Расчет тканевого рукавного фильтра
Практическая работа № 9
Очистка газов и воздуха на фильтрах. Расчет тканевого рукавного фильтра
Цель работы: ознакомление обучающихся с основами процесса очистки газов и воздуха на фильтрах, освоение методики расчета рукавного фильтра и приобретение навыков расчета рукавного фильтра.
Задание:
1. Ознакомиться с теоретическим материалом по теме занятия.
2. Изучить методику расчета рукавного фильтра. Разобрать пример расчета рукавного фильтра.
3. Выполнить расчет рукавного фильтра в соответствии с выданным вариантом.
4. Ответить на контрольные вопросы для самопроверки в письменной форме.
Теоретические сведения
В основе работы аппаратов фильтрующего действия лежит процесс фильтрации газа через пористую фильтрующую среду, в ходе которого твердые частицы, содержащиеся в газе, задерживаются, а газ полностью проходит сквозь пористую перегородку.
Обычно процесс фильтрации разделяется на две стадии. В начальной стадии происходит осаждение частиц в чистом фильтре. На этой стадии, называемой стационарной фильтрацией, эффективность улавливания и гидравлическое сопротивление не изменяются во времени и величины их определяются только структурой фильтрующей перегородки, свойствами улавливаемых частиц и параметрами газового потока. Стадия стационарной фильтрации важна для фильтров, работающих при очень низких концентрациях аэрозолей.
|
|
Вторую стадию фильтрации называют нестационарной: она характеризуется структурными и другими изменениями в фильтрующей среде. В результате накопления частиц пыли, воздействия влаги, агрессивных газов и других явлений эффективность улавливания и гидравлическое сопротивление изменяются в процессе фильтрации. Явления, вызывающие изменения эффективности h и сопротивления D р во времени, независимо от их природы, называют вторичными процессами.
В потоке аэрозоля в поровых каналах фильтров или в пространстве между волокнами волокнистых фильтров частицы следуют по линиям тока, огибающим препятствия фильтрующей перегородки или волокна. Частицы, движущиеся в непосредственной близи от поверхности препятствия (волокна), могут просто зацепиться за фильтрующий материал (волокно) из-за своих геометрических размеров. Кроме того, частицы под действием сил инерции, сил тяжести, электрических сил и броуновской диффузии смещаются с линии тока газов, что может привести к осаждению на стенках поровых каналов или волокнах. Частицы, коснувшиеся поверхности волокон, прочно удерживаются на них за счет сил адгезии. Таким образом, возможными механизмами осаждения частиц в поровых каналах фильтров или на волокнах волокнистых фильтров являются:
|
|
1) Механизм касания (зацепления), который проявляется, если частица движется по линии тока газов, проходящей около твердого элемента фильтра на расстоянии, меньшем радиуса частицы или равном ему, т.е. когда она непременно коснется этого элемента и удержится на нем. Если размер частиц больше размера пор, то происходит отсеивание. Ситовой эффект является частным случаем эффекта касания.
2) Инерционный механизм, который проявляется, если масса частицы или скорость ее движения настолько велики, что она не может полностью следовать вместе с газом по линии тока; частица, стремясь по инерции продолжить свое движение по более прямолинейной траектории, сходит с линии тока и осаждается на препятствии.
3) Диффузионный механизм, который проявляется за счет неуравновешенных ударов молекул, находящихся в броуновском движении; в этом случае происходит смещение мелких частиц аэрозоля с линий тока и осаждение их на обтекаемых препятствиях. Чем мельче частицы и меньше скорость течения, тем интенсивнее они смещаются с линий тока, и тем больше вероятность их осаждения на поверхности обтекаемых тел. Этот механизм осаждения подобен массообмену за счет молекулярной диффузии.
|
|
4) Гравитационный механизм, при котором осаждение частиц происходит в результате вертикального смещения частиц с линий тока под действием силы тяжести во время прохождения их через фильтр.
5) Электростатический механизм, который проявляется в том случае, если поровый канал или волокно фильтра несет электростатический заряд или поляризован внешним электрическим полем и создает вокруг себя неравномерное электрическое поле. Нейтральные частицы пыли поляризуются этим полем и притягиваются к поверхности фильтрующего элемента, причем знак заряда в этом случае роли не играет.
