Расчет производительности пресса для склеивания фанеры и построение циклограммы
Методические указания на 16-19 занятия
Расчет древесного сырья и проклеивающих веществ
При изготовлении твердых ДВП расчет сырья и материалов определяются из расчета на 1000 м2 плит.
Чистый расход абсолютно сухого волокна, кг, определяется по формуле
![]() | (1) |
где – толщина плиты, мм;
– плотность плиты, кг/м3;
– абсолютная влажность готовых плит, %, принимаем
;
– коэффициент удержания проклеивающих веществ, принимаем
;
– суммарный расход проклеивающих веществ к абсолютно сухой массе волокна, %, принимаем по таблице А1 в зависимости от содержания древесины лиственных пород.
1.2 Общий расход технологической щепы, м3, определяется по формуле
![]() | (2) |
где Р – чистый расход абсолютно сухого волокна, кг;
– организационно-технические отходы, связанные с отбором проб, %, принимаем
%;
– неиспользуемые отходы, полученные в результате форматной резки плит, такие как пыль, опилки, принимаем
;
– отходы, полученные результате потерь волокна со сточными водами, %, принимаем
при содержании лиственных пород до 30 %
при содержании лиственных пород более 30 %
– выход древесноволокнистой массы от поступающей массы сырья, %, определяется по формуле
![]() | (3) |
где – выход массы, %, полученной после термообработки щепы в пропарочной камере дефибратора при t = 1850С и продолжительности пропаривания 1 минута, принимаем по таблице А2 в зависимости от содержания в щепе гнили и коры;
|
|
– коэффициент, учитывающий изменение выхода массы при отклонении температуры термообработки в пропарочной камере дефибратора, принимаем по таблице А3;
- коэффициент, учитывающий изменение выхода массы при отклонении длительности термообработки в пропарочной камере дефибратора, принимаем по таблице А4;
– коэффициент, учитывающий изменение выхода массы в зависимости от количества мелкой фракции, принимаем по таблице А5;
– средневзвешенная условная плотность древесины при заданном породном соотношении, кг/м3, определяется по формуле
![]() | (4) |
где – плотность древесины данной породы, кг/м3, определяется по таблице А6;
– доля данной породы в общем объеме сырья.
Расчет расхода проклеивающих веществ производится отдельно для каждого вещества по формуле
![]() | (5) |
где – расход данного вещества (П1 – парафина, П2 – серной кислоты, П3 – фенолформальдегидной смолы), кг;
– расход данного вещества к абсолютно сухой массе волокна, %, принимаем по таблице А1 в зависимости от содержания древесины лиственных пород.
|
|
Расчет расхода стружки, древесного сырья и проклеивающих веществ для производства однослойных ДСтП плоского и экструзионного прессования
Расчет расхода стружки
а) расход абсолютно сухой стружки на 1 м3 плит, кг/м3, определяется по формуле
![]() | (6) |
где – плотность изготавливаемых плит, кг/м3;
– абсолютная влажность готовых плит, %, принимаем
;
Р – средняя норма расхода связующего в пересчете га сухой остаток, %, принимаем Р=10 % для плит плоского прессования, Р=8 % для плит экструзионного прессования.
б) расход стружки с некоторой влажностью, %, определяется по формуле
![]() | (7) |
где – влажность стружки, %, принимается по заданию.
2.2 Расчет расхода древесины, м3, производится по формуле
![]() | (8) |
где – коэффициент, учитывающий потери при изготовлении ДСтП, определяется по формуле
![]() | (9) |
где – коэффициент потерь при разделке сырья, принимаем
;
– коэффициент, учитывающий вид сырья при сортировке щепы, принимаем
;
– коэффициент, учитывающий вид сырья, принимаем
для кусковых отходов,
для технологической щепы;
– коэффициент потерь стружки в период ее сушки, принимаем
;
|
|
– коэффициент потерь сырья при транспортировке стружки, принимаем
– коэффициент потерь сырья и смолы при обрезке плит по периметру, принимаем
;
– коэффициент потерь сырья и смолы при шлифовании плит, принимаем по таблице А7. Для экструзионных плит принимаем
;
– средняя условная плотность древесины, кг/м3, принимаем по таблице 6. При использовании нескольких древесных пород находится средневзвешенная плотность древесины по формуле
![]() | (10) |
где – плотность древесины данной породы, кг/м3, определяется по таблице А6;
– доля данной породы в общем объеме сырья.
2.3 Расчет расхода смолы на 1м3
а) Расчет расхода смолы определяется по формуле
![]() | (11) |
где – коэффициент потерь смолы на отдельных участках технологического процесса, определяется по фомуле
![]() | (12) |
где – коэффициент потерь смолы на участках ее приготовления и смешивания со стружкой, принимаем
.
