Міністерство освіти і науки України Національний транспортний університет
Міністерство освіти і науки України
Національний транспортний університет
Методичні вказівки
до виконання курсового проекту
з навчальної дисципліни «Процеси і
апарати у виробництві будівельних матеріалів»
Для підготовки фахівців освітньо – кваліфікаційного рівня
«бакалавр» освітнього напрямку «Будівництво»
за спеціальністю 7.092104 –
«Технологія будівельних конструкцій, виробів і матеріалів».
«Затверджено»
на засіданні навчально
- методичної ради
Національного транспортного
Університету
Протокол №___________ від
«___»_______________2009р.
Київ НТУ 2009
Методичні вказівки для виконання курсового проекту з навчальної дисципліни «Процеси і апарати у виробництві будівельних матеріалів» для студентів за напрямом підготовки «Будівництво» за спеціальностю 6.092104 «Технологія будівельних конструкцій, виробів і матеріалів».
К.: НТУ, 2008 - ________________ с.
Укладачі: В.В. Кожушко, к.т.н.
В.В. Мозговий, д.т.н.
А.Л. Юнак,
О.В. Марченко,
Б.Ю. Ольховий,
О.С. Кирієнко.
|
|
___________________________
___________________________
Рецензент __________________
___________________________
Зміст
Зміст. 3
Вступ. 4
1. Вимоги до виконання курсового проекту. 5
2. Процеси і апарати для подрібнення матеріалів. 5
2.1 Машини для дроблення матеріалів. 5
2.1.1 Щелепні дробарки. 5
2.1.1.1 Розрахунок щелепної дробарки (варіант 1) 5
2.1.1.2 Розрахунок щокової дробаки (варіант 2) 7
2.1.2 Конусні дробарки. 9
1.2 Машини для помолу матеріалів. 16
1.2.1 Кульові млини. 16
2.2.2 Кільцеві млини. 19
2.3 Машини для розділення сипучих матеріалів. 21
2.3.1 Розрахунок хитного гіраційного грохоту(варіант1) 24
2.3.2 Розрахунок хитного гіраційного грохоту(варіант 2) 28
2.3.3 Вібраційні грохоти. 30
2.4 Машини для висушування матеріалів. 33
2.5 Машини для змішування матеріалів. 35
2.6 Машини для зберігання та дозування сипучих матеріалів. 36
2.7 Теплові процеси і апарати. 48
3. Алгоритм розрахунку теплообмінних апаратів. 58
Додатки. 65
Додаток А1. 66
Додаток А2. 67
Додаток А3. 68
Додаток А4. 69
Додаток Б. 71
Додаток В.. 89
Додаток Г. 90
|
|
Додаток Д.. 90
Додаток Е. 91
Додаток Є.. 92
Додаток Ж.. 92
Додаток З. 93
Додаток К.. 93
СПИСОК ЛІТЕРАТУРИ.. 94
Вступ
Курсовий проект (КП) виконується в термін, передбачений учбовим планом. Результатом виконання КП є набуття навичок проектування технологій та апаратів будівельного виробництва, методів їх розрахунків.
Мета курсового проекту:
- систематизація, закріплення і розширення теоретичних знань з дисципліни «Будівельні матеріали та вироби» та «Процеси і апарати у виробництві будівельних матеріалів».
- одержання студентами навичок розрахунку основних параметрів технологічних процесів в умовах виробництва
При розробці проекту особливу увагу необхідно приділити розрахунку процесів і апаратів, охороні навколишнього середовища, зниження трудових, паливно – енергетичних ресурсів, випуску продукції (відповідно ТУ, ДСТУ) повної заводської готовності і застосування прогресивних рішень у технологіях виробництва.
Загальні положення
Завдання курсового проекту – полягає у поглибленні теоретичних положень лекційного курсу, оволодіння практичними навичками інженерних розрахунків і аналізу отриманих результатів, що дозволить самостійно визначитись у процесах і апаратах що використовуються у будівельному виробництві
|
|
Методичні вказівки містять вихідні дані і порядок виконання курсової роботи, що дозволяє студентам виконувати їх під час самостійної роботи.
1. Вимоги до виконання курсового проекту
Курсовий проект складається із розрахунково – пояснювальної записки обсягом 30-60 сторінок тексту та графічного матеріалу на двох листах формату А1 і А2.
В залежності від завдання проектування на першому листі розміщують технологічну схему. Другий лист – основний апарат в двох проекціях.
2. Процеси і апарати для подрібнення матеріалів
2.1 Машини для дроблення матеріалів
Машини для дроблення називають дробарками. У хімічній технології застосовують здебільшого щелепні, конусні, валкові та молоткові дробарки.
2.1.1 Щелепні дробарки
Щелепні дробарки широко застосувують для крупного і середнього дроблення.
Дроблення у щелепних дробарках відбувається між рухомою і нерухомою щелепами у результаті роздавлювання шматків матеріалу, який надходить у завантажувальний отвір. Подрібнений матеріал вивантажується під час відходу рухомої щелепи.
Усі типи щелепних дробарок можна класифікувати за такими конструктивними ознаками: за характером коливання рухомої щелепи (із простим і складним коливанням щелепи); за методом підвісу рухомої щелепи (з верхнім і нижнім підвісом рухомої щелепи); за конструкцією урухомника (дробарки із шарнірно-важільним і роликовим механізмами).
|
|
Основні параметри, що характеризують щелепну дробарку, — це розміри завантажувального і розвантажувального отворів. Продуктивність щелепних дробарок коливається від 1 до 500 т/год.
2.1.1.1 Розрахунок щелепної дробарки (варіант 1)
Одна з важливих характеристик щелепної дробарки — кут захоплення а. Це найбільший кут між рухомою і нерухомою щелепами, що забезпечує нормальне дроблення й унеможливлює виштовхування нагору шматка матеріалу. Розглянемо умову рівноваги шматка матеріалу кулястої форми (рис. 2.1):
(2.1)
де Р — зусилля роздавлювання матеріалу; — коефіцієнт тертяматеріалу по плиті;
— кут тертя. З умови рівноваги
(2.2)
Рис. 2.1 Рис. 2.2
Визначення обертової частоти ексцентрикового вала.Позначимо найменшу ширину випускного отвору — а, ахід щоки S (рис. 2.2). За один період коливання щелепи з дробарки випаде матеріал у вигляді прими трапецеїдального перетину. Час відходу щелепи:
(2.3)
де 2п — кількість повних коливань щелепи.
Шлях, пройдений шматками між щелепами дробарки:
(2.4)
де ; g— прискорення вільного падіння, м/с2.
З огляду на тертя, що гальмує вільне випадіння шматка, одержимо робочу обертову частоту:
(2.5)
Продуктивність.За один оберт ексцентрикового вала з дробарки випадає об'єм (див. рис. 2.2).
(2.6)
деb — ширинащоки.
Тоді об'ємна продуктивність, м3/год
(2.7)
де — коефіцієнт розпушення матеріалу. Підставивши значення об'єму, одержимо:
(2.8)
де dср = 0,5(2a + S) — середній діаметр шматка матеріалу,що випадає з дробарки.
Потужність, потрібну для подрібнювання, визначають за допомогою формули процесу дроблення, кВт,
(2.9)
де E — модуль пружності матеріалу, МН/м2; д = 0,2...0,3 — ККД для щелепної дробарки;
ур — ККД урухомника.
2.1.1.2 Розрахунок щокової дробарки (варіант 2)
Необхідно визначити основні параметри щокових дробарок, до яких відносяться: кут захоплення дробарки α; частота хитання рухливої щоки Z, розміри камери дроблення.
Розміри камери дроблення визначаються розміром матеріалу, що подрібнюється. Ширина завантажувального отвору А і середній діаметр найбільш великих кусків dnповинні бути у співвідношенні dn/А=0,80-0,85. Ступінь роздрібнювання матеріалу у щокових дробарках знаходиться в межах
(2.10)
Довжина завантажувального отвору для дробарок із простим хитанням щоки і L= (1,2-1,4)A; зі складним L=(1,4-3,5)A. Висота робочої частини рухомої щоки
(2.11)
Кут захоплення залежить від коефіцієнта тертя f матеріалу, що дробиться, по сталі ( плиті щоки).
На кусок матеріалу, затиснутий між двома щоками (рис. 2.3) діє сила виштовхування R що являє собою рівнодіючу стискаючих сил Р: (R=2Р sin α/2) і утримуючі сили N, що є проекціями сил тертя F на вісь, рівнобіжну напрямку сили R: (N=Fсоs α/2).
Рис. - 2.3 Схема дії сил на матеріал
Куски матеріалу залишаться в камері дроблення за умови, якщо 2N ≥ R чи Рf соs α/2 ≥ 2Р sin α/2, звідси
(2.12)
Коефіцієнт тертя f часто виражають через кут тертя φ, тобто f = tgφ, тоді α ≤ 2φ. Коефіцієнт тертя кам'яних матеріалів по сталі f=0,3, при цьому φ=16°, а α=33° У роботі кут захоплення для кам'яних матеріалів приймається α= 17-25°. Для розрахунків α=20°
Число хитань рухливої щоки і частоти обертання привідного валу. При роботі дробарки рухлива щока фіксує два крайніх положення 1 і 2 (рис. 2.4)
Рис. 2.4 Схема для визначення продуктивності дробарки
Хід щоки дорівнює S. При русі щоки з положення 2 у положення 1 відбувається стискання і дроблення матеріалу, а при русі в зворотному напрямку матеріал висипається з дробарки під дією власної ваги. Оптимальні значення ходів стискання у верхній і нижній точках камери дроблення можуть бути знайдені за експериментальними залежностями:
- для дробарок зі складним рухом щоки
(2.13)
(2.14)
- для дробарок з простим рухом щоки
(2.15)
(2.16)
де В та в - розміри прийомного отвору і вихідної щілини, мм.
Обсяг матеріалу, що висипається, приблизно відповідає добутку площ заштрихованого контуру (рис. 2.4) на довжину завантажувального отвору Для цього необхідно, щоб час відходу щоки з положення 1 у положення 2 відповідав часу висипання матеріалу з висоти призми h. Якщо ексцентриковий вал робить п оборотів у секунду, а час відходу щоки дорівнює часу половини обороту, то t = 0,5/n.
З рисунку 2.4 випливає, що h = Sн/tgα і h=gt2/2. Прирівнявши значенню h і зробивши відповідні перетворення, одержимо
(2.17)
Продуктивність щокових дробарок (м3/с) визначається за умови, що розвантаження матеріалу з вихідної щілини відбувається тільки при відході рухливої щоки і що за один оборот ексцентрикового вала з камери випадає деякий об'єм V (м3) матеріалу
(2.18)
де п - частота обертання ексцентрикового валу, с-1;
Кр - коефіцієнт розпушення матеріалу, Кр = 0,35-0,45.
Підставивши обсяг матеріалу, обчислений за відповідними параметрами, одержимо
(2.19)
Виходячи з умов дроблення потужність електродвигуна щокових дробарок (кВт):
- з простим рухом щоки
(2.20)
- зі складним рухом щоки
(2.21)
де L,H- довжина і висота камери дроблення, м;
Sн - хід стискання в нижній зоні камери, м;
Кк - конструктивний коефіцієнт, КК - 0,55-0,6;
r - ексцентриситет вала, м.
2.1.2 Конусні дробарки
Конусні дробарки застосовують для дроблення всіляких порід, за винятком в'язких і дуже твердих.
У конусних дробарках шматки матеріалу роздавлюються між зовнішнім і внутрішнім конусами у результаті натискання внутрішнього конуса на матеріал. Конус при цьому переміщається по коловій траєкторії, коливаючись щодо нерухомої точки (гірації). Під час зближення конусів матеріал дробиться, а під час віддалення — вивантажується. Конусні дробарки класифікують за такими ознаками:
а) технологічним призначенням: дробарки крупного дроблення (Dcp = 0,3... 1,5 м; dср = 0,05...0,2 м, де Dcp, dср — середній розмір відповідно завантажуваного і вивантажуваного шматка); дробарки середнього дроблення (Dcp = 0,075...0,3 м; с/ср = 0,015...0,05 м); дробарки дрібного і середнього дроблення (Д.р = 0,03...0,075 м; dср = 0,003...0,015 м);
б) конструктивним оформленням: дробарки з підвішеним валом, дробарки ексцентрикові, дробарки з консольним валом.
Кут захоплення дробарки з крутим конусом визначають так само, як і для щелепної дробарки (рис. 2.5):
(2.22)
Визначення обертової частоти рухомого конуса.У конусній дробарці з крутим конусом за один оберт випадає об'ємматеріалу, який до того був між двома конусами (рис. 2.6, 2.7).
|
Рис. 2.5 Рис. 2.6
Рис. 2.7
Висоту шару матеріалу, що випадає здробарки, визначають так:
(2.23)
де S1+ S2 = S.
Шлях матеріалу, що вільно випадає,
(2.24)
де t= .
З огляду на тертя між шматками матеріалу і конусом остаточноодержимо
(2.25)
де S = 2r 1,3dср; r — ексцентриситет, м.
Щоб визначити обертову частоту конусної дробарки з положистим конусом, розглянемо поводження матеріалу в зоні паралельності (рис. 2.8).
