Колесные пары для определения их технического состояния и пригодности к эксплуатации подвергаются осмотру с регистрацией в книге формы ТУ-28:
Рама тележки
Рама тележки предназначена для соединения в единую систему всех функциональных узлов тележки, восприятия, распределения по колесным парам вертикальной и горизонтальной нагрузки от кузова (при помощи рессорного подвешивания), восприятия тяговых и тормозных сил. Рама является связующим, несущим элементом всех узлов тележки.
Массо-габаритные характеристики рамы тележки:
Длина рамы, мм 4700
Ширина рамы, мм 2580
Высота рамы, мм 1180
Масса рамы тележки, кг 2800
Рама тележки представляет собой цельносварную конструкцию прямоугольной формы в плане, сваренную из двух боковин 4, связанных между собой средней балкой 12 и двумя концевыми балками 15. Боковины и балки коробчатого типа, сварены из четырех листов прокатной стали.
К нижним листам рамы приварены: литые малые 2 и большие буксовые 3 кронштейны, кронштейны 1 под тормозную систему, кронштейн 11 для крепления наклонной тяги и кронштейны 6 для крепления тяговых электродвигателей.
К наружным вертикальным листам боковин приварены накладки боковых упоров.
К верхним листам рам тележек приварены: кронштейны для установки люлечного подвешивания 7, фланцы 5 для крепления вертикальных гидродемпферов и кронштейны 9 для крепления горизонтальных гидродемпферов, кронштейны для крепления вертикальных упоров 10. К вертикальным листам боковины приварены кронштейны 13 для крепления подвесок тормозной системы.
|
|
К вертикальным листам средней балки 12 приварены кронштейны 6, к которым крепятся тяговые электродвигатели и кронштейны 14 тормозной системы.
Тормозная рычажная передача .
Рычажная тормозная система предназначена для передачи силы от тормозных цилиндров или привода стояночного тормоза к тормозным колодкам при торможении.
Система выполнена с двухсторонним нажатием чугунных гребневых колодок на колесо, с приводом от индивидуального тормозного цилиндра на каждую сторону тележки.
Техническая характеристика.
Давление в тормозном цилиндре, кПа (кгс/см2) 372 (3,8)
Нажатие колодок на одну колесную пару, кН (кгс) 164(16840)
Действительный тормозной коэффициент 0,674
Удельное давление тормозных колодок на бандаж, кПа (кгс/см2) 975 (9,95)
Передаточное число 1,43
Диаметр поршня тормозного цилиндра, мм 356
Установочный выход штока, мм 70...85
Максимальный выход штока в эксплуатации, мм 150
На каждой тележке установлено два тормозных цилиндра, каждый из которых воздействует на четыре колодки двух колес одной стороны тележки.
Тормозные цилиндры 14 крепятся шестью болтами M16 каждый, на бобышках среднего бруса рамы тележки. От штоков тормозных цилиндров усилие передается через балансиры 11,16, планки 18 и тяги 13 на подвески 10 и внутренние тормозные колодки и дальше посредством тяг 4 на подвески 1 и наружные тормозные колодки.
|
|
Тормозные колодки 6 при помощи чек 7 крепятся к башмакам 8, которые соединены с подвесками 1 и 10 валиками 9,21. Балансиры 11,16 связаны между собой тягой 13 с помощью валиков 15.
Крайние подвески 1 подвешены к кронштейнам концевых брусьев, а средние подвески 10 через валик башмака и подвеску 20 к кронштейнам боковины рамы тележки.
Верхние концы подвески 10 соединены планками 18 с балансирами 11,16, подвешенными через подвеску 17 к кронштейну среднего бруса рамы тележки и к кронштейну задней крышки цилиндра.
Через фигурные вырезы в нижней части подвесок 1 и 10 проходят поперечины 19, соединенные попарно тягами 4, расположенными с внешней стороны каждой колёсной пары.
Балансиры 11 и 16 внизу соединены тягами 13 постоянной длины. Тяги 4 и поперечины 19 застрахованы от падения на путь при их обрыве тросами 3, 5 и 25, которые закреплены на кронштейнах рамы тележки. Длина тросов выдерживается на 20-25 мм более расстояния между точками их крепления.
|
|
Шарнирные соединения рычажной системы выполнены посредством валиков, поверхности которых закалены на глубину 2-4 мм до твёрдости 45-62 HRCэ и втулок из марганцовистой стали, запрессованных в отверстия сопрягаемых деталей.
