Выполнить сравнительный анализ способов сварки
Задачи сварки в машиностроении
Сварка – технологический процесс получения неразъемных соединений из металлов, сплавов и других однородных или разнородных материалов в результате образования атомно-молекулярных связей между частицами соединяемых заготовок.
Основной задачей сварки является получение прочного неразъемного соединения свариваемых заготовок с заданными физико-механическими свойствами. Процесс соединения деталей с помощью сварки в большинстве случаев является сборочным и может быть введен непосредственно в поток узловой или общей сборки. Во время сварки собираемые элементы конструкции (детали) удерживаются в специальных приспособлениях фиксаторами или конвекторами, что обеспечивает правильное положение элементов относительно друг друга.
Сварка является одним из наиболее совершенных, экономически выгодных, высокопроизводительных и в значительной степени механизированных технологических процессов. Поэтому ее широко применяют практически во всех отраслях машиностроения. Поэтому сварные изделия или отдельные их узлы могут иметь очень сложную форму в сочетании с незначительной массой при относительно простой и нетрудоемкой технологии изготовления.
Рисунок 1 – Сварочные работы
Виды сварки в учебно-производственных мастерских НМК, продукция
В Нефтекамском Машиностроительном колледже используются полностью работоспособные сварочные аппараты разных типов, и есть возможность опробовать себя следующих видах сварки:
|
|
1) Полуавтомат (KEMPPI Kempact 323R)
Механизированная сварка — процесс сварки, при котором электродная проволока подается с постоянной или переменной скоростью в зону сварки и одновременно в эту же зону поступает активный (к примеру: углекислый газ) или инертный газ (к примеру: аргон) или газовые смеси, который обеспечивает защиту расплавленного или нагретого электродного и основного металлов от вредного воздействия окружающего воздуха. Защитный газ при этом подается из баллона (о маркировке см. здесь) через газовый редуктор.
![]() |
Кроме того, что механизированная сварка обеспечивает высокое качество шва, значительно облегчается поджог дуги, резко возрастает удобство и скорость работы — сварщик избавлен от необходимости смены электродов.
Рисунок 2 – аппарат KEMPPI Kempact 323R.
2) -Ручная дуговая сварка с обширными параметрами и Аргонодуговая сварка (KEMPPI MasterTig MLS 2300ACDC)
Ручная дуговая сварка (ММА) - это процесс дуговой сварки, при котором используется дуга, горящая между покрытым электродом и сварочной ванной. Покрытый электрод представляет собой металлический стержень, на который нанесено покрытие.
|
|
![]() |
Дуга при этом способе сварки зажигается быстрым касанием торцом электрода поверхности основного металла, которая под воздействием тепла дуги расплавляется, образуя сварочную ванну. Под действием дуги также происходит плавление электродного стержня, металл которого переходит в сварочную ванну, образуя наплавленный металл сварного шва (при этом часть металла теряется в виде брызг). При расплавлении покрытия электрода образуются газы и шлак, которые защищают зону дуги и сварочную ванну от вредного воздействия окружающего воздуха. Более того, шлак, покрывающий наплавленный металл, обеспечивает его правильное формирование при кристаллизации. После каждого прохода шлак необходимо удалять. Некоторые марки электродов обеспечивают самоотделение шлаковой корки.
Рисунок 3 – аппарат KEMPPI MasterTig MLS 2300ACDC.
3) Электромуфтовая сварка (HST300 Print 315 2.0)
Электромуфтовая сварка – один из основных видов соединения полиэтиленовых труб (ПНД), особенностью которого является использование специального нагревательного элемента – электромуфты. Данный метод сварки обходится дороже, чем применения сварки встык, но иногда без этого способа не обойтись. В этой статье мы рассмотрим, в каких именно случаях применяется электромуфтовая сварка и каков принцип ее работы.
|
|
Сегодня электромуфтовую сварку ПНД используют для труб разной толщины стенок и разного диаметра, при монтаже безнапорного трубопровода – систем дренажа и самотечной канализации, врезке в действующий трубопровод и ремонте уже существующих трубопроводов. При соединении электромуфтой скорость выполнения работ очень высокая и требуется мало свободного пространства.
Как правило, электромуфтовая сварка полиэтиленовых труб проводится с помощью специального оборудования, оснащённого микропроцессорным управлением. Благодаря этому, муфтовая сварка обеспечивает контроль параметров процесса, автоматическое регулирование времени сварки, которое зависит от параметров фасонного элемента и температуры воздуха.
![]() |
Рисунок 4 – Электромуфтовая сварка (HST300 Print 315 2.0)
4) Плазменная (многофункциональный аппарат PHOENIX 500 PRO
GRESS puls, TETRIX – 400 plazma)
При плазменной сварке для получении плазмы применяются плазменные горелки, состоящие из вольфрамового электрода, труб водяного охлаждения, подачи газа, сопла плазмы.
|
|
Температура в плазменной дуге достигает 30 000°С, в отличие от плазмы электрической дуги, температура которой — 5000-7000°С.
![]() |
В плазмотроне в зону плазменной дуги подводится газ, образующий плазму. Газ нагревается дугой и ионизируется. Благодаря тепловому расширению газа, увеличивающему объём газа в 50-100 раз, происходит скоростное истекание его из канала сопла плазмотрона. Кинетическая энергия ионизированных частиц газа и тепловая энергия является основными источником энергии для сварки.
Рисунок 5 – аппараты PHOENIX 500 PRO GRESS puls и TETRIX – 400 plazma.
