Сотовые заполнители на основе алюминия
Российская Федерация
Министерство образования и науки
ФГБОУ ВПО
«Орловский государственный университет»
факультет естественных наук
кафедра химии
Реферат
Композитные материалы. Получение и применение
Выполнил:
студент 5го курса 4й группы
Калинин М.Н.
Орел, 2012 г.
Содержание:
Введение………………………………………………………………………………………………………….3
1. Общая характеристика методов получения композитов с металлической матрицей…………………..3
1.1. Классификация методов получения и обработки композитов с металлической матрицей………..3
1.2. Технологические процессы получения и обработки металлических композиционных материалов………………………………………………………………………………………………4
1.3. Низкотемпературные методы изготовления композитов с металлической матрицей……………..5
2. Металлические волокнистые композиционные материалы (МВКМ)……………………………………7
2.1. Характеристика волокнистых КМ……………………………………………………………………..7
2.2. Области применения МВКМ…………………………………………………………………………..7
|
|
3. Псевдосплавы………………………………………………………………………………………………..8
3.1. Свойства и методы получения псевдосплавов………………………………………………………..8
3.2. Области применения псевдосплавов…………………………………………………………………..8
3.3. Методы получения псевдосплавов…………………………………………………………………….9
4. Эвтектические композиционные материалы………………………………………………………………9
4.1. Общая характеристика эвтектических КМ……………………………………………………………9
4.2. Методы получения эвтектических композиционных материалов…………………………………11
5. Дисперсно-упрочненные композиционные материалы (ДКМ)…………………………………………11
5.1. Общая характеристика ДКМ и механизм упрочения……………………………………………….11
5.2. Методы получения дисперсно-упрочненных композитов………………………………………….12
5.3. Области применения ДКМ……………………………………………………………………………12
6. Композиты на основе полимерной матрицы……………………………………………………………..13
6.1. Состав и основные свойства полимерных композитов……………………………………………..13
6.2. Методы получения полимерных композитов………………………………………………………..14
6.3. Метод изготовления слоистых и намотанных ПКМ………………………………………………..14
|
|
6.4. Золь-гель методы получения наногибридных полимер-неорганических композитов……………15
6.5. Области применения полимерных композитов……………………………………………………..16
6.6. Дендримеры - новый вид полимеров и композиты на их основе…………………………………..18
7. Жидкокристаллические композиты……………………………………………………………………….18
7.1. Основные свойства жидких кристаллов……………………………………………………………..18
7.2. Методы получения жидкокристаллических композитов…………………………………………...19
7.3. Области применения ЖКК……………………………………………………………………………20
8. Углерод - углеродные композиционные материалы……………………………………………………..21
8.1. Углеродные волокна (УВ). Принципы получения углеродных волокон………………………….21
8.2. Методы получения и области применения УУКМ………………………………………………….23
9. Применение композиционных материалов………………………………………………………………24
9.1. Основные требования, предъявляемые к конструкционным композиционным материалам……24
9.2. Основы структурного конструирования……………………………………………………………..25
9.3. Сандвичевые конструкции……………………………………………………………………………25
|
|
Заключение……………………………………………………………………………………………………..28
Литература……………………………………………………………………………………………………...29
Введение
За последние десятилетия композиты активно вошли в нашу жизнь и заменили традиционные материалы в энергетике, транспорте, электронике и других сферах деятельности.
Композиционные материалы (КМ) - это материалы из двух, трех и более разнородных фаз (веществ) в одном объеме. Они однородны в макромасштабе, но гетерогенны в микромасштабе. В настоящее время к числу композиционных материалов принять относить сравнительно небольшую группу материалов - полимеры, металлы, керамику и углерод, армированные волокнами, а так же наполненные полимеры, дисперсно-упроченные сплавы и псевдосплавы. Отличие большинства композиционных материалов от традиционных, состоит в том, что процесс их изготовления может быть совмещен с процессом изготовления изделия.
Быстро растущая востребованность композиционных материалов, требует подготовки специалистов в данной области. Предлагаемый цикл лекций предназначен для углубленной подготовки специалистов в области получения, применения композиционных материалов, создания конструкций из них. В курсе рассматриваются история и принципы создания композиционных материалов (КМ); виды и материалы дисперсных и волокнистых включений; материалы матрицы; сочетание различных включений и матрицы в одном КМ; технология изготовления КМ и их свойства; прогнозирование состава и технологии КМ с заданными свойствами; применение композиционных материалов.
|
|
1. Общая характеристика методов получения композитов с металлической матрицей
Металлические композиционные материалы изготавливают:
- -твердофазными методами;
- -жидкофазными методами;
- -методами осаждения - напыления;
- -возможны также комбинированные методы.
Для твердофазных методов характерно использование матрицы в твердом состоянии, преимущественно в виде порошка, фольги или компактного металла.
Жидкофазные методы предусматривают получение металлических композитов путем совмещения армирующих волокон с расплавленной матрицей. К ним относят методы пропитки волокон жидкими матричными сплавами и метод направленной кристаллизации.
При получении металлических композитов методами осаждения - напыления матричный металл наносят на волокна из растворов солей или других химических соединений, из парогазовой фазы, с помощью плазмы и т.д.
Комбинированные методы представляют собой последовательное или параллельное применение первых трех методов. Волокна в большинстве случаев вводят в металлический композит в твердофазном состоянии за исключением эвтектических композиционных материалов, в которых армирующая фаза (волокна и пластины) образуется из расплава в процессе направленной кристаллизации эвтектик.
Выбор метода получения композита с металлической матрицей зависит от вида исходных компонентов, возможности введения армирующей фазы без повреждения, обеспечения прочной связи между компонентами, равномерного распределения армирующих элементов в матрице. Учет этих факторов обеспечивает максимальную реализацию свойств арматуры и матрицы.
1.1. Классификация методов получения и обработки композитов с металлической матрицей
Методы получения и обработки композиционных материалов с металлической матрицей более детально можно подразделить на:
- химические (химического осаждения) и электрохимические (гальванические);
- газо- и парофазные (вакуумное осаждение паров, газотермическое нанесение покрытий: плазменные, газопламенные, электродуговые, высокочастотные) ;
- жидкофазные (направленная кристаллизация, протягивание жгутов и волокон через расплав, пропитка жгутов и каркасов волокон: вакуумная, компрессионная, при нормальном давлении, ваккумно- компрессионная);
- твердофазные (импульсные: сварка взрывом, магнитно- импульсное компактирование, гидроимпульсное компактирование, электроимпульсное компактирование; статические: диффузионная сварка, гидростатическое компактирование, спекание под давлением, изо- статическое компактирование, термокомпрессионное компактирование, прессование, статическая формовка; динамические: прокатка, волочение, динамическое горячее прессование, роликовая формовка, вальцовочная формовка, плазменное напыление и др).
Жидкофазные методы
Жидкофазные процессы пропитки и направленной кристаллизации получения композитов дают возможность использовать в качестве матриц недеформируемые литейные сплавы и получать изделия сложной конфигурации без дополнительного формоизменения. Недостатком является высокая реакционная способность большинства металлических расплавов в контакте с армирующими элементами.
По условиям пропитки жидкофазные методы можно разделить на несколько разновидностей:
- -свободная пропитка при нормальном давлении;
- -пропитка при повышенном давлении;
- -вакуумное всасывание;
- -комбинированная с использованием давления и вакуума, центробежных сил и др.
Условия пропитки определяются реакционной способностью расплавленной матрицы и смачиваемостью наполнителя матрицей. Чем ниже реакционная способность матрицы, тем больше вероятность сохранения формы, структуры и свойств армирующего наполнителя. Соблюдение требования хорошей смачиваемости волокон матрицей способствует обеспечению наибольшей площади контакта на границе волокно - матрица, а, следовательно, позволяет осуществлять наиболее прочную связь и эффективное перераспределение напряжений между компонентами. При несмачиваемости значительно увеличивается вероятность образования пустот и дефектных участков границы между волокном и матрицей, а технология получения качественного МВКМ существенно усложняется.
Металлические матрицы, как правило, плохо смачивают керамические волокна и усы. Увеличить способность металлов, например, никеля, смачивать керамику удается путем введения в расплав легирующих элементов Ti, Cr, Zr.
Химическое взаимодействие матричного расплава и армирующих волокон усложняет условия пропитки, как в случае смачивания, так и в случае несмачивания. При этом, из-за растворения волокна или воздействия загрязняющих примесей и атмосферы может измениться поверхностное натяжение жидкой фазы или границы раздела между твердой и жидкой фазами.
Методы осаждения - напыления
Это газофазные, химические и электрохимические процессы получения армированных металлических композитов. Главной технологической операцией процессов осаждения-напыления является нанесение на арматуру покрытий из матричного металла, который, заполняя пространство между армирующими элементами, образует матрицу композита.
Преимуществами осаждения-напыления являются: отсутствие разупрочнения армирующих элементов (волокон, частиц и др.), не подвергающихся действию высоких температур, или значительных механических напряжений при совмещении армирующих элементов и матрицы; предотвращение непосредственного контакта армирующих элементов друг с другом, возможность формирования полуфабрикатов и изделий сложной конфигурации.
Главным недостатком процессов осаждения-напыления является трудность использования в качестве матриц сложнолегированных сплавов.
В практике производства композитов на основе металлической матрицы наиболее широкое применение получило плазменное, при котором используют контролируемую дугу между двумя электродами, ионизирующую вдуваемый газ (аргон, гелий, азот, водород и их смеси). Напыляемый материал подается в плазменную горелку в виде проволоки или порошка.
1.2. Технологические процессы получения и обработки металлических композиционных материалов
При получении металлических композитов используются преимущественно следующие технологические процессы: обработка давлением, процессы порошковой металлургии, процессы пропитки и направленной кристаллизации, процессы осаждения - напыления.
Обработка давлением
В результате этого процесса можно получать металлические композиты с матрицей из деформируемых металлов и сплавов, как компактной (листы, слои, фольги, прутки, трубы, проволока), так и пористой (слои, полученные методом осаждения-напыления) формы. В качестве арматуры используют
как пластичные, так и хрупкие волокна. Главным преимуществом получения МВКМ обработкой давлением является отсутствие вредного взаимодействия между волокнами и матрицей при ограниченном времени их контакта, а главным недостатком -возможность повреждения волокон, особенно хрупких или малопластичных, вследствие высоких напряжений, возникающих при больших пластических деформациях. Режимы процесса уплотнения МВКМ, например, температура, давление, степень и направление деформации, количество проходов должны быть выбраны так, чтобы совместная пластическая деформация компонентов композита не приводила к разрушению арматуры, а на границе волокно - матрица возникала прочная связь.
При использовании волокон или проволоки со значительным запасом пластичности применимы практически все методы уплотнения:
- -прокатка,
- -импульсное прессование с помощью взрыва или ударной нагрузки,
- -гидроэкструзия и др.
В случае армирования металлов хрупкими или малопластичными волокнами чаще всего применяют процессы, при которых степень пластической деформации невысока, например, диффузионную сварку или прокатку с малыми единичными обжатиями.
Процессы порошковой металлургии
|
В этих процессах используется матрица в виде порошка. Армирующими элементами могут быть нитевидные кристаллы, непрерывные и дискретные волокна, сетки и ткани из волокон, дисперсные частицы и др. (рис. 1).
Рис. 1 Схема технологического процесса получения МВКМ методами порошковой металлургии
Преимуществами метода являются возможность использования в качестве матрицы труднодеформируемых металлов, сплавов, соединений, достижение высоких концентраций армирующей фазы, обеспечение в случае необходимости сочетания армирования с дисперсным упрочнением, использование оборудования, существенно не отличающегося от обычно применяемого в порошковой металлургии. Недостатки - неравномерность распределения коротких волокон по объему изделия из-за комкования в ходе перемешивания шихты с волокнами, возможность повреждения хрупких волокон при смешивании, уплотнении или деформации МВКМ, повышенное содержание оксидов и других примесей из-за развитой поверхности матричных порошков.