Осаждение частиц может происходить посредством одновременного действия нескольких механизмов фильтрации. Для частиц определенного размера возможно преобладание одного или двух механизмов. Роль каждого механизма определяется типом, размером и пористостью фильтрующего элемента, размером и плотностью взвешенных частиц, скоростью газового потока, свойствами газа и действием электростатических сил.
Применяемые фильтрующие пористые перегородки по своей структуре весьма разнообразны, но в большинстве своем они состоят из волокнистых или зернистых элементов, которые могут быть разделены на следующие типы:
|
|
Ø Гибкие пористые перегородки:
1. тканевые материалы из природных, синтетических и минеральных волокон;
2. нетканые волокнистые материалы (войлоки, клееные или иглопробивные материалы, бумага, картон, волокнистые маты);
3. ячеистые листы (губчатая резина, пенополиуретан, мембранные фильтры).
Ø Полужесткие пористые перегородки – слои волокон, стружка, вязаные сетки, расположенные на опорных устройствах или зажатые между ними.
Ø Жесткие пористые перегородки:
1. зернистые материалы – пористая керамика и пластмасса, спеченные или спрессованные порошки металлов (металлокерамика), пористые стекла, углеграфитовые материалы и др.;
2. волокнистые материалы – сформированные слои из стеклянных и метал-лических волокон;
3. металлические сетки и перфорированные листы.
Ø Зернистые слои:
1. неподвижные, свободно насыпанные материалы;
2. периодически или непрерывно перемещающиеся материалы.
В фильтрующих перегородках частицы пыли накапливаются в порах или образуют пылевой слой на поверхности перегородки, и таким образом сами становятся для вновь поступающих частиц частью фильтрующей среды. Однако по мере накопления частиц размер пор и общая пористость перегородки неизбежно уменьшаются, а сопротивление движению газов возрастает. Поэтому в определенный момент возникает необходимость в регенерации – разрушении и удалении пылевого слоя (для снижения гидравлического сопротивления и сохранения начальной скорости фильтрации).
Современные фильтры в зависимости от назначения и величин входной и выходной концентраций улавливаемой дисперсной фазы условно разделяют на три класса:
1. Фильтры тонкой очистки (высокоэффективные или абсолютные фильтры) – предназначены для улавливания с очень высокой эффективностью (обычно выше 99 %) в основном субмикронных частиц из промышленных газов и воздуха при низкой входной концентрации (менее 1 мг/м3) и малой скорости фильтрации (менее 10 см/с). Такие фильтры применяют для улавливания особо токсичных или радиоактивных частиц, а также для ультратонкой очистки воздуха при проведении некоторых технологических процессов или в особо чистых помещениях, в которых воздух служит рабочей средой. Как правило, такие фильтры не подвергаются регенерации.
2. Фильтры для очистки атмосферного воздуха (воздушные фильтры) – используются в системах приточной вентиляции и кондиционирования воздуха. Они рассчитаны на работу при концентрации пыли менее 50 мг/м3, часто при высокой скорости фильтрации (до 2,5–3 м/с). Фильтры этого класса бывают нерегенерируемые, а также периодически или непрерывно регенерируемые.
3. Промышленные (тканевые, зернистые, грубоволокнистые) фильтры применяются для очистки промышленных газов в основном с высокой концентрацией дисперсной фазы (до 60 г/м3). Для периодического или непрерывного удаления накапливающейся в фильтрующей перегородке пыли фильтры этого класса снабжены устройствами для регенерации, позволяющими поддерживать производительность на заданном уровне и возвращать ценные продукты в производство; фильтры этого класса нередко являются частью технологического оборудования.
Тканевые рукавные фильтры
Для тонкой очистки газа чаще всего используются тканевые рукавные фильтры. При этом фильтровальный материал может быть выполнен как из тканого, так и из нетканого материалов.
Главным элементом тканевого фильтра является фильтрующий элемент-рукав, изготовленный из фильтровального материала. Корпус рукавного фильтра как правило разделен на несколько камер (секций), в каждой из которых размещено по несколько рукавов. Отдельные секции имеют самостоятельные системы регенерации.
