Промышленность органического синтеза и полимеров
Промышленность органического синтеза и полимеров отличается большой сложностью, отраслевого состава. Ее продукция непрерывно увеличивается, по ассортименту и стоимости. Возрастает также роль этой продукции в народном хозяйстве, обороне и в быту.
Многочисленные сложные продукты органического синтеза получаются в результате химической переработки исходных веществ — простых углеводородов, выделяемых из нефти, природных газов, ископаемого угля, торфа, горючих сланцев, древесины и другого сырья органического происхождения и, кроме того, некоторых неорганических веществ.
Если раньше главную роль в промышленности органического синтеза играли продукты коксования и полукоксования угля (еще раньше—растительное сырье), то в настоящее время наибольшее значение имеют углеводороды нефти, попутного нефтяного и природного газа.
Важнейшими исходными углеводородами для органического синтеза являются метан и олефины — этилен С2Н4, пропилен С3Н6, бутилен С4Н8; кроме того, ацетилен С2Н2, бензол С6Н6, толуол С7Н5 и многие другие.
Исходные углеводороды используют для синтеза промежуточных продуктов (полупродуктов), например фенола С6Н5ОН, анилина С6Н5NН2, метанола (метилового спирта) СН3ОН, этилового спирта С2Н5ОН, бутадиена (дивинила) С4Н6, стирола С8Н8, винилацетилена С4Н4, формальдегида СН2О и др.
Соответствующей переработкой полупродуктов получают более сложные органические вещества — синтетические смолы и пластмассы, каучуки, волокна, красители, фармацевтические препараты др.
|
|
На отдельных стадиях переработки исходных углеводородов и полупродуктов применяются процессы окисления, гидратации, дегидратации, гидрирования, дегидрирования, хлорирования, полимеризации, поликонденсации и др.
Таким образом, промышленность органического синтеза и полимеров характеризуется многостадийностью производства, что определяет некоторые общие характерные особенности ее размещения.
Выделение исходных углеводородов из первичного сырья территориально связано с местами добычи и переработки нефти и природного газа, термического разложения угля, горючих сланцев, древесины. Это основные сырьевые базы промышленности органического синтеза.
В этих же районах и центрах, иногда даже на самих нефте-, газо- и сланцеперерабатывающих или коксохимических предприятиях осуществляется также производство полупродуктов, отличающееся большим удельным расходом исходного сырья и, как правило, высокой топливо- и энергоемкостью.
Размещение же производства готовых изделий из полупродуктов ориентируется главным образом на районы потребления, так как такие производства не имеют значительных отходов, и, перерабатывая транспортабельное сырье (полупродукты), выпускают малотранспортабельную продукцию (изделия из каучука и пластмасс, волокно и т. д.).
|
|
Синтетический каучук . Каучук и основной продукт его переработки— резина — находят очень широкое применение во всех отраслях техники. Из каучука делают автомобильные и другие шины, тысячи наименований резинотехнических изделий, обувь, изоляцию для электропроводов, водолазные костюмы, надувные лодки, противогазы, санитарно-гигиенические предметы и многое другое. Такому широкому применению каучука способствуют присущие резине ценные свойства: упругость и эластичность, водо- и газонепроницаемость, стойкость против разрушающего действия многих химических реагентов, механическая прочность, высокие электроизоляционные показатели. Благодаря этим свойствам резина во многих случаях незаменима.
Каучук стал известен в Европе и начал применяться для практических целей еще в первой четверти прошлого столетия. Изделия из необработанного каучука, однако, не могли найти массового применения, так как состояние этих изделий в сильной степени зависит от внешней температуры: они твердеют и ломаются на холоде, а при нагревании становятся липкими. Только с открытием способа переработки каучука в резину (вулканизации) он быстро получил универсальное применение. Самыми крупными потребителями изделий из каучука в настоящее время являются автомобильная промышленность и автотранспорт. Современное мировое потребление каучука составляет свыше 6 млн. т в год, в том числе более 3,5 млн. т синтетического. Получение синтетического каучука. Первоначально единственным источником каучука был млечный сок тропического каучуконосного дерева — гевеи. С увеличением потребности в каучуке и в связи с невозможностью возделывания гевеи в странах умеренного пояса появилась необходимость получения синтетического каучука.
|
|
Практическое решение этой очень важной проблемы принадлежит советскому химику С. В. Лебедеву, получившему а 1928 г. синтетический каучук на основе углеводорода бутадиена.
