ПРОИЗВОДСТВО ВИНТОВЫХ ДВИГАТЕЛЕЙ
РАЗВИТИЕ ПРОИЗВОДСТВА ДВИГАТЕЛЕЙ
Производство опытных образцов ВЗД в России началось в конце 60-х годов [94]. В середине 70-х годов ВНИИБТ и его Пермским филиалом было организовано промышленное производство этих машин на Кунгурском и Павловском машиностроительных заводах, а позднее производство двигателей Д1-195 и Д2-195 развернулось на заводе "Прогресс" (Украина). Производство статоров было размещено в специализированном цехе завода синтетического каучука в г. Чайковском.
Пик производства пришелся на 1985-1987 гг., когда ежегодно выпускалось 7000-8000 секций ВЗД общего назначения и для капитального ремонта скважин. В последующие годы объем производства двигателей снизился.
С начала 90-х годов НПО "Буровая техника" - ВНИИБТ на своих заводах в Пермском филиале и г. Котово Волгоградской области помимо двигателей общего назначения начинает изготавливать ВЗД для горизонтального бурения типа ДГ. Наряду с узлами и деталями, традиционными для турбобуров, винтовой двигатель содержит такие оригинальные детали, как многозаходные статор и ротор (рис. 11.1), изготовление которых потребовало разработки уникальных технологических процессов и специального оборудования.
Впервые технология изготовления многозаходных РО ВЗД была разработана в Пермском филиале ВНИИБТ. Большой творческий вклад в ее создание и совершенствование внесли С.С. Никомаров, А.Н. Вшивков, С.А. Ганелина, А.Д. Коновалов, Ю.А. Коротаев, Н.Д. Сумцова, А.В. Цепков и специалисты упомянутых выше заводов.
|
|
ТЕХНОЛОГИЯ ИЗГОТОВЛЕНИЯ РОТОРОВ
Ротор винтового двигателя и стержень пресс-формы статора как объект металлообработки нужно рассматривать как зубчатое колесо с винтовыми зубьями специального профиля с отношением длины к диаметру в пределах от 10 до 25.
Для ВЗД различных типоразмеров шаг винтовой поверхности роторов изменяется от 150 до 1200 м. Число шагов, как правило, не менее двух.
При изготовлении ротора регламентируются допуски на профиль и диаметральные размеры зубьев, их осевые и окружные шаги, а также чистота поверхности.
Способы зубообразования.В практике отечественного производства известны три способа зубообразования роторов:
способ обработки червячными фрезами по методу обкатки на горизонтально-зубофрезерных станках [126];
способ гидроштамповки роторов с применением специального технологического оборудования [115];
способ горячей прокатки с использованием миниатюрных прокатных станов.
Наибольшее распространение (более 90 % всех изделий) получил способ зубофрезерования.
К числу преимуществ этого способа изготовления относится: универсальность применения, стандартные требования к заготовкам изделия и умеренные капитальные затраты на приобретение оборудования.
|
|
Для фрезерования используют горизонтальные зубофрезерные станки модели 5В370 Коломенского завода и станки производства фирмы "Heckert" (ФРГ). Последние обладают большой жесткостью и позволяют обрабатывать роторы при увеличенных подачах на один оборот изделия. Длина обрабатываемых деталей достигает 3 м.
Для повышения жесткости системы станок - деталь и качества обработки разработана специальная технологическая оснастка, в частности подвижной люнет и специальная оправка.
Роторы обрабатываются специальной червячной фрезой (рис. 11.2), имеющей ряд специфических особенностей [140, 141]. Фрезы изготавливаются из инструментальной стали.
Режимы фрезерования подбираются исходя из допустимой скорости резания и требуемой чистоты обработки поверхности детали с учетом жесткости и мощности станка. Нарезка осуществляется, как правило, за один проход. Фрезы не приспособлены обрабатывать детали высокой твердости, поэтому твердость заготовок роторов не превышает НВ 320.
Рис. 11.2. Фреза для нарезания винтовых поверхностей
|
|
Типичный режим механической обработки: частота вращения фрезы 45 об/мин при подаче на один оборот изделия 1,25 мм. Точность изготовления детали длиной порядка 2000 мм: конусность по длине до 0,05 мм, отклонение от прямолинейности не более 0,15 мм. Чистота поверхности сравнительно невысока и находится в пределах 5 класса (высота неровностей 20 мкм). Машинное время обработки ротора (длиной 2000 мм, диаметром 140 мм и высотой зуба 10 мм) составляет 3,5-4 ч.