Рис. 2.8
Силу, що рухає матеріал Р, визначають так:
(2.26)
де С = тg; т— маса шматка; а — прискорення руху шматка. Розв'язуючи рівняння (2.13) щодо прискорення, одержуємо
(2.27)
Тоді шлях шматка, що дорівнює довжині зони паралельності, визначають так:
(2.28)
Розв'язуючи рівняння (2.14) щодо обертової частоти п, одержуємо
(2.29)
де — кут між твірною і основою рухомого конуса,
= 40...45°;f - коефіцієнт тертя; L = 0,08dн; dн— нижній діаметр рухомого конуса, м (рис. 2.9).
Рис. 2.9
Визначення продуктивності.Площу перерізу об'єму, що випадає,для дробарки зкрутим конусом визначають (див. рис. 2.7) так:
(2.30)
За один оберт випадає об'єм матеріалу
(2.31)
де — коефіцієнт розпушення матеріалу; D1 =Dн— нижній діаметр нерухомого конуса.
Масова продуктивність
(2.32)
де лінійні розміри виражено в метрах.
Для дробарки з положистим конусом
(2.33)
Тоді
(2.34)
Потужність дробарок визначають за формулою (2.10), якщо д =0,2.. .0,3.
Молоткові дробарки
Молоткові дробарки застосовують для подрібнювання крихких матеріалів з невеликою вологістю.
Подрібнювання в молотковій дробарці відбувається внаслідок:
—удару швидкообертових молотків безпосередньо по шматках матеріалу й удару шматків один об один;
—удару матеріалу об дробильні плити;
—подрібнювання матеріалу між молотками і броньовими плитами;
—подрібнювання матеріалу між молотками і колосниками.
На підставі конструктивних ознак молоткові дробарки поділяють за кількістю роторів на однороторні і двороторні, за способом кріплення молотків — із жорстко закріпленими і шарнірно підвішеними молотками, за розміщенням молотків — однорядні й багаторядні. Продуктивність молоткових дробарок залежно від розмірів машини і шматків, що надходять до неї, ступеня подрібнювання і твердості матеріалу коливається в межах від 3 до 250 т/г.
Розрахування параметрів ротора.Довжина молотка
(2.35)
де Dр — діаметр ротора, м.
Швидкість молотка після удару визначають з рівняння динамічної рівноваги (рис. 2.10):
(2.36)
де V1 — колова швидкість центра ваги молотка після удару, м/с; М0 — маса молотка, кг; ІA — момент інерції ротора, кгм2; т— маса максимального розміру шматка подрібнюваного матеріалу, кг; z— кількість молотків; сої — кутова швидкість молотка після удару, 1/с; VК = (R+ l1) к— колова швидкість центра ваги до удару, м/с; Vшм— швидкість шматка подрібнюваного матеріалу у напрямку колової швидкості ротора
За вертикального завантаження Vшм = 0.
Розрахування продуктивності молоткової дробарки.Продуктивність молоткової дробарки визначають за емпіричною формулою, т/г,
n – обертова частота,с-1
(2.37)
де Dр — діаметр ротора, м; Lр — довжина ротора, м; п — обертова частота, сч.
|
Визначення потужності молоткової дробарки.У молотковій дробарці потужність витрачається на відновлення енергії, що втрачають молотки під час ударів по шматку матеріалу (N1) і стирання подрібнюваного матеріалу на колосникових ґратах (.N2).
Потужність, потрібна для відновлення енергії, втраченої молотками під час ударів по шматку матеріалу, кВт,
(2.38)
Кінематична енергія, втрачена молотком під час ударів по шматку подрібнюваного матеріалу, Нм,
(2.39)
де V`y1 =(R+ l1 +l2`) 0 — швидкість молотка до моменту удару (у точці удару), м/с; l1 — відстань від осі обертання молотка до осі центра ваги, м; l2`— відстань від осі центра ваги молотка до точки удару,м;
(2.40)
— маса середнього за продуктивністю шматка подрібнюваного матеріалу, що припадає на один молоток, кг.
Рис. 2.10
Відстань
(2.41)
де Lм — довжина робочої частини молотка;
(2.42)
Середнє значення глибини проникнення матеріалу (точки зіткнення); - мінімальна глибина проникнення,
- максимальна глибина проникнення.
|
Маса молотка, зведена до точки удару, кг:
(2.43)
де — полярний момент інерції молотка щодо ротора.
Полярний момент інерції елемента молотка щодо власного центра ваги
(2.44)
де і0— полярний момент інерції молотка щодо осі, що проходить через центр його маси; т'0 — маса елемента молотка; а — відстань від осі, що проходить через центр маси молотка, до осі, що проходить через центр маси елемента.
Потужність, споживана на стирання подрібнюваного матеріалу на колосникових ґратах, кВт,
(2.45)
Робота, витрачена всіма молотками на стирання на колосникових ґратах, Нм,
(2.46)
де - відцентрова сила шматка подрібнюваного матеріалу:
; (2.47)
- швидкість маси шматка подрібнюваного матеріалу;
(2.48)
- відстань від осі ротора до центра тяжіння шматка подрібнюваного матеріалу, м;
(2.49)
- розмір шматка масою т0, м;
(2.50)
f0 — коефіцієнт тертя матеріалу по металу; zзаг— загальна кількість молотків; Lкол — потрібна довжина колосникових ґрат, м.
Споживана на дроблення потужність
(2.51)
1.2 Машини для помелу матеріалів
1.2.1 Кульові млини
Кульові млини призначені для топкого помелу матеріалів. Матеріал у млині подрібнюється ударом молотильних тіл, а також стиранням під час їх перекочування.
Кульові млини класифікують за такими ознаками:
—за принципом роботи (періодичної і неперервної дії);
—за характером роботи (що працюють у відкритому і закритому циклах);
—за способом помелу (сухого і мокрого помелу);
—за формою робочого барабана (циліндричні, конічні і трубні);
—за способом розвантаження (з механічним і пневматичним розвантаженням);
—за конструкцією завантажувального і розвантажувального пристрою (з центральним завантаженням і розвантаженням через пустотілу цапфу; із розвантаженням через торцеві грати; з периферійним розвантаженням через ґрати, завантаженням і розвантаженням через люк у барабані).
У промисловості застосовують переважно млини неперервної дії, що працюють у відкритому чи замкненому циклі, сухим чи мокрим способом.
Теорія роботи кульових млинів.Основні характеристики млина — продуктивність і питома витрата енергії. Вони залежать від фізико-механічних властивостей матеріалу, розміру шматків, заданого ступеня подрібнювання, конструктивних особливостей, способу живлення, розмірів барабана і молотильних тіл, кількості обертів барабана.
Розгляньмо три можливі види руху куль залежно від кількості обертів барабана.
Під час повільного обертання млина кулі з подрібнюваним матеріалом піднімаються до кута природного укосу і потім скочуються вниз (рис. 2.11, а). Зерна матеріалу перетираються між кулями, перетворюючись па тонкий порошок. Якщо обертання швидше (рис. 2.11, б), кулі під впливом відцентрової сили, що притискає їх до стійки млина, піднімаються вгору і під впливом сили тяжіння каскадом падають па матеріал і кулі в нижній частині млина. При цьому матеріал подрібнюється не тільки тертям між кулями, але і за рахунок удару. Максимальній швидкості падіння куль відповідає найбільша енергія, використовувана для подрібнення матеріалу. Продуктивність млина в цьому разі найбільша.
Подальше збільшення колової швидкості зумовлює виникнення відцентрових сил, що перевищують сили тяжіння куль. Тоді кулі, притиснуті до футерівки, будуть переміщатися разом з нею (рис. 2.11, в), і подрібнювання матеріалу в млині припиниться. Колову швидкість, за якої кулі перестають відриватися від футерівки, називають критичною.
На рис. 2.12, а подано характерну картину помелу ійого параметри, де А — точка відриву, у якій зовнішній шар відривається від футерівки; — кут відриву, кут між радіусом відриву і вертикальною віссю; R0 — радіус редукованого шару куль; h — висота підйому куль.
Обертова частота.На кулю в точці відриву (рис. 2.12, б) діють сила тяжіння кулі G і відцентрова сила інерції І.
Рис. 2.11
Рис. 2.12
Сила інерції спрямована по радіусу під кутом підйому α. Швидкість обертання барабана визначають з умови рівноваги радіальної складової сили тяжіння і відцентрової сили інерції.
Умова, за якої куля буде притиснута до стінки відцентровою силою, така:
(2.51)
де m – маса кулі, кг; V=pDn – колова швидкість кулі, м/с; R1= D/2 – радіус обертання кулі чи відстань від центра млина до центра тяжіння кулі, м.
Максимального свого значення сила інерції набуває, коли кут α = 90°, sin α = 1. Для цього випадку з рівняння (2.51) критична кількість обертів
(2.52)
Для помелу сухих матеріалів оптимальна кількість обертів.
(2.53)
Під час мокрого способу помелу волога послабляє удар куль, і в цьому випадку потрібно брати більшу оптимальну кількість обертів:
(2.54)
Продуктивність. Продуктивність кульових млинів залежить від таких чинників: розмірів млина, їх конструкції, схеми помелу, способу і регулярності завантаження, крупності матеріалу, вологості матеріалу, тонкості готового продукту.
Щоб визначити сприятливі умови роботи млинів і розрахувати їх продуктивність було проведено дослідні роботи, на підставі яких вивели формули для обчислення продуктивності. Найбільш достовірна для практичних цілей формула, запропонована В. В. Алявдіним й уточнена ДІПРО-цемент:
(2.55)
де Пр— продуктивність млина для заданої тонкості помелу, т/г; V— внутрішній об'єм млина; м3; D0 — внутрішній діаметр млина, м; Mм.т— маса завантажених молотильних тіл, т; Qс — питома продуктивність млина під час розмелу матеріалу, узятого за еталон, яка дорівнює 40 кг/год. на 1 кВт/год. енергії, витраченої на підйом куль у млині; Кμ— коефіцієнт помелоспроможності матеріалу, що дорівнює 0,5...4,0; ήп— коефіцієнт, що характеризує відносну ефективність помелу в певних умовах; у — залишок розмеленого матеріалу па ситі № 009, %; у0 — залишок вихідного матеріалу на ситі № 009; т — показник степеня, що залежить від властивостей матеріалу й умов розмелу; т=- 0,8... 1,2.
Потужність двигуна урухомника барабанного млина з урахуванням маси подрібнюваного матеріалу (зазвичай Ммат = 0,14Мм.т), кВт,
(2.56)
де ήп— ККД урухомника.
Маса завантажених молотильних тіл, кг:
(2.57)
де — коефіцієнт заповнення млина; μ = 0,65 — коефіцієнт розпушення завантажених куль; ρ = 7800 кг/м3 — об'ємна маса матеріалу куль; R — внутрішній радіус, м; L — довжина камери млина, м.
2.2.2 Кільцеві млини
Кільцеві млини застосовують для розмелу матеріалу середньої твердості чи м'яких матеріалів. Робочі органи — кільце і ролики, що притискаються до нього, чи сталеві кулі. Матеріал, що потрапляє між кільцем і роликом, залежно від їх форми тільки роздавлюється чи одночасно роздавлюється і стирається. Залежно від конструкції роликові млини поділяють на ролико-маятникові, із пружинним натиском роликів, відцентро-вокульові, пружинні з обертовим вертикальним кільцем.
Щоб визначити співвідношення між розмірами кільця роликів і шматків подрібнюваного матеріалу розглянемо шматок матеріалу, захопленого роликом (рис. 2.13). Матеріал не буде буксувати між кільцем і роликом тільки за умови затягування шматка: . Звідки
чи
.
За теоремою косинусів для АВС маємо:
(2.58)
Підставивши значення сторін, дістанемо
(2.59)
Звідки
(2.60)
Рис. 2.13
Виразивши cos2α через tgα, одержимо:
(2.61)
Значення tgα має бути меншим за значення f , тобто
(2.62)
Розв'яжемо щодо Rср:
(2.63)
Розв'язок для Rср вибираємо зі знаком мінус:
(2.64)
оскільки за f= 0 і позитивного значення кореня Rср = R-r, що суперечить фізичному змісту, бо, якщо немає тертя, шматок не буде затягуватися між роликом і кільцем. За негативного кореня f= 0 маємо Rср = 0, що відповідає фізичному змісту. У роликових кільцевих млинах радіус ролика коливається в межах
Центральний кут кола ролика, що відповідає дузі між лініями зіткнення ролик — шматок і ролик — кільце, рад,
Зусилля стискання матеріалу між роликом, що обертається, і кільцем, НМ,
|
(2.65)
|
де — межа міцності матеріалу на стискання, МПа
Обертова частота вертикального вала, с-1,
(2.66)
де G – сила тяжіння ролика, Н.
Продуктивність млина, т/год:
(2.67)
де Кц — коефіцієнт, що враховує кратність циркуляції матеріалу у млині; Vр — колова швидкість ролика, що дорівнює швидкості обертання на радіусі від центра вертикального вала до кільця, м/с; b — ширина ролика, м; h — товщина шару матеріалу під роликом, м; — об'ємна маса матеріалу, Т/м3; z — кількість роликів.
