Цикловые СУ со штеккерной панелью
Штеккерная панель является разнавидностью управляющих устройств циклового управления. Это решетка, состоящая из горизонтальных и вертикальных электрошин, изолированных друг от друга и соединяемых между собой специальными штеккерами.
Штекер - металлический стержень с изолированной ручкой, устанавливаемый в гнезда штеккерной панели, если необходимо выполнить данный переход в заданной последовательности.
Таким образом с помощью штеккеров достигается многочисленность вариантов соединений указанных шин и тем самым изменяется последовательность включения отдельных приводов. Для сложных панелей при наборе программы штеккерами рекомендуют применять специальные бумажные трафареты с вырезанными отверстиями в месте установки штекеров.
Рисунок 26 – СУ со штекерной панелью
Примером использования штеккерной панели является система управления промышленным роботом модели “Циклон – 3Б”. Работа данной схемы производится при повороте лапки, закрепленной храповом колесе при срабатывании электромагнита (Э). Ток от положительного источника (постоянный U=24В) через лапку подается на контакт и далее на горизонтальную шину, если в данном месте установлен штеккер то ток подается и на вертикальную шину и запитывает контактор (Рi) в результате этого запускается в действие один из приводов данного устройства (станка). В конце перемещения, который обеспечил данный привод срабатывает установленный там конечный выключатель (ВК). Он подготавливает цепь управления в которую входит следующий электрический контакт. Таким образом пр повторном включении электромагнита лапка перемещается на контакт №2. Который содержит в своей цепи замкнутый конечный выключатель.
|
|
Преимущества:
ü Простота реализации схемы и конструкции управляющего устройства
ü Достаточно простое перепрограммирование , сводимое к замене положения штеккеров.
Недостатки:
ü Ограниченный объем информации, вводимой на управляемое оборудование (порядок включения привода).
ü Электромеханический контакт штеккеров с гнездами в производственных условиях является ненадежным и ведет к возможным отказам.
В настоящее время для устранения указанных недостатков в качестве управляющих устройств для цикловых СУ разработаны новые устройства “программируемые контроллеры”.
8. Иерархия задач упр-я применит к соврем гибкому пр-ву. Взаимодействие задач управления при автоматизации вспомогательных операций. Уровни управления.
Примеры конфигурации систем управления для гибкого производственного модуля (ГПМ) (рис 1)
|
|
|
1 – станок с ЧПУ; 2 – устройство загрузки и разгрузки деталей в накопитель; 3 – накопитель; 4 – устройство загрузки накопителя; 5 – транспортная система для подачи деталей на ГПМ; 6 – устройство замены режущего инструмента на станке; 7 – механизм смены комплекта инструментов в магазине станка; 8 – система транспортирования инструмента; 9 – устройство загрузки деталей в виде промышленного робота; 10 – контрольно-измерительные устройства; 11 – вспомогательные системы; 12 – стружкодробление; 13 – стружкоудаление; 14 – устройство регенерации и подачи СОЖ.
Рисунок 2 – Пример №2 конфигурации СУ для ГПМ
Среди основных особенностей машиностроительного производства является его многоуровневая структура, что в свою очередь сказывается на характере задач управления, делая их многоуровневыми (иерархическими):
|
1. отдельные рабочие машины или станки, ведущие обработку деталей (оборудование) сюда же входят промышленные работы, например, в составе ГПМ. там их функция сводится к установке заготовке и снятию готовой детали. Работа этих единиц обор-я идет по программе, вводимой извне, причем каждая разновидность обор-я наделена своей степенью самост-ти (степенью адаптации).
Цель управления: задание станкам и роботам необходимых координат опорных точек (для станков и роботов с позиционной СУ), либо задание траекторий или линий (для контурных СУ) во втором случае появляется возможность задавать изменяемую скорость подачи инструмента вдоль этой траектории. Для оборудования с многомерными системами может задаваться сложная поверхность (при объемной обработке пресс-форм).
|
|
2. уровень –объектами управления являются упомянутые выше виды оборудования и кроме того транспортно-накопительная система участка или цеха, автоматизированный склад заготовок и деталей, и комплект инструментов и оснастки. Возможности СУ расширяются путем переналадки, путем перераспределения работ между станками (т.н. ГПС или ГАЛ)
Цель управления: наиболее полное и эффективное использование имеющегося оборудования. При условии обеспечения заданного коэффициента использования и исправности оборудования.
