Термодинамика процессов получения наноструктур 2D-размерности
МИНИСТЕРСТВО СЕЛЬСКОГО ХОЗЯЙСТВА РОССИЙСКОЙ ФЕДЕРАЦИИ
Федеральное государственное образовательное учреждение высшего профессионального образования
«Московский государственный агроинженерный университет имени В.П. Горячкина»
Кафедра «Вычислительная техника и прикладная математика»
РАСЧЕТНО-ГРАФИЧЕСКАЯ РАБОТА
_____________________________________________________________________________________________________________________________________________________________________________
Преподаватель ____________ _____________________________
подпись, дата инициалы, фамилия
Студент _________ ___________ ______________________________
номер группы подпись, дата инициалы, фамилия
Москва 2013
1. Основные методы и исходные материалы
Тонкие наноструктурированные пленки представляют собой организованные наносистемы, в которых наноразмер проявляется только в одном измерении, а два других могут обладать макроразмерами.
Существует несколько хорошо зарекомендовавших себя методов получения данных структур: эпитаксия, молекулярное наслаивание, осаждение и выпаривание коллоидных растворов, технология Ленгмюра–Блоджетт и химическое газофазное осаждение летучих соединений.
Хорошо известно получение нанопленок методами эпитаксии. В этом случае на ориентированную поверхность монокристалла наносят лазерным испарением или с помощью молекулярных пучков требуемое вещество. Несмотря на достаточно простую идею, реализация данной технологии требует чрезвычайно сложных технических решений. Основные требования к установке эпитаксии следующие:
|
|
1) в рабочей камере установки необходимо поддерживать сверхвысокий вакуум (около 10−8 Па);
2) чистота испаряемых материалов должна достигать 99,999999%;
3) в рабочей камере установки необходимо регулировать плотность потока вещества.
Особенностью эпитаксии является невысокая скорость роста пленки (обычно менее 1000 нм в час).
Метод наиболее часто используется для выращивания полупроводниковых гетероструктур из растворов, основанных на элементах из третьей и пятой групп Периодической системы химических элементов. Основное преимущество метода – возможность создания уникальных наноструктур с очень высокой чистотой, однородностью и малым количеством дефектов. К недостаткам метода можно отнести высокую цену оборудования и исходных материалов, малую скорость роста, сложность поддержания высокого вакуума [14].
Метод молекулярного наслаивания состоит в организации поверхностных химических реакций с пространственным и временным разделением. С помощью замещения, например, гидроксильных групп на поверхности оксида алюминия или оксида кремния на различные анионы, затем на катионы можно создавать нанопленки любой толщины – от монослоя атомов до десятка слоев на поверхности.
|
|
Главным условием воспроизводимого и максимально полного замещения функциональных групп на поверхности матрицы при проведении синтеза по методу молекулярного наслаивания является осуществление различных стадий взаимодействия реагентов (АС4, АВ4, NB4, NC4, MC4) c функциональными группами (ФГ) твердого тела (В, С) в условиях максимального удаления от поверхности.
Различные по химическому составу нанопленки получают путем осаждения и выпаривания коллоидных растворов по принципу свободного падения кластеров на подложку. Данные структуры характеризуются как высокоорганизованные, но непрочные. Попытки связать кластеры лигандами и сделать пленку прочнее приводят к потере ее организованности. Данное противоречие ограничивает возможность практического применения наноструктур [29].
Эффективным методом получения нанопленок служит технология Ленгмюра–Блоджетт. Метод был предложен лауреатом Нобелевской премии (1932) Ленгмюром еще в 1920 г. и развит его коллегой Блоджетт в 1935 г. Сущность метода заключается в следующем. На поверхность воды впрыскивается раствор амфифильного соединения (ПАВ). Количество вещества подбирается так, чтобы площадь его монослоя не превысила площади рабочей поверхности ванны Ленгмюра–Блоджетт. Затем с помощью плавучего барьера задается поверхностное давление, для того чтобы перевести монослой в жидкокристаллическое состояние, которое необходимо для его переноса на твердую подложку. Далее с помощью микрометрической подачи подложка опускается или поднимается сквозь монослой со скоростью от см/мин до см/с. Перед нанесением каждого следующего монослоя барьер автоматически сдвигается так, чтобы сохранить давление на пленку. В зависимости от направления движения подложки сквозь монослой получаются пленки с различной молекулярной ориентацией. При движении подложки вниз (рис. 2) на твердой гидрофобной поверхности формируется монослой с ориентированными к подложке гидрофобными хвостами ПАВ, которые образуют структуру Х-типа. При движении гидрофильной подложки вверх формируется мультислой со структурой Z-типа. Поочередное прохождение подложки сквозь монослой сверху вниз и снизу вверх дает мультислой Y-типа, аналогичный по структуре липидным слоям биологических мембран.
|
|
Возможно получение как мономерных, так и полимерных пленок. В случае полимерных пленок применяются три варианта: формирование монослоев полимеров на поверхности жидкости и их перенесение на твердую подложку; формирование монослоев из мономеров с последующей полимеризацией, а затем перенесение на твердую подложку; формирование монослоев из мономеров, перенесение их на твердую подложку, а затем полимеризация в пленке Ленгмюра–Блоджетт.
