Расчет турбины турбопривода УТДУ
Для параметров спроектированного турбопривода были проведены расчеты осевой одноступенчатой активной турбины мощностью 720 кВт (9 сопловых вставок) и турбины мощностью 80 кВт (1 сопловая вставка) при перепаде на турбине (1,2 МПа/0,6МПа).
Исходные данные:
Частота вращения:
Входное полное давление: Па
Выходное полное давление: Па
Входная температура торможения: К
Свойства газа:
Газовая постоянная:
Показатель изоэнтропы:
Средний диаметр турбины Dср=640 мм
Основные данные, полученные в расчете для соплового аппарата с 9 сопловыми вставками (мощность турбины: Вт.
mг=13,137 кг/с | Cад=450,529 м/с | ω=314 |
NТ=722900 Вт | U=100 м/с | Pоо=1200000 Па |
η=0,542 | Dср=640,1 мм | P2=600000 Па |
ε=0,479 | Hл=31,2 мм | Tоо=300 К |
Основные данные, полученные в расчете для соплового аппарата с 1 сопловой вставкой (мощность турбины: 80000 Вт).
mг=2,252 кг/с | Cад=450,548 м/с | ω=314 |
NТ=79500 Вт | U=100 м/с | Pоо=1200000 Па |
η=0,348 | Dср=640,1 мм | P2=600000 Па |
ε=0,046 | Hл=47,2 мм | Tоо=300 К |
Расчеты на прочность и колебания элементов турбопривода.
Первый вариант конструкции турбопривода показан на рис. 8.1.
Рис. 8.1.Турбопривод.
Основные элементы турбопривода:
1 – посадочные места под опоры в корпусной детали 2;
2 – корпусная деталь турбопривода;
3 – диск турбины;
4 – корпус соплового аппарата;
5 – сопловая вставка;
6 – область определения максимальных, эквивалентных напряжений.
|
|
Все расчеты производился в среде Solid Works Simulation 2009 и Solid Works Simulation 2010 [6,7].
Расчет корпуса сопловых вставок
При расчете эквивалентных напряжений в корпусе сопловых вставок были заданы основные исходные данные:
1. максимальный, статический перепад давления на корпусной части соплового аппарата - 40×105 Па;
2. конструкция соплового аппарата должна обеспечивать дискретное изменение парциальности простыми и надежными методами.
На основании этого было принято решение о применении конструктивной схемы соплового аппарата с 10 сопловыми вставками. Такая схема позволяет изменять парциальность в диапазоне от 0.55 (для 10 рабочих лопаточных сопловых вставок) до 0.055, с одной рабочей сопловой вставкой, (в остальные 9 установочных мест устанавливаются заглушки). При расчете соплового аппарата было принято допущение о том, что сопловые вставки (и заглушки) не являются несущими элементами всей конструкции соплового аппарата, при определении напряжений в нем от воздействия заданного статического перепада давления.
Начальный внешний вид корпуса сопловых вставок, для моделирования соплового аппарата, представлен на Рис. 8.2.
Так как сопловой аппарат является телом вращения, в дальнейшем расчет будет производиться для одной десятой его части (угловой сегмент) (для сокращения времени вычислений).
|
|
Расчеты соплового аппарата производились в два этапа.
Допущением при расчете эквивалентных напряжений являлось следующее условие:
- сопловой аппарат (без вставок) жестко фиксировался по фланцу (глухая заделка по контуру или «фиксированная геометрия») (Поз. 6, рис. 8.1).
Рис. 8.2. Корпус сопловых вставок
При таком условии фиксации фланца и заданной нагрузке, возникали большие напряжения на внутренней границе заделки соплового аппарата и в элементах перемычек (в зоне Поз. 6, рис. 8.1.) (сингулярность - бесконечные напряжения, возникающие при использовании МКЭ). Необходимо отметить, что одна из выше перечисленных задач первого этапа, заключалась в определении геометрии «перемычек» и геометрии других несущих элементов соплового аппарата (из условия допускаемых напряжений). На появление скачков напряжений, при условии «фиксированной геометрии» (не корректная постановка решения задачи), не принималось во внимание. Но при таком допущении достаточно быстро определилась предварительная геометрия, и были решены вопросы собираемости (затрачивалось меньше машинного времени). Первый этап проходил в несколько итераций.
|
|
Основные элементы, используемые для моделирования на втором этапе, показаны на рис. 8.1.