Потужність, споживана млином, витрачається:
— на подолання тертя кочення ролика по матеріалу, Вт:
(2.68)
де μ — коефіцієнт опору коченню ролика;
— на подолання сил тертя, спричинених проковзуванням ролика, Вт:
(2.69)
деf— коефіцієнт тертя валка об матеріал; Vквз — швидкість ковзання,
рекомендовано брати Vкт = (0,095.. .0,098) Vрол;
— на подолання сил тертя в підшипниках вала маятника з роликом, Вт:
(2.70)
де fквз — коефіцієнт, що враховує ковзання; прол— обертова частота ролика, с
2.3 Машини для розділення сипучих матеріалів
Просіювання матеріалів
Механічне сортування (просіювання) виконують за допомогою машин з пристроями для просіювання. Застосовують просіювання, щоб одержати два чи декілька сортів зерен, що різняться крупністю. Кількість одержуваних сортів залежить від кількості решіт (сит), через які було пропущено оброблюваний матеріал. Якщо застосувати п решіт, то виходить (п + 1) сорт матеріалу.
Просіювання буває самостійне, коли отриманий матеріал — це готова продукція для споживача, проміжне, коли продукти і падалі подрібнюють, і допоміжне — для виділення дрібних фракцій, наявність яких у матеріалі зменшує продуктивність устаткування.
Послідовність механічного сортування матеріалу залежить від розміщення сит і решіт. Розрізняють три схеми розміщення решіт: «від дрібного до крупного», «від крупного до дрібного», комбінована схема.
Просіювання вихідного матеріалу за схемою «від дрібного до крупного» починають з решета із найменшими отворами, продовжують на решетах із щораз більшими отворами і закінчують на решеті з найбільшими отворами (рис. 2.14).
Рис. 2.14
Розміщені за цією схемою сита зручно ремонтувати, а також знімати з них готовий продукт. Однак якість просіювання погіршується через стирання крупного матеріалу.
У схемі просіювання «від крупного до дрібного» верхнє сито маєнайбільші отвори, а нижнє — найменші (рис. 2.15).
|
Рис. 2.15
Недоліки схеми — велика висота установлення і вузький фронт розвантаження сортів.
У процесі просіювання за комбінованою схемою суміш надходить спочатку на решето з отворами середнього розміру. Шматки, які пройшли через отвори в першому решеті, надходять на розміщене під ним решето із найменшими отворами, тоді як шматки великих розмірів надходять на друге решето із найбільшими отворами (рис. 2.16). Ця схема поєднує в собі недоліки і переваги двох перших схем.
Рис.2.16
Усі частинки матеріалу, що пройшли через отвори в ситі, являють собою продукт нижнього класу, а всі частинки великого розміру, що не пройшли через сито, — продукт верхнього класу.
Показником ефективності сортування може слугувати відношення кількості продукту нижнього класу, отриманого у процесі просіювання, до фактичної кількості частинок у вихідному. Звідси коефіцієнт якості просіювання:
(2.71)
|
де А1 — кількість частинок нижнього класу, що пройшли через сито; А — кількість частинок нижнього класу у початковому продукті.
Коефіцієнт якості просіювання чи ККД грохоту залежить від конструкції установки, її кінематики, гранулометричного складу матеріалу, вологості матеріалу.
Пристрої для механічного сортування матеріалу називають грохотами. Грохоти поділяють:
—за принципом дії (на нерухомі і рухомі);
—за орієнтацією в просторі (на похилі і горизонтальні);
—за видом руху робочих органів (на обертові, хитні, гіраційні і вібраційні);
—за видом поверхонь для просіювання (плоскі листові, дротяні і колосникові, а також барабанні).
2.3.1 Розрахунок хитного гіраційного грохоту(варіант1)
Гіраційні грохоти — це машини, у яких поверхня для просіювання робить коловий плоскопаралельний рух.
Розрахунок швидкостей грохота. Розгляньмо умову підкидання шматка матеріалу на поверхні для просіювання (рис. 2.17). Аналіз схеми дії сил показує, що в квадрантах І і IV матеріал може підкидатися вгору, у І і II — рухатися вправо, у III і IV — вліво. Запишемо умови підкидання:
(2.72)
тобто нормальна складова сили інерції, що дорівнює Isinγ, більша від
тобто нормальна складова сили інерції, що дорівнює /зіпу, більша від нормальної складової сили тяжіння частинки G. Підставивши значення сили інерції, одержимо
(2.73)
де r – радіус кривошипа; γ – кут розміщення кривошипа.
Максимальна висота підкидання буде, якщо γ=900, тобто sinγ=1, і з попередньої формули дістанемо:
(2.74)
Рис. 2.17
Умова руху матеріалу вниз
(2.75)
Розв’язуючи цю умову для випадку, коли γ=0, тобто cosγ=1, одержимо розрахункову залежність для визначення швидкості
(2.76)
Умова руху матеріалу вгору
(2.77)
дає значення швидкості
(2.78)
Потужність урухомника грохота витрачається на подолання сил тертя в цапфах, зумовленого силами інерції і силами тяжіння. Робота сил тертя в цапфах
(2.79)
де М – маса завантаженого грохота; ώ – обертова частота вала урухомника; r – ексцентриситет; rц – радіус цапфи.
Потужність урухомника, кВт:
(2.80)
де ή – ККД урухомника.
На рис. 2.14 наведено схему нестійкої конструкції грохота. Різновид традиційних грохотів — грохоти па похилих гнучких стояках (рис. 2.18).
Рис. 2.18
Розрахування швидкостей грохота.Умова підкидання матеріалу (рис. 2.18) звідки
(2.81)
Якщо матеріал рухається вправо,
Тоді швидкість
(2.82)
Якщо матеріал рухається вліво,
Тоді швидкість (2.83)
Для зрівноважування грохотів стояки защемляють жорстко, роблячи їх пружинними. Зрівноважування грохота на похилих пружинних, жорстко затиснених стояках зводиться до розрахунку цих стояків на міцність (рис. 2.19).
Рис. 2.19
Вимоги до розрахунку стояка:
—стояк має працювати на ділянці пружних деформацій за умови
(2.84)
|
- сила інерції; М — маса завантаженого грохоту; ώ, r – відповідно обертова частота і радіус кривошипа; і – кількість стояків;
зрівноважування визначають за певної обертової частоти. Розрахунок стояка подібне розрахунку пружинної опори. Стояк розглядають як дві консольні балки з величиною прогину.
(2.85)
де l — довжина стояка ;
— момент інерції перерізу стояка.
Згинальний момент
(2.86)
де [σ] — межа міцності на згинання;
- момент опору.
Вибирають співвідношення розмірів a/b=x, що дорівнює 8…12. У результаті розв`язання наведених вище рівнянь одержимо значення розмірів стояка (b, a, l).
Потужність урохомника витрачається:
- на надання кінетичної енергії хитним масам
(2.87)
- на деформацію стояків
(2.88)
Оптимальна продуктивність грохотів — це максимальна продуктивність грохота за заданого коефіцієнта корисної дії. За методом транспортера масова продуктивність
(2.89)
де V— швидкість переміщення насипного вантажу з максимальним розміром шматка по поверхні, через яку просіюють
(2.90)
де Dср — розмір нижньої фракції; α — кут нахилу сита; μ — коефіцієнт розпушення матеріалу на ситі.
2.3.2 Розрахунок хитного гіраційного грохоту(варіант 2)
Вихідні дані:
- продуктивність Q, т/год.(за продуктивністю дробарки);
- найбільша крупність зерен, що просіюються, dk, мм;
- кут нахилу сита α ;
- розмір отвору грохоту d0=-dk,, мм;
- ексцентриситет ĺ мм;
Зміст і порядок виконання
До основних параметрів грохоту, які необхідно розрахувати, відносяться: частота обертання грохоту п, с-1; розміри грохоту В,L; потужність N
Частота хитань грохоту й ексцентриситет приводного валу є важливими технологічними характеристиками, що визначають відносну швидкість W руху матеріалу по ситу, продуктивність грохоту, споживану потужність.
Для похилих грохотів частота повних хитань
(2.91)
Для плоских хитних грохотів частота хитань (частота обертання ексцентрика)
(2.92)
де f- коефіцієнт тертя між ситом і матеріалом. Для кускових кам'яних матеріалівf=0,58;
α - кут нахилу сита. Для промислових грохотів кут α прийнятий 2-4°;
l - ексцентриситет приводного валу, l=7—13 мм.
Розміри грохоту. Продуктивність грохоту оцінюється кількістю матеріалу, який пройшов через нього за одиницю часу, т/год.;
(2.93)
де В - ширина шару матеріалу (ширина грохоту), м;
d - товщина шару матеріалу, м; приймається рівною діаметру найбільших кусків dк;
ρн - насипна щільність матеріалу, кг/м3;
µ- коефіцієнт розпушення матеріалу, який рухається на ситі, µ=0,6-0,7;
W- відносна швидкість руху матеріалу на ситі, м/с, W = f (d0 r, α),
d0=dk діаметр отвору сита, м;
r- радіус куска матеріалу, що просіюється, м.
Щоб зерна проходили через отвори сита того ж розміру, тобто d0=2r, відносну швидкість руху матеріалу на ситі визначають з рівняння:
(2.94)
Після розв'язання рівняння (2.93) відносно В знаходять ширину грохоту.
Довжина грохоту L впливає на затрачувану на просіювання потужність. Зі збільшенням довжини грохотів збільшується витрата енергії на подолання тертя. Тому довжина грохоту L визначається тривалістю перебування матеріалу на ситі до необхідного поділу фракцій.
Споживана грохотом потужність витрачається на надання масам, що рухаються, кінетичної енергії Nk і на подолання опору тертя матеріалу по ситу грохоту Nm Отже,
(2.95)
Потужність, затрачувана на надання масам, що рухаються, кінетичної енергії, кВт,
(2.96)
де Р=Р2+РМ - вага рухливої маси грохоту Р2 і матеріалу РM
Вагу матеріалу на грохоті знаходять виходячи з геометричних параметрів шару: Рт = ВLdkρH
Вагу рухливої частини гуркоту Р2 визначають конструктивним рішенням грохоту. Приймемо для розрахунку Р2=0,5РM.
(2.97)
У такий спосіб
(2.98)
2.3.3 Вібраційні грохоти
У вібраційних грохотах коливання сита зумовлюють динамічні фактори— інерційні, ударні чи електромагнітні сили. Вібраційний грохот має такі особливості:
—траєкторія сита визначається динамічними факторами;
—амплітуда коливань змінна.
Залежно від конструкції пристрою, що спричиняє вібрації сита, вібраційні грохоти поділяють на інерційні, ударні, електричні.
Вібраційні інерційні грохоти застосовують для класифікації порошків. Інерційний грохот відрізняється від гіраційною конструкцією механізму, який забезпечує вібрацію рухомого жолоба, установленого на пружинах
Ефективність просівання, %:
(2.99)
де С — зміст фракцій нижнього класу у вихідному материалі, %; А — маса відібраної проби верхнього продукту просівання, кг; А1 — маса проби верхнього продукту після відсівання з неї зерен нижнього класу, кг.
Значення Е можна визначити і як середнє значення з розсіву не менш трьох проб, відібраних у різний час роботи грохота:
(2.100)
де l – еталонне значення ефективності просівання; К1 – коефіцієнт, що враховує кут нахилу грохота; К2 – коефіцієнт, що враховує відсотковий уміст нижнього класу у вихідному матеріалі; Кт, — коефіцієнт, що враховує відсотковий уміст у нижньому класі зерен, менших за половину розміру отворів сита. Продуктивність грохота, м3/год.:
(2.101)
де т — коефіцієнт, що враховує можливу нерівномірність живлення і зернового складу матеріалу, форму зерен і тип грохота (для горизонтального грохота т = 0,8...0,65; для похилого т = 0,5...0,6); g— питома продуктивність сита площею 1 м; F— площа сита, м; К'1,К'2,K'3 — коефіцієнти, фізичне значення яких відповідає коефіцієнтам з формули (2.3). Потужність, споживана інерційним грохотом, кВт:
(2.102)
де f — зведений коефіцієнт тертя кочення підшипників, що дорівнює 0,01...0,0025; т — маса дебаланса, кг; п— обертова частота вала, с-1; r — відстань від центра ваги неврівноваженої частини дебаланса до осі обертання, м; d— діаметр цапфи вала, м; ή — ККД грохота.
Розрахувати вібратор. На систему (рис. 2.20) діють сили тяжіння вібрувальних мас М та інерції дебаланса, радіус якого r0 і маса т. На одну пружину (якщо грохот чотирипружинний) діє зусилля, що дорівнює M g/ 4, і сила інерції I/4.
Навантаження на пружину від дії сили тяжіння
Рис. 2.20
(2.103)
де а — статичне осідання, м; k — жорсткість, Н/м.
Період вільного коливання грохота
(2.104)
Період вимушеного коливання грохота
(2.105)
де п — обертова частота дебаланспого вала. Під час резонансу
Підставивши значення а з рівняння (2.94), одержимо значення жорсткості пружини для умов резонансу:
(2.106)
За цією жорсткістю підбирають пружини.
Значення жорсткості пружини з умови дії сил інерції
(2.107)
де k — половина амплітуди коливання системи; т— маса дебалансу; r0 — радіус дебалансу.