1.3.Низкотемпературные методы изготовления композитов с металлической матрицей
Способы изготовления композитов с металлической матрицей весьма разнообразны. Трудности связаны с высокими температурами, при которых происходит пропитка арматуры металлическим расплавом. При высоких температурах протекают химические реакции на поверхности армирующих элементов. Если химическая реакция затрагивает тонкий граничный слой, то это упрочняет связь армирующего элемента с матрицей, но если слой утолщается, то продукты реакции могут сильно ослабить связь и даже вызвать разрушение. Отсюда следует актуальная научная физико-химическая проблема изучения реакций на межфазных границах.
В настоящее время разрабатывается ряд низкотемпературных способов изготовления композитов с металлической матрицей. Все они прямо или косвенно основаны на диффузионном связывании. При прямом диффузионном связывании используют нанесение фольги или порошка металла на волокно и нагрев при температурах ниже температуры плавления металла.
В ряде случаев более эффективно диффузионное связывание происходит при высоких давлениях. Этот способ применяют, например, при изготовлении композитов из А1 или Mg - матриц с волокнами из бора или углерода. Однако и в этих случаях протекают поверхностные реакции, что указывает на необходимость изучения реакций на межфазных границах не только при температурах плавления металла, а в более широком интервале температур. Примером непрямого диффузионного связывания (хотя это определение и не точно) является способ лазерного воздействия на композит.
2. Металлические волокнистые композиционные материалы (МВКМ)
Армирование металлов высокопрочными и высокомодульными волокнами и дисперсными частицами позволяет улучшить комплекс их физико-механических характеристик: повысить предел прочности, предел текучести, модуль упругости, предел выносливости, расширить температурный интервал эксплуатации.
У волокнистых композитов матрица, чаще всего пластичная, армирована:
1. высокопрочными волокнами,
2. проволокой,
3. нитевидными кристаллами.
Идея создания волокнисто-армированных структур состоит не в том, чтобы исключить пластическое деформирование матричного материала, а в том, чтобы при его деформации обеспечивалось нагружение волокон и использовалось бы их высокая прочность.
Механические свойства высокопрочных материалов определяются наличием поверхностных дефектов (разрезов, трещин и т.д.). Около вершин этих дефектов при нагружении концентрируются внутренние напряжения, которые зависят от внешнего приложенного напряжения, глубины трещины и радиуса кривизны в вершине трещины. Для хрупких материалов коэффициент концентрации напряжений равен ККН = 10 -10 . В этом случае при действии уже относительно небольших средних напряжений у кончика трещины растягивающие напряжения достигают предельных значений и материал разрушается.
Существует критическая длина трещины, при которой проявляется тенденция к ее неограниченному росту, приводящая к разрушению материала. Важен тот факт, что соответствующее критическое напряжение зависит от абсолютного размера трещины. Из хрупких веществ материал с высокой воспроизводимой прочностью можно получать в основном в виде волокон. Это обусловлено тем, что волокна намного менее чувствительны к имеющимся в них дефектам, чем монолитные изделия. Из-за геометрии волокна трещины в них должны быть либо короткими, либо они должны быть преимущественно параллельны продольной оси волокон и, следовательно, относительно безопасные.
Изделие с высокой прочностью (например, канат) может быть в принципе получено путем объединения параллельных волокон, расположенных должным образом в пространстве. В канате волокна нагружаются в основном растягивающими напряжениями. При объединении волокон в изделие (путем соответствующих навивок) напряжения между отдельными волокнами создаются вследствие трения скольжения, возникающего при растяжении каната.
При изготовлении и в процессе эксплуатации канатов (ВКМ) волокна в них подвергаются изгибам, взаимному трению, что приводит к падению прочности волокон, а иногда к невозможности использования их. Например, высокопрочные волокна (стеклянные, углеродные, борные) очень чувствительны к поверхностным повреждениям и их нельзя применять в канатах, не использовав среду, которая защитила бы поверхность волокон и связала их воедино. Такой средой может быть полимерный материал или пластичный металл.
Когда используются не непрерывные волокна (как в канатах), а объединяются связующим короткие (прерывистые, дискретные) волокна, то и в этом случае сохраняется принцип волокнистого армирования. Он состоит в том, что при нагружении композита на границе раздела матрицы с волокном возникают касательные напряжения, которые приводят к полному нагружению волокон.
Особенность волокнистой композиционной структуры заключается в равномерном распределении высокопрочных, высокомодульных волокон в пластичной матрице (содержание их, т.е. объемная доля , может достигать 75% об.
2.1. Характеристика волокнистых КМ
Механические свойства ВКМ определяются тремя основными параметрами:
1. высокой прочностью армирующих волокон,
2. жесткостью матрицы,
3. прочностью связи на границе матрица-волокно.
Соотношение этих трех параметров характеризуют весь комплекс механических свойств материала и механизм его разрушения.
Работоспособность ВКМ обеспечивается как правильным выбором исходных компонентов, так и рациональной технологией производства, обеспечивающей прочную связь между компонентами при сохранении первоначальных свойств.
Армирующие волокна
Армирующие волокна, применяемые в конструкционных композитах, должны удовлетворять комплексу эксплуатационных и технологических требований. К первым относятся требования по прочности, жесткости, плотности, стабильности свойств в определенном температурном интервале, химической стойкости и т. д.
Теоретическая прочность материалов ам возрастает с увеличением модуля упругости Е и поверхностной энергии у вещества и падает с увеличением расстояния а0 между соседними атомными плоскостями а0. Следовательно, высокопрочные твердые тела должны иметь высокие модуль упругости и поверхностную энергию и возможно большее число атомов в единице объема. Этим требованиям удовлетворяют Ве, В, С, N2, O2, Al и Si (7 элементов, самых легких, самих верхних в периодической системе). Наиболее прочные материалы всегда содержат один из этих элементов, а зачастую состоят только из указанных элементов.
При создании ВКМ применяются высокопрочные стеклянные, углеродные, борные и органические волокна, металлические проволоки, а также волокна и нитевидные кристаллы ряда карбидов, оксидов, нитридов и других соединений (SiC, SiO2, Al2OC, Si3N4, ....).
Технологичность волокон определяет возможность создания высокопроизводительного процесса изготовления изделий на их основе. Важным требованием является также совместимость волокон с материалом матрицы, т.е. возможность достижения прочной связи волокно-матрица при условиях, обеспечивающих сохранение исходных значений механических свойств компонентов.
Примеры ВКМ Mg-B(вoлoкнa), Mg-С^олокна), Mg-стальные волокна, Ti - Мо(волокна), Ti -В; Ti -SiC; Ti - Be, Ni -A12O3 и др.
2.2. Области применения МВКМ
Композиционные волокнистые материалы с металлической матрицей применяют при низких, высоких и сверхвысоких температурах, в агрессивных средах, при статических, циклических, ударных, вибрационных и других нагрузках. Наиболее эффективно используются МВКМ в конструкциях, особые условия, работы которых не допускают применения традиционных металлических материалов. Однако чаще всего в настоящее время армированием металлов волокнами стремятся улучшить свойства матричного металла, чтобы повысить рабочие параметры тех конструкций, в которых до этого использовали неармированные материалы. Использование МВКМ на основе алюминия в конструкциях летательных аппаратов, благодаря их высокой удельной прочности, позволяет достичь важного эффекта - снижения массы. Замена традиционных материалов на МВКМ в основных деталях и узлах самолетов, вертолетов и космических аппаратов уменьшает массу изделия на 20 - 60%.
Наиболее актуальна в газотурбостроении задача повышения термодинамического цикла энергетических установок. Даже малое повышение температуры перед турбиной значительно увеличивает КПД газотурбинного двигателя. Обеспечить работу газовой турбины без охлаждения или, по крайней мере, с охлаждением, не требующим большие конструктивных усложнений газотурбинного двигателя, можно используя высокожаропрочные МВКМ на основе никеля и хрома, армированные волокнами А12О3.
Алюминиевый сплав, армированный стекловолокном, содержащим оксид урана, обладает повышенной прочностью при температуре 823К и может быть использован в качестве топливных пластин ядерных реакторов в энергетике.
Металлические волокнистые композиты используют в качестве уплотнительных материалов. Например, статические уплотнения, изготовленные из Мо или стальных волокон, пропитанных медью или серебром, выдерживают давление 3200 МПа при температуре 923К.
Как износостойкий материал в коробках передач, дисковых муфтах, пусковых устройствах можно использовать МВКМ, армированные "усами" и волокнами. Области применения МВКМ определяются не только механическими, но и физическими свойствами - электрическими, магнитными, ядерными, акустическими и др. В армированных W-проволокой магнитотвердых материалах удается сочетать магнитные свойства с высоким сопротивлением ударным нагрузкам и вибрациям. Введение арматуры из W, Мо в медную и серебряную матрицу позволяет получать износостойкие электрические контакты, предназначенные для сверхмощных высоковольтных выключателей, в которых сочетаются высокие тепло- и электропроводность с повышенным сопротивлением износу и эрозии.
Принцип армирования можно положить в основу создания сверхпроводников, когда в матрицах из Al, Cu, T1, N1 создают каркас из волокон сплавов, обладающих сверхпроводимостью, например, Nb - Sn, Nb - Zr. Такой сверхпроводящий композит может передавать ток плотностью 105 - 107 А/см2.
3. Псевдосплавы
3.1. Свойства и методы получения псевдосплавов
Псевдосплавы - композиционные материалы, состоящие из двух или более металлоподобных фаз, не взаимодействующих или слабо взаимодействующих между собой. Псевдосплавы могут иметь матричную или каркасную структуру. Псевдосплавы с матричной структурой обычно отличаются от дисперсно-упрочненных композитов большим размером упрочняющих включений (>10мкм) и большей их концентрацией.
Примеры псевдосплавов: Fe-Pb, Fe-Mg, W-Cu, W-Ag, Mo-Cu, Mo-Ag и др.
Псевдосплавы, сочетающие в себе структурные составляющие с резко отличными физико-механическими характеристиками, обладают важными техническими свойствами - высокими стойкостью при воздействии интенсивных тепловых потоков и демпфирующей способностью при вибрационном нагружении, самосмазкой в условиях сухого трения, электроэрозионной стойкостью и износостойкостью при работе в качестве электроконтактов. Рассмотрим более подробно основные свойства, технологические методы получения и области применения ряда конкретных псевдосплавов..
3.2. Области применения псевдосплавов
Псевдосплавы Fe-Cu (15-25%Cu) применяются в качестве конструкционных материалов для изготовления крупных деталей машин, подверженных ударным нагрузкам. На детали можно наносить гальванические покрытия. Из псевдосплавов Fe-Cu изготовляют компрессорные лопатки, детали буровых снарядов, резцов и корпусов фрез. Из псевдосплавов Fe-Cu (70%Fe-30%Cu) делают электрические контакты, которые отличаются хорошей пластичностью и термостойкостью.
Применение псевдосплавов Fe-Pb связано, в основном, с их хорошими антифрикционными свойствами. Из них изготавливают подшипники скольжения. Из псевдосплавов Fe-Pb производят седла клапанов двигателей внутреннего сгорания, а также контактные пластины токоприемников электротранспорта, поскольку они сочетают хорошие антифрикционные свойства с высокой электропроводностью и дугостойкостью.
Псевдосплавы Fe-Mg предназначены для изготовления анодов электрохимической защиты конструкционных материалов.
Из псевдосплавов W-Cu, W-Ag изготовляют контакты для сильноточной и высоковольтной коммутационной аппаратуры. Вольфрам придает псевдосплавам твердость, прочность, сопротивляемость истиранию и эрозии, медь и серебро - электро- и теплопроводность, пластичность. Высокопористые псевдосплавы предназначены для изготовления сопел плазмотронов. Повышенная стойкость пористых псевдосплавов против высокотемпературного окислительного износа связана с образованием на рабочих поверхностях пленки оксида меди, защищающей вольфрам. Для изготовления электрод - инструментов применяют псевдосплав W-Cu, в который введены добавки сложных оксидов La3BO6, LаВО3 и др. Присутствие комплексного оксида стабилизирует электрический разряд, позволяет увеличить скорость обработки и уменьшить износ электродов. Псевдосплавы W -Сr как и тяжелые сплавы можно использовать для защиты от действия рентгеновского и g-излучения .