3. уровень – включает в себя системы координирования различных участков, по изготовлению деталей и их сборке, сюда же включаются отделы подготовки программ, отделы САПР, а так же отделы по подготовке инструментов и оснастки.
Цель управления: разработка основ для создания так называемых гибких производственных комплектов ГПК.
|
|
4. уровень – включает в себя все предыдущие с их задачами и целями и дополнительно объектами управления становятся отделы анализа рынка (маркетинг), связи с поставщиками, отделы сбыта продукции и т.п., т.е. объектом управления является целое предприятие.
Процесс управления в условиях машиностроительного производства можно подразделить в зависимости от способа управления на 2 вида:
*человеко-машинная система, когда в управлении принимает участие и человек.
*дистанционного управления. когда человек наблюдает за зоной обработки или сборки, находясь на некотором расстоянии, это связано с вредными условиями производства (используются системы технического зрения СТЗ. системы управления копирующего действия, когда движения человека – оператора с помощью специальных регуляторов воспроизводятся и передаются на значительные расстояния).
11. Цикловое програмное управление (ЦПУ). Устройство и принцип действия систем с командоаппаратом.
Простейшим случаем управления оборудованием (станками) , имеющим несколько электрических приводов является ЦПУ. Управление в этом случае сводится к включению отдельных приводов в нужной нам последовательности. Кроме последовательности можно задавать режимы обработки, если используются регулируемые приводы. Как правило, величина перемещений исполнительного органа станка контролируется с помощью жестких упоров, в сочетании с датчиками конечного положения обработки (погрешность позиционирования по жестким упорам ±0,1мм). В качестве управляющего устройства в СЦПУ широко применяются командоаппараты.
1- барабан; 2 – блок конечных выключ-й (БВК), срабатыв-щих по упору; 3 – упоры или кулачки; 4 – кинематическая цепь; 5 – электродвигатель; 6 – шпиндель станка; 7 – обрабатываемая деталь
Рисунок 25 – СУ с командоаппаратом
Особенность работы - командоаппарат обеспечивает команду на выполнение заданного перемещения инструмента ( по 1 какой-то оси), окончание перемещения командоаппаратом не задается, по этому такая система использует прямолинейный профиль обработки детали. Командо аппарат может задавать изменение режимов резания за счет 1 из упоров (поз.3) воздействует на соответствующий конечный выключатель, а он подает команду на регулируемый привод подачи или главного движения.
10. Модели систем упр-я технол обор-ем и их классификация
К разновидностям моделей СУ можно отнести:
1. Аналоговые системы - получили широкое распространение в машиностроении и других отраслях, где ведут обработку резанием.
Аналог- некий прототип (копир, кулачок, комбинация упоров и т.п.) той поверхности обрабатываемой детали, которую надо получить т.е. программоносителем при обработке деталей являются вышеназванные элементы, которые создают модель обработываемой детали.
Для таких моделей характерны 2 потока информации:
ü Информация о размерах обработки – она задается положением упоров или профилем кулачков
ü Данные о фактическом положении исполнительного устройства - они получаются при воздействии подвижного элемента на датчик конечного положения.
Рисунок 22 - Примеры аналоговых СУ
Подобного рода аналоговые системы получили название незамкнутых (если используется только управляющий кулачок) и замкнутых (если используется информация обоих видов).
а – пример СУ от распределительного вала с кулачками, а именно барабанный кулачок, обеспечивающий перемещение детали вдоль ее оси, дисковый кулачок обеспечивает поперечное перемещение суппорта с резцом (токарные автоматы).