Звідки
(2.108)
З рівності співвідношень випливає
(2.109)
що дозволяє розрахувати масу дебалансу.
2.4 Машини для висушування матеріалів
Розрахунок барабанної сушарки
Вихідні дані:
- продуктивність вихідного матеріалу Gп, кг/год;
- вологість матеріалу (на загальну масу), %;
- початкова, Wn;
- кінцева ,Wk;
- температура матеріалу, °С;
- початкова, tn;
- кінцева, tм
- температура повітря, °С;
- на вході в калорифер при φ=50 %, t0;
- на виході з калорифера (вході в барабан);
- на виході з барабану , t2;
- насипна щільність матеріалу, ρн, кг/м3 ;
- напруга барабана по вологості, А, кг/м3 ·год;
Барабанні сушарки застосовуються для сушіння сипучих зернистих матеріалів. Сушарка (рис. 2.21) являє собою порожній циліндричний сталевий барабан, на якому встановлюються бандажі і вінцева шестірня. Барабан встановлюється бандажами на опорні ролики під кутом 0,5-6°.
Завантажувальний кінець барабана за допомогою ущільнювальних пристроїв з'єднується з топкою або калорифером, з якого надходять топочні гази або нагріте повітря. Завдяки внутрішній насадці барабану матеріал багаторазово пересипається з певної висоти. Топочні гази, змішуючись у спеціальній камері з атмосферним повітрям, що має визначену температуру, надходять у барабан і, проходячи уздовж нього, висушують матеріал, що пересипається.
У процесі розрахунку необхідно визначити: продуктивність барабана по вологості; розміри сушильного барабана; число обертів барабана.
Продуктивність барабана по вологості. Кількість вологи, що випаровується за годину, кг:
(2.110)
Рис 2.21 Схема сушильної установки: 1 - барабан; 2- прийомний бункер; 3- циклон; 4- бункер; 5- калорифер; 6- вентилятор.
Кількість матеріалу, висушеного за годину, кг:
(2.111)
Розміри сушильного барабана: - об'єм барабана, м3
(2.112)
Відношення довжини барабана до діаметра повинне бути L/d=3,5-7. Звичайно приймають відношення L/d=5;
- діаметр барабана знаходять із співвідношення, м
(2.113)
- довжина барабана, м
(2.114)
Остаточні розміри барабана вибирають по додатку 3. Приймають розміри, рівні розрахованим або близькі до них з більшої сторони. Число обертів барабана в секунду
(2.115)
де а - коефіцієнт для підіймально-лопатевої насадки, α=1,2;
τ - час перебування матеріалу в барабані, с,
(2.116)
де ρн - середня насипна щільність матеріалу, кг/м3; В - коефіцієнт заповнення барабана, В = 0,15; Gср - середня маса матеріалу, що проходить через барабан, кг/год.; tgα - тангенс кута нахилу барабана.
Барабани мають кут нахилу до обрію (по горизонталі) 0,5-6°.
2.5 Машини для змішування матеріалів
Теоретичні основи процесу
Змішування застосовують для усереднення матеріалу за вологістю і гранулометричним складом, створення сталої в об'ємі і часі температури хімічної реакції.
Мета змішування визначається процесом, для якого його призначено. Змішування можна виконувати механічним, пневматичним, мішаним (комбінованим) способами.
Механізми для змішування називають мішалками та змішувачами. Мішалки застосовують для змішування рідин, сипучих матеріалів, пластичних мас.
Класифікація мішалок. Для змішування рідин застосовують: лопатеві, пропелерні, турбінні, пневматичні, планетарні та інші мішалки.
Для змішування сипучих матеріалів застосовують: лопатеві змішувачі, z -подібні, гвинтові, барабанні мішалки.
Для змішування пластичних мас використовують гвинтові, дискові, черв'ячні, комбіновані змішувачі.
Оскільки всі механічні змішувачі мають робочі органи типу лопатей, а лопатеві мішалки застосовують для змішування рідин і сипучих матеріалів, то є сенс розглянути розрахунок лопатевої мішалки.
Пропелерні мішалки
Пропелерні мішалки застосовують для інтенсивного змішування малов'язких рідин.
Робочий орган мішалок — звичайний гребний гвинт з 2—4 лопатями, який створює горизонтальний і вертикальний потоки рідини. Кут нахилу до осі обертання змінний, унаслідок чого створюється вертикальний потік рідини.
Конструктивні розміри: діаметр пропелера дорівнює 0,25...0,33 діаметра посудини; обертова частота— 1,50... 10,0 с-1 (для в'язких рідин) та 7...25 с-1 (для малов'язких рідин).
Потужність пропелерної мішалки витрачається на подолання опору рідини, а також на подолання тертя пропелера у рідині, її визначають за формулою, кВт:
(2.117)
де D — діаметр кола, описаний крайньою точкою лопаті; п — складна функція, яка залежить від кратності змішування рідини, за хвилину, об'єму рідини, змішуваної за хвилину, і кроку гвинта:
(2.118)
де К — кратність змішування рідини за секунду; V — об'єм змішуваної рідини, м3; - кут підйому гвинтової лінії.
2.6 Машини для зберігання та дозування сипучих матеріалів
Великі потоки насипних вантажів у хімічній промисловості потребують створення парку найефективніших машин, приладів і споруд для механізації та автоматизації операцій з ними. Обов'язкова частина таких споруд — бункерні установки, які слугують проміжними резервуарами і пересипними лійками технологічних установок.
Бункерні установки складаються з таких частин: завантажувальні пристрої, спускні лотки і труби, пристрої для зважування, несучі та будівельні конструкції.
Найбільш подібні до бункерів за формою та експлуатаційними характеристиками пересипні лійки, півбункери й силоси. Пересипні лійки відрізняються від бункерів розмірами і зазвичай не мають затворів. Півбункери відрізняються від бункерів малою глибиною порівняно з розмірами в плані; розміщають півбункери найчастіше неглибоко, на поверхні завантажувальної площадки.
Силосами називають резервуари з вертикальними стінками, які застосовують для довгострокового зберігання насипних вантажів. Силоси (рис. 2.22) відрізняються від бункерів (рис. 2.23) більшою висотою порівняно з розмірами в плані.
Рис. 2.22 Рис. 2.23
Властивості насипних вантажів
Вибір конструкцій окремих елементів бункерних установок і визначення їх параметрів залежить від властивостей насипних вантажів, для яких призначена установка. Характерні властивості насипних вантажів — гранулометричний склад (крупність частинок), вологість, об'ємна (насипна) та питома маса, рухливість та зв'язність частинок, злежуваність, змерзання, опір переміщенню відносно твердих поверхонь, липкість, абразивність, корозійність тощо.
Гранулометричним складом насипного вантажу називають кількісний розподіл частинок, які складають вантаж, за їх крупністю. Крупність частинок визначається їх найбільшим розміром а.
Розрізняють насипні вантажі сортовані та рядові. Сортованими називають вантажі, у яких відношення розмірів найбільших атах до розмірів найменших amin кусків не перевищує 2,5. Якщо таке співвідношення більше 2,5, то насипний вантаж називають рядовим.
Більшість параметрів елементів бункерних установок визначають залежно від розміру типових кусків для певного насипного вантажу. Для сортованих вантажів під розміром типового куска розуміють розмір середнього куска, тобто
(2.119)
Для рядових вантажів розмір типових кусків визначають порізному, залежно від маси групи найбільших кусків.
Насипні вантажі залежно від розмірів типових кусків поділяють на категорії, мм:
крупнокускові — аТ >160;
середньокускові — 60 < аT < 160;
дрібнокускові — 10 < аТ < 60;
крупнозернисті — 2 < аТ < 10;
дрібнозернисті — 0,5 < аТ < 2;
порошкоподібні — 0,05 < аТ < 0,5;
пилоподібні — аТ < 0,05.
Вологу в насипних вантажах поділяють на такі різновиди:
—хімічно зв'язана з речовиною волога;
—гігроскопічна волога, яку частинки вантажу вбирають з навколишнього повітря;
—зовнішня волога, яку поділяють на плівкову чи молекулярну вологу, що утворює плівки на поверхні частинок, та гравітаційну вологу, яка заповнює пори між частинками насипного вантажу.
Насипні вантажі, які містять лише хімічно зв'язану вологу, називають сухими. Вантажі, які містять гігроскопічну вологу, називають повітряно-сухими, ті, що містять зовнішню вологу, — вологими. Якщо зовнішня волога міститься у вигляді плівок, які обволікають частинки вантажу, такий вантаж називають вогким, за наявності гравітаційної вологи — мокрим.
Вологість насипного вантажу розраховують за формулою
(2.120)
де G1, G2 — маса матеріалу відповідно до і після просушування у сушильній шафі.
Об'ємною масою сипучого тіла називають масу одиниці об'єму, яку воно займає. Розрізняють об'ємну масу вільного насипу та об'ємну масу ущільненого насипного вантажу.
Коефіцієнт динамічного ущільнення Кущ визначається як співвідношення об'ємної маси ущільненого матеріалу ρущ до об'ємної маси вільно насипаного матеріалу ρ0, тобто
(2.121)
Приблизне середнє значення коефіцієнта динамічного ущільнення можна визначити за формулою
(2.122)
де f — коефіцієнт внутрішнього тертя.
Насипні вантажі за об'ємною масою бувають: легкі — 0,6 т/м3, середні— 0,6... 1,1, важкі— 1,1...2, надзвичайно важкі — від 2 та вище.
Маса насипного вантажу — це середня маса твердих частинок, що складають його. Для визначення маси насипного вантажу в скляну посудину насипають порцію сухого вантажу, наливають рідину, яка змочує, але не розчинює частинок вантажу, ретельно перемішують і визначають об'єм утвореної суспензії. Об'ємну масу рв визначають за формулою
(2.123)
де Gсв — маса порції сухого насипного вантажу; Vсс, Vрд — об'єми відповідно суспензії та рідини.
Рухливість частинок насипного вантажу. Насипні вантажі належать до категорії сипучих тіл. Сипучі тіла відрізняються від рідин тим, що їх частинки обмежено рухливі через значні сили тертя, причому ці сили тим більші, чим вищий тиск у товщі насипного вантажу. На рис. 2.24 лінія ас показує залежність найбільшого граничного дотичного напруження т від нормальної напруги стискання о в сипучому тілі. Кут нахилу лінії ас до осі абсцис φσ — це кут внутрішнього тертя насипного вантажу, а тангенс цього кута — коефіцієнт внутрішнього тертя f.
Рис. 2.24
Коефіцієнт внутрішнього зрушення характеризує силу зчеплення частинок вантажу між собою:
(2.124)
де τ0 — початковий опір зрушенню.
Насипні вантажі, які не мають початкового опору зрушенню (τ0 = 0), називають легкосипучими. Вантажі, що володіють початковим опором зрушенню то, називають важкосипучими.
Коефіцієнт внутрішнього тертя практично постійний як під час ущільнення вантажів, так і під час їх зволоження. Лише якщо вміст вологи близький до повного насичення пор, коли насипний вантаж уже на грані переходу в суспензію, коефіцієнт внутрішнього тертя різко знижується внаслідок появи великої кількості вільної (гравітаційної) вологи, що відіграє роль змащення.
Рухливість легкосипучих вантажів характеризується також кутом природного укосу. Кутом природного укосу називають найбільший кут, що може утворити вільна поверхня сипучого тіла з горизонтальною площиною (кут а0, рис. 2.25, а).
Для легкосипучих вантажів кут природного укосу дорівнює куту внутрішнього тертя і не залежить від способу формування укосу.
Рис. 2.25
Значення та
можна визначити так (рис. 2.26):
(2.125)
(2.126)
Рис. 2.26
Кут насипу (див. рис. 2.25, б) а можна взяти рівним куту внутрішнього тертя φσ та визначити за формулою
(2.127)
Кут обвалення (рис. 2.25, б) визначають за формулою
(2.128)
Бункери
Класифікація бункерів.За формою бункери бувають:
—прямокутні, пірамідальні, з вертикальними стінками, комбіновані;
—круглі (конічні, циліндричні, циліндро-конічні, циліндро-сферичні);
—коритоподібні;
—призматичні і параболічні.
За розміщенням у просторі розрізняють бункери: підвісні, підземні, заглиблені в грунт.
За матеріалом, з якого виготовлені бункери, їх поділяють на металеві, залізобетонні, дерев'яні і комбіновані.
Стікання насипних вантажів з отворів бункерів.Кожен бункер у нижній частині має отвір, з якого витікає матеріал під час вивантаження. Витікання буває гідравлічне, нормальне і мішане.
Якщо матеріал суцільною масою витікає з бункера, це гідравлічний вид витікання (рис. 2.27). Нормальний вид витікання (рис. 2.28) — коли матеріал у вигляді стрижня над отвором рухається в бункері. Комбінація нормального і гідравлічного — мішаний вид витікання (рис. 2.29).
Рис. 2.27 Рис. 2.28 Рис. 2.29
Швидкість гідравлічного витікання
(2.129)
де X. — коефіцієнт витікання; к — висота шару матеріалу над випускним отвором. Швидкість гідравлічного витікання не залежить ні від розміру кусків матеріалу, ні від розміру отворів.
