Ультразвуковой толщиномер УТ-82 1 страница
В.П. Ившин, М.Ю. Перухин, И.А. Дюдина, А.В. Фафурин
Интеллектуальная автоматика в курсовых и дипломных проектах
Том 2
Учебное пособие
|
2010
Федеральное агентство по образованию
Государственное образовательное учреждение
высшего профессионального образования
«Казанский государственный технологический университет»
Интеллектуальная автоматика в курсовых и дипломных проектах
Том 2
Учебное пособие
Казань
КГТУ
2010
УДК 658.5:66
ББК 32.965
И 28
Ившин, В.П.
Интеллектуальная автоматика в курсовых и дипломных проектах: учебное пособие (Том 2)/ В.П.Ившин, М.Ю.Перухин, И.А.Дюдина, А.В.Фафурин - Казань: Изд-во Казан. гос. технол. ун-та, 2010. - 220 с.
ISBN
Учебное пособие предоставляет студентам алгоритм самостоятельных действий по усвоению материала. Пособие содержит около 100 функциональных схем контроля и регулирования технологических параметров и будет, несомненно, полезно студентам всех форм обучения, изучающих дисциплину СУХТП, при выполнении ими дипломных (курсовых) проектов и дипломных работ.
Подготовлено на кафедре «Автоматизированные системы сбора и обработки информации» (АССОИ).
|
|
Табл. 33.; Ил. 57.; Библиогр.: 4 назв.
Печатается по решению редакционно-издательского совета Казанского государственного технологического университета.
Рецензенты: Начальник НИО-16 ФГУП ВНИИР, к.т.н. В.М. Красавин
Профессор кафедры спец. двигателей КГТУ (КАИ) А.С. Черенков
ISBN
ÓИвшин В.П., Перухин М.Ю.,
Дюдина И.А., Фафурин А.В., 2010
ã Казанский государственный
технологический университет, 2010
Глава 1. Автоматизированная система управления технологическими процессами (АСУТП)
§ 1. Автоматизированные системы управления (АСУ)
Автоматизированная система управления (АСУ) – это человеко-машинная система, обеспечивающая автоматизированный сбор, обработку информации и оптимизацию управления в различных сферах человеческой деятельности. Цель внедрения АСУ – создание общегосударственной системы управления всем народным хозяйством (ОГАС). Создание ОГАС возможно лишь на базе АСУ низших уровней:
|
|
· отраслевых автоматизированных систем управления (ОАСУ);
· автоматизированных систем управления производственными объединениями (АСУП);
· автоматизированных систем управления технологическими процессами (АСУТП).
АСУТП предназначены для выработки и реализации управляющих воздействий на технологический объект управления (ТОУ) в соответствии с принятым критерием управления и с помощью современных средств ЭВМ. ТОУ – это совокупность технологического оборудования и реализованного на нем по соответствующим регламентам технологического процесса. Критерий управления – это соотношение, характеризующее качество работы ТОУ в целом и принимающий конкретные числовые значения. Наиболее распространенным критерием управления является прибыль предприятия.
Классификация потенциально опасных процессов
Из всей совокупности процессов химической технологии можно выделить процессы, которые при определенных условиях выходит в аварийный режим. Причинами возникновения аварийной ситуации могут быть:
отступление от технологического регламента;
|
|
неисправность технологического оборудования;
отказ системы управления.
Такие процессы называются потенциально опасными процессами. Можно выделить 4 основных группы потенциально опасных процессов химической технологии:
1) процессы с токсичными веществами;
2) процессы с взрывоопасными веществами и смесями;
3) процессы с большой скоростью реакции;
4) смешанные процессы.
Специфика потенциально опасных процессов состоит в том, что они могут протекать в двух режимах:
1) нормальное функционирование;
2) предаварийное состояние.
Способность переходить в предаварийное состояние отличает потенциально опасные процессы от обычных процессов химической технологии.
Специфичность потенциально опасных процессов предопределяет особое требование к АСУ этими процессами. В составе АСУ должны иметься автоматические системы, которые обеспечивали бы управление процессом в предаварийном состоянии. Таковыми являются автоматические системы защиты АСЗ.
Таким образом, АСУ потенциально опасными процессами включает в себя: автоматическую систему регулирования (АСР), автоматическую систему защиту (АСЗ), автоматическую систему контроля (АСК), автоматическую систему сигнализации (АСС).
|
|
Функции систем АСУ потенциально опасными процессами
Автоматическая система регулирования (АСР), выполняет управление процессом в режиме нормального функционирования.
Автоматическая система защиты (АСЗ) анализирует предаварийное состояние и степень развития аварийной ситуации, осуществляет выбор управляющих воздействий, предотвращающих аварийную ситуацию. Они еще называются защитные воздействия. Защитные воздействия в зависимости от степени развития аварийной ситуации сводятся к двум видам: защитное воздействие, возвращающее процесс в режим нормального функционирования, т.е. они медленно завершают аварийную ситуацию; защитное воздействие, прекращающее процесс: сброс реакционной массы в специальную емкость, заполненную разбавителем, такая емкость еще называется аварийный чан; подача в реактор разбавителя для затормаживания процесса; подача жесткого хладагента и т.д.