б -система копирования профиля прямого действия (не применяются специальные усилители для рзвития силы резания)
Недостатки:
üПовышенный износ копира, т.к. он непосредственно воспринимает усилие резания
в - пример следящего привода при использовании в системе гидравлического копирования
1 – поперечные салазки с резцедержателем
2 – продольные салазки, приводимые в действие ГЦ 1
3 – копир
4 – золотник усилителя для управления ГЦ 2 поперечной подачи
При работе данной СУ золотник взаимод-вует с копиром, отслеживает его профиль при этом средний поршень будет подниматься вверх, при этом откроется нижняя часть проточки корпуса золотника, масло поступает в нижнюю часть ГЦ.
При использовании следящего привода особое значение приобретает быстродействие данного привода т.к. качество обработки деталей будет определять шереховатость.
Системы ЧПУ
Преимущества применения систем ЧПУ:
ü Запись программы может производиться на различные прграммоносители (перфокарты, перфоленты, магнитные диски и ленты, оптические системы)
ü Высокая гибкость управления оборудованием т.к. ввод –вывод программ значительно упрощен (особенно оперативные системы управления).
ü Большой объем и разнообразие информации вводимой в систему ЧПУ (записываются точки позиционирования со своими координатами, режимы обработки, скорости перемещения, а так же вспомогательные команды).
ü Производится управление сменой инструмента
ü Удобство в хранении программ
ü Возможность корректировки управляющих программ
Недостатки применения систем ЧПУ:
ü Некоторая сложность и высокая стоимость по сравнению с аналоговыми
Разновидности систем ЧПУ по их технологическому назначению
1. Позиционные системы ЧПУ - обработка деталей производится в процессе перемещения от одной опрпорной точки к другой, при этом возможна обработка с управлением пложения этих точек. Характерные операции – сверление отв. по заданным координатам; станок при перемещении из точки в точку (point to point) производится на ускоренной подаче, т.е. оно неуправляемое.
Эти же сисстемы позволяют обрабатывать детали по контуру, когда исполнительное устройство перемещается на заданную величину параллельно координатным осям ОХ и ОУ. Допускается совмещенное перемещение (обработка под углом, обработка по прямой линии). Станки, использующие эту систему маркируются Ф2.
2. Контурные СУ (функциональные, непрерывные) – данные системы позволяют вести обработку деталей по сложному контуру, или обеспечивают сложные пространственные перемещения по 2 или по 3 координатам. Сложная траектория движения инструмента обеспечивается одновременной работой нескольких исполнительных узлов, в частности, системы применяются для токарных станков. Управление перемещением производится от единой программ, состоящей из нескольких траекторий (маркируют Ф3).
3. Универсальные системы ЧПУ (позиционно-контурные) – применяются для многооперационных станков, для них характерно:
ü смена инструмента из магазинов высокой емкости
ü наличие коррекции размеров
ü большой набор вспомогательных функций
Универсальные системы (системы с дополнительными потоками информации Ф4).Существует простейшая разновидность СУ – системы с одним потоком информации (цифровая индикация текущих размеров). В целом станки не имеют системы ЧПУ, а работают по следующему принципу : станочник задает упрощенную программу на величину перемещения, а далее визуально наблюдает за ходом обработки (Ф1).
Рисунок 24 - разновидности систем ЧПУ
13. Системы ЧПУ
Преимущества применения систем ЧПУ:
ü Запись программы может производиться на различные прграммоносители (перфокарты, перфоленты, магнитные диски и ленты, оптические системы)
ü Высокая гибкость управления оборудованием т.к. ввод –вывод программ значительно упрощен (особенно оперативные системы управления).
ü Большой объем и разнообразие информации вводимой в систему ЧПУ (записываются точки позиционирования со своими координатами, режимы обработки, скорости перемещения, а так же вспомогательные команды).
ü Производится управление сменой инструмента
ü Удобство в хранении программ
ü Возможность корректировки управляющих программ
Недостатки применения систем ЧПУ:
ü Некоторая сложность и высокая стоимость по сравнению с аналоговыми
Наиболее перспективное использование ЧПУ в серийном и мелкосерийном производстве и для наиболее ответственных деталей.
