Проектирование операционной технологии.
Постановка задачи.
После того как уточнена структура УТП и получена структура рабочего ТП, начинается проектирование отдельных операций. Назначение операций выполняется на 2-м уровне проектирования ТП.
Возникает вопрос: о какой операции начать проектирование - с первой или с последней. Если начать с первой операции, то обычно неизвестна исходная заготовка, так как для ее определения нужно знать припуски, удаляемые на последующих операциях. Эти операции еще не спроектированы и, следовательно, величины припусков неизвестны. Поэтому как правило проектирование операций ведется от последней операции, на которой получается уже готовая деталь, к первой» Такой подход удобен тем, что при проектировании операции уже известно описание межоперационной заготовки, которая должна быть получена на проектируемой операции.
Назовем межоперационную заготовку, поступающую на операцию, входной, а соответственно заготовку, полученную после выполнения операции, выходной.
Преобразование межоперационных заготовок можно проиллюстрировать, так же как и ранее изменение состояния поверхности элемента детали, о помощью линейного графа состояний заготовки.
Каждая вершина графа отображает межоперационную заготовку Zi, а дуга Oi - технологическую операцию, позволяющую преобразовать заготовку Z(i-1) в заготовку Zi. Заготовка Zо является исходной заготовкой, а последняя заготовка Zn представляет собой готовую деталь Д.
|
|
Техническими ограничениями, определяющими возможные варианты проектируемой операции, служит технологическое оснащение, имеющееся на предприятии. Поэтому при решении данной задачи применяют базы данных: "Оборудование", "Приспособление", "Инструмент". Кроме того необходимо использовать технологические стандарты на припуски, напуски, режимы резания и др. Для них создается база данных "Нормативы".
Задача проектирования технологической операций заключается в:
- выборе технологического оснащения;
- определении структуры ТО;
- вычислении себестоимости операции;
- составлении описания заготовки Z(i-1) , поступающей на i-ю операцию.
Проектирование технологической операции является одной из наиболее сложных и слабоформализованных задач, поэтому оптимизация ТО также является сложным процессом.
В качестве критерия оптимизации целесообразно взять приведенную себестоимость операции Со :
Со=Спер+Спр+Сн
где
Спер- суммарная стоимость обработки по переходам;
Спр - приведенная стоимость приспособления;
Сн - приведенная стоимость наладки станка.
Спер=SСj
|
|
где Cj - стоимость j -го перехода;
Cпр=Сп/N
где Cпр - стоимость приспособления, отнесенная к году;
N - годовой объем выпуска;
Сн=Cпн/Р
где Спн- полная стоимость наладки;
Р - размер партии.
Структурная оптимизация ТО заключается в выборе такого оборудования, приспособления и порядка выполнения переходов при которых достигается наименьшая приведенная стоимость.
Параметрическая оптимизация обычно выполняется на уровне перехода, т.е. на 3-м уровне проектирования. Оптимизация на уровне операции выступает как глобальная по отношению к оптимизации на уровне перехода, причем возможна ситуация, когда сумма стоимостей оптимальных переходов больше Спер для оптимальных переходов, т.е. когда глобальный оптимум не совпадает о локальным.
Это имеет место при совмещении переходов, т.е. при манипулировании структурой операции. Например, выполняемые последовательно оптимизированные переходы Рн и Рm , могут быть совмещены и выполняться параллельно.
При этом должны изменяться режимы резания для выравнивания времени обработки по переходам. И хотя каждый переход в отдельности становится весьма далек от оптимального, однако tn+tm>tn,m и соответственно стоимость двух совмещенных неоптимальных переходов будет ниже стоимости двух оптимальных переходов, но выполняемых последовательно.
|
|
Результатом проектирования операционной технологии являются: описание ТО; описание заготовки, поступающей на операцию; управляющая программа; задания на проектирование специальных приспособлений и инструмента.
Проектирование операций методом адресации.
Проектирование операции методом адресации выполняется в соответствии с общим алгоритмом приведенным на рис. 12. При этом для каждой проектируемой операции выбирается унифицированная операция (УНО), необходимая для получения рабочей операции (РО).