Автоматическая система контроля (АСК) служит для получения информации о состоянии объекта и условиях его работы. Параметрами контроля этой системы являются входные и выходные параметры, характеризующие нормальный режим работы и предаварийное состояние.
Автоматическая система сигнализации (АСС) предназначена для автоматического оповещения обслуживающего персонала о наступлении интересующих процессов в управляемом объекте путем подачи звуковых и световых сигналов. Сигналы выдаются о значении параметров, характеризующие о возникновении аварийной ситуации и о состоянии исполнительных органов, выполняющих защитное воздействие.
В настоящее время АСУ потенциально опасными процессами строится на базе контроллеров и компьютеров. В частности, для системы АСР используется контроллер РСУ (распределенная система управления). Для системы АСЗ используется контроллер противоаварийной защиты (ПАЗ). Ниже представлена соответствующая структурная схема автоматизированной системы управления технологическим процессом (АСУТП). Внедрение АСУ является наиболее прогрессивным направлением в области автоматизации. При большом расстоянии между технологическими аппаратами и щитами управления целесообразно применять электрические средства автоматизации. Химические производства относятся к числу взрывопожароопасных, и автоматизация осуществляется на основе использования взрывозащищенных средств автоматизации с использованием контроллеров и персональных компьютеров (ПК). Контроллер – многофункциональное программируемое средство организации измерительных каналов.
Применительно к АСУТП, контроллер – это электронное устройство с программным управлением и расширенными аппаратными возможностями измерения, управления и связи. Иначе говоря, контроллер представляет собой электронную схему, управляющую технологическим оборудованием, собирающую и анализирующую данные, на основе которых принимаются те или иные решения. Основное назначение контроллера – связь между уровнем датчиков и исполнительных механизмов и уровнем управляющих ЭВМ (серверов).
Конструктивно контроллер представляет собой отдельное устройство, имеющее собственное питание. Контроллер может, как правило, функционировать автономно. При этом контроллер выполняется защищенным от пыли, влаги, электромагнитных излучений. В качестве локальных программируемых логических контроллеров (ПЛК) в настоящее время применяется большое количество устройств как отечественных, так и зарубежных производителей.
Структура ПЛК приведена на рисунке 1.1.
Рис. 1.1. Структура ПЛК
Блок согласования сигналов осуществляет электрическое согласование датчиков и исполнительных механизмов с входом блока преобразования сигналов.
Блок преобразования сигналов преобразует аналоговый электрический сигна, поступающий от датчиков, в цифровую форму и передает его центральному процессору, а также преобразует управляющие сигналы процессора в форму, необходимую для управления исполнительными механизмами.
Процессор осуществляет управление всеми блоками контроллера, математическую обработку измеренных технологических параметров, организует хранение данных в блоке памяти, а также осуществляет передачу данных через интерфейс в локальную вычислительную сеть (ЛВС). В данном случае роль ЛВС играет промышленная локальная сеть.
Основные задачи, решаемые контроллером:
ü измерение, опрос и управление оборудованием;
ü первичное преобразование результатов измерений;
ü хранение локального архива данных;
ü быстрая и надежная доставка информации на следующий уровень автоматизации;
ü обеспечение автономной и бесперебойной работы управляемого узла объекта автоматизации;
ü автоматическое управление локальным узлом автоматизации.
Локальный контроллер. В настоящее время распространяются несколько типов локальных контроллеров:
ü контроллер, встаиваемый в оборудование (агрегат, машину, прибор) и являющийся его неотъемлемой частью. Примеры такого «интеллектуального» оборудования: станки с программным управлением, автомашинисты, современные аналитические приборы;
ü автономный контроллер, реализующий функции контроля и управления небольшим, достаточно изолированным технологическим узлом (объектом).
Контроллеры, обычно, могут иметь десятки входов/выходов от датчиков и исполнительных механизмов. Их вычислительная мощность может быть разной (малые, средние и большие контроллеры). Они реализуют типовые функции обработки измерительной информации, логического управления, регулирования. Многие из них имеют один или несколько физических портов для передачи информации в другие средства/системы автоматизации.
Сетевой комплекс. Этот класс ПТК является наиболее широко распространенным и внедряемым средством управления технологическими процессами во всех отраслях промышленности. Программируемые микропроцессорные контроллеры – это построенные на основе МП специализированные устройства, предназначенные для реализации алгоритмов логического типа или алгоритмов аналогового управления.
Минимальный состав такого средства:
ü ряд контроллеров;
ü несколько дисплейных рабочих станций операторов;
ü системная (промышленная) сеть, соединяющая контроллеры и рабочие станции между собой.