|
|
Нанопленки, полученные вышеописанными способами, находят разнообразное практическое применение в различных областях науки и техники:
1) в электронике (нанолитография с разрешением 20–50 нм, изолирующие и проводящие ультратонкие пленки, туннельные диэлектрики, пассивирующие и защитные покрытия, элементная база молекулярной электроники, матрицы, содержащие полупроводниковые наночастицы, матрицы для создания ультратонких слоев окислов металлов);
2) оптике (активные слои для записи информации оптическим способом и атомно-зондовым методом, фотохромные покрытия со встроенными светочувствительными белковыми молекулами, просветляющие покрытия, дифракционные решетки, интерференционные и поляризационные светофильтры, плоские моно- и полимодовые световоды, удвоители частот, барьерные слои в фотодиодах);
3) прикладной химии (химия поверхности и поведения частиц на поверхности, катализ, фильтрация и обратный осмос мембран, адгезия);
4) микромеханике (антифрикционные покрытия).
Однако для создания новейших конструкционных материалов с заданными свойствами наиболее перспективным считается метод химического газофазного осаждения летучих соединений.
Химическое газофазное осаждение представляет собой процесс получения твердых веществ реакциями с участием газообразных соединений. Сущность данного метода заключается в следующем: исходное соединение, переведенное путем испарения или возгонки в газообразное состояние, поступает в реакционную камеру, где осаждается на поверхности подложки, нагретой до температуры разложения реагента. По механизму реакции, протекающие в ходе реализации метода, подразделяются на четыре типа:
1) термическое разложение, диспропорционирование газообразных соединений (например, SiH4→Si, Ni(CO)4 →Ni);
2) взаимодействие двух и более газообразных веществ
(WF6 + H2→W, SiCl4 + NH3 →Si3N4);
3) пиролиз газообразных углеводородов
(C2H5OH + O2 → CO2 + С + H2O);
4) взаимодействие газообразных веществ с твердыми, так называемое контактное осаждение (WF6 + Si → W).
Активирование процесса осуществляют термически, фотохимически либо посредством плазмы [30].
При этом метод химического газофазного осаждения обладает следующими характеристиками:
1. Широкий диапазон скоростных (от 0,01 мкм/мин до 10 мкм/мин) и температурных (от 70 до 1500˚С) режимов ведения процесса.
2. Высокая плотность (беспористость) получаемых пленок и покрытий.
3. Обеспечение равномерного «омывания» парами реагента поверхности подложки любой конфигурации.
4. Возможность ведения процесса по замкнутому циклу, что обеспечивает его экологическую чистоту и безопасность.
К основным преимуществам химического газофазного осаждения относится тот факт, что при его реализации практически отсутствуют ограничения по химическому составу получаемых структур. Все присутствующие частицы могут быть осаждены на поверхности материала. Состав и структура получаемых объектов зависят от комбинации реагентов и параметров процесса.
В качестве исходных реагентов используются различные соединения металлов, обладающие рядом характерных свойств:
высокая летучесть при относительно низких температурах;
стабильность (в газообразном состоянии не разлагаются ниже рабочих температур термораспада, установленных в конкретном процессе химического газофазного осаждения);
возможность создания высокой концентрации паров, достаточной для достижения оптимальной скорости роста металлической структуры;
исключение образования высокотоксичных соединений в ходе реализации процесса;
отсутствие агрессивности по отношению к подложке и технологической аппаратуре [31].
Перечисленным требованиям полностью удовлетворяют некоторые группы металлоорганических соединений (МОС). МОС – органические соединения, содержащие в составе молекул как металл, так и собственно неметаллические элементы при наличии связей «металл – углерод» и «металл – элемент – углерод». Современный уровень развития органической химии позволяет получать МОС практически для всех металлов Периодической системы Д.И. Менделеева. В настоящее время таких соединений, синтезированных, апробированных в лабораторных условиях и пригодных к практическому применению, насчитывается свыше пятнадцати тысяч. Многообразие видов МОС, выпускаемых в промышленных масштабах, расширяет возможности по их применению для получения наноструктур как в качестве исходных материалов в виде индивидуальных соединений, так и в виде катализаторов и стабилизирующих добавок.
В монографии рассматриваются карбонильные, циклопентадиенильные и β-дикетонатные соединения переходных металлов как наиболее пригодные для использования в условиях ремонтного производства благодаря разнообразию структурных особенностей и физико-химических свойств (рис. 3).
Для упрочнения и восстановления деталей машин, а также в процессах создания наноматериалов широкое применение получили карбонильные соединения никеля и железа. Под термином «карбонильные материалы» подразумеваются, с одной стороны, карбонилы различных металлов и, с другой, – чистые металлы в виде высокодисперсных порошков, покрытий и тонких пленок, полученных при термической диссоциации карбонильных соединений соответствующих металлов.
Особая природа связи между атомами металла и лигандами монооксида углерода (СО) предопределяет специфику химических свойств данных соединений. Изначально в молекуле СО имеются две свободные пары электронов, одна из которых находится на s-орбитали кислорода, а другая – на р-орбитали углерода, вытянутой в сторону, противоположную связи С-О. Данная орбиталь, обладая высокой энергией, обуславливает донорные свойства монооксида углерода. В целом связи как алкильных, так и арильных групп с переходными металлами малоустойчивы. Это происходит, с одной стороны, вследствие малой разности электроотрицательностей между металлом и углеродом, а с другой, из-за небольшой величины двухцентрового интеграла перекрывания между sp3- (или sp2-) атомными орбиталями углерода и атомными орбиталями металла.
