Назначение и физико-химические свойства покрытий
Покрытие - это слой одного или несколько слоев разных материалов, последовательно нанесенных на поверхность детали, для придания поверхностному слою свойств, отличных от свойств основного материала, например электропроводности, электроизоляционных свойств, твердости, паяемости, износоустойчивости, антикоррозийных свойств, декоративности и т. д.
Покрытия наносят на металлы, керамику, пластмассы толщиной от десятых долей до сотен микрометров. Выбор покрытия и его толщина определяется материалом и назначением детали, особенностями технологии ее изготовления и условиями эксплуатации.
По своему назначению покрытия делятся на защитные, защитно-декоративные и специальные.
Защитные покрытия служат для защиты металлов от коррозии (кадмиевые, цинковые, оловянные и оксидные покрытия). Металлическим деталям свойственна атмосферная коррозия под тонкой пленкой влаги в присутствии кислорода, солей, щелочей и кислот. Степень коррозии для наиболее распространенных металлов приведена в табл. 17, где 0 материал стоек в данной среде; 1 - медленно корродирует; 2 - корродирует; 3 - разрушается.
В таблице 8 выделены металлы, используемые в качестве покрытий.
Таблица 8 - Степень коррозии металлов в среде различных внешних воздействий
Металл | Влажный воздух без солей | Морская вода | ШОН | Н28О4 | НС1 | НЧО |
Сталь углеродистая | 2 | 2 | 0 | 3 | 3 | 3 |
Сталь нержавеющая | 0 | 0 | 0 | 2 | 2 | 2 |
Алюминий | 1 | 2 | 3 | 3 | 3 | 1 |
Бронза оловянистая | 1 | 1 | 2 | 3 | 3 | 3 |
Хром | 0 | 0 | 0 | 1 | 3 | 0 |
Никель | 0 | 0 | 0 | 3 | 3 | 3 |
Кадмий | 0 | 0 | 2 | 3 | 3 | 3 |
Цинк | 0 | 2 | 3 | 3 | 3 | 3 |
Медь | 2 | 2 | 1 | 3 | 3 | 3 |
Латунь | 2 | 2 | 2 | 3 | 3 | 3 |
Свинец | 0 | 1 | 3 | 1 | 2 | 3 |
Олово | 0 | 0 | 3 | 3 | 3 | 3 |
Серебро | 0 | 0 | 0 | 1 | 1 | 3 |
Золото | 0 | 0 | 0 | 0 | 0 | 0 |
Платина | 0 | 0 | 0 | 0 | 0 | 0 |
|
|
Металлические покрытия могут быть анодными по отношению к защищаемому металлу, при этом электродный потенциал покрытия (таблица 9) является более отрицательным по сравнению с электродным потенциалом защищаемого материала и, следовательно, при нарушении покрытия оно должно разрушаться в первую очередь.
При катодном покрытии, наоборот электродный потенциал покрытия является положительным по отношению к электродному потенциалу защищаемого материала, и при его нарушении разрушениям в первую очередь будет подвергаться защищаемый материал.
Металлические покрытия получают, главным образом, гальваническим путем из-за большой производительности и точности толщины пленки.
Пористость анодных покрытий значительно меньше по сравнению с катодными.
|
|
Таблица 9
Металл | Электродный потенциал | Металл | Электродный потенциал |
Магний | -1,55 | Свинец | -0,13 |
Алюминий | -1,30 | Водород | 0,00 |
Марганец | -1,10 | Сурьма | 0,10 |
Цинк | -0,76 | Висмут | 0,20 |
Хром | -0,56 | Мышьяк | 0,30 |
Железо | -0,44 | Медь | 0,34 |
Кадмий | -0,40 | Родий | 0,68 |
Кобальт | -0,26 | Серебро | 0,81 |
Никель | -0,25 | Ртуть | 0,86 |
Олово | -0,14 | Золото | 1,50 |
С другой стороны, контактная разность потенциалов покрытий и материалов определяет их совместимость. Характер взаимодействия различных сочетаний металлов в жестких условиях приведен в таблице 10. Условные обозначения в таблице 10: 0 - коррозия отсутствует, 1 - коррозия слабая, 2 - значительная коррозия.
