Обжиговые установки (в т.ч. печи)
Дисциплина
«ВЫСО КОТЕМПЕРАТУРНЫЕ
ТЕПЛОТЕХНОЛОГИЧЕСКИЕ ПРОЦЕССЫ И УСТАНОВКИ »
Лекции № 6 12.11.2021
3.4. Физико-химические и теплофизические
особенности процессов обжига
Обжиг — одна из наиболее распространенных технологических операций обработки минерального сырья.
Температурный график технологического процесса (рис.3.7) – графическая иллюстрация изменения температуры обрабатываемого материала в теплотехнологическом реакторе (по длине или по времени).
Максимальная температура, при которой происходит технологическая обработка материала, называется температурным уровнем технологического процесса. Температурный уровень определяет температуру газов, отходящих из зоны основной технологической обработки
Рис.3.7. Температурный график для цементной вращающейся печи:
по зонам: 1- нагрев материала, 2 - испарение влаги, 3 - нагрев, 4 - декарбонизация, 5 - нагрев и плавление частичное, 6-процесс изотермической выдержки (спекание), 7-охлаждение.
На рис. 3.10 и 3.11 в качестве примера приведены температурные и тепловые графики. По оси ординат (рис. 3.10 ) отложены относительная средняя температура обрабатываемого в печи материала и относительное внешнее теплопоглощение этого же материала (рис. 3.11). По оси абсцисс отложено относительное текущее время процесса.
Иногда температурный график полезно дополнить температурной кривой для греющих газов (характеризует температурный режим обжиговой установки). Наглядно видно на какую величину tГАЗОВ выше tМАТЕРИАЛОВ, поэтому наглядно виден температурный напор ∆t. Температурный напор должен обеспечивать передачу теплоты от газов к материалу (∆min ≈ 50…100 К).
|
|
От температурного уровня процесса зависит вид источника энергии (вид топлива). Чем выше температурный уровень tмах, тем обычно ниже тепловая эффективность теплотехнологического процесса, так как возрастает температура отходящих газов и снижется температурный напор ∆t, и тем более высококалорийное топливо необходимо использовать, так как температура продуктов сгорания топлива должна быть выше температурного уровня процесса. Поэтому топливо оценивается с точки зрения максимально достижимой температуры горения.
Возможности повышения температуры горения зависят:
1) от вида топлива (низко-, высококалорийное);
2) применение кислородного дутья (добавление кислорода к воздуху или замена техническим кислородом).
Чтобы провести процесс в материале выше 2000 °С необходимо переходить на кислородное дутье, либо использовать электрические источник теплоты. Если температура процесса до 1700 °С – можно использовать высококалорийное топливо. Если температурный уровень процесса 1700…2000 °С – кислородное дутье и высококалорийное топливо.
|
|
Существуют 3 принципиально разных способа сжигания топлива.
1. С предварительное смешение топлива с воздухом.
2. Без предварительного смешения.
3. С частичным смешением (комбинированный).
Уровень расхода топлива в теплотехнологической установке в первую очередь определяется следующими особенностями температурного графика технологического процесса:
- начальной температурой исходных материалов TМН;
- средней температурой продуктов TМП.И, при которой они используются непосредственно после выдачи из теплотехнологического реактора (средней температурой продуктов на выходе).
Если принять за основу классификации эти два фактора, то многообразие температурных и тепловых графиков сводится к следующим четырем группам.
Группа А включает графики технологических процессов, в которых начальная температура исходных материалов равна температуре окружающей среды (TМН = TО.С), а температура TМП.И равна средней максимальной температуре материала в процессе (TМП.И = TММАКС).
Группа Б включает графики технологических процессов c TМН = TО.С и TМП.И меньше TММАКС.
|
|
Группа В включает графики технологических процессов с TМН > TО.С и TМП.И = <TММАКС.
Группа Г включает графики технологических процессов с TМН > TО.С и TМП.И меньше <TММАКС
В каждой из указанных групп можно выделить несколько подгрупп, отличающихся числом ступеней (стадий) теплотехнологического процесса.
Тепловой график технологического процесса (рис.3.8) – графическая иллюстрация изменения теплопоглощения обрабатываемого материала в теплотехнологическом реакторе (по длине или по времени). График характеризует теплопоглощение по зонам.
Рис. 3.8. Тепловой график для цементной вращающейся печи по зонам:
1- нагрев материала, 2 - испарение влаги, 3 - нагрев, 4 - декарбонизация, 5 - нагрев и плавление частичное, 6 - процесс изотермической выдержки (спекание), 7- охлаждение.
Тепловой график не учитывает потери теплоты в окружающую среду, потери с недожогом топлива. Реальные затраты теплоты значительно больше.
Температурные и тепловые графики высокотемпературных теплотехнологических процессов отличаются большим многообразием.
Поэтому обобщающая классификация этих графиков является также весьма полезной при энергетическом и теплотехническом анализе технологических процессов и установок.
|
|
В зависимости от технологического назначения различают следующие виды обжига: кальцинирующий, восстановительный, хлорирующий, окислительный, сульфатизирующий и спекающий. Температурные графики процессов обжига приведены на рис. 3.9.
Рис. 3.9. Температурный режим процессов обжига:
1– кальцинирующий; 2– восстановительный; 3 – хлорирующий; 4 – окислительный; 5 – сульфатизирующий; 6 –спекающий.
Кальцинирующий обжиг – один из самых распространенных видов обжига. Он предназначен для разложения карбонатов (известняка, мела, СаСОз, доломита СаСОз•МgСО3•nН2О, мергелей nСаО•mAl2O3•рFe2Оз• гН2О, бокситов) и применяется в производстве извести, обогащении железных, цинковых и других руд, в производстве глинозема и цемента.
