Зачем нужна очистка (зачистка) листов и профилей?
Лекция 9 МДК 03.01 Сборка, монтаж (демонтаж) элементов судовых конструкций, корпусов, устройств и систем металлических судов
Зачистка корпусной стали от окалины и ржавчины.
Правка листовой и профильной стали
Методы очистки металла и нанесения защитных покрытий
Поступающая на судостроительные заводы сталь обычно имеет на поверхности окалину и ржавчину, наличие которых затрудняет обработку деталей, оборку и сварку конструкций и особенно подготовку конструкций под окраску. Поэтому листовой и профильный прокат перед обработкой подвергают очистке механическим (дробеметным) или химическим (травлением в ваннах) способами.
Наиболее распространенным на судостроительных заводах является дробеметный способ. По сравнению, с химическим он имеет более высокую производительность и эффективность. и Процесс дробеметной очистки состоит в том, что на очищаемую поверхность листа под действием центробежной силы из специальной дробеметной головки выбрасывается со скоростью 50— 60 м/с чугунная дробь (круглая или колотая). Ударяясь с большой скоростью об очищаемую поверхность, дробь удаляет с нее ржавчину окалину. Дробеметная очистка проводится в специальных стационарных установках, представляющих собой закрытые камеры с расположенными по бокам дробеметными аппаратами.
Очищенный металл подвергается интенсивной коррозии. Поэтому на межоперационный период производственного цикла обработки деталей, изготовления узлов и секций, формирования корпуса и окраски последнего необходимо защитить металл от коррозии. С этой целью очищенный прокат подвергают пассивированию или грунтовке. Пассивирование заключается в нанесении на очищенную поверхность стали раствора Мажеф и раствора натуральной олифы в уайт-спирите. Для грунтовки применяют фосфатирующие грунты, например ВЛ-02 и ВЛ-023.
|
|
В настоящее время процесс очистки и защиты листов от коррозии полностью автоматизирован. Для этого созданы специальные поточные линии, на которых выполняется правка, очистка от окалины и ржавчины, грунтовка и сушка листов. Один из проектов таких линий показан на рис. 11.4.
Рис. 11.4. Поточная линия правки, очистки и грунтовки листовой стали.
Правка листовой и профильной стали
Правка листовой стали.
Точность и качество разметки и обработки деталей корпуса, а также последующей сборки и сварки корпусных конструкций в значительной мере зависят от степени ровности поверхности листового и профильного материала.
Сталь (листовая и тонколистовая), поступающая на завод, имеет выпучины, бухтины, волнистость, возникающие в процессе ее прокатки и транспортировки. Неровности могут возникнуть также в результате механических воздействий и по другим причинам. Поэтому листовой и профильный материал, имеющий недопустимую волнистость поверхности и отклонения от прямолинейности, до обработки подвергают правке. При необходимости правят также детали корпуса, получившие недопустимую волнистость поверхности или криволинейность в процессе обработки
|
|
Перед подачей в цех на разметку и вырезку деталей листовую сталь подвергают правке. Необходимость правки обусловливается тем, что иногда величина бухтины и волнистости листов превышает допустимые нормы. Допускаемая величина стрелки прогиба выправленных листов при подаче их на разметку — до 3 мм на 1 пог. м., на фотопроекционную разметку — не более 2 мм на 1 пог. м.
Принцип правки основан на растяжении сжатых волокон листа. Правку производят в холодном состоянии на валках листоправильных машин. При этом лист пропускают между рядами вращающихся валков, которые многократно его изгибают. Сжатые волокна листа растягиваются и принимают такую же длину, что и волокна вне района натяга, вследствие чего лист правится. Для обжатия участков, примыкающих к бухтинам (выпучинам), применяют прокладки. Концы прокладок должны быть расплющены, а кромки закруглены с радиусом не менее 3 мм. В процессе правки прокладки последовательно укладывают в районе сжатых участков листа.
|
|
В зависимости от толщины листов для правки их применяют правильные вальцы с числом валков 5—21. Для листов толщиной более 5 мм — 5—9 валков, толщиной 3—5 мм — 11 —13, а толщиной менее 3 мм —21.