Из псевдосплавов Mo-Cu, Mo-Ag, Ni-Ag изготовляют электроконтакты.
Известны псевдосплавы триботехнического назначения на основе меди и бронзы, пропитанные свинцом, оловом, галлией, индием и их сплавами. Лучшие антифрикционные свойства имеют псевдосплавы бронза-олово и бронза- сплав Sn -Pb.
Псевдосплавы T1-Mg используют для изготовления подшипников в узлах трения, работающих в вакууме и агрессивных средах.
3.3 Методы получения псевдосплавов
Изготовляют псевдосплавы методами порошковой металлургии - пропиткой или спеканием в присутствии жидкой фазы. Пропитка заключается в заполнении пор спеченной или неспеченной формовки из тугоплавкого металла расплавом более легкоплавкого материала. Самопроизвольное протекание процесса пропитки сопровождается уменьшением свободной энергии системы и осуществляется при условии cosj >0, где j - краевой угол смачивания. Пропитку производят методами полного или частичного погружения пористого каркаса в расплав либо путем наложения пропитывающего материала на пористый каркас. Температура пропитки превышает точку плавления легкоплавкой фазы, но не достигает точки плавления тугоплавкой. Скорость пропитки растет при увеличении исходной пористости каркаса, размера пор и температуры процесса. Атмосфера, в которой ведется пропитка, должна быть совместимой с обеими составляющими псевдосплава и обеспечивать максимальную степень пропитки. Если 0 « 90, то движущая сила процесса пропитки (капиллярное давление) может оказаться недостаточной для ее осуществления. В этом случае необходимо применение дополнительных воздействий (автоклавного давления, вакуумного всасывания, электромагнитного поля и др.). Пористые каркасы под пропитку получают путем уплотнения порошков. Легкоплавкая составляющая для пропитки используется в виде литого материала, прессованной стружки или порошка.
Спекание в присутствии жидкой фазы заключается в спекании прессовок порошковой смеси компонентов псевдосплава при температурах, превышающих температуру плавления легкоплавкой составляющей. Процесс спекания в жидкой фазе, за счет большей скорости переноса вещества, протекает значительно интенсивнее, чем в твердой. Псевдосплавы, полученные методом жидкофазного спекания, имеют матричную структуру - в легкоплавкой матрице диспергированы частицы тугоплавкой фазы.
4. Эвтектические композиционные материалы
4.1. Общая характеристика эвтектических КМ
Эвтектические композиционные материалы (ЭКМ) - сплавы эвтектического или близкого к нему состава, в которых армирующей фазой служат ориентированные волокнистые или пластинчатые кристаллы, образованные в процессе направленной кристаллизации. Поскольку структура в эвтектическом композиционном материале создается естественным путем, а не в результате искусственного введения армирующей фазы в матрицу, эвтектический композит, в отличие от других композиционных материалов, называется естественным.
Эвтектический композит (ЭКМ) - естественный материал, поскольку его структура формируется при направленной кристаллизации естественным путем, а не в результате искусственного введения арматуры в матрицу. Форма выделяющейся фазы - волокнистая или пластинчатая - зависит от объемной доли упрочнителя. При объемной доле упрочнителя (меньше 32%) для ЭКМ характерна волокнистая структура, а при большей концентрации - пластинчатая. Поскольку прочность волокон выше прочности пластин, то волокнистое строение предпочтительней пластинчатого.
Прочность ЭКМ существенно зависит от структуры материала, в значительной степени определяемой скоростью кристаллизации. Например, ударная вязкость ЭКМ Al - Al3Ni при малых скоростях кристаллизации (g<0,6см/ч), когда образуется пластинчатая микроструктура, имеет более низкие значения, чем у волокнистого материала. Однако даже в этом случае, ударная вязкость составляет 1,1-3,7 10 Дж/м . что значительно выше ударной вязкости литейных алюминиевых сплавов. Пластинчатая эвтектика Al-СuАl2 при испытаниях на ударную вязкость обнаруживает большую хрупкость, что является существенным недостатком этого материала. Эвтектические композиты на основе А1 хорошо свариваются методом диффузионной сварки и ввиду хорошей высокотемпературной стабильности структуры, сварку можно проводить при температурах до 798К.
Если при охлаждении расплава эвтектического состава удается создать плоский фронт кристаллизации, то возникает упорядоченная ориентированная микроструктура. Это один из путей формирования нитевидных кристаллов (типа усов) непосредственно в матрице. Такие композиты получены, в частности, из меди и хрома, алюминия и никеля, меди и вольфрама. В последнем случае была достигнута прочность 175кг/мм. Металлографические исследования показали, что процесс разрушения в таких композитах начинается с разрушения усов. Это говорит о высокой прочности связи на поверхности раздела нитевидный кристалл - матрица.
Для эвтектического сплава N1-NbC (11% об.) средняя прочность волокон - 586 кгс/мм . Эти же волокна, выделенные путем растворения матрицы, имели прочность 1030 кгс/мм2, что свидетельствует о высоком совершенстве нитевидных кристаллов, формирующихся в процессе направленной кристаллизации эвтектики (рис. 2).
Жаропрочные ЭКМ можно разделить на две группы: хрупкие; пластичные.
Хрупкими, например, являются никелевые пластинчатые ЭКМ с объемной долей упрочнителя 33-35%. Свойства хрупких ЭКМ, рассчитанные по закону аддитивности, удовлетворительно совпадают с результатами испытаний. К пластичным ЭКМ относятся волокнистые композиты с невысокой долей упрочнителя (от 3 до 15%), например, сплавы Ni, Co, упрочненные монокарбидами Та, Nb, Hf. Высокие механические свойства волокнистых ЭКМ на основе Ni и Со, упрочненных карбидной фазой являются результатом создания композитной структуры, пластичная матрица которой армирована высокопрочными нитевидными кристаллами.
Рис. 35 - Торец направленно- кристаллизованного эвтектического сплава Ta-(Co-Ni-Cr), протравленный после кристаллизации. Нитевидные волокна - TaC
Направленные эвтектики, состоящие из фаз с резко отличным электронным строением, обладают специальными физическими свойствами: магнитными, термоэлектрическими, оптическими и др. Наиболее изучены ЭКМ на основе полупроводниковой матрицы - антимонида индия InSb с волокнами проводников FeSb, NiSb, MnSb, CrSb. Матрица в таких композитах обладает электропроводностью 2,2*102 (Ом*см)-1 и существенно отличается от электропроводности волокон (для волокон NiSb - 7*104 (Ом- см)-1. Электросопротивление ЭКМ InSb-NiSb при взаимно перпендикулярной ориентации волокон, электрического тока и магнитного поля на порядок выше, чем для случая расположения волокон параллельно направлениям тока или магнитного поля.
ЭКМ, в которых одна или обе фазы ферромагнитны, обладают высокими магнитными свойствами. В качестве магнитных материалов используют ЭКМ, у которых коэрцитивная сила существенно увеличивается за счет создания ориентированной структуры с ферромагнитными волокнами, имеющими поперечный размер близкий к размеру доменов (~1мкм). ЭКМ с ферромагнитными матрицей и волокнами, такие как Sm2Co17 -Co, У2Со17 -Со, FeSb-Fe, CoSb-Sb характеризуются большой коэрцитивной силой и остаточной индукцией, зависящей от содержания ферромагнитной фазы и др.
Магнитомягкие ЭКМ системы Fe-NbC, Co-NbC, (Fe-Co)-NbC состоят из магнитомягкой матрицы и неферромагнитного упрочнителя. Эти ЭКМ из- за высокой термической стабильности могут работать в условиях высоких температур и напряжений.
Направленно закристаллизованные эвтектические сплавы имеют анизотропные электронные, магнитные и другие свойства, что определяет их применение в электронике. Так, эвтектическую композицию А1-А13Ni можно использовать как материал для прочных проводников. Взаимосвязь угла между направлением токопроводящих волокон в полупроводниковых эвтектических композитах InSb-Sb, GaSb-Sb, InAs-As с магнитным сопротивлением материалов позволяет использовать эти композиты в бесщеточных коммутаторах, бесконтактных переменных сопротивлениях.
Таким образом, к преимуществам эвтектических композитов следует отнести простоту их изготовления (нет необходимости отдельного изготовления "усов", исчезают трудности, связанные с их использованием), высокую прочность связи на поверхности раздела и отсутствие окисных слоев (что обеспечивает высокую термическую устойчивость - возможность длительной работы при повышенных температурах). Но для таких КМ характерно постоянство объемной доли эвтектической фазы, что делает невозможным воздействие на их свойства путем изменения состава, также для реализации плоского фронта кристаллизации необходимо использовать высокочистые вещества, так как примеси этому препятствуют.
4.2. Методы получения эвтектических композиционных материалов
Методы, применяемые для направленной кристаллизации эвтектических расплавов, аналогичны методам получения монокристаллов полупроводниковых материалов: Чохральского, направленная кристаллизация, зонная плавка (рис. 3).
Рис. 3. Схемы методов кристаллизации
Вытянутые фазы эвтектики кристаллизуются перпендикулярно к поверхности раздела (фронта кристаллизации) и следуют за ним по мере перемещения, образуя ориентированные стерженьковые или пластинчатые структуры. При большой скорости кристаллизации образуются дисперсно-упрочненные многофазные сплавы.
Эвтектические композиционные материалы (ЭКМ) получают в процессе направленной кристаллизации сплавов, поэтому они называются естественными композитами. По микроструктуре ЭКМ похожи на матричные композиты, армированные дискретными волокнами в виде усов или тонких пластин. Для реализации такой строго ориентированной микроструктуры, которая дает наименьшую площадь поверхности раздела фаз или наименьшие значения удельной энергии межфазных границ, необходимо обеспечить плоскую поверхность между расплавом и кристаллизующимся твердым телом.
Вытянутые фазы эвтектики кристаллизуются перпендикулярно к поверхности раздела (фронта кристаллизации) и следуют за ним по мере перемещения, образуя ориентированные стерженьковые или пластинчатые структуры. При большой скорости кристаллизации образуются дисперсно-упрочненные многофазные сплавы.
Эвтектические композиционные материалы получают также методом Бриджмена. Эвтектический сплав, помещенный в тигель, сначала нагревают до расплавления с помощью индуктора, затем вытягивают с постоянной скоростью из зоны нагрева. Расплав последовательно затвердевает и фронт кристаллизации перемещается вверх. Скорость кристаллизации зависит от скорости вытягивания и условий теплообмена в системе. Скорость перемещения тигля с расплавом регулируется в широких пределах от 5 до 2000мм/ч. Метод зонной плавки при получении ЭКМ заключается в локальном расплавлении и перемещении узкой зоны из сплава эвтектического состава по длине прутка-заготовки. При зонной плавке применяют электронно-лучевой и локальный индукционный нагрев. Равномерность прогрева расплавленной зоны и ее перемешивание для выравнивания состава по объему достигается вращением одной части образца, отделенной зоной расплавленного металла от другой.
5. Дисперсно-упрочненные композиционные материалы (ДКМ)
5.1. Общая характеристика ДКМ и механизм упрочения
ДКМ представляют собой матрицу из чистого металла или сплава, в котором равномерно распределены на заданном расстоянии одна от другой частицы упрочняющей фазы размером <0,1 мкм. Объемная доля включений составляет 0,1 - 15%. В качестве упрочняющей фазы применяют дисперсные частицы оксидов, карбидов, нитридов, боридов, и других тугоплавких соединений.
Известно, что вязкий, лишенный хрупкости материал перед разрушением претерпевает значительную деформацию. Причем пластические деформации (сдвиг) в реальных кристаллических материалах начинается при напряжениях, которые меньше, чем теоретически рассчитанные, примерно в 1000 раз.
Определение деформации. Деформацией называется изменение размеров или формы тела под действием внешних сил либо физико-химических процессов, протекающих в самом теле. Такая низкая прочность по сравнению с теоретической объясняется двумя возможными факторами:
1. в пластической деформации (сдвиг) активно участвует в дислокации;
2. сказывается масштабный фактор соотношения длины межатомных связей и размеров образца.
