Плотность газожидкостной смеси
М. В. Клыков
МОДЕЛИРОВАНИЕ ПЛЕНОЧНЫХ
ТЕПЛОМАССООБМЕННЫХ АППАРАТОВ
Машины и аппараты химических производств |
Моделирование энерго – и ресурсосберегающих процессов в химической технологии, нефтехимии и биологии |
Основная образовательная программа |
Бакалавры |
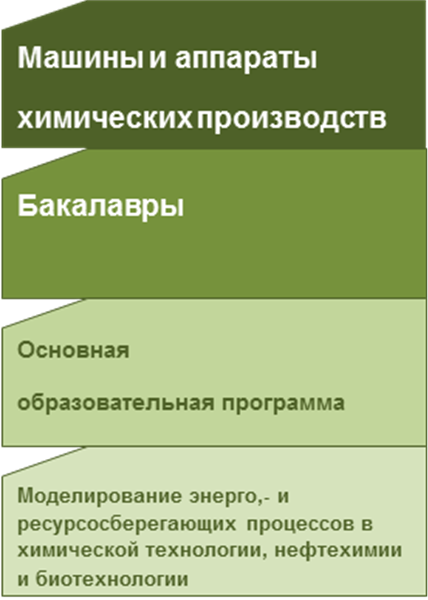
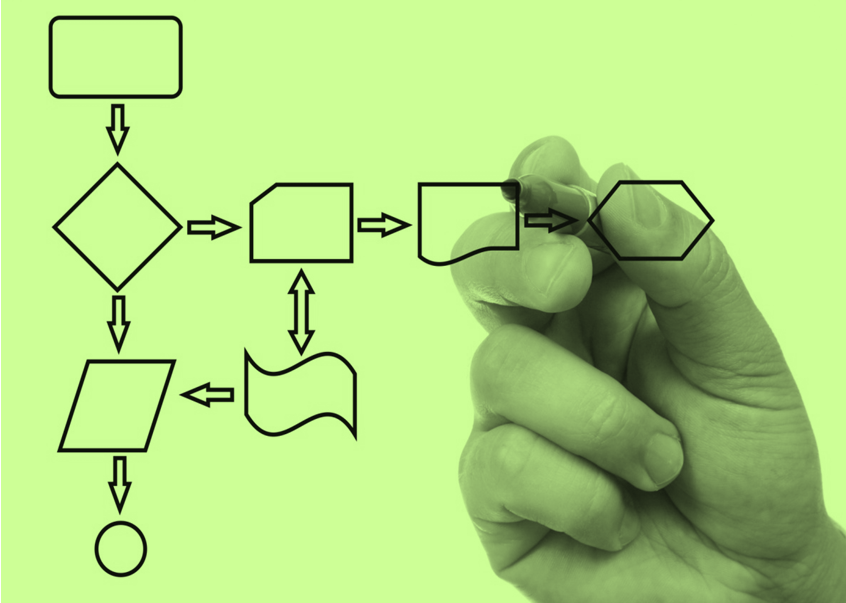
Уфа
Издательство УГНТУ
2015
Министерство образования и науки Российской Федерации федеральноЕ государственноЕ бюджетноЕ
образовательноЕ учреждениЕ
высшего профессионального образования
«УФИМСКИЙ ГОСУДАРСТВЕННЫЙ НЕФТЯНОЙ
ТЕХНИЧЕСКИЙ УНИВЕРСИТЕТ»
Филиал УГНТУ в г. Салавате
МОДЕЛИРОВАНИЕ ПЛЕНОЧНЫХ ТЕПЛОМАССООБМЕННЫХ АППАРАТОВ
Учебное пособие
Уфа
Издательство УГНТУ
2015
УДК 621.016
ББК 35.11
К 51
Утверждено Редакционно – издательским советом УГРТУ в качестве учебного пособия.
Рецензенты:
Кандидат технических наук, начальник отдела нефтехимических производств и производственных стоков ООО «Научно-технологическая компания Салават» К.А.Куцуев
Кандидат технических наук доцент кафедры «Оборудование предприятий нефтепереработки и нефтехимии» ФГБОУ ВПО УГНТУ Т.В Алушкина
Клыков М.В.
К 51 Моделирование пленочных тепломассообменных аппаратов: учеб. пособие.-Уфа: Издательство УГНТУ, 2015.- 92 с.
|
|
ISBN 978-5-7831-1303-1
Даны основные понятия моделирования энерго- и ресурсосберегающих процессов, приведена конструкция оборудования пленочных тепломассообменных аппаратов, их математическое описание и модели пленочных прямоточных, противоточных, многопоточных испарителей и модель ректификации с использованием теплового насоса с совмещенным тепломассообменом.
Учебное пособие предназначено для студентов бакалавриата, обучающихся по направлению подготовки 18.03.02 «Энерго- и ресурсосберегающие процессы в химической технологии, нефтехимии и биотехнологии», профиль подготовки «Машины и аппараты химических производств» (бакалавры) для изучения дисциплины «Моделирование энерго- и ресурсосберегающих процессов в химической технологии, нефтехимии и биотехнологии», а также в дипломном проектировании и научно-исследовательской работе студентов.
УДК 621.016
ББК 35.11
ISBN 978-5-7831-1303-1 | © ФГБОУ ВПО «Уфимский государственный нефтяной технический университет», 2015 © Клыков М.В., 2015 |
Содержание
Введение | 5 |
1 Основы моделирования и анализа энерго- и ресурсосберегающих процессов | 7 |
1.1 Цели, задачи и способы моделирования энерго- и ресурсосберегающих процессов | 7 |
1.2. Методы построения математических моделей | 15 |
2 Модели пленочных испарителей | 17 |
2.1 Конструкции и область применения пленочных испарителей | 17 |
2.2 Пленочные испарители с падающей пленкой | 20 |
2.3 Распределительные устройства пленочных испарителей | 25 |
2.4 Пленочные аппараты с распределением жидкости по трубам с отрицательной обратной связью по парообразованию | 33 |
2.5 Гидродинамика потоков в пленочных тепломассообменных аппаратах | 39 |
2.5.1 Однофазное установившееся течение жидкости | 39 |
2.5.2 Неустановившееся течение и распределение жидкости в пленочных аппаратах | 45 |
2.5.3 Двухфазное течение газа и жидкости в пленочных аппаратах | 48 |
2.6 Модели процессов в пленочных испарителях с падающей пленкой | 52 |
2.6.1 Распределение жидкости по трубам в прямоточных и противоточных пленочных испарителях с отрицательной обратной связью по парообразованию | 52 |
2.6.2 Тепловой процесс в пленочных испарителях с падающей пленкой | 55 |
2.6.3 Расчет процесса однократного испарения в испарителях | 57 |
2.6.4 Равновесие между паровой и жидкой фазами | 58 |
2.6.5 Давление насыщенных паров | 59 |
2.6.6 Динамические свойства распределительных устройств с отрицательной обратной связью по парообразованию | 60 |
2.7 Распределение жидкости в многопоточных испарителях с восходящей пленкой | 65 |
3 Модель ректификации с использованием теплового насоса с совмещенным тепломассообменом | 77 |
Библиографический список | 87 |
|
|
|
|
Введение
Задачи энергосбережения, определенные в Законе РФ «Об энергосбережении», предполагают реализацию правовых, организационных, научных, производственных, технических и экономических мер, направленных на эффективное использование энергетических ресурсов и вовлечение в хозяйственный оборот возобновляемых источников энергии.
Одним из самых энергоемких и широко используемых процессов на предприятиях нефтепереработки и нефтехимии являются тепломассообменные процессы ректификации смесей. Оборудование процессов имеет сложную конструкцию, большую металлоемкость и повышенное потребление энергии в виде греющих (чаще всего водяной пар) и охлаждающих агентов. Расход энергии в значительной мере зависит от совершенства оборудования, то есть от эффективности контактных устройств в колоннах и эффективности кипятильников.
|
|
Повышение коэффициента теплопередачи в кипятильниках, снижение образования отложений на греющих поверхностях позволяет полнее использовать энергетический потенциал греющего водяного пара за счет его конденсации при более низких давлении и температуре.
Пленочные испарители в значительной степени удовлетворяют этим требованиям. Высокая скорость стекания жидкости в падающей пленке повышает коэффициент теплопередачи в сравнении с кипением жидкости в затопленных трубах в 2-5 раз. В связи с испарением жидкости в поверхности стекающей пленки в пленочных аппаратах в сравнении с кипением в затопленных трубах, где пар образуется на поверхности трубы, снижается или полностью исключается образование отложений на теплообменной поверхности труб.
Внедрение принципов термодинамически обратимой ректификации с использованием тепловых насосов и интеграции тепловых потоков возможно с применением процессов нагрева и испарения в пленочных трубчатых аппаратах. При помощи тепловых насосов возможно использование теплоты сжатия верхних паров ректификационных колонн для нагрева и испарения сырья, в результате чего снижается потребление энергоресурсов от внешних источников.
В массообменном аппарате с совмещенными потоками процесс ректификации с использованием теплового насоса и интеграции тепловых потоков осуществляется в одном аппарате.
В соответствии с постановлением Правительства РФ №857 от 25.10.2010, тепловые насосы включены в перечень объектов и технологий, имеющих высокую энергетическую эффективность, осуществление инвестиций в создание которых является основанием для предоставления инвестиционного налогового кредита.
Моделирование и оптимизация пленочных тепломассообменных аппаратов позволяет обеспечить снижение потребления энергии и материальных ресурсов для осуществления процессов ректификации.
1 Основы моделирования и анализа энерго- и ресурсосберегающих процессов
Моделированием называется процесс создания модели, ее исследования и распространения результатов на оригинал. Математическая модель энерго- и ресурсосберегающих процессов является математическим описанием, представленным в виде зависимостей одного параметра, характеризующего процесс, от другого и предназначена для использования поиска оптимальных параметров процесса и оборудования для его осуществления отвечающих требованиям энерго – и ресурсосбережения. В наиболее простом случае математическое описание энерго- и ресурсосберегающих процессов и аппаратов представляет собой одно уравнение или систему уравнений, связывающих функции отклика с влияющими факторами. Функция отклика должна характеризовать энерго- и ресурсосбережение процесса.
1.1 Цели, задачи и способы моделирования
энерго- и ресурсосберегающих процессов
Одной из главных задач изучения энерго- и ресурсосберегающих процессов (ЭРСП) является их анализ с целью дальнейшей оптимизации — поиска таких параметров ведения процесса, при которых будут получены наилучшие результаты по производительности, качеству конечного продукта и энерго- и ресурсосбережению.
Анализ ЭРСП осуществляется при разработке и проектировании нового нефтехимического или нефтеперерабатывающего производства либо при эксплуатации действующего для его модернизации (реконструкции), для сравнения различных вариантов реализации процесса. В общем смысле слова анализ ЭРСП заключается в получении сведений о следующих аспектах производственного процесса:
— состоянии ЭРСП;
— показателях его функционирования и эффективности;
— влиянии на ЭРСП схемы и структуры технологических связей, свойств и состояния элементов;
— влиянии условий эксплуатации процессов и аппаратов на общую производственную технологию и энергоэффективность.
Исследование любого ЭРСП при переходе от расчета (проектирования) к внедрению в промышленных масштабах начинается с представления его в виде различных моделей. Модели технологических процессов можно разделить на две основные группы: графические (в виде схем и других изображений) и описательные. К графическим моделям (схемам) можно отнести функциональную, технологическую, структурную и специальные схемы. Описательные модели подразделяются на имитационные, операционные и математические [1].
Анализ моделей на основе теплофизических и химических закономерностей процесса дает возможность прогнозировать его развитие при варьировании входящих технологических параметров. Также моделирование процессов позволяет осуществлять дальнейшую их оптимизацию, выполнение проектных расчетов и вычислений.
Общий анализ производственных процессов нефтехимии и нефтепереработки происходит в следующей последовательности:
1 Выделение элементов процесса, которые определяют анализируемые свойства.
2 Выявление зависимостей выходных потоков от входных на основании описания процесса и определение его свойств и особенностей, которое основывается на физических, теплотехнических и химических закономерностях.
3 Определение связей между элементами, обусловливающих проявление анализируемых свойств процесса.
Совокупность элементов и связей между ними определяет структуру ЭРСП. Существует множество иерархических уровней представления структуры ЭРСП. Однако при рассмотрении ЭРСП с целью составления математического описания элементов, их расчета (проектирования) и оптимизации рекомендуется использовать в качестве низшего уровня представления элементов типовые технологические операторы, соответствующие первому уровню представления.
В этом случае из всего множества технологических процессов выделяют 7 типовых технологических операторов (основных и вспомогательных), с использованием которых возможно синтезировать процесс и систему процессов любой сложности [1].
Таблица 1.1 – Типовые технологические операторы
Основные технологические операторы | Вспомогательные технологические операторы |
| |
| |
| |
| — / — |
Основные технологические операторы обеспечивают функционирование производственного процесса в требуемом целевом направлении. Вспомогательные отличаются тем, что используются для повышения эффективности функционирования системы в результате изменения ее энергетического и фазового состояний.
Ключевым этапом исследования является расчет параметров производственного процесса при заданных структуре и состоянии элементов. Элементом является определенный аппарат или узел, в котором проводится соответствующая стадия процесса. Состояние элемента включает в себя данные, от которых зависит изменение показателей протекающей стадии процесса.
Связи параметров между собой описываются различными уравнениями, совокупностью интегральных, дифференциальных и алгебраических уравнений фундаментальных теплофизических и химических законов и некоторых экспериментальных данных.
Параметры, от которых зависит процесс, можно разделить на параметры состояния и регулируемые параметры - параметры управления. Задачи исследования математической модели сводятся к выбору параметров управления, соответствующих определенному критерию оптимальности — численной оценке процесса при различных значениях параметров управления. Часто на одной и той же модели с помощью относительно небольших изменений в вычислительном процессе можно произвести анализ по довольно разным критериям.
Основной задачей моделирования производственного процесса при заданных параметрах функционирования технологических операторов является нахождение параметров состояния потоков, связывающих указанные технологические операторы.
Различаются два типа моделей: детерминированные и статистические.
Детерминированные (теплофизические и химические) модели используют законы сохранения массы и энергии, законы переноса вещества, энергии и импульса, закономерности равновесия и кинетики протекающих химических реакций, гидродинамику потоков и т.д.
Принципы построения этих моделей подразделяются на две группы: интегральные (композиционные) и декомпозиционные.
Суть интегральных (композиционных) методов построения модели заключается в объединении систем уравнений, описывающих работу отдельных элементов, в одну большую систему уравнений с дальнейшим решением этой системы. Данная система содержит множество выражений различного типа от линейных до дифференциальных уравнений в частных производных. Такие системы уравнений называются смешанными и требуют специальных математических методов для своего решения. Для использования интегрального метода необходимо иметь специальные компьютерные программы для решения смешанных систем уравнений (линейных, нелинейных, дифференциальных, в частных производных и др.).
Суть декомпозиционного метода расчета заключается в том, что химико-технологический процесс представлен в виде отдельных блоков, соответствующих элементам процесса, и анализ ЭРСП сводится к последовательному расчету отдельных блоков. В данном случае размерность каждой отдельной системы уравнений, соответствующей блоку ЭРСП, относительно невелика.
При расчете отдельного модуля требуется рассчитать только ограниченное количество уравнений, соответствующих конкретному модулю, т.е. выполнить проверочный расчет конкретного процесса. Следует отметить, что при наличии ограниченного количества возможных модулей ЭРСП их алгоритмы расчета давно разработаны и приведены в специальной литературе и в виде компьютерных программ.
Благодаря этому наиболее предпочтителен декомпозиционный метод расчета ЭРСП, заключающийся в последовательном расчете ЭРСП от модуля к модулю.
Ввиду сложности технологических процессов при разработке их математических моделей обычно вводится ряд упрощающих допущений. В этом случае осуществляется анализ взаимосвязи входных и выходных параметров без рассмотрения физико-химических закономерностей самого процесса. В этих случаях на основании экспериментальных данных с помощью статистических методов составляется регрессионная модель процесса (зависимости выходных параметров от входных), адекватно описывающая реальный технологический объект на некотором интервале изменения его параметров.