Рабочие валки 2, 3, 5, 6, 7 (рис. 69) приводятся в движение от электродвигателя через редуктор и коробку передач. У некоторых вальцов верхние валки вращаются за счет трения, возникающего между листом и валками 2, 3 во время правки.
Рис. 69. Схема правки листа:
1, 4 — вспомогательные валки, 2, 3, 5, 6, 7 — рабочие валки
Верхний ряд валков перемещают вверх и вниз вручную или вспомогательным электродвигателем через устройство, состоящее из ползуна и направляющих, закрепленных на станине. Перемещением верхних валков устанавливают зазор между валками и регулируют давление на лист при правке листов различной толщины. На правильных вальцах имеется механизм с циферблатом, показывающим расстояние между рабочими валками.
Профильный прокат правят в большинстве случаев на горизонтально-гибочных прессах, роликовых машинах или гидравлических прессах.
|
|
Горизонтально-гибочные прессы для правки профилей имеют ползун, к которому присоединяется толкач. Ползун вместе с толкачом могут совершать возвратно-поступательное движение. Против толкача располагаются два упора, расстояние между которыми может изменяться. Упоры могут перемещаться и в продольном направлений. Профильная полоса, подлежащая правке, упирается в упоры (ролики) пресса. Правка осуществляется нажатием на профиль движущимся толкачом (рис. 11.3).
Рис. 11.3. Схема правки профиля на горизонтально-гибочном прессе.
1 — профильная полоса; 2 — толкач; 3 — упоры пресса.
Принцип действия роликовых машин аналогичен принципу действия правильных вальцов. Эти машины имеют фасонные ролики, соответствующие сечению профиля. При прохождении профиля через ролики реборды последних придают профилю прямолинейную форму. Правильные ролики сменные, что позволяет править профили различного сечения.
Рассмотренные методы правки перегибами имеют ряд существенных недостатков. Не всегда удается достичь требуемой точности правки; время правки листов с одинаковыми размерами и из одинакового материала зависит от первоначального искривления и длины листа; на вальцах с определенными характеристиками можно править листы с относительно узким диапазоном толщин, вследствие чего на заводах устанавливают двое-трое вальцов с разными характеристиками. Качество правки профильного проката зависит также от квалификации правщика, а процесс правки на прессах требует больших затрат труда и пока не поддается автоматизации.
Заслуживает внимания процесс правки методом растяжения на специальных растяжных машинах, который лишен указанных выше недостатков. При этом производительность повышается в 3—4 раза и увеличивается диапазон толщин выправляемых листов на одной машине. В рассматриваемом случае лист или профиль зажимают в специальных зажимах. После этого зажимы с помощью гидравлических домкратов раздвигаются и растягивают выправляемую деталь. К сожалению, по ряду обстоятельств растяжные машины не получили пока распространения на судостроительных заводах, хотя и являются весьма перспективными, особенно в условиях комплексно-механизированного корпусообрабатывающего производства.
Контрольные вопросы к лекции 9 МДК 03.01 Сборка, монтаж (демонтаж) элементов судовых конструкций, корпусов, устройств и систем металлических судов:
Зачем нужна очистка (зачистка) листов и профилей?
Дата добавления: 2021-11-30; просмотров: 13; Мы поможем в написании вашей работы! |
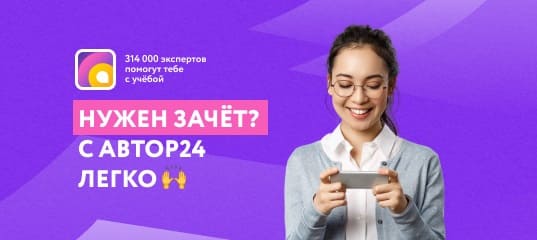
Мы поможем в написании ваших работ!