Таблица 10 - Коррозийностойкость различных сочетаний металов
Металл | Номер металла | ||||||||||||||
1 | 2 | 3 | 4 | 5 | 6 | 7 | 8 | 9 | 10 | 11 | 12 | 13 | 14 | 15 | |
Ag | Х | 0 | 0 | 0 | 0 | 1 | 1 | 0 | 0 | 2 | 2 | 2 | 2 | 2 | 2 |
Au,Pt,Pd | 0 | Х | 0 | 0 | 0 | 1 | 1 | 0 | 0 | 2 | 2 | 2 | 2 | 2 | 2 |
Сталь нержавеющая | 0 | 0 | Х | 0 | 0 | 0 | 0 | 0 | 0 | 1 | 2 | 2 | 2 | 2 | 2 |
Cr | 0 | 0 | 0 | Х | 1 | 0 | 1 | 0 | 0 | 2 | 2 | 2 | 2 | 2 | 2 |
Cu и сплавы | 0 | 0 | 0 | 1 | Х | 0 | 1 | 0 | 1 | 2 | 2 | 2 | 2 | 2 | 2 |
Ni | 1 | 1 | 0 | 0 | 0 | Х | 0 | 0 | 0 | 2 | 2 | 1 | 2 | 2 | 2 |
Sn,Sn-Pb | 1 | 1 | 0 | 1 | 1 | 0 | Х | 0 | 1 | 2 | 1 | 0 | 1 | 1 | 2 |
Ti | 0 | 0 | 0 | 0 | 0 | 0 | 0 | Х | 0 | 2 | 2 | 1 | 2 | 2 | 2 |
Сталь хромистая | 0 | 0 | 0 | 0 | 1 | 0 | 1 | 0 | Х | 2 | 2 | 2 | 2 | 2 | 2 |
Сталь углеродистая | 2 | 2 | 1 | 2 | 2 | 2 | 2 | 2 | 2 | Х | 1 | 2 | 2 | 2 | 2 |
Cd | 2 | 2 | 2 | 2 | 2 | 2 | 1 | 2 | 2 | 1 | Х | 0 | 1 | 1 | 2 |
Оксид Al | 2 | 2 | 2 | 2 | 2 | 1 | 0 | 1 | 2 | 2 | 0 | Х | 0 | 0 | 1 |
Al | 2 | 2 | 2 | 2 | 2 | 2 | 1 | 2 | 2 | 2 | 1 | 0 | Х | 1 | 2 |
Zn | 2 | 2 | 2 | 2 | 2 | 2 | 1 | 2 | 2 | 2 | 1 | 0 | 1 | Х | 1 |
Mg | 2 | 2 | 2 | 2 | 2 | 2 | 2 | 2 | 2 | 2 | 2 | 1 | 2 | 1 | Х |
|
|
Защитно-декоративные покрытия используются для придания деталям декоративного вида с одновременной защитой от коррозии (медь-никель-хром, никель-хром, никель, золото, серебро и др.).
Специальные покрытия служат для придания деталям определенных (новых) физических свойств: твердости, отражательной способности, паяемости, электропроводности с одновременной защитой от коррозии.
Классификация и условные обозначения покрытий
Классификация покрытий по способу нанесения включает: анодное оксидирование - Ан.; покрытия, окрашивающиеся в процессе анодного окисления металла и его сплавов - Аноцвет; покрытия химическим способом - Хим.; горячим способом - Гор.; диффузионным способом Диф.; металлизацией - Мет.; конденсационным (вакуумным) способом - Кон.; контактным способом - Кт.; вжиганием - Вж.; катодным распылением - Кр.; эмалированием - Эм.; плакированием - Пк.
|
|
Неметаллические неорганические покрытия: оксидное - Окс.; хроматное - Хр.; фосфатное - Фос.
Специальные свойства покрытий включают:
твердое - тв.; износостойкое - изн.; электроизоляционное - эиз.; шероховатое - шр.; электропроводное - э.; светостойкое - сс.; пористое - пор.; микропористое - мр.; микротрещиноватое - мт.
Специальные свойства декоративных покрытий:
зеркальное - зк.; блестящее - б.; блестящее из электролита с блесткообразователем - бо.; полублестящее - пб.; матовое - м.; гладкое - гл.; слегка шероховатое - сш.; шероховатое - ш.; весьма шероховатое - вш.; рельефный рисунок - рсч.; кристаллическое - кр.; слоистое - сл.