Бутадиен, а следовательно синтетический каучук (СК), по методу Лебедева получают из этилового спирта. Производство СК из спирта слагается из двух основных процессов. Первым является получение бутадиена. Он осуществляется при температуре до 400° С без доступа воздуха и при соответствующих катализаторах. При этих условиях молекулы спирта «расщепляются», а из их частей образуется новое вещество—бутадиен. Упрощенно эту реакцию разложения спирта представляют следующим уравнением:
|
|
2С2Н6ОН →катализ С4Н6 +2Н2О.+ Н2.
Бутадиен образуется и в результате отнятия от двух молекул спирта двух молекул воды и одной молекулы водорода (дегидратация и дегидрирование спирта).
Очищенный жидкий бутадиен подвергают полимеризации, при которой происходит соединение молекул бутадиена и образование нового вещества — каучука. В процессе полимеризации из большого числа п молекул бутадиена образуется одна большая и сложная молекула каучука:
nС4Н6 → (С4Н6)n
Полимеризацию бутадиена осуществляют под давлением и с натриевым катализатором. Отсюда и название каучука — нат рийбутадиеновый.
Полученный каучук очищают от газообразных примесей и остатков катализатора, сушат и раскатывают в листы. Расход этилового спирта на 1 т каучука составляет 2,2 т. Натрийбутадиеновый каучук, производство которого сыграло огромную роль в становлении и развитии новой отрасли промышленности СК, в настоящее время почти утратил свое значение. Это объясняется невысоким качеством получаемых из него изделий, которые по прочности и эластичности уступают изделиям из натурального каучука.
СК, характеризующихся более ценными свойствами, превосходящими свойства натурального каучука. Удельный вес новых каучуков в общем производстве СК быстро возрастает, а натрийбутадиенового соответственно снижается и уже стал незначительным. Новые виды СК получают главным образом на основе полимеризации бутадиена (дивинила) с другими веществами, или сополимеризации его с другими мономерами. В результате получаются сополимеры. Наибольшее значение в настоящее время имеют сополимеры бутадиена со стиролом и метилом СНз — бутадиенстироль ный (дивинилстирольный) и бутадиенметилстирольный (дивинил- метилстирольньсй) каучуки, -на долю которых приходится около двух пятых всего производства СК в стране.
Сополимерные каучуки применяют главным образом для изготовления автомобильных шин, отличающихся повышенной износоустойчивостью и, следовательно, ходимостью.
Быстро развивается производство полибутадиеновых каучуков. Благодаря иному строению молекул эти каучуки обладают высокими механическими свойствами. Полибутадиеновые каучуки характеризуются регулярным строением цепей молекул в отличие от разветвленного строения молекул натрийбутадиенового каучука, ухудшающего эластические и механические свойства последнего. Полибутадиеновые каучуки составляют уже свыше трети общего производства СК. Теперь СК получают не только на, основе этилового спирта, но и главным образом на основе бутилена и нормального бутана путем их каталитического дегидрирования, дающего бутадиен. Это упрощает производство СК (исключаются процессы получения спирта) и непосредственно связывает его, с нефтяной промышленностью, обеспечивающей это производство нетранспортабельным сырьём.
Из каучука и необходимых добавок серы и других веществ (ингредиентов — сажи, мела, каолина, различных смол и др.) готовят соответствующую резиновую смесь, служащую исходным материалом для заготовок резиновых изделий. Заготовки получают прокаткой, штамповкой или формовкой резиновой смеси, придающей ей форму соответствующего изделия. Полученные таким образом заготовки затем подвергают вулканизации, т. е. тепловой обработке при температуре примерно 140° С в прессах или автоклавах. В результате получаются резиновые изделия. Для получения мягкой резины (шины, гигиенические предметы и т. п.) содержание серы в резиновой смеси не должно превышать 3%. Чем больше содержание серы, тем тверже получается резиновое изделие (эбонит, который тоже является продуктом вулканизации каучука, содержит 35% серы).
Переработкой каучука и производством резиновых изделий заняты многие десятки промышленных предприятий (шинные заводы, заводы резинотехнических изделий, резиновых изделий, резиновой обуви и др.), размещенных преимущественно в районах потребления их продукции.