В описании унифицированной операции уже указаны модель оборудования и обозначение применяемого приспособления, а также указана последовательность выполнения переходов и виды инструмента, используемые для выполнения переходов.
Наличие такой информации облегчает проектирование РО, например, не нужен этап определения модели оборудования и выбора приспособления.
Важная задача проектирования РО - это определение структуры oпeрации применительно к конкретной заготовке. На предшествующих этапах проектирования для каждой поверхности были определены их промежуточные состояния» а также номера операций и переходов, необходимые для получения этих состояний.
|
|
На первом этапе определения структуры операции необходимо из унифицированной операции убрать те переходы, которые отсутствуют у конкретной детали.
Далее возможны два варианта продолжения решения задачи.
Первый вариант основан на том, что в УО ее структура задана жестко и структура РО получается автоматически после удаления лишних переходов.
Второй вариант предполагает, что последовательность выполнения переходов задана не жестко и поэтому необходимо структуру операции откорректировать.
Сложность корректировки структуры У0 заключается втом, что в УО могут быть несколько одинаковых переходов, а у заготовки могут быть одинаковые поверхности, которые можно обработать с помощью этих переходов,
В этом случае возможна оптимизация структуры путем нахождения рациональной последовательности выполнения переходов, дающей например, наименьшую себестоимость перехода. Такую структуру будем называть структурой о оптимизацией, в отличие от прежней, называемой простой структурой.
Рассмотрим следующий пример. На рис. 13.а. показан операционный эскиз заготовки, получаемой на револьверной операции.
Соответствующая для данной заготовки откорректированная структура УО приведена на рис. 14.а. Здесь оптимизируемыми переходами яв
ляются переходы на черновой обработке Р3…Р8. Отметим, что оптимизируемые перехода могут выполняться в любой последовательности, но обозначаются, как и выполняемые параллельно, добавляется лишь дополнительная дуга, соединяющая ребра для вершин обозначающих оптимизируемые переходы.
|
В УО указано максимально возможное количество переходов по черновой обработке цилиндрических поверхностей ( Р3…Р8).
Дляэтих переходов допустим любой порядок их выполнения.
После оптимизации, результата которой зависят от соотношения диаметров цилиндрических поверхностей и максимально допустимой глубины резания, количество переходов уменьшится и определится порядок их выполнения. На рис. 13.б. показан эскиз заготовки о указанием оптимизированных переходов.
Соответствующая структура операции после оптимизации приведена на рис.14.б.
Алгоритм корректировки состоит из нескольких последовательно выполняемых модулей:
- корректировка состава У0 по переходам;
- уточнение структуры операции;
- оптимизация однородных переходов;
- упорядочение номеров переходов (присваивание новых номеров переходам в порядке их выполнения).
Разработка структуры операции является сложной многовариантной задачей, тесно связанной с проектированием переходов. Полученные варианты уточняются на более низких уровнях проектирования, в данном случае на уровне перехода. Если на этом уровне определено, что переход по каким-либо причинам спроектирован неудачно, то осуществляется возврат на уровень проектирования операции и проводится соответствующая корректировка структуры операции.
При формировании структуры операции необходимо использовать комплекс общетехнологических правил. Выделим наиболее общие правила:
- обработка поверхностей в порядке возрастания рангов поверхностей;
- предварительное выполнение черновых переходов, а затем чистовых (окончательных);
- ведение обработки таким образом, чтобы жесткость заготовки понижалась в наименьшей степени;
- поверхности, которые являются базовыми, должны быть обработаны в предшествующих операциях или должны создаваться в первую очередь;
- использование в качестве базы поверхностей, от которых задано наибольшее количество размеров.
Применительно к каждому классу деталей и виду оборудования эти общие правила дополняются и уточняются. Для токарной обработки можно привести следующие правила:
- обработка детали начинается с подрезки торца и создания центрового отверстия;
- сначала выполняется обработка наружных поверхностей, а затем внутренних;
- обработка ведется таким образом, что канавки и фаски выполняются в конце операции; переход по нарезанию резьбы производится обычно в самом конце операции (если операция является окончательной для данной стороны детали).
Необходимо отметить, что в условиях конкретного предприятия эти правила также могут быть изменены или им могут быть даны другие приоритеты для учета специфики предприятия.