Чаще придерживаются 1-ой теории. При деформации благодаря дислокациям сдвиг атомов в соседнее положение происходит не одновременно по всей поверхности скольжения, а скачками во времени. Такое постепенное скольжение за счет небольших смещений атомов в области дислокаций не требует значительных напряжений, что и проявляется при испытаниях пластичных материалов.
Дислокации играют принципиальную роль в структуре и свойствах (прежде всего в прочности) ДКМ. Поэтому напомним, что такое дислокации и как происходит пластическая деформация твердых тел при скольжении краевой дислокации (особый вид линейных несовершенств кристаллической решетки, нарушающих правильное чередование атомных плоскостей).
5.2. Методы получения дисперсно-упрочненных композитов
Дисперсно-упрочненные композиционные материалы относятся к классу порошковых. Поэтому процесс получения полуфабрикатов ДКМ включает операции: приготовление порошковой смеси, формование, спекание, деформационная и термическая обработка.
Для приготовления порошковых смесей матричного материала и упрочняющих включений применяют механическое и химическое смешивание (разложение смеси солей, поверхностное окисление, внутреннее окисление, водородное восстановление, химическое осаждение из растворов и др.).
Далее порошковые смеси матричного материала и упрочняющих включений, полученные одним из указанных выше методов, формуют путем прессования в прессформах или прокаткой.
Смешивание порошков может сочетаться с их измельчением, что может вызвать дополнительное окисление. Поэтому смешивание с измельчением металлов, имеющих большое сродство к кислороду (Nb, Та, Ti, Cr, Zr), нужно проводить в защитной атмосфере или с применением активных добавок, образующих с оксидами легко восстанавливаемые соединения. Оксидные пленки на металлах с низким сродством к кислороду (W, Fe, Со, Си, Mo, Ni) удаляются при последовательной термообработке в восстановительной атмосфере.
Сформованные из порошковых смесей брикеты подвергают спеканию. Поскольку при следующей операции - пластической деформации - происходит уплотнение до монолитного состояния, главной целью спекания прессовок является не повышение плотности, а дегазация и довосстановление оксидных пленок на матричном металле, что способствует повышению физико-механических свойств полученных композиций. При спекании методами горячего прессования процессы прессования и спекания совмещаются. С целью уплотнения до беспористого состояния и формирования дислокационной структуры матрицы, обеспечивающей высокую термическую стабильность, заготовки ДКМ после спекания подвергают пластической деформации. Наиболее благоприятный метод деформирования ДКМ - горячая экструзия с высокими степенями обжатия.
Для изготовления лент и листовых полуфабрикатов из ДКМ применяют горячую прокатку. Деформированные заготовки ДКМ подвергают термообработке для повышения стабильности структуры, пластичности и жаропрочности.
5.3 Области применения ДКМ
ДКМ на основе алюминия применяют в изделиях длительно работающих при температурах 573 - 773К. Из САПов изготовляют противопожарные экраны самолетов, теплообменники для авиастроения и химической промышленности, крепеж. Высокая коррозионная стойкость и способность поглощать нейтроны позволили использовать САП для изготовления опорных элементов трубопроводов атомных реакторов. ДКМ Al-С используются для изготовления поршней двигателей внутреннего сгорания.
Никелевые ДКМ применяют для изготовления деталей двигателей, подверженных воздействию температур до 1573К и невысоких напряжений. Такие условия работы характерны для деталей сопла, камер сгорания и форсажных камер авиационных двигателей.
Дисперсно-упрочненный нихром используют в производстве горячих газопроводов, теплозащитных панелей, высокотемпературных крепежных деталей. Дисперсно-упрочненные композиты на основе хрома перспективны для изготовления рабочих и сопловых лопаток газотурбинных двигателей, нагревателей для электропечей. Прочность печных нагревателей из хромовых ДКМ значительно превышает прочность си-литовых нагревателей.
Молибденовые ДКМ, обладающие такими характеристиками, как высокая температура плавления, высокие прочность, твердость и жесткость при повышенных температурах, хорошие тепловые и электрические свойства, сопротивление термическим ударам, коррозионная стойкость в различных агрессивных средах наряду с достаточной технологичностью, обеспечивает перспективы для применения в различных областях техники. Для изготовления деталей, работающих в окислительной среде, используют молибденовые ДКМ с покрытиями.
Вольфрамовые ДКМ, упрочненные оксидами, широко применяют в светотехнике, электротехнике и электронике. Из них производят спирали для мощных ламп накаливания. Торированный вольфрам используют для изготовления электродов газоразрядных ламп. Благодаря высоким эмиссионным свойствам ДКМ используют в электронике в качестве эмиттера электронов.
Из ДКМ на основе серебра производят электрические контакты для низковольтной аппаратуры, обладающие высокими электро- и теплопроводностью, электроэрозионной и коррозионной стойкостью, малой склонностью к свариванию и низким контактным сопротивлением.
Упрочненные оксидами фехрали (сплавы Fe -Cr -А1) используют в качестве нагревателей в электротехнической промышленности.
Медь эффективно упрочняется тугоплавкими оксидами ^hO2, ВеО, А12О3). Сочетание высокой жаропрочности и электропроводности открывает возможности для изготовления из медных ДКМ электрокон тактов, обмоток роторов электродвигателей, трубчатых теплообменников.
ДКМ на основе титана с оксидами и карбидами служат для изготовления компрессорных дисков и других изделий, эксплуатируемы; при 873-973К.
ДКМ на основе свинца с оксидами применяют в электротехнике (пластины кислотных аккумуляторов, ванны электрохимического хромирования).
ДКМ на основе платины используют для изготовления термометров сопротивления, высокотемпературных термопар, нагревательных элементов, сосудов для получения стекловолокон и др. При использовании ДКМ увеличивается долговечность изделий, что позволяет получить существенный экономический и технический эффект.
6. Композиты на основе полимерной матрицы
Материалы, которые использовал человек в своей деятельности, всегда играли важную роль в прогрессе цивилизации. Они даже дали названия целым этапам развития человечества: каменный век, бронзовый век, железный век... Сейчас круг материалов, созданных и используемых в быту и технике, особенно военной, чрезвычайно широк, однако современную эпоху нельзя представить без полимеров.
6.1. Состав и основные свойства полимерных композитов
Полимерные композиционные материалы (ПКМ) или армированные пластики состоят из высокопрочных волокон (частиц, слоев) различной природы (стеклянных, углеродных, металлических, полимерных и др.) и полимерного связующего - матрицы, склеивающей волокна в монолитный материал. Настоящий бум в современном материаловедении возник в конце первой половины XX в., когда появились прочные и легкие стеклопластики и из них начали делать планеры, а затем и многое другое.
Многообразие армирующих волокон и полимерных связующих, а также схем армирования позволяет направленно регулировать прочность, жесткость, уровень рабочих температур и другие свойства ПКМ. Эффективными средствами регулирования являются сочетание в одном материале волокон с различными упруго-прочностными свойствами (например, борных и стеклянных, углеродных и органических), введение нитевидных кристаллов и дискретных волокон в полимерную матрицу. Это определяет одно из важнейших достоинств ПКМ - возможность создавать элементы конструкций с заранее заданными свойствами, наиболее полно отвечающими характеру и условиям их работы.
Компоненты армированного пластика - это наполнитель (волокна, частицы) и полимерная матрица. Для создания стабильных и устойчивых в работе ПКМ важно состояние границы раздела.
Армирующие волокна для ПКМ
Армирующие волокна несут основную механическую нагрузку и именно они определяют прочность и жесткость (модуль упругости) материала.
Стеклянные волокна вытягивают из расплавленной, специально приготовленной смеси оксида кремния с оксидами разных металлов. Основные затраты - затраты энергии на расплавление и гомогенизацию смеси. Стеклопластики - наиболее дешевые композиты, однако их главные недостатки - сравнительно большая плотность и низкий модуль упругости.
Для преодоления этих недостатков применяют углеродные волокна. В качестве сырья для получения углеродных волокон используют полимерные полиакрилонитрильные или вискозные волокна. Специальная многостадийная термическая обработка полимерных волокон при высоких температурах (2000°С и выше) приводит к карбонизации и графитизации волокон, в результате чего конечное волокно состоит только из углерода и имеет различную структуру и свойства в зависимости от режима термообработки и структуры исходного сырья. Углеродные волокна непрерывно совершенствуются, повышаются их прочность и жесткость, увеличивается ассортимент. Один из перспективных путей снижения их цены - использование нефтяных и других пеков (тяжелых полиароматических соединений) в качестве исходного сырья. Кроме того, волокна из пеков обладают повышенным модулем упругости. Углеродные волокна и композиты на их основе имеют глубокий черный цвет и хорошо проводят электричество, что определяет и ограничивает области их применения.
6.2. Методы получения полимерных композитов
Отличительная особенность изготовления изделий из ПКМ состоит в том, что материал и изделие в большинстве случаев создаются одновременно. При этом изделию сразу придают заданные геометрические размеры и форму, что позволяет существенно снизить его стоимость и сделать конкурентноспособным с изделиями из традиционных изотропных материалов.
6.3. Метод изготовления слоистых и намотанных ПКМ
Выбор материала матрицы и геометрической структуры композита диктует и выбор способа его изготовления. На рис. 4 показан обычный способ изготовления слоистых и намотанных композитов с полимерной матрицей.
Рис. 4. Изготовление слоистых намотанных композитов с полимерной матрицей: а - общая схема изготовления ПКМ; б - схема изготовления многослойного листового ПКМ; в - схема изготовления многослойного намотанного ПКМ
Волокна сматывают с бобин, подвергают поверхностной обработке, улучшающей адгезию, протягивают через ванну с полимерной смолой. В результате смола скрепляет волокна в плоский жгут - ленту. Готовые ленты собирают в слоистый листовой материал (аналог фанеры) или наматывают на форму. Собранный в листы материал отверждают термообработкой. Слои можно накладывать поочередно с разным направлением волокон и формировать в композите клетчатую структуру арматуры, что придает материалу жесткость. Недостатком такого композита является отсутствие поперечного армирования в каждом отдельном слое и между слоями, поэтому материал может расслаиваться. К тому же появившаяся трещина в объемном образце из такого композита легко находит путь распространения между слоями. Для устранения этого недостатка изготавливают тканые композиционные материалы.
Как отмечалось, подготовка волокнистого наполнителя предусматривает операции, заключающиеся в обработке поверхности волокон для улучшения их смачивания связующим и увеличения прочности сцепления между наполнителем и связующим в готовом ПКМ. Это могут быть следующие операции: аппретирование, активирование и химическая очистка поверхности, удаление влаги и др.
В производстве ПКМ используются твердые и жидкие связующие. Приготовление связующего включает измельчение, отсев нужной фракции, сушку, добавление необходимых ингредиентов (отвердителей, пластификаторов, катализаторов), гомогенизацию смеси или приготовление раствора, эмульсии, а для термопластов - переработку в листовой или пленочный материал.
Совмещение волокнистого наполнителя со связующим производится различными способами: нанесением раствора или расплава связующего на поверхность волокнистого наполнителя при прохождении его через жидкое связующее или с помощью вращающегося ролика, погруженного в связующее; напылением жидкого связующего: пропиткой под вакуумом или давлением армирующего наполнителя, имеющего форму изделия и заключенного в герметичную полость; напылением на поверхность ленты или ткани порошка связующего с последующей пропиткой расплавом полимера при прокатке между горячими роликами и др. Для улучшения проникновения связующего в межволоконное пространство применяют принудительную пропитку, например, с помощью отжимных роликов или ультразвука.
После совмещения волокнистого наполнителя с полимерным связующим полученный материал (препрег) подвергают тепловой обработке для удаления растворителей, летучих продуктов и придания препрегу липкости, необходимой для последующих технологических операций.