Химические волокна и их получение. Современная текстильная промышленность наряду с натуральными волокнами перерабатывает огромные массы химических — искусственных и синтетических — волокон. Эти волокна и изделия из них широко используются также в других отраслях народного хозяйства. Химические волокна во многих случаях успешно заменяют хлопок, шелк и другие натуральные волокна, а по целому ряду свойств превосходят их. При этом изделия из синтетических, волокон в несколько раз дешевле изготовленных из натурального сырья.
Искусственными называют волокна, которые получают переработкой главным образом древесины (целлюлозы) и других сложных органических веществ—природных полимеров (например; хлопкового пуха). Синтетическими называют волокна, получаемые путем синтеза из относительно простых органических и неорганических веществ.
Мировое производство химических волокон составляет более 5 млн. т; химические волокна заняли второе место после хлопка в мировом балансе текстильного сырья.
Около 60% общего производства химических волокон приходится на искусственные волокна. Производство их началось раньше и достигло высокой уровня развития. Однако доля искусственных волокон постепенно снижается вследствие ускоренного развития более эффективной производства новейших видов синтетических волокон.
Наиболее широко применяемым искусственным волокном является вискозный шелк. Кроме того, вырабатывают немалое количество ацетатного шелка. Их получают соответствующей переработкой целлюлозы, которую растворяют в специальных химически растворителях. Полученный раствор (прядильный раствор) продавливают через тонкие отверстия (фильеры) особого прядильного аппарата. Выступающие из отверстий струйки раствора, затвердевая, образуют тонкие нити, которые с огромной скоростью (сотни метров в минуту) наматывают на бобины. Свойства волокон могут быть различными в зависимости от применяемого растворителя и метода растворения целлюлозы.
Для получения вискозного - шелка древесную целлюлозу обрабатывают щелочью и сероуглеродом СS2. В результате образуется соединение (ксантогенат целлюлозы), растворяющееся в щелочи и образующее при этом густой раствор — вискозу. Вискозные тонкие струйки превращают в нити путем удаления из вискозы щелочи (растворителя), для чего на струйки воздействуют серной кислотой.
По вискозному способу производят также штапельное волокно. Для его получения нити вискозного шелка собирают толстым жгутом, который затем разрезают на части определенной длины и таким образом получают соответствующей длины волокна. Такое резаное волокно называют штапельным. Расход целлюлозы на 1 т вискозного шелка составляет несколько более 1 т. Кроме того, расходуется 0,87 т каустической соды, 0,3 т сероуглерода и около 1,2 т серной кислоты. Полезным отходом производства является сульфат натрия (0,48 т на 1 т волокна).
Ацетатный способ, по которому получают ацетатный шелк, заключается в обработке хлопковой или древесной целлюлозы уксусным ангидридом (СН3СО)2О в присутствии уксусной СН3СООН и серной кислот. В результате образуется ацетилцеллюлоза. Последняя растворяется в смеси ацетона СН3СОСН3 и спирта и образует прядильный раствор, из которого уже известным способом получают волокно. Ацетатный шелк обладает большой прочностью и высокими электроизоляционными свойствами. Благодаря доступности и дешевизне сырья более массовым является производство вискозного шелка. Но удельный вес ацетатного шелка постепенно возрастает.
Синтетические волокна получают главным образом из полиамидных смол (полиамидные волокна), вырабатываемых на основе нефтяного, газового и угольного сырья. Наиболее распространенное синтетическое волокно капрон получают из капролактама, который вырабатывают на основе фенола, бензола или циклогексана. Если на 1 т капронового волокна расход капролактама составляет только 1,2 т, то производство самого капролактама отличается гораздо более высокой материалоемкостью, превышающей 8 т (малотранспортабельного сырья)'на 1 т продукта. Этим определяется размещение производства капролактама, как и других полиамидных смол, вблизи от источников сырья (центров переработки угля, нефти).
Смесь расплавленного при 95—100° С капролактама и необходимых добавок подвергают полимеризации, в результате которой образуется смола - капрон. Ее применяют для приготовления с (плавлением) прядильного раствора, из которого получают капроновое волокно.