Построенная математическая модель должна быть проверена на адекватность экспериментальным данным, и в случае необходимости корректируются ее параметры. Затем разрабатывается алгоритм решения уравнений и формируется модуль в виде соответствующей программы для компьютера.
Статистические модели элементов ЭРСП не включают детальное описание закономерностей процессов, происходящих в моделируемых объектах. Обычно математическое описание элемента строится в виде регрессионных зависимостей выходных параметров объекта от входных переменных и представляет собой адекватные линейные и нелинейные полиномиальные уравнения.
Коэффициенты этих уравнений определяются путем обработки данных полного факторного или пассивного эксперимента, что позволяет значительно сократить трудоемкость составления модели и все расчетные процедуры.
Оптимизация ЭРСП представляет собой целенаправленную деятельность, заключающуюся в получении наилучших результатов при соответствующих условиях проведения процесса. При постановке задачи оптимизации применяются следующие аспекты:
1 Наличие цели оптимизации. Одновременно системе не должно приписываться два и более критерия оптимальности, так как обычно экстремум (минимум или максимум) одного критерия не соответствует экстремуму другого. Для оптимизации ЭРСП в качестве критерия оптимальности могут быть использованы приведенные затраты на ведение процесса при заданном качестве продуктов и производительности.
2 Наличие ресурсов оптимизации, под которыми понимается возможность выбора значений некоторых параметров оптимизируемого объекта. Объект должен обладать определенными степенями свободы (управляющими воздействиями).
3 Возможность количественной оценки оптимизируемой величины, поскольку только в этом случае можно сравнивать эффекты от выбора тех или иных управляющих воздействий.
Количественная оценка оптимизируемого качества объекта — критерий оптимальности — обладает следующими свойствами:
— критерий оптимальности должен выражаться количественно;
— критерий оптимальности должен быть единственным;
— величина критерия оптимальности должна изменяться монотонно (без разрывов и скачков);
— критерий оптимальности должен отражать наиболее существенные стороны процесса;
— критерий оптимальности должен иметь ясный физический смысл и удобную форму расчета.
Этим требованиям удовлетворяют удельные приведенные затраты, включающие амортизацию оборудования, его обслуживание, затраты на сырье и реагенты, отнесенные к объему продукции.
На основании выбранного критерия оптимальности составляется целевая функция, представляющая собой зависимость критерия оптимальности от параметров, влияющих на ее значение. Вид критерия оптимальности или целевой функции определяется конкретной задачей оптимизации. Таким образом, задача оптимизации сводится к нахождению экстремума целевой функции.
Общей постановкой задачи оптимизации является выражение критерия оптимальности в виде экономической оценки (приведенные затраты, себестоимость продукции, прибыль, рентабельность). Однако в частных задачах, когда объект является частью технологического процесса, не всегда целесообразно выделять прямой экономический показатель, который полностью характеризует эффективность работы рассматриваемого объекта. В таких случаях критерием оптимальности может служить технологическая характеристика, косвенно оценивающая экономичность работы аппарата (затраты энергии на единицу продукции, стоимость оборудования на единицу продукции, выход продукта, степень превращения).
Нахождение экстремума функции возможно различными методами. Выбор того или иного метода нахождения оптимума является одним из важнейших этапов оптимизации. Методы поиска оптимума можно разделить на следующие группы:
— аналитические методы;
— методы математического программирования.
Группа аналитических методов оптимизации объединяет аналитический поиск экстремума функции, метод множителей Лагранжа, вариационные методы и принцип максимума. Аналитический поиск экстремума функции, заданной без ограничений на независимые переменные, является наиболее простым, но применяется к задачам с небольшим числом переменных и целевой функцией, представляющей собой аналитическое выражение, дифференцируемое во всем диапазоне исследования.
Группа методов математического программирования включает динамическое программирование, линейное программирование и нелинейное программирование.
Динамическое программирование используется для решения задач оптимизации многостадийных процессов. Метод предполагает разбивку анализируемого процесса на стадии во времени или в пространстве (например, реактор в каскаде или массообменная тарелка в колонне). Рассмотрение задачи начинается с последней стадии процесса и оптимальный режим определяется поэтапно.
Линейное программирование — метод для решения задач оптимизации с линейными выражениями для критерия оптимальности и линейными ограничениями на область изменения переменных. Подобные задачи решаются итерационными способами.
Методы нелинейного программирования объединяют различные способы решения оптимальных задач: градиентные, инградиентные и случайного поиска. Нелинейное программирование используется при решении задач с нелинейными критериями оптимальности. Все методы нелинейного программирования представляют собой численные методы поискового типа. Суть их заключается в определении набора независимых переменных, дающих наибольшее приращение оптимизируемой функции. Данная группа методов применяется как для детерминированных, так и стохастических процессов.
Таким образом, для решения задачи оптимизации необходимо:
1) составить математическую модель объекта оптимизации;
2) выбрать критерий оптимальности и составить целевую функцию;
3) установить возможные ограничения, которые должны накладываться на переменные;
4) выбрать метод оптимизации, который позволит найти экстремальные значения искомых величин.
В общем виде оптимизация ЭРСП — это представление ЭРСП в виде последовательности характеризующих его математических уравнений и выражений, решения составленного математического описания и анализа полученных результатов решения, выявления критерия оптимальности. В этих целях могут использоваться классические методы математического анализа и оптимизации функций, представленных в явном виде. Для более сложных и неявных функций применяют также методы приближенных вычислений: аппроксимацию, интерполяцию (для экспериментально статистических моделей), численные методы поиска оптимума.
1.2 Методы построения математических моделей
Процесс создания математической модели, ее исследования и распространения результатов на оригинал может быть осуществлен различными способами. К наиболее распространенным способам построения математического описания ЭРСП аналитические, статистические, эвристические и комбинационные методы.
Аналитический метод построения моделей заключается в представлении модели в виде уравнений, строго отражающих физико-химические и смежные процессы, протекающие в моделируемом объекте. Обязательным условием построения адекватной модели при этом является достаточное знание механизмов, лежащих в основе моделируемого процесса. Преимущество данного метода состоит в определенной точности модели, отражении физического смысла процесса, достоверности и результативности в широком диапазоне изменения переменных.
Статистический метод основан на математической обработке данных эксперимента и практического производственного опыта методами математического анализа и статистики. В общем виде результаты статистической обработки выражаются в виде уравнения полиномиального типа:
y =b0 + b1x1+b2x2+ b3x1x2+ b4x12 + b5x22 + …
+ bnxn+bn+1xn+1+ bn+2xnxn+1+ bn+3xn2 + bn+4xn+1, (1.1)
где b0, b1, b2, bn — коэффициенты регрессии.
Существенным недостатком статистических моделей является их применение в диапазоне переменных, который ограничен крайними значениями экспериментальных данных. Однако они используются в тех случаях, когда точное математическое описание физико-химической фундаментальной основы процесса не представляется возможным. Для вычисления значения функции в точке (xi , yi), расположенной в пределах крайних значений экспериментальных данных - точек ( x1, y1) и (x2 , y2), широко используется метод линейной интерполяции.
Прогноз и определение значений функции yi+1 при значениях переменных xi+1, которые не входят в интервал ограничений эксперимента, производится с помощью экстраполяции.
Зависимости y = f(x) могут быть выражены различными функциями (например, гиперболическими, параболическими, синусоидальными функциями).
Параметры зависимостей выбираются из условий минимального отклонения от контрольных (экспериментальных) точек. При этом минимальное отклонение не отражает физической сущности рассматриваемых зависимостей и отношений. Одним из наиболее распространенных методов определения минимального отклонения от истинного значения функции является метод наименьших квадратов. Для уточнения численных параметров уравнений, которыми характеризуются экспериментальные данные, могут применяться корреляционный, регрессионный, кластерный анализ.
Существует ряд возможностей для повышения точности и достоверности моделей статистического типа, среди которых распространен метод сравнения и связи моделируемого объекта, с аналогичным действующим в реальности.
Так, например, в проектировании и моделировании процессов химической технологии экспериментальные зависимости связываются с аналогичными моделями действующих процессов или явлений, на основе чего производится расчет создаваемого объекта. Количественные параметры и эмпирические коэффициенты можно уточнить методами математической статистики.
2 Модели пленочных испарителей
2.1 Конструкции и область применения пленочных испарителей
В выпарных, дистилляционных и ректификационных установках, для генерации пара используются теплообменные аппараты, обычно называемые кипятильниками. В кипятильниках к раствору, подвергаемому обработке, подводится теплота, за счет которой происходит парообразование.
Основными типами конструкций являются: вертикальные трубчатые кипятильники, кипятильники с паровым пространством и пленочные испарители. Последние по способу обеспечения пленочного течения жидкости можно разделить на аппараты с падающей пленкой жидкости, восходящей пленкой жидкости и роторно - пленочные испарители [1, 2].
Вертикальные трубчатые кипятильники - аппараты, получившие широкое распространение в выпарных и ректификационных установках. Основной их частью является трубчатый теплообменник - кипятильник.
Вертикальные трубчатые кипятильники применяются как с естественной, так и с принудительной циркуляцией раствора. В обоих случаях трубчатый кипятильник соединяется с аппаратами таким образом, чтобы образовался замкнутый циркуляционный контур. В аппаратах с естественной циркуляцией движение раствора обуславливается различием плотностей жидкости в опускной части циркуляционного контура и парожидкостной смеси в подъемной его части. В аппаратах с принудительной циркуляцией для обеспечения движения жидкости внизу, на входе в кипятильник, устанавливается циркуляционный насос [1, 3, 4].
По конструктивному оформлению трубчатые кипятильники с естественной циркуляцией раствора делятся на аппараты с выносными кипятильниками, встроенными кипятильниками и с вынесенной циркуляционной трубой. В аппаратах со встроенным кипятильником циркуляционная труба располагается по его оси. Поскольку труба обогревается, в ней происходит парообразование и образуется парожидкостная смесь, плотность которой меньше плотности жидкости. В результате уменьшается скорость циркуляции.
Пленочные испарители - аппараты, в которых обрабатываемый раствор распределяется по поверхности теплообмена в виде пленки. За счет этого исключается гидростатическое давление и связанное с ним уменьшение разности температур за счет повышения температуры кипения раствора.
Пленочные трубчатые испарители различаются направлением движения жидкой и паровой фаз. По направлению движения жидкости различают испарители с падающей пленкой, в которых жидкость стекает под действием силы тяжести, и испарители с восходящей пленкой. Такое движение пленки возможно лишь в результате динамического воздействия на нее парового потока. Поэтому в испарителях с восходящей пленкой имеет место прямоточное восходящее движение паровой и жидкой фаз.
Восходящий прямоток обеих фаз обеспечивается лишь при больших скоростях пара, что неизбежно связано со значительным перепадом давления по высоте труб испарителя вследствие гидравлического сопротивления при движении в них парожидкостной смеси. Это является существенным недостатком таких аппаратов. Достоинством являются высокие коэффициенты теплоотдачи от трубы к восходящей пленке жидкости [5]. Это определяет область их применения в процессах при повышенных давлениях, где относительно высокое гидравлическое сопротивление не играет существенной роли.
При движении жидкости в виде пленки коэффициент теплоотдачи от греющей трубы к пленке стекающей жидкости составляет от 1,5 до 4,0 кВт/(м2×К), что от 2 до 10 раз превосходит аналогичные коэффициенты теплоотдачи от стенки трубы к кипящей жидкости, заполняющей эту трубу.
Пленочные испарители применяют в тех случаях, когда использование обычных трубчатых кипятильников оказывается невозможным или нецелесообразным. Достоинством пленочных испарителей являются высокие коэффициенты теплопередачи, отсутствие гидростатического давления столба жидкости и малое время пребывания в них жидкости.
В процессах ректификации, регенерации абсорбентов, выпаривания растворов одним из направлений экономии энергетических ресурсов, снижения металлоемкости оборудования является интенсификация процесса теплообмена. При использовании в качестве теплоносителя конденсирующихся паров воды или высокоорганических жидкостей повышение коэффициента теплопередачи в кипятильниках, испарителях и выпарных аппаратах, при прочих равных условиях, приводит к более полному использованию энергетического потенциала теплоносителей.
2.2 Пленочные испарители с падающей пленкой
Пленочные испарители с падающей пленкой выполняются в виде вертикальных кожухотрубчатых теплообменников, которые состоят из вертикального пучка труб, закрепленных в трубных решетках. В межтрубное пространство испарителя подается теплоноситель. Для организации движения обрабатываемой жидкости в виде пленки, стекающей по внутренней поверхности труб, на верхней трубной решетке имеются распределительные устройства.
У прямоточного испарителя жидкость и вторичный пар движутся сверху вниз через пучок труб и поступают в нижнюю часть ректификационной колонны или в сепаратор (рисунок 2.1, а, б). У противоточного испарителя вторичный пар движется навстречу стекающей пленке жидкости
(рисунок 2.1, в, г).
Основные схемы пленочных испарителей с падающей пленкой показаны на рисунке 2.1.
а, б - прямоточные; в, г - противоточные пленочные испарители
Рисунок 2.1 – Схемы пленочных испарителей с падающей пленкой
Для того чтобы интенсифицировать процесс теплообмена в тонкой пленке, внутри труб может быть размещена кольцевая спираль [6]. Кольцевые спирали позволяют дополнительно перемешивать слои жидкостной пленки, стекающие по поверхности витков кольцевой спирали.
Для интенсификации теплообмена применяют также искусственную шероховатость в виде спиральных и кольцевых канавок и насечек [1, 2,7] на внутренней поверхности теплообменных труб. Недостатком таких аппаратов является трудность очистки поверхности труб от отложений.
Известен пленочный выпарной аппарат (рисунок 2.2), содержащий цилиндрический корпус 1 с патрубками 2 и 3 для подвода и отвода рабочей жидкости и газа, в верхней части которого размещена насадка из колец
Рашига 4. В средней части расположена трубная решетка 5 с переливными патрубками 6. Внутри патрубков 6 расположены металлические цепи 7, свисающие к основанию корпуса 1 [6].
1-цилиндрический корпус; 2- патрубок для ввода теплоносителя; 3- патрубок для ввода обрабатываемой жидкости; 4- каплеотбойник; 5- трубная решетка;
6- переливные патрубки; 7- цепи
Рисунок 2.2 - Пленочный выпарной аппарат с прямым контактом теплоносителя с пленкой жидкости
Использование цепной навесы позволяет добиться равномерного распределения жидкости по сечению аппарата при незначительном его гидравлическом сопротивлении. Это, в свою очередь, ведет к увеличению поверхности контакта фаз в аппарате.
В длиннотрубных пленочных испарителях, используемых при удалении из смеси значительного количества легколетучего компонента, существенно изменяются по мере стекания жидкой пленки физико-химические свойства выпариваемой жидкости, гидродинамика пленочного течения, температурный напор и характер парообразования. Вследствие этого, интенсивность тепло- и массообмена значительно изменяется по длине аппарата, достигая максимума лишь на небольшой части всей длины аппарата.
Поэтому для проведения процесса концентрирования термолабильных веществ, когда выделяется значительное количество легколетучих примесей, целесообразно применять пленочные трубчатые испарители, выполненные в виде секций небольшой длины с уменьшающимся числом труб в каждой ниже- лежащей секции, в соответствии с рисунком 2.3 [3].
Аппарат состоит из нескольких секций, каждая из которых содержит кожух 1, трубную доску 2, испарительные трубы 3, имеющие в верхней кромке прорези 4 для распределения жидкости в виде пленки и пароотводные трубы. Между секциями расположен каплеотбойник, наличие которого исключает попадание капель жидкости в нижнюю часть аппарата [3].
При работе аппарата исходная смесь поступает через верхний штуцер на трубную доску и затем распределяется по внутренней поверхности испарительных труб, стекает в виде пленки и закипает. Образующийся пар направляется вверх и удаляется через штуцер, а жидкость стекает вниз и попадает в испарительные трубы нижележащей секции. Пар направляется по пароотводным трубам в вышележащие секции и удаляется через общий штуцер.
1- кожух; 2- трубная доска; 3- испарительные трубы; 4- прорези на верхней кромке труб; 5- труба для отвода пара из секции; 6- конус (каплеотбойник)
Рисунок 2.3 - Пленочный секционный испаритель
Испарители с внутренним циркуляционным контуром обладают всеми преимуществами трубчатых пленочных аппаратов (рисунок 2.4). Циркуляционный контур позволяет обеспечить необходимые плотности орошения труб в широком диапазоне нагрузок по жидкости аппарата [3].
