Анализ неисправностей и предельного состояния элементов оборудования
Техническая эксплуатация оборудования
Общие положения
Под эксплуатацией понимается совокупность использования изделий по назначению, технического обслуживания, хранения и транспортирования.
В технической литературе и официальных эксплуатационно-ремонтных документах применяются термины «Техническая эксплуатация» и «Производственная эксплуатация» машин и оборудования [13].
Первое определение (техническая эксплуатация) охватывает комплекс мероприятий по техническому обслуживанию и ремонту, направленных на обеспечение работоспособности оборудования в течение всего срока его службы.
Второе (производственная эксплуатация) охватывает все, что связано с производственно-технологическим использованием оборудования.
Под термином техническое обслуживание подразумевается комплекс работ для поддержания исправности и работоспособности оборудования при его хранении и транспортировании, подготовке к использованию по назначению, а также в процессе производственной эксплуатации.
Эксплуатационные свойства оборудования характеризуются рядом показателей. Среди них важное место занимает эксплуатационная технологичность, под которой понимают такое свойство конструкции оборудования, которое определяет приспособленность его к работам, выполняемым при подготовке к использованию в процессе непосредственного применения и по окончании использования.
|
|
Эксплуатационная технологичность, в свою очередь, оценивается несколькими количественными показателями, такими как: периодичность технического обслуживания; трудоемкость технического обслуживания, ремонта; коэффициенты приспособленности конструкции изделия к техническому обслуживанию, ремонту, коэффициент применяемости инструмента и др.
Оборудование после приобретения или монтажа не сразу вводится в эксплуатацию, особенно в обустраивающихся производственных участках нового предприятия, а через определенное время, связанное с организацией производства. В течение этого времени должна быть обеспечена его сохранность, для чего выполняют ряд мероприятий.
При хранении оборудования в течение более месяца оно должно быть подвергнуто консервации и очередному техническому обслуживанию с целью сохранения его в полной исправности и работоспособности.
Надлежащим образом должно быть обеспечено хранение оборудования с длительными перерывами в работе (сезонное, энергетическое оборудование и т. п.). При этом неокрашенные и хромированные поверхности покрывают защитным лаком; резиновые изделия снимают и хранят при температуре 15 °С. Также снимают и хранят в закрытых помещениях электрооборудование, аккумуляторы, приборы и др.
|
|
Ввод в эксплуатацию оборудования после его длительного хранения производят в определенной последовательности – производят наружную расконсервацию; проверяют техническое состояние внешним осмотром; устраняют выявленные неисправности; проверяют работоспособность опробованием вхолостую и под нагрузкой на рабочих режимах.
Если в течение гарантийного срока нормальной эксплуатации оборудования обнаруживаются заводские дефекты, то в этом случае заводу-изготовителю предъявляются рекламации, обоснованность которых подтверждается актом, составленным и подписанным специально созданной для этого комиссией, в состав которой при необходимости включаются представители завода-изготовителя.
Морально устаревшее, а также изношенное и непригодное к дальнейшей эксплуатации оборудование после отработки им установленных сроков службы и при условии, что восстановление или модернизация его невозможны или экономически нецелесообразны, подлежит списанию.
Эксплуатационная документация
Согласно ГОСТ 2.601-2006 «Эксплуатационная и ремонтная документация» предусмотрена следующая номенклатура основных эксплуатационных документов: техническое описание; инструкция по эксплуатации; инструкция по техническому обслуживанию; инструкция по монтажу; формуляр; паспорт; этикетка; ведомость ЗИП. Эти документы могут быть объединены в различных вариантах.
|
|
Техническое описание предназначено для изучения устройства и принципа действия изделия, его технических характеристик и возможностей. Структура технического описания включает следующие разделы: введение; назначение изделия; технические данные изделия; состав изделия; устройство и работа изделия и его составных частей; контрольно-измерительные приборы, а также инструмент и принадлежности, поставляемые с изделием; размещение и монтаж; маркировка и пломбирование; тара и упаковка; приложения.
В инструкции по монтажу, пуску, регулированию и обкатке изделия на месте его применения отражается следующая информация: указания мер безопасности; подготовка изделия к монтажу; монтаж; наладка и монтажные испытания; пуск (опробование); регулирование; комплексное опробование; обкатка; сдача в эксплуатацию смонтированного изделия; приложения. Инструкцию по монтажу составляют в случаях, когда перечисленные выше вопросы нецелесообразно или невозможно изложить в инструкции по эксплуатации изделия.
|
|
В инструкции по эксплуатации должны быть отражены и в достаточной мере регламентированы правила и критерии качества производственной и технической эксплуатации технического объекта. Для этой цели инструкция по эксплуатации включает следующие разделы: введение; общие указания; указания мер безопасности; порядок установки; подготовка к работе; порядок работы; измерение параметров; регулирование и настройка; проверка технического состояния; возможные неисправности и способы их устранения; правила хранения; транспортирование; приложения.