Величина выхода штока тормозного цилиндра регулируется изменением длины тяг 4 посредством вращения винта. При исчерпании возможности регулировки выхода штока посредством винта осуществляется ступенчатое регулирование перестановкой валиков 2 в последующее отверстие этих тяг.
Болты 22 служат для регулирования зазоров между колодками и бандажами.
Предельная величина разности зазоров на каждой стороне тележки не более 5 мм.
Зазоры между бандажом и колодками по концам каждой колодки регулируется разворотом колодок на валиках 9, 21 при помощи гаек 23 на крюках 24, предельная величина разности зазоров не более 5 мм, причем больший зазор должен быть на нижнем конце колодки.
Балансир 16 верхним концом упирается в ребро подвески 17, а балансир 11 упирается в головку болта 12, при этом необходимо иметь в виду, что упорным болтом 12 следует пользоваться только лишь при замене тормозного цилиндра 14 и деталей: подвески 17, балансиров 11,16 тяг 13.
|
|
Система смазки гребней колёсных пар.
Система смазки гребней колёсных пар (гребнесмазыватели) предназначена для уменьшения темпа износа гребней колесных пар и боковых граней рельсов.
На раме тележки монтируется исполнительная система гребнесмазывателя состоящая из:
1 - бак объемом 15д м3 для смазки;
2 - масляный фильтр;
3 - форсунка;
4 - маслопровод;
5 - гибкий шланг;
6,7 - штуцер;
8 - кронштейн;
От датчика угла поворота определяется цикличность подачи смазки на гребень и сигнал поступает в электронный блок (установлен в кабине), который подаёт команду с заданной цикличностью на электропневматические клапаны (установленные в кузове), которые открывают доступ сжатого воздуха в форсунки 3.
Кронштейн 8 служит для регулировки зазоров И и К, которые необходимо контролировать и поддерживать по мере износа бандажа.
Форсунки 3 включаются на первой или восьмой колесной паре в зависимости от направления движения.
2.2. Колёсная пара.
Колёсная пара предназначена нести весовые нагрузки всех узлов электровоза, направлять движение электровоза по рельсовому пути, передавать силу тяги, развиваемую электровозом, и тормозную силу при торможении, воспринимать статические и динамические нагрузки, возникающие между рельсом и колесом и преобразовывать вращающий момент тягового двигателя в поступательное движение электровоза.
Техническая характеристика.
Номинальный диаметр по кругу катания, мм 1250
Расстояние между внутренними гранями бандажей, мм 1440
Ширина бандажа, мм 140
Толщина нового бандажа по кругу катания, мм 90
Допускаемая в эксплуатации толщина изношенного бандажа по кругу катания, мм, не менее 45
Колесная пара состоит из оси 5, колесных центров 4, бандажей 2, бандажных колец 1, зубчатых колес 3.
Ось колесной пары - кованая из специальной осевой стали. Для монтажа на ней колес и буксовых узлов имеются специально обработанные участки: буксовые, предподступичные, подступичные шейки и моторно-осевые шейки. Все поверхности оси, за исключением торцов, подвергнуты шлифовке и упрочняющей накатке роликом.
На буксовых шейках имеется резьба для гаек, закрепляющих приставные кольца роликовых подшипников.
На торцах оси выполнено по два отверстия М16-6Н для крепления планок, предохраняющих гайки от ослабления и отвинчивания.
После окончательной механической обработки ось подвергается неразрушающему контролю на отсутствие поверхностных и внутренних дефектов.
Средняя часть – 200мм.;
Две шейки под МОП - 205мм.;
Две подступечные части – 235мм. для напресовки на них колесных центров;
Две предступечные части – 210мм., для напресовки на них лабиринтных колец;
Колесные центры 4 коробчатого сечения отлиты из стали 20Л или 25Л.
На удлиненные ступицы колесных центров горячим способом с натягом в пределах 0,25...0,33 мм. напрессованы зубчатые колеса.
Бандаж 2 изготавливается из специальной стали.
Профиль бандажа изготавливается по требованиям ГОСТ 11018 и инструкции №ЦТ/329. Правильность профиля проверяется специальным шаблоном.
Бандаж посажен на обод колесного центра в горячем состоянии. Перед посадкой бандаж подвергается неразрушающему контролю на отсутствие трещин.
Для предупреждения сползания с колесного центра бандаж стопорится бандажным кольцом 1 из стали специального профиля. Собранное колесо напрессовывается на ось усилием 1040 кН...1490 кН (106 тс...152 тс).
