения, тепловыделение и т. д. Молекулы поверхностно- и химически активных веществ (ПХАВ), входящих в состав СОТС, адсорбируются на поверхности, снижают адгезию, уменьшают нарост. Вследствие уменьшения интенсивности адгезионных явлений уменьшается длина контакта стружки с передней поверхностью инструмента. Наиболее широко применяемые ПХАВ содержат атомы серы, фосфора, галогенов, группы ОН и СООН, высокомолекулярные органические и металлоорганические соединения.
Смазочное действие по-разному влияет на процесс резания. При лезвийной обработке углеродистых и легированных сталей в зоне низких скоростей резания повышение смазочных свойств СОТС стабилизирует нарост, уменьшает его размеры, прочность и силу сцепления между отдельными слоями. Известно, что в случае нестабильного наростообразования интенсифицируется абразивное изнашивание инструмента. Поэтому, если нарост оказывает защитное действие, например, при резании инструментами из быстрорежущих сталей, использование СОТСможет отрицательно сказаться на их стойкости. С ростом толщины среза и скорости резания влияние СОТС снижается.
При шлифовании смазочное действие способствует повышению периода стойкости круга, позволяет избежать налипов, сократить цикл обработки путем увеличения бесприжоговой подачи.
Охлаждающее действие.
В результате этого действия изменяется температурное поле инструмента, заготовки, стружки, что влияет на период стойкости инструмента, точность обработки, шероховатость и остаточные напряжения в поверхностном слое, форму стружки. При лезвийной обработке это наблюдается, когда скорость резания менее 150 м/мин, а при более высоких скоростях температура обрабатываемой заготовки стабилизируется.
Снижение температуры резания при применении СОТС обеспечивается за счет активного теплоотвода с незанятых стружкой рабочих поверхностей инструмента и, в меньшей степени, с самой стружки. Исходя из прямой взаимосвязи между температурой резания и периодом стойкости инструмента, можно прогнозировать положительное влияние охлаждения. Однако в результате этого процесса могут разупрочняться режущая часть инструмента при прерывистом резании в результате колебаний температуры; образовываться растягивающие напряжения в поверхностном слое; увеличиваться силы резания. Кроме того, при определенных режимах резания может возрастать изнашивание инструмента из-за смещения экстремума интенсивности изнашивания в зону более высоких скоростей резания (рисунок 61).
Теплообмен с СОТС уменьшает радиус завивания стружки, так как приводит к разным тепловым удлинениям ее наружной и прирезцовой сторон. В целом охлаждающее действие уменьшается с увеличением толщины среза и скорости резания.
1— без охлаждения; 2— с охлаждением
Рисунок 61 – Зависимость интенсивности изнашивания инструмента от скорости резания
Моющее действие.
Оно определяется степенью очистки обрабатываемой детали и инструмента в зоне резания от шлама, содержащего мелкие частицы стружки, обрабатываемого металла, инструментального материала, которые удерживаются на поверхности твердых тел электростатическими, электромагнитными и механическими силами. Чем меньше частицы шлама, тем легче они проникают в микронеровности на поверхности инструмента и детали и тем прочнее там удерживаются, ухудшая технологические показатели процесса обработки.
Эффективным моющим действием обладают вещества, хорошо смачивающиеся и адсорбирующиеся на границе раздела металл — жидкость и уменьшающие поверхностное натяжение жидкости. Образующиеся при этом пленки уменьшают адгезию шлама к поверхностям инструмента и детали. К поверхностно-активным веществам, обладающим моющим действием, относятся сульфаты, сульфанолы, мыла, высшие жирные спирты и др. Повышение моющего действия СОТС можно обеспечить за счет увеличения скорости потока и расхода жидкости, подаваемой в зону резания в единицу времени.
Моющим действием можно назвать также удаление частиц стружки с базирующих и крепежных элементов автоматизированного оборудования, на которые подается жидкая технологическая среда (СОЖ) под давлением из специальных сопел перед установкой обрабатываемой детали.
Режущее и пластифицирующее действие.
Под режущими свойствами СОТС понимают ее способность облегчать разрыв связей в обрабатываемом материале при внедрении инструмента. Это способствует повышению стойкости инструмента и облегчению процесса резания. Пластифицирующее действие СОТС заключается в облегчении пластического деформирования металлов за счет локализации деформации в тонких поверхностных слоях. Эти слои выполняют роль смазочного материала и препятствуют налипанию обрабатываемого металла на инструмент, уменьшают трение на контактных площадках и силу резания.
Режущее и пластифицирующее действие вызывается совокупностью физических явлений. К ним, в частности, относится эффект П. А. Ребиндера. Он заключается в изменении механических свойств твердых тел под влиянием на них поверхностных физико-химических процессов. Например, в результате адсорбции ПАВ уменьшается поверхностная энергия обрабатываемого материала. Проникая в микротрещины, которые образуются в процессе пластического деформирования металла, активные жидкости снижают его предел текучести на сдвиг за счет образования поверхностных пленок и создания расклинивающего давления. Например, добавка к чистой воде около 1 % стеариновой кислоты или натриевого мыла почти в два раза облегчает процесс резания.
При попадании поверхностно-активных компонентов жидкости в зону предельно деформированного срезаемого слоя возможно распадение ее на атомы Н, О, N, которые внедряются в кристаллическую решетку наиболее сильно деформированных зерен металла. В результате этого металл упрочняется и переходит в хрупкое состояние. При этом уменьшаются предельная пластическая деформация перед разрушением и удельная работа резания.
Дата добавления: 2021-12-10; просмотров: 83; Мы поможем в написании вашей работы! |
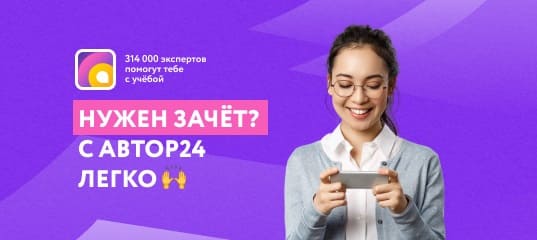
Мы поможем в написании ваших работ!