Во введении указывается назначение инструкции, возможный период ее использования и т. п. В общих указаниях конкретизируются назначение технического объекта и условия, необходимые для его функционирования (виды энергии и др.). В указаниях мер безопасности приводятся правила (в том числе нормативные) и критерии безопасной эксплуатации (уровни звука, освещенность и др.). В указанном выше стандарте дается более полная характеристика возможного содержания разделов инструкции по эксплуатации.
В инструкции по техническому обслуживанию излагаются порядок и правила технического обслуживания оборудования. Содержание инструкции раскрывается в таких ее разделах, как: введение; общие указания; указания мер безопасности; периодичность и виды технического обслуживания; подготовка к работе; порядок технического обслуживания; порядок технического обслуживания составных частей изделия; консервация; приложения. Инструкция по техническому обслуживанию составляется тогда, когда необходимо установить единые правила технического обслуживания изделия и его составных частей, а также с целью уменьшения объема инструкции по эксплуатации изделия.
Формуляры на изделия составляют в тех случаях, когда необходимо вести учет их технического состояния и данных по эксплуатации (времени работы, наработке, неисправностях, результатах периодического контроля и др.).
Формуляр должен содержать следующую информацию: общие сведения об изделии, его основных технических данных и характеристиках; комплект поставки; свидетельство об упаковке; гарантийные обязательства; сведения о рекламациях, хранении, консервации и расконсервации при эксплуатации; учет работы; учет неисправностей, технического обслуживания; особые замечания по эксплуатации изделия и аварийным случаям; периодический контроль основных эксплуатационно-технических характеристик; проверка измерительных приборов; техническое освидетельствование; сведения об изменениях конструкции, замене составных частей, установлении категории изделия, его ремонте; особые отметки в процессе эксплуатации; приложения.
Паспорт составляют на изделия, для которых гарантированные предприятием-изготовителем технические данные необходимо сообщить потребителю. Паспорт не составляется, если на изделие составляется формуляр. Если паспорт не совмещается в одном документе с техническим описанием и инструкцией по эксплуатации, то он должен содержать такие разделы: общие сведения об изделии; основные технические данные и характеристики; комплект поставки; свидетельство о приеме; сведения о консервации и упаковке; гарантийные обязательства; сведения о рекламациях.
Руководство по эксплуатации составляется в том случае, когда до сведения потребителя необходимо довести описание конструкции, правил использования изделия, его основные характеристики и параметры, гарантируемые заводом-изготовителем.
Руководство по эксплуатации должно состоять из следующих разделов: общие указания; технические данные; комплект поставки; требования по технике безопасности; устройство изделия; подготовка к работе; порядок работы; техническое обслуживание; правила хранения; возможные неисправности и методы их устранения; сведения о приемке; гарантийные обязательства; приложение.
Анализ систем технической эксплуатации оборудования и
критерии их выбора
Под наработкой изделия понимают продолжительность или объем его работы, выраженные в часах или единицах работы, например, для подъемников – в количестве подъемов автомобиля.
Технический ресурс – наработка изделия до предельного состояния от начала эксплуатации или ее возобновления после ремонта определенного вида.
Ресурс работы оборудования связан с показателем безотказности:
![]() | (1) |
Так как P(t) – величина случайная, то действительные ресурсы даже двух единиц оборудования одного типа или модели будут различны.
Техническое состояние технологического оборудования определяет способность и потенциальную возможность качественно и экономично выполнять заданные функции.
Оборудование может находиться в одном из следующих состояний (рисунок 1): исправном и работоспособном; неисправном и работоспособном; неисправном и неработоспособном.
Диаграмма состояний объекта
Исправное состояние характеризуется максимальным q 1 и минимальным q 2 допустимым значением параметра q; D q 1 – допуск на параметр по НТД. Неисправному состоянию соответствует соотношение q t<q 2. Работоспособное состояние: q, находится в пределах D qn. Неработоспособное состояние: qt < q 3.
Как известно из теории надежности, отклонения фактических технических параметров от их начальных значений определяют уровень работоспособности оборудования.
Пусть параметр состояния объекта – h, тогда его изменение во времени f=h(t) показано на рисунке 2.
h0 – начальное значение параметра при t = 0;
h – текущее значение параметра в момент времени t = Т;
Dh = h - h0 — отклонение параметра;
h* – предел исправности изделия (наработка T*);
h** – предельное значение параметра, при котором происходит износ объекта в момент времени t = Т**
Рисунок – Функция изменения параметра состояния
При Dh > h0 - h** возникает отказ; оборудование переходит из работоспособного состояния в неработоспособное.
Вероятность отказа
![]() | (2) |
В процессе эксплуатации оборудование и его составные части подвергаются постоянному воздействию ряда факторов, по-разному влияющих на техническое состояние.
К ним относятся конструктивно-производственные факторы (схемное и конструктивное решение изделия, технология изготовления и сборки, качество производства) и эксплуатационные факторы.