При анализе структуры карбонильных соединений установлено, что связи атомов в них значительно ослаблены из-за использования металлом электронов, приобретенных от лигандов СО, которые в свою очередь постоянно перетягивают электроны от атомов металла, поэтому при нагревании электроны стремятся занять исходное положение и атом металла из возбужденного состояния пытается перейти в нейтральное.
По структурному признаку карбонилы делятся на четыре группы:
одноядерные – с одним атомом металла в молекуле, например Fe(CO)5, Ni(CO)4 и др.;
многоядерные монометаллические – с двумя или более атомами металлов, например Co2(CO)8, Fe3(CO)12 и др.;
полиметаллические – с двумя или более разными атомами металлов, например Mn2Fe(CO)14, FeRu(CO)12, MnReFe(CO)14 и др.;
смешанные – с атомами металлов и неметаллов, например CFe(CO)15, CRu(CO)17 и др.
В каждой из обозначенных групп могут иметь место следующие типы связей:
ковалентная связь М-М в биметаллических карбонилах, при которой каждый атом металла поставляет для связи один электрон;
координационно-ковалентная связь М-СО, при которой атом С отдает металлу электронную пару (σ-связь) и дополнительно связывается с металлом обратной π-связью с участием d-электронов металла;
ковалентная σ-связь между металлом и СО, причем атом С служит «мостиком» между атомами металла, образуя связь с каждым из них;
в карбонилах типа M6(CO)16 имеется связь M-CO, при которой СО служит «мостиком» между тремя атомами металла.
Для одноядерных карбонилов, к которым относятся, в частности, тетракарбонил никеля Ni(CO)4, пентакарбонил железа Fe(CO)5, гексакарбонил молибдена Мо(СО)6, связь между металлом и лигандами СО носит координационно-ковалентный характер, когда атом углерода отдает металлу электронную пару (σ-связь) и дополнительно связывается с ним обратной π-связью при участии d-электронов металла. В многоядерных моно- полиметаллических и смешанных карбонилах возможно формирование ковалентной связи М-М, при которой каждый атом металла поставляет для связи один электрон, а также ковалентной σ-связи между металлом и СО, причем атом С служит «мостиком» между атомами металла, образуя связь с каждым из них.
Из анализа структуры и связей карбонилов металлов следует, что связи атомов в этих соединениях значительно ослаблены благодаря использованию металлом «чужих» электронов, приобретенных им от лигандов СО, которые в свою очередь постоянно «перетягивают» электроны от атомов металла. При нагревании карбонила электроны пытаются занять исходное положение, и атом металла из возбужденного состояния стремится перейти в нейтральное.
В целом, карбонилы металлов представляют собой легколетучие легкоплавкие кристаллические соединения либо низкокипящие жидкости и газы. Свойства некоторых карбонильных соединений переходных металлов представлены.
Данные карбонильные соединения металлов легколетучи и являются исключительно удобными реагентами для получения металлов путем термической диссоциации по формуле
где М – переходный металл V…VIII групп Периодической системы [31…34].
Увеличение номенклатуры модифицированных волокон достигается за счет расширения технологических возможностей получения композиционных материалов с заданными свойствами. Важная роль при этом отводится циклопентадиенильным соединениям металлов, так как они термически более устойчивы по сравнению с карбонильными, что позволяет варьировать температурные интервалы ведения металлизации.
Специфика сэндвич-π-связей заключается в том, что система делокализованных π-электронов лиганда осуществляет химическое взаимодействие с вакантными орбиталями атома переходного металла в подходящем валентном состоянии (s-, p-, d-орбиталями).
При этом возможно образование следующих типов связей:
1) связи, сформированные за счет неспаренных электронов в орбиталях металла и лиганда;
2) донорно-акцепторные связи, образованные при взаимодействии пар электронов в орбиталях лиганда с вакантными атомными орбиталями металла;
3) дативные связи – за счет взаимодействия неподеленных пар электронов в атомных орбиталях металла и вакантных обычно разрыхляющих молекулярных орбиталях лиганда [35, 36].
Для металлизации подложек в виде волокон перспективным направлением является использование циклопентадиенила никеля (никелецена) Ni(C5H5)2. Никелецен проявляет значительную химическую устойчивость, так как его реакционные центры – атом металла и химические связи С5---Ni---С5 – экранированы от действия таких агрессивных реагентов, как сольватированный протон, ОН- и других.
Вместе с тем на атоме Ni и на каждом из координированных колец циклопентадиенила локализованы эффективные заряды величиной +0,7 и –0,35 соответственно, поэтому никелецен намного легче подвержен реакциям электрофильного замещения, чем бензол.
Исследованиями [31, 32] установлено, что большинство циклопентадиенильных соединений образуют изоморфные с никелеценом кристаллы и имеют аналогичные значения температур плавления (173 ºС) и разложения (470 ºС). Это позволяет осуществлять технологический процесс нанесения пленок и покрытий при их совместном использовании.
В процессе химического газофазного осаждения важная ниша отведена β-дикетонатам металлов, так как в отличие от карбонилов, образование которых возможно лишь для переходных металлов V–VIII групп, данные соединения получены практически для всех металлов ПСХЭ Д.И. Менделеева.
