Безопасность технологического оборудования. Терминология ИСО/МЭК и стандартов РФ
ТРЕБОВАНИЯ К РАЗРАБАТЫВАЕМОМУ ТЕХНОЛОГИЧЕСКОМУ ОБОРУДОВАНИЮ
Анализ международных и российских стандартов в области надежности и риска машин и оборудования
Задачей анализа является установление связи, прямой или кос- венной, между динамично развивающимся и достаточно обширным рынком программных средств и системой стандартов, которые отно- сятся к вопросам надежности, риска и безопасности технологических (технических) систем на производстве [20]. По данным этого исследо- вателя возникла необходимость терминологического согласования та- ких терминов как «надежность», «риск», «безопасность» именно в области действия стандартов, а также оценки соответствия терминов,
определений и методов содержанию основных нормативных докумен- тов. Тем более, что во многих научных работах и нормативных доку- ментах часто встречаются сочетания «надежность и риск», «надеж- ность и безопасность», «риск и безопасность». Использование про- граммных методов в данном случае позволит свести к минимуму за- траты труда и времени на научные разработки.
Документом, регламентирующим основные понятия и термины в области надёжности, является ГОСТ 27.002-2015 «Надежность в тех- нике. Термины и определения». В этом документе надежность – это свойство объекта сохранять во времени способность выполнять тре- буемые функции в заданных режимах и условиях обслуживания, хра- нения и транспортирования объекта.
|
|
Безотказность: свойство объекта сохранять способность вы- полнять его функции в течение времени или в заданных режимах и условиях применения.
Ремонтопригодность: свойство объекта, заключающееся в приспособленности к поддержанию и восстановлению состояния, в котором он способен выполнять требуемые функции, при техническом обслуживании и ремонтах.
Восстанавливаемость: свойство объекта восстанавливаться после отказа без ремонта. При этом для восстановления могут требо- ваться или не требоваться внешние воздействия. Для случая, когда внешние воздействия не требуются, может использоваться термин самовосстанавливаемость.
Долговечность: свойство объекта, заключающееся в его спо- собности выполнять требуемые функции в заданных режимах и усло- виях использования, технического обслуживания и ремонта до дости- жения предельного состояния.
Сохраняемость: свойство объекта сохранять способность к выполнению требуемых функций после хранения и (или) транспорти- рования при заданных сроках и условиях хранения и (или) транспор- тирования.
Готовность: свойство объекта находиться в состоянии, в кото- ром он может выполнять требуемые функции в заданных режимах и условиях применения, технического обслуживания и ремонта в пред- положении, что все необходимые внешние ресурсы обеспечены. При этом готовность зависит от свойств безотказности, ремонтопригодно- сти и восстанавливаемости объекта.
|
|
Исправное состояние (исправность): состояние объекта, в ко- тором он соответствует всем требованиям, установленным в доку- ментации на него. Такое соответствие может быть определено как со-
стояние, в котором значения всех его параметров соответствуют тре- бованиям документации на этот объект.
Неисправное состояние (неисправность): состояние объекта, в котором он не соответствует хотя бы одному из требований, уста- новленных в документации на него. Несоответствие хотя бы одному из предъявляемых требований может быть определено как состояние, в котором значение хотя бы одного параметра объекта не соответст- вуют требованиям документации на него.
Работоспособное состояние: состояние объекта, в котором он способен выполнять требуемые функции. Оно может быть определе- но, например, как состояние объекта, в котором значения всех пара- метров, характеризующих способность выполнять заданные функции, соответствует требованиям, установленным в документации на этот объект. Отсутствие необходимых внешних ресурсов может препятст- вовать работе объекта, но это не влияет на его пребывание в работо- способном состоянии.
|
|
Неработоспособное состояние: состояние объекта, в котором он не способен выполнять хотя бы одну требуемую функцию по при- чинам, зависящим от него или из-за профилактического технического обслуживания.
Неработоспособное состояние определяется как состояние, в котором значение хотя бы одного из параметров, характеризующих способность выполнять заданные функции, не соответствует требо- ваниям документации на этот объект. Объект может быть способен выполнять одни функции и одновременно не способен выполнять дру- гие, в этом случае он находится в частично работоспособном со- стоянии – это примечание относится также и к термину.
Исправный объект всегда работоспособен, неисправный объ- ект может быть и работоспособным, и неработоспособным. Работо- способный объект может быть исправен и неисправен, неработоспо- собный объект всегда неисправен. Это относится к терминам «ис- правность» или «неисправность объекта».
Предельное состояние: состояние объекта, когда его даль- нейшая эксплуатация недопустима, нецелесообразна, или восстанов- ление его работоспособного состояния невозможно или нецелесооб- разно. Недопустимость эксплуатации устанавливается оценкой рис- ков, тогда как нецелесообразность или невозможность восстановле- ния устанавливают различными способами.
|
|
Критерий предельного состояния: признак или совокупность признаков предельного состояния объекта, установленные в докумен- тации на него.