Основными стадиями этого процесса являются: удаление свободной влаги (сушка), удаление химически связанной влаги (дегидратация), разложение карбонатов (кальцинация).
Итоговая реакция разложения карбонатов имеет вид: MeCO3 = MeO+CO2
Время полного обжига зависит от эндотермического эффекта процесса, теплопроводности, плотности, размера и степени прогрева куска обжигаемого материала.
Плотность продукта обжига повышается с ростом температуры обжига. При этом с ростом температуры увеличивается и размер зерна кристаллов с соответствующим снижением реакционной способности образовавшегося оксида. Установлено, что процесс диссоциации карбонатов усиливается, размеры кристаллов оксидов увеличиваются в присутствии солей щелочных и щелочно-земельных металлов.
Восстановительный обжиг – тепловая обработка оксидов металлов восстановительным газом и получение металлизованных окатышей или металлической губки (в том числе прямое восстановление железа), угольных изделий (преимущественно электродов) с целью их графитизации, изделий из металла с целью их поверхностного упрочнения.
Основными стадиями этого процесса являются: сушка и дегидратация; кальцинация; взаимодействие паров воды и диоксида углерода с углеродом по реакциям Н2О+C=CO+H2; CO2+C=2CO и установление равновесия по реакции водяного газа СО + H2O=H2+CO2; насыщение (адсорбция) поверхности кусков обжигаемого материала СО и Н2; взаимодействие оксидов с адсорбированным восстановительным газом МеО + СОадс = Ме(СО2) адс; МеО+(Н2) = Ме(Н20) адс; перенос адсорбированных продуктов реакции в пограничный газовый слой (десорбция) Ме(СО2)адс= Ме+ (СО2)адс; (СО2)адс= С02; Ме(Н2О)адс= Ме+(Н20) адс
Хлорирующий обжиг – один из наиболее перспективных методов тепловой обработки оксидов и сульфидов металлов с целью получения растворимых хлоридов ‒ основного сырья для гидрометаллургических процессов в новой металлургической технологии. Обработка производится при 400…600 °С при непрерывной продувке шихтовых материалов газообразным хлором. Химические реакции, протекающие при этом обжиге эндотермичны, поэтому требуется внешний подогрев хлора и шихты до температуры 700 … 800 °С.
Окислительный обжиг широко применяется в металлургии меди, никеля, цинка и молибдена, если последние получают из руд, содержащих их сульфиды. Все сульфиды в окислительной среде воспламеняются и горят с выделением такого количества теплоты, которое может оказаться достаточным для подъема температуры в зоне реакции до 900 …1300 °С и реализации всей технологии обжига.
Сульфатизирующий обжиг – разновидность окислительного обжига, отличающаяся тем, что с целью получения растворимых в воде сульфатов цветных металлов обжиг производится при недостатке, кислорода (воздуха), при пониженных по сравнению с окислительным обжигом на 200 …300 °С температурах, в результате чего протекают реакции. Оксид железа при этом переходит в нерастворимый в воде диоксид.
Обжиг окатышей – одна из разновидностей окислительно- восстановительного обжига, заключающаяся в специальной обработке окомкованного рудного концентрата (в основном оксидов железа) с целью получения легко восстанавливающейся сыпучей и хорошо газопроницаемой шихты для шахтных печей и выплавки металла (чугуна).
Спекающий окислительный обжиг наиболее широко используется впроизводстве цемента. Обжиг минеральной многокомпонентной шихты (А1203, SiO2, СаО, MgO, Fе2О3 и т. д.) в окислительной среде при температурах 1500…1800 °С приводит кполучению твердого негигроскопичного камневидного материала – клинкера, который содержит до 75% СаО, 10…15% SiO2, 8…10% Аl2Оз.
Тонкий размол его (чаще в смеси с добавками доменного шлака, гипса, золы, горючих сланцен и т. п.) позволяет получить цемент – порошок, реагирующий с водой и обладающий способностью переходить из тестовидного пластического состояния в твердое.
Обжиговые установки (в т.ч. печи)
По конструкции и характеристикам обжиговые установки подразделяются на пять основных типов: камерные кольцевые, туннельные, трубчатые (вращающиеся), шахтные, «кипящего» слоя, ванные.
При выборе обжиговой установки для конкретного технологического процесса факторы, принимаемые во внимание, располагаются в следующей последовательности по важности:
- характер целевого химического процесса и фазовый состав исходного сырья и продуктов реакции;
-химическое взаимодействие энергоносителя с сырьем и целевым продуктом;
-удельные затраты тепла и топлива на получение нужной температуры при заданной производительности;
- соответствие температурного поля в рабочей зоне реактора технологическим требованиям;
- возможности автоматизации загрузки сырья и выгрузки готового продукта;
- выход годного продукта в соответствии с техническими требованиями на него;
- удельные затраты на отделение конечного продукта от побочных продуктов процесса;
- возможности полной автоматизации процесса;
- отходы и экологическая нагрузка на окружающую среду.
Представленные на нижерасположенных рисунках варианты печей в принципе позволяют решать почти любую технологическую задачу с использованием разных типов реакторов с различным технико-экономическим результатом.
Дата добавления: 2021-12-10; просмотров: 48; Мы поможем в написании вашей работы! |
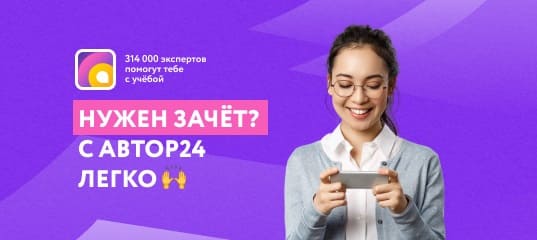
Мы поможем в написании ваших работ!