Класс β-дикетонатов относится к внутрикомплексным соединениям, которые часто называют клешневидными, или хелатами (от греч. «chele» – «клешня»). Общая формула β-дикетонатов металлов представлена на рис. 6, где n – степень окисления металла, R и R' – концевые лиганды СН3, CF3 и другие.
Природа связи «металл – хелат» была предметом ряда исследований [27, 33], однако наиболее надежные данные по расчету β-дикетонов и их хелатов с медью, в частности, были опубликованы в работах [34…36], согласно которым в образовании σ- и π-связей хелатообразующего лиганда с центральным атомом принимают участие все атомные орбитали металла, молекулярные орбитали и неподеленные пары атомов кислорода, азота или серы хелатообразующего лиганда. При этом разделение зарядов (отрицательный заряд на атомах кислорода) уменьшается при образовании хелата, что объясняет наличие ковалентных связей с определенной степенью ионности.
В настоящее время экспериментально подтверждено, что хелатный эффект не является энергетическим и не влияет на прочность связи, а вызывает структурно-кинетические изменения, приводящие к усложнению механизма диссоциации комплекса и снижению скоростей диссоциации хелатных соединений по сравнению с нехелатными [31, 35].
Летучесть и термическая стабильность β-дикетонатов – важнейшие их параметры для процесса химического газофазного осаждения – зависят прежде всего от природы концевых лигандов и металла, а также от стехиометрии комплексов и структуры кристаллической решетки. Так, для β-дикетонатов меди отмечен следующий ряд летучести:
Cu(CF3-CF3acac)2 > Cu[C3F7-C(CH3)3acac]2 > Cu[CF3-C(CH3)3acac]2 > > Cu(CH3-CF3acac)2 > Cu[CH3-C(CH3)3acac]2 > Cu[C(CH3)3-C(CH3)3acac]2 > > Cu(acac).
Введение CF3- и C3F7-групп в боковые цепи увеличивает летучесть β-дикетонатов меди. Наоборот, наличие ароматических, гетероциклических и эфирных групп снижает этот показатель [31]. Таким образом, строение и тип металлоорганических соединений, используемых в качестве исходных реагентов химического газофазного осаждения, определяют механизм термической диссоциации и качество получаемых покрытий.
2. Технологические возможности и аппаратурное оформление процессов нанесения наноструктурированных пленок на различные типы подложек методом химического газофазного осаждения металлоорганических соединений
Химическое газофазное осаждение различных соединений в настоящее время используется как универсальный способ получения функциональных наноструктурированных пленок и покрытий.
Сущность метода заключается в том, что исходное соединение, находящееся в жидком или твердом состоянии, переводится в газообразное путем испарения или возгонки. Полученная газовая смесь подается в реакционную камеру и при контактировании с подложкой осаждается на ее поверхности, нагретой до температуры разложения используемого металлоорганического соединения. Процесс осаждения покрытий может проводиться как в вакууме, так и в среде транспортирующих МОС газов. Особенностью метода химического газофазного осаждения металлоорганических соединений является механизм образования покрытий, когда металлизируемая поверхность подложки находится в окружении газовой смеси, включающей в себя пары металлоорганического соединения, молекулы которого постоянно перемещаются во всех направлениях в объеме реакционной камеры, что позволяет им, в отличие от других способов металлизации, приближаться и вступать в контакт со всеми частями и участками подложки, имеющими температуру, необходимую для разложения данного соединения.
В настоящее время разработано и апробировано несколько технологических методов нанесения покрытий из газовой фазы, при которых лабораторные и промышленные установки действуют по схеме: подготовка исходных веществ к реакционному состоянию; транспортировка их в зону металлизации; термическое разложение и осаждение на поверхность подложки; сбор побочных продуктов химических реакций процесса. При этом широко применяется серийно выпускаемое промышленностью электровакуумное оборудование, узлы привода, контрольно-измерительные приборы, арматура и другие комплектующие изделия. Основным узлом любой из установок для металлизации является реакционная камера, проектирование и изготовление которой производится индивидуально, в зависимости от вида и программы выпускаемой продукции, требований по толщине наносимых покрытий, шероховатости поверхностей, твердости и т.д. Решение этих вопросов достигается применением различных способов нагрева и конструктивными особенностями реакционных камер, позволяющих производить разнонаклонное размещение деталей, подвод реакционных смесей, отвод побочных продуктов, образовавшихся в результате химических реакций процесса разложения МОС.
Принятые технологическая схема или способ проведения процесса осаждения покрытий оказывают влияние как на производительность процесса и его аппаратурное оформление, так и на состав и свойства получаемых покрытий, поэтому правильный выбор этих параметров имеет важное значение для обеспечения эффективности процесса при его реализации в условиях производства.
Успешное решение поставленных задач во многом зависит от правильного использования технологических методов и оборудования для металлизации с учетом совместимости исходных металлоорганических соединений, размеров и геометрической формы подложек.
В работах [31, 34, 37] предприняты попытки систематизировать существующие способы газофазного разложения МОС и осаждения покрытий. Это позволяет производить выбор оптимальных схем организации технологических процессов и их аппаратурного оформления при нанесении покрытий с учетом формы, размеров, физико-механических и технологических свойств деталей в условиях организации работ на предприятиях, в том числе и ремонтных.