Эти признаки устанавливаются по мере эксплуатации объекта.
Опасное состояние: состояние объекта, в котором возникает недопустимый риск причинения вреда людям, или окружающей среде, существенных материальных потерь, и других неприемлемых послед- ствий. Опасное состояние может возникнуть как в результате отказа, так и в процессе работы объекта.
Техническое состояние: состояние объекта, характеризуемое совокупностью установленных в документации параметров, описы- вающих его способность выполнять требуемые функции в рассматри- ваемых условиях.
Предотказное состояние: состояние, имеющее повышенный риск отказа. Предотказное состояние может возникнуть как от внут- ренних процессов (причин), так и внешних воздействий на объект при его функционировании.
Критерий предотказного состояния: признаки этого состояния объекта.
Система технического обслуживания и ремонта: совокуп- ность взаимосвязанных средств, документации обслуживания, ремон- та, исполнителей, требуемых для поддержания, восстановления ра- ботоспособности объекта.
Техническое обслуживание (ТО): комплекс организационных мероприятий и технических операций, направленных на поддержание работоспособности (исправности) объекта и снижение вероятности его отказов при использовании по назначению, хранении и транспор- тировании. Основные виды ТО:
– плановое ТО (другие отраслевые названия: профилактиче- ское, регламентированное ТО, постановка на которое соответствует документации;
– внеплановое ТО (другие названия: корректирующее, нерег- ламентированное), если постановка осуществляется без предвари- тельного назначения.
Эти термины должны использоваться и при составлении доку- ментации на технологическое оборудование, а также инструкций и со- проводительных документов при подтверждении соответствия про- дукции требованиям ТР.
Количественным показателем риска аварии является техниче- ский риск. Он определяется как вероятность отказа технических устройств с последствиями определенного уровня (класса) за опреде- ленный период функционирования опасного производственного объ- екта (ОПО). Это определение относится к производственному объекту как технической системе в состоянии отказа.
Анализ опасностей и оценки риска аварий на ОПО представляют совокупность научно-технических методов исследования опасностей возникновения, развития и последствий возможных аварий, вклю- чающую планирование работ, идентификацию опасностей аварий, оценку их риска, установление степени опасности аварий, разработку и корректировку мер по их снижению.
Состояние отказа классифицируется как опасное, т.е. состоя- ние, при котором возникают некоторые потери (убытки) в производст- венной и непроизводственной сфере жизнедеятельности человека, и могут нанести вред окружающей среде. Для идентификации рисков следует осуществлять систематическую проверку исследуемой сис- темы для своевременного определения и по возможности устранения типа (вида) неустранимых опасностей и способов (признаков) их про- явления. В настоящее время наиболее широко используются такие методы, как ведомости проверок работы и обзоры данных по эксплуа- тации. Также применяются методы исследования опасности (HAZOP), и анализ видов и последствий отказов – АВПО (FMEA). В программ- ных средствах идентификации риска в отечественной промышленно- сти используются средства, применяющие так называемую методоло- гию анализа древ неисправностей (FTA).
Количественная оценка риска по ГОСТ Р 51897-2011 – это про- цесс присвоения значений вероятности возможным последствиям риска. В описании методов оценки величины риска в ГОСТ Р 51901.1- 2002 отмечается, что при недостатке информации о системе или ее функционировании возможно использование количественного или ка- чественного ранжирования рисков специалистами или учеными, хо- рошо информированными в этой области.
Элементы процесса оценки величины риска включают в себя расчет частот появления (оценку вероятностей) и расчет последствий. Управление риском по ГОСТ Р 51897-2011 – это действия, осуществ- ляемые для выполнения решений в рамках менеджмента для сниже- ния степени риска. Иногда для обозначения этих действий используют термин «обработка риска», хотя последний больше относится к выбо- ру вида действий. Такими видами являются действия типа уменьше- ния риска и последствий, предотвращение риска и перенос риска.
Анализ и оценивание остаточного риска после реализации выполненных решений может также осуществляться как для опреде- ления достаточности реализованных действий, так и в рамках процес- са оценки риска.
Безопасность технологического оборудования. Терминология ИСО/МЭК и стандартов РФ
Безопасность обеспечивают путем снижения уровня риска до до- пустимого значения (допустимый риск). Допустимый риск представляет собой оптимальный баланс между безопасностью и требованиями, ко- торым должны удовлетворять продукция, процесс или услуга, а также такими факторами, как выгодность для пользователя, эффективность затрат, обычаи и пр. Другими словами допустимый риск не должен приводить к возможности появления опасных ситуаций, приводящих к возникновению отказов в процессе эксплуатации продукции [21].
