Расчет оптимальной продолжительности заполнения формы и скорости подъема уровня металла в форме
Содержание
Введение………………………………………………………………………. | 3 |
1 Краткое описание литниковой системы………………………………….. | 4 |
2 Расчет оптимальной продолжительности заполнения формы и скорости подъема уровня металла в форме………………………………. | 7 |
3 Расчет элементов литниковых систем……………………………………. | 8 |
4 Бланк задания………………………………………………………………. | 15 |
5 Результаты расчетов………………………………………………………. | 16 |
6 Список используемых источников………………………………………. | 17 |
Введение
Значение литейного производства в народном хозяйстве чрезвычайно велико ; почти все машины и приборы имеют литейные детали.
Литье является одним из старейших способов, которым еще в древности
пользовались для производства металлических изделий : в начале из меди и
бронзы а затем из чугуна , а позже из стали и др. сплавов.
В 1868 году на Мальцевских заводах впервые были стальные фасонные отливки. Основными процессами литейного производства являются : плавка металла, изготовление форм, заливка металла и охлаждение, выбивка, очистка, обрубка отливок, термическая обработка и контроль качества обработки.
Основной способ изготовления отливок - литье в песчаные формы, в который получают около 80% отливок. Однако точность и шероховатость поверхности отливок, полученных в песчаных формах, во многих случаях не удовлетворяют требованиям современного машиностроения.
|
|
Литейное производство позволяет получить заготовки сложной конфигурации с минимальными припусками на обработку резанием и с хорошими механическими свойствами. Технологический процесс изготовления механизирован и автоматизирован, что снижает стоимость литых заготовок. Достижения современной науки во многих случаях позволяют коренным образом изменить технологический процесс, резко увеличить новые высокопроизводительные машины
и автоматы. Что в конечном счете помогает улучшить качество продукции и
повысить эффективность производства.
Краткое описание литниковой системы
Литниковая система представляет собой совокупность каналов в форме, через которые сплав поступает из ковша в её полость. (рис. 1)
Рис. 1. Литниковая система: 1 – воронка; 2 – стояк; 3 – зумпф; 4 – шлакоуловитель: 5 – питатель: 6 – тупик: 7 – полость формы
Для обеспечения качественного заполнения формы сплавом литниковая система должна удовлетворять следующим требованиям:
– обеспечивать заполнение формы за некоторое оптимальное время;
– создавать возможность надёжного улавливания шлака, неметаллических и газовых включений;
– способствовать плавному поступлению сплава в полость формы без разбрызгивания и размывания поверхностей формы и стержней;
– создавать тепловые условия, благоприятствующие направленному затвердеванию отливки и снижению развивающихся в ней литейных напряжений;
– быть возможно компактной с минимальным расходом металла.
|
|
Важное значение имеет замкнутость литниковой системы для обеспечения улавливания шлака, неметаллических включений и исключения подсоса газов.
Для обеспечения замкнутости литниковую систему делают сужающейся, т.е. по ходу потока сплава площади сечений элементов системы уменьшаются. При этом скорость движения расплава увеличивается, достигая наибольшего значения на выходе в полость формы. Замкнутые системы неприемлемы для сплавов, склонных к вспениванию и окислению (алюминиевых, магниевых, высоколегированных сталей, алюминиевых бронз и латуней). Для таких сплавов применяют незамкнутые, расширяющиеся литниковые системы.
Конструктивно типы литниковых систем разделены на IV класса. В наибольшей степени распространены замкнутые системы III класса [2].
Характер гидравлических процессов в литниковых системах разных типов, методика расчёта последних зависят от типа разливочных ковшей. Для заливки каждой формы нужно выбирать такой ковш, который обеспечивает необходимую массовую скорость заливки металла. Возможность плавного изменения расхода сплава из поворотного ковша в процессе заливки формы является его существенным преимуществом. Однако при использовании поворотных ковшей велика вероятность попадания шлака с поверхности металла в ковше в литниковую систему.
|
|
Важным технологическим параметром, определяющим качество отливки, является температура заливки, т.е. температура сплава в ковше в начале заливки формы.
При выборе уровня подвода сплава необходимо учитывать достоинства и недостатки как подвода сверху, так и подвода снизу.
При подводе сверхуобеспечивается положительный температурный градиент в направлении к прибыли, что улучшает условия её работы и улучшает заполняемость формы. Подвод сверху желателен при изготовлении массивных толстостенных чугунных и стальных отливок, имеющих небольшую высоту.