Таким образом, технология изделий из ПКМ включает комплекс операций, обеспечивающий получение изделий с заданными свойствами: прессование; литье под давлением (инжекция, центробежное литье); автоклавный метод литья под давлением; экструзия (выдавливание, шприцевание, шнекование); контактное формование; намотка; пневматическое формование; спекание; штампование; напыление и др.
Например, прессование применяют для получения листовых материалов и толстостенных изделий сложной формы, переменного сечения, а также заготовок простой формы, подвергающихся дальнейшей механической обработке и др. Метод обеспечивает получение изделий с высоким качеством поверхностей и высокой плотностью материала. Основной недостаток - локальная неоднородность содержания компонентов.
Для получения требуемой ориентации волокнистого наполнителя в деталях, имеющих форму тел вращения, широко применяют метод намотки, выполняемой из волокон, предварительно пропитанных связующим (препреги) и непропитанных. В последнем случае (метод мокрой намотки) пропитка связующим производится в процессе намотки. Метод намотки позволяет получать изделия с равномерным распределением наполнителя по объему. Содержание волокнистого наполнителя в ПКМ, получаемых намоткой, достигает 60-85%, что обеспечивает высокую прочность материала.
Многие изделия из волокнистых ПКМ могут быть изготовлены несколькими методами. Выбор метода изготовления и параметров технологического режима определяется природой полимерного связующего и армирующих волокон, текстильной формой армировки, геометрией изделия, условиями его эксплуатации и вытекающими из них техническими требованиями к материалу.
Для выпуска небольших партий изделий можно использовать малопроизводительные методы формования с применением дешевой оснастки, тогда как крупносерийное производство экономически оправдывает значительные расходы на изготовление оснастки с использованием наиболее производительных методов.
6.4. Золь-гель методы получения наногибридных полимер-неорганических композитов
Для получения гибридных дисперсных полимер-неорганических композитов интенсивно развиваются золь-гель-методы и интеркаляция полимеров и частиц в слоистые и сетчатые системы. Как отмечалось, полимерные молекулы - длинные молекулярные цепочки. Повторяющиеся единицы цепи - молекулярные звенья имеют две свободные валентности и поэтому объединяются в линейные цепи. Если, однако, при синтезе в цепь могут встраиваться звенья с валентностью три и выше, то в результате образуется трехмерный пространственный каркас из цепочек, соединенных друг с другом ковалентными связями, - полимерная сетка. Такие сетки, будучи помещены в хороший растворитель и набухают в нем. Полимерная сетка, адсорбировавшая в себя значительное количество растворителя, называется полимерным гелем.
Вообще методов проведения золь-гель реакции несколько. Дж.Марк, например, предложил осуществлять гидролиз и конденсацию в набухшей полимерной матрице. В ходе такой реакции образуются взаимопроникающие органическая и керамическая сетки, что обеспечивает уникальные механические свойства конечного материала.
Существует также метод синтеза, в котором полимеризация и образование неорганического стекла протекают одновременно. За счет этого расширяется класс используемых мономеров, кроме того, при сушке конечного продукта не происходит заметной усадки, как в способе Марка.
Суть золь-гель-метода заключается в том, что на первой стадии процесса формируется химический состав продукта в виде высокодисперсного коллоидного жидкого раствора - золя (размер частиц дисперсной фазы 10^ -10"' м). Увеличение концентрации дисперсной фазы приводит к появлению коагуляционных контактов между частицами и образованию геля. Золь-гель-процесс - удобный путь получения дисперсных материалов (называемых керамерами) через рост металлоксополимеров в растворах. Он основан на неорганических реакциях полимеризации. Золь- гель-метод включает следующие основные этапы: приготовление раствора ^ образование геля ^ сушка ^ термообработка. В большинстве случаев исходными веществами служат алкоксиды металлов. Реакцию осуществляют в среде органических растворителей. Алкоксиды металлов (в большей степени титана и кремния) - сшивающие реагенты для многих природных полимеров, таких как полисахариды, целлюлозные материалы и др. Такие полимеры содержат высокоактивные гидроксильные группы, способные in situ формировать оксополимеры. Для других видов полимеров вода является реагентом, при добавлении которого происходит гидролиз алкоксидов металлов M(OR)n (M=Si, Ti, Zr, VO, Zn, Al, Sn, Ce, Mo, W, а также лантаниды и др.) с последующей конденсацией образующихся соединений, приводящих к формированию геля.
Экологически оптимальными являются бессточные способы получения композиционных материалов, к которым относится и золь-гель-метод, применяемый для получения катализаторов, связующих и адсорбентов для фармацевтической и косметической промышленности и др.
6.5. Области применения полимерных композитов
Возможность существенного улучшения массовых характеристик изделий при замене легированных сталей, цветных металлов и их сплавов на ПКМ привела к довольно широкому применению ПКМ в качестве материалов конструкционного, теплоизоляционного, теплозащитного, антифрикционного, коррозионно-стойкого и других назначений.
Современная авиация, ракетно-космическая техника, судостроение, машиностроение немыслимы без полимерных композитов. Чем больше развиваются эти отрасли техники, тем шире в них используют композиты, тем выше становится качество этих материалов. Многие из них легче и прочнее лучших алюминиевых и титановых сплавов, их применение позволяет снизить вес изделия (самолета, ракеты, космического корабля) и, соответственно, сократить расход топлива. В настоящее время в скоростной авиации используют от 7 до 25% по весу полимерных композитов, что снижает вес изделия она 5 -30%.
Важно и то, что при изготовлении деталей из полимерных композитов в отходы идет не более 10-30% материала, в то время как у аналогичных деталей из высокопрочных сплавов алюминия и титана, применяемых в авиации, отходы могут в 4-12 раз превышать массу изделия. Кроме того, при изготовлении деталей из ПКМ требуются меньшие трудовые и энергетические затраты, уменьшается количество производственных циклов.
Снижение стоимости углеродных, борных волокон, разработка термостойких органических волокон делают экономически целесообразным внедрение волокнистых ПКМ в машино- автомобиле- и судостроение, медицину и т.д. Из этих ПКМ изготавливают однослойные изделия или их используют в качестве одного из слоев в многослойных конструкциях. Комбинированные конструкции обеспечивают снижение массы до 50% по сравнению с массой металлической конструкции равной прочности, повышение жесткости, демпфирующей способности и увеличение срока службы. Более четверти полимерных композиций идет на цели строительства, широкое применение ПКМ находят в производстве товаров народного потребления и др.
Стеклопластики - наиболее дешевые композиционные материалы, поэтому они широко используются в строительстве, быту, судостроении, в том числе подводном, в наземном транспорте, в производстве спортивного инвентаря.
ПКМ с углеродными волокнами (углепластики) широко применяют в авиации, ракетостроении, для усиления металла в комбинированных конструкциях цилиндрических обечаек, емкостей, работающих под давлением, деталей, находящихся в поле действия центробежных сил или подвергающихся вибрациям и др. Так, усиление оболочки корпуса компрессора газотурбинного двигателя Д-36, выполненного из алюминиевого сплава намоткой углепластика, позволило уменьшить уровень вибронапряжений на 15%, увеличить ресурс работы в 2 раза, снизив при этом массу на 15%.
Применение высокомодульных углепластиков в производстве лопастей несущих винтов, обшивок и других деталей вертолетов обеспечивает снижение массы и повышение долговечности изделия.
Стойкость углепластиков к тепловому удару делает эффективным использование их для тепловой защиты. Кроме того, углеродные волокна и углепластики имеют очень низкий, практически нулевой коэффициент линейного расширения, что делает их незаменимыми в некоторых специальных областях применения, например, в космических телескопах или других аналогичных элементах космической техники.
Низкий коэффициент трения обусловливает применение углепластиков в узлах трения. Эти материалы могут оказаться незаменимыми в качестве самосмазывающихся подшипников, сальников, а также вкладышей опорных подшипников.
По мере снижения стоимости углеволокна применение углепластиков становится все более экономически выгодным в разных отраслях. Широкое применение находят углепластики в автомобиле- и судостроении (повышается грузоподъемность судна, увеличивается скорость).
Высокая химическая стойкость углепластиков позволяет использовать их в химическом машиностроении, нефтяной промышленности для изготовления трубопроводов и других конструкций, работающих в агрессивных средах.
Электропроводность углепластиков используется при создании различных нагревательных устройств: нагревательных панелей для жилых помещений, теплиц, кабин автомобиля и др.
Биологическая совместимость углеродного волокна с тканями живого организма позволяет использовать углепластики для изготовления протезов, деталей медицинской аппаратуры.
Углепластики используют для изготовления спортинвентаря (велосипедов, теннисных ракеток, удилищ, луков и др.).
Применение боропластиков эффективно в элементах конструкций, определяющим критерием работоспособности которых являются высокие удельные значения прочности и жесткости при действии сжимающих нагрузок. Боропластики обладают рекордной прочностью при сжатии и применяются в военной аэрокосмической технике для изготовления деталей, работающих в сложном напряженном состоянии, из них делают небольшие глубоководные аппараты. Стоимость конструкций из бороволокнитов, несмотря на большую стоимость исходного сырья (волокон бора), оказывается меньше стоимости металлических конструкций. При изготовлении конструкций из боропластиков практически не требуется механической обработки.
Низкая плотность, высокие прочность, жесткость, влагостойкость, химическая стойкость, диэлектрические и теплофизические свойства органопластиков определили их применение в качестве конструкционных материалов в изделиях электроизоляционного, коррозионностойкого и фрикционного назначения. Органопластики (армированные пластики на основе органических полимерных волокон) применяют в авиационной технике и ракетостроении для изготовления деталей, работающих под растягивающей нагрузкой, например, сосудов внутреннего давления, высокоскоростных маховиков. Органопластики применяют для внутренней и внешней отделки самолетов вместо стеклопластиков.
Высокая эффективность применения органопластиков в качестве тепловой защиты определяется сочетанием в них сравнительно низкой теплопроводности и повышенной теплоемкости. Органопластики широко используются в качестве теплоизоляции контейнеров для хранения и транспортирования сжиженных природных газов, автомобилей- рефрежераторов и др.
Высокая жесткость и низкая плотность являются основными требованиями к материалам, применяемым в производстве судов, особенно спортивных. Использование материалов на основе арамидных волокон в производстве катеров, глиссеров, гоночных яхт обеспечивает необходимую жесткость конструкций при малой их массе.
Высокая стойкость органопластиков к действию агрессивных сред позволяет широко использовать их для изготовления химической аппаратуры. Органопластики широко используются в электро- и радиотехнической промышленности. Благодаря высоким диэлектрическим характеристикам органопластики применяют в качестве обмоточных лент роторов электродвигателей, для изготовления защитных элементов конструкций крупногабаритных электрогенераторов.
Легкие листовые материалы на основе тканей и войлока из арамидных волокон используют в производстве динамиков радиоприемников, магнитофонов и других деталей радио- и телеаппаратуры. Из органопластиков делают средства индивидуальной защиты от огнестрельного оружия: бронежилеты, каски и прочее.
Искусственные кожи - широкий класс ПКМ (в основном органопластики), применяемый для изготовления обуви, одежды, головных уборов, галантереи, а также многочисленных материалов и изделий технического назначения, признанных восполнить дефицит натурального сырья.
Как отмечалось, в последние годы широко исследуются композиты, где в качестве армирующего элемента выступают микро- и наночастицы. например, магнитопласты, изготовленные из порошка высококоэрцитивных сильных магнитных материалов, таких как SmCos и Nd-Fe-B с диэлектрическим полимерным связующим (термопласт). Такие материалы обладают сильным текстурированием в магнитном поле и могут найти широкое применение при разработке и создании новых приборов микроэлектроники.
6.6. Дендримеры - новый вид полимеров и композиты на их основе
Полимерами нового поколения называют дендримеры, синтезированные в последнее десятилетие XX в. В отличие от обычных цепных полимеров, у которых длина цепи или линейного отрезка цепи существенно превосходит диаметр, дендримеры имеют принципиально иное строение, которое напоминает строение кораллов или дерева. Такие полимеры называют каскадными и их получают менее «затратным» одностадийным методом.