Испаритель представляет собой кожухотрубчатый теплообменник 1, в центральной части которого установлен вращающийся транспортирующий цилиндр 2 с заборным устройством 3 в виде ленточной спирали 4, укрепленной на внутренней поверхности втулки 5. На внутренней поверхности цилиндра укреплены перегородки 10, предотвращающие проскальзывание жидкости при ее транспортировке, а в верхней части имеются отверстия 18 для выхода транспортируемой жидкости и диск 17 для распределения раствора, поступающего в аппарат. Транспортирующий цилиндр крепится при помощи верхней 16 и нижней 7 цапф. На верхней трубной решетке 12 установлен кольцевой распределитель жидкости 14 с гасителем из нескольких слоев металлической сетки 15. Испарительные трубки 11 снабжены прорезями 13 для распределения пленки жидкости по их внутренним поверхностям. Для предотвращения воронкообразования жидкости при вращении циркуляционного органа в днище аппарата 8 установлены перегородки 9.
Рисунок 2.4 - Пленочный испаритель с внутренней циркуляцией жидкости
Исходный продукт подается на диск вращающегося транспортирующего цилиндра, отбрасывается на кольцевой распределитель и, стекая с него, равномерно распределяется по внутренним поверхностям испарительных трубок, обогреваемых теплоносителем. Под действием центробежной силы жидкость в транспортирующем цилиндре поднимается вверх, а достигнув отверстий, выбрасывается через них на кольцевой распределитель. Пары обрабатываемой жидкости удаляются из аппарата через верхний патрубок, а обработанная жидкость - через нижний.
Недостатком аппаратов с внутренним циркуляционным контуром является сложность конструкции , что усложняет условия монтажа и ремонта, приводит к существенному увеличению объема жидкости в системе, а следовательно, к возрастанию времени ее пребывания при высокой температуре.
2.3 Распределительные устройства пленочных испарителей
Регулярность потоков по сечению аппарата и в каждой трубе достигается определенной конфигурацией элементов распределительного устройства и их взаимным расположением. Кроме того, при выборе типа распределительного устройства требуется учитывать простоту изготовления, монтажа и ремонта, коррозионные свойства и чистоту жидкости, ее физические свойства, а также возможность снижения затрат энергии на подачу жидкости в аппарат.
Известные распределительные устройства по конструкции весьма разнообразны. Как правило, вначале с помощью диффузоров, дросселей или отражателей гасят скорость струи жидкости, поступающей в аппарат. Затем, комбинируя желоба, решетки и перфорированные плиты, распределяют жидкость по сечению испарителя [3, 4].
Более энергоемкий метод - распыление жидкости форсунками. При конструировании устройств руководствуются эмпирическими соотношениями, установленными экспериментально. Выбор обосновывают гидравлическим расчетом основных элементов [9].
Известны листовые (тарельчатые) распределители, устройства с прорезями на выступающих концах труб и устройства, распределяющие жидкость с помощью различных вкладышей и насадок (рисунок 2.5).
а – перфорированные листы (тарелки); б – прорези на концах труб;
в – вкладыши внутри концов труб
Рисунок 2.5. Распределительные устройства
Листовые распределители (рисунок 2.5, а) выполняются в виде перфорированных тарелок, расположенных над верхней трубной доской. Обычно используют две или три тарелки, в которых число и координаты отверстий выбирают таким образом, чтобы обеспечивалась равномерность расположения отверстий по поверхности и симметричность их относительно отверстий нижележащей тарелки [4]. Образующаяся парожидкостная смесь с помощью перфорированных тарелок равномерно распределяется по испарительным трубкам. Такие распределители используются при плотности орошения 0,4-1,5 м3/(м2×ч) [4].
Основные конструкции распределительных устройств показаны на рисунке 2.6.
а - со скошенными тангенциальными прорезями; б - с прямоугольными прорезями; в - с вкладышем; г - со специальными закручивающими насадками
Рисунок 2.6 - Основные типы элементов распределительных устройств
Устойчивую работу испарителя при плотностях орошения от 0,25 до 0,4 м3/(м2×ч) обеспечивают распределители в виде вкладышей (рисунок 2.6, в) или специальные закручивающие насадки длиной 100 мм (рисунок 2.6, г) [3, 9].
Выбор конструкции и размеров распределительного устройства определяется главным образом плотностью орошения.
В распределителях, изображенных на рисунке 2.6,а, концы испарительных трубок выступают на 25 мм над верхней трубной доской и снабжаются тремя-четырьмя скошенными прорезями глубиной около 20 мм. Закраины прорезей отгибаются таким образом, чтобы обеспечить тангенциальный ввод жидкости в трубки. Возникающая при этом центробежная сила способствует более полному смачиванию внутренней поверхности стенок труб. При использовании распределителей этого типа плотность орошения должна быть не менее от 1,2 м3/(м2×ч).
Более простыми являются распределители в виде прямоугольных прорезей шириной от 2 до 5 мм и глубиной до 15 мм.
Разновидностью таких устройств являются накручивающиеся на трубы зубчатые патрубки (рисунок 2.7) [4]. Испарительные трубы 1 обогреваются снаружи паром, поступающим в нагревательную камеру через штуцер 2. Подачу раствора в распределительную камеру 7 производят по штуцеру 4. Распределение жидкости по периметру камеры 7 обеспечивается двумя концентрически установленными обечайками 5 и 6, имеющими зубчатые торцы снизу и сверху. Высоту подъема зубчатых колпачков 3 устанавливают после монтажа аппарата измерением количества жидкости, стекающей в отдельных трубках.
Продукты с незначительными механическими включениями обрабатывают при плотностях орошения от 0,5 до 1,5 кг/(м×с) с использованием распределительных устройств в соответствии с рисунком 2.6, г.
77
Рисунок 2.7 - Распределительное устройство с регулируемыми зубчатыми патрубками
С повышением плотности орошения увеличивается скорость течения жидкости в проходных каналах распределительных устройств, чем снижается вероятность их засорения. Для распределения жидкости в этом случае используют устройства со вставками, в соответствии с рисунком 2.8.
Рисунок 2.8 - Распределительное устройство со вставками
Жидкость через штуцер 5 поступает в кольцевой зазор, образованный камерой 7 и установленной в ней цилиндрической обечайкой 6. Переливаясь через зубчатую кромку перегородки, поток попадает на распределительную перфорированную тарелку 4, прижимающую вставки 3 к трубной решетке 2. С трубной решетки жидкость стекает в кольцевой зазор между вставками 3 и трубками 1. Каждая вставка центрируется в трубке с помощью трех ребер, расположенных по отношению друг к другу под углом 120°. Трубки обогреваются снаружи паром, подаваемым в нагревательную камеру через штуцер 9.
Также применяют распределительные устройства с перфорированными тарелками (рисунок 2.9). Плотность орошения выбирают в пределах от 0,5 до
2,0 кг/(м×с). Жидкость подают через штуцер 1 в центр распределительной камеры 2.
Рисунок 2.9 - Распределительное устройство с перфорированными тарелками
Внутри камеры установлены распределительный диск 3 и три перфорированные тарелки 4, 5, 6, закрепленные на трубной решетке 7, в которую завальцованы теплопередающие трубки 9. Обогрев трубок производится паром, подаваемым в нагревательную камеру 8 через штуцер 10. Число и координаты отверстий верхней тарелки 4 определяют проецированием на нее координат отверстий трубкой решетки 7 с последующим удалением рядов, начиная с крайнего к центру (рисунок 2.9).
Диаметр отверстий выбирают из условия установления уровня жидкости на верхней тарелке от 0,03 до 0,04 м, на средней - от 0,02 м, на нижней – от
0,01 м. Устройство простое в изготовлении и удобное при эксплуатации, однако не обеспечивает равномерного распределения жидкости при малых плотностях орошения [4].
Установлено, что равномерность орошения труб улучшается при увеличении числа вводов жидкости в аппарат и возрастании симметрии этих вводов по отношению к оси аппарата. Однако такой метод значительно усложняет конструкцию, поэтому опыты были ограничены двумя вариантами: вводом жидкости по центральной оси аппарата и двумя противоположными периферийными вводами, перпендикулярно к оси аппарата [4]. Осевая симметрия вставок (рисунок 2.6) обеспечивает генерацию пленок в каждой трубе, но не по сечению аппарата. Использование закономерностей симметрии в расположении отверстий перфорированных тарелок (рисунок 2.9) позволяет распределить жидкость по сечению испарителя, но не гарантирует генерацию пленки в каждой трубе.
Наконец, оба типа распределительных устройств требуют расхода жидкости на порядок больше экономически оправданной величины. В этих условиях только возрастание числа осей симметрии дроссельных элементов и симметричности перфорации тарелок по отношению к координатам расположения труб дает необходимые результаты. Стремясь удовлетворить оба эти требования, приходят, с одной стороны, к перфорированной тарелке, координаты отверстий которой совпадают с координатами расположения труб в трубной решетке, а с другой стороны - к дроссельному элементу, выполненному в виде шара, погруженного на треть своего диаметра в теплообменную трубу (рисунок 2.10) [4].
Рисунок 2.10 - Пульсирующее распределительное устройство с шарами
Основным элементом устройства являются полые шары (дроссельные элементы) 4, расположенные на верхних концах теплопередающих труб 2, закрепленных в трубной решетке 3. Трубы размещены в испарительной камере 11, питаемой паром через штуцер 1. Над шарами помещена перфорированная пластина 5. Распределительная камера 6 снабжена пульсатором 8 с клапанами 7, штуцерами для подвода раствора 10 и выхода вторичного пара 9.
У шара, как известно, бесконечное число осей симметрии бесконечного порядка. Но этого оказалось недостаточно. Кроме геометрической симметрии элементов в трех измерениях понадобилась симметрия в четвертом измерении. Другими словами, шары должны совершать колебательное движение между трубной решеткой и ограничительной перфорированной тарелкой. Подъем шаров (под действием разрежения в распределительной камере) и их опускание (под действием силы тяжести) симметричны во времени.
Исходный раствор при подаче его в нижнюю часть распределительной камеры в момент, когда дроссельные элементы опущены, растекается ровным слоем по всей трубной решетке. При движении поршня пульсатора вверх в распределительной камере создается разрежение относительно давления в испарительных трубах. Дроссельные элементы поднимаются. Поскольку каждый дроссельный элемент выполнен в виде полого шара и при подъеме центр шара перемещается по траектории, близкой к оси трубы, то в результате перемещения образуется кольцевая щель равной толщины. В эту щель поступает определенное количество жидкости. При движении поршня вниз открываются клапаны 7, и пар, поступивший в момент подъема шаров из труб в распределительную камеру, направляется в сепаратор. Шары возвращаются на место, причем под действием силы тяжести они устанавливаются по центру трубок. Далее все повторяется сначала. При движении вниз и вверх шары вращаются вокруг своего центра тяжести.
Стекающая в пульсационном режиме пленка упаривается, затем отделяется от вторичного пара в сепараторе. Снижение плотности пульсирующего орошения от 5 до 10 раз (по сравнению с применяемым в известных распределителях) дает значительный выигрыш в электроэнергии, несмотря на некоторое потребление ее пульсатором.
С увеличением диаметра аппарата до нескольких метров перфорированная пластина снабжается регулирующими винтами, установленными над каждым дроссельным элементом. Одновременно вместо поршневого пульсатора на штуцере выхода вторичного пара устанавливается трехходовой пневматический клапан для попеременного соединения распределительной камеры с паровым пространством данного аппарата и с вакуумной системой установки. В качестве генератора импульсов вместо трехходового крана может быть использован пульсатор с вращающимся ротором, оснащенным электродвигателем с вариатором.
Устройство позволяет полностью ликвидировать асимметрию, обусловленную подачей раствора в распределительную камеру в одном месте, и добиться полной геометрической симметрии стекающих потоков в отдельных трубках и по сечению аппарата.
Недостатком аппарата является сложность устройства и управления его работой.
2.4 Пленочные аппараты с распределением жидкости по трубам
с отрицательной обратной связью по парообразованию
Наибольшую трудность при конструировании пленочных испарителей с падающей пленкой представляет обеспечение равномерного распределения обрабатываемой жидкости как между отдельными трубами, так и по периметру каждой трубы. Распределение жидкости по трубам с отрицательной обратной связью по парообразованию реализуется в пленочных прямоточных и противоточных испарителях [10, 11, 12], у которых над верхними концами теплообменных труб над трубной решеткой расположены соответственно колпачки и патрубки с диафрагмами (рисунок 2.11).
а б в
1-цилиндрическая греющая камера: 2-теплообменные трубы; 3 - трубная решетка; 4, 5-штуцера для ввода и вывода теплоносителя; 6, 7 - штуцера для выхода и входа обрабатываемой жидкости; 8 - штуцер для выхода вторичного пара; 9 - патрубки; 10 - колпачки; 11 - штуцер для поддержания над колпачками давления, равного давлению вторичного пара на выходе из аппарата;
12 - диафрагмы; 13 - вставка пленкообразователя
Рисунок 2.11 - Противоточный (а) и прямоточный (б) пленочные испарители, а также вставка пленкообразователя с патрубком и диафрагмой (в)
Пленочный выпарной аппарат содержит вертикальный цилиндрический корпус 1, прикрепленные к трубным решеткам 3 верхнюю и нижнюю распределительные камеры, размещенные в нем теплообменные трубы 2, закрепленные в трубных решетках 3, размещенные в верхних концах теплообменных труб 3 пленкообразователи 13 с закрепленными на них соосно патрубками 9 с диафрагмами 12. Обрабатываемая жидкость подается и выводится через штуцер 6 и 7. Греющий пар подается через штуцер 4, а его конденсат выводится через штуцер 5. Образующийся вторичный пар выводится через штуцер 8.
Испаритель работает следующим образом. Обрабатываемая среда подается в верхнюю распределительную камеру на верхнюю трубную решетку 3, растекается по ней, затекает под патрубки 9 и переливается через верхнюю кромку пленкообразователя 13 в теплообменные трубы 2. Стекая по теплообменным трубам, низкокипящая часть обрабатываемой жидкости испаряется. Пар поднимается по теплообменным трубам и через диафрагму 12 на патрубках поступает в верхнюю распределительную камеру. В результате сопротивления диафрагм уровень жидкости на трубной решетке выше, чем уровень жидкости на переливе в пленкообразователи. Если в какую-либо трубу жидкости поступает меньше, то в ней образуется меньше вторичного пара. Следовательно, уменьшается сопротивление диафрагмы над этой трубой, что приведет к подъему уровня жидкости на переливе в пленкообразователи, и повысит расход жидкости в эту трубу, то есть устройство работает как регулятор расхода жидкости в теплообменные трубы.
Развитием конструкции является прямоточный выпарной пленочный аппарат [13] (рисунок 2.12), содержащий вертикальный цилиндрический корпус 1 с размещенными в нем теплообменными трубами 2, закрепленными в трубных решетках 3. На верхних концах теплообменных труб расположены пленкообразователи 4 с закрепленными на них соосно колпачками 5. Нижние концы труб заканчиваются вставками 6 с продольными прорезями, концы которых отогнуты внутрь в виде лопастей. На верхней трубной решетке размещена кольцевая перегородка 7. В нижней части аппарата под теплообменными трубами находится подвижная тарелка – сепаратор 8.
