Точность механической обработки. Суммарная погрешность. Система СПИД. Виды погрешностей.
Под точностью обработки следует понимать степень соответствия действительного значения показателя к номинальному.
Точность геометрических параметров является комплексным понятием, включающим в себя:
— точность размеров элементов деталей;
— точность геометрических форм поверхностей элементов деталей;
— точность взаимного расположения элементов деталей;
— шероховатость поверхностей деталей (микрогеометрия);
— волнистость поверхностей (макрогеометрия).
Повышение точноти исходных заготовок снижает трудоемкость и с/c обработки мех обработки, снижает значения припусков, приводит к экономии металла.
Точность детали зависит от ряда факторов:
-отклонение от геом. формы детали или ее отд. элементов.
-отклонение действительных размеров детали от номинальных
-отклонение поверхностей и осей деталей от точного взаимного расположения (от параллельности, перпендикулярности, концентричности)
Т.к. точность обработки в произ-ых условиях зависит от многих ф-ров, обработку на станках ведут не с достижимой, а с экономической точностью.
Эк.точность мех. обработки – такая точность, при кот. min с/c обработки достигается в нормальных произ-ых условиях (работа произ-ся на исправных станках с применением необх-ых приспособлений и инструментов при нормальных затратах времени и нормальной эксплуатации рабочих) Достижимая точность – точность, кот. можно достичь при обработке в особых наиб. благоприятных усл., необходимых для данного произ-ва высококвалифицированными рабочими при значительном увеличении затрат времени, на считаясь с с/c обработки.
|
|
СПИД: станок, приспособление, инструмент, деталь.
Суммарная погрешность измерения – это совокупность погрешностей, возникающих под влиянием большого числа факторов.
Погрешности: теоретичские, погрешн., вызваные действием упругой силы СПИД, погрешности, вызванные деформацией заготовки под действием неуравновешенных сил, из-за действия тепла, из-за износа режущего инструмента, погрешность базирования
Методы образования форм
С использованием механизма станка
1.токарная обработка (точение): черновое, получистовое, чистовое, тонкое. Процесс формообразования на токарных станках осуществляется при вращательном главном движении, сообщаемом обрабатываемой заготовке, и при прямолинейном (поступательном) движении подачи, сообщаемом резцу.
2. шлифование: предварительное, чистовое, тонкое. Обработка происходит с помощью круглошлифовальных, плоскошлиф-ых, бесцентрово-шлиф-ых станков
3.отделочная обработка: хонингование, доводка (тонкая притирка), суперфиниширование, полирование. 4.обработка давлением: обкатывание, выглаживание, накатывание. При обработке цилиндрических поверхностей применяют как обычные станки, так и с числовым программным управлением (ЧПУ)
|
|
С использованием фасонного инструмента.
Фасонными резцами обрабатывают на токарных станках обычно фасонные поверхности небольшой длины методом врезания.
Наиболее широкое применение находят строгание, фрезерование, протягивание и шлифование.
Обработку можно производить различными методами на различных станках - строгальных, долбежных, фрезерных, протяжных, токарных, расточных, многоцелевых, шабровочных и др.
Комбинированый метод – совместное использование первых двух методов (напряжение резьбовой поверхности в токарном станке).
Размерообразование
Разметкой называется операция нанесения на обрабатываемую поверхность детали или заготовки разметочных рисок, определяющих контуры профиля детали и места, подлежащие обработке. Основное назначение разметки заключается в указании границ, до которых надо обрабатывать заготовку. Для экономии времени простые заготовки часто обрабатывают без предварительной разметки.
Применяют различные способы разметки: по чертежу, шаблону, образцу и по месту. Выбор способа разметки определяется формой заготовки, требуемой точностью и количеством изделий. Точность выполнения разметки в значительной мере влияет на качество обработки. Степень точности разметки колеблется в пределах 0,25 — 0,5 мм.
|
|
При обработке деталей необходимую точность и требуемые размеры можно достичь различными методами.
Обработка по разметке или с использованием пробных проходов путем последовательного приближения к заданной форме и размерам; после каждого прохода инструмента контролируют полученные размеры и решают, какой еще припуск необходимо снять; точность в этом случае зависит от квалификации рабочего;
Метод пробных ходов заключается в индивидуальной выверке устанавливаемой на станок заготовки, последовательной обработке и измерении небольших участков поверхности.
После уточнения по результатам измерений положения режущего инструмента производят окончательную обработку поверхности. Данный метод требует высокой квалификации рабочего и большей трудоемкости, применяется в единичном и реже — в мелкосерийном производстве.
Обработка методом автоматического получения размеров, когда инструмент предварительно настраивается на нужный размер, а затем обрабатывает заготовки в неизменном положении; в этом случае, точность зависит от квалификации наладчика и способа настройки ;
|
|
Метод автоматического получения размеров производительнее метода пробных ходов, требует специальных приспособлений и более стабильных по размерам исходных заготовок и широко используется в серийном и массовом производстве. В этом случае от рабочего не требуется наблюдение за процессом и внесение нужных коррекций. Опвышене точноести, снижение брака, точность обработки не зависит от толщины снимаемой стружки.
автоматическую обработку на копировальных станках и станках с числовым программным управлением (ЧПУ), где точность зависит от точности действия системы управления.
Дата добавления: 2018-02-15; просмотров: 838; Мы поможем в написании вашей работы! |
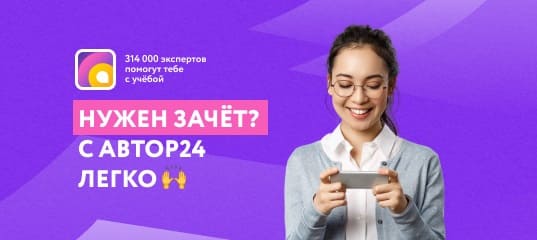
Мы поможем в написании ваших работ!