Формирование пар колесных производится в соответствии с инструкцией №ЦТ/329.
Формирование колесной пары
Формирование К.П. производится после подготовки всех основных элементов:- бандаж, колесный центр, зубчатое колесо, бандажное кольцо, ось.
1. Зубчатое колесо в горячем состоянии при t° 200-250°С напрессовывают на удлиненную ступицу колесного центра с натягом 0,23- 0,25 мм. (внутренний диаметр бандажа меньше диаметра колесного центра на 1,1-1,6 мм.- это и есть натяг).
2. Бандаж укладывается горизонтально гребнем вверх, нагревается до t° 250-320°С и в него опускается колесный центр. Далее, не дожидаясь остывания, в канавку бандажа укладывают бандажное кольцо, затем роликом, с усилием 150 тонн, обжимается буртик и бандажное кольцо.
3. Колесный центр с бандажом и зубчатым колесом, в холодном состоянии, напрессовывается на подступечную часть оси К.П. ( диаметром 235мм.).
В процессе запрессовки давление непрерывно и плавно увеличивается и в конце составляет 110-150 тонн, при этом выдерживается расстояние между внутренними гранями бандажей К.П. - 1440±3мм. и симметричность относительно середины оси.
4. После полной сборки К.П. производят обточку бандажей. Рабочая поверхность бандажа обтачивается по обычному локомотивному профилю и имеет определенную коническую форму, размеры и назначение:
- Диаметр по кругу катания – 1250мм.;
- Ширина бандажа- 140±2мм
-Толщина бандажа- 90+5мм.;
-Толщина гребня – 33мм., на высоте 20мм. от его вершины;
Уклон 1:20 - служит для уменьшения проскальзывания при вписывании в кривые участки пути и для самоцентровки К.П. на прямых участках;
Уклон 1:7 - служит для уменьшения проскальзывания колес при вписывании в кривые малого радиуса и для восприятия металла с рабочей поверхности бандажа при его выдавливании;
Фаска - служит для восприятия металла при его выдавливании, чтобы уменьшить увеличения ширины бандажа.
- Для контроля проворота на бандаже ставится контрольные отметки в виде 4-5 кернов глубиной 1,5 – 2 мм., а на колесном центре риска. После чего краской наносится контрольная полоса: на бандаже красная, на колесном центре белая шириной - 25мм.
- Если проводилось плазменное упрочнение гребней и поверхности катания, то на бандаж дополнительно наносят полосу зеленого цвета шириной – 10 мм.
- Если проводилось наплавление гребней, то на бандаж дополнительно наносят полосу желтого цвета шириной – 10мм.
После полной обработки и проверки всех замеров, колесную пару принимает инспекция «ОАО» РЖД на заводе изготовителе и на торце оси ставят знаки и клейма.
Сторона оси К.П. на которой находятся клейма о времени, месте изготовления и формировании К.П.- считается правой.
На левом торце оси ставят клеймо полного освидетельствования.
1 — условный номер предприятия-изготовителя необработанной оси;
2 — месяц (римскими цифрами) и год (две последние цифры) изготовления необработанной оси;
3 — порядковый номер плавки и номер оси;
4 — клейма техническою контроля предприятия-изготовителя и представителя приемки, проверивших правильность переноса маркировки и принявших обработанную ось;
5 — условный номер предприятия-изготовителя, обработавшего ось:
6 — клейма метода формирования колесной пары (Ф — прессовый, ФГ — тепловой);
7 — условный номер предприятия, производившего формирование колесной пары;
8 — месяц (римскими цифрами) и год (две последние цифры) формирования колесной пары;
9 — клейма технического контроля предприятия-изготовителя и представителя приемки, принявших колесную пару;
10 — клейма балансировки;
Знаки и клейма на наружной грани бандажа:
1 — условный номер предприятия изготовителя;
2 — год (две последние цифры) изготовления;
3 — марка бандажа;
4 — клейма приемки;
5 — номер плавки;
6 — порядковый номер бандажа по системе нумерации предприятия-изготовителя.
Дефекты колесных пар и их составных частей
Ползун (выбоина) - образуется при заклинивании К.П. и движении ее юзом. В результате в месте контакта колеса с рельсом происходит интенсивный износ поверхности катания колеса сообразованием плоской площадки.
Раковина – это дефект металлургического литья в виде неметаллических включений (песок, шлак и т.д. ), закатанных внутрь металла и пустот и пустот от усадки металла при неравномерном остывании, которые выходят на поверхность катания колеса при его износе.