Эксплуатационные факторы делятся на субъективные (связаны с воздействием на оборудование обслуживающего персонала – выбор режимов эксплуатации, ТО и Р, ошибки в управлении и т. п.) и объективные (отражают влияние нагрузок в техпроцессе, температурный режим, физико-химические характеристики материалов и т. п.).
Система ТО и Р представляет собой совокупность взаимодействующих объектов ТО и Р (оборудования), средств ТО и Р, программы ТО и Р и мероприятий. Реализация системы ТО и Р осуществляется силами ИТР и рабочих цехового персонала и РМЦ.
Программа ТО и Р – совокупность основных принципов и принятых решений по применению наиболее эффективных методов и режимов ТО и Р изделий при эксплуатации с учетом заданных требований и условий.
Таким образом, основное значение системы ТО и Р заключается в поддержании области исправного и работоспособного состояния оборудования с максимальным использованием его потенциального ресурса Т.
Недоиспользование ресурса при замене изделий (деталей, сборочных единиц и комплектующих изделий), находящихся все еще в работоспособном состоянии, в процессе ремонта на новые составляет
![]() | (3) |
В зависимости от того, как используется в планировании технической эксплуатации зависимость h - Т, различают следующие системы.
Система проведения ТО и Р по потребности. Ремонт оборудования выполняется только тогда, когда дальнейшая эксплуатация его оказывается невозможной и когда ht>h**. Мероприятия по восстановлению работоспособности выполняются здесь после обнаружения отказа при неработоспособном состоянии оборудования, по объему работ и затратам они соответствуют аварийному режиму. Система проста, но имеет существенные недостатки: отсутствие планирования; невозможность управления надежностью оборудования; невозможность исключения внезапного выхода машины из строя.
Система стандартных ремонтов. Эта система предусматривает принудительный вывод оборудования в ремонт и принудительную замену деталей и сборочных единиц на запасные в заранее установленные сроки эксплуатации независимо от состояния оборудования. Ремонт выполняется по единожды разработанному процессу с определенной схемой, технологией и объемом работ. Система имеет как достоинства, так и недостатки.
К достоинствам относится наличие планирования материально-технического и технологического обеспечения при реализации ТО и Р оборудования.
К недостаткам – неэкономичность технической эксплуатации, так как при проведении работ заменяются все детали, в том числе и те, межремонтный ресурс которых не вышел, а также то, что не учитывается техническое состояние конкретной единицы оборудования.
Система послеосмотровых ремонтов. Согласно этой системе планирование сроков и видов ремонта конкретного оборудования осуществляется на основе анализа его технического состояния во время осмотров.
Достоинством системы является возможность планирования ТО и Р.
Недостатки: субъективизм оценки технического состояния из-за отсутствия объективных критериев и методов определения состояния; отсутствие критериев расчета сроков и видов ремонтов; возможность внеплановых выходов оборудования в ремонт.
Система ТО и Р по состоянию с контролем параметров. Объем, сроки и периодичность ремонтных и профилактических работ устанавливаются на основе объективного анализа технического состояния. Объективная оценка технического состояния производится за счет непрерывного или периодического контроля параметров оборудования.
Планируется в этой системе: часть стандартных операций при соответствующей их переработке; работы по техническому диагностированию и контролю параметров и их периодичность.
Система носит упреждающий характер и обеспечивает максимально возможное использование технического ресурса всех элементов оборудования. Основная сложность – обеспечение точного непрерывного или периодического объективного контроля параметров в процессе эксплуатации, поэтому в настоящее время данная система нашла очень ограниченное применение.
Система планово-предупредительного ремонта и технического обслуживания (ППР). Эта система имеет следующие разновидности:
– ППР по наработке (регламентный);
– ППР по сроку службы (календарный);
– ППР комбинированный.
В соответствии с принципами этой системы оборудование с определенным объемом эксплуатации (наработкой или сроком) подвергают техническим осмотрам и плановым ремонтам различных видов. В промежутках между плановыми ремонтами оборудование подвергают текущему и междуремонтному обслуживанию.
Регламентная система ППР характерна для оборудования или отдельных его агрегатов, систем и сборочных единиц, изменение показателей качества функционирования которых зависит от конкретных условий эксплуатации и действительной наработки. Основной критерий оценки технического состояния – величина физического износа. Календарная система ППР характерна для оборудования, его агрегатов, систем и сборочных единиц, изменение показателей качества функционирования которых зависит от процессов старения в условиях воздействия окружающей среды и не зависит от наработки.
Комбинированная система ППР представляет собой комбинацию регламентной и календарной систем.
Рассмотрим более подробно систему ППР.