Капроновое волокно обладает очень высокой механической прочностью, оно не набухает и не уменьшает прочности в воде; капрон не гниет, не боится моли. Благодаря ценным свойствам капрон широко применяют во многих отраслях техники (парашютная ткань, рыболовные сети и т. д.) и для изготовления предметов широкого потребления. Особенно ценные технические и потребительские свойства имеет волокно лавсан, изготовляемое из полиэфирной смолы, которую в свою очередь получают на основе нефтяного сырья. Будучи по внешнему виду сходными с шерстяными, эти волокна отличаются высокой прочностью и упругостью. Ткани из лавсана не мнутся даже при смачивании. Лавсан широко применяют в технике, в том числе в электротехнической промышленности. Из него производят транспортерные ленты, специальные технические ткани и другие изделия.
Производство химических волокон характеризуется высокой электроемкостью - на 1 т вискозного волокна расходуется 11 тыс., а на 1 т капронового — свыше 17 тыс. кВт-ч. Еще больше расход тепловой энергии — до 15 т условного топлива на 1 т волокна. Затраты на топливо и энергию достигают 40—45% себестоимости химических волокон.
Предприятия, выпускающие химические волокна, потребляют также огромное количество воды (до 3—5 тыс. м3 более на 1 т готовой продукции) и нуждаются, следовательно, в мощных источниках водоснабжения.
Производство химических волокон отличается и высокой трудоемкостью (700—1500 чел-ч на 1 т продукции), намного превышающей трудоемкость других отраслей химической промышленности.
Фактором, влияющим на размещение производства химических волокон, является и относительно низкая транспортабельность готовой продукции (большой объем на единицу веса) по сравнению с потребляемым для ее изготовления сырьем.
Химический комплекс России
Место химической индустрии в развитии экономики страны определяется ее важной ролью как одного из крупных базовых комплексов народного хозяйства России, который обеспечивает многие отрасли промышленности и сельское хозяйство сырьем, социально-ориентированной продукцией, способствует формированию прогрессивной структуры производства и потребления, развитию новейших отраслей и направлений, обеспечивает экономию и сохранение жизненно важных ресурсов, повышение производительности труда в смежных отраслях. Все большее значение приобретает использование химических технологий и методов при очистке и обезвреживании жидких и газообразных сред в различных отраслях, переработке и утилизации отходов. Химический комплекс, являясь крупным поставщиком сырья, полупродуктов, различных материалов и изделий (пластмассы, химические волокна, шины, лаки и краски, красители, минеральные удобрения, кормовые добавки, лекарственные препараты, медоборудование и т. д.) почти во все отрасли промышленности, сельского хозяйства, в здравоохранение, сферу услуг, торговлю, науку, культуру и образование, оборонный комплекс, оказывает воздействие на эффективность их функционирования, развитие в них новых перспективных направлений. Несмотря на известные потери в ходе проводимых в стране реформ, химическая промышленность сохраняет заметную роль в формировании важнейших макроэкономических показателей. На предприятиях отрасли сосредоточено около 8% основных фондов промышленности страны, производится почти 6% промышленной продукции России. Они обеспечивают более 7% налоговых платежей и других доходов в консолидированный бюджет и около 5% общероссийского объема валютной выручки. О роли и значении химической индустрии в развитии экономики свидетельствует то обстоятельство, что уровень химизации народного хозяйства является общепризнанным в мировой практике критерием научно-технического прогресса. В рамках начавшихся в экономике страны позитивных процессов положительные результаты достигнуты и в химической промышленности. Рост объема производства химический продукции составил 39%. Положительная динамика сохраняется и в первом полугодии текущего года. Уровень загрузки производственных мощностей в целом по отрасли повысился до 61%, превысив на 14% показатель 1998 года. По ряду важнейших продуктов (полипропилен, смола ПВХ и сополимеры винилхлорида, метанол) загрузка мощностей превысила 75%, а по полиэтилену достигла 87%. Финансово-экономическое состояние большинства предприятий отрасли в 1999-2000 годах улучшилось, что расширило их возможности инвестирования технического развития. Для обеспечения стабилизации работы предприятий комплекса и его устойчивого экономического развития в перспективе требуется решение целого ряда вопросов и, прежде всего, повышения технической и ценовой конкурентоспособности химического комплекса. Это обусловлено значительным отставанием уровня технической и экономической конкурентоспособности многих производств и продукции комплекса от зарубежного уровня. Большинство предприятий придерживается в своей инновационной деятельности в основном имитационной, догоняющей стратегии, внедряют уже существующую продукцию.