1 – посадочные места под опоры в корпусной детали 2;
2 – корпусная деталь турбопривода;
4 – корпус соплового аппарата;
Переход ко второму этапу с ответной деталью (корпусная деталь турбопривода (деталь 4)) заключался в необходимости определения оптимальных условий моделирования и оптимизации геометрии корпусных деталей. В качестве ответной детали можно использовать значительно более простую деталь (например, ответный фланец), но так как в дальнейшем будет необходимо производить расчет сборки целиком, была применена деталь 4. Расчетная модель с ответной деталью, медной прокладкой и виртуальными болтами имела жесткую фиксацию по посадочным местам подшипников Поз. 1 и 2, рис. 8.1 и рис. 8.3 (зеленые стрелки). Такая фиксация корпусных деталей в дальнейшем возможна (только по наружной поверхности детали 2), но в данном случае такое условие позволяет реализовать максимально возможные напряжения в ответной детали (если моделировать показанную фиксацию детали 2 согласно рис. 8.1, напряжения будут меньше). В данном случае моделируются самые тяжелые условия нагружений.
|
|
Рис. 8.3. Расчетная модель
Между фланцами деталей 2 и 4 установлена медная прокладка. Это позволило сместить сингулярность напряжений в зоне контакта между фланцем соплового аппарата и медной прокладкой на медную прокладку (прокладка - компенсирующий элемент в модели). Модель сопловой аппарат и ответной детали рассчитывалась с условием «не проникновения» и «узел к поверхности» в зоне контакта между деталью 2, медной прокладкой и деталью 4. В расчетную модель введены виртуальные болты. Виртуальные болты позволяют учитывать нормальные напряжения в зоне затяжки. Это упрощает расчетную модель, и уменьшает расчетное время за счет уменьшения контактных поверхностей и большей размерности сетки (при расчете настоящего болта нужна достаточно мелкая сетка, и большее время расчета за счет дополнительных поверхностей соприкосновения: болт-гайка, гайка - сопловой аппарат, болт - ответная деталь, болт – медная прокладка). Момент затяжки виртуальных болтов изменялся в диапазоне 100 - 200 (Н×м).
Распределения напряжений в сопловом аппарате показаны на
рис. 8.4. (вид со стороны подвода рабочего тела).
Рис. 8.4. Распределение напряжений
Материал соплового аппарата – литейная сталь. σ0.2 = 530 МПа. Максимальное напряжение – 357 МПа. Минимальный запас прочности – 1.48. На рисунке видна область напряжений от виртуальных болтов. Момент затяжки виртуальных болтов 150 (Н×м).
На рис. 8.5 показан вид на сопловой аппарат со стороны диска турбины (область максимальных напряжений).
Рис. 8.5. Распределение напряжений
Распределения напряжений в ответной детали и медной прокладке показаны на рис. 8.6. (вид со стороны диска турбины)
Рис. 6. Распределение напряжений
Материал ответной детали – литейная сталь. σ0.2 = 530 МПа. Максимальное напряжение – 357 МПа. Минимальный запас прочности – 1.48. В процессе определения распределений напряжений в модели, проводилось изменение геометрии ответной части из условия одинакового запаса прочности с сопловым аппаратом. Вычисления проводились для различной плотности сетки и уплотнения сетки в зоне максимальных напряжений. На рис. 8.5 и 8.6 видно смещение максимальных напряжений в область медной прокладки.
Рис. 8.7. Распределение напряжений
Рис. 8.8. Распределение напряжений (область сингулярности увеличена)
На рис. 8.7 и 8.8 показано возникновение сингулярности при решении этой же контактной задачи и тех же условий моделирования в случае отсутствия компенсирующего элемента (медной прокладки). На рисунках видна область напряжений, где значения σ0.2 достигает значений 1075 МПа (на внутреннем диаметре фланцевого соединения).
Второй этап проходил так же в несколько итераций. Таким образом, внешний облик корпусных элементов турбопривода был сформирован.
Дата добавления: 2018-02-18; просмотров: 614; Мы поможем в написании вашей работы! |
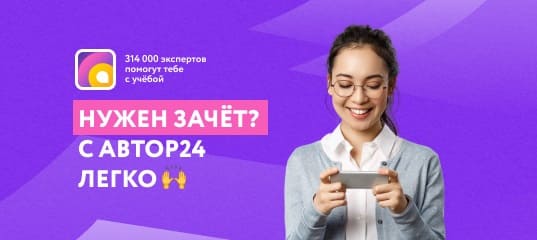
Мы поможем в написании ваших работ!