А |
Б |
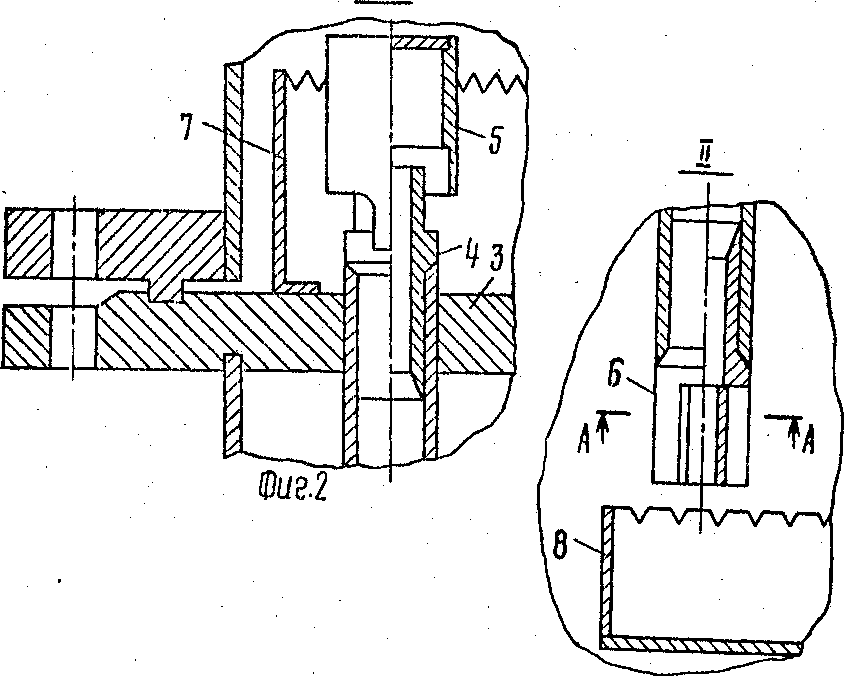
А-А |
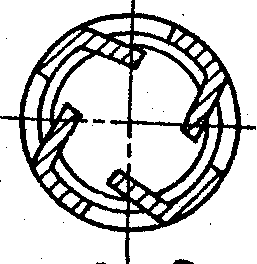

Рисунок 2.12 - Пленочный прямоточный аппарат с регулируемым сопротивлением труб
Тарелка 8 соединена со штоком 9 регулирующего устройства, с помощью которого тарелка может подниматься или опускаться.
При значительных нагрузках по вторичному пару сопротивление труб достаточно велико, чтобы обеспечить качественное регулирование поступления жидкости во все трубы. В этом случае тарелка 8 находится в нижнем положении. При малой нагрузке по вторичному пару для увеличения сопротивления труб тарелка поднимается, что и приводит к улучшению регулирования поступления жидкости во все трубы.
Повышение эффективности и надежности работы аппарата при большом его диаметре, в широком диапазоне нагрузок по вторичному пару, за счет более равномерного распределения обрабатываемой жидкости по теплообменным трубам достигается в прямоточно-противоточном пленочном аппарате (рисунок 2.13) [14].
7 |
7 |
8 |
6 |
2 |
5 |
9 |
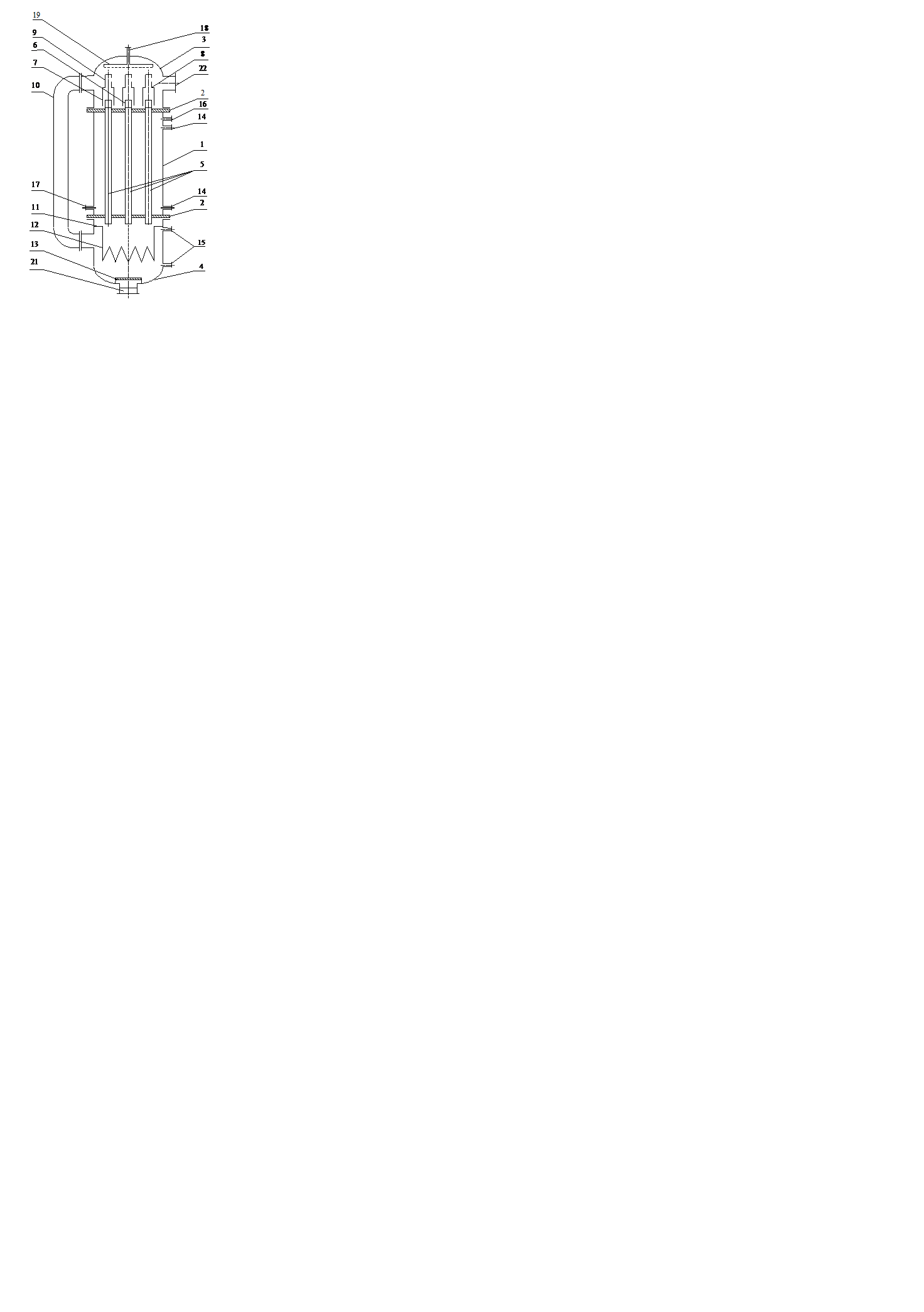
Рисунок 2.13 - Прямоточно-противоточный пленочный аппарат (а) и распределительное устройство (б)
Пленочный выпарной аппарат содержит вертикальный цилиндрический корпус 1, прикрепленные к трубным решеткам 2 верхнюю 3 и нижнюю 4 распределительные камеры, размещенные в аппарате теплообменные трубы 5, закрепленные в трубных решетках 2. В верхних концах теплообменных труб 5 размещены пленкообразователи 6 с закрепленными на них соосно патрубками 7 с диафрагмами 8. К диафрагмам 8 прикреплены колпачки 9 с отверстием в боковой стенке. Верхняя 3 и нижняя 4 распределительные камеры соединены переточной трубой 10. К стенкам нижней распределительной камеры 4, выше отверстия для переточной трубы 10, прикреплена диафрагма 11 с закрепленным в ней патрубком 12, нижний конец которого расположен ниже отверстия для переточной трубы и снабжен V-образными вырезами. Нижняя камера 4 и межтрубное пространство испарителя снабжены уровнемерами, которые подключены соответственно к штуцерам 14 и 15.
Обрабатываемая жидкость подается через штуцера 18 и распределительный коллектор 19 выводится через штуцер 21. Для предотвращения образования воронки над отверстием штуцера 21 установлен отбойник 13. Греющий пар подается через штуцер 16, а его конденсат выводится через штуцер 17. Образующийся вторичный пар выводится через штуцер 22.
Испаритель работает следующим образом. Обрабатываемая среда подается в верхнюю распределительную камеру 3 через штуцер 18 и распределительный коллектор 19 на верхнюю трубную решетку 2, растекается по ней, затекает под патрубки 7 и переливается через верхнюю кромку пленкообразователя 6 в теплообменные трубы 5. Стекая по теплообменным трубам 5, низкокипящая часть обрабатываемой жидкости испаряется. При малой нагрузке по вторичному пару, пар поднимается по теплообменным трубам 5 и через патрубок 7, диафрагму 8, колпачок 9 с отверстием в боковой стенке поступает в верхнюю распределительную камеру 3. В результате сопротивления диафрагм 7 и колпачка 9 с отверстием в боковой стенке уровень жидкости на трубной решетке 2 выше, чем уровень жидкости на переливе в пленкообразователи 6. Если в какую-либо трубу 5 жидкости поступает меньше, то в ней образуется меньше вторичного пара. Следовательно, уменьшается сопротивление диафрагмы 8 и колпачка 9 с отверстием в боковой стенке над этой трубой 5, что приведет к подъему уровня жидкости на переливе в пленкообразователи 6. Устройство работает как регулятор расхода жидкости в теплообменные трубы 5. При этом уровень жидкости в нижней распределительной камере 4 закрывает V-образные прорези в нижнем патрубке 12 и пар не может перетекать по переточной трубе 10.
При большой нагрузке по вторичному пару для предотвращения захлебывания теплообменных труб и снижения сопротивления диафрагм 8 уровень жидкости в нижней распределительной камере 4 опускается, и часть вторичного пара движется прямотоком в теплообменных трубах 5 и перетекает по переточной трубе 10 в верхнюю камеру 3. Для увеличения перетока вторичного пара по переточной трубе 10 уровень жидкости в нижней распределительной камере 4 опускается, при этом открывается большая часть V-образных прорезей в нижнем патрубке 12 и сопротивление перетоку вторичного пара снижается. Уровень жидкости в нижней распределительной камере 4 контролируется уровнемером, подключаемым к штуцерам 15.
Преимущества испарителя заключаются в том, что колпачок с отверстием в боковой стенке, прикрепленный к патрубку с диафрагмой, предотвращает попадание жидкости в отверстие диафрагм, тем самым повышает равномерность распределения жидкости по теплообменным трубам.
Соединение верхней и нижней распределительной камеры переточной трубой в сочетании с прикрепленной к стенке нижней распределительной камеры диафрагмой с закрепленной в ней патрубком с V-образными прорезями расширяет диапазон нагрузок при высокой эффективности распределения жидкости и, следовательно, повышается эффективность аппарата в целом.
В последнее время разработаны многоходовые пленочные испарители, в которых реализуется движение пленки испаряемой жидкости в нисходящем и в восходящем прямотоке и в противотоке с падающей пленкой [15, 16]. Рассмотрение этих устройств выходит за рамки настоящего методического пособия.
2.5 Гидродинамика потоков в пленочных тепломассообменных аппаратах
2.5.1 Однофазное установившееся течение жидкости
Течение пленки жидкости в пленочных аппаратах происходит в условиях воздействия на пленку газового (парового) потока. При небольших скоростях газа это воздействие незначительно и течение пленки жидкости можно рассматривать как однофазное. Подробный критический анализ теоретических и опытных данных по гидродинамике пленочного течения приведен в литературе [1, 17, 18].
Решение задачи об установившемся пленочном течении жидкости по поверхности твердого тела было дано Нуссельтом на основе интегрирования уравнения Навье-Стокса [19]. Для одномерного ламинарного движения жидкости в направлении оси Х под действием силы тяжести уравнение Навье-Стокса имеет вид
(2.1)
где - соответственно компоненты скорости жидкости в направлении вдоль и по нормали к поверхности, м/с;
p - давление, Па;
- угол наклона поверхности к горизонту;
- плотность жидкости, кг/м3;
g - ускорение силы тяжести, м/с2;
- динамическая вязкость жидкости, Па×с.
При установившемся движении: так как профиль скоростей в направлении движения остается неизменным. Сила тяжести уравновешивается силой трения :
При ламинарном режиме течения жидкости движения по нормали к поверхности нет и vy = 0. В результате этого уравнение (2.1) упрощается:
(2.2)
При отсутствии напряжения сдвига на границе раздела жидкости с газом (паром) граничные условия имеют вид:
1) при y=0, то есть на поверхности твердого тела;
2) при y= , то есть на наружной поверхности пленки,
dvx /dy=0,
где - толщина пленки жидкости, м.
В результате интегрирования уравнения (2.2) с учетом граничных условий получено
(2.3)
где - кинематическая вязкость, м2/с.
Скорость жидкости vx изменяется по параболическому закону от нуля у твердой стенки до vxmax у свободной поверхности.
Уравнения, выраженные через критерий Рейнольдса, для средней скорости и толщины пленки имеют вид
, (2.4)
, (2.5)
=
, (2.6)
где Г – Массовый расход жидкости на единицу периметра, кг/м.
С увеличением плотности орошения струйное движение становится неустойчивым. Как показали теоретические исследования П. Л. Капицы и
С. П. Капицы, более устойчивым является волновое течение с образованием гравитационных волн. В развитой ими модели [20, 21] принималось, что волновое движение является установившимся, наружная поверхность жидкости имеет в сечении форму синусоиды и амплитуда колебаний толщины пленки мала по сравнению с длиной волны. Теоретический анализ основывается на решении уравнений Навье-Стокса. Анализ показал, что переход от струйного течения к волновому происходит при некотором значении критерия Рейнольдса, называемом критическим волновым. Для определения критического волнового числа Рейнольдса получена формула
, (2.7)
где - поверхностное натяжение, Н/м.
Каждому удельному расходу жидкости соответствует определенная длина волн. Наибольшая скорость имеет место на гребнях волн, наименьшая во впадинах. Для определения средней толщины пленки получено выражение
. (2.8)
При установившемся волновом течении амплитуда волн составляет 0,46 от средней толщины пленки. На гребне волны поверхностная скорость принимает максимальное значение, в 2,3 раза превышающее среднерасходную скорость течения пленки, а усредненная по длине волны поверхностная скорость превышает среднерасходную в 1,34 раза.
Детальное исследование волнового пленочного течения жидкости выполнено Н. М. Жаворонковым и В. А. Малюсовым с сотрудниками [22, 23], давшими строгое решение системы уравнений Навье-Стокса и неразрывности в предположении, что установившееся волновое течение является потенциальным. Анализ показал, что при определенной средней толщине пленки максимальный расход жидкости получается для волнового режима течения с определенной длиной волны. С увеличением расхода жидкости фронт волны становится более резким и отношение максимальной толщины пленки к минимальной возрастает. При небольшой толщине пленки профиль скоростей в ее сечении близок к параболическому. Отклонение от последнего возрастает с ростом толщины пленки.
Характерная черта волнового течения - резкое падение скорости в наименьшем сечении пленки; здесь возможно направление скорости, противоположное направлению движения пленки. Это явление наблюдается при значении модифицированного числа Рейнольдса:
В работе [22] экспериментально определена средняя поверхностная скорость течения пленки в волновом режиме, которая представлена следующими эмпирическими соотношениями:
1) переходный режим
(2.9)
2) первый волновой режим
, (2.10)
3) второй волновой режим
(2.11)
Установившееся течение с длинными гравитационными волнами устойчиво в сравнительно узком диапазоне . По данным П. Л. Капицы и С. П. Капицы [20, 21], уже при
на поверхности крупных волн появляются мелкие волны и течение приобретает трехмерность. Такой режим волнового течения называют вторым волновым. Верхней его границей является число Рейнольдса, соответствующее переходу к турбулентному режиму.
Развитие турбулентности в пленке более затруднено, чем в сплошном потоке жидкости, поскольку размер образующихся вихрей ограничен толщиной пленки, а наличие свободной поверхности обуславливает колебания давления [24]. Граница перехода к турбулентному режиму течения пленки в значительной мере условна и зависит от возмущений на входе и случайных возмущений.
Принято считать границей перехода > 1600, а при обеспечении специальных мер по стабилизации потока на входе переход к турбулентному режиму отмечен [24] при
3000 .
В большинстве теоретических исследований пленочного течения при турбулентном режиме принимается трехслойная модель потока: ламинарный подслой, переходная область и область развитого турбулентного течения вблизи свободной поверхности пленки [25]. Распределение скоростей в этих областях описывается с помощью универсального профиля скоростей Прандтля-Кармана, основанного на использовании безразмерной скорости и безразмерной координаты по толщине плёнки :
;
, (2.12)
где v - скорость вдоль стенки , м/с ;
Y - её расстояние от стенки, м/c;
- скорость трения, м/c;
- касательное напряжение на стенке, Па;
.