В настоящее время разработано большое число конструкций тканевых фильтров, которые отличаются по следующим признакам:
1) форме тканевых фильтровальных элементов (рукавные, плоские, клиновые и др.) и наличию в них опорных устройств (каркасные и бескаркасные);
2) месту расположения вентилятора относительно фильтра (всасывающие, работающие под разрежением, и нагнетательные, работающие под давлением);
3) методу регенерации ткани (с импульсной продувкой, с встряхиванием, с обратной продувкой и др.);
4) наличию и форме корпуса для размещения ткани (прямоугольные, цилиндрические, открытые (бескамерные));
5) числу секций в установке (однокамерные и многосекционные);
6) виду используемой ткани (например, стеклотканевые)
Кроме того возможна классификация тканевых фильтров по характеру их работы (длительности работы) с учетом основной особенности их конструкции:
1) тканевые фильтры периодического действия;
2) тканевые фильтры непрерывного действия:
а) многосекционные рукавные фильтры;
б) рукавные фильтры с обратной струйной продувкой;
в) рукавные и плоские фильтры, регенерируемые импульсами сжатого воздуха;
г) рукавные фильтры, регенерируемые пульсирующим потоком газа;
д) рукавные фильтры, регенерируемые встряхиванием;
е) рукавные фильтры с регенерацией встряхиванием и обратной продувкой.
Наибольшее распространение получили тканевые рукавные фильтры с фильтрующим элементом в виде цилиндрического рукава с регенерацией обратной продувкой или импульсной продувкой сжатым воздухом. Фильтрование газов в фильтрах может идти как снаружи внутрь рукава (обычно имеют каркас), так и изнутри рукава наружу.
Расчет тканевого рукавного фильтра
Расчет тканевых фильтров сводится к определению площади фильтрации, на основе которой выбирают типоразмер фильтра и способ регенерации. Кроме того, определяют гидравлическое сопротивление фильтра и продолжительность работы фильтра между регенерациями.
Площадь фильтрации зависит прежде всего от объема запыленного газа с учетом его увеличения за счет увлажнения и подсоса воздуха при движении по газовому тракту, работе оборудования, при охлаждении технологических газов, а также от газовой нагрузки q ф (м3/(м2×мин)) или от эквивалентной ей скорости фильтрования wф (м/мин). Величину удельной газовой нагрузки на фильтр можно определить из выражения
qф=qн С1 С2 С3 С4 С5, (1)
где qн – нормативная удельная нагрузка, зависящая от вида пыли и ее слипаемости, принимаемая равной: qн =1,2 м3/(м2×мин) для возгонов черных и цветных металлов, активированного угля, технического углерода, моющих веществ; qн =1,7 м3/(м2×мин) для кокса, летучей золы, порошков металлов, оксидов металлов, пластмассы, красителей, силикатов, крахмала, сухих химикатов из нефтяного сырья; qн=2,0 м3/(м2×мин) для горных пород, цементной пыли (глинозем, плавиковый шпат, каолин, известняк, кварц, руда, уголь, цемент, порошковые пигменты, резина, сахар); qн=2,6 м3/(м2×мин) – асбест и другие волокнистые материалы, в том числе целлюлозные; пыль, образующаяся при выбивке отливок из формы, гипс, гашеная известь, соль, песок и пыль от пескоструйных аппаратов, кальцинированная сода, тальк;
С1 – коэффициент, учитывающий способ регенерации и принимаемый равным: С1=1,0 – при импульсной регенерации тканей; С1=1,1 – при импульсной регенерации нетканых материалов; С1=0,7–0,85 – при регенерации обратной продувкой с встряхиванием; С1=0,55–0,7 – при регенерации обратной продувкой без встряхивания; С2 – коэффициент, учитывающий начальную запыленность газа и принимаемый равным: С2=1,1 – при запыленности газов до 1-5 г/м3; С2 =1,0 – при запыленности газов до 5-20 г/м3; С2=0,9 – при запыленности газов до 20-70 г/м3; С2 =0,8 – при запыленности газов более 70 г/м3;
С3 – коэффициент, учитывающий дисперсный состав пыли:
dm, мкм . . .>100 50-100 10-50 3-10 <3
С3 . . . . . . .1,2-1,4 1,1 1,0 0,9 0,7-0,9;
С4 – коэффициент, учитывающий влияние температуры газа:
Т, оС . . . 20 40 60 80 100 120 140 160
С4 . . . . 1,0 0,9 0,84 0,78 0,75 0,73 0,72 0,70;
С5 – коэффициент, учитывающий требования к качеству очистки газа оценивается по концентрации пыли в очищенном газе: С5 =1,0 – при концентрации равной 30 мг/м3 и выше; С5 =0,95 – при концентрациях 10 мг/м3 и ниже 30 мг/м3 .