Синтезированные к настоящему времени дендримеры и дендрито- подобные полимеры являются вязкими жидкостями или твердыми аморфными веществами, хорошо растворимыми в большинстве известных органических растворителей. В отличие от цепных полимеров для них не характерно кристаллическое состояние, однако возможно жидкокристаллическое упорядочение. До настоящего времени физико- механические свойства дендримеров недостаточно изучены. Дендримеры имеют большое будущее как материалы специального назначения. Наличие каналов и пор в макромолекулах дендримеров позволяет использовать их для капсулирования «гостевых молекул», в том числе физиологически активных. Такие композиты, построенные по типу гость-хозяин, перспективны для применения в биологии, медицине, фармакологии, косметике и др. Высокая степень функциональности создает поистине неограниченные возможности для широкого применения макромолекул дендримеров в различных областях.
Таким образом, создание, изучение и использование полимерных композиционных материалов - чрезвычайно перспективная и бурно развивающаяся область современного материаловедения.
7. Жидкокристаллические композиты
Современные жидкокристаллические композиты (ЖКК) представляют собой в основном полимерные пленки, в которые в виде отдельной фазы введены жидкие кристаллы.
Жидкокристаллические композиты созданы ради эксплуатации их уникальных оптических и электрооптических свойств. Последние есть свойства самих, входящих в состав жидкокристаллических композитов, жидких кристаллов, лишь измененные в той или иной степени влиянием матрицы.
Сейчас еще до конца не ясно, все ли физические свойства жидких кристаллов сохраняются в композитах. Те же, которые сохраняются, естественно, несколько изменяются. Это связано с особенностями структуры, которые образуют жидкие кристаллы в ЖКК.
7.1.Основные свойства жидких кристаллов
Жидкие кристаллы являются главным рабочим элементом ЖКК. Поскольку основным признаком жидких кристаллов является наличие ориентационного порядка, естественно, все свойства композитов, так или иначе, определяются степенью их ориентационного упорядочения.
Жидкие кристаллы - это большой класс преимущественно органических соединений. Наличие ориентационного порядка предполагает, что их структурные элементы являются анизометричными, чаще всего вытянутой или дисковидной формы. Ориентационный порядок проявляется в том, что выделенные оси структурных элементов - длинные (для вытянутых) или короткие (для дисковидных) - ориентированы вдоль некоторого направления. Таких направлений в пространстве может быть одно (одномерный порядок), два (двумерный) или три (трехмерный ориентационный порядок).
Некоторые жидкие кристаллы дополнительно имеют частичный трансляционный порядок. Он не может быть трехмерным, что характерно для твердого кристалла. Но двух- и одномерные трансляционные порядки наблюдаются довольно часто. Характерная особенность структуры жидких кристаллов - их высокая лабильность. Структурные элементы связаны слабыми дисперсионными силами. Поэтому небольшие внешние воздействия (температура, электрические и магнитные поля, механические напряжения) приводят к заметным изменениям в структуре жидких кристаллов и, следовательно, изменяют их физические свойства.
Как отмечалось, в зависимости от характера микроскопической упорядочения жидкие кристаллы принято делить на несколько главньг типов - нематические (нематики), холестерические (холестерики) и смектические (смектики) (рис. 5.).
Рис. 5. Главные типы жидких кристаллов: а - нематический; б - холестерический; в - «голубая фаза», г - смектический (А); д - смектический (С) (черточками показаны выделенные оси структурных элементов; их длина пропорциональна наклону структурных элементов к плоскости рисунка).
7.2. Методы получения жидкокристаллических композитов
Впервые ЖКК были созданы на базе холестерических кристаллов в 70-е годы для целей термографии. В водный раствор поливинилового спирта (ПВС) при перемешивании добавляли раствор холестерика для образовании эмульсии. Испарение воды приводило к затвердеванию пленки ПВС, в порах которой формировалась планарная текстура холестерика. Зачерненная с одной стороны пленка ЖКК обладала свойством выраженного селективного отражения, которое зависело от температуры. На этой основе в дальнейшем были разработаны термоиндикаторы.
В 80-е годы были разработаны композиты с нематиками для применения в электрооптике. ЖКК с нематиками получены на основе полимерной матрицы, в свободных полостях которой находится нематик. Для получения ЖКК. как с холестериками. так и с нематиками, существуют две основные технологии: 1) эмульгирование с последующим отверждением; 2)фазовое разделение, включающее: получение раствора жидкого кристалла в растворе полимера или пористой матричной среде и отверждение, при котором микрокапли жидкого кристалла отделяются от матрицы в результате полимеризации при охлаждении расплава и испарении растворителя.
Хорошая эмульсия готовится тщательным перемешиванием компонентов композита с помощью коллоидной мельницы или обычной мешалки (скорость перемешивания 1,5-2 тыс. об/мин, время перемешивания 1-3 мин). При таких параметрах эмульгирования образуется эмульсия с размером капель порядка нескольких микрометров.
Большая часть используемых сейчас ЖКК с нематиками получена на основе полимеров. Такой композит сохраняет все механические свойства полимерной основы, в частности, позволяет использовать его в виде тонких пленок любого размера, что является важным техническим преимуществом.
Морфология таких ЖКК определяется соотношением нематик - полимер. При умеренных концентрациях нематика (60 % масс.) в полимере образуются сферические или эллиптические пустоты (капсулы), которые заполняет нематик. Такую структуру называют структурой «швейцарского сыра». При большей концентрации нематика сам полимер собирается в виде мелких шариков и такую структуру называют структурой «полимерных мячей».
7.3.Области применения ЖКК
Жидкие кристаллы широко используются в различных областях техники. Наиболее массовое их применение - индикаторы и дисплеи. Однако на пути еще более широкого внедрения жидких кристаллов в технику стоят серьезные трудности, связанные с технологией их изготовления. Все электрооптические эффекты жидких кристаллов, используемых в экранах отображения информации, наблюдаются в тонких слоях с определенной структурой. Организация такой структуры связана с процессами ориентации молекул жидкого кристалла между двумя стеклянными подложками, на внутреннюю сторону которых нанесены прозрачные электроды для управления. Высокие требования к качеству стеклянных подложек (часто кривизна их поверхности не должна превышать кривизну поверхности земного шара), длительность процессов ориентации и герметизации не только сужают возможности экранов с точки зрения их размеров, но и делают технологию изготовления таких устройств достаточно сложной. Многие из этих трудностей снимают жидкокристаллические композиты.
Преимущества ЖКК несомненны. Они твердые и гибкие, им можно придать любую форму, их размеры практически не ограничены. Особенностью ЖКК является необычный характер деформаций. Деформации сжатия, растяжения, как и во всех жидкостях, очень малы, а деформации сдвига приводят к течению.
Любая функциональная система, механическая или электронная, в процессе работы выделяет тепло. Образуется как бы температурный портрет тела, точно воспроизводящий его функциональное состояние. Спиральная структура холестериков определяет их высокую оптическую активность и способность селективно отражать поляризованный свет, видимого, ПК- и УФ- диапазонов. При изменении температуры, состава среды, напряженности электромагнитного поля изменяется шаг спирати, что сопровождается изменением оптических свойств, в частности, цвета.
Техника применения ЖКК с холестериками сравнительно проста. Первое - необходимо, чтобы изучаемое тепловое поле при нагревании пленки композита не только не выводило ее за пределы холестериче-ской мезофазы, но и оставляло ее в рамках цветотемпературной характеристики, т.е. чтобы наибольшая и наименьшая температуры пленки соответствовали началу и концу области селективного отражения видимого света. Второе - пленка холестерика не должна существенно нарушать тепловое поле, поэтому теплоемкость материала изучаемого объекта должна быть больше теплоемкости пленки. Третье - скорость изменения теплового поля должна быть меньше постоянной времени пленки холестерика. Это время, в зависимости от технологии капсули-рования, составляет 0,2-0,3с, поэтому быстро изменяющиеся тепловые поля с помощью холестерических пленок измерить затруднительно.
Высокая чувствительность ЖКК с холестериками к небольшим изменениям температуры, их способность работать в широком диапазоне температур позволяют использовать их в качестве термоиндикаторов для панорамных измерений полей температур. Если тонкую пленку ЖКК поместить в тепловое поле, которое не перегревает ее и не переводит в изотропную фазу, то по-разному нагретые участки будут иметь разный цвет, если же освещать ее монохроматическим светом (рассматривать через светофильтр, что тоже самое), то - разную интенсивность. Зная заранее какой температуре соответствует тот или иной цвет (или интенсивность), можно построить изотермическую карту изучаемого теплового поля. Это позволяет измерять температуру тела по изменению цвета жидкого кристалла, контактирующего с поверхностью тела.
Метод жидкокристаллической термографии не является универсальным, однако есть области, где только этот метод может дать быструю и достаточную информацию о поле температур. Это, прежде всего области, где требуется панорамное изображение температур без нарушения исследуемой поверхности, когда исследуемая область настолько мала, что не представляется возможным препарирование ее термодатчиками, сенсорами и другими приборами. К таким областям можно отнести неразрушающий контроль качества различных материалов. Это быстрый и дешевый метод отбраковки изделий электронной техники, выпрямителей, интегральных и печатных плат, транзисторов. ЖКК с холестериками широко используются для визуализации невидимых излучений (контроль ИК - лазеров, визуализация аэродинамического нагрева при изучении перехода от ламинарного течения в турбулентное и др.).
Применение ЖКК с тематиками связано в основном с электрооптическими свойствами жидких кристаллов - способностью изменять пропускание света под действием электрического поля. ЖКК с тематиками являются перспективными материалами для построения различных: устройств отображения информации (просветных и отраженных дисплеев), создания проекционных систем, разработки систем управления световыми потоками (ослабители, модуляторы, ограничители мощности, дефлекторы и др.).
Успешно применяются ЖКК в медицинской диагностике, в создании биокомпозитов, поскольку многие сложные биологически активные молекулы (ДНК) и макроскопические тела (вирусы) могут находиться в жидкокристаллическом состоянии.
Новые жидкокристаллические композиты разрабатываются весьма активно и области их применения постоянно расширяются.
8. Углерод - углеродные композиционные материалы
На основе углеродных волокон делают самый теплостойкий углерод-углеродный композит (УУКМ), в котором матрицей, склеивающей углеродные волокна, служит практически чистый углерод.
8.1. Углеродные волокна (УВ). Принципы получения углеродных волокон
Как известно, механическая прочность твердых тел определяется силой межатомной связи этого вещества. Для твердого тела механическая прочность и твердость пропорциональны. Из природных тел наибольшую твердость имеет алмаз, в котором имеются прочные межатомные связи углерод-углерод. Вот эти связи и можно использовать для создания высокопрочных волокон.
Связи углерод-углерод имеются не только в алмазе, но и в графите. Последний имеет слоистую структуру. Внутри слоев имеются прочные связи углерод-углерод, а между слоями межатомные связи углерод-углерод слабые, их называют Ван-дер-Ваальсовыми. Если чещуйки графита расположить вдоль волокон, то волокно получится прочное.
Вопрос о том, как осуществить эту ориентацию? Возможны несколько вариантов:
1. механически вырезать чешуйки и механически их ориентировать;
2. расплавить углерод и направленно закристаллизовать;
3. расплавить высокомолекулярные углеводороды и после их механической однонаправленной ориентации закристаллизовать, а затем удалить все атомы кроме углерода;
4. это же самое можно сделать не в расплаве, а из раствора углерода;
5. на подложку в виде какого-то волокна нанести ориентированно слои графита или высокомолекулярного углеводорода, а затем подложку оставить или удалить.
Первый и второй варианты теоретически возможны, но потребуют очень больших энергетических затрат, т.е. не технологичны и не реальны. А вот 3-й, 4-й и 5-й варианты как раз и используются в промышленности. Рассмотрим их более подробно.
Существуют два термина "графитовые волокна" и "углеродные волокна". Иногда их путают и называют УВ. Термин "графитовые волокна" применяются к волокнам, подвергнутым температурной обработке при > 1700°С, обладающих высокой степенью ориентации и имеющим высокий модуль упругости (~ 345 ГПа). Термин "углеродные волокна" применим к волокнам, термообработанным при <1700°С и имеющим малую степень ориентации и модуль которых не превышает 345 ГПа.