Приемлемость универсального профиля скоростей Прандтля-Кармана для описания пленочного течения подтверждена экспериментально методом скоростной киносъемки движения окрашенного трассера, образующегося в пленке жидкости под действием ультрафиолетового излучения, тонкий луч которого создавался с помощью лазера [25]. Профиль скоростей при пленочном течении жидкости как для ламинарного, так и для турбулентного режимов хорошо передается одним уравнением:
. (2.13)
В связи с неявным видом функции (2.13) определение и v с ее ис-пользованием должно выполняться численными методами или графически.
Предложены эмпирические уравнения для определения средней толщины пленки при турбулентном течении жидкости [9]. Л. Я. Живайкиным и Б. Н. Волгиным предложено уравнение
(2.14)
Е. Г. Воронцовым предложено уравнение
(2.15)
Выше рассмотрено течение пленки жидкости по гладкой поверхности. При течении жидкости по шероховатой поверхности происходит турбулизация пограничного слоя за счет обтекания неровностей. В результате переход от ламинарного пленочного течения к турбулентному происходит при иных значениях критерия Рейнольдса, чем при движении жидкости по гладкой поверхности.
Исследования пленочного течения жидкости по трубам с иcкусственной шероховатостью в виде продольной, поперечной, шахматной накатки, сильно корродированной поверхности [26], а также по внутренней поверхности труб с поперечным элементом шероховатости прямоугольного профиля [27] показали, что при ламинарном режиме течения пленки ее средняя толщина может рассчитываться, как и для гладкой поверхности.
Средняя толщина пленки для турбулентной области течения в зна-чительной степени зависит от геометрических характеристик шероховатости. По данным работы [26]:
, (2.16)
где и n - значения, зависящие от вида шероховатости.
В работе [28] предложено уравнение
, (2.17)
где s и h - шаг и высота выступов шероховатости, м.
2.5.2 Неустановившееся течение и распределение жидкости в пленочных аппаратах
Равномерное распределение обрабатываемой жидкости по орошаемым поверхностям пленочных аппаратов представляет важную задачу, от решения которой в значительной степени зависит эффективность тепломассообменного оборудования.
При распределении жидкости с помощью различных распределительных устройств в пленочных аппаратах на входном участке происходит формирование профиля скоростей. При этом скорость является функцией координат как в поперечном, так и в продольном направлениях [3, 26].
В результате решения уравнения Навье-Стокса для неустановившегося течения пленки жидкости по орошаемой поверхности, имевшей на входе постоянную толщину и одинаковую по сечению скорость
, получен профиль скоростей по длине пленки. Расстояние x от входа жидкости, на котором стабилизируется профиль скоростей по длине пленки, можно найти из уравнения [3]:
, (2.18)
где
- толщина пленки при установившемся движении.
В исследованиях времени пребывания жидкости при гравитационном пленочном течении в трубах обнаружено [29], что эффективный коэффициент продольного перемешивания возрастает с увеличением длины пленки ℓ пропорционально ℓ0,32 Сходные результаты получены при исследовании перемешивания жидкости в колонне с плоскопараллельной насадкой [30]. Возрастание объясняют тем, что по длине пленки существенно меняются параметры волнового течения. Изменение параметров волнового течения наблюдается вплоть до очень больших длин пленки, и лишь при длинах, равных примерно 3,6 м, оно начинает затухать [29].
Растекание жидкости по орошаемым поверхностям тесно связано с условием стабильности пленочного течения. Теоретический анализ условия устойчивости изотермического пленочного течения основывается на сопоставлении поверхностных сил F1 и сил кинетической энергии текущей жидкости, направленных против потока F2 (рисунок 2.14).
Условие устойчивости имеет вид [31]
(2.19)
где - скорость течения жидкости в направлении силы, м/с;
- удельная свободная межфазная энергия жидкости на границе с окружающей средой, Н/м;
- краевой угол смачивания.
F1 - равнодействующая сил поверхностного натяжения; r - радиус кривизны поверхности
Рисунок 2.14 - Схема сил поверхностного натяжения на смачиваемой поверхности
С учетом того, что краевой угол при течении пленки отличен от статического угла смачивания
, а радиус изгиба поверхности жидкости на границе с несмоченной поверхностью пропорционален толщине пленки для
и
, получены следующие соотношения [32]:
(2.20)
(2.21)
где - краевой угол при течении пленки жидкости;
- коэффициент, который может быть функцией угла
.
Очевидно, если F1<F2, то возможно растекание жидкости, приводящее к растягиванию пленки. В исследованиях [33, 30] определена минимальная плотность орошения гmin , отвечающая условию равенства сил F1 и F2.
В исследованиях [33] на стальной трубке со смесью метанола и воды при изменении поверхностного натяжения от 30 до 73 дин/см, вязкости
от 0,26 до 26 спз и плотности
от 0,86 до 1 г/см3 для гmin получено эмпирическое уравнение
(2.22)
При отклонении орошаемой поверхности от вертикали величина гmin снижается [31].
Шероховатость уже в несколько микрон отражается на смачивании, изменяя краевой угол [34]. Кроме того, выступы шероховатости оказывают сопротивление течению пленки. Поскольку краевой угол смачивания подвержен гистерезису, то он отражается на значении минимальной плотности орошения гmin1, при которой возможно растекание, и на плотности орошения гmin2, когда произойдет разрыв пленки, причем гmin1>гmin2 [35].
Исследованно [34] растекание жидкости по поверхности, шероховатость которой имела вид продольных, поперечных и шахматных канавок трапецеидального сечения. При всех видах шероховатости с ростом высоты выступов h гmin1,2 увеличивается. Поперечные к направлению потока выступы шероховатостей оказывают местное сопротивление течению пленки и способствуют растеканию жидкости. Это проявляется в более низком значении гmin1 и более медленном возрастании гmin1 с ростом h. Продольная накатка увеличивает гmin1,2. Еще более возрастает гmin1 для шахматной накатки.
Если течение пленки жидкости сопровождается тепло- или массо-
передачей, то зависимость для гmin должна учитывать влияние этих факторов на поверхностное натяжение жидкости [31, 32].
2.5.3 Двухфазное течение газа и жидкости в пленочных аппаратах
Одной из важных характеристик тепло- и массообменных аппаратов является гидравлическое сопротивление. При движении газа в трубах сопротивление выражается уравнением
(2.23)
где - коэффициент гидравлического сопротивления;
wг - скорость газа в трубе, м/с;
z - длина трубы, м;
d - диаметр трубы, м.
Уравнение Дарси-Вейсбаха (2.23) при замене в нем диаметра трубы на эквивалентный диаметр канала становится универсальным, применимым к каналам любого поперечного сечения.
Эквивалентный диаметр вычисляют по формуле
d э = 4f/П, (2.24)
где f - сечение каналов, м2;
П - периметр каналов, м.
Если стенки каналов шероховаты, рекомендовано [27] находить dэ за вычетом объема, между выступами шероховатостей, занятого вихревым возвратным течением. В этом случае зависимости коэффициента сопротивления от числа Рейнольдса в ламинарном режиме для гладких и шероховатых труб совпадают.
Для круглых труб при ламинарном движении газа (Re г ):
. (2.25)
Турбулентное течение (Re>2300) для гладких труб:
, (2.26)
где Reг - число Рейнольдса, Re г =w г dэ
- динамическая вязкость газа, Па×с.
Для шероховатых труб при турбулентном течении зависит от размеров и форм шероховатости [27].
В общем случае зависит также и от формы сечения каналов, в которых движется газ [3, 37].
При движении газа в каналах гидравлическое сопротивление возрастает за счет влияния начального участка канала, на котором происходит стабилизация поля скоростей.
При пленочном движении жидкости по стенкам каналов в пленочных аппаратах гидравлическое сопротивление газового потока, движущегося в тех же каналах, выражается соотношением, принятым для однофазного потока [38, 39, 40].
(2.27)
где wотн - относительная скорость газа и жидкости, м/с;
- коэффициент сопротивления орошаемого канала;
d э1 - эквивалентный диаметр орошаемого канала, м.
В рассмотренном случае зависит, прежде всего, от состояния поверхности раздела фаз.
В экспериментальных работах [38, 39, 40] в широком диапазоне нагрузок по газу и жидкости в трубках с орошаемыми стенками показано, что волнообразование на поверхности пленки увеличивает толщину пленки аналогично, как шероховатость стенок трубы. С изменением скорости течения пленки жидкости изменяются параметры волнового течения, то есть изменяется шероховатость каналов. Для противотока получено: при ламинарном движении газа и Reпл 600
при турбулентном движении газа при Reпл <30
а при
<1600:
, (2.28)
где l - коэффициент сопротивления гладкой трубы.
Коэффициент сопротивления орошаемой трубы для прямотока зависит от режима течения пленки жидкости [40].
Ламинарно-волновое течение жидкости (Reпл<500):
l1=l. (2.29)
При 500£Reпл£1600:
l1=l(1,74×10-3 Reпл -0,11)+l, (2.30)
где Reж - критерий Рейнольдса для пленки жидкости;
l - коэффициент сопротивления гладкой трубы.
Критерий Рейнольдса:
Reпл =4Г/mж, (2.31)
где Г- массовый расход жидкости на единицу периметра трубы, кг/(м×с). Турбулентное течение жидкости (Reпл>1600):
l1=l(1,29×10-4 Reпл -0,16)+l. (2.32)
Для ламинарного движения пара(Reг£1400):
l=64/ Reг. (2.33)
В области турбулентного течения пара (Reг>1400):
l=0,335/ Reг0,25. (2.34)
Критерий Рейнольдса для паровой фазы рассчитывается по относительной скорости пара:
Reг=wот(dв-2d)/mг. (2.35)
Относительная скорость пара:
wот= , (2.36)
где Gп- массовый расход пара, кг/с;
vж- скорость движения поверхности пленки жидкости, м/с.
=
- скорость трения, м/c.
Известны и другие корреляции для [3]. Приведенные соотношения справедливы для слабого взаимодействия газа с жидкостью, так как не учитывают влияние движения газа на волновое течение пленки.
Теоретический анализ движения пленки жидкости по вертикальной поверхности при наличии напряжения трения на границе ее раздела с газом выполнен П. А. Семеновым. Им получено распределение скорости течения в пленке [41]:
(2.37)
где - градиент давления в направлении движения;
- напряжение трения на границе раздела фаз.
Уравнение (2.37) является приближенным, поскольку оно получено при условии, что наружная поверхность пленки жидкости гладкая и движется ламинарно.
В более поздних теоретических работах показано, что напряжение трения на границе раздела фаз при волновом пленочном течении жидкости изменяет распределение скоростей в пленке жидкости, а также фазовую скорость, длину и амплитуду волн [42]. Аналогичные результаты получены и при пленочном течении жидкости по шероховатым поверхностям [43].
При пленочном движении жидкости в вертикальных каналах касательные напряжения на границе раздела фаз выражают соотношениями, обычно принятыми для однофазного потока [3, 38, 39, 40]:
(2.38)
При противоточном движении с увеличением скорости восходящего потока газа увеличивается касательное напряжение, что в конечном итоге приводит к захлебыванию аппарата. При дальнейшем увеличении скорости газа имеет место однонаправленное восходящее движение обеих фаз. Теоретический анализ явления захлебывания представляет значительные трудности ввиду нестационарного характера гидродинамической обстановки, характерной для этого явления.
Известно много эмпирических уравнений для определения скорости газа, соответствующей захлебыванию [3, 36].
В более поздних работах для трубчатых пленочных аппаратов, работающих под вакуумом, предложено определять эту скорость для пленочных аппаратов по уравнению [44]
Y=4,2 exp(-4X)j,
, (2.39)
где D – внутренний диаметр труб, м.
2.6 Модели процессов в пленочных испарителях с падающей пленкой
2.6.1 Распределение жидкости по трубам в прямоточных и противоточных пленочных испарителях с отрицательной обратной связью по парообразованию
Расход жидкости в теплообменные трубы в зависимости от напора жидкости на переливе можно выразить уравнением, аналогичным таковому для слива через прорези трубы [45,46]:
Q = 795,8 pdвrж H2,24, (2.40)
где Q - расход жидкости в теплообменные трубы, кг/с;
dв - внутренний диаметр трубы, м;
rж - плотность жидкости, кг/м3;
H - напор жидкости на переливе, м.
Схема распределения жидкости по трубам испарителя представлена на рисунке 2.15.
Рисунок 2.15 - Схема распределения жидкости по трубам испарителя
На узком интервале изменения расхода жидкости напор на переливе
j-й трубы можно выразить через средний напор при среднем расходе жидкости Qср:
Hj = Hср(Qj/Qср)0,446. (2.41)
Сопротивление диафрагмы j-й трубы противоточного испарителя можно выразить через среднее сопротивление диафрагмы DРср при среднем расходе паров через нее (Qсреср):
DPj = DPср Qj2 еj2 rпj/ Qср2 еср2 rпср, (2.42)
где еср, еj - массовая доля отгона в средней по жидкостной нагрузке и j - й трубе;
rпср, rпj - плотность паров средняя и в j-й трубе, кг/м3.
В прямоточном испарителе расход пара меняется по длине теплообменных труб. В этих условиях сопротивление трубы можно найти как интегральное:
DPj = (2.43)
где ℓ1 - длина теплообменной трубы, м;
x - коэффициент сопротивления орошаемой трубы;
wот - относительная скорость пара, м/с;
d - толщина стекающей пленки, м.
Коэффициент сопротивления орошаемой трубы зависит от режима течения пленки жидкости и может быть определен с использованием ранее приведенных формул (2.29) – (2.36).
Подставляя уравнения (2.29)- (2.75) в уравнение (2.52) и интегрируя по длине трубы, найдем сопротивление трубы DP.
Разность уровней жидкости на трубной решетке около наиболее и наименее нагруженной теплообменной трубы:
, (2.44)
где max и min - индексы, относятся к наиболее нагруженной и наименее нагруженной трубе.
Ей соответствует неравномерность распределения жидкости по трубам:
. (2.45)
Из уравнений (2.42, 2.44) следует, что при прочих равных условиях DH возрастает пропорционально DPср:
. (2.46)
Допустимая неравномерность распределения жидкости по трубам пленочного испарителя с падающей пленкой может быть найдена из условия разрыва пленки при минимальной нагрузке испарителя по жидкости в минимально нагруженной трубе:
, (2.47)
где гmin- минимальный расход жидкости на единицу длины периметра, исключающий срыв пленки, кг/(м×с), может быть найден по уравнению
. (2.48)
Свойства жидкости следует определять при температуре кипения раствора.
2.6.2 Тепловой процесс в пленочных испарителях с падающей пленкой
Локальные коэффициенты теплоотдачи от трубы к пленке жидкости a1 рассчитываются по формуле Лабунцова [3]. При Reж³500:
, (2.49)
где Prж =Сжrжnж/lж - критерий Прандтля;
Reж= Г/mж;
lж - теплопроводность конденсата теплоносителя, Вт/(м×К);
rж - плотность конденсата теплоносителя, кг/м3;
nж - кинематическая вязкость теплоносителя, м2/с;
Сж – теплоемкость жидкости, Дж/кг.
При 60<Reж<500:
. (2.50)
Наихудшим случаем для рассматриваемого распределения жидкости по трубам испарителя будет использование в качестве теплоносителя конденсирующегося насыщенного пара, так как коэффициент теплоотдачи от теплоносителя к трубам a2 обратно пропорционален тепловой нагрузке qт трубы [47]:
, (2.51)
гдеlк - теплопроводность конденсата теплоносителя, Вт/(м×К);
rк - плотность конденсата теплоносителя, кг/м3;
rк - теплота конденсации теплоносителя, Дж/кг;
mк - динамическая вязкость теплоносителя, Па×с;
qт - удельная тепловая нагрузка теплообменной трубы, Вт/м2.
Коэффициент теплопередачи:
K= , (2.52)
где dст - толщина стенки трубы, м;
lст - теплопроводность стенки трубы, Вт/(м×К);
rт - термическое сопротивление отложений на трубах, (м2×К)/Вт.
Температуру начала и конца кипения обрабатываемой жидкости находили по уравнениям процесса однократного испарения.
Количество образующегося в теплообменной трубе пара обрабатываемой жидкости равно
, (2.53)
где rж - теплота испарения жидкости, Дж/кг;
tк, tн - температура конца и начала кипения жидкости, К.