Выщерблина – это выкрашивания кусочков метала на поверхности катания колеса.
Плена – это отшелушивание металла, тонкое, языкообразное отслоение частично соединенное с основным металлом. Располагается с наружной боковой поверхности колеса, бандажа, гребня, обода.
Навар – это кольцевые наплывы со смещением металла на поверхности катания колеса.
Волосовина – это кольцевые наплывы металла в виде пленообразных складок.
Прокат, ползун, навар и толщину гребня измеряют обсалютным шаблоном.
Универсальным шаблоном УТ-1 измеряют толщину гребня и параметр крутизны ( опасная форма гребня ).
Параметр крутизны измеряется между двумя точками, одна из которых находится в 2-х мм. от вершины гребня, а вторая в 13-и мм. от круга катания.
Шаблон ДО-1 не имеет цифровых значений и является шаблоном допускного контроля параметра крутизны гребня для отбраковки колес.
Колесные пары для определения их технического состояния и пригодности к эксплуатации подвергаются осмотру с регистрацией в книге формы ТУ-28:
- под ТПС — при всех видах технических обслуживании и текущих ремонтов ТР-1, ТР-2, каждой проверке ТПС в эксплуатации;
- при первой подкатке под ТПС новой колесной пары (после формирования) и после производства полного освидетельствования, если после них прошло не более 2 лет. При этом проверка даты формирования и освидетельствования производится по клеймам на торце (бурте) оси;
- после крушений, аварий, схода с рельсов, если отсутствуют повреждения элементов колесной пары, требующие их замены.
Осмотр колесных пар под ТПС должны производить:
- машинист — при каждой приемке ТПС (местах по доступной осмотру стороне); в эксплуатации при стоянках локомотивов на станциях и в пунктах оборота.
- мастер — при техническом обслуживании ТО-3 ТПС;
- мастер или бригадир — при техническом обслуживании ТО-2 ТПС; - мастер и приемщик локомотивов — при техническом обслуживании ТО-4, ТО-5, текущих ремонтах ТР-1 и ТР-2 ТПС, при первой подкатке новых колесных пар.
При осмотре колесных пар проверять:
— отсутствие трещин, ползунов (выбоин), плен, раздавленностей, вмятин, отколов, раковин, выщербин, ослабления бандажей на ободе центра (остукиванием молотком), сдвига бандажа (по контрольным меткам на бандаже и ободе центра), предельного проката (предельной высоты гребня) или износа, вертикального подреза гребня, ослабления бандажного кольца, опасной формы гребня и остроконечного наката, являющегося признаком возможности опасной формы гребня.
Предельный прокат (предельная высота гребня) и наличие опасной формы гребня проверяются шаблоном УТ-1 при технических обслуживаниях ТО-2, ТО-3, ТО-4, ТО-5, текущих ремонтах ТР-1, ТР-2 и ежемесячных обмерах колесных пар.
Допускается при проведении технического обслуживания ТО-2, контролировать опасную форму гребня шаблоном ДО-1.
После выявления колес с опасной формой гребня с помощью этого шаблона, необходимо шаблоном УТ-1 измерить величину этого параметра и по результатам этого измерения принимать решение о допуске их к эксплуатации или о назначении ремонта.
Недопустимые значения при эксплуатации колесных пар
Прокат по кругу катания – более 7мм.;
Разность прокатов по кругу катания у левого и правого колеса – более 2мм.;
Толщина гребня – более 33мм. и менее 25мм.;
Параметр крутизны, (опасная форма гребня), - менее 6мм.;
Ползун (выбоина), на поверхности катания, - более 1мм.;
Выщерблины, вмятины на поверхности катания бандажа глубиной – более 3мм. и длиной - более 10мм.;
Выщерблины, вмятины на вершине гребня длиной – более 4мм.;
Толщина бандажей К.П. – менее 45мм.;
Протертые места на средней части оси К.П. – глубиной более 4мм.;
Местное или общее увеличение ширины бандажа – более 6мм.;
Кольцевые выработки на поверхности катания глубиной – более 2мм. и шириной – более 15мм. на расстоянии до 40мм. от наружного торца бандажа. На других участках поверхности катания глубиной – более 1мм. и шириной более 2мм.
Остроконечный накат на гребне в зоне поверхности на расстоянии 2мм. от вершины гребня и 13мм. от поверхности катания;
Ослабления бандажного кольца – недопускается более чем в 3-х местах по его окружности и суммарной длиной ослабленного места – более 30%, а так же ближе 100мм. к замку кольца;
Навар, (смещение металла), на поверхности катания – более 0,5мм.