Общепринятая технология производства углеродного волокна основана на термической обработке различных органических волокон:
1. гидратцеллюлозных (ГТЦ), (вискозные),
2. полиакрилонитрильных (ПАН),
3. пека (смола из нефти или каменного угля),
4. полиэфиров,
5. полиамидов (-NH2), полиимидов (=NH),
6. поливинилового спирта (ПВС),
7. поливинилдехлорида,
8. поли-п-фенилена,
9. фенольных смол и т.д.
Из всех видов исходных волокон наиболее пригодными по технологическим и экономическим параметрам оказались:
1. ГТЦ (гидратцеллюлозы, вискозные, (Красноярск), скупают во всем мире,
2. ПАН (полиакрилонирилов),
3. из пека (смолы нефти- и угольные)
На сегодня они являются основным сырьем для изготовления УВ. УВ, полученные, из ГТЦ, были впервые исследованы еще в 1880 г. Они были использованы Т. Эдисоном в его первом патенте на лампы накаливания. Нить, которая была использована в лампе, получена в результате пиролиза хлопкового гидратцеллюлозного волокна. Нити были очень хрупкими, обладали высокой пористостью, что приводило к неравномерному их нагреву, а при высокой температуре они окислялись.
В последующие 30 лет для преодоления этих недостатков был предложен метод пиролитического нанесения покрытий на волокно (пиролиз - превращение органических соединений с одновременной деструкцией их под действием высокой температуры). Приблизительно в то же время в лампах накаливания стали применять гибкую вольфрамовую проволоку и интерес к углеродным нитям угас и не возраждался до середины 50-х годов ХХ столетия.
Термическая обработка исходных волокон в инертном газе при повышенной температуре 1000°С позволила получить волокна с пределом прочности при растяжении 275 МПа = 0,3 ГПа. Довольно высокий.
Возрождение интереса к УВ совпало с усиленными поисками армирующей составляющей, которую можно было бы использовать при создании ракет и ракетных двигателей. В 1959 г. фирма "Юнион карбайд" начала выпускать углеродные ткани, нетканные материалы и пряжу, исходным сырьем для которых служило гидратцеллюлозное (ГТЦ, вискозное) волокно. Партия исходного материала подвергалась предварительному нагреву до температуры ~900°С в среде инертного газа, а затем проводился процесс карбонизации (обуглероживание) при температурах, превышающих 2500°С (интенсивная сублимация, Тпл ~3500°С при 100 тыс. ат.). Волокна, полученные этим методом, имели предел прочности при растяжении 0,3-0,9 ГПа, а = 300-900 МПа.
В 1960 г. Бэкон врастил "усы" графита в дуге при Т = 3600°С и давлении 0,27 МПа (2,7 ат). Базовые плоскости кристаллитов ориентированы параллельно оси "усов" и предел прочности при растяжении составляет 20 ГПа (в 60 раз повысил) при модуле упругости Е = 690 ГПа. Теоретическое значение модуля упругости, оцененного параллельно основной плоскости кристалла графита составляет Е = 1000 ГПа.
Из исследований стало ясно, что структура графитированного волокна в основном определяется надмолекулярной структурой исходных волокон. Было показано, что модуль упругости при растяжении возрастает в 2-3 раза, если процессу корбонизации предшествовала вытяжка исходных нитей до 150%. Вытяжка уже графитированных нитей далее.
Об использовании полиакрилнитрила (ПАН) для производства УВ было впервые сообщено в 1961 г. Для повышения надмолекулярной ориентации вводилась стадия вытяжки ПАН-волокна. Последующая стабилизация проводилась в атмосфере кислорода под нагрузкойц (смесь Аг + О2). Затем волокно карбонизировалось при температуре 1000-3500°С. Механизм процесса пиролиза, структура и свойства УВ волокон из ПАН были тщательно изучены. Была показана возможность получения промышленного УВ из ПАН с модулем упругости 210-800 ГПа при пределе прочности при растяжении 1,6-3,3 ГПа (1966 г.).
Об использовании пеков при производстве УВ сообщили в 1965 г. Сначала волокна получали в основном формованием из расплавов изотропных пеков или аналогичных дешевых продуктов нефтепереработки. Эти волокна также подвергались окислению с последующей карбонизацией в инертной атмосфере при температуре ~1000°С. Свойства таких изотропных волокон были весьма невысокими.
Новый метод получения УВ из пека: пек переводился в жидкокристаллическую (мезоморфную) форму перед процессом прядения. Жидкокристаллическое состояние реализуется в процессе вытягивания в инертном газе при температуре 400-500°С. Пек, переведенный хотя бы частично в мезоморфную фазу, формуется, подвергается окислению и дальнейшей карбонизации при температуре 1000-3000°С. Волокна, полученные этим способом, обладают достаточно высокой степенью ориентации (анизотропией), что предопределено исходным, жидкокристаллическим состоянием. В 1975 г. получили УВ с модулем упругости 700 ГПа.
8.2. Методы получения и области применения УУКМ
Изделия из однонаправленно-, перекрестно- и хаотически армированных углерод-углеродных композитов получают карбонизацией углепластиков при температуре около 1000°С или уплотнением пористой углеродной матрицы с помощью повторяющихся процессов пропитки волокон термореактивными смолами с последующей карбонизацией.
Основные методы получения углерод-углеродного композита включают высокотемпературную обработку углепластиков и нанесение на углеродный волокнистый наполнитель пироутлерода, образующегося при разложении углеводородов. Существуют жидкофазный, газофазный и комбинированный способы получения УУКМ.
Жидкофазный метод включает пропитку исходных армирующих углеродных каркасов специальным, например, фенолформальдегидным связующим (пеками или другими высокоуглеродсодержащими органическими смолами), которое отверждают, а затем карбонизуют при высокой температуре (2000°С и выше). Так как при этом материал становится пористым, его еще раз пропитывают связующим и опять карбонизуют. Эту операцию повторяют несколько раз. Другой способ - газофазный, включает химическое осаждение пироуглерода из газовой фазы на армирующий каркас при высоких температурах и давлениях. Перспективен и комбинированный метод, суть которого заключается в жидкофазной пропитке или газофазном уплотнении армирующего каркаса пироуглеродом с последующим доуплотнением газофазным или жидкофазным способами до получения необходимых свойств. Полученный материал может работать при температурах до 3000°С, если его поверхность защитить от окисления.
Первые стадии производства углерод-углеродного композита аналогичны изготовлению композита с полимерной матрицей. Углеродные волокна пропитывают фенолформальдегидной смолой, т.е. термореактивной смолой. Затем соответствующим образом собранные и пропитанные смолой волокна нагревают в инертной атмосфере. При этом происходит пиролиз смолы (обугливание, аналогичное процессу превращения дерева в древесный уголь) и остается углерод. Полученный композит снова под давлением пропитывают смолой и подвергают пиролизу. В результате многократного повторения процесса образуется прочный материал с минимальным числом внутренних пустот.
Уникальные свойства УУКМ - высокая температуростойкость в сочетании с малой плотностью, высокими прочностью и модулем упругости, стойкостью к тепловому удару, а также способностью устойчиво работать при температурах до 773К в окислительной среде и до 3273К в инертной среде и вакууме обусловили их широкое применение. Области применения углерод-углеродных композитов чрезвычайно разнообразны: авиация и космонавтика, металлургия, машиностроение, реакторостроение, медицина и др.
Из УУКМ делают носовые обтекатели ракет, детали скоростных самолетов, подвергающиеся максимальным аэродинамическим нагрузкам, сопла ракетных двигателей и др.
Пресс-формы для горячего прессования тугоплавких металлов и сплавов из УУКМ обладают высокой прочностью (в 5 - 10 раз выше, чем у графита), термостабильностью, высоким сопротивлением к термическому удару, малой массой, химической инертностью, способностью быстро охлаждаться и более длительным сроком эксплуатации.
Подшипники скольжения на основе графитов, обладают малым коэффициентом трения, высокими теплопроводностью и стойкостью в агрессивных средах. Особенно эффективно их применение в узлах трения, где другие антифрикционные материалы, требующие смазки, не работают из- за высоких или низких температур и агрессивности среды.
Углерод-углеродные композиты обладают высокой радиационной стойкостью. Поскольку они по своим прочностным характеристикам превосходят все известные марки реакторных графитов, представляется перспективным их применение для узлов активной зоны высокотемпературных газоохлаждаемых реакторов. Их применение позволяет значительно повысить надежность работы реактора.
Нагревательные элементы из УУКМ могут применяться в высокотемпературных вакуумных печах или печах с инертной атмосферой при температурах до 3000°С.
Углерод-углеродные композиты широко используют в медицине для изготовления армирующих пластинок для соединения костей при переломах, изготовления сердечных клапанов, имплантации зубов. Эти материалы характеризуются биосовместимостью с тканями человека, прочностью, гибкостью, легкостью. Они отлично приживаются, не давая нежелательных реакций. Например, стержни тазобедренных суставов из УУКМ, разработанные в Германии, обладают высокой усталостной прочностью и заданной деформацией. Французская фирма СЕМ выпускает композиты сложного состава: УУКМ+керамика («био-карб»), сочетающие биологические свойства углерода, биомеханические и трибологические свойства керамики для изготовления зубных протезов.
9. Применение композиционных материалов
Комбинирование различных веществ остается сегодня одним из основных способов создания новых материалов. Большинство современных конструкционных материалов представляют собой композиции, которые позволяют техническим изделиям обладать определенным сочетанием эксплуатационных свойств, например железобетонные конструкции, стеклопластиковые баллоны давления, автомобильные шины и т. п. Во всех случаях — это система разных материалов, каждый из составляющих которой имеет свое конкретное назначение применительно к рассматриваемому готовому изделию. Ни резина, ни корд автомобильной шины не могут выполнять своей функции независимо, они используются совместно и должны рассматриваться как единая композиция. Совместная работа разнородных материалов дает эффект, равносильный созданию нового материала, свойства которого и количественно и качественно отличаются от свойств каждого из его составляющих.
9.1. Основные требования, предъявляемые к конструкционным композиционным материалам
К конструкционным относятся материалы, из которых изготавливаются конструкции и детали машин, воспринимающие механические нагрузки. В конструкциях материалы могут испытывать различные воздействия, связанные, например, с видом нагрузки (растяжение, сжатие, изгиб), характером нагружения (статический, динамический) и, наконец, действием окружающей среды (температура, влажность и т. п.). Перечисленные факторы определяют комплекс конструктивно-эксплуатационных требований, предъявляемых к конструкционным материалам. Способность материалов удовлетворять комплексу требований выявляется при анализе их механических свойств, т. е. характеристик, определяющих поведение материала под действием приложенных внешних механических сил.
При оценке механических свойств материалов различают несколько видов показателей.
1. Показатели свойств материалов, определяемые вне зависимости от конструктивных особенностей и характера службы изделий. Эти показатели определяются путем стандартных испытаний образцов на растяжение, сжатие, изгиб, твердость. Прочностные и пластические свойства, определяемые при статических испытаниях на гладких образцах, не полностью характеризуют прочность материала в реальных условиях эксплуатации. Полученные характеристики могут быть использованы лишь для расчета деталей и конструкций, работающих при нормальных (комнатных) условиях и действии статических нагрузок.
2. Показатели конструктивной прочности материалов, характеризующие их работу в условиях эксплуатации конкретного изделия.
К этим показателям относятся характеристики долговечности изделий (усталостная прочность, износоустойчивость, коррозионная стойкость) и надежности материала в изделии (вязкость разрушения, энергия, поглощаемая при распространении трещины, живучесть при циклическом нагружении и т. д.)
Проблема повышения конструкционной прочности состоит не только в повышении прочностных свойств, но и в том, как при высокой прочности обеспечить высокое сопротивление вязкому разрушению, т. е. повысить надежность материала.