При обработке стержня пресс-формы подача на один оборот изделия снижается до 0,5 мм, что позволяет увеличить чистоту обработки на один класс.
Получаемая методом фрезерования чистота и твердость изделия не удовлетворяют современным требованиям. Поэтому почти повсеместно применяется полирование поверхности ротора червячным абразивным кругом на вулканитовой связке или наждачным ремнем на токарном станке.
В ходе развития производства ВЗД был апробирован большой ассортимент марок стали для роторов и способов упрочняющей технологии.
В настоящее время роторы изготавливаются из коррозионно-. стойкой стали марки 20X13 или 40X13 (ГОСТ 5632-72) с термообработкой профиля токами высокой частоты до твердости HRc 40-45, а также из легированной стали марки 40ХНМА или 40ХН (ГОСТ 4543-71) с последующим твердостным хромированием профиля толщиной 0,15-0,25 мм. При хромировании чистота поверхности обеспечивается двойным полированием.
|
|
В опытном порядке применялись и другие методы упрочнения роторов: ионное азотирование, борирование, наплавка твердых сплавов и др.
Повышенная точность профиля обеспечивается контролем фрез, их корректировкой с учетом толщины слоя упрочнения и проверкой на специальных приборах.
За рубежом для изготовления многозаходных роторов также используется технология зубофрезерования. Специальные станки позволяют изготавливать роторы длиной до 5 м. Однозаходные роторы изготавливаются на токарных станках с применением вихревых головок.
Способ гидроштамповкироторов разработан Пермским филиалом ВНИИБТ. Прогрессивная безотходная технология гидроштамповки базируется на пластической деформации тонкостенной заготовки (трубы), принимающей под действием наружного давления конфигурацию формирующего стержня. Изготовленный таким способом ротор (см. рис. 11.1, в) отличается повышенной чистотой поверхности и резким снижением массы. Оба эти фактора способствуют повышению долговечности РО.
Производительность способа исключительно высока: весь процесс гидроштамповки, не включая время сборки и разборки пресс-формы, занимает 5-7 мин. Вместе с тем для реализации способа требуются прецизионные трубчатые заготовки и весьма дорогой состав технологического оборудования. Кроме того, имеется ограничение использования способа: рационально изготавливать детали с высотой зубьев до 8-10 мм и числом зубьев
Рис. 11.3. Схема установки микрометра для замера диаметральных размеров ротора
до 7-8. Для упрочнения рабочей поверхности обычно применяется хромирование.
Способ горячей прокаткироторов, разработанный ВНИИ-МЕТМАШ, был внедрен на заводе "Прогресс" при изготовлении роторов двигателей Д1-195 и Д2-195. Этой технологии присущи бесспорные преимущества: высокая производительность (прокатка ротора диной 2300 мм продолжается не более 10 мин) и возможность получения износостойкой детали (высокая твердость и рациональное расположение волокон металла).
Однако, как и предыдущий способ, горячая прокатка роторов рентабельна только при серийном производстве.
Система контроля.Высокая работоспособность ВЗД во многом зависит от точности изготовления РО.
При изготовлении ротора контролируют:
диаметральные размеры выступов и впадин винтовой поверхности ротора (микрометром) (рис. 11.3);
прямолинейность оси детали (на инструментальном столе);
профиль поперечного сечения (сравнение с эталонным профилем на инструментальном микроскопе);
осевой шаг (индикатором).
В зарубежной практике используются компьютезированные методы контроля размеров РО.
Дата добавления: 2018-02-18; просмотров: 1298; Мы поможем в написании вашей работы! |
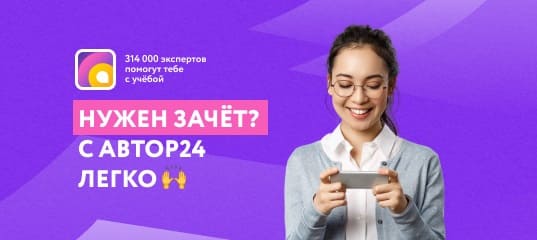
Мы поможем в написании ваших работ!