Таблица - Значения констант для определения необходимой поверхности фильтра
Параметр | Условия | Значение |
qн | Жмых. Зерно. Комбикорм. Мука. Кожа. Опилки. Табак. Картон | 3.5 |
Асбест и другие волокнистые материалы, в том числе целлюлозные; пль, образующаяся при выбивке отливок из формы, кальцинированная сод, тальк, при полировке; гипс, гашеная известь, соль, песок и пыль от пескоструйных аппаратов, кальцинированная сода, тальк. | 2.6 | |
Глинозем, плавиковый шпат, каолин, известняк, кварц, руда, минеральная пыль, уголь, цемент, порошковые пигменты, резина, сахар. | 2,0 | |
Кокс, летучая зола, порошки металлов, оксиды металлов, пластмассы, красители, силикаты, крахмал, сухие химикаты из нефтяного сырья. | 1,7 | |
Технический углерод, активированный уголь, моющие вещества, порошковое молоко, возгоны цветных и черных металлов. | 1,2 | |
С1 | Импульсная регенерация ткани | 1,0 |
Импульсная регенерация нетканых материалов | 1.1 | |
Обратная продувка со встряхиванием | 0.7-0,85 | |
Обратная продувка без встряхивания | 0,55-0,7 | |
С3 | dm>100 мкм | 1.2-1,4 |
50< dm<100 | 1,1 | |
10< dm<50 | 1,0 | |
3< dm<10 | 0,9 | |
dm <3мкм | 0,7-0,9 | |
С4 | ![]() | 1 |
![]() | 0,9 | |
![]() | 0,84 | |
![]() | 0,78 | |
![]() | 0,75 | |
![]() | 0,73 | |
![]() | 0,72 | |
![]() | 0,70 | |
| Концентрация пыли в очищенном газе 30 мг/м3 и выше | 1 |
Концентрация пыли в очищенном газе 30 мг/м3 и ниже | 0,95 |
Полное гидравлическое сопротивление, фильтра Dр (Па) складывается из сопротивления корпуса аппарата Dрк и сопротивления фильтровальной перегородки Dрф
Dр=Dрк+Dрф (2)
Гидравлическое сопротивление корпуса фильтра определяется величиной местных сопротивлений при входе и выходе газа из аппарата и распределении потока по фильтровальным элементам
Dрк = , (3)
где z - коэффициент сопротивления, отнесенный к скорости газа во входном патрубке фильтра (при стандартной скорости газов равной 5-15 м/с, коэффициент сопротивления составляет z =1,5-2,5).
Гидравлическое сопротивление фильтровальной перегородки при проведении технических расчетов можно находить по эмпирической формуле
Dр =
, (4)
где wф - скорость фильтрования, м/с; m - динамический коэффициент вязкости газа, Па×с; e тк - пористость ткани, доли ед.; d m - среднемедианный размер пылевых частиц, м; r ч - плотность частиц пыли, кг/м3; z1 - начальная запыленность газа, кг/м3; t ф – время работы фильтра с момента его включения, с; h о – удельное гидравлическое сопротивление фильтровального материала, отнесенное к толщине, равной 1 м при скорости воздуха 1 м/с, Па; e п – пористость слоя пыли.
Пористость слоя пыли зависит от ее дисперсности и может быть определена из выражения
e п = . (5)
Удельное гидравлическое сопротивление ткани можно принимать равным: ho=0,84×105 Па для шерстяной ткани; ho=0,83×105 Па для нитрона НЦМ; ho= 27×105 Па для стеклоткани.
Динамический коэффициент вязкости газа при рабочих условиях (Па×с)
m =
, (6)
где m о – коэффициент динамической вязкости газа (для воздуха m о=17,5×10-6 Па×с), Тг - температура очищаемых газов, К, То=273 оС - температура газа при н. у., С - константа, зависящая от состава газов или иными словами, постоянная Сазерленда для того газа, вязкость которого требуется определить (принимается по данным таблицы П.Б Приложения Б).