В дисперсно-упрочненных материалах заданные прочность и надежность достигаются путем формирования определенного структурного состояния, при котором эффективное торможение дислокаций сочетается с их равномерным распределением в объеме материала либо (что особенно благоприятно) с определенной подвижностью скапливающихся у барьеров дислокаций для предотвращения хрупкого разрушения.
Возможность получения дисперсно-упрочненных композитов заданной структуры можно продемонстрировать на примере гетерогенных сплавов, подвергнутых закалке и старению. Во многих сплавах после затвердевания происходят фазовые превращения, связанные с изменением взаимной растворимости компонентов в твердом состоянии. Неустойчивый пересыщенный твердый раствор при нагреве (а в некоторых случаях и при комнатной температуре) начинает распадаться. На начальных стадиях распада в пересыщенном твердом растворе образуются объемы, обогащенные компонентом растворенного вещества. При дальнейшем распаде твердого раствора эти зоны растут, образуя ультрадисперсные частицы, равномерно распределенные в объеме материала.
Упрочнение при старении объясняется тем, что при деформировании в случае встречи частиц избыточной фазы дислокации вынуждены либо огибать эти частицы, либо их перерезать, на что требуется приложение дополнительной работы.
У волокнистых композитов матрица (чаще всего пластичная) армирована высокопрочными волокнами, проволокой, нитевидными кристаллами. Идея создания волокнисто-армированных структур состоит не в том, чтобы исключить пластическое деформирование матричного материала, а в том, чтобы при его деформации обеспечивалось нагружение волокон, и использовалась бы их высокая прочность.
9.2. Основы структурного конструирования
Структурное конструирование является итерационным процессом, начинающимся с создания конструкционных представлений о целесообразных путях использования новых материалов. Существует целый ряд требований, которые должны учитываться в процессе производства: масса материала, цена материала, включая стоимость его разработки; легкость в переработке; надежность и испытанность. Значимость того или иного фактора зависит от области применения материала. Уменьшение массы особенно важно при создании материалов для космической и авиационной техники, снижение стоимости - в гражданском строительстве и т.п. Как правило, снижение массы изделия приводит в конечном итоге к снижению цены изделия.
Процесс конструирования начинается с выбора структуры материала. Итерационный подход заключается во все более глубоком изучении свойств материалов при выборе из все меньшего числа предполагаемых структур. Конечным итогом первой операции является начало самой конструкторской работы. Композиционные материалы сами являются объектом оптимизации для использования в конкретных структурах.
Так как композиционные материалы формируются из большого числа индивидуальных слоев, каждый из которых имеет свою ориентацию, можно теоретически рассчитать структуру с оптимальными характеристиками.
От основных характеристик материала существенно зависит выбор конструкции проектируемых деталей.
9.3. Сандвичевые конструкции
Структура сандвичевых конструкций состоит из следующих элементов: двух тонких прочных облицовочных пластин — обшивок, толстой легкой сердцевины — заполнителя, разделяющего несущие пластины и распределяющие нагрузку между ними, и адгезионных слоев, связывающих пластины с заполнителем и передающих нагрузку от заполнителя к облицовкам и обратно. Сэндвичевую конструкцию обычно рассматривают как двутавровую балку, одна из горизонтальных полок пластин которой «работает» на сжатие, а другая — на растяжение. Сотовый заполнитель, связывающий пластины, аналогичен вертикальной полке балки, «работает» на сдвиг и повышает изгибную жесткость структуры, хотя, в противоположность двутавру, основным его назначением является опора для пластин облицовки.
Эффективность различных Сандвичевых конструкций показана на рис. 6.
Сандвичевые конструкции используются в несущих конструкциях самолетов и ракет, применяются при создании различных транспортных контейнеров, подвижных частей и обшивок самолетов, в отделке интерьеров морских судов, катеров и яхт, для производства деталей автомобилей и при создании различных предметов быта: корпусов телевизоров, лыж и т. д.
|
Рис. 6. Примеры, иллюстрирующие уникальное свойство сандвичевых конструкций существенно увеличивать жесткость материала практически без увеличения массы
Сандвичевые конструкции применяются и в домостроении в качестве конструкционных отделочных материалов, для дверей, перегородок и многих других деталей._____
Материалы для несущих пластин
Главными функциями несущих облицовочных материалов (листов) для Сандвичевых конструкций являются обеспечение их жесткости относительно изгиба и сдвига в плоскости пластин, а также передача нагрузок в той же плоскости. Чаще всего используются стекловолокнистые препреги, препреги на основе углеродных волокон (тканей или однонаправленных материалов), алюминиевые сплавы марок 2024 и 7075, титановые или стальные листы. Зачастую возможность использования того или иного материала диктуется ценой на него, и конструкторские разработки могут меняться в зависимости от стоимости исходных материалов. При замене материала несущих пластин (так же как и при замене заполнителя, адгезива и других материалов) необходимо выяснить, насколько изменились свойства композита. Основными свойствами, подлежащими проверке, являются жесткость и хрупкость материала, вид разрушения, надежность и погодостойкость, возможность применения заклепочных и болтовых соединений, а также все другие свойства, которые могут интересовать потребителя. Основным же является анализ изменения прочностных и массовых характеристик. В результате появления новых материалов алюминиевые пластины в панелях интерьеров кабин самолетов были заменены сначала на стеклопластиковые, а стекловолокнистые наполнители — на наполнители из арамидных волокон. В 80-х годах при строительстве ряда новых самолетов фирмы «Боинг» были применены сандвичевые конструкции с покрытием из гибридных материалов на основе углеволокнистых структур и арамидных тканей.
Материалы для заполнителей
Основной функцией заполнителя в сандвичевых конструкциях является придание устойчивости несущим поверхностям и обеспечение передачи сдвиговых нагрузок по толщине композита. Для выполнения этой задачи заполнитель должен быть по возможности более жестким и легким, не должен изменять свойства при воздействии окружающей среды, особенно после специальной обработки.
Дерево
Среди материалов, наиболее часто используемых для заполнения сандвичевых структур, выделяется дерево. Одно из самых старых применений дерева как заполнителя — использование его в строительных конструкциях: в фанерованных дверях, перегородках и т. д. Используется дерево и при производстве лыж в виде плоскостей или ребер жесткости, заполненных ячеистыми структурами, пенопластами и армированными пластиками.
Пены
В последнее время все более широкое распространение получает структура заполнителя на основе твердой пены (пенопласта). Последние исследования в области технологии инжектирования этого материала привели к резкому возрастанию объема его использования. В последнее время наиболее совершенной технологией является использование одноступенчатого простого инжектирования расплава в полость структуры с последующим его охлаждением. Точное регулирование реакции отверждения и эффекты тепловой усадки расплава приводят к большей плотности пены на границе с несущими пластинами, чем непосредственно в сердцевине.
Высокая производительность и низкая цепа такой схемы получения КМ привели к тому, что этот процесс был автоматизирован и получил широкое применение. Другая технология - быстро вспенивающиеся материалы заполнителя для стеклопластиковых лыж и теннисных ракеток. В этой технологии облицовочные структуры образуют закрытые полости, в которые инжектируется пенообразующий субстрат. Такой субстрат, отверждаясь, является одновременно и заполнителем, и адгезивом для стекло- волокнистого препрега облицовки. Пенам придаются иногда и специальные свойства, такие как изоляционность или радиопрозрачность.
Низкая цена полистирольных пенопластов привела к использованию их не только в сэндвичевых конструкциях. Они играют большую роль при создании теплоизоляции в рефрижераторном транспорте. В строительстве этот материал конкурирует с полиуретанами. Поливинилхлоридные (ПВХ) пенопласты используются в самолетостроении в качестве заполнителя в панелях полов. Они имеют меньшую плотность по сравнению с сотовыми структурами на основе арамидов.
Сотовые структуры
Сотовые структуры являются общим видом продукции, использующей непропитанные и пропитанные связующим крафт-бумаги, различные алюминиевые сплавы, арамидные бумаги, стеклопластики на основе различных видов тканей и связующих. В меньших количествах для этих целей используются титановые и стальные листы. Виды ячеистых структур на основе адгезионно соединенных полос тонкого материала показаны на рис. 7. Существуют два основных процесса производства сотовых структур:
процесс растяжения: предварительно соединенный по исходным линиям пакет растягивается, одновременно образуя ячеистую структуру; преимущества процесса — одностадийность операции;
процесс рифления: листы исходного материала предварительно подвергаются рифлению; это могут быть листовые металлы, пластики, бумага, армированные пластики и т. д., причем некоторые материалы термофиксируются, а затем склеиваются или соединяются другим способом.
Используя сотовую структуру на основе арамидной бумаги, можно получить материал заполнителя с высокой прочностью, обладающий плотностью 16 ... 48 кг/ма и использующийся для облицовки внутренних стен и потолка. Несущие панели — стеклотекстолит толщиной менее 0,25 мм. Физические и механические свойства сотовых структур для заполнителя сандвичевой конструкции зависят в основном от свойств материалов, из которых эти конструкции производятся.
Рис. 7. Отдельные этапы производства сотовых заполнителей |
Теплопроводность сандвичевых панелей складывается из теплоизоляционных свойств каждого из компонентов: пластин, заполнителя и связующего. Тепловое сопротивление R (величина, обратная теплопроводности) является суммой сопротивлений всех трех компонентов (включая эффекты на границах раздела).
Форма ячейки.
Все сотовые структуры являются анизотропными и их свойства в выбранном направлении должны соответствовать прилагаемым нагрузкам. Для большинства сотовых структур наблюдаются очень малые потери соотношения прочность/масса при формовании или отверждении материала.
Форма ячейки может иметь различную конфигурацию в зависимости от производителей этих заполнителей композитов. Для некоторых материалов, например для алюминия, форма вольно или невольно может быть изменена при переработке. Необходимо заметить, что недорастяжка или перерастяжка сотового наполнителя меняет не только форму ячейки, но и ее плотность. В случае перерастяжки, изменение свойств в одном направлении ослабляет заполнитель и по двум другим.
Размер ячейки.
Размер ячейки является как бы вторичным фактором, определяющим большинство механических свойств материалов заполнителя. Первичным является уровень прочности соединения заполнителя с несущими пластинами. Размер ячейки определяет и уровень напряжений, возникающий в адгезионном слое между торцами ячеек и несущими пластинами.
Толщина.
Сдвиговые характеристики и свойства заполнителя при сжатии могут быть корректно оценены только с учетом толщины сотовых заполнителей. Параметр эффективности толщины позволяет прогнозировать поведение сандвичевого материала. Необходимо заметить, что корректно можно определить фактор толщины только с учетом свойств материала несущих пластин.
Сотовые заполнители на основе алюминия
Большинство алюминиевых сплавов используется для получения сотовых заполнителей методом рифления, рифления с усиливающими элементами; для получения сотового заполнителя с предельно вытянутой ячеистой структурой и со специальными формами ячейки. Часть материалов на основе алюминии используется при раскрое деталей слоистых геометрических форм - цилиндров переменного радиуса, сфер и т. д. Некоторые виды алюминиевой фольги используются для заполнителей в виде намотанной рифленой спирали. Последние, в виде цилиндров или труб используются для поглощения тепла.
Алюминий для сотовых структур до сих пор является самым распространенным среди материалов для заполнителей. Зачастую стоимость производства сотовых структур из алюминия ниже, чем при использовании других материалов. Эффективная плотность сотового заполнителя, полученного растяжением пакета лежит в пределах 32 ... 192 кг/м3, а заполнителей, полученных рифлением. - 128 ... 880 кг/м3. При более низких плотностях для заполнителей, полученных рифлением, снижается сдвиговая прочность
Дата добавления: 2023-01-08; просмотров: 50; Мы поможем в написании вашей работы! |
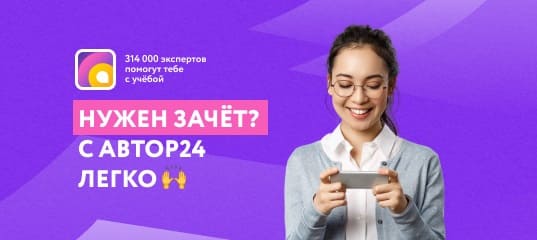
Мы поможем в написании ваших работ!