Технический регламент ТР ТС 010/2011 предполагает использо- вание методов оценки надежности, применяемых и при анализе тех- нических рисков:
1. Анализ причин/следствий – комбинация ETA и FTA. Одним из вариантов этого метода является подход, предложенный в 1999 г. на Европейской конференции по безопасности и получивший название
«галстук-бабочка» (Bow-Tie approach), (рис. 8.1). На этом рисунке по- казан графический прием размещения схем деревьев отказов и собы- тий, давший название этому методу.
![]() |
Рис. 8.1. Графическая иллюстрация метода «галстук-бабочка»
2. Анализ динамических деревьев неисправностей (DFTA). Мето- дика анализа древ неисправностей развивалась в сторону учета дина- мических свойств анализируемых систем и вначале сводилась к до- бавлению к традиционным операторам (И, ИЛИ, НЕ, исключая ИЛИ) та- ких операторов, как «приоритетное И». При этом осуществлялся учет функциональных и вероятностных зависимостей элементов и загру-
женности резервных элементов. Современные методы анализа DFTA более широко используют результаты так называемого Марковского моделирования. Первый программный комплекс для анализа динами- ческих деревьев неисправностей разработан в университете штата Вирджиния, США, профессором Дж.Б. Дуганом (J.B. Dugan).
3. Двоичные диаграммы решений (Binary-Decision Diagrams – BDD). Их чаще применяют для анализа сложных логических функций, реализованных в микроэлектронных устройствах, являются графиче- скими аналогами аналитических методов ортогонализации. Применя- ется функциональный анализ отказов.
В рамках АВПО функциональные блок-схемы позволяют осуще- ствлять проектный анализ влияния отдельных компонентов на показа- тели стоимости разрабатываемых систем. Этот метод чаще использу- ется для разработки критериев оценки эффективности или человеко- машинного интерфейса.
Изложенные методики и подходы могут с успехом применяться при написании программного обеспечения к современным станкам с ЧПУ в программном модуле с открытым кодом под названием САПР ЧПУ «Тиграс» (Технологическая интерактивная графическая система1), а также при проектировании дорожных машин и подъемно-транспорт- ного оборудования. Для оценки рисков рекомендуется использовать ГОСТы из дополнительного списка литературы (см. с. 117). В нем при- ведены новые российские и соответствующие им международные стандарты по менеджменту риска.
Нормативная документация по менеджменту рисков учтена при составлении Программного комплекса автоматизированного структур- но-логического моделирования и расчета надежности и безопасности систем АРБИТР (ПК АСМ СЗМА). ПК Арбитр2 помогает разработчикам снизить появление рисков при проектировании нового и модернизации устаревшего оборудования. Среди многих полезных его функций сле- дует выделить пункты, рекомендуемые для расчета дорожных, техно- логических машин и оборудования:
– расчет коэф. готовности, средней наработки на отказ, среднего времени восстановления и вероятности безотказной работы восста- навливаемых систем;
– расчет показателей готовности смешанных систем, состоящих из восстанавливаемых и невосстанавливаемых элементов;
– расчет значимости разных вкладов элементов исследуемых систем;
![]() |
1См. URL: https://tigras.ru/ (дата обращения: 07.12.2017).
2См. URL: www.szma.com/pkasm.shtml (дата обращения: 07.12.2017).
– приближенный расчет вероятностных характеристик системы;
– структурный и автоматический учет отказов групп элементов по общей причине (модели альфа-фактора, бета-фактора и др.);
– учет различных видов зависимостей и множественных со- стояний элементов, представляемых с помощью групп несовмест- ных событий;
– учет числа циклических (мостиковых) связей между элемента- ми СФЦ;
– логико-статистическое моделирование вероятных показателей систем.
Анализ безопасности, надежности и рисков отказов в работе технологического оборудования при помощи отечественных про- граммных средств позволит повысить надежность и безопасность из- делий машиностроения, а также конкурентоспособность машино- строительных предприятий.
Вопросы и задания по главе 8
1. Какова роль стандартизации в обеспечении надежности оборудования?
2. Какие существуют виды состояния оборудования и каковы его характери- стики с точки зрения работоспособности и безопасности?
3. Что такое состояние отказа? Перечислите методы оценки рисков отказов.
4. Что такое остаточный риск? Дерево неисправности?
5. Что такое функциональный метод обнаружения отказов?
6. Каким ГОСТом регулируются марковские методы оценки рисков?
7. Что представляют собой и для чего применяются двоичные диаграммы?
Дата добавления: 2021-05-18; просмотров: 60; Мы поможем в написании вашей работы! |
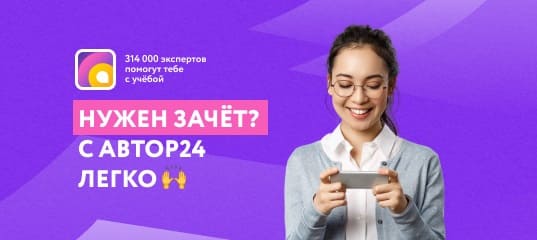
Мы поможем в написании ваших работ!