Тепловая нагрузка qm, при которой начинается пузырьковое кипение и срыв пленки жидкости, может быть рассчитана по формуле
qm =[0,75A1 +(0,56A12 +130A2)0,5]2, (2.54)
где А1 =a1 ;
при 60<Reж<500;
при Reж>500;
Тнас-температура насышения, К.
ρп – плотность пара, кг/м3.
При отсутствии пузырькового кипения должно выполняться условие
KDtj <qm. (2.55)
2.6.3 Расчет процесса однократного испарения в испарителях
Однократное испарение - это процесс, при котором в течение всего периода сообщения системе тепла жидкую и образующуюся паровую фазу не разделяют, а по достижении известной конечной температуры нагрева - разделяют в один прием, то есть однократно.
Аналитический расчет процесса однократного испарения (ОИ) основан на уравнении материального баланса ОИ при установившемся равновесии [48].
Уравнение материального баланса процесса ОИ для каждого компонента смеси в относительных единицах равно
ci = еyi + (1- е)xi, (2.56)
где ci, yi, xi - мольная концентрация i - го компонента в сырье, парах и жидкости соответственно;
е - мольная доля отгона.
При установившемся равновесии
yi = ki xi, (2.57)
где ki - константа фазового равновесия i - го компонента.
Совместное решение уравнений (2.53) и (2.54) определяет величину концентраций компонентов в паровой и жидкой фазе.
; (2.58)
. (2.59)
В паровой фазе:
; (2.60)
в жидкой фазе:
. (2.61)
Уравнения (2.53) – (2.58) решают путем последовательного приближения относительно доли отгона е либо определяют давление или температуру при известной величине доли отгона е.
Начало кипения
. (2.62)
Полное испарение жидкости
. (2.63)
Аналитический метод расчета ОИ применим к сложным смесям. Для этого смесь условно разделяют на ряд фракций, которые отождествляют с индивидуальными компонентами, имеющими те же температуры кипения.
2.6.4 Равновесие между паровой и жидкой фазами
Для расчета нефтезаводских процессов необходимы сведения о состоянии равновесия между сосуществующими паровой и жидкой фазами.
При давлении p и температуре T в системе “жидкость - пар” комбинированное уравнение Дальтона-Рауля применительно к равновесным условиям имеет следующий вид:
, (2.64)
где Рi - давление насыщенного пара i-го компонента;
p - давление в системе.
В общем случае константа фазового равновесия ki изменяется в зависимости от концентрации, температуры и общего давления в системе, и потому термин константа равновесия является условным.
Уравнение (2.64) дает точные результаты только для идеальных систем, однако оно с достаточной точностью может описывать реальные системы близкокипящих гомологов при давлении не выше 0,3 МПа, когда свойства паров индивидуальных компонентов не сильно отличаются от свойств идеального газа. При высоких давлениях и температурах, близких критическим значениям для рассматриваемых компонентов, уравнение (2.61) не применяют.
Из большого числа различных методов определения констант фазового равновесия, известных в настоящее время [48], в учебной практике наиболее применима номограмма Уинна. Номограмма Уинна позволяет определять константы фазового равновесия в зависимости от температуры, давления и нормальной температуры кипения соединения. Номограммой Уинна можно пользоваться, если давление не привышает 70 МПа [1].
2.6.5 Давление насыщенных паров
Давление насыщенного пара - это давление, при котором паровая фаза вещества находится в состоянии равновесия с его жидкой фазой при определенной температуре.
Для индивидуальных углеводородов давление насыщенных паров компонентов находится по уравнению Антуана
LgP = А - , (2.65)
где А, В, С - константы, зависящие от природы веществ и от температуры.
Константы уравнения Антуана для большого количества веществ приведены в справочной литературе [49, 50].
Давление насыщенных паров нормальных парафиновых углеводородов при температуре Т рассчитывается по формуле Вильсона [48] в зависимости от температуры кипения Т0 при атмосферном давлении
LgP = 5,006 + Ав Вв, (2.66)
где Ав = ; (2.67)
Вв = . (2.68)
Давление насыщенных паров н-алканов и узких нефтяных фракций определяется по формуле Ашворта [48].
Lg ( P - 3158 ) = 7,6715 - ; (2.69)
f(T) = ; (2.70)
f(T) = , (2.71)
где Т - температура кипения при давлении Р, К;
Т0 - нормальная температура кипения К.
2.6.6 Динамические свойства распределительных устройств
с отрицательной обратной связью по парообразованию
Динамические свойства распределительных устройств рассматриваются как совокупность элементарных типовых звеньев. Они могут быть представлены обыкновенными дифференциальными уравнениями первого и второго порядков [51]. Для случая, когда переходные процессы во всех трубах осуществляются синхронно, структурная схема рассматриваемых распределительных устройств представлена на рисунке 2.16, а.
Рисунок 2.16 - Структурная схема распределительных устройств в пленочных испарителях с синхронными (а) и асинхронными (б) переходными процессами в трубах
Дифференциальное уравнение первого порядка представляет собой уравнение изменения уровня жидкости в распределительной камере в результате изменения расхода жидкости на входе в аппарат:
, (2.72)
где F - площадь сечения распределительной камеры (площадь трубной решетки за вычетом занятой распределительными устройствами), м2.
Уравнением второго звена является уравнение (2.73) расхода жидкости на переливе. В узком интервале изменения входной величины уравнение второго звена можно представить линейной зависимостью:
, (2.73)
где K2 - коэффициент усиления, м2/с.
Уравнение третьего звена учитывает изменение сопротивления труб или диафрагм при изменении расхода жидкости в трубы и может быть представлено дифференциальным уравнением первого порядка, если жидкость подается в аппарат при температуре кипения:
, (2.74)
где - изменение уровня жидкости на переливе за счет изменения расхода жидкости, стекающей в трубы, м;
K3 - коэффициент, c/м2.
Временная характеристика звена:
T3=l1/3vср, (2.75)
где vср - средняя скорость течения жидкости, м/с.
За время, равное 3Т3, изменение выходной величины D[DP/(grж)] достигает 95% от своего максимального значения.
Звенья, входящие в структурную схему (рисунок 2.16, а), являются соответственно интегрирующим, усилительным и апериодическим, а их передаточные функции могут быть представлены выражениями:
W1(P)=1/T1P; W2(P)=K2; W3(P)=K3/(T3P+1), (2.76)
где Т1=F - временная характеристика первого звена.
Передаточная функция системы:
; (2.77)
или
. (2.78)
Система будет устойчивой [51], если:
T1T3/K2>0 и [(1/K2)+K3]T1+T3>0. (2.79)
Форма переходного процесса зависит от корней характеристического уравнения:
. (2.80)
Величины K2, K3, T3 находятся с использованием статических характеристик, полученных при моделировании.
Для случая, когда переходные процессы во всех трубах осуществляются асинхронно, в качестве входной величины можно рассматривать высоту напора жидкости на переливе Н. Структурная схема, отвечающая этому случаю, представлена на рисунке 2.16, б. Передаточная функция этой системы описывается уравнением
. (2.81)
Система представляет апериодическое звено и устойчива, так как
K2K3+1>0. (2.82)
Если обрабатываемая жидкость подается в аппарат при температуре ниже температуры кипения, то:
, (2.83)
где t - время, с;
t - время запаздывания, необходимое для движения пленки жидкости по участку трубы, где происходит ее нагрев до температуры кипения, с.
Передаточная функция третьего звена:
. (2.84)
С учетом W3в(P) передаточная функция системы:
. (2.85)
Запаздывание является причиной перехода системы от устойчивой работы к неустойчивой.
Из вышесказанного следует, что устойчивой работы системы можно достичь при T1®0, применяя специальную конструкцию колпачков или патрубков, тесно прилегающих друг к другу и заполняющих всю площадь распределительной камеры. Это подтвердилось при испытании физической модели испарителя [45]. Опыты показали, что период и амплитуда пульсаций снижаются пропорционально произведению K3T1, а при K3Т1<0,5 с пульсации исчезают. В рассматриваемых опытах 0£t£0,3T3.
Исследования статических характеристик распределения жидкости по теплообменным трубам испарителей осуществлялось на математической модели. В качестве теплоносителя рассматривался насыщенный водяной пар давлением 2 МПа, обрабатываемой жидкости - смесь, состоящую из 30% (моль.) диэтиленгликоля и 70% (моль.) триэтиленгликоля. Систему уравнений (2.40)–(2.55) решали относительно DH в зависимости от В на ЭВМ [45].
Как следует из результатов расчета, поступление жидкости во все трубы испарителя осуществляется, даже если разность уровней на трубной решетке более чем на порядок превышает напор жидкости на переливе. Теплопроизводительность теплообменной трубы
Qтj=Qjejr. (2.86)
Сравнение средней теплопроизводительности наиболее и наименее нагруженных теплообменных труб с теплопроизводительностью теплообменной трубы Qтср со средней жидкостной нагрузкой показало, что в диапазонах изменения 1>B>0,3 и 0,08<e<0,8 при условии, что пленка течет по всему периметру всех труб:
/ Qтср³0,995. (2.87)
Следовательно, условие неразрывности пленки является достаточным для выбора неравномерности распределения жидкости по трубам.
Расчет пленочных испарителей может быть выполнен с применением программной системы АРМ «Пленочный испаритель» [52].
Для целей расчета однократного испарения без расчета пленочного испарителя может быть использован программный модуль «Программа расчета процесса однократного испарения Eva [53].
Теплофизические свойства индивидуальных веществ и нефтепродуктов, необходимых для моделирования процессов, можно рассчитать с использованием программного модуля АРМ «Свойства» (расчет теплофизических свойств индивидуальных веществ и нефтепродуктов) [54].
Сравнение энергопотребления в пленочных кипятильниках и кипятильниках с затопленными трубками можно рассчитать с помощью программного продукта «Технологический расчет теплообменного оборудования» [62].
2.7 Распределение жидкости в многопоточных испарителях с восходящей пленкой
Многопоточные пленочные испарители с падающей и восходящей пленкой наряду с преимуществами, присущими испарителям с падающей пленкой, имеют более высокие коэффициенты теплопередачи и требуют меньший расход циркулирующей жидкости.
Широкое применение пленочных аппаратов сдерживается необходимостью принудительной циркуляции жидкости с помощью насосов, следовательно, дополнительными затратами энергии.
Для устранения этого недостатка разработана серия конструкций многоходовых (многопоточных) пленочных [15].
Достоинствами многопоточных пленочных испарителей являются уменьшение расхода обрабатываемой среды, циркулирующей через аппарат, увеличение коэффициента теплоотдачи для восходящей пленки в сравнении с падающей пленкой и экономия пара (теплоносителя) за счет снижения температуры конденсации пара.
Высокая эффективность аппаратов достигается за счет использования распределительных устройств, в которых реализуется регулированием распределения жидкости по трубам с отрицательной обратной связью по парообразованию в них.
Повышенное гидравлическое сопротивление в трубах с восходящим движением пленки жидкости не оказывает существенного влияния при повышенном давлении в системе.
На рисунках 2.17 и 2.18 представлены схемы включения пленочных многоходовых испарителей в ректификационных системах, которые работают следующим образом.
Флегма колонны с глухой тарелки 1 поступает в верхнюю распределительную камеру испарителя на верхнюю трубную решетку, растекается по ней, затекает под колпачки и переливается через верхнюю кромку пленкообразователя в теплообменные трубы. Стекая по теплообменным трубам, низкокипящая часть обрабатываемой жидкости испаряется. Пар движется по теплообменным трубам в нижнюю распределительную камеру и через отверстия в боковой стенке патрубков поступает в теплообменные трубы с противоточным движением обрабатываемой жидкости, верхние концы которых, оканчивающиеся удлинительными патрубками, расположенными по другую сторону перегородки.
Рисунок 2.17 – Схема 1 подключения двухходового пленочного испарителя к ректификационной колонне
а б
Рисунок 2.18 – Схема 2 (а) и схема 3 (б) подключения трехходового пленочного испарителя к ректификационной колонне
Греющий пар подается через штуцер 3, а его конденсат выводится через штуцер 6. Затем пар и неиспарившаяся жидкость выходят из аппарата через штуцер в ректификационную колонну.
Запорные устройства 8 и 9 служат для дренирования жидкости в процессе остановки аппарата на ремонт, а для схемы 3 запорное устройство 9 также служит для поддержания нужного уровня обрабатываемой жидкости в нижней распределительной камере трехходового испарителя. При этом для уровнемера используются штуцера 10 и 11.
Насос 7 используется в представленных ректификационных системах для откачки жидкости из колонны (открыто запорное устройство 5). Дополнительная подача обрабатываемой жидкости в верхнюю распределительную камеру пленочного испарителя (открыто запорное устройство 4) осуществляется при пуске испарителя в работу. В этом случае обратный клапан 2 может быть закрыт.
В представленном на схеме (рисунок 2.17 а) трехходовом пленочном испарителе пар в третьем ходе испарителя может двигаться противотоком стекающей пленке жидкости и через верхний штуцер поступает в колонну, а жидкость поступает в колонну через нижний штуцер. Возможно также прямоточное движение всего пара и жидкости в третьем ходе испарителя. В этом случае верхний штуцер, соединяющий испаритель с колонной, должен отсутствовать.
На схеме (рисунок 2.17,б) предусмотрено противоточное движение пара и жидкости в третьем ходе испарителя.
Выбор той или иной схемы подключения испарителей зависит от расходов обрабатываемой среды и требуемой производительности системы по вторичному пару.
Схема распределения жидкости по трубам в секции испарителя с восходящей пленкой представлена на рисунке 2.19. Поток пара G и жидкость L из секции с падающей пленкой испарителя поступает в секцию испарителя с восходящей пленкой. Пар через отверстие в стенках труб поступает внутрь их и увлекает за собой жидкую фазу.
Рисунок 2.19 - Схема распределения уровня жидкости в нижней распределительной камере около наиболее нагруженной и наименее нагруженной теплообменной трубы
Модель распределения жидкой фазы по трубам восходящей секции испарителя с учетом разности уровня жидкости ΔН около наиболее нагруженной и наименее нагруженной трубы этой секции связана уравнением со скоростью пара ω.
, (2.88)
где max и min - индексы, относятся к наиболее нагруженной и наименее нагруженной трубе;
ξ – коэффициент сопротивления отверстия;
ωп – скорость пара в отверстиях, с-1.
Ей соответствует неравномерность распределения жидкости по трубам:
, (2.89)
где Qmax и Qmшт –максимальный и минимальный расход жидкости в теплообменные, м3/с.
Локальные коэффициенты теплоотдачи от трубы к пленке жидкости в восходящем потоке удобно представить в виде отношения коэффициента теплоотдачи при пленочном течении α1 к коэффициенту теплоотдачи αж при гомогенном потоке того же количества жидкости [56].
a1 =aж∙аХ-b, (2.90)
где Х- параметр Мартинелли;
а и b –коэффициенты.
Параметр Мартинелли зависит только от величины газосодержания φг
. (2.91)
Коэффициенты а и b у различных авторов имеют различное значение: по данным Денглера и Адомса а=3,5 и b=0,5; по данным Кольера и Пуллинга а=2,5 и b=0,7 [56].
Для нахождения величины гозосодержания, φг (или δ=1-φг), может использоваться уравнение [56]
, (2.92)
где Frг – критерий Фруда по газу;
Frж – критерий Фруда по жидкости;
λж – коэффициент гидравлического трения пленки жидкости;
λго – коэффициент гидравлического трения при движении газа в неорошаемых трубах;
Y – брызгоунос, характеризующий долю жидкостного потока, взвешенного в газе от всей жидкой фазы;
dв – внутренний диаметр трубы, м;
ρсм – плотность газожидкостной смеси, кг/м3.
Критерий Фруда по газу и жидкости определяется по следующим формулам
, (2.93)
, (2.94)
где Δρ – разность плотностей фаз, кг/м3;
Г – плотность орошения, м2/с.
Плотность газожидкостной смеси
. (2.95)
Для количественной оценки величины уноса в длинных трубах, когда происходит динамическое уравновешивание срыва капель и осаждения их на пленке, можно воспользоваться графической зависимостью Y от Х [56]
, (2.96)
где - средняя скорость пара, м/с;
s - поверхностное натяжение жидкости, Н/м.