Важнейшим показателем любой СЧПУ является точность с которой перемещаются подвижные узлы станка.
Здесь следует выделить 2 величины:
1. Цена элементарного импульса (погрешность СУ ? оговаривается в паспорте станка мах. 0,001 мм)
2. Погрешность позиционирования
(3)
где mд – масса обрабатываемой детали;
Vрх – скорость рабочих ходов;
ΔР – колеб-е давл-й масла или воздуха в сист станка;
ΔU – величина износа направляющих станка;
Т – степень нагрева деталей привода, вызывающих его температурные деформации.
Вывод: Дп характеризует фактически достижимую точность обработки и реально составляет погрешность в пределах:
Дп = ±(0,02…0,03) мм.
Разновидности систем ЧПУ по их технологическому назначению
1. Позиционные системы ЧПУ - обработка деталей производится в процессе перемещения от одной опрпорной точки к другой, при этом возможна обработка с управлением пложения этих точек. Характерные операции – сверление отв. по заданным координатам; станок при перемещении из точки в точку (point to point) производится на ускоренной подаче, т.е. оно неуправляемое.
Эти же сисстемы позволяют обрабатывать детали по контуру, когда исполнительное устройство перемещается на заданную величину параллельно координатным осям ОХ и ОУ. Допускается совмещенное перемещение (обработка под углом, обработка по прямой линии). Станки, использующие эту систему маркируются Ф2.
2. Контурные СУ (функциональные, непрерывные) – данные системы позволяют вести обработку деталей по сложному контуру, или обеспечивают сложные пространственные перемещения по 2 или по 3 координатам. Сложная траектория движения инструмента обеспечивается одновременной работой нескольких исполнительных узлов, в частности, системы применяются для токарных станков. Управление перемещением производится от единой программ, состоящей из нескольких траекторий (маркируют Ф3).
3. Универсальные системы ЧПУ (позиционно-контурные) – применяются для многооперационных станков, для них характерно:
ü смена инструмента из магазинов высокой емкости
ü наличие коррекции размеров
ü большой набор вспомогательных функций
Универсальные системы (системы с дополнительными потоками информации Ф4).Существует простейшая разновидность СУ – системы с одним потоком информации (цифровая индикация текущих размеров). В целом станки не имеют системы ЧПУ, а работают по следующему принципу : станочник задает упрощенную программу на величину перемещения, а далее визуально наблюдает за ходом обработки (Ф1).
Рисунок 24 - Разновидности систем ЧПУ
Использование метода ЧПУ для МРС.
Структура кадровой управляющей программы:
-выбор базовой точки
-выбор инструмента
-выбор корректора на инструмент
-запуск шпинделя с указанием частоты вращения
-перемещение инструмента с указанием подачи и припуска на обработку
-задание значений интерполяции (при необходимости)
22. Временная диаграмма при вып-и логич-й операции “И”
Временная диаграмма – это графический метод, позволяющий специалисту изображать переходы любой из входных переменных из одного состояния в другое (0 или1) и проследить их влияние на состояние выходной характеристики.
Любая логическая операция (в нашем случае С=А·В) может быть изображена графически в виде временной диаграммы.
Рисунок 39 - Временная диаграмма при выполнении логической операции “И”
Таким образом, временные диаграммы позволяют:
1. Графически изображать ход процессов управления с использованием таймеров
2. Такие диаграммы позволяют изображать состояние всех элементов системы и состояние системы в целом
3. Можно построить диаграмму для любого логического выражения
4. Построение диаграмм позволяет избежать ошибок из-за наложения по времени срабатывания различных элементов.
14. Логические задачи в СУ. Роль этих задач при разработке СУ.
В усл-ях реального производства любая производственная система должна учитывать внешние воздействия в которые входят и управляющие воздействия.
Управляющие воздействия подразделяются:
ü Вырабатываемые под конкретные условия, изменяющейся производственной обстановки, они требуют решения “по значениям переменных” (например изменяющаяся t сушильной камеры).