Швидкість нормального витікання
(2.130)
Гідравлічний радіус отвору витікання
(2.131)
де F — площа поперечного перерізу отвору; П — його периметр. З урахуванням розмірів типових кусків вантажу атмаємо:
— для круглого отвору
(2.132)
— для прямокутного отвору з розмірами (А*В)
(2.133)
— для квадратного отвору з розмірами (А*А)
(2.134)
|
Швидкість витікання важкосипучих матеріалів залежить від критичного радіусу витікання:
(2.135)
Якщо R> Rкр, швидкість витікання
(2.136)
(2.137)
Якщо R> Rкр,
Коефіцієнт λ має значення:
а) для сухих дрібнозернистих матеріалів:
б) для кускових та крупнозернистих:
в) для пилоподібних матеріалів:
Для вивантаження матеріалів через бічні поверхні бункерів вищенаведені формули використовують з sinα (α — кут нахилу до горизонту днища бункера в зоні випускного отвору).
Утворення склепіння.Утворення склепіння насипних вантажів над випускним отвором бункерів надзвичайно шкідливий фактор.
Розрізняють два види:
—утворення склепіння крупнокускових вантажів, коли випадкова комбінація великих шматків матеріалу в процесі витікання утворює стійке склепіння над отвором;
—утворення склепіння дрібнофракційних вантажів, частинки яких зв'язані між собою.
Поява стійких склепінь в останньому випадку пояснюється тим, що зв'язане сипуче тіло в зоні вільної поверхні може мати великі напруги стискання в площинах, нормальних до вільної поверхні, у той час як у площинах, дотичних до вільної поверхні, напруги дорівнюють нулеві.
Якщо випускний отвір більший за отвір утворення склепіння, то стійке склепіння не може утворитися, і витікання вантажу відбувається безперешкодно. Розмір отвору в разі утворення склепіння визначають з рівняння
(2.138)
де Rск — гідравлічний радіус отвору в разі утворення склепіння.
Основний засіб боротьби з утворенням склепіння — правильно вибрати розміри випускного отвору.
Внутрішня поверхня стінок бункера в зоні випускного отвору має бути гладкою без виступних частин. Виступні деталі і шорсткість стінок можуть спричинити виникнення склепінь.
Якщо з конструктивних міркувань випускний отвір бункера менший, ніж розрахований отвір утворення склепіння, то над отвором утворюються склепіння. Для руйнування склепінь застосовують різні способи:
—шурувальні операції;
—нанесення ударів по стінках бункерів;
—надання бункеру коливального руху.
Пропускну спроможність бункерів неперервної дії вимірюють кількістю тонн насипного вантажу, що може пройти через випускний отвір за одиницю часу:
(2.139)
де V — швидкість витікання насипного вантажу з отвору бункера; ρ — об'ємна маса; F— площа отвору витікання.
Пропускна спроможність бункерів, які спорожнюються з кожним відкриттям затвора, характеризується часом їх спорожнення tсп, с:
(2.140)
де G0 — ємність бункера, т.; W— ємність бункера, м3.
Тиск на стінки бункерів. Тиск вантажу на стінки бункерів залежить від властивостей цього вантажу і від конфігурації бункерів. Для стаціонарних бункерів з вантажами, які за властивостями близькі до рідини, тиск на стінки визначають за формулою
(2.141)
де h — глибина розташування місця на стінці під рівнем матеріалу, для якого визначається нормальний тиск.
Для пересувних, переносних і транспортних бункерів тиск обчислюють за формулою
(2.142)
де kд— поправковий коефіцієнт, що враховує динамічність навантаження, його визначають за формулою
(2.142)
де j — найбільше прискорення вертикальних коливань посудини, що містить напіврідкий вантаж.
У процесі наповнення бункера насипним вантажем глибоко розміщені шари матеріалу вертикально переміщаються відносно вертикальних стінок. У результаті цього на поверхні зіткнення сипучого тіла зі стінками бункера виникають спрямовані вертикально дотичні напруження. Тому розподіл тисків буде відрізнятися від гідростатичного закону, і тим більше, чим більшою буде глибина занурення порівняно з поперечним розміром.
Загальний вираз для нормального тиску о на вертикальні стінки має такий вигляд:
(2.143)
де ε — коефіцієнт, який враховує вертикальні сили тертя насипного вантажу об стінки бункера, «коефіцієнт зависання»; п — коефіцієнт бокового тиску.
Коефіцієнт бокового тиску вважають рівним коефіцієнтові рухомості т, який визначають за Формулою
(2.144)
де φσ – коефіцієнт внутрішнього тертя.
Для легкосипучих вантажів
Коефіцієнт є визначають залежно від значення добутку
(2.145)
де f1, — коефіцієнт тертя насипного вантажу об стінки посудини; Rδ — гідравлічний радіус бункера:
(2.146)
Тиск легкосипучих вантажів на похилі стінки неглибоких бункерів визначають за формулою
(2.147)
де h — глибина розміщення точки ди напруження під вільною поверхнею насипного вантажу; — кут нахилу стінок до горизонту; т — коефіцієнт рухомості.
Тиск на горизонтальні ділянки днища неглибоких бункерів визначається гідростатичним законом.
Тиск на горизонтальні ділянки днища глибоких бункерів
(2.148)
Тиск на затвори визначають як тиск на горизонтальні стінки бункерів:
Цей тиск можна визначити за формулою:
(2.149)
де k0 — коефіцієнт, що враховує осооливості експлуатації оункерів.
Для похилих і вертикальних затворів тиск визначають за формулою
(2.150)
де ά — кут нахилу затвора до горизонту.
Для бункерів, які повністю спорожнюють, k0=2. Для неспорожнюваних повністю k0=1.
Знаючи середній тиск на затвор σ, можна розрахувати силу G, яка діє на затвор, за формулою:
(2.151)
де F – площа випускного отвору.
Затвори. Затвором називають пристрій для відкривання і закривання випускного отвору бункера.
За способом керування розрізняють затвори ручні і урухомні. Як урухомні застосовують електродвигуни і пневматичні циліндри, рідше гідравлічні двигуни. Конструюючи затвори бункерів, слід прагнути досягти мінімальних габаритів; малої маси затвору; зручності обслуговування; уникнути нещільності, через яку сипучий матеріал може висипатися в закритому положенні; гарантувати безпечну роботу для обслуговуючого персоналу і поліпшення умов праці.
За видом робочого органу затвори поділяють на клапанні, секторні, щелепні, пальцеві, ланцюгові й ін.
Секторні затвори. Секторний затвор (рис. 2.30, 2.31) складається зі штуцера, прикріпленого до фланців випускного отвору бункера болтами, й шарнірної циліндричної заслінки з боковими щелепами у вигляді секторів.
Рис. 2.30 Рис. 2.31
Секторні затвори придатні для перекриття випускного отвору під навантаженням. Виконують їх у вигляді ручних і урухомних затворів, часто з пневматичним урухомником. За розміщенням сектора ці затвори поділяють на прямі й зворотні. За напрямком руху сектора під час відкривання затвора розрізняють: секторні затвори з відкриванням угору й з відкриванням униз.
Розрахунок секторних затворів:
а) без противаги (рис. 2.30).
Найбільше зусилля на ручку Р у момент зрушення сектора з місця визначають за формулою
(2.152)
де Т= Gf1 — сила тертя; G — сила тиску вантажу на затвор; f1 — коефіцієнт тертя насипного вантажу об матеріал; Rс — радіус сектора; R1 — радіус ручки. Момент опору в шарнірі
(2.153)
де Gс— сила тяжіння сектора з ручкою, d — діаметр цапф сектора; fц = 0,25 — коефіцієнт тертя в цапфах.
б) з противагою (рис. 6.13).
Зусилля на ручку Р для відкривання визначають за формулою
(2.154)
де Gп – сила тяжіння противаги; Rп – плече противаги.
Живильники. Термін живильник позначає апарат, призначений для рівномірного живлення різних приймальних пристроїв: конвеєрів, дробарок, формувальних машин.
За принципом дії робочих органів бувають такі живильники:
—тяглові (стрічкові, пластинчасті, ланцюгові);
—обертові (гвинтові, тарілчасті, барабанні й лопатеві);
—хитні (плунжерні, маятникові й кареткові).
Стрічкові й пластинчасті живильники. Робочий орган стрічкового живильника — текстильна гумована конвеєрна стрічка, що обгинає два барабани — урухомний й натяжний (рис. 2.32).
Рис. 2.32
Робоча гілка стрічки лежить на опорних роликах чи ковзає по нерухомому металевому настилу, а нижня гілка провисає вільно між барабанами. Над стрічкою розміщено нерухомі борти, що перешкоджають розтіканню матеріалу по обидва боки.
Стрічкові живильники застосовують для транспортування середньокускових й більш дрібних матеріалів, можуть також транспортувати вологі й липкі матеріали за умови застосування очищувальних пристроїв для стрічки. Недолік — не можуть транспортувати гарячі матеріали з температурою, вищою за 70 °С.
Продуктивність стрічкових живильників
(2.155)
де b — відстань між бортами, м; h — висота бортів, м; V — швидкість стрічки, м/с; ρ — об'ємна маса насипного вантажу; i = 0,75...0,8 — коефіцієнт використання об'єму жолоба. Встановлена потужність двигуна, кВт:
(2.156)
де kз = 0,1... 1,5 — коефіцієнт запасу; ή — ККД урухомника; N1 — частка потужності на валу урухомного барабана для подолання всіх опорів, крім опорів N2 і N3 ; N2 — опір бортів рухові насипного вантажу, який треться по них; N3 — опір у зоні активного тиску.
Потужність на валу урухомного барабана, кВт:
(2.157)
де Пр — продуктивність живильника; L — довжина живильника;Н — висота підйому вантажу.
Потужність, яка враховує опір бортів, кВт:
(2.158)
де h — висота шару матеріалу в жолобі; l — розрахункова довжина бортів, м; ρ — об'ємна маса насипного вантажу; f1 — коефіцієнт тертя вантажу об борти; n'— коефіцієнт бокового тиску; V— швидкість стрічки. Потужність, яка враховує опір у зоні активного тиску, кВт:
(2.159)
де G— сила активного тиску вантажу на стрічку.
Кількість прокладок стрічки, які забезпечують умову її міцності:
(2.160)
де in — кількість прокладок стрічки; п" — запас міцності; S — найбільший натяг стрічки; В — ширина стрічки; σр — напруга на розрив однієї прокладки:
(2.161)
де — к'= 1,5...1,85.
Робочий орган пластинчастого живильника — настил зі сталевих пластин (рис. 2.33), що перекривають одна одну й прикріплені до ланок двох тягових ланцюгів.
Ланцюгам надає руху механічний урухомник за допомогою урухомних зірочок, а відповідний натяг ланцюгів створюється гвинтовим натяжним пристроєм, приєднаним до осі холостих зірочок. Ланцюги забезпечені роликами, які котяться по напрямних шинах. Продуктивність живильника регулюють за допомогою плоского затвору.
Пластинчасті живильники мають перевагу перед стрічковими в тому, що можуть транспортувати важкі крупнокускові насипні вантажі — руду, камінь, що мають високу температуру.
Рис. 2.33
За розміщенням настилу у просторі розрізняють горизонтальні, похилі, горизонтально-похилі живильники.
Продуктивність пластинчастого живильника визначають так само, як і стрічкового, якщо значення коефіцієнта використання об'єму жолоба i = 0,8.
Швидкість руху пластинчастого настилу беруть у межах У = 0,02...0,25 м/с.
Потужність визначають так само, як і для стрічкового живильника, якщо значення кз = 1,15...1,2, кВт:
(2.162)
де q0 — сила тяжіння одного метра погонної довжини настилу з ланцюгами й роликами, Н/м; V — швидкість руху настилу; L2 — горизонтальна проекція номінальної довжини живильника; Н — висота підйому вантажу. Дві останні складові у дужках обчислюють так само, як й для стрічкового живильника.
Гвинтові живильники.Гвинт живильника (рис. 2.34) розміщено поблизу дна кожуха лотка й занурено в транспортований сипучий матеріал. Під час обертання гвинта матеріал переміщується в напрямку до випускного отвору лотка, причому під впливом гвинта й сил тертя об стінки лотка частинки матеріалу рухаються по криволінійній траєкторії, яка має вигляд гвинтової лінії.
Рис. 2.34
Гвинтові живильники застосовують для переміщення легкосипучих матеріалів — від дрібнокускових до пилоподібних, причому шматки дрібнокускових вантажів мають бути невеликої твердості й абразивності.
Перевага гвинтових живильників — герметичність; недолік — швидке спрацювання гвинта й лотка.
Продуктивність гвинтових живильників, т/г:
(2.163)
де D — діаметр гвинта, м; S — крок гвинта; n0 —обертова частота гвинта; i — коефіцієнт використання об'єму жолоба. Потужність двигуна, кВт:
(2.164)
де кз = 1,1...1,2; к1 — коефіцієнт, який враховує умови роботи гвинта; L2 — довжина горизонтальної проекції шляху переміщення; W — коефіцієнт опору, W = 1,5.. .4; Н— висота підйому вантажу.
