Сущность кислородной и плазменной и лазерной резки.
Практическое занятие №6.
Резка металла в судостроении.
Резка металла — технологический процесс, в результате которого происходит разделение сортового или листового металла на части и заготовки, или изготовление детали.
Существует несколько методов промышленного разрезания металла. Это традиционные механические (при помощи специальных ножниц, резцов и пил) и ударные способы (посредством гильотины), термические (газокислородная, плазменная и лазерная резка) и холодный гидроабразивный метод.
Механическая резка. Главное преимущество механической резки по сравнению с тепловой заключается в ее высокой производительности. Однако необходима предварительная разметка деталей, которую выполняют, как правило, вручную. Значительных физических усилий требует и ориентация листов относительно ножей.
Виды механической резки металла.
Все процедуры, связанные с механической резкой металла, можно разделить на несколько видов.
- Механическая резка металла с помощью стационарной циркулярной пилы. Чаще всего этот вид резки применяется, когда необходимо обработать профильный металл небольшого размера – например, профильные трубы, а также разрезать металл на квадраты или круги. Кроме того, именно этот вид резки применяется при обработке изделий из цветного металла. Преимуществом резки с применением циркулярной пилы является то, что в ее процессе можно добиться очень ровного среза высокого качества, а допуски при этом будут минимальными.
|
|
Рис. 1 Механическая резка металла с помощью стационарной циркулярной пилы.
- Механическая резка с использованием болгарки. Чаще всего этот вид резки применяется, когда необходимо выполнить поперечные разрезы изделий, выполненных из черного металла, например, арматуры, швеллеров, труб или уголков. Использование этого вида резки позволяет добиться очень высокой точности – допуски здесь бывают меньше, чем при применении газовой резки. Но недостатком резки металла с помощью болгарки является то, что она является очень трудоемкой, а следовательно, и очень дорогой.
Рис. 2 Механическая резка с использованием болгарки (углошлифовальной машинки – УШМ).
- Механическая резка металла с помощью гильотины. Этот вид резки называют еще рубкой металла. Основной спектр применения этого вида резки – резка листового металла, причем, это может быть как черный металл, так и все виды стали – нержавеющая сталь, оцинкованная сталь или электротехническая сталь.
Рис. 3 Схема механической обработки листового проката:
а — резка на гильотинных ножницах; б — разделка кромок на станке СКС-25
|
|
Гильотинная резка металла
Инструмент для гильотинной резки впервые был разработан доктором Гильотеном в 1789 году, и использовался он тогда как орудие казни; сейчас этот страшный инструмент нашел себе другое применение – в изготовлении металлических изделий. Современные гильотинные станки способны работать в продольном и поперечном направлении; конечные срезы получаются без вмятин и зазубрин, а окраска и полимерное покрытие при этом не получают повреждений.
Сейчас активно используется ручной, пневматический, гидравлический и электромеханический инструмент. Стандартный станок предоставляет точность реза в 0,1 мм, длиной в 3000 мм. Работать гильотинными ножницами можно с изделиями толщиной от 0,5 мм; возможно использование алюминиевых листов толщиной до 8 мм; нержавеющей стали – до 12 мм; черной стали – до 20 мм.
Резка металла гильотиной всегда получается прямолинейной. Сам процесс рубки гильотиной схож с принципом работы ножниц (резка осуществляется благодаря опусканию верхнего ножа), только зафиксированными и обладающими куда большими размерами. Высокая точность реза обеспечивается благодаря прижимному механизму.
Выполнять рубку изделий рекомендуется благодаря созданию закладных полос, косынок, нетипичных изделий. Использование электромеханического инструмента предоставляет возможность выбирать наиболее оптимальный режим рубки листов и размещения ножей при резе. К этому оборудованию в комплекте идут системы задач листов для резки, элементы для поддержания листа, а также контролирующие датчики.
|
|
Рис. 4 Машина гильотинной резки
Гидроабразивная резка. Это современный вид резки металла, считающийся наиболее перспективным в настоящее время. Формально она относиться к механической резке металла, но по возможности автоматизации она приближается к лазерной и другим современным видам тепловой резки. Поэтому она изучается несколько обособленно.
Это самый прогрессивный метод на сегодняшний день, позволяющий проводить высококачественную резку металла толщиной до 300 мм. Основной конструктивный элемент установок гидроабразивной резки – это насос сверхвысокого давления. Сейчас уже существуют экспериментальные модели агрегатов с рабочим водяным давлением 6 000 бар. Это просто фантастическая цифра. Когда вода проходит через рубиновое, алмазное или сапфировое сопло, имеющее диаметр всего 0,1 мм, то она набирает скорость, которая в три раза превышает скорость звука! Эта тончайшая направленная струя раскраивает практически все известные виды металлов и их сплавы.
Производительность гидроабразивной резки впечатляет. К примеру «распускание» листа «нержавейки» со стенкой 100 мм производится со скоростью 22 мм в минуту. А нержавеющая сталь со стенкой 1 мм разрезается в десятки раз быстрее – 2 700 мм в минуту. Гидроабразивным методом, как и лазерным, раскраивают не только металлы, то и другие материалы. Приработе с более «податливым» сырьем скорость резки посредством гидроабразивной струи может быть еще больше. В случае со стеклом средней толщины она составит примерно 11 000 мм в минуту. Прочные композиты режутся немного медленнее.
|
|
Как правило, разрезание материалов с мягкой структурой осуществляют струей чистой воды. Абразивы (чаще всего это гранатовый песок) подмешивают для работы с металлами и другими твердыми материалами. Однозначно сказать, что гидроабразивная технология «лучше всех», нельзя. Каждый метод имеет свои преимущества и недостатки. Например, для разрезания заготовок толщиной до 6 мм лучше подходит лазер – в плане экономичности. А вот для качественного разрезания металлов толщиной более 6 мм лучше всего использовать гидроабразивные или плазменные установки.
Рис. 5 Схема гидроабразивной резки.
Конечно же, холодная гидроабразивная струя позволяет получать кромки высочайшего качества. Любая деформация, образование окалины, окислов и т.п. полностью исключаются. Идеально ровные кромки не требуют проведения никакой дополнительной обработки.
Некоторые материалы проблематично разрезать плазмой по причине их низкой электропроводности. Лазер не «режет» заготовки, которые отражают луч. В этом отношении гидроабразивный способ является универсальным.
Метод разрезания металла водно-абразивной струей обеспечивает наименьшие металлопотери. При работе с заготовками, имеющими стенку 50 мм, ширина реза при использовании газокислородного способа составит 20 мм, а гидроабразивная технология «переводит» всего 2 мм ширины. Экономия на 1 метр реза – 15 кг сырья.
Что касается минусов гидроабразивной резки, то их два: высокая стоимость процесса и быстрый износ определенных узлов и деталей самого оборудования. Из-за работы под высоким давлением гидроабразивные установки требует регулярного проведения обслуживания и ремонта.
Тепловая резка металла
Сущность кислородной и плазменной и лазерной резки.
Дата добавления: 2023-02-21; просмотров: 28; Мы поможем в написании вашей работы! |
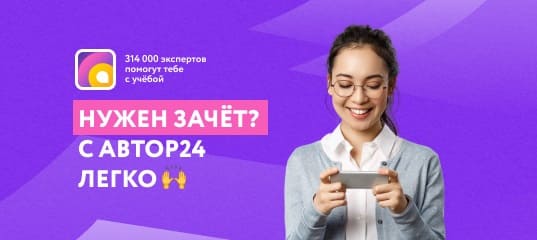
Мы поможем в написании ваших работ!