Классификация способов проведена по следующим основным признакам: исходному соединению, методу нагрева, составу среды в реакторе, виду подложки и конструктивным особенностям основных узлов реактора [38].
Для исследования физико-механических свойств покрытий на образцах из конструкционных сталей представляет интерес лабораторная установка с реакционной камерой, оборудованной внешним источником нагрева образцов и деталей. Металлические покрытия получаются в результате разложения жидких МОС в емкости, из которой газовая смесь подается по трубопроводу через расходомер в реакционную камеру, где находится образец. В реакционной камере пары металлоорганических соединений распадаются на металл, осаждаемый на нагретую поверхность образца, и побочные продукты химических реакций процесса, которые через расходомер и фильтр откачиваются вакуумным насосом.
Нагрев образцов осуществляется инфракрасной лампой через кварцевое стекло, охлаждаемое направленной струей воздуха.
Температурный режим в реакционной камере контролируется и поддерживается регулятором температуры с использованием термопары. Для предотвращения осаждения металла на стенки реакционной камеры имеется система охлаждения. В случае нанесения покрытий при термическом разложении металлоорганических соединений, находящихся в твердом состоянии, используется сублиматор, оборудованный электрическим подогревом. Это позволяет увеличить температурные режимы.
Время проведения процесса устанавливается в зависимости от необходимой толщины покрытия и реакционной способности газовой смеси. В случаях использования инфракрасных ламп в промышленных установках применяется конструкция, когда система нагрева размещается внутри реакционной камеры.
В лаборатории высоких технологий ГНЦ РФ ГНИИХТЭОС (г. Москва) создана установка, оборудованная системой нагрева, когда одна или несколько подложек при помощи специальных контактов последовательно включаются в электрическую цепь, обладающую активным сопротивлением. При пропускании тока определенной величины детали нагреваются до заданной температуры. Дальнейший процесс разложения МОС и осаждения покрытий протекает аналогично и в соответствии с описанием схемы. Реакционная камера представляет собой металлический колокол с объемом, рассчитываемым для конкретного технологического процесса, при этом предусматриваются специальные вводы для присоединения контактов-зажимов и термопары, а также для подвода газовой смеси из испарителя и сублиматора [37].
Сублиматор представляет собой цилиндрическую емкость с регулятором подачи МОС.
Для влияния на процессы подготовки газовой смеси при использовании различных видов МОС имеется термостат. Для предотвращения выбросов загрязняющих веществ в атмосферу предусматриваются печь доразложения МОС и печь дожига монооксида углерода.
Преимуществом этого метода является рациональное использование исходных металлоорганических соединений ввиду того, что в ходе процесса металлизации нагревается только подложка, а остальные части реакционной камеры имеют температуру, не превышающую режимы осаждения МОС. Процесс легко поддается автоматизации и может модернизироваться применением специальной оснастки и доработкой в конструкции реактора при нанесении покрытий на изделия, что можно проиллюстрировать на примере модернизации базовой модели промышленной установки 1МК608, для которой разработан способ нагрева при нанесении покрытий на внутренние поверхности деталей, имеющих форму полых цилиндров. В этом случае система работает следующим образом: нагреваемые детали устанавливаются на контакты нижней крышки камеры; при закрывании верхней крышки ее контакты, аналогичные контактам на нижней крышке, прижимают детали сверху. Контакты при помощи перемычек электрически соединены между собой так, чтобы получилась последовательная цепь из деталей, изолированных от металлических крышек реакционной камеры прокладками. Под контакты верхней крышки установлены упругие прокладки, необходимые для компенсации лишних расширений деталей при нагреве и разнице их по длине. Надежное электрическое соединение между деталями, контактами и крышками обеспечивается необходимым усилием прижатия верхней крышки [31].
Описанные выше установки имеют индивидуальные системы испарения МОС, когда образование газовой фазы происходит в автономном испарителе или сублиматоре, находящемся вне реакционной камеры, с последующей транспортировкой паров по термостатируемому трубопроводу. Такой способ применяется при использовании однородных металлоорганических соединений.
При использовании смесей исходных реагентов первоначально насыщенная равновесная газовая фаза МОС по мере подачи по трубопроводам, поступления в реакционную зону и разбавления ее продуктами распада в процессе осаждения становится ненасыщенной и неравновесной.
Отклонение состава газовой смеси от равновесного состояния и состояния насыщения по МОС трудно поддается оценке, что в большинстве случаев оказывает негативное влияние на стабильность протекания различных процессов в ходе газофазной металлизации и качество полученных покрытий. Устранение этого недостатка может быть достигнуто обеспечением динамической подачи в зону осаждения МОС, находящихся в жидкой фазе, с последующим испарением их в непосредственной близости от поверхности покрываемой подложки. По своему положению относительно изделия испарители могут быть стационарными и нестационарными. Вмонтированные в крышку реакционной камеры испарители стационарного типа могут снабжаться автономным электронагревателем. Испаритель имеет два нагревателя: один для испарения МОС, а другой для подогрева газовой смеси. Испаритель нестационарного типа обычно закрепляется на нижней части подвижного термостатируемого питателя и применяется без автономного нагревателя.