2.7 Теплові процеси і апарати
Інтенсифікація теплових процесів — це сукупність науково-технічних заходів, що сприяють:
1)збільшенню теплового ККД установки;
2)збільшенню теплового потоку з одиниці поверхні на раніше і знову створюваних установках;
3)повторному використанню теплової енергії — регенерації;
4)створенню теплового процесу із замкненим тепловим циклом;
5)зниженню втрат теплоти (за рахунок застосування сучасних теплоізоляційних матеріалів);
6)використанню енергії внутрішнього тертя (дисипативної енергії), особливо в процесах переробки полімерних матеріалів;
7)автоматизації і механізації процесів;
8)розробці і використанню природних джерел енергії (вітрової, хвильової, сонячної, геотермальної).
Теплові установки загального призначення
До теплових установок загального призначення належать пристрої, у яких відбувається процес нагрівання однієї рідини за допомогою другої. За принципом дії теплообмінні апарати можна поділити на рекуперативні, регенеративні й змішувальні.
Рекуперативні теплообмінники являють собою пристрої, у яких теплоносії рухаються кожний своїм каналом. Канали розділені між собою перегородками. Теплообмін відбувається за рахунок конвекції й теплопровідності перегородки чи стінки. Приклад таких апаратів — парогенератори, конденсатори, випарні апарати й ін.
Регенеративні — це такі теплообмінники, у яких та сама поверхня нагрівається по черзі і омивається різними теплоносіями. Спочатку, наприклад, поверхня регенератора відбирає теплоту від гарячої рідини, нагрівається, потім поверхня регенератора віддає енергію холодній рідині.
У змішувальних теплообмінниках теплоносії безпосередньо контактують і змішуються.
Конструктивні схеми теплообмінних пристроїв загального призначення
Найпростіша схема, у якій один з каналів виконано у вигляді змійовика, а другий — у вигляді резервуара великого об'єму. Ці теплообмінники мають мішалку, їх називають реакторами (рис. 2.35).
Реактори металомісткі, поверхня тепловіддачі нерозгалужена, тому інтенсивність теплообміну не досить висока. Рух одного з теплоносіїв організовано, другого — неорганізовано.
Теплообмінник типу «труба у трубі» (теплообмінники з кільцевим зазором)(рис. 2.36). Ці теплообмінники складаються з ряду послідовно з'єднаних ланок. Кожна ланка являє собою дві співвісні труби. Теплообмінники працюють як за прямоструминиою, так і за протиструминною схемою. Вони більш ефективні, ніж реактори: коефіцієнт тепловіддачі значно вищий. Секції теплообмінників можна набирати із стандартних деталей, збільшуючи у такий спосіб поверхню теплообмінника. Основний недолік теплообмінників цього типу — металомісткість і громіздкість унаслідок великої витрати металу на зовнішні труби.
|
Рис. 2.35 Рис. 2.36
Кожухотрубні теплообмінники.Основні елементи кожухотрубних теплообмінників — пучки труб, трубні решітки, корпус, кришки, днища, патрубки. Кожухотрубні теплообмінники можуть бути вертикальними, горизонтальними (рис. 2.37), похилими відповідно до вимог технологічного процесу і зручності монтажу. Усередині трубок рухається один теплоносій, у міжтрубному просторі — другий. Ці теплообмінники мають ряд переваг порівняно з розглянутими вище типами теплообмінних пристроїв.
Вони компактні, мають високий вміст теплообмінних поверхонь в одиниці об'єму, допускають високі швидкості теплоносіїв у трубному й міжтрубному просторі.
Рис. 2.37
Багатоходові кожухотрубні теплообмінники.Щоб збільшити швидкість руху теплоносіїв та інтенсифікувати теплообмін, установлюють перегородки й організовують ходи теплоносія по трубному й міжтрубному простору.
За організацією ходів у трубному просторі розрізняють теплообмінники:
—з непарною кількістю ходів;
—з парною кількістю ходів.
Схему вертикального теплообмінника з непарною кількістю ходів наведено на рис. 2.38 Теплоносій, що рухається по трубному простору, входить і виходить через отвори в обох днищах.
На рис. 2.39 подано схему вертикального теплообмінника з парною кількістю ходів. Теплоносій входить і виходить в одному місці, наприклад через верхню кришку.
Організація ходів збільшує тривалість перебування одного теплоносія в зоні активного впливу на нього другого теплоносія.
За організацією ходів у міжтрубному просторі розрізняють теплообмінники:
—з подовжнім рухом теплоносія;
—з поперечним рухом теплоносія.
Схему вертикального теплообмінника з подовжнім рухом теплоносія подано на рис. 2.40, з поперечним — на рис. 2.41. Усі конструкції кожухотрубних теплообмінників належать до конструкцій жорсткого типу. їх використовують за невеликих різниць температур корпусу й пучка труб. Якщо перепад температур значний, виникають термічні напруження, які спричиняють розширення трубок і поломку теплообмінника. Тому застосовують теплообмінники напівжорсткої й нежорсткої конструкції.
Рис. 2.38 Рис. 2.39
Рис. 2.40 Рис. 2.41
У теплообмінниках напівжорсткої конструкції температурні деформації компенсуються осьовим стиском чи розширенням спеціальних лінзових компенсаторів, установлених на корпусі (рис. 2.42). Якщо виникають температурні напруження, діафрагма рветься й лінза розпрямляється.
У теплообмінниках нежорсткої конструкції передбачено можливість деякого незалежного переміщення теплообмінних труб і корпусу для усунення додаткових напружень від температури. Нежорсткість конструкції забезпечує пристрій з плаваючою головкою (рис. 2.43), пучок V — подібних труб (рис. 2.44).
Рис. 2.42
Рис. 2.43 Рис. 2.44
Розрахунок теплообмінних апаратів
Повний розрахунок апаратів чи машин, у яких відбуваються теплові процеси, треба виконувати в такому порядку: 1) тепловий розрахунок; 2) конструктивний розрахунок; 3) гідравлічний розрахунок; 4) розрахунок на міцність.
Тепловий розрахунок може бути проектним і перевірним. У проектному розрахунку теплообмінника вихідні дані такі: кількість речовини, яку треба нагріти чи остудити в певному апараті за одиницю часу; температура речовини на вході і на виході. Порядок проектного розрахунку такий:
Рис. 2.45
а) задають температури теплоносія на вході і на виході, який буде нагрівати чи охолоджувати основну рідину, t2` і t2`` ;
б) підраховують кількість теплової енергії, потрібної для нагрівання чи охолодження, за формулою
(2.165)
де G1 — відомі витрати рідини;
С — теплоємність.
Якщо теплоносій пара, слід підрахувати витрати пари за відомою залежністю: , де r – прихована теплота пароутворення;
в) розраховують площу поверхні теплообміну, що становить кінцеву мету проектного розрахунку:
(2.166)
- коефіцієнт теплопередачі;
- середньологарифмічна різниця температур;
- більша та менша різниця температур з графіка зміни температур теплоносіїв уздовж теплообмінних поверхонь.
Щоб розрахувати коефіцієнти тепловіддачі, потрібно знати швидкість руху теплоносія. Задають кількість трубок та їх розмір (внутрішній діаметр трубок) і за відомою витратою визначають швидкість руху рідини в каналах:
(2.167)
де f— площа перерізу трубки; п — кількість трубок. Якщо не можна розрахувати швидкість чи потрібно перевірити отриманий результат, слід
вибирати швидкість у кожухотрубному теплообміннику в таких межах: V 1 м/с — для рідини; V
20...30 м/с — для газу. Далі треба визначити довжину труб і габарити теплообмінника.
Наступний етап теплового розрахунку теплообмінного пристрою — перевірний розрахунок. Відомо площу поверхні теплообміну, коефіцієнт теплопередачі К, температури рідин на вході в теплообмінник t1`і t2` витрати цих рідин G1, Gг. Завдання полягає в тому, щоб визначити кількість теплоти, переданої за годину від однієї рідини до другої, і температури теплоносіїв па виході з теплообмінника, t1``і t2``.
Для розв'язання цієї задачі використовують величину, названу водяним еквівалентом:
(2.168)
Водяний еквівалент — це кількість речовини, еквівалентної за тепло-іністю кількості води, що проходить за той самий час теплообмінником. Складемо тепловий баланс теплообмінника:
(2.169)
Визначимо відношення водяних еквівалентів:
(2.170)
Як бачимо, перепади температур у межах одного теплоносія обернено пропорційні водяним еквівалентам. Можна визначити температури теплоносіїв на виході з теплообмінника:
(2.171)
Вважаючи, що температури теплоносіїв змінюються за лінійним (рис. 2.45), а не за логарифмічним законом, запишемо рівняння теплопередачі:
(2.172)
Вираз у дужках — середній перепад температур між теплоносіями чи середній температурний напір. Підставимо в рівняння значення температур. Тоді
(2.173)
Одержимо:
(2.174)
Гідравлічний розрахунок теплообмінників
|
Для забезпечення швидкості руху теплоносія потрібно знати продуктивність гідравлічних машин (компресора, вентилятора, насоса), їх напір встановлену потужність.
Напір залежить від довжини трубопроводу, а також від різних переходів, змін на шляху руху рідини.
Розгляньмо вертикальний жорсткий двоходовий кожухотрубний теплообмінник як гідравлічний апарат (рис.2.46). У трубках теплоносій зазнає шляхових і місцевих опорів: 1,4, 6— місцеві втрати через раптове
Рис. 2.46
розширення; 2,5,8 — місцеві втрати через раптове звуження; 3, 7 — шляхові втрати.
Щоб теоретично визначить втрати напору, слід розв'язати диференціальне рівняння Нав'є — Стокса в критеріальному вигляді:
(2.175)
Результат розв’язання – значення втрат напору:
(2.176)
де ξ — коефіцієнт опору.
Коефіцієнт опору через раптове розширення (рис. 2.46, а) визначають за формулою
(2.177)
через раптове звуження
(2.178)
де f1, f2 – площі перерізів каналів.
Рис. 2.46
Місцеві втрати не залежать від режиму руху рідини, а визначаються критеріальною залежністю:
(2.179)
У цьому прикладі Р визначають з рівняння
(2.180)
Щоб визначити коефіцієнт опору трубопроводів під час руху рідини в різних режимах вимушеної конвекції, потрібно розглядати питання шорсткості труб. Щодо цього труби поділяють на гідравлічно гладкі і шорсткі. У разі ламінарного руху рідини всі труби вважають гідравлічно гладкими. У разі турбулентного режиму, якщо товщина пристінного шару рідин > δ, трубу називають гідравлічно гладкою, якщо
< δ — шорсткою, чи якщо Rер < Rекр, труба гладка, якщо Rер >Rекр — шорстка.
Значення Rекр визначають за формулою
(2.181)
де r — радіус труби; δ — висота шорсткостей (рис. 2.47).
Визначення коефіцієнта опору ξ для гідравлічно гладких труб. Під час ламінарного режиму руху рідини, якщо Rе < 33, для ізотермічного процесу
(2.182)
для неізотермічного процесу варто враховувати вплив співвідношення (Рrст/Рrр), а також критерію Gr:
|
(2.183)
Рис. 2.47
Під час перехідного режиму руху рідини, якщо 3 103 < Rе < 1 105, для ізотермічного процесу
(2.184)
для неізотермічного процесу
(2.185)
Під час турбулентного режиму руху рідини, якщо 110 < Rе < НО , тепловий режим не має значення:
(2.186)
Визначення коефіцієнта опору, для шорстких труб. Для шорстких труб Rер>3103. Для всіх режимів і температурних станів формула для визначення коефіцієнта опору ξ має вигляд:
(2.187)
Якщо пучок труб кожухотрубного теплообмінника перебуває в поперечному потоці рідини, то втрати напору визначають за формулою
(2.188)
а коефіцієнт опору визначають з виразу
(2.189)
де а, b, т — коефіцієнти, що залежать від конструктивного оформлення пучка труб; п — кількість рядів за напрямком руху теплоносія. Критерій Rе розраховують за швидкістю у вузькому місці.
Щоб визначити витрати енергії на циркуляцію теплоносіїв у будь-якому теплообміннику, треба знати сумарні втрати напору:
(2.190)
Потужність гідроурухомника, КВт:
(2.191)
де GV — об'ємні витрати рідини; Р — повний опір чи сумарні втрати напору;
— ККД гідромашини.
3. Алгоритм розрахунку теплообмінних апаратів
Визначення середнього температурного напору
Для визначення середньої різниці температур між середовищами вибирається схема руху теплоносіїв, будується графік змінення температур середовищ уздовж поверхні й обчислюється більша і менша
різниця температур. Середня різниця температур загалом визначається як середньологарифмічна з крайніх значень різниць температур:
(3.1)
Якщо відношення , то з достатньою точністю можна скористатися середньоарифметичним значенням
(3.2)
Основні критерії подібності, що входять у формули конвективної тепловіддачі
Критерій Рейнольдса
(3.3)
Критерій Прандтля
(3.4)
Критерій Галілея
( 3..5 )
Критерій Грасгофа
(3.6)
Критерій конденсації
(3.7)
Критерій Нуссельта
(3.8)
У формулах(3.3)—(3.8) —швидкість руху рідини, м/с; l—визначальний геометричний розмір, м (для кожного випадку теплообміну вказується, який розмір є визначальний), м;
— кінематична в'язкість, м2/с; а — коефіцієнт
температуропровідності, м2/с,
(3.9)
— коефіцієнт теплопровідності, Вт/(м·К); с — питома теплоємність, Дж/(кгК); — густина, кг/м3;q — прискорення вільного падіння, м/с2;β— коефіцієнт об'ємного розширення, К-1; r — питома теплота конденсації, Дж/кг;Dt — у критерії Кn — різниця температур насичення ts і поверхні стінки tcт; у критерії Dt — різниця температур поверхні стінки і рідини, град;
— коефіцієнт тепловіддачі, Вт/(м2×К).