Потери давления при восходящем пленочном течении определяются по следующей зависимости [56]
, (2.97)
где ℓ – длина трубы, м.
Наихудшим случаем для рассматриваемого распределения жидкости по трубам испарителя будет использование в качестве теплоносителя конденсирующегося насыщенного пара, так как коэффициент теплоотдачи от теплоносителя к трубам a2 обратно пропорционален тепловой нагрузке qт трубы (уравнение 2.51).
Коэффициент теплопередачи находится по уравнению 2.52.
Температура начала и конца кипения обрабатываемой жидкости находится по уравнениям процесса однократного испарения.
Количество образующегося в теплообменной трубе пара обрабатываемой жидкости равно
, (2.98)
где rж – теплота испарения жидкости, Дж/кг;
tк, tн - температура конца и начала кипения жидкости, К;
Δt – движущая сила процесса;
еj – доля отгона;
сj – теплоемкость, Дж/(кг·К);
Кj – коэффициент теплопередачи, Вт/(м·К);
j – индекс рассматриваемой трубы.
Моделирование испарителей с восходящей пленкой можно выполнить с использованием программного продукта АРМ «Восходящая пленка» [63].
Например, результаты моделирования испарения шестикомпонентной смеси остатка колонны К-2 производства товарного ортоксилола ОАО «Салаватнефтеоргсинтез» представлены на рисунках 2.20 – 2.25. Как следует из результатов моделирования, равномерность распределения жидкости по теплообменным трубам В = 0,15 может быть достигнута при разности уровней в нижней распределительной камере ΔН, равной 100 мм.
1 – В = 0,05
2 – В = 0,10
3 – В = 0,15
ξ = 0,2
Рисунок 2.20 – Зависимость уровня жидкости в нижней распределительной камере около наиболее нагруженной и наименее нагруженной теплообменной трубы от удельного расхода и неравномерности поступления жидкости в трубы
1 – ен = 0,3;
2 – ен = 0,33;
3 – ен = 0,36;
ен – началь-ная доля отгона;
ξ = 0,2
Рисунок 2.21 - Зависимость общего гидравлического сопротивления теплообменных труб с восходящим пленочном движением жидкости от ее расхода в испаритель
1 – ен = 0,3;
2 – ен = 0,33;
3 – ен = 0,36;
ен – начальная доля отгона; ξ =0,2
Рисунок 2.22 - Зависимость конечной доли отгона при восходящем пленочном движении жидкости от плотности орошения
1 – ен = 0,3; 2 – ен = 0,33; 3 – ен = 0,36; ξ = 0,2; ен – начальная доля отгона
Рисунок 2.23 - Зависимость коэффициента теплоотдачи от трубы к пленке жидкости от плотности орошения теплообменных труб при восходящем пленочном движении жидкости
Динамические свойства распределительных устройств рассматриваются как совокупность элементарных типовых звеньев. Они могут быть представлены обыкновенными дифференциальными уравнениями первого и второго порядков. Для случая, когда переходные процессы во всех трубах осуществляются синхронно, структурная схема рассматриваемых распределительных устройств представлена на рисунке 2.24. Для случая, когда переходные процессы во всех трубах осуществляются асинхронно, структурная схема представлена на рисунке 2.25.
Для схемы 2.24,а дифференциальное уравнение первого порядка представляет собой уравнение изменения уровня жидкости в распределительной камере в результате изменения расхода жидкости на входе в аппарат:
W1(P)= , (2.99)
где F - площадь сечения распределительной камеры (площадь трубной решетки за вычетом занятой распределительными устройствами), м2.
а – для жидкости; б – для пара
Рисунок 2.24 - Структурная схема распределительных устройств для восходящего потока с синхронными переходными процессами в трубах
Уравнением второго звена является уравнение расхода жидкости. В узком интервале изменения входной величины уравнение второго звена можно представить линейной зависимостью:
, (2.100)
где K2 - коэффициент усиления, м2/с.
а – для жидкости; б – для пара
Рисунок 2.25 - Структурная схема распределительных устройств пленочных испарителей для восходящего потока с асинхронными переходными процессами в трубах
Для схемы 2.24,б уравнением первого звена является уравнение расхода жидкости. В узком интервале изменения входной величины уравнение первого звена можно представить линейной зависимостью:
, (2.101)
где K3 - коэффициент усиления, м2/с.
Дифференциальное уравнение второго звена представляет собой
уравнение изменения уровня жидкости в распределительной камере в
результате изменения расхода жидкости на входе в аппарат
. (2.102)
Для схемы 2.25,а уравнение третьего звена учитывает изменение сопротивления труб или диафрагм при изменении расхода жидкости в трубы и может быть представлено дифференциальным уравнением первого порядка, если жидкость подается в аппарат при температуре кипения
, (2.103)
где - изменение уровня жидкости на переливе за счет изменения расхода жидкости, стекающей в трубы, м;
K4 - коэффициент, c/м2.
Уравнение четвертого звена представляет собой уравнение изменения поступления жидкости в трубы в результате изменения поступления количества пара
, (2.104)
где K5 - коэффициент усиления, м2/с.
Для схемы 2.25,б уравнение первого звена представляет собой уравнение изменения поступления жидкости в трубы в результате изменения поступления количества пара
, (2.105)
где K6 - коэффициент усиления, м2/с.
Уравнение второго звена учитывает изменение сопротивления труб и отверстий в трубах при изменении расхода жидкости в трубы и может быть представлено дифференциальным уравнением первого порядка, если жидкость подается в трубы при температуре кипения
, (2.106)
где K7 - коэффициент, c/м2.
Уравнение третьего звена учитывает изменение количества пара, поступающего в трубы, при изменении сопротивления труб или диафрагм и может быть представлено дифференциальным уравнением первого порядка, если жидкость подается в аппарат при температуре кипения
, (2.107)
где K8 - коэффициент, c/м2.
Передаточные функции:
W2(P)=K2; W3(P)=К4/(T3P+1); W4(P)=K5; W’1(P)=K6;
W’2(P)=-К7/(T4P+1); W’3(P)=-K8/(T5P+1). (2.108)
Передаточные функции системы:
;
. (2.109)
Временные характеристики звеньев:
T3=T4=l/(3νср ж); T5=l/(3νср п), (2.110)
где νср ж, νср п – средняя скорость течения жидкости и движения пара соответственно, м/с.
Коэффициенты типовых звеньев передаточных функций можно вычислить на основании моделирования распределения жидкости по тубам при дискретном изменении входных параметров. Коэффициенты К2, К4, K5, К6, К7 и К8 находятся с использованием статических характеристик.
Анализ динамических свойств восходящего движения пленки жидкости с синхронными и асинхронными переходными процессами в трубах испарителя с использованием передаточных функций системы показывает динамическую устойчивость процесса.
3 Модель ректификации с использованием теплового насоса
с совмещенным тепломассообменом
Для разделения близкокипящих компонентов рассматривается тепломассообменный аппарат, в котором теплообменные трубы выполняют роль контактных устройств, а сам процесс ректификации протекает в пленочном режиме.
При этом функции исчерпывающей секции выполняет трубное пространство, а функции конденсатора для образования дистиллята и укрепляющей секции – межтрубное пространство [55, 57].
Схема ректификации с совмещенным теплообменом представлена на рисунке 3.1.
Процесс ректификации с совмещенным теплообменом осуществляется следующим образом. Сырье вместе с флегмой из межтрубного пространства поступает в верхнюю часть тепломассообменного аппарата 1 и с помощью распределительных устройств распределяется по трубам и стекает по внутренней поверхности теплообменных труб в виде пленки. Пары в межтрубном пространстве 3 обогревают стенки труб, конденсируются на них и образующаяся флегма стекает вниз. Жидкость в трубном пространстве 2, стекающая в виде тонкой пленки, по стенкам труб обогреваемых снаружи теплом конденсирующихся паров, частично испаряется. Пар, образующийся в трубном пространстве 2, сжимается в компрессоре 4 и подается в межтрубное пространство 3 укрепляющей секции.
1 – тепломассообменный аппарат; 2 – трубное пространство; 3 – межтрубное пространство; 4 – компрессор; 5 – кипятильник, работающий во время пуска установки; 6 – ситчатая тарелка
Рисунок 3.1 - Схема процесса ректификации с совмещенным теплообменом
Для отвода дистиллята в межтрубном пространстве 3 установлена ситчатая тарелка 6, отделяющая укрепляющую секцию от конденсатора.
Теплообменные трубы ниже ситчатой тарелки 6 снабжены продольными ребрами U-образной формы, что позволяет увеличить поверхность теплообмена, и выполнены с переменным диаметром по длине для устойчивости пленочного течения жидкости по их внутренней поверхности (рисунок 3.2).
Рисунок 3.2 - Теплообменная труба с оребрением
Для достижения рабочих параметров процесса необходим пусковой теплообменник 5.
Распределительное устройство (рисунок 3.3) представляет собой патрубок с диафрагмой и выполняет функции регулятора расхода жидкости в теплообменные трубы.
Рисунок 3.3 - Схема распределения жидкости по теплообменным трубам
При увеличении расхода жидкости в ту или иную трубу исчерпывающей секции увеличивается количество парообразования в ней, что приводит к увеличению сопротивления диафрагм патрубков, тем самым снижается уровень жидкости в патрубке на переливе через край труб исчерпывающей секции и, следовательно, уменьшается расход жидкости в них, т.е. патрубки с диафрагмой выполняют функции регулятора расхода жидкости в трубы исчерпывающей секции.
Существенные отличия предлагаемого тепломассообменного аппарата от известных:
- совмещение процессов массообмена и теплообмена в одной конструкции кожухотрубчатого аппарата;
- процессы массообмена и теплообмена идут в пленочном режиме;
- поступление греющего пара в компрессор с верха исчерпывающей секции;
- подача греющего пара после компрессора в нижнюю часть межтрубного пространства аппарата, выполняющего функцию укрепляющей части ректификационной колонны.
Технические результаты разработанного тепломассообменного аппарата:
- снижение затрат энергии в результате снижения требуемой разности температур между теплоносителем и испаряемой жидкостью;
- увеличение поверхности теплообмена за счет оребрения теплообменных труб при равном объеме тепломассообменного аппарата;
- уменьшение гидравлического сопротивления движению пара в ректификационной колонне;
- снижение степени сжатия пара в компрессоре;
- снижение металлоемкости конструкции.
Таким образом, предлагаемый аппарат одновременно является теплообменным для создания парового орошения и флегмы с одновременным процессом массообмена между флегмой и паровым потоком. Это позволяет в 3–4 раза увеличить поверхность теплообмена, повысить коэффициент теплопередачи примерно в 2 раза в связи с использованием пленочного движения жидкой фазы, что позволяет снизить в 3 раза степень сжатия пара в компрессоре и снизить тем самым почти во столько же раз расход энергии.
Количество флегмы, сконденсировавшейся на 1 теоретической тарелке в результате процесса теплообмена в укрепляющей части аппарата, можно определить по формуле
, (3.1)
где К – коэффициент теплопередачи, Вт/(м2·К);
ΔF – поверхность теплообмена, соответствующая одной теоретической тарелке, м2;
Δt – разница температур в межтрубном и трубном пространствах аппарата, °С;
r – теплота парообразования смеси при температуре на теоретической тарелке.
Равновесная концентрация низкокипящего компонента (НКК) в жидкой фазе в укрепляющей части аппарата, находящейся на n-й тарелке
(3.2)
Рабочая концентрация НКК в паровой фазе, поступающей снизу на тарелку
, (3.3)
где PD – расход дистиллята, кмоль/ч;
n – номер тарелки;
– количество флегмы, сконденсировавшейся на iтеоретических тарелках, кмоль/ч;
хn-1 – равновесная концентрация НКК в жидкой фазе, находящейся на
n–1-й тарелке.
Максимальное флегмовое число
, (3.4)
где N1 – число теоретических тарелок в отпарной секции аппарата.
Постепенно переходя от тарелки к тарелке, начиная от состава дистиллята, расчет производим до тех пор, пока xn будет равна или меньше содержания НКК в сырье xF.
Расчет ЧТТ в исчерпывающей части выполняется по уравнениям (3.5), (3.6).
Рабочая концентрация НКК в жидкой фазе, стекающей с n-й тарелки
, (3.5)
где yn-1 – равновесная концентрация НКК в паровой фазе, находящейся на n–1-й тарелке.
Равновесная концентрация НКК в паровой фазе, находящейся на n-й тарелке
, (3.6)
где G0 – расход пара, подаваемого на всас компрессора, кмоль/ч;
– количество испарившейся жидкой фазы на n-1теоретических тарелках, кмоль/ч;
Тепловой расчет в тепломассообменном аппарате сводится к определению коэффициента теплопередачи по формуле
, (3.7)
где a1 – коэффициент теплоотдачи от трубы к пленке жидкости, Вт/м2∙К;
a2 – коэффициент теплоотдачи от теплоносителя к трубам, Вт/м2·К;
– сумма термических сопротивлений труб с загрязнениями.
Коэффициенты теплоотдачи a1 и a2 рассчитываются по уравнениям (2.49 – 2.51) с учетом теплофизических свойств компонентов.
Высота теплообменной трубы эквивалентная теоретической тарелки (ВЭТТ) в тепломассообменном аппарате определяется по уравнению
, (3.8)
где G – мольный поток пара, кмоль/с-1;
Коп – общий коэффициент массопередачи, кмоль/(м2×с);
F – площадь поперечного сечения секции колонны, м2;
а – удельная поверхность массообменных труб, м2/м3.
Коэффициент массопередачи определяется по уравнению
(3.9)
где m – тангенс угла наклона линии равновесия;
bг и bж – коэффициенты массоотдачи в газовой и жидкой фазах.
Коэффициент массоотдачи в газовой (паровой) фазе определяется из уравнения[58]
, (3.10)
где Nuг – критерий Нуссельта;
bг – коэффициент массоотдачи в газовой фазе;
d – диаметр трубы, м;
Dг – коэффициент диффузии, м2/с.
Перенос вещества в пленке жидкости, как и для паровой фазы, опре-деляется гидродинамической обстановкой, то есть режимом движения пленки. При ламинарном режиме движения преобладает диффузионный механизм переноса. По мере турбулизации жидкости возрастает роль переноса за счет турбулентных пульсаций.
Аналитический расчет массоотдачи в жидкой фазе осложняется взаимодействием фаз на границе их раздела, а также влиянием структуры орошаемой поверхности. В этой связи было предложено большое число различных моделей переноса вещества в пленке жидкости.
В работах [59-61] получены решения для массоотдачи в пленке с учетом входного участка, при волновом течении и течении по шероховатой поверхности. При малых амплитудах волн [58]:
, (3.11)
где bж – коэффициент массоотдачи в жидкой фазе, м/с;
a – амплитуда волны, м;
dср – средняя толщина пленки жидкости, м;
l – длина волны, м;
Dж – коэффициент диффузии, м2/с;
vср – средняя скорость движения пленки жидкости, м/с;
ℓ – длина пленки, м.
При больших амплитудах волн (35 £ Reж £ Reкр):
, (3.12)
где vж – скорость движения пленки жидкости, м/с.
На рисунке 3.4 представлена зависимость высоты трубы (ВЭТТ), эквивалентная теоретической тарелке, которая увеличивается с ростом фактора нагрузки (F) и диаметра труб.
В связи с тем, что увеличение флегмы в укрепляющей части происходит постепенно сверху вниз на поверхности теплообменных труб, следовательно, и флегмовое число (R) увеличивается постепенно. Вследствие, этого число теоретических тарелок (ЧТТ) в укрепляющей и исчерпывающей частей аппарата с совмещенным теплообменом требуется больше при прочих равных условиях, чем в ректификационной колонне с кипятильником.
Рисунок 3.4 - Зависимость высоты трубы (ВЭТТ), эквивалентная теоретической тарелке от фактора нагрузки (F), при внутреннем диаметре труб: 1 – dтр = 34 мм; 2 – dтр = 28 мм
Например, результаты расчета ректификации смеси пропана и пропилена представлены на рисунке 3.5.