Испаритель и холодильник для утилизации продуктов разложения могут быть смонтированы в рабочей части камеры разложения. В этом случае процесс реализуется по следующей схеме: металлизируемое изделие (подложку) размещают в реакционной камере на специальной вращающейся подставке; включают нагреватели и вакуум-насос; металлизируемые поверхности подложки нагревают до температуры разложения МОС, наружную поверхность конусной камеры испарителя – до температуры кипения МОС, а внутреннюю поверхность – до температуры, на 10–20 ˚С ниже температуры разложения МОС. Одновременно подают хладагент и исходное соединение, которое, стекая по поверхности конусной камеры, испаряется, и его пары, перемещаясь вдоль внутренней поверхности камеры, нагреваются до температуры, на 20–30 ˚С ниже температуры разложения, поступают в зону металлизации, где разлагаются с образованием металлического покрытия на поверхности подложки. В ходе процесса газообразные продукты через патрубок поступают в аппарат дополнительного разложения или возвращаются для последующего использования, остатки неразложившегося МОС конденсируются в нижней части реакционной камеры и через патрубок стекают в сборник.
В промышленных масштабах значительная часть металлоорганических соединений используется в качестве промежуточного сырья при получении порошковых материалов. Так, производство порошкового карбонильного железа, основанное на термическом разложении пентакарбонила железа (ПКЖ), организованное в г. Дзержинске Нижегородской области, обеспечивает все заказы предприятий электротехнической промышленности такими материалами с необходимыми физико-механическими и химическими свойствами для достижения заданных электромагнитных параметров [34].
В применяемой установке жидкий ПКЖ из напорной емкости через фильтрующие и дозирующие устройства поступает в испаритель, из которого образовавшаяся газовая смесь через теплообменник направляется в аппарат разложения. В верхней части аппарата пары ПКЖ смешиваются с аммиаком, в результате чего происходит термическая диссоциация Fe(CO)5 с образованием порошка карбонильного железа, монооксида углерода и побочных продуктов химических реакций. Газообразные продукты процесса направляются в рукавный фильтр, увлекая за собой порошок карбонильного железа. При этом около 80% порошка осаждается в приемнике аппарата разложения, 17…18% его задерживается фильтром и 2…3% улавливается в соединительном коллекторе и конечном рукавном фильтре. Отходящий монооксид углерода на выходе из конечного фильтра поступает на очистку от аммиака в скруббер и далее направляется в газгольдер для повторного использования на стадии синтеза ПКЖ.
Основными параметрами, характеризующими технологический режим процесса разложения ПКЖ, являются: температурный режим (величина и распределение температур) по высоте аппарата разложения, которая составляет у промышленных установок 5000 мм при диаметре до 1000 мм; дозировка аммиака и подача ПКЖ на единицу объема аппарата.
На мончегорском комбинате «Североникель» (Мурманская область) никелевые порошки получают на установках, работающих по следующей схеме. В колонну, состоящую из шести смонтированных в вертикальном направлении емкостей длиной 800 мм и диаметром 700 мм постоянно по замкнутому циклу подаются частицы никеля, которые под воздействием воздушного потока находятся в постоянном движении. Пары тетракарбонила никеля из отдела синтеза через распределительную трубу поступают одновременно во все шесть емкостей и, соприкасаясь с нагретыми частицами, разлагаются на их поверхностях. В результате нарабатываются никелевые окатыши, которые при достижении размеров 8…12 мм являются готовой продукцией и задерживаются в накопителе, остальные проваливаются через ячейки распределителя в отсеки сборника, ковшовым элеватором загружаются в верхнюю емкость колонны, и процесс металлизации продолжается до получения заданных размеров [32].
Основываясь на рассмотренной технологии, в лаборатории высоких технологий ГНЦ РФ ГНИИХТЭОС (г. Москва) создана опытная установка, в которой металлизация частиц с размерами более 30 мкм осуществляется в аппарате с псевдоожиженным слоем. Известно, что явление псевдоожижения заключается в том, что при продувании газа снизу через слои мелкодисперсных частиц, которые приходят в беспорядочное движение, слой расширяется, приобретает вид кипящей жидкости и приобретает свойство текучести [31, 34]. При металлизации основным преимуществом кипящего слоя является интенсивное движение и высокая текучесть составляющих его частиц, которые, циркулируя, одновременно являются теплоносителем, а перемещение их во всем объеме реактора обеспечивает равномерность металлического покрытия.
В установке применяется фонтанирующий слой, для образования которого подача нагретой газовой смеси производится из сублиматора-смесителя в центральную часть аппарата разложения, оборудованного системой электронагрева. Восходящий газовый поток, проходя вдоль оси реактора, вступает в контакт с нагретыми частицами, в результате чего происходит разложение паров МОС и осаждение металла на поверхность частиц. Необходимо отметить, что процесс металлизации одновременно идет и на периферии реактора, так как здесь также происходит их интенсивный подогрев и контакт с газовой смесью. В качестве несущего газа используются продукты реакции процесса. Для поддержания материального баланса используется дополнительный баллон с монооксидом углерода.