Поэтому алгоритм определения структуры носит субъективный характер и требует доработки при переходе на другое предприятие. Кроме того, при определении структуры операции применение всех технологических правил не приводит к полной однозначности. В этом случае направленный поиск варианта может осуществляться технологом в режиме диалога.
Проектирование переходов.
Проектирование перехода выполняется на 3-м уровне проектирования ТП.
Обращение к задаче назначения перехода происходит при проектировании операций на соответствующем этапе. После решения задачи происходит возврат ко 2-му уровню проектирования и проектирование операции продолжается.
При обработке поверхности для каждого перехода требуется выполнить рабочие и вспомогательные ходы. Совокупность ходов и последовательность их выполнения образует структуру перехода.
Пример перехода и соответствующая ему структура приведены на рис. 15.
Исходными данными при проектировании перехода являются:
1 - информация об обработанной поверхности заготовки, т.е. о форме, размерахиих точности i -го состояния поверхности заготовки;
2 - технологическая информация (тип перехода, схема установки детали, модель станка, обозначение приспособления и т.д.).
Выходной информацией служит следующая информация о переходе:
- обозначения выбранных вспомогательного и режущего инструмента;
- структура перехода;
- режимы резания и нормы времени (основное и вспомогательное время) на переход;
- стоимость выполнения перехода;
- задание на проектирование специального режущего инструмента;
- значение припусков и размеров поверхностей.
В процессе проектирования перехода происходит многократное обращение к базе данных для получения характеристик:
- о заданной модели оборудования (частоты вращения, возможные подачи, мощность привода, усилие подачи и т.д.);
- о выбранном приспособлении;
- об искомых инструментах и т.д.
![]() |
Кроме того, при расчетах режимов резания и нормы временя проводится обращение к соответствующим нормативным таблицам.
Для каждого варианта может быть подсчитана стоимость перехода Сn:
Cn=Cp+Cu
Где Ср=(tp+tb)3pc
Cu»Cинсtp/Ta
При этом Ср - стоимость обработки поверхности;
Сu- приведенная стоимость режущего инструмента;
3пс- стоимость I мин. работы рабочего и станка;
Cинс- стоимость инструмента;
tp,tb - время рабочего и вспомогательного ходов;
Т- период стойкости инструмента;
a- количество переточек»
Оптимальный переход - это переход, имеющий минимальное значение Сn из всех возможных вариантов перехода
Функция Сn имеет минимум, так как увеличение режимов резания (скорость вращения шпинделя и подачи) приводит сначала к уменьшению tp и соответственно Сn, а затем, когда стойкость инструмента начинает падать из-за увеличения скорости резания, происходит быстрое увеличение стоимости инструмента и кривая стоимости и начинает идти вверх.
Критерий Cn является локальным по отношению к стоимости операции в целом и может с ней не совпадать.
В соответствии о принципом неокончательных решений в результате проектирования перехода может быть разработано несколько вариантов, Первым используется вариант с наименьшим Сn.
Проектирование перехода проводится в такой последовательности:
1. Выбор допустимых способов выполнения переходов.
2. Определение припусков.
З. Определение типоразмеров режущего инструмента.
4. Назначение вспомогательного инструмента.
5. Выбор допустимых вариантов структуры перехода.
6. Расчет режимов резания и определение основного времени для каждого варианта структуры перехода.
7. Определение времени выполнения вспомогательных ходов для каждого варианта структуры перехода.
8. Выбор оптимального по себестоимости перехода.
9. Формирование описания перехода.
10. Разработка задания на проектирование специального инструмента.
Дата добавления: 2018-02-15; просмотров: 606; Мы поможем в написании вашей работы! |
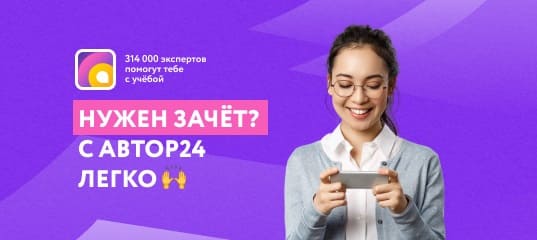
Мы поможем в написании ваших работ!