По ГОСТ 2789-73 степень шероховатости покрытий определяется Ка, мкм: для гладких покрытий - не менее 0,63; для слегка шероховатых 0,63-2,5; для весьма шероховатых - более 20.
Классификация цветных покрытий включает:
хроматирование (Хр.): радужный, желтый, бесцветный, голубой, хаки, зеленый, черный, серый разных оттенков;
тонирование (Тн): хроматический яркий;
химическое или электрохимическое окрашивание (Хим.окр или Элх.окр): черный, коричневый, красный, зеленый различных оттенков;
анодное окисление трех разновидностей:
1) Аноцвет - черный, коричневый, зеленый разных оттенков, голубой;
2) наполнение органическими красителями (цвет красителя): непрозрачный, молочный, хроматический яркий;
3) эматалирование (ЭМТ): молочный непрозрачный эмалевый вид, легко окрашиваются органическими красителями.
Для обозначения покрытий и способа их нанесения принята буквенно-цифровая система:
- для металлических покрытий буквы указывают металл покрытия, цифра после буквы его толщину в микрометрах (мкм) и буквы в конце определяют его характеристики или характер дополнительной обработки. Цвет покрытия записывается в конце обозначения полностью, исключая черный (ч). Примеры записи покрытий : Хим. Н6; Х.мол.9 ч; М60-С(60)3; Аноцвет зеленый; Кд. 15.хр.; Диф.Ц и т. д.;
- для лакокрасочных покрытий (лкп) указывают вид покрытия, тип красителя, цвет и нормативную документацию, например: Эмаль.АС182, голубая. ГОСТ 19024 - 73.
Характеристики и основные свойства покрытий
Металлические покрытия
Цинковоепокрытие (серебристо-белое) имеет среднюю твердость, выдерживает гибку и развальцовку, сохраняется при свинчивании. Оно непригодно для деталей, работающих на трение, плохо выдерживает запрессовку и термообработку, пайку и сварку. На воздухе покрывается белым налетом окиси цинка, неухудшающим свойства покрытия. Более надежно цинковое покрытие с хроматированием (цвет радужный с зеленоватым,желтым или золотистым оттенками). Предельная рабочая температура Тпред = 250 о С.
Кадимиевое покрытие (серебристо-белое) применяется для морских условий, обладает высокой эластичностью, выдерживает пайку и сварку, хорошо сохраняется в резьбовых соединениях. Эти покрытия применяют для деталей из стали, меди и ее сплавов, требующих плотной сборки (притираемости) с одновременной защитой от коррозии; они более дорогостоящи. Кадмиевые покрытия нельзя применять для среды с сернистыми соединениями, а также в закрытых объемах с деталями, пропитанными олифой и высыхающими маслами. Кадмий токсичен!
Никелевое покрытие (серебристо-белый цвет с желтоватым оттенком) применяют для защитной и декоративной отделки деталей из стали, меди и алюминия, а также контактных пружин и токопроводящих деталей из меди и медных сплавов. Эти покрытия выдерживают гибку и запрессовку, но отслаиваются при клепке и развальцовке. Легко полируются. Твердость средняя. Покрытие катодно по отношению к железу, поэтому необходима его беспористость или применение многослойных покрытий.
Хромовое покрытие (серебристо-белого цвета с синеватым оттенком) применяют для защитно-декоративной отделки и повышения износостойкости деталей. Покрытие не тускнеет при нагревании до 500 оС. На воздухе хром покрывается невидимой пленкой, увеличивающей стойкость покрытия. Твердость составляет 500-1000 НВ. Из-за пористости электролитического хрома обычно используют многослойные покрытия. Наименьшей пористостью и максимальной эластичностью обладает молочный хром, прочно сцепляющийся со сталью. Детали оптических приборов покрывают износостойким черным хромом. Для коррозийной защиты обычно используют подслои никеля и меди.
Покрытие ПОС обладает хорошим сцеплением с основным металлом, эластичностью и химической стойкостью в обычной и морской атмосферах. Покрытие хорошо паяется, выдерживает гибку, вытяжку, развальцовку, штамповку, свинчивание, наносится обычно по гальваническим покрытиям цинка, никеля и меди.