Перспективным направлением при создании композиционных материалов считается применение в качестве армирующих наполнителей нитевидных кристаллов – вискеров [29]. К вискерам относят монокристаллы с высокими прочностными показателями, достигаемыми за счёт больших значений (более 20) отношения их длины к их условному диаметру. Так, например, прочность 13100 и 13200 МПа при длине 3–30 мкм и диаметре 0,5–20 мкм установлена у вискеров железа и вольфрама при осаждении пентакарбонила железа и гексакарбонила вольфрама [39]. Данные структуры также получают методом химического газофазного осаждения металлоорганических соединений с применением вышеописанных установок.
Практический интерес представляет технология металлизации синтетических и стеклянных волокон, которые используются в том числе и в качестве армирующих наполнителей при разработке композиционных материалов.
Металлизация волокон, находящихся в пучке, достигается за счёт теплоизлучения от пучка предварительно нагретых волокон, обладающих большой суммарной теплоемкостью и находящихся в непосредственной близости от конденсированной фазы разлагаемого МОС. При этом происходит термораспад МОС, и покрытие осаждается на каждом отдельном волокне. Совмещение процесса испарения МОС с терморазложением имеет преимущество в том, что отпадает необходимость дополнительно применять испаритель и осуществлять подачу паров МОС в зону осаждения. Применение предварительного перегрева позволяет использовать для металлизации волокна, обычно обработанные замасливателем в процессе вытяжки с целью предотвращения их запутывания. Замасливатель легко удаляется в вакууме при 500–600 ˚С.
Кроме того, волокно, находящееся в параллельном пучке, обладает большей прочностью на разрыв, в результате исключается обрыв волокна при протяжке в процессе непрерывного осаждения металла. Этим методом на каждом волокне получается достаточно равномерное по толщине покрытие.
Металлизацию волокна проводили на модельной вакуумной установке периодического действия, состоящей из двух камер с размещёнными внутри вращающимися бобинами, одна из которых подаёт волокно, другая – принимает [37]. Схема устройства представлена на рис. 2.8.
Камеры соединены между собой трубкой с внешними нагревателями, один из которых расположен перед реактором (зоной металлизации), другой – после реактора. Устройство снабжено также вибратором, выполненным в виде эбонитового стержня, по которому скользит жгут волокна, когда это необходимо. Вибратор выполняет роль дополнительного расталкивателя волокон, тем самым увеличивает доступ МОС к волокнам.
В работах [31, 37] отмечается возможность нанесения металлических электропроводящих слоёв металлов, таких как хром, кобальт, медь и других, на волокна диаметром 7–10 мкм, находящихся в пучках из 100–10000 отдельных волокон, причём металлизация проводится непрерывной протяжкой предварительно нагретых волокон в среде металлоорганических соединений.
Стержень подвергают вибрации до частоты 4–7 кГц, и одновременно от источника переменного тока и конденсатора подаётся отрицательный заряд 2·10-7–1·10-5 Кл, затем подаются пары МОС. В результате вибрации происходит первая стадия металлизации, затем частично заряженные волокна отталкиваются друг от друга, что способствует образованию на поверхности равномерного покрытия необходимой толщины с электросопротивлением до 20 Ом/см [37].
Известен способ металлизации стеклянных и базальтовых волокон диаметром 15...20 мкм, находящихся в пучке. После подготовки поверхности пропиткой в растворе ацетилацетона меди в этиленгликоле волокна помещают в реакционную камеру, где нагревают до 300 ˚С, при этом происходит распад ацетилацетона меди с образованием медной плёнки. В результате металлизации на поверхностях стеклянных и базальтовых волокон получено равномерное медное покрытие толщиной до 1 мкм. Электросопротивление волокон достигает значений до 13 Ом/см, при этом металлизированные волокна имеют поверхностную прочность по металлическому покрытию, которая зависит не от общего сечения волокна, а от сечения и свойств покрытия. Полученные свойства по показателям электросопротивления являются определяющими в случаях использования волокон в качестве армирующих наполнителей при создании композиционных материалов (КМ), так как эти значения являются обратными величинами важной характеристики таких материалов – электропроводности. На рис. 10 представлена схема металлизации волокон ограниченной длины подачей жидких МОС под давлением вдоль металлизируемой поверхности. При этом необходимая концентрация паров МОС обеспечена по всей длине волокон, что увеличивает скорость металлизации при проведении процесса как в вакууме, так и в среде транспортирующих газов. Особенностью этого метода является то, что МОС попадает в реактор под давлением, превышающим давление в зоне металлизации. Скорость струи МОС превышает скорость свободного падения, что обеспечивает равномерное по всей длине распределение рабочего вещества. В рассматриваемом случае испарение и распад МОС происходят за счёт теплоизлучения от поверхности покрываемого изделия [37, 40].
Приведенные описания технологических установок и схемы металлизации относятся к числу потенциальных объектов, использование которых после модернизации позволит получать наноструктуры в промышленном масштабе и использовать достижения нанотехнологии в процессах изготовления, восстановления и упрочнения деталей в условиях предприятий ТС.
Термодинамика процессов получения наноструктур 2D-размерности
организованная материальная наносистема
Адекватный выбор подхода к описанию материальных систем (термодинамический, кинетический, макротермодинамический, синергетический), а также установление основных параметров модели (подходящих независимых переменных, управляющих параметров, параметров порядка) являются необходимыми этапами исследования наноструктур.
В процессе термодинамического анализа выявляются условия возникновения зародышей новой фазы, оценивается их критический размер и производится поиск механизмов управления ими.