Основные принципы, положенные в основу системы:
– все профилактические и ремонтные работы в течение ремонтного цикла проводятся планово, периодически;
– все профилактические и ремонтные работы выполняются в объеме, необходимом для восстановления утраченной на данный момент работоспособности и достаточном для создания запаса работоспособности до следующего ремонта или ТО;
– объем и содержание профилактических и ремонтных работ устанавливается предварительно в зависимости от наработки до момента их проведения, ремонтопригодности и ремонтосложности по типам оборудования и окончательно, на момент проведения работ в зависимости от условий, режимов эксплуатации оборудования в предшествующем периоде и действительного технического состояния на момент проведения работ.
В систему ППР входят: текущее ежесменное (ЕТО) и периодическое обслуживание (ПТО); технический осмотр (О); текущий ремонт (ТР); средний ремонт (СР); капитальный ремонт (КР).
Текущее и периодическое обслуживание, технический осмотр являются составными частями технического обслуживания (ТО) оборудования. Все работы по ТО проводятся в соответствии с инструкциями и планами-графиками в периодах между сменами, после работы и в нерабочие дни.
Виды работ, выполняемых персоналом различных подразделений предприятия по техническому обслуживанию, представлены в таблице слайда 3.
Одним из основных принципов ППР является периодичность и цикличность проведения всех профилактических и ремонтных работ. При планировании используют следующие понятия:
Ремонтный цикл ТРЦ – наименьший повторяющийся период эксплуатации оборудования, в течение которого в определенной последовательности осуществляются установленные виды ТО и Р, предусмотренные нормативной документацией.
Межремонтый цикл ТМЦ – период времени между двумя капитальными ремонтами или с момента сдачи оборудования в эксплуатацию до первого капитального ремонта.
Межремонтный период ТМП – период оборудования между двумя ближайшими плановыми ремонтами.
Межосмотровый период Тмо – период между двумя осмотрами или ремонтами и осмотром.
Структура межремонтного цикла – последовательность выполнения ремонтных работ и работ по техническому обслуживанию в межремонтном цикле (рисунок, слайд 5).
Структура межремонтного цикла зависит от сложности и количества потребных ремонтов, конструкционных особенностей оборудования, срока износа основных деталей, условий эксплуатации.
Величины циклов и периодов в структуре определяются по формулам:
![]() | (4) (5) (6) (7) |
где ТН – нормативный срок работы оборудования между ремонтами (определяется как средняя наработка на отказ);
Кпр, Киз, Кэо – коэффициенты, учитывающие тип производства, вид обрабатываемых изделий, условия эксплуатации оборудования;
nс, nт, – количество средних и текущих ремонтов в межремонтном цикле; n0 – количество осмотров в межремонтном цикле.
На основании структуры межремонтного цикла на предприятии составляют графики капитального, среднего и текущего ремонтов, а также периодических профилактических осмотров.
Возможны следующие сочетания ремонтов и осмотров в межремонтном цикле:
– капитальный, средний, текущий ремонты – осмотр;
– капитальный, средний ремонты – осмотр, совмещенный с текущим ремонтом;
– капитальный, текущий ремонты – осмотр.
Для различных видов специфичного и уникального оборудования нормативы ППР должны разрабатываться главным механиком предприятия и утверждаться директором.
Разработка нормативов ППР для такого оборудования осуществляется на основе сравнения его технических показателей (надежность, интенсивность отказов, конструктивная сложность, ремонтная сложность и др.) с типовыми видами оборудования.
Структура межремонтных циклов оборудования задается в табличной форме и схематичном изображении чередования работ (таблица слайдах 6, 7).
Степень сложности ремонта оборудования или его агрегата (составной части) оценивается категорией ремонтной сложности R. Она зависит от конструктивных и технологических особенностей. Устанавливается R на основании анализа конструкции и технических характеристик.
Категория ремонтной сложности оценивается в единицах ремонтной сложности (или в ремонтных единицах).
Единица ремонтной сложности – это ремонтная сложность некоторого условного агрегата с нормированными затратами времени на выполнение работ.
Нормируемая трудоемкость на единицу ремонтной сложности зависит от профиля предприятия. Для механической части оборудования при капитальном ремонте:
а) предприятия машиностроения – 50 ч;
б) ремонт и эксплуатация автомобилей – 35 ч;
в) для теплотехнического оборудования – 40 ч.
Ремонтная сложность оборудования указывается числом единиц и буквой R (1R, 10R, 15R и т. д).
За эталон принят:
– для технологического, металлорежущего, подъемно-транспортного, кузнечно-прессового, литейного и деревообрабатывающего, токарно-винторезный станок 1К62 с ремонтной сложностью 19,5R(10,5Rм и 9Rэ);
– для электротехнического оборудования – асинхронный электродвигатель с короткозамкнутым ротором в защищенном исполнении мощностью 0,6 кВт с ремонтной сложностью 1R.
Для оборудования АТП и ПТС нормативы времени, распределенные по видам работ для единицы ремонтной сложности, представлены в таблице слайда 8.
Ремонтная сложность механической части оборудования Rм рассчитывается по формуле
![]() | (8) |
где RK RГ, RП – ремонтная сложность кинематической, гидравлической, пневматической частей.