Выполнить сравнительный анализ способов сварки
Рассматриваются: ручная аргонодуговая сварка, полуавтоматическая аргонодуговая сварка и лазерная сварка.
Аргонодуговая сварка – дуговая сварка в среде инертного газа аргона. Может осуществляться плавящимся или неплавящимся электродом. В качестве неплавящегося электрода обычно используется вольфрамовый электрод.
Для обозначения аргонодуговой сварки могут применяться следующие названия
РАД – ручная аргонодуговая сварка неплавящимся электродом, ААД – автоматическая аргонодуговая сварка неплавящимся электродом, ААДП – автоматическая аргонодуговая сварка плавящимся электродом.
Для обозначения аргонодуговой сварки вольфрамовым электродом: TIG – Tungsten Inert Gas (Welding) – сварка вольфрамом в среде инертных газов GTAW – Gas Tungsten Arc Welding – газовая дуговая сварка вольфрамом
Общие характеристики аргонодуговой сварки
Аргон практически не вступает в химические взаимодействия с расплавленным металлом и другими газами в зоне горения дуги. Будучи на 38% тяжелее воздуха, аргон вытесняет его из зоны сварки и надежно изолирует сварочную ванну от контакта с атмосферой.
При аргонодуговой сварке возможен крупнокапельный или струйный перенос электродного металла. При крупнокапельном переносе процесс сварки неустойчивый, с большим разбрызгиванием. Его технологические характеристики хуже, чем при полуавтоматической сварке в углекислом газе, так как вследствие меньшего давления в дуге капли вырастают до больших размеров. Диапазон токов для крупнокапельного переноса достаточно велик, например для проволоки диаметром d = 1,6 мм Iсв = 120–240А. При силе тока Iсв больше 260А происходит резкий переход к струйному переносу, стабильность процесса сварки улучшается, разбрызгивание уменьшается. Однако такие токи не всегда соответствуют технологическим требованиям. Поэтому более рационально для обеспечения стабильности процесса использовать импульсные источники питания дуги, которые обеспечивают переход к струйному переносу на токах около Iсв ≈ 100А.
Технология аргонодуговой сварки неплавящимся электродом
Дуга горит между свариваемым изделием и неплавящимся электродом (обычно из вольфрама). Электрод расположен в горелке, через сопло которой вдувается защитный газ. Присадочный материал подается в зону дуги со стороны и в электрическую цепь не включен.
![]() ![]() |
Сущность лазерного процесса сварки состоит в следующем: лазерное излучение направляется в фокусирующую систему, где фокусируется в пучок меньшего сечения и попадает на свариваемые детали, где частично отражается, частично проникает внутрь материала, где поглощается, нагревает и расплавляет металл, формируя сварной шов.
Лазерную сварку производят сквозным и частичным проплавлением в любом пространственном положении. Сварка проводится непрерывным или импульсным излучением. При сварке изделий малых толщин от 0,05 до 1,0 мм сварка проходит с расфокусировкой лазерного луча.
При импульсном лазерном излучении сварной шов образуется сварными точками, их перекрытием на 30 - 90%. Современные сварочные установки с твердотельными лазерами проводят шовную сварку со скоростью до 5 мм/с с частотой импульсов около 20 Гц. Сварку проводят с использованием присадочных материалов (проволока диаметром около 1,5 мм, лента или порошок). Присадка увеличивает сечение сварного шва.
Лазерная сварка разделяется на три вида: микросварка (толщина или глубина проплавления до 100 мкм), мини-сварка (глубина проплавления от 0,1 до 1 мм), макросварка (глубина проплавления более 1 мм).
Недостатки
- высокая стоимость лазерных установок;
- низкий КПД (0,01 - 2,0%).
Преимущества
- возможность сварки высокоточных конструкций
- сварка без правок или механической обработки
- высокая скорость сварки и производительность работ (стальной лист толщиной 20 мм электрической дугой сваривают со скоростью 15 м/ч за 5 - 8 проходов, при сварке непрерывным лазерным лучом лист сваривается со скоростью 100 м/ч за 1)
- высокая экологическая безопасность по сравнению с традиционной сваркой
- минимальные температурные поводки и коробление металла (в сравнении с другими методами).
Оборудование:
В состав оборудования для лазерной сварки входит лазер, системы фокусировки излучения, газовой защиты изделия, перемещения луча и изделия.
В сварке используют твердотельные и газовые лазеры. Твердотельные лазеры выполняют на основе рубина, стекла с присадкой ионов неодима, алюмоиттриевого граната (АИГ) с неодимом, а также на базе иттербиевого волокна. Газовые лазеры - в качестве рабочего тела используют смесь СO2, N2 и Не.
Российская промышленность выпускает лазерные установки LRS-100-500 HTS-200-500 ЛГТ-2.01, ТЛ-5М, МУЛ-1, ЛТА4-1, ЛТА4-2, установки серии ALFA и ALFA-AUTO[1]. Установки позволяют проводить полуавтоматическую сварку в импульсном режиме с микропроцессорным управлением.
Рисунок 8 – Лазерная сварка.
Дата добавления: 2021-11-30; просмотров: 68; Мы поможем в написании вашей работы! |
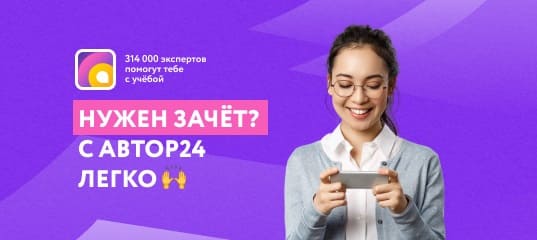
Мы поможем в написании ваших работ!