Фізичні параметри, що входять у формули (3.3) — (3.9), беруться з довідникових таблиць за визначальною температурою, що вказується для кожного окремого випадку теплообміну.
Розрахункові критеріальні рівняння для різних випадків теплообміну
1. Вимушений рух — турбулентний режим ( Rе > 10000):
(3.10)
Як визначальний розмір 1 у критеріях Nu і Rе приймається еквівалентний діаметр dек
Якщо f — площа живого перетину потоку, п — змочений периметр, то
dек=4f/п (3.11)
Для труб круглого перетину (рис. 3.1)
Рис. 3.1. До визначення еквівалентного діаметра
dек= dв (3.12)
Для кільцевого перетину (теплообмінник типу «труба в трубі»)
Dек=Dв- dз (3.13)
Для каналу прямокутного перетину
(3.14)
Якщо b<a (спіральний теплообмінник), то
D =2b. (3.15)
У формулі (3.10) фізичні константи варто брати при обчисленні критерію Рrст при температурі стінки tст, що стикається з потоком, а при обчисленні всіх інших критеріїв — при середній температурі рідини tp .
2. Зона перехідна (2320 < Rе < 10000):
(3.16)
Визначальний геометричний розмір і визначальна температура приймаються так само, як і для турбулентного режиму.
Поправка, що враховує напрямок теплового потоку (Рr/Рrст)0,25, у формулах (3.10) і (3.16) при невеликих різницях tp - tст мало відрізняється від одиниці. Тому розрахунок попередньо ведеться без урахування впливу напрямку теплового потоку, тобто без обліку співвідношення (Рr/Рrст)0,25 .
Після обчислення коефіцієнта теплопередачі за формулою визначають температуру стінки з рівняння
(3.17)
де К — коефіцієнт теплопередачі, Вт/(м2×К); α2 — коефіцієнт тепловіддачі від стінки до рідини, Вт/( м2×К).
Знак «+» у цьому рівнянні буде при нагріванні рідини, знак «-» — при охолодженні.
Подальший розрахунок проводиться з урахуванням співвідношення
(3.18)
3. Конденсація пари:
а) при конденсації на зовнішній поверхні горизонтальних труб
(3.19)
де ε — поправковий коефіцієнт, що враховує компонування поверхні нагріву і залежить від кількості труб у пучку, береться з табл.1. Як визначальний геометричний розмір береться зовнішній діаметр труб l= dз;
б) при конденсації на вертикальних поверхнях
(3.20)
Визначальний геометричний розмір — висота вертикальної стінки чи труби.
Значення теплоти конденсації в критерії Кu формул (3.19) і (3.20) треба брати за температурою конденсації ts, а всі інші параметри — для середньої температури плівки конденсату, °С,
(3.21)
Оскільки в рівняннях (19) і (20) невідома величина температурного напору Dtу суміжному шарі, ці рівняння розв'язують відносно α і надають їм вигляду:
α1 = А Dt0,25, (3.22)
де α1— коефіцієнт тепловіддачі від пари до стінки, Вт/( м2×К).
4. Природна конвекція
а) ламінарний режим (GrPr<2×107)
(3.23)
б)турбулентний режим (GrPr>2×107)
(3.24)
Для горизонтальних труб визначальним розміром є їхній діаметр (l=dз)> для вертикальних труб — їх висота (l=Н). Значення фізичних констант у формулах варто брати за визначальною температурою:
(3.25)
Оскільки в рівняннях (3.23) і (3.24) невідомий температурний напір Dt у суміжному шарі, ці рівняння розв'язують відносно α1 і надають їм вигляду:
α1= А Dt 0,25 (3.26)
чи
α1= А Dt 0,33 (3.27)
Де α1 — коефіцієнт тепловіддачі від стінки до рідини, Вт/(м2 К).
Визначення коефіцієнта теплопередачі
Коефіцієнт теплопередачі К, Вт/( м2 К) визначають за формулою
(3.28)
де α1 і α2 — відповідно коефіцієнти тепловіддачі від нагрівального теплоносія до стінки і від стінки до нагрівної рідини, Вт/( м2 К); rст — термічний опір забрудненої стінки, (м2 К)/Вт,
(3.29)
δст, δзаб — товщина металевої стінки труби і шару забруднення, м; lст, lзаб — коефіцієнт теплопровідності металевої стінки і шару забруднення, Вт/( м К).
Якщо в критеріальне рівняння входить невідома величина температурного напору Dt у суміжному шарі (конденсація пари, природна конвекція), то коефіцієнт теплопередачі визначається графоаналітичним методом. Для цього задаються трьома значеннями Dt у межах (0,1...0...0,5) Dt сеp і з рівняння (3.22), (3.26) чи (3.27) знаходять α1, а потім з рівняння (28) — коефіцієнт теплопередачі К
Після цього визначаються величина теплового потоку, Вт/м2,
q= α1 Dt (3.30)
і величина загального температурного напору, град,
Dt=q/K (3.31)
Обчислення зводять у таку таблицю:
Визначена величина | Одиниця вимірювання | Температурний напір | ||
Dt,¢ | Dt,¢¢ | Dt,¢¢¢ | ||
α1 Кп q Dt | Вт/(м2×К) Вт/(м2×К) Вт/(м2×К) град |
На міліметровому папері будується навантажувальна характеристика у вигляді графіка Dt = f (q) і за відомою величиною Dt визначається значення теплового потоку q (рис. 2).
Рис. 3.2. Навантажувальна характеристика Тоді коефіцієнт теплопередачі визначиться зі співвідношення, Вт/(м2-К),
(3.32)
Розрахунок ізоляції і теплових втрат у навколишнє середовище
Товщина шару ізоляції, м, визначається за рівнянням
(3.33)
Де lіз— теплопровідність ізоляційного матеріалу, Вт/(м2×К); Кп — коефіцієнт теплопередачі в навколишнє середовище, Вт/(м2×К).
Величину Кп можна визначити двома методами:
1.При заданих теплових втратах у навколишнє середовище. У цьому разі теплові втрати в навколишнє середовище Qв, Вт, беруть у розмірі 2...З % від тепла, витраченого на корисне нагрівання, Вт/(м2×К).
Тоді (3.34)
Де Fп — поверхня ізоляції апарата, м2; tсеp — температура середовища усередині апарата, °С; tп— температура навколишнього повітря, °С.
Після визначення величини Кп перевіряють температуру поверхні ізоляції tiз за рівнянням
(3.35)
Де ап — коефіцієнт тепловіддачі від поверхні ізоляції до навколишнього повітря, Вт/(м2×К).
Величину ап можна обчислити за емпіричною формулою
ап = 9,3 + 0,058 tiз. (3.36)
2.При заданій температурі поверхні ізоляції. За вимогами техніки безпеки температура поверхні ізоляції не повинна перевищувати 60 °С. Для розрахунку беруть tiз. = 40...50 °С.
Тоді
(3.37)
Після визначення величини Кп визначають теплові втрати в навколишнє середовище Qв з рівняння (34).
Гідравлічний розрахунок теплообмінних апаратів
Метою гідравлічного розрахунку є обчислення гідравлічного опору теплообмінника і визначення потужності, споживаної двигуном насоса. Повна втрата тиску в теплообміннику, Па, підраховується за рівнянням
åDР = DРшв + DРтер + DР мо + DР під, (3.38)
де DРшв, DРтер, DР мо, DР під—втрата тиску відповідно на створення швидкості потоку на виході з теплообмінника, Па, на подолання опору тертям, Па, на подолання місцевих опорів, Па, на підйом рідини, Н/м2.
Витрата тиску на створення швидкості потоку:
DР = (3.39)
де ω — швидкість рідини на виході з теплообмінника, Па; ρ — густина рідини, кг/м3.
Втрата тиску на подолання сил тертя:
(3.40)
де l' — коефіцієнт тертя, що може бути визначений для значень Rе> 5000 за формулою
(3.41)
Втрата тиску на подолання місцевих опорів (поворот, звуження, розширення та ін.):
(3.42)
де åξ — сума коефіцієнтів місцевих опорів, коефіцієнти вибираються з табл. 1; ω — швидкість руху рідини в трубах чи каналах, м/с.
Таблиця 1. Коефіцієнти місцевих опорів
Вид опору | Коефіцієнт х |
Поворот у U-зворотній трубі на 180° Поворот на 90° при виході (вході) з міжтрубного простору теплообмінника в патрубок Поворот на 180° усередині камери при переході з одного пучка трубок в інший Вхід у розподільну камеру (чи вихід) Вхід у трубний простір з розподільної камери (чи вихід) Рух по спіральному чи кільцевому каналу (n - кількість витків) | 0,5 1,1 2,5 15 1,0 0,5n |
Втрата тиску на підйом рідини:
DР під=ρgH (3.43)
де g — прискорення вільного падіння, м/с2; Н — висота підйому рідини, м.
Потужність, кВт, споживана двигуном насоса, розраховується за формулою
N = , (3.44)
де G — масова витрата рідини, кг/с; ρ — густина рідини, кг/м3; DР— повна втрата тиску в теплообміннику, Па; ζ, — загальний коефіцієнт корисної дії насосної установки, для відцентрових насосів можна прийняти ζ = 0,6 ... 0,7.
Визначення діаметрів патрубків
Діаметри вхідних і вихідних патрубків визначаються за формулою
D=1,18 (3.45)
де G — витрата рідини чи пари, кг/с; ρ — густина рідини чи пари, кг/м3; ω — швидкість руху рідини чи пари в патрубках, м/с.
Величина ω приймається, м/с: для рідин 1,0... 1,5, для пари 15...20, для конденсату 0,3...0,7.
Остаточно діаметри патрубків приймаються за Нормалями.
Додатки
Додаток А1
Приклад розрахунку. Необхідно підібрати і розрахувати продуктивність щокової дробарки для дроблення гранітного щебеню з максимальним розміром кусків - 600 мм.
Виходячи зі співвідношення розмірів завантажувального отвору і діаметра кусків матеріалу, одержуємо:
- ширину завантажувального отвору: А - 600/0,8 = 750 мм;
- довжину - L =1,4·750 = 1050 мм;
- висоту робочої частини рухливої щоки
мм
На підставі отриманих результатів приймаємо стандартну щокову дробарку з простим рухом щоки і розмірами камери дроблення А·L= 900·1200.
Значення ходів стискання у верхній і нижній точках камери дроблення визначаємо для дробарок із простим рухом щоки:
мм
мм
Знаходимо частоту обертання ексцентрикового валу
У цьому випадку продуктивність обраної дробарки складе
Після переведення секунд в години одержимо продуктивність дробарки - 323,87 м3/год.
Додаток А2
Приклад розрахунку. Необхідно визначити основні параметри плоского грохоту для сортування гранітного щебеню продуктивністю 200 т/год; максимальна крупність зерен - 70 мм. Кут нахилу сит – 3o, ексцентриситет приводного валу - 10 мм.
Для плоского грохоту частота коливання складає:
Після розв'язання рівняння (2.3) відносно В знаходимо ширину грохоту
Відносна швидкість руху матеріалу по ситі складає:
Таким чином, ширина грохоту дорівнюватиме
Показники процесу просіювання багато в чому залежать від конструкції поверхні, що просіває, а саме від розмірів поверхні, розміру і форми отворів. Поверхня, що просіває, для грохотів звичайно характеризується співвідношенням ширини і довжини, рівним 1:2,5. У колосникових грохотів важкого типу це співвідношення дорівнює 1:2, що характеризується більш низькими вимогами до ефективності просівання.
Таким чином, розміри грохоту приймаємо B=1,57 м,L-=3,92 м.
Остаточно вибираємо грохот із круговими коливаннями і розмірами поверхні, через яку просіюють: ширина - 1750 мм, довжина - 4500 мм.
Енергія, що затрачується на переміщення і сортування матеріалу в колосниковому грохоті, змінюється прямо пропорційно масі матеріалу, що знаходиться на грохоті.
Для визначення потужності, що споживається грохотом, необхідно визначити вагурухливої маси грохоту та матеріалу
Тоді
кВт
Додаток А3
Приклад розрахунку. Підібрати барабанну сушарку, що обігрівається повітрям, для сушіння гранульованого шлаку з продуктивністю 90 т/год.
Згідно з додатком Д визначаємо основні параметри сушіння гранульованого шлаку:
- початкова вологість матеріалу Wn = 20 %;
- кінцева вологість матеріалу Wk= 0,3 %;
- температура повітря на вході в барабан t1 = 500 °С;
-температура на виході з барабана t2 = 80 °С;
- напруга барабана по вологості А = 50 кг/м3 год.
На підставі цих даних визначаємо продуктивність барабана по вологості:
кг
Кількість матеріалу висушеного за 1 годину:
кг
Отже, об'єм барабану буде дорівнювати:
м3
Знаючи об'єм барабану, знаходимо його розміри:
- з формули (3.4) - значення діаметра барабана:
- довжина барабана L = 5d = 5·4,49=22,455 м = 22455 мм .