Ремонтная сложность электрической части оборудования RЭ определяется по формуле
![]() | (9) |
где Rд, Rа — ремонтная сложность электродвигателей, арматуры (аппаратура, приборы, провода и т. п).
При планировании ремонтов ремонтная сложность используется для расчета ряда показателей:
а) трудоемкость ремонта в целом по механической и электрической частям оборудования:
![]() | (10) |
где tН – нормативы времени на 1 единицу ремонтной сложности; R – категории ремонтной сложности;
б) продолжительность ремонта оборудования:
![]() | (11) |
где Np — число ремонтных рабочих, работающих в одну смену; Tсм — длительность смены; NCM — количество смен; Кн – коэффициент выполнения нормы ремонтными рабочими;
в) потребное количество рабочих:
![]() | (12) |
где tт, tс, tк – нормативы времени на 1 единицу ремонтной сложности для текущего, среднего и капитального ремонтов; ∑ Rт, ∑ Rс, ∑ Rк – суммарное ежегодное количество единиц оборудования (единиц ремонтной сложности) при текущем, среднем и капитальном ремонтах; Ф – годовой фонд времени рабочего;
г) количество дежурных слесарей:
![]() | (13) |
где ∑ R – сумма ремонтных единиц обслуживаемого оборудования; Ксм — коэффициент сменности работы оборудования; G – норматив межремонтного обслуживания на одного слесаря в смену в единицу ремонтной сложности.
Инженерное обеспечение технического
обслуживания оборудования
В процессе технической эксплуатации оборудования должно выполняться два вида его технического обслуживания – ежесменное техническое обслуживание (ЕТО) и периодическое техническое обслуживание (ТО).
При ЕТО рекомендуется выполнять такие работы:
– наружный осмотр, чистку и смазку оборудования;
– устранение небольших неисправностей и регулировку отдельных устройств;
– надзор за соблюдением правильности эксплуатации оборудования.
Указанный перечень работ ориентирован на техническую эксплуатацию оборудования применительно к системе ППР по наработке (или ресурсу).
Однако применение этого варианта системы ППР без постоянного учета технического состояния оборудования неэффективно с точки зрения управления безотказностью и долговечностью этого оборудования. Поэтому указанный перечень работ целесообразно дополнить операцией, работой по контролю технического состояния (КТС) оборудования. Алгоритм КТС представлен на рисунке слайда 9.
Оценка (контроль) технического состояния (КТС) – комплекс процедур и мероприятий, позволяющий определить исправность и степень работоспособности оборудования.
Различают следующие КТС: ежесменный (ЕС КТС); еженедельный (ЕН КТС); периодический (П КТС); предремонтный (ПР КТС); аварийный (А КТС) – выполняется по потребности.
Инженерное обеспечение ежесменного технического обслуживания оборудования сводится к проработке методов и средств КТС, поиска и устранения неисправностей (при начале эксплуатации импортных, новых моделей оборудования).
При периодическом, плановом ТО рекомендуется выполнять такие работы, как:
– постоянную очистку оборудования и помещений, в которых оно установлено;
– ежесменные и периодические технические осмотры;
– периодическую замену смазки в картерах оборудования;
– периодическую промывку резервуаров и систем смазки;
– регулировку подвижных сопряжений деталей в механизмах оборудования;
– подтяжку креплений разъемных соединений оборудования;
– периодическую проверку параметров оборудования и его юстировку (контроль точности);
– проверку и испытание электрооборудования и программных устройств.
Как видно из перечисленного вида работ, при плановом ТО контроль технического состояния уже предусмотрен, хотя лишь по точности и выходным параметрам функционирования оборудования. Однако и здесь, как и при ЕТО, заложены принципы системы ППР по наработке (замене подлежат детали, имеющие ресурс меньше межремонтного ресурса, т. е. фактически без учета их технического состояния). Таким образом, этот вид ТО, с точки зрения инженерного обеспечения, также сводится к проработке методов и средств КТС, а также методов и средств поиска и устранения неисправностей для новых или впервые внедряемых на предприятии моделей импортного или отечественного оборудования.
В процессе ТО оборудования рекомендуется проводить пять видов КТС, из которых ЕС КТС, ЕН КТС проводятся постоянно, ТО КТС и ПР КТС можно проводить планово в сроки проведения периодического ТО и перед плановыми ремонтами, а аварийный (А КТС) – по потребности. В зависимости от интенсивности, ремонтосложности, количества однотипного оборудования может оказаться рациональным ЕС КТС не проводить, ограничиваясь лишь ЕН КТС.
Ежесменный контроль технического состояния в принципе является обязательным, его содержание и порядок проведения следующие:
– производится предварительная оценка технического состояния оборудования на основе опроса (экспертных оценок) лиц, работающих на этом оборудовании;
– проводится регистрация средствами контроля технических и энергетических параметров, их экспертная оценка и анализ соответствия заданным значениям.