Покрытие белой бронзой применяют как защитно-декоративное, а также вместо серебрения для СВЧ-трактов, хорошо паяется. Покрытие по внешнему виду похоже на серебряное, не тускнеет под действием сернистых соединений, отличается большим сопротивлением коррозии, по твердости уступает хрому, но лучше никеля. При толщине более 10 мкм поры отсутствуют.
Серебряное покрытие применяется для токонесущих контактирующих деталей, работающих при трении, для трактов СВЧ, монтажных шин и проводов, требующих пайки. Обладает высоким коэффициентом отражения, хорошо паяется с использованием слабоактивных флюсов и полируется, но тускнеет под воздействием сернистых соединений (контакт с эбонитом и резиной). Для декоративной отделки покрытие оксидируют в черный цвет.
Золотое покрытие легко подвергается износу и истиранию, но устойчиво по отношению к кислотным, щелочным и сернистым соединениям.
Неметаллические покрытия
Фосфатирование представляет собой простой и экономичный способ защиты от коррозии черных металлов (не фосфатируются только нержавеющие стали). Фосфатная пленка (7-50 мкм) имеет хорошую адгезию и электроизоляционные свойства, которые улучшаются при пропитке лаками. Она является хорошим грунтом под многие лакокрасочные покрытия, устойчива к топливам, маслам, бензину, толуолу и многим газам, но нестойка в кислотах, щелочах, морской воде, сероводороде и атмосфере водяного пара. Фосфатные пленки не смачиваются расплавами олова, свинца и цинка.
Чаще всего применяют химическое фосфатирование, как наиболее простой технологический процесс. Электрохимическое фосфатирование используют для металлов, не взаимодействующих с ортофосфорной кислотой. Химическое фосфатирование применяют для цинковых и кадмиевых покрытий, магния и его сплавов, алюминия и его сплавов. Для повышения защитных свойств фосфатных пленок их обрабатывают в растворах хрома (У1), бихроматах калия (натрия), промасливают веретенным или авиационным маслом, гидрофобизируют кремнийорганическими соединениями.
Оксидирование - получение оксидных пленок на металле. Такие пленки имеют хорошие декоративные свойства и защищают от коррозии. Оксидирование осуществляют химическим и электрохимическим методами. В первом случае пленка, полученная в растворе хромового ангидрида, бесцветна и сохраняет блеск полированного алюминия. Пленка, полученная электрохимическим способом в растворе серной кислоты, имеет снежно-белый цвет, высокую твердость, износостойкость и электроизоляционные свойства. После пассивирования в растворе хромпика приобретает лимонно-желтый цвет. Возможно окрашивание оксидированного алюминия анилиновыми красителями. Пленка прочно сцепляется с алюминием и служит хорошим грунтом для лакокрасочных покрытий. Покрытие устойчиво при эксплуатации внутри помещений в умеренном и тропическом климате. При эксплуатации в атмосфере при тех же климатических условиях применяют окисное хроматированное покрытие с лакокрасочным покрытием.
Химическое оксидирование медных сплавов применяют для декоративной отделки деталей, не имеющих паяных швов и соединений. Цвет пленки - от темно-фиолетовой до сиреневой. Для увеличения стойкости покрытие промасливают.
Химическое оксидирование стали применяют для защиты от коррозии и декоративной отделки деталей, не имеющих паяных швов. Цвет черный с синеватым или коричневым оттенками. Варианты: а) погружение в раствор каустической соды и натриевой селитры; б) воронение (500 оС); в) погружение в расплав натриевой селитры; г) обдув горячим воздухом или перегретым паром. Толщина пленки 0,6-10 мкм.
Пассивирование металлических покрытий осуществляется путем химической или электрохимической обработки в соответствующих растворах.
Дата добавления: 2018-02-18; просмотров: 1148; Мы поможем в написании вашей работы! |
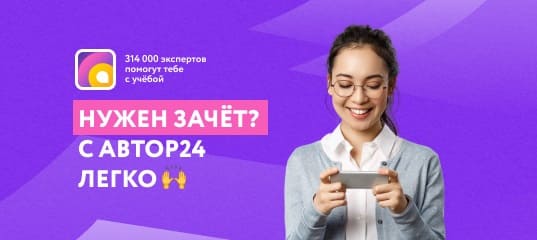
Мы поможем в написании ваших работ!