1 – ректификационная колонна с совмещенным теплообменом при диаметре теплообменных труб dтр=38 мм; 2 – тарельчатая колонна с кипятильником Рисунок 3.5 - Зависимости числа теоретических тарелок (ЧТТ) от флегмового числа (R)
Моделирование процесса ректификации пропан – пропиленовой фракции в тепломассообменном аппарате с совмещенным теплообменом выявило его преимущество в сравнении с традиционными ректификационными системами.
1 Ректификационная колонна совмещает в себе испаритель и конденсатор, выполненные в одном аппарате, что приводит к снижению металлоемкости конструкции и повышает эффективность использования энергии.
2 Пленочная конденсация пара на оребренных трубах и испарение жидкости в пленочном режиме увеличивают коэффициент теплопередачи и поверхность теплообмена, что приводит к снижению затрат энергии.
3 Оребрение теплообменных труб позволяет увеличить поверхность теплообмена и массообмена в межтрубном пространстве.
4 Высокий коэффициент теплопередачи и большая поверхность теплообмена приводит к снижению разницы температур между конденсирующим паром и кипящей жидкостью в трубах колонны, что, в свою очередь, приводит к снижению требуемого давления пара после компрессора, т.е. степени сжатия пара и снижения затрат энергии.
5 В результате движения пара по прямым каналам внутри труб и в межтрубном пространстве уменьшается гидравлическое сопротивление движению пара.
6 Оребрение труб требует, при прочих равных условиях, более низкую разность температур между трубным и межтрубным пространством.
Применение тепломассообменного аппарата с совмещенным теплообменом снижает расход энергии, потребляемой компрессором более чем в три раза в сравнении с традиционной ректификационной системой.
БИБЛИОГРАФИЧЕСКИЙ СПИСОК
1 Справочник по теплообменникам: в 2 т. /пер. с англ., под ред. Б. С. Петухова, В. К. Шикова.-М.: Энергоатомиздат, 1987. –352 с.
2 Пленочная тепло- и массообменная аппаратура (Процессы и аппараты химической и нефтехимической технологии)/ под ред. В. М. Олевского. - М.: Химия, 1988. -240 с.
3 Коган В. Б., Харисов М. А. Оборудование для разделения смесей под вакуумом. - Л.: Машиностроение, 1976.- 374 с.
4 Циркуляционные и пленочные испарители и водородные реакторы /
Б. А. Трошенькин. - Киев: Наукова думка, 1985. - 176 с.
5 Соколов В. Н., Доманский И. В. Газожидкостные реакторы. - Л.: Машиностроение, 1975. - 216 с.
6 А. с. 1611360 СССР, МКИ4 В 01 D 1/08. Теплообменная секция пленочного аппарата/ Н. А. Воинов, А. А. Юдаков, Н. М. Коновалов, Н. А. Николаев (СССР). -№4653090/23-26; заявл. 21. 02. 89; опубл. 07. 12. 90, Бюл. №45.
7 Воронцов Е. Г. Минимальная плотность орошения пленкой стенок с упорядоченной шероховатостью // ЖПХ. - 1978. - Т. 51.- № 2. -С. 2713-2716.
8 А. с. 1581337 СССР, МКИ4 В 01 D 1/22. Пленочный выпарной аппарат/ Е. Г. Воронцов, Ю. М. Гандзюк и И. В. Ильинко (СССР).
-№4310314/31-26; заявл. 29. 07. 87; опубл. 30. 09. 87, Бюл. №28.
9 Тананайко Ю. Н., Воронцов Е. Г. Методы расчета и исследования пленочных процессов. - Киев: Техника, 1975.- 300 с.
10 А. с. 965439 СССР, МКИ3 B 01 D 1/22. Пленочный выпарной аппарат / М. В. Клыков, А. Г. Свинухов, Р. Б. Измайлов (СССР).
-№ 2811096/ 23-26; заяв.17.08.79; опубл. 15.10.82, Бюл. № 38.
11 А. с. 993967 СССР, МКИ3 B 01 D 1/22. Выпарной пленочный аппарат/ М. В. Клыков, А. Г. Свинухов, Р. Б. Измайлов (СССР).
-№ 2970927/ 23-26; заявл. 05.08.80; опубл. 17.02. 83, Бюл. № 5.
12 Клыков М. В., Измайлов Р. Б., Фомичева Л. А. Разработка пленочного испарителя с падающей пленкой //Всесоюз. конф. по теории и практике ректификации: - Северодонецк; ГосНИИметалпроект, 1984, - С. 10-12.
13 А. с. 1790965 СССР, МКИ4 B 01 D 1/22. Пленочный выпарной аппарат/ М. В. Клыков, Н. В. Патрина (СССР).-№4802218/26; заявл. 14. 03. 90; опубл. 30. 01. 93, Бюл. №4.
14 Пат. 2144412 РФ, МКИ4 B 01 D 1/22. Пленочный выпарной аппарат/
Н. Н. Истомин, М. В. Клыков (РФ).-№98112555/12; заявл. 29.06.98; опубл.
29. 06. 00, Бюл. №2.
15 Пат. 2178324 РФ, МКИ4 B 01 D 1/22. Пленочный выпарной аппарат/ М. В. Клыков, Н. Н. Истомин, Э.Ф Тимергазин. (РФ).-№99110098/12; заявл. 12.05.99; опубл. 20. 01. 02, Бюл. №2.
16 Клыков М. В., Тимергазин Э.Ф. Пленочные выпарные аппараты в ресурсосберегающей технологии// Химия и химические технологии – настоящее и будущее: сб. науч. тр. Междунар. науч. конф.- Стерлитамак, 1999, -С. 108-111.
17 Исследование турбулентных течений двухфазных сред /
З. Е. Накоряков, А. П. Будуков, Б. Г. Покусаев и др.; под ред. С. С. Кутателадзе. - Новосибирск: Изд-во СО АН СССР, ин-т теплофизики, 1973.- 315 с.
18 Fulford G. D. The flow of liguids inthin filns // Advances in Chemical Engineering, Bd. 5. N-Y.- London. Academie Press.- 1964.- P. 151-236.
19 Nusselt W. Die Oberflächenkondensation des Wasserdampfes // Zeitschrift Bd. I.- 1916.- N 27.- S. 514-546; № 28.- S. 669-575.
20 Капица П. Л. Волновое течение тонких слоев вязкой жидкости // ЖЭТФ.- 1948.- Т. 18.- № 1.- С. 3-28.
21 Капица П. Л., Капица С. П. Волновое течение тонких слоев вязкой жидкости // ЖЭТФ.- 1949.- Т. 19. -№ 2. -С. 105-133.
22 Мясников С. К., Кулов Н. Н., Малюсов В. А. Скорость движения свободной поверхности пленки жидкости при волновом течении // ДАН СССР. Хим. технология. - 1971. -Т. 197.- № 3.- С. 646-649.
23 Шкадов В. Я., Холпанов Л. П., Малюсов В. А., Жаворонков Н. М.
К нелинейной теории волновых течений пленки жидкости //Теоретические основы химической технологии. - 1970. -Т. 4.- № 6.- С. 859-867.
24 Ho F. C. K., Hummel P.L. Averege velocity distributions roithin falling // Liguid films. chem. Eng. Sci.- 1970.- V. 25.- № 7.- P. 1225-1237.
25 Germerdonk R. Gleichstromdestillation // Chem. Ing. Techn.- 1970.- Bd. 42.- № 22.- S. 1364-1366.
26 Воронцов Е. Г., Тананаико Ю. М. Теплообмен в жидкостных пленках. - Киев: Техника, 1972.- 196 с.
27 Субботин В. И., Ибрагимов М. Х., Тараков Г. С., Гусаков В. И., Чайстришин Н. С. Гидравлическое сопротивление труб с искусственной шероховатостью стенок при низких числах Рейнольдса. - Обнинск: Физико-энергетический ин-т, 1975.- 21 с.
28 Харин В. Ф., Николаев Н. А., Николаев А. М. Влияние шероховатости стенки на толщину пленки жидкости при гравитационном стекании // Изв. вузов. Сер. Химия и хим. Технология. -1972.- Т. 9.- С. 1406-1410.
29 Хернышев В. И., Олевский В. М., Галицкий А. Я. Распределение времени пребывания жидкости при гравитационном пленочном течении // Теорет. основы хим. технологии. - 1972. -Т. 6.- № 3.- С. 426-433.
30 Горожанкин Э. В., Олевский В. М., Ручинский В. П. Исследование гидродинамики пленочных абсорбционных аппаратов // Хим. и нефт. машиностроение. - 1969.- № 10.- С. 9-13.
31 Coulson H. Stabilitätsverhaltnisse bei Rieselfilmen // Chim. et ind.- Gen. Chim..- 1967.- V. 98.- № 4.- P. 669-685.
32 Puckenstein E. On the break-up of thin liquid layers flowing aloug a Surface // International Journal of Heat and Mass Transfer.- 1971.- V. 14.- P. 165-169.
33 Олевский 3. М., Ручинский В. Р. Ректификация термически нестойких веществ.- М.: Химия, 1972.- 200 с.
34 Зимон А. Д. Адгезия жидкости и смачивание. - М.: Химия, 1974.-
416 с.
35 Воронцов Е. Г. Минимальная плотность орошения пленкой стенок с упорядоченной шероховатостью // ЖПХ. -1978. -Т. 51. -№ 2. -С. 2713-2716.
36 Уоллис Г. Одномерные двухфазные течения. - М.: Мир, 1972. - 440 с.
37 Лойцянский Л. Г. Механика жидкости и газа. - М.: Наука, 1970.- 904 с.
38 Живайкин Л. И. К вопросу о методике расчета гидравлического сопротивления пленочных аппаратов // Теоретические основы химической технологии. - 1969.- Т. 3.- № 1.- С. 145-147.
39 Кадер Т. Л., Олевский В. М., Дмитриев М. А. Гидродинамика газового потока в пленочной трубчатой колонне при противоточном течении фаз // Теоретические основы химической технологии. - 1971. -Т. 5.- № 2.- С. 259-266.
40 Малюсов В. А., Мясников С. К., Кулов Н. Н. Гидравлическое сопротивление при движении в трубке с орошаемой стенкой // Теоретические основы химической технологии .- 1973. -Т. 7.- № 1.- С. 524-533.
41 Семенов П. А. Течение тонких слоев жидкости // ЖТФ, 1944. - № 7-8.
- С. 427-437; 1950. - № 8. - С. 980-990.
42 Холпанов Л. П., Шкадов В. Я., Малюсов В. А., Жаворонков П. М. Влияние газового потока на течение тонких слоев жидкости при волно-образовании // Теоретические основы химической технологии. -1973. -Т. 7.
-№ 5. -С. 788-792.
43 Полуэктов Н. Г., Свинухов А. Г., Кафаров В. В. Исследование гидродинамики и массообмена на сетчатой насадке // ЖПХ. -1977. -Т. 50.
- Вып. 7. - С. 1562-1568.
44 Трейман А. А., Михалл В. Я., Сийрде Э. К. Захлебывание при условии умеренного вакуума // Труды Талменского политехнического ин-та. Сер. А.
-1969. -№ 283. -С. 47-54.
45 Клыков М. В. Распределение жидкости в пленочных испарителях // Хим. технология. - 1989. - № 1 (163). - С. 67 - 72.
46 Клыков М. В., Свечников А. В. Модернизация выпарных пленочных аппаратов // Экономический рост: проблемы развития науки, техники и совершенствование производства: материалы межвуз. науч. – практ. конф. – Стерлитамак, 1996. - С. 24.
47 Основные процессы и аппараты химической технологии: пособие по проектированию / под ред. Ю. И. Дытнерского. - М.: Химия, 1983. - 272 с.
48 Расчеты основных процессов и аппаратов нефтепереработки: справочник /Рабинович Г. Г., Рябых П. М., Хохряков П. Л., и др.; под ред. Е. Н. Судакова. -3-е изд., перераб. и доп. – М: Химия, 1979. -568 с.
49 Рид Р., Праусниц Дж., Шервуд Г. Свойства газов и жидкостей: справочное пособие /пер. с англ.; под ред. Б. И. Соколова. – 3-е изд., перераб. и доп. – Л.: Химия, 1982. – 592 с.
50 Справочник химика. – М. –Л.: Химия, 1966. - Т. 5.-723 с.
51 Дианов В. Г. Автоматическое регулирование и регуляторы в химической промышленности. - М.: Химия, 1978. - 375 с.
52 Свидетельство отраслевой регистрации разработки № 5294. АРМ Пленочный испаритель/ М.В. Клыков, М.А. Эц. Зарегистрировано в отраслевом фонде алгоритмов и программ 25.08.2005.
53 Свидетельство отраслевой регистрации разработки № 10540. Программа расчета процесса однократного испарения Eva / М.В. Клыков, Е.Н.Журавлев. Зарегистрировано в отраслевом фонде алгоритмов и программ 29.04.2008.
54 Свидетельство отраслевой регистрации разработки № 5294. АРМ Свойства (расчет теплофизических свойств индивидуальных веществ и нефтепродуктов) / М.В. Клыков, А.Ю. Спащенко. Зарегистрировано в отраслевом фонде алгоритмов и программ 20.10.2005.
55 Клыков М.В., Сурков Г.С. Исследование ректификационной колонны с интегрированным теплообменом// Молодежь в науке: Новые аргументы: Сборник научных работ II-го Международного молодежного конкурса (Россия) Липецк: Научное партнерство «Аргумент», 2015. – С. 171-179.
56 Соколов В.Н., Доманский И. В. Газожидкостные реакторы. - Л.: Машиностроение, 1976. - 216 с.
57 Клыков М.В., Степанцов А.С. Ректификационная система с тепловой интеграцией // Нефтегазопеработка-2010: Материалы международной научно-практической конференции (Уфа, 26 мая 2010 г.). – Уфа: ГУП ИНХП РБ, 2010. – С. 35–36.
58 Холпанов Л. П. Гидродинамика и массообмен в активных гидродинамических режимах // Химическое и нефтяное машиностроение.
- 1997. - № 2. - С. 1-2.
59 Холпанов Л. Н., Шкадов В. Я., Малюсов В. А., Жаворонков Н. М. Исследование гидродинамики и массообмена в пленке жидкости с учетом входного участка //Теоретические основы химической технологии. -1976.
-Т. 10. -№ 5. - С. 659-669.
60 Бабак В. М., Холпанов Д. П., Малюсов В. А., Жаворонков Н. М. Сравнение результатов численного решения задачи двухфазного безволнового пленочного массообмена с экспериментальными данными //Теоретические основы химической технологии. - 1974. -Т. 8. - № 1. -С. 3-10.
61 Соколов В. Г. Массообмен при волновом движении тонкого слоя вязкой жидкости в контакте с газовым потоком //Теоретические основы химической технологии. - 1971. Т. 5. - № 4. - С. 519-525.
62 Свидетельство о государственной регистрации программы для ЭВМ № 2014617821. Технологический расчет теплообменного оборудования/ М.В. Клыков, С.В. Котов. Дата государственной регистрации в Реестре программ для ЭВМ 04.08.2014.
63 Свидетельство отраслевой регистрации разработки № 6448. АРМ Восходящая пленка/ М.В. Клыков. Зарегистрировано в отраслевом фонде алгоритмов и программ 22.06.2006.
Учебное издание
Клыков Михаил Васильевич
Моделирование пленочных тепломассообменных аппаратов
Редакто р М.Е. Галина
Подписано в печать . Бумага офсетная №2. Формат 60х84 1/16
Гарнитура «Таймас». Печать трафаретная. Усл. печ. л. 5,6. Уч.-изд. л. .
Тираж 120 экз. Заказ .
Издательство
Уфимского государственного нефтяного
технического университета
Адрес издательства:
450062, Республика Башкортостан, г. Уфа, ул. Космонавтов 1
Дата добавления: 2021-06-02; просмотров: 196; Мы поможем в написании вашей работы! |
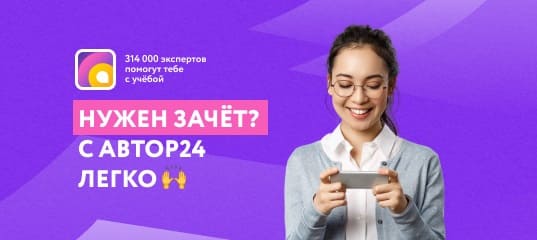
Мы поможем в написании ваших работ!