Згідно з додатками Ж і 3 вибираємо остаточні розміри сушильного барабана, тип і товщину теплоізоляції:
- діаметр d = 4500 мм;
- довжина L = 28000 мм;
- теплоізоляція - діатоміт товщиною 125 мм.
Для визначення кількості обертів сушильного барабана за секунду необхідно знати час перебування матеріалу в барабані:
с
Об'єм прийнятого барабану складає V =3,925d3 = 3,925· 4,53=358м3
Таким чином, число обертів барабана буде дорівнювати
с-1
Додаток А4
Приклад розрахунку. Необхідно визначити розміри циклона для усунення запиленості повітря (2 кг/м3) у виробничому приміщенні, ступінь очищення повітря в даному циклоні і його гідравлічний опір.
Вихідні дані:
- об’єм газу, що надходить - Vс = 3 м3/с;
- швидкість газу в циклоні - Wц = 12 м/с;
- швидкість газу у вхідному патрубку - WВХ = 16 м/с;
- швидкість повітря у вихлопній трубі - Wтр = 5 м/с.
Площа перетину вхідного патрубка
м2
Виходячи з площі вхідного патрубка, визначаємо його розміри, що становлять
м
м
Розраховуємо діаметр циклона і внутрішній діаметр вихлопної труби
м
м
З урахуванням товщини стінок вихлопної труби її зовнішній діаметр буде складати
м
Висота циклона складається з висоти циліндричної і конусної частин.
Розраховуємо висоту циліндричної частини
м
Висота конусної частини h2=0,86,D=0,86·1,247 = 1,10 м. Таким чином, загальна висота циклона
м
Для даного циклона визначаємо фактор поділу
Гідравлічний опір визначає енергетичні витрати на подачу і проходження повітря через циклон
Па
Додаток Б
Міністерство освіти і науки України Національний транспортний університет
Кафедра дорожньо-будівельних матеріалів і хімії
Курсовий проект
з дисципліни:
«Процеси і апарати в будівельному виробництві»
(зразок)
Виконав студент
гр.ТК-Ш-1
Керівник проекту
Кожушко В.В.
Київ2008
ЗМІСТ
1. Вступ
2. Загальні положення
2.1. Опис проектованих процесів та апаратів
2.2.Місце та призначення процесів та апаратів в технологічній схемі
3. Розрахунки
3.1. Тепловий розрахунок
3.2. Конструктивний розрахунок
3.3. Гідравлічний розрахунок
3.4. Техніко-економічний розрахунок
3.5. Розрахунок оптимальної швидкості
4. Список використаної літератури
ВСТУП
1.1 Опис проектувального апарату.
У вступі розкривається:
- актуальність;
- мета;
- завдання курсового проекту.
Сучасне виробництво будівельних матеріалів, збірних залізобетонних виробів і конструкцій містить у собі велику розмаїтість механічних, гідромеханічних і хімічних процесів. Без знання їх теоретичних основ не може бути раціональної організації екологічно чистої технології виробництва будівельних матеріалів.
Мета курсового проекту – одержання студентами навичок розрахунку основних параметрів технологічних процесів в умовах виробництва.
У процесі роботи над курсовим проектом потрібно виявити знання в області теорії процесів і їх апаратурного оформлення, методики, техніки розрахунку і вибору на їх основі найбільш обґрунтованого рішення; уміти скористатися новітньою технічною літературою, технічними умовами, інше.
1.2 Місце та призначення апарату в технологічній схемі.
Загальні положення
2.1. Опис проектованих процесів та апараті
Теплообмінними апаратами, або теплообмінниками називаються апарати для передачі теплоти від більш нагрітого теплоносія до менш нагрітого. Теплообмін застосовується на підприємствах промисловості будівельних матеріалів. Для нагрівання і охолодження різних середовищ при проведенні технологічних процесів.
За способом передавання теплоти усі теплообмінники поділяють на дві великі групи: поверхневі і змішувальні. В поверхневих теплообмінниках обидва теплоносії відокремлені один від одного твердою стінкою або по черзі контактують з однією і тією самою стінкою, яка бере участь у процесі теплообміну і утворює так звану поверхню теплообміну. Залежно від призначення теплообмінного апарата цю поверхню також часто називають поверхнею нагріву або охолодження. У змішувальних теплообмінниках, або апаратах змішування, теплообмін здійснюється внаслідок безпосереднього контакту і змішування гарячого і холодного теплоносіїв.
Поверхневі теплообмінники, у свою чергу, поділяють на рекуперативні і регенеративні. В рекуперативних апаратах один бік поверхні теплообміну весь час омиває гарячий теплоносій, а другий - холодний. Теплота від одного теплоносія до другого передається крізь стінку з теплопровідного матеріалу, що їх розділяє. Напрямок теплового потоку в стінці лишається незмінним. У регенеративних апаратах одна й та сама поверхня теплообміну поперемінно омивається то одним, то другим теплоносієм. У період нагрівання, тобто під час контакту з гарячим теплоносієм, у твердих тілах (насадці), що заповнюють апарат, акумулюється теплота, яка в період охолодження віддається рухомому холодному теплоносію. Напрямок потоку теплоти в стінках періодично змінюється.
У промисловості будівельних матеріалів для нагрівання й охолодження використовують переважно рекуперативні теплообмінники. Тому далі під назвою «поверхневі теплообмінники» або просто «теплообмінник» ми розуміємо рекуперативні теплообмінники.
Теплообмінники класифікують так:
• за видом теплоносіїв залежно від їх агрегатного стану - парорідинні, рідиннорідинні, газорідинні, газогазові, парогазові;
• за конфігурацією поверхні теплообміну - трубчасті апарати з прямими трубками, трубчасті апарати з ІІ-подібним трубним пучком, спіральні, пластинчасті, змійовикові, ребристі;
• за компонуванням поверхні нагріву - кожухотрубні, типу «труба в трубі», зрошувальні, заглибні, оболонкові.
Крім зазначених основних класифікаційних ознак теплообмінних апаратів, останні також можна класифікувати за рядом додаткових ознак. Усі теплообмінні апарати поверхневого типу можна класифікувати залежно від напрямку потоків теплоносіїв:
1. прямотечійні, коли обидва теплоносії рухаються паралельно в одному напрямку;
2. протитечійні, коли обидва теплоносії рухаються в протилежних напрямках назустріч один одному;
3. з перехресною течією - теплоносії рухаються взаємно перпендикулярно;
4. із складнішими схемами різного поєднання прямотечії, і перехресної течії.
Теплообмінні апарати можна також класифікувати за призначенням (підігрівники, охолодники тощо), за кількістю ходів теплоносіїв і т.д.
2.2.Місце та призначення процесів та апаратів в
Технологічній схемі
Кожухотрубні теплообмінники. Вони найпоширеніші в промисловості будівельних матеріалів, дають можливість створювати великі поверхні теплообміну в одному апараті, прості у виготовленні і надійні в експлуатації.
Кожухотрубний теплообмінник складається з корпусу, приварених до нього нерухомих трубних решіток, пучка труб, кінці яких закріплені в трубних решітках розвальцюванням або зварюванням. До трубних решіток прикріплені кришки. Один з теплоносіїв рухається всередині труб, а другий - у просторі між кожухом і трубами (в міжтрубному просторі).
Через малу швидкість руху теплоносіїв одноходові теплообмінники працюють з низьким коефіцієнтом тепловіддачі. Щоб збільшити швидкість руху теплоносіїв, застосовують багатоходові теплообмінники, в яких пучок труб за допомогою поперечних перегородок, встановлених у кришках, розділений на кілька секцій (ходів), по яких теплоносій проходить послідовно. Швидкість руху теплоносія в міжтрубному просторі підвищують, встановлюючи ряд сегментних перегородок. З двох теплоносіїв, що рухаються в трубках і в міжтрубному просторі, треба збільшувати швидкість руху насамперед того, в якого при теплообміні вищий термічний опір.
Двотрубні теплообмінники типу «труба в трубі». Теплообмінники цього типу складаються з кількох послідовно з'єднаних елементів, утворених двома концентрично розміщеними трубами. Один теплоносій рухається у внутрішніх трубах, а другий - у кільцевому зазорі між внутрішніми і зовнішніми трубами. Внутрішні труби окремих елементів з'єднані послідовно колінами (калачами), а зовнішні - патрубками. Завдяки невеликому поперечному перерізу в теплообмінниках «труба в трубі» досягають високих швидкостей руху теплоносіїв і високої інтенсивності теплообміну. Проте ці теплообмінники дуже громіздкі та металомісткі. Тому їх використовують лише при малих об'ємних витратах теплоносія і незначних поверхнях теплообміну.
Заглибні теплообмінники. їх звичайно виготовляють у вигляді змійовиків. Змійовик занурений у рідину, яку нагрівають або охолоджують теплоносієм, що рухається всередині змійовика. Коефіцієнт теплопередачі в цих теплообмінниках порівняно низький, але через простоту виготовлення вони набули значного поширення.
Щоб збільшити швидкість руху рідини і, отже, інтенсифікувати теплообмін, у корпусі встановлюють витіснювальний стакан. Через порівняно великий гідравлічний опір змійовика швидкість руху рідини в ньому витримують в межах 0,3...0,8 м/с, а для газів при атмосферному тиску - 3...10 м/с. Змійовики часто виготовляють з прямих труб, з'єднаних калачами.
Зрошувальні теплообмінники. Їх складають із змійовиків, зрошуваних ззовні рідким теплоносієм (звичайною водою), і застосовують переважно як холодильники. Змійовики виготовляють з прямих горизонтальних труб, розміщених одна над одною і послідовно з'єднаних між собою калачами. Зверху змійовики зрошують водою, яка рівномірно розподіляється копитечком із зубчастими краями. Відпрацьовану воду відводять з піддона встановленого під змійовиками. Зрошувальні теплообмінники прості за будовою, але досить громіздкі. Теплообмін від труб до зрошувальної води характеризується невеликими значеннями коефіцієнтів тепловіддачі.
Спіральні теплообмінники. У цих теплообмінниках поверхню теплообміну утворюють два зігнутих у вигляді спіралей металевих листи,внутрішні кінці яких приварені до перегородки. Зовнішні кінці листів зварені один з одним. Між листами утворюються канали прямокутного перерізу, в яких рухаються теплоносії. З торців канали закриті плоскими кришками на прокладках.
Переваги спіральних теплообмінників - компактність, можливість пропускання обох теплоносіїв з високими швидкостями, що забезпечує великий коефіцієнт теплопередачі. При однакових швидкостях робочих середовищ у спіральних теплообмінниках гідравлічний опір менший, ніж у кожухотрубних.
Недоліками спіральних теплообмінників слід вважати складність виготовлення та низький робочий тиск.
Пластинчасті теплообмінники. Останнім часом у промисловості будівельних матеріалів широко використовуються пластинчасті теплообмінники. Поверхню теплообміну в них створюють гофровані паралельні пластини. У складеному вигляді пластини стиснуті між нерухомою та рухомою плитами. Ущільнені пластини гумовими прокладками. Велика прокладка обмежує канал для проходження рідини між пластинами крізь отвори. Малі кільцеві прокладки ущільнюють отвори, крізь які протитечійно до рідини надходить і входить через отвори і рідина. Продукт для оброблення у пластинчастому теплообміннику рухається тонким шаром (3...6 мм), що сприяє інтенсифікації процесу. Завдяки рифленій поверхні пластин при порівняно малій швидкості руху рідини (0,3...0,8 м/с) внаслідок штучної турбулізації потоку досягають високих коефіцієнтів теплопередачі при незначному гідравлічному опору.
Конструктивні, експлуатаційні та теплотехнічні переваги пластинчастих теплообмінників сприяють дедалі ширшому застосуванні їх на підприємствах ромисловості будівельних матеріалів. Недолік їх - велика кількість довгих ущільнювальних прокладок.
Ребристі теплообмінники. Для більшої компактності теплообмінників використовують вторинні поверхні (ребра) з боку теплоносія, що відрізняється низьким значенням коефіцієнта тепловіддачі
Оболонкові теплообмінники. В них нагрівання і охолодження здійснюють поряд з іншими технологічними процесами. Поверхню теплообміну в них утворюють стінки самого апарата. До корпусу кріплять оболонку за допомогою фланцевого з'єднання. У просторі між оболонкою і зовнішньою поверхнею корпуса апарата циркулює теплоносій 1, в апараті - теплоносій 2. Застосування таких апаратів обмежене невеликою поверхнею теплообміну і тиском в оболонці (до 1 МПа).
Дата добавления: 2018-02-15; просмотров: 765; Мы поможем в написании вашей работы! |
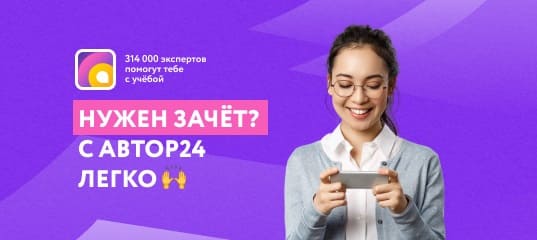
Мы поможем в написании ваших работ!