Постоянная Сазерленда практически не зависит от температуры (для воздуха при 0 °C CS =113 , при 1600 °C CS =124.
Постоянные фильтрования можно определить по формулам
А= ; (7)
В= . (8)
При ориентировочных расчетах коэффициенты А и В для различных пылей можно принимать из таблицы 1.
Таблица 1 – Значения коэффициентов А и В для некоторых пылей (ткань – лавсан)
dm, мкм | А, м-1 | В, м/кг | Вид пыли |
10-20 2,5-3 0,5-0,7 | (1100-1500)×106 (2300-2400)×106 (13000-15000)×106 | (6,5-16)×109 80×109 330×109 | Кварцевая, цементная Сталеплавильная, возгонная Кремниевая, возгонная |
Если величина оптимального перепада давления на фильтровальной перегородке задана, то можно найти гидравлическое сопротивление фильтрующей перегородки Dp ф и продолжительность периода фильтрования t ф, т. е. время между регенерация
рф = Dр1 + Dр2 = m w ф(А + В z 1 w ф tф) , (9)
t ф = , (10)
где D р1 – сопротивление фильтрующей перегородки, Па, D р2 – сопротивление лобового слоя уловленной пыли, Па, А, В – постоянные фильтрования, определяемые по формулам (7, 8) или по данным таблицы 1.
Количество пыли, осаждающееся на единице площади фильтра за время t ф примерно равно
М1 = z 1 w ф t ф. (11)
Оптимальная продолжительность фильтрации находится экспериментально, но упрощенно эту величину можно определить, задав величину переменного гидравлического сопротивления слоя пыли D р2. Для мелких пылей она не должна превышать 600-800 Па, а для крупных пылей с медианным размером частиц более 20 мкм – 250-350 Па.
Общий объемный расход газа, проходящего через фильтр при проведении регенерации обратной продувкой, равен
V = V 1 + Vp, (12)
где V1 – объемный расход газа, подводимого к фильтру с учетом содержания водяных паров и подсосов по тракту между технологическим агрегатом и фильтром при рабочих условиях, м3/ч; Vр – объемный расход воздуха, подаваемого на обратную продувку и подмешивающегося к очищаемому газу, м3/ч; предварительно он может быть определен из выражения
=
, (13)
где tp – время отключения секции на обратную продувку (обычно до 1 минуты); np - количество регенераций в течение одного часа, определяемое по формуле
np = . (14)
Необходимую площадь фильтрации аппарата , м2, предварительно определяют из выражения
=
, (15)
где q ф - удельная газовая нагрузка при фильтровании, м3¤ (м2× мин).
Выбор фильтра производится по каталогам с запасом 10-15 %.
Фильтрующую поверхность, отключаемую на регенерацию в течение часа, находят по формуле
Fp = , (16)
где Nc - число секций; Fc - фильтрующая поверхность секции, м2.
Далее при расчете уточняют расход воздуха, подаваемого на обратную продувку в течение часа
Vp = w ф nptpNcFc. (17)
После этого находят окончательную площадь фильтрования по формуле
F ф = . (18)
Удельную газовую нагрузку q¢ф, м3¤ (м2×мин), выбранного фильтра находят из выражения
=
. (19)
Продолжительность периода фильтрования для любой секции фильтра tф должна быть всегда больше суммарной продолжительности регенерации остальных секций, т. е. tф > (Nc - 1) tр.
При расчете фильтров, работающих с импульсной регенерацией, расход воздуха на регенерацию не превышает 0,2 % от расхода очищаемого газа и при проведении расчетов может не учитываться.
Дата добавления: 2021-06-02; просмотров: 538; Мы поможем в написании вашей работы! |
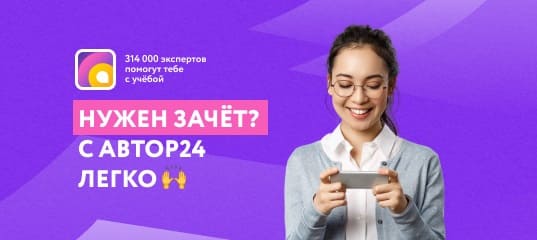
Мы поможем в написании ваших работ!