При отсутствии отклонений значений параметров от нормативных КТС считается завершенным.
При наличии отклонений параметров необходимо выполнить следующее:
– установить абсолютные значения выявленных отклонений параметров;
– провести операции по регулировке, поднастройке регулирующей аппаратуры и элементов, деталей машины с целью компенсации изменений звеньев размерных цепей и отклонений параметров.
Результаты контроля технического состояния заносятся в журнал учета и контроля технического состояния (таблица слайда 10).
Средствами ЕС КТС являются: элементы контроля и сигнализации, постоянно установленные на контролируемой машине и дополнительные средства прямого измерения; алгоритмы контроля технического состояния машины.
Методами ЕС КТС являются: опрос обслуживающего машину персонала; регистрация показаний элементов контроля и сигнализации; сравнение результатов с заданными значениями.
ЕС КТС проводится в конце смены слесарем по обслуживанию оборудования, является обязательным, периодическим и включает проведение анализа работоспособности машины за неделю. Он совмещается с ежесменным контролем и проводится, как правило, в последний день рабочей недели.
При установлении наличия за неделю отклонений параметров необходимо:
1. Выявить характер возможных отклонений технологических и энергетических параметров (случайные, систематические) путем анализа данных, зарегистрированных в журнале контроля технического состояния.
2. Сравнить интенсивность и абсолютные значения систематических отклонений с заданными значениями.
3. Определить возможные причины систематических отклонений.
4. Сформулировать альтернативный вывод:
а) о проведении регулировочно-настроечных работ систем, являющихся источниками причин;
б) контроля технического состояния в объеме предстоящего планового ТО. Дата его заносится в график ППР.
Результаты контроля технического состояния заносятся в журнал учета контроля технического состояния.
Средствами EH KTC являются: элементы контроля и сигнализации, постоянно установленные на контролируемой машине, и дополнительные средства прямого контроля; алгоритмы контроля технического состояния машины.
Методом EH KTC является анализ данных о контроле технического состояния за неделю. Этот вид КТС проводится слесарем по обслуживанию оборудования при участии представителей отдела главного механика (энергетика).
Контроль технического состояния в объеме периодического ТО (ТОКТС) является плановым. При этом анализу подвергаются не только выходные параметры качества функционирования оборудования, но и параметры его сборочных единиц, сопряжений, деталей. Содержание и порядок проведения ТО КТС заключается в следующем:
1. Проведение предварительного анализа причин появления систематических отклонений технологических и энергетических функциональных параметров оборудования.
2. Определение дефектных деталей, элементов оборудования прямым (путем разборки предполагаемой неисправной сборочной единицы и замера значений параметров сопряжений, деталей) или косвенным методами (по остаточному ресурсу, безразборными методами, например, методом подобия технических состояний).
3. После замены дефектных деталей, элементов проведение операции по регулировке, поднастройке соответствующих механизмов, систем оборудования.
4. Проведение повторного КТС в объеме ЕН КТС.
При несоответствии или предельных значениях выходных параметров оборудования по отношению к их нормативным значениям, необходимо скорректировать сроки ближайшего планового ТО или ремонта, намеченных планом-графиком ППР.
Средствами контроля являются элементы контроля и регистрации, штатно установленные на контролируемом оборудовании, и дополнительные средства прямого контроля.
Методами контроля при ТО КТС являются: анализ данных о КТС после последнего проведенного ТО КТС, косвенные методы оценки состояния деталей, сопряжений оборудования.
Этот вид КТС совмещается с одним из ЕН КТС и проводится высококвалифицированным слесарем по ремонту и обслуживанию оборудования при участии инженера по оборудованию отдела главного механика предприятия.
Предремонтный контроль технического состояния оборудования (ПР КТС) является контролем, проводимым перед плановым ремонтом, поэтому заранее планируется. Порядок и содержание его заключаются в следующем:
1. Проведение контроля технического состояния в объеме ТО КТС.
2. Определение наиболее вероятных причин зафиксированных систематических отклонений.
3. Проведение КТС источников причин систематических отклонений параметров с возможными состояниями источников:
а) без демонтажа и разборки;
б) без демонтажа с частичной разборкой;
в) с демонтажем, но без разборки;
г) с демонтажем и разборкой.
4. Проведение КТС системы контроля самой машины.
5. Проведение по результатам КТС технического обслуживания источников причин с регулировкой, заменой сборочных единиц, деталей, материалов, рабочих сред и др.
6. Проведение повторного КТС источников причин.
7. Проведение повторного КТС всей машины в объеме ЕН КТС.
8. Принятие решения о сроках выполнения ближайшего или иного предстоящего планового (по плану-графику ППР) ремонта оборудования.
9. Регистрация проведенного контроля технического состояния в журнале учета.
Средствами контроля являются: приборы прямого и косвенного контроля, имеющиеся и дополнительно установленные на машине; тесты, алгоритмы, критерии.