ü Управляющие воздействия (сигналы) могут вызывать ответную реакцию (решение по основным признакам). Если на вопрос можно ответить “Да” или “Нет”, то он относится к основным признакам (например: управляющий сигнал при автоматизации контроля размера, приводящий к решению принять деталь или забраковать ее).
Количественные значения размеров не учитываются. Под данную разновидность основных признаков можно отнести состояние оборудования (Например “Вкл”, “Выкл”).
Вывод: если объект управления может быть автоматизирован с помощью основных признаков типа “Да – Нет” то такие СУ называются логическими СУ. Логические СУ в начале проектирования основываются на разработке так называемых “таблиц истинности”.
Таблица истинности - матрица, устанавливающая связь между всеми возможными комбинациями логических элементов и соответствующих им значениями функции.
“ИЛИ” - Логическое сложение.Если характеристика А или характеристика В имеет истинное значение то и все выражение будет истинно.
у=х1+х2+…+хn
х1 | 0 | 1 | 0 | 1 |
х2 | 0 | 0 | 1 | 1 |
у | 0 | 1 | 1 | 1 |
“И” - Логическое умножение (А,В – логические переменные). Как А так и В должны быть истинными ,чтобы все выражение было истинным. Если выражение равно 1 или значение переменных равно 1 , то они истинны.
у=х1*х2*…*хn
х1 | 0 | 1 | 0 | 1 |
х2 | 0 | 0 | 1 | 1 |
у | 0 | 0 | 0 | 1 |
“НЕ” - Логическое отрицание (инверсия) – Если значение А истинно то значение выражения будет ложным. Таким образом последний оператор меняет значение переменной на противоположное.
у=х (не х)
х | 0 | 1 |
у | 1 | 0 |
16 Кнопочный выключатель станка как устр-во, реализ-е логич-ю задачу упр-я. Сведения из алгебры логики.
Управление станком с помощью кнопочной станции
НО-нормально-открытый контакт, при котором цепь управления разомкнута до тех пор, пока нет воздействия на этот контакт.
НЗ-нормально закрытый контакт
Обозначим переменные следующим образом:
G – состояние кнопки “Пуск”:
G=1 - кнопка нажата;
G=0 - кнопка выключена.
S – состояние кнопки “Стоп”
S=1 - кнопка нажата;
S=0 - кнопка отжата.
Для процесса управления станком не безразлично состояние объекта управления до начала воздействия, поэтому:
R – состояние станка до начала воздействия;
R=1 – станок до начала воздействия работал;
R=0 – станок находился в выключенном состоянии
(не работал)
G | S | R | R’ |
0 | 0 | 0 | 0 |
0 | 0 | 1 | 1 |
0 | 1 | 0 | 0 |
0 | 1 | 1 | 0 |
1 | 0 | 0 | 1 |
1 | 0 | 1 | 1 |
1 | 1 | 0 | 0 |
1 | 1 | 1 | 0 |
В основе алгебры-логики лежит использование 3 основных операторов или действий с логическими переменными:
Оператор | Символ | Мат. Запись |
И | · | А·В |
ИЛИ | + | А+В |
НЕ | - | А-В |
“И” - Логическое умножение (А,В – логические переменные). Как А так и В должны быть истинными ,чтобы все выражение было истинным. Если выражение равно 1 или значение переменных равно 1 , то они истинны.
“ИЛИ” - Логическое сложение.Если характеристика А или характеристика В имеет истинное значение то и все выражение будет истинно.
“НЕ” - Логическое отрицание (инверсия) – Если значение А истинно то значение выражения будет ложным. Таким образом последний оператор меняет значение переменной на противоположное.
С помощью алгебры – логики легко записываются выражения более сложного вида: например, сочетающие в себе 2 или более оператора. Y=(AB)+C (4)
Любое выражение алгебры-логики может быть представлено в виде строки таблицы истинности, причем слева от знака “=” принято ставить обозначение выходной переменной, а справа все остальные переменные.