Остальные коэффициенты принимаются такие же, как при расчете сырья.
б) расход жидкой смолы, кг, определяется по формуле
![]() | (13) |
где К – концентрация жидкого раствора смолы, %, принимается по заданию.
в) расход жидкого раствора отвердителя определяется по формуле
|
|
![]() | (14) |
где – расход отвердителя, %, принимаем
Расчет производительности пресса для склеивания фанеры и построение циклограммы
Производительность пресса, м3/час, определяется по формуле
![]() | (15) |
где – количество этажей пресса (принимается по технической характеристике пресса (таблица А8));
– количество пакетов, прессуемых на одном этаже пресса, для расчета принимается 1;
– площадь листа фанеры, м2;
– толщина фанеры, м, принимается из расчета по формуле
![]() | (16) |
где – суммарная толщина пакета шпона, помещенного в один промежуток пресса, мм, определяется умножением на слойность фанеры, которые приводятся в задании;
У – величина упрессовки, %, принимается по заданию.
Толщина фанеры принимается с градацией 0,5 мм. Например, по формуле (16) толщина фанеры получилась мм. Принимается
мм, 0,35 мм – припуск на шлифование.
– коэффициент использования рабочего времени, для расчета принимается 0,94-0,95;
– продолжительность (цикл) прессования, мин., рассчитывается по формуле (21).
Цикл прессования состоит из следующих операций и определяется в следующей последовательности:
1) Загрузка пакетов в пресс.
Продолжительность операции, с, определяется по формуле
![]() | (17) |
где – ход толкателя загрузочной этажерки, равный размеру пакета шпона, совпадающему с направлением движения толкателя, увеличенный на 150-200 мм;
– скорость движения толкателя загрузочной этажерки, равная 420 мм/с.
2) Подъем стола пресса до закрытия промежутков.
Продолжительность операции, с, определяется по формуле
![]() | (18) |
где – высота рабочего промежутка пресса, мм, принимается по технической характеристике пресса (таблица А8);
– суммарная толщина пакета шпона, помещенного в один промежуток пресса, мм, определяется умножением толщины шпона на слойность фанеры, которые приводятся в задании;
– число этажей пресса, принимается по технической характеристике пресса (таблица А8);
– скорость подъема стола пресса, мм/с, принимается по технической характеристике пресса (таблица А8).
3) Создание рабочего давления на пакеты шпона.
Продолжительность операции, с, определяется по формуле
![]() | (19) |
где – продолжительность подъема давления, с, отнесенная к одному этажу пресса (принимается как 0,2-0,3 с);
– число этажей пресса, принимается по технической характеристике пресса (таблица А8).
4) Выдержка пакетов под давлением.
Продолжительность операции, , определяется по таблице А9.
5) Снятие давления плит пресса на пакет шпона.
Продолжительность операции, , определяется по таблице А9.
6) Опускание стола пресса.
Продолжительность операции, с, определяется по формуле
![]() | (20) |
где – высота рабочего промежутка пресса, мм, принимается по технической характеристике пресса (таблица А8);
– суммарная толщина пакета шпона, помещенного в один промежуток пресса, мм;
У – величина упрессовки, %, приводится в задании;
– число этажей пресса, принимается по технической характеристике пресса (таблица А8);
– скорость подъема стола пресса, мм/с, принимается равной
.
7) Выгрузка фанер из пресса.
Выгрузка фанеры из пресса производится одновременно с загрузкой прессованных пакетов шпона.
Общий цикл работы пресса, с, определяется по формуле
![]() | (21) |
где – продолжительность каждой операции, входящей в общий цикл работы пресса, с.
После расчетов необходимо построить циклограмму прессования работы по принципу, показанному на рисунке 1.
Давление прессования подобрать самостоятельно исходя из того, что максимальное давление прессования составляет для хвойного шпона – 1,5-1,7 МПа, для березового шпона – 1,8-2,2 МПа. За время операции , давление снижается до 0,4-0,5 МПа.
Рис.1 – Циклограмма процесса прессования фанеры
- продолжительность загрузки пресса;
- продолжительность поднятия давления;
- продолжительность выдержки пакетов под давлением;
- продолжительность снятия давления;
- продолжительность размыкания плит пресса.
Дата добавления: 2021-05-18; просмотров: 488; Мы поможем в написании вашей работы! |
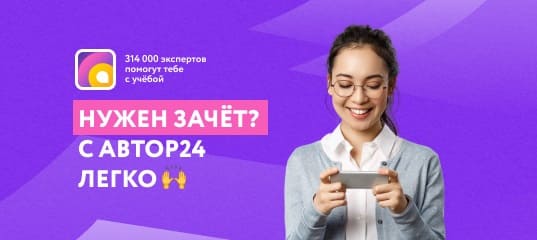
Мы поможем в написании ваших работ!