Рекомендуемые классы чистоты поверхности (заполнить дома)
Класс чистоты поверхности
Обозначение
Обрабатываемые поверхности
5
Rz20
Нерабочие поверхности зубчатых колес
Внутренние поверхность юбки поршня
Внутренняя нерабочая поверхность втулки
6
Rа2,5
Торцовые поверхности, служащие опорой для ступиц зубчатых колес.
Боковая поверхность зубьев больших модулей долбленных и строганных колес
Наружная поверхность зубчатого венца
Внутренняя поверхность корпуса под подшипники качения
7
Rа1,25
Нерабочие поверхности бронзовых колес
Опорная плоскость крышки блока
Опорная шаброванная плоскость контрольной инструментальной линейки
Шлифованный пруток для шпилек
8
Rа0,63
Сопрягаемые поверхности бронзовых колес
Нерабочие шейки коленчатого и распределительного валов
Гнезда под вкладыши коленчатого вала
Цилиндрическая поверхность силовых шпилек
Рабочие поверхности ходовых винтов
Поверхности валов под подшипники качения
9
Rа0,32
Наружная поверхность днища поршня
Отверстия поршневых бобышек палец под палец
Поверхность полок шатунов. Рабочие поверхности центров
Поверхности валов под подшипники качения классов В, А и с
10
Rа0,16
Рабочие шейки коленчатого вала быстроходного двигателя. Рабочие шейки распределительного вала. Рабочая плоскость клапана. Наружная поверхность юбки поршня. Поверхность лопастей крыльчатки нагнетателя
11
Rа0,08
Ведущий щиток клапана. Наружная поверхность поршневого пальца. Зеркало цилиндрической гильзы. Шарики и ролики подшипников качения. Рабочие шейки прецизионных быстроходных станков.
|
|
12
Rа0,04
Измерительные поверхности предельных калибров для 4 и 5го классов точности.
Рабочие поверхности деталей измерительных приборов в подвижных сочленениях средней точности Шарики и ролики высокоскоростных ответственных передач.
13
Ra0,1
Измерительные поверхности приборов и калибров высокой точности (1, 2 и 3го классов). Рабочие поверхности деталей в подвижных сочленениях средней точности.
14
Rz0,05
Измерительные поверхности плиток. Измерительные поверхности измерительных приборов весьма высокой точности. Измерительные поверхности плиток высоких классов. Поверхности исключительно ответственных точнейших приборов
Средство измерения (СИ) — это техническое средство или совокупность средств, применяющееся для осуществления измерений и обладающее нормированными метрологическими характеристиками. При помощи средств измерения физическая величина может быть не только обнаружена, но и измерена.
В научной литературе средства технических измерений делят на три большие группы. Это: меры, калибры и универсальные средства измерения, к которым относятся измерительные приборы, контрольно-измерительные приборы (КИП), и системы.
|
|
Калибрами называются бесшкальные контрольные инструменты, предназначенные для ограничения отклонений размеров, формы и взаимного расположения поверхностей изделий. При помощи калибров невозможно определить действительные отклонения размеров изделия, но их применение позволяет установить - находятся или нет отклонения размеров изделия в заданных пределах.
Калибры служат не для определения действительного размера деталей, а для рассортировки их на годные и две группы брака (с которых снят не весь припуск и с которых снят лишний припуск).
Иногда с помощью калибров детали сортируют на несколько групп годных для последующей селективной сборки.
В зависимости от вида контролируемых изделий различают калибры для:
· проверки гладких цилиндрических изделий (валов и отверстий),
· гладких конусов,
· цилиндрических наружных и внутренних резьб,
· конических резьб,
· линейных размеров,
· зубчатых (шлицевых) соединений,
· расположения отверстий, профилей и др.
Предельные калибры делятся на проходные и непроходные.
При контроле годной детали проходной калибр (ПР) должен входить в годное изделие, а непроходной (НЕ) входить в годное изделие не должен. Изделие считается годным, если проходной калибр входит, а непроходной - нет. Проходной калибр отделяет годные детали от брака исправимого (это детали, с которых снят не весь припуск), а непроходной - от брака неисправимого (это детали, с которых снят лишний припуск).
|
|
По технологическому назначению калибры делятся на рабочие калибры, используемые для контроля изделий в процессе изготовления и приемки готовых изделий работниками ОТК и контрольные калибры (контркалибры) для проверки рабочих калибров.
Основные требования к калибрам
1. Точность изготовления. Рабочие размеры калибра должны быть выполнены в соответствии с допусками на его изготовление.
2. Высокая жесткость при малом весе. Жесткость необходима для уменьшения погрешностей от деформаций калибров (особенно скоб больших размеров) при измерении. Малый вес требуется для повышения чувствительности контроля и облегчения работы контролера при проверке средних и больших размеров.
3. Износоустойчивость. Для снижения расходов на изготовление и периодическую проверку калибров необходимо принимать меры к повышению их износоустойчивости. Измерительные поверхности калибров выполняют из легированной стали, закаливают до высокой твердости и покрывают износостойким покрытием (например, хромируют). Выпускают также калибры небольших размеров, изготовленные из твердого сплава.
|
|
4. Производительность контроля обеспечивается рациональной конструкцией калибров; по возможности следует применять односторонние предельные калибры.