Для получения наноразмерных объектов в процессе химического газофазного осаждения и прогнозирования их свойств и функциональных характеристик необходимо исследовать термодинамическую возможность протекания прямых и побочных реакций разложения исходных соединений. Также это позволяет решать вопросы совместимости реагентов с материалом подложки и определять оптимальные технологические режимы металлизации.
В общем виде полная колебательная потенциальная энергия наноматериалов складывается из суммы энергий
, (2.1)
где Uρ – энергия растяжения связи;
Uθ – энергия изменения угла между соседними связями;
Utor – энергия выхода связей из плоскости, сопровождающегося их кручением;
Uω – энергия изгиба плоскости за счет изменения π-электронной плотности;
Uvdw – энергия нековалентных взаимодействий.
Исходя из практической формулировки, термодинамика как феноменологическая теория процессов превращения теплоты в работу и познания роли энергии и других свойств вещества при этих процессах ограничивается рассмотрением равновесных состояний вещества. При этом переход из одного равновесного состояния в другое происходит бесконечно медленно, поэтому он не зависит от времени [41].
Известно, что принципиальная вероятность осуществления любой химической реакции определяется изменением ее энергии Гиббса ∆GºТ. Если ∆GºТ < 0, то реакция протекает самопроизвольно в заданном направлении, если ∆GºТ > 0, то она термодинамически невозможна. Абсолютная величина ∆GºТ (при ∆GºТ < 0) характеризует, насколько изучаемая система отдалена от состояния равновесия; реакции, протекающие с большей потерей ∆GºТ, идут со значительной глубиной превращения.
Значение ∆GºТ = ƒ(Т) для реакций в широком интервале температур можно вычислять различными способами, в том числе методом коэффициентов Ср, методом приведенных потенциалов ∆Ф*, а также приближенными методами.
В первом случае применимо уравнение
∆GºТ = ∆Н˚0 - аТlnТ – ½ вТ2 – 1/6 сТ3 + IT, (2.2)
где ∆Н˚0 – изменение энтальпии, рассчитанное по формуле
∆Н˚0 = ΣН˚0(конечных веществ) – ΣН˚0(начальных веществ);
а, в, с – коэффициенты уравнения теплоемкости реакции типа
Ср = а + вТ + сI2;
I – константа, определяемая подстановкой значения ∆G˚298 вместо ∆GºТ в уравнение типа
∆GºТ=-RTlnKp,
где Kp – константа равновесия.
В свою очередь,
∆G˚298 = ∆Н˚298 - 298,16 ∆S˚298.
При вычислении ∆GТ˚ по второму методу используют формулу
- ∆GºТ /Т = ∆Ф* - ∆Н˚0/Т , (2.3)
где ∆Ф* – изменение приведенного термодинамического потенциала реакции;
∆Ф* = Σ∆Ф* (конечных веществ) – Σ∆Ф* (начальных веществ).
В ряде случаев для расчета целесообразно применять метод Темкина–Шварцмана. При этом величины ∆GТ˚ вычисляют по уравнению
∆G˚Т /Т = ∆Н˚298 /Т - ∆S˚298 - (аМ0 + вМ1 + сМ2 + вМ-2), (2.4)
где ∆Н˚298 и ∆S˚298 – стандартные изменения энтальпии и энтропии при 298К;
а, в, с, d – коэффициенты уравнений типа
Ср = а + вТ2 и Ср = а + вТ + dТ-2;
М0, М1, М2, и М-2 – константы, зависящие от температуры Т, находят из таблиц [41…45].
Данные расчеты проводятся с рядом допущений. Это связано с тем, что термодинамическая теория описывает наиболее вероятное макроскопическое поведение больших систем (состоящих из 1023 частиц в объеме ~ 1 см2 или больше) при медленном изменении нескольких макроскопических свойств. Очень большие системы (подобные астрофизическим объектам), а также малые (нанообъекты) исключаются, так как структурные особенности наносистем отражают динамическое поведение, а не статическое равновесие макроскопических фаз. Предполагается, что фазы сосуществуют в пределах протяженных областей температур и давлений, поэтому четко определить точки фазовых переходов не представляется возможным.
Определение термодинамической возможности получения металлических нанопорошков и наноструктурированных покрытий можно представить на примере карбонильных соединений переходных металлов – гексакарбонила молибдена Mo(CO)6, пентакарбонила железа Fe(CO)5, тетракарбонила никеля Ni(CO)4.
Термическое разложение карбонилов металлов представляет собой сложный химический процесс, основной реакцией которого является уравнение
Побочные реакции являются причиной формирования в металлическом покрытии примесей оксидной и карбидной фаз.
Размещено на Allbest.ru
Дата добавления: 2023-02-21; просмотров: 20; Мы поможем в написании вашей работы! |
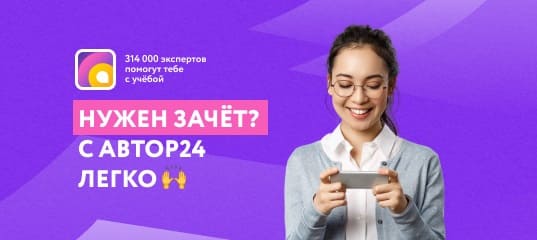
Мы поможем в написании ваших работ!