Подвод снизу целесообразно применять для тонкостенных отливок сложной конфигурации, а также для сплавов, склонных к окислению. Однако ввиду ухудшения при этом заполняемости форм подвод снизу пригоден только для отливок небольшой высоты.
|
|
На практике (с точки зрения удобства формовки) подвод сплава осуществляется на некотором среднем уровне, отвечающем плоскости разъёма формы. При этом нижняя часть отливки заполняется сверху, а верхняя – снизу.
Основные рекомендации при выборе места подвода:
– следует обеспечивать подвод металла в такие места отливки, разогрев которых будет способствовать усилению направленного затвердевания; целесообразно подводить металл под прибыль в толстостенные части отливки из сплавов с большой объёмной усадкой (сталь, ковкий чугун);
– при склонности к внутренним напряжениям металл следует подводить в тонкие части отливки; при этом требование снижения литейных напряжений может быть несовместимым с обеспечением направленного затвердевания;
– необходимо избегать размещения литниковых каналов вблизи границ знаков стержней, поверхности форм и стенок опоки; наименьшие расстояния должны быть в пределах 30…60 мм;
– следует стремиться к созданию одностороннего движения металла в форме, т.е. питатели размещать так, чтобы направление движения металла было в одну сторону и было исключено встречное движение потоков;
– при изготовлении отливок колёсного типа целесообразно подводить металл в ступицу и обод или только в обод; при наличии массивной ступицы целесообразно подводить металл только в обод;
– подвод металла к относительно тонкостенной отливке следует осуществлять в тонкостенные части через большое число питателей, рассредоточенных по её длине;
– следует стремиться к осуществлению подвода металла в форму при её заполнении наиболее коротким путём.
В процессе заливки расход сплава из ковша за счёт изменения его наклона (степени торможения струи) согласовывается с расходом через литниковую систему. Расход сплава через литниковую систему определяется площадью узкого места системы ω уз и величиной действующего напора Нр.
Расчет оптимальной продолжительности заполнения формы и скорости подъема уровня металла в форме
При выборе оптимальной продолжительности заполнения формы нужно учитывать уровень металла в месте подвода сплава. При подводе снизу при прочих равных условиях продолжительность заливки должна быть меньше, чем при подводе сверху, так как при этом нужно обеспечить достаточно высокую температуру сплава в прибыль. При подводе в тонкие части большая продолжительность заливки будет способствовать меньшим внутренним напряжениям в отливке.
Аналитическое определение τmin и τmax в настоящее время затруднительно. Поэтому в практике расчетов широко используются эмпирические зависимости. Наиболее широко известна формула Г.М. Дубицкого:
,
где τопт – оптимальное время заполнения формы, с; S1 – коэффициент продолжительности заливки, зависящий от температуры отливки, рода сплава, места подвода, материала формы и т.д. (значения коэффициента S1 для ряда сплавов приведены в справочниках), выбираем значение коэффициента S = 1,5; δ – преобладающая толщина стенки отливки, м; G – масса жидкого металла, приходящегося на одну отливку в форме, кг.
Под преобладающей толщиной стенки понимается толщина стенки, наиболее удаленной от питателей и находящейся в наиболее неблагоприятных для заливки условиях. При этом δ не всегда совпадает с геометрической толщиной стенки.
Масса заливаемого в форму сплава:
Gж = N ∙ Gотл + Gприб + Gл.с = 1 ∙ 40 + 8 + 2 = 50 кг,
где N – количество отливок в форме, шт; Gотл – черновая масса отливки, кг; Gприб, Gл.с – масса прибылей и литниковой системы (принимается 25–30 % и 4–10 %, соответственно, от Gотл); кг.
= 14,67 с.
3.
4.
5.
Дата добавления: 2018-02-15; просмотров: 1900; Мы поможем в написании вашей работы! |
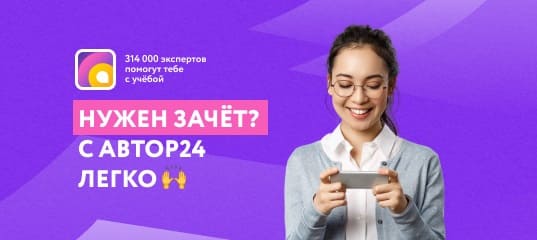
Мы поможем в написании ваших работ!