Для ПР КТС методами контроля являются: тестирование, в том числе методом подобия, термовиброакустические измерения, анализ экспертных оценок; сравнение действительных значений параметров, критериев с заданными.
По результатам ПР КТС отделом главного механика (энергетика) составляется акт. Сроки контроля заранее планируются, например, за неделю до планового ремонта. ПР КТС проводится в нерабочее время для персонала, эксплуатирующего данное технологическое оборудование.
При выполнении рассмотренных выше видов КТС основной целью является определение истинных значений параметров деталей, сопряжений, определяющих их состояние и возможность дальнейшей эксплуатации.
Использовать для этого прямой метод определения значений – непосредственное измерение размеров, деформаций и т. д. – не всегда возможно и, в принципе, нежелательно, так как этот метод связан с разборочно-сборочными операциями, увеличивающими время простоя оборудования и, как правило, снижающими кинематическую и иную точность оборудования. Чтобы избежать этого, используют различные косвенные методы измерений, диагностики.
К таким методам относится, например, метод подобия функционирования, в котором действительное состояние машины рассматривается как аналог заданному. Соответствие действительного технического состояния заданному в этом случае можно оценивать критериями подобия, которые содержат информацию о процессах, реализуемых машиной, механизмом, и могут быть составлены из групп параметров, связанных функциональной зависимостью.
При контроле технического состояния интерес представляют критериальные зависимости, составленные из диагностических (скорость, давление и т. п) и структурных (зазор и т. п) параметров машины, агрегата, механизма.
В составе работ по техническому обслуживанию оборудования важное место занимают работы по выявлению причин возможных или имеющихся на момент ТО неисправностей. Как правило, каждая отдельная неисправность в общем случае является следствием множества возможных причин. Рациональная последовательность выявления истинной причины, особенно сложных систем оборудования, является условием сокращения времени ТО и повышения его качества.
Один из методов установления рациональной последовательности поиска и устранения причин неисправностей основан на статистических (экспертных) данных о времени поиска и устранения причин (tпy)i, а также о вероятности их появления Р0i (здесь i — порядковый номер причины).
Сущность метода заключается в определении коэффициента последовательности проверок Кпр i, представляющего собой отношение Poi/tпуi, по всем i-м причинам и сравнении значений этих коэффициентов.
Первой проверяется причина, для которой значение Кпр i является максимальным, последней проверяется причина с минимальным значением Кпр i. Для сложных систем после установления рациональной последовательности поиска и устранения причин неисправностей целесообразно составлять схемы поиска и устранения, на которых показывается последовательность и содержание работ по устранению причин. В принципе такая схема является алгоритмом поиска и устранения неисправностей.
В последнее время при технической эксплуатации импортного оборудования широко используется его техническое обслуживание отечественными или смешанными сервисными организациями, фирмами-поставщиками, фирмами-изготовителями. В этом случае периодичность и содержание ТО оговариваются контрактами.
Анализ неисправностей и предельного состояния элементов оборудования
Образование и развитие неисправностей оборудования объясняется действием существующих закономерностей. Неисправности появляются в результате постоянного или внезапного снижения физико-механических свойств материала деталей, их истирания, деформирования, смятия, коррозии, старения, перераспределения остаточных напряжений и других причин, вызывающих разрушение деталей. В большинстве случаев происходят изменения в сопряжениях – нарушения заданных зазоров в подвижных соединениях или натягов в неподвижных. Практически любая неисправность является следствием изменения состава, структуры или механических свойств материала, конструктивных размеров деталей и состояния их поверхностей.
Появление неисправностей обусловлено конструктивными, технологическими и эксплуатационными факторами.
К конструктивным факторам относятся: расчетные нагрузки, скорости относительного перемещения, давления, материалы, их физико-механические характеристики и структура, конструктивное исполнение деталей и сборочных единиц, форма и величина зазоров или натягов в сопряжениях, макрогеометрия, шероховатость и твердость поверхностей, условия смазывания и охлаждения деталей.
Технологическими факторами являются приемы, способы, точность и стабильность получения заготовок, виды механической, термической, упрочняющей и финишной обработки при изготовлении деталей, правильность сборки, регулирования, приработки и испытания узлов, агрегатов и машин.
Эксплуатационные факторы оказывают решающее воздействие на сохранение свойств элементов машин, обеспечиваемых их конструкцией и технологией изготовления. К эксплуатационным относятся следующие факторы:
– определяемые назначением машины, ее нагрузочными и скоростными режимами, а также интенсивностью эксплуатации;
– не зависящие от назначения машины (условия эксплуатации, своевременность, полнота и качество технического обслуживания и др.).
Например, детали типа валов и осей в процессе эксплуатации подвергаются действию переменных нагрузок. Эти детали испытывают четыре вида нагрузки: односторонний изгиб, одностороннее кручение, переменный изгиб и переменный изгиб с кручением. Около 75% цилиндрических поверхностей имеют различные концентраторы напряжений: галтели, пазы под шпонки, кольцевые канавки, отверстия, лыски и резьбы.