Средняя энергоемкость единицы химической продукции в 2-3 раза выше, чем в США, на 20-50% выше потребление воды, как технологической, так и оборотной, производительность труда, по сравнению с США, в 5-20 раз ниже. Смена поколений технологических процессов осуществляется через 20-25 лет, при 7-8 летних сроках смены в ведущих странах.
Износ основных производственных фондов и, особенно их активной части, превысил в целом по отрасли 75%, а в ряде подотраслей (химических волокон и нитей, основной химии, стеклопластиков и стекловолокна) и на многих предприятиях - более 80%.
Состояние сырьевой базы отрасли является одной из критических проблем, которая во многом определяет важнейшие параметры ее функционирования. Устойчивое развитие химической и нефтехимической промышленности невозможно без решения проблемы обеспечения предприятий отрасли углеводородным сырьем, на базе которого производится более 70% производимой химической продукции. Несмотря на принимаемые в последние годы меры, потребности отрасли в углеводородном сырье удовлетворяются далеко не в полной мере.
В химической индустрии насчитывается около 800 крупных и средних промышленных предприятий и свыше 100 научных и проектно-конструкторских организаций, опытных и экспериментальных заводов с общей численностью более 740 тыс. человек.
Интенсивное развитие химической промышленности в России во второй половине прошлого века привело к тому, что к 1990м годам потребности внутреннего рынка в химических материалах почти полностью удовлетворялись. По общему объему производства страна вышла на первое место в Европе и второе в мире. Однако затем перестроечные поспешные, порой не продуманные преобразования, "сверхскоростная" приватизация привели к резкому спаду в химическом комплексе России.
С 2002 года Россия превратилась в нетто-импортера химической продукции, ввозящего более 50% потребляемых пластмасс, химволокон, лакокрасочных материалов. Ежегодный прирост продукции (4-6%) происходит за счет экспортабельной ее части - удобрения, каучуки и др. Большая доля в этом приросте - цена природного газа, позволяющая отдельным видам химической продукции быть конкурентоспособной на мировом рынке. К сожалению, большинство наших технологий - высокоэнергозатратные, безнадежно устаревшие. Страна - крупнейший в мире экспортер углеводородов, а многие российские предприятия этого сырья недополучают. Крупные нефтяные компании мало внимания уделяют модернизации собственных нефтеперерабатывающих мощностей. (Степень износа оборудования - более 80%, глубина переработки - менее 70% После длительного периода спада производства в 1999 году наметился подъем химической отрасли. За последние шесть лет (2000-2005 годы) объем производства в отрасли увеличился в 1,45 раза. Рост производства в прошлом году составил 105,5% к уровню 2004 года В отрасли созданы такие крупные корпоративные структуры, как "Сибур", "ЛУКОЙЛ-Нефтехим", "Татнефть", "Фосагро", "Еврохим", "Акрон", "Амтел" и другие, на которых выпускается свыше 50% минеральных удобрений, около 40% полимерных материалов, 82% легковых и 95% грузовых автомобильных шин. Но, несмотря на эту положительную динамику, отрасль находится на 20м месте в мире по объему производства и на 11м - по объему продукции на душу населения. Позитивные изменения в основном связаны с ростом производства минеральных удобрений, синтетических каучуков, полимерных материалов, шин для легковых автомобилей и других материалов. Дальнейшее развитие химического комплекса сдерживается целым рядом факторов: недостаточным уровнем научно-технических разработок и их внедрением в промышленность; отсталостью технологий и низкой конкурентоспособностью выпускаемой продукции; ужесточением конкуренции на внешнем и внутреннем рынках; диспаритетом цен и тарифов на продукцию естественных монополий; высокой степенью физического и морального износа оборудования, дефицитом инвестиционных ресурсов; нестабильным обеспечением отрасли углеводородным сырьем (природный и сжиженный газ), на базе которого производится до 80% химической и нефтехимической продукции, и рядом других факторов.
Дата добавления: 2021-11-30; просмотров: 22; Мы поможем в написании вашей работы! |
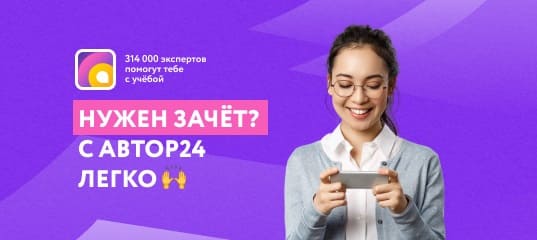
Мы поможем в написании ваших работ!