15 Пульт управления с блокировкой
При автоматизации производства возникает задача осуществлять управление в режиме “Вкл-Выкл” при этом при использовании сложного дорогостоящего оборудования необходимо исключить доступ посторонних лиц к этому процессу управления. На этой основе возникает логическая система управления 2 переменными, которые могут принимать только 2 значения, а именно положение: “Вкл” – 1, “Выкл” - 0
Рисунок 27 - Пульт управления с блокировкой
Примем условные обозначения:
S – переменная соответствующая положению переключателя или
тумблера
S=0 - положение выключено
S=1 – положение включено
L – переменная в состоянии блокировки
L=0 – блокировка работает т.е. положение ключа в состоянии блокировки
L=1 – ключ находится в состоянии деблокировки
R – состояние процесса до начала управления им
R=0 – данный станок не был в работе до начала упр-я
(процесс управления не шел)
R=1 – процесс управления протекал до начала упр-я
Таблица 1 – Таблица истинности
Вход | Выход | ||
S | L | R | R’ |
0 | 0 | 0 | 0 |
0 | 0 | 1 | 1 |
0 | 1 | 0 | 0 |
0 | 1 | 1 | 0 |
1 | 0 | 0 | 0 |
1 | 0 | 1 | 1 |
1 | 1 | 0 | 1 |
1 | 1 | 1 | 1 |
Таблица истинности содержит 3 входных переменных, которые могут принимать только 2 значения “0” или “1”. В таблице обязательно рассматриваются все возможные комбинации этих значений. Одна крайняя графа выделяется по выходную переменную и она обозначает своим состоянием как ведет себя объект управления (при значении =0 станок будет отключен т.е. процесс обработки невозможен и наоборот).
Пример прочтения 3 строки таблицы: если переключатель находится в положении “выкл” и если ключ вставлен в замок и если процесс отсутствовал, то станок останется выключенным т.е. процесс обработки будет невозможным.
Рекомендации по построению таких таблиц:
1. Количество входных и выходных переменных может быть любым
2. Последовательность строк и столбцов этой таблицы может быть произвольной
3. Каждая строка таблицы представляет из себя двоичный код, отражающий взаимосвязь этих переменных
4. Если переменных в таблице много, то их комбинаций становится еще больше, поэтому достаточно бывает рассмотреть только реально встречающиеся “естественные состояния системы”
5. Таблица истинности может быть записана в математической форме и используя так называемую “алгебру логики”. Она получила название – Булева-алгебра.
Управление станком с помощью выключателя с кнопочной станции
Обозначим переменные следующим образом:
G – состояние кнопки “Пуск”:
G=1 - кнопка нажата;
G=0 - кнопка выключена.
S – состояние кнопки “Стоп”
S=1 - кнопка нажата;
S=0 - кнопка отжата.
Для процесса управления станком не безразлично состояние объекта управления до начала воздействия, поэтому:
R – состояние станка до начала воздействия;
R=1 – станок до начала воздействия работал;
R=0 – станок находился в выключенном состоянии (не работал)
G | S | R | R’ |
0 | 0 | 0 | 0 |
0 | 0 | 1 | 1 |
0 | 1 | 0 | 0 |
0 | 1 | 1 | 0 |
1 | 0 | 0 | 1 |
1 | 0 | 1 | 1 |
1 | 1 | 0 | 0 |
1 | 1 | 1 | 0 |
Дата добавления: 2018-02-15; просмотров: 1050; Мы поможем в написании вашей работы! |
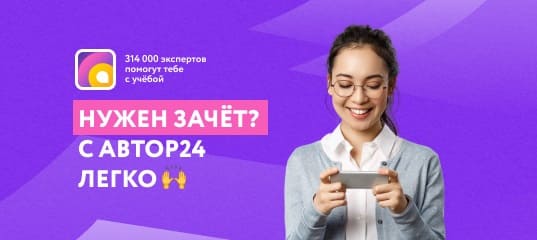
Мы поможем в написании ваших работ!