Различный срок службы (ресурс) даже однотипных деталей обусловлен многими причинами. Основными из них являются следующие: разнообразие функций деталей в машине; широкий диапазон изменения действующих на детали нагрузок; наличие как активных (движущихся), так и пассивных (неподвижных) деталей; разнообразие видов трения в сопряжениях; использование разных материалов в парах трения, вызванное необходимостью снижения сил трения; отклонения в свойствах материалов; точность и качество обработки сопрягаемых деталей; условия эксплуатации.
Неисправности деталей машин можно разделить на три группы: износы, механические повреждения и химико-тепловые повреждения.
Износы деталей машин определяются давлением, циклическими нагрузками, режимом смазывания и степенью его стабильности, скоростью перемещения поверхностей трения, температурным режимом работы деталей, степенью агрессивности окружающей среды, качеством обработки и состоянием поверхностей трения и т. д.
Различают следующие виды изнашивания:
1. Мехнические: абразивное; гидроабразивное; газообразивное; усталостное; кавитационное.
2. Молекулярно-механическое (при заедании).
3. Коррозионно-механическое: окислительное; фретинг-коррозия.
В зависимости от условий работы все детали по виду изнашивания можно разбить на пять групп.
К первой группе относятся детали, для которых основным фактором, определяющим их долговечность, является абразивное изнашивание.
Ко второй (шлицевые детали, зубчатые муфты, венцы маховиков) – детали, у которых основным фактором, лимитирующим долговечность, является износ вследствие пластического деформирования.
К третьей (гильзы, головки блоков цилиндров, распределительные валы, толкатели, поршни, поршневые кольца) – детали, для которых доминирующим фактором является коррозионно-механическое или молекулярно-механическое изнашивание.
К четвертой (шатуны, пружины, болты с циклической осевой нагрузкой) – детали, долговечность которых лимитируется пределом выносливости.
К пятой (коленчатые валы, поршневые пальцы, вкладыши подшипников, отдельные зубчатые колеса коробки передач и др.) – детали, у которых долговечность зависит одновременно от износостойкости трущихся поверхностей и предела выносливости материала деталей.
Интенсивность нарастания износа деталей и изменение зазоров подвижных сопряжений в зависимости от продолжительности работы происходят в определенной закономерности (см. рисунок).
Первый период характеризуется интенсивным нарастанием износа за сравнительно малый период работы – это время приработки деталей. Износ в этот период во многом зависит от шероховатости поверхности деталей, условий смазывания и нагрузки. С ростом шероховатости рабочей поверхности, а также с увеличением нагрузки в начальный период работы износ деталей значительно повышается.
Рисунок – Интенсивность износа
Второй период, наибольший по протяженности, соответствует нормальной работе деталей и сопряжений. За время нормальной эксплуатации износ деталей увеличивается на сравнительно небольшую величину, часто называемую естественным износом. Интенсивность изнашивания при этом во многом зависит от условий эксплуатации, а также от своевременности и качества проводимого технического обслуживания.
Третий период характеризуется интенсивным нарастанием износа деталей вследствие увеличивающихся зазоров в сопряжениях.
Механические повреждения вызываются ударным воздействием,
перенапряжением, концентрацией местных нагрузок.
К ним относятся: трещины; пробоины; риски и задиры; выкрашивание; разрушение; изгибы; вмятины; скручивание и др.
Химико-тепловые повреждения возникают в результате одновременного воздействия нескольких физических и/или химических факторов.
К ним относятся: коробление; коррозия; раковины; нагар; накипь; электроэрозионное разрушение; изменение намагниченности и др.
Неисправности деталей называются дефектами. Различают дефекты:
а) по вероятности появления: закономерные; случайные;
б) связям с другими дефектами: независимые; зависимые;
в) возможности устранения: устраняемые; неустраняемые;
г) виду: нарушения целости; несоответствие формы; несоответствие размеров; отклонение качества поверхности;
д) причине возникновения: конструкционные; производственные; эксплуатационные.
Вероятность появления дефектов количественно оценивается на основании обработки статистических материалов и характеризуется коэффициентами повторяемости дефектов.
Коэффициент повторяемости дефекта определяют из выражения
,
где nд – число деталей с данным дефектом из общего количества продефектованных; nв – общее число продефектованных ремонтопригодных деталей.
Дата добавления: 2021-06-02; просмотров: 463; Мы поможем в написании вашей работы! |
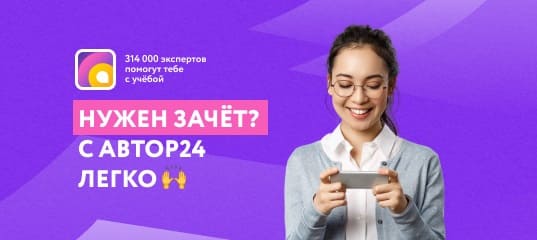
Мы поможем в написании ваших работ!