5. Стабильность рабочих размеров достигается соответствующей термообработкой (искусственным старением).
6. Устойчивость против коррозии, необходимая для обеспечения сохранности калибров, достигается применением антикоррозионных покрытий и выбора материалов, мало подверженных коррозии.
Штангенинструменты являются распространенными в машиностроении видами измерительного инструмента. Их применяют для измерения наружных и внутренних диаметров, длин, толщин, глубин и т. д.
Штангенциркули применяют трех типов: ШЦ-I, ЩЦ-И и ШЦ-Ш.
Штангенциркуль ШЦ – I: 1— штанга, 2, 7 — губки, 3— подвижная рамка, 4— зажим,5– шкала нониуса, 6— линейка глубиномера
Штангенциркуль ШЦ - I применяется для измерения наружных, внутренних размеров и глубин с величиной отсчета по нониусу 0,1 мм. Штангенциркуль (рисунок 1.8) имеет штангу 1, на которой нанесена шкала с миллиметровыми делениями. На одном конце этой штанги имеются неподвижные измерительные губки 2и 7а на другом конце линейка 6для измерения глубин. По штанге перемещается подвижная рамка 3с губками 2и 7.
Рамка в процессе измерения закрепляется на штанге зажимом 4.
Нижние губки 7 служат для измерения наружных размеров, а верхние 2 — для внутренних размеров. На скошенной грани рамки 3нанесена шкала 5, называемая нониусом. Нониус предназначен для определения дробной величины цены деления штанги, т. е. для определения доли миллиметра. Шкала нониуса длиной 10 мм разделена на 10 равных частей; следовательно, каждое деление нониуса равно 19:10=1,9 мм, т. е. оно короче расстояния между каждыми двумя делениями, нанесенными на шкалу штанги, на 0,1 мм (2,0—1,9=0,1). При сомкнутых губках начальное деление нониуса совпадает с нулевым штрихом шкалы штангенциркуля, а последний—10-й штрих нониуса — с 19-м штрихом шкалы.
Перед измерением при сомкнутых губках нулевые штрихи нониуса и штанги должны совпадать. При отсутствии просвета между губками для наружных измерений или при небольшом просвете (до 0,012 мм) должны совпадать нулевые штрихи нониуса и штанги.
При измерении деталь берут в левую руку, которая должна находиться за губками и захватывать деталь недалеко от губок, правая рука должна поддерживать штангу, при этом большим пальцем этой руки перемещают рамку до соприкосновения с проверяемой поверхностью, не допуская перекоса губок и добиваясь нормального измерительного усилия.
Рамку закрепляют зажимом большим и указательным пальцами правой руки, поддерживая штангу остальными пальцами этой руки; левая рука при этом должна поддерживать нижнюю губку штанги. При чтении показаний штангенциркуль держат прямо перед глазами. Целое число миллиметров отсчитывается по шкале штанги слева направо нулевым штрихом нониуса. Дробная величина (количество десятых долей миллиметра) определяется умножением величины отсчета (0,1 мм) на порядковый номер штриха нониуса, не считая нулевого, совпадающего со штрихом штанги. Примеры отсчета показаны на рисунке ниже.
39+0,1*7= 39,7; 61+0,1*4=61,4
Штангенрейсмусы предназначены для измерения высот от плоских поверхностей и точной разметки, изготавливаются по ГОСТ 164-90.
Штангенрейсмусы устроены следующим образом: они имеют основание с жестко закрепленной на нем штангой со шкалой, передвижную рамку с нониусом и стопорным винтом, устройство микрометрической подачи, которая состоит из движка, винта, гайки и стопорного винта, что позволяет устанавливать сменные ножки с острием для разметки (нанесения рисок).
Список рекомендованной литературы:
1. Зайцев С. А. Допуски и технические измерения. / С.А. Зайцев, А. Д. Куранов, А. Н. Толство. – М.: Академия, 2017. – 304 с.
2. Таратина Е.П. Допуски, посадки и технические измерения. Учебное пособие –М.:Академкнига \ Учебник, 2014
3. Зайцев, С.А. Допуски, посадки и технические измерения в машиностроении / С.А. Зайцев, А.Д. Куранов, А.К. Толстов. – М.: Академия, 2016. – 238 с.
Интернет-ресурсы:
3. https://studfiles.net/
Дата добавления: 2021-05-18; просмотров: 133; Мы поможем в написании вашей работы! |
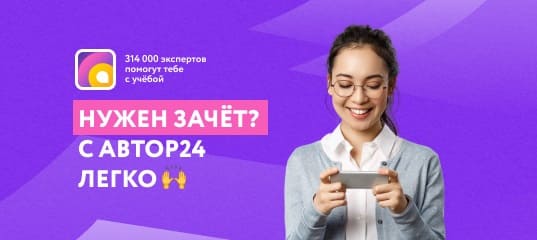
Мы поможем в написании ваших работ!