Прокат определяется как разность между исходной высотой гребня и действительной его высотой, полученной при измерении шаблоном УТ-1, (УТ-1М).
За исходную высоту гребня для локомотивов принимается – 30мм., для МВПС – 28мм.
2.4. Буксовый узел.
Буксовые узлы (буксы) предназначены для связи колесной пары с рамой тележки и передачи вертикальной нагрузки от подрессоренной массы электровоза на колесные пары, а также передачи силы тяги, торможения и боковых горизонтальных сил от колесной пары на раму тележки.
Устройство
Буксы двухповодковые с роликовыми подшипниками качения. Конструктивно букса состоит из корпуса 4, отлитого из стали, с четырьмя приливами для крепления тяг с сайлентблоками и двух тарельчатых приливов для установки на них пружин буксовой ступени рессорного подвешивания. К нижнему приливу приварен кронштейн для установки буксового гидродемпфера.
Горизонтальный и вертикальный упоры крепятся к кузову на шпильках.
В нижней части корпуса буксы предусмотрена площадка для опирания стоек или домкратов при вывешивании колесных пар.
Внутри корпуса размещаются два роликовых подшипника 3, 7 типа 30-42536ЛМ с размерами 180x320x86 мм и типа 30-52536ЛМ с размерами 180x320x86/12.
Внутренние кольца роликовых подшипников устанавливаются на шейку оси в горячем состоянии при температуре от 100°С до 120°С.
Кольцо лабиринтное 1 перед посадкой на ось нагревают до температуры 120°...130°С. Нагрев внутренних колец подшипников и кольца лабиринтного производится способом, исключающим их намагничивание.
Наружные кольца подшипников с роликами и сепараторами устанавливаются в корпус буксы с гарантированным зазором.
Внутренние и наружные кольца роликовых подшипников разделены дистанционными кольцами 5 и 6.
Внутренние кольца подшипников через дистанционное кольцом стягиваются гайкой 8, которая стопориться планкой 9, закрепленной двумя болтами 10 в специальном пазу оси.
Осевой разбег двух спаренных подшипников составляет 0,5... 1,0 мм. и достигнут за счет подбора дистанционных колец по толщине.
Разность радиальных зазоров двух роликоподшипников на одной буксе не более 0,03 мм.
С внутреннего торца букса закрыта лабиринтным кольцом 1, установленным на предподступичную часть оси и крышкой 2. Канавки в кольце и крышке образуют лабиринтное уплотнение, предохраняющее от попадания в полость буксы инородных тел и вытекания смазки из буксы.
На передней 11 и задней 2 крышках буксы имеются кольцевые канавки для установки уплотняющих резиновых колец круглого сечения.
Пространство в лабиринте задней крышки, между подшипниками и передней крышкой, а также в самих подшипниках заполнено смазкой марки «Буксол». Общее количество смазки в одну буксу 3,5...4,0 кг. Как избыток смазки, так и ее недостаток вызывает нагрев буксы и усиленный износ подшипников. Пополнение смазки производится через отверстие в цилиндрической части корпуса буксы, закрытое пробкой.
Передача тяговых и тормозных сил от корпуса буксы на раму тележки производится через тяги 13, которые одним шарниром прикреплены к приливам корпуса буксы, а другим - к кронштейнам рамы тележки. Шарниры тяг выполнены в виде резино-металлических валиков 12 и 14 и резино-металлических шайб 15.
Буксы первой и восьмой колесных пар, имеют передние крышки 1 с фланцами для установки датчиков угла поворота 2.
Передача вращения от оси колесной пары к датчикам угла поворота осуществляется специальным болтом, ввинченным в торец оси колёсной пары и входящим в паз полумуфты приборов.
Дата добавления: 2021-12-10; просмотров: 87; Мы поможем в написании вашей работы! |
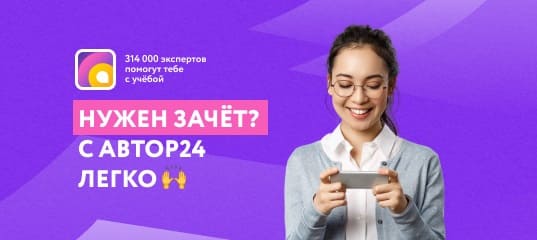
Мы поможем в написании ваших работ!