Контроллеры определенного сетевого комплекса имеют обычно ряд модификаций, отличающихся друг от друга мощностью, быстродействием, объемом памяти, возможностями резервирования, приспособлением к разным условиям окружающей среды, максимально возмоным числом каналов входов и выходов. Это облегчает использование определенного сетевого комплекса для разных технологических объектов, поскольку позволяет наиболее точно подобрать контроллеры требуемых характеристик под разные отдельные узлы автоматизируемого агрегата и под разные функции контроля и управления.
Рассматриваемые сетевые комплексы контроллеров имеют верхние ограничения как по сложности выполняемых функций (обычно, типовые функции измерения, контроля, учета, регулирования, блокировки), так и по объему самого автоматизируемого объекта, в пределах десятков тысяч измеряемых и контролируемых величин (обычно, отдельный технологический агрегат, производственный участок).
Сетевые контроллеры (комплексы) выполняют следующие функции:
- воспринимают унифицированные аналоговые, дискретные электрические сигналы;
- измеряют и нормируют принятые сигналы;
- выполняют программную обработку сигналов с первичных преобразователей и формируют аналоговые и дискретные управляющие сигналы;
- отображают информацию на экране;
- управляются при помощи стандартной клавиатуры.
Пример типичного сетевого контроллера представлен рис. 1.2.
Рис.1.2. Сетевой контроллер БАЗИС-21
Технические характеристики БАЗИС-21
Ø макс, кол-во собственных вх. каналов ……………………56
ü двухпозиционных………………………………………..56
ü аналоговых……………………………………………….24
Ø макс, кол-во расчетных параметров……….………………24
Ø макс, кол-во вых. каналов………………………………….135
Ø внешних табло / кнопок квитирования……………………8
Ø кол-во событий архива ……………………………………1000
Ø цв. дисплей TFT — 5,5" (139 мм), кол-во цветов . . . . …256
Ø потребляемая мощность, ВА, не более …………………..50
Ø масса, кг, не более…………………………………………..5
Ø габаритные размеры: Н = 156 мм; В = 220 мм; L = 276 мм
Иерархическая структура АСУТП включает в себя;
- 1– й уровень полевого КИП;
- 2– й уровень - станции управления процессом;
- З–й уровень оперативного персонала, базирующийся на инженерных и станциях операторов технологического процесса.
1-й уровень АСУТП реализован на базе датчиков и исполнительных механизмов. На уровне 1 частично применяются датчики интеллектуальной серии, и на них выполняются функции опроса и шкалирования измеряемых сигналов с передачей информации по протоколу HART. Технические средства 2 и 3 уровней размещаются в помещении операторной. Станции управления процессом реализованы на базе контроллера РСУ (распределенная система управления), которая собирает информацию, вырабатывает регулирующие воздействия, и контроллера ПАЗ (система противоаварийной защиты) для контроля нарушений в ходе технологического процесса и осуществления защиты, блокировки аппаратов, выработки защитных воздействий.
Функции РСУ и ПАЗ выполняют программируемые контроллеры.
З-й уровень АСУТП представлен автоматизированными рабочими местами оператора-технолога и оператора-инженера. Обеспечивается ведение базы данных, визуализация состояния технологического оборудования, обработка данных, формирование и печать отчетных документов, ручное дистанционное управление технологическим оборудованием. Станции оснащены современными ПК. ПК обрабатывает по заложенной в него программе информацию, поступившую от датчиков, высвечивает на табло значения измеренных параметров. ПК применяется во-первых, для облегчения работы оператора, т.к. за короткий промежуток времени обрабатывается большое количество информации; во-вторых может выполнять роль «советчика», при котором ЭВМ рекомендует оператору оптимальные знания режимных параметров процесса. Информация с контрольно–измерительных приборов и датчиков в виде аналоговых и дискретных сигналов поступает с 1 уровня на технические средства 2 уровня, на которых реализуются в автоматическом режиме функции сбора, первичной обработки информации, регулирования, блокировки. Информация, необходимая для контроля и управления технологическими процессами, поступает от контроллеров на 3-й уровень - операторские станции и станции главных специалистов завода.
Структурная схема АСУТП, представленная ниже, наглядно демонстрирует связи между уровнями.Многие химические производства относятся к числу взрывопожароопасных, и автоматизация осуществляется на основе использования взрывозащищенных средств автоматизации с использованием контроллеров (сетевой комплексов) и станций управления на базе персональных компьютеров (ПК).
Нижеприведенные, применяемые в отечественной практике стандарты и нормативные документы устанавливают порядок проектирования, стадии и этапы создания АСУТП наиболее распространенных в отечественной химической промышленности:
1) ГОСТ 24.104-85 «Информационная технология. Автоматизированные системы управления. Общие требования».
2) ГОСТ 34.003-90 «Информационная технология. Автоматизированные системы. Термины и определения».
3) ГОСТ 34.201-89 «Информационная технология. Виды, комплектность и обозначение документов при создании автоматизированных систем (АС)».
4) ГОСТ 34.601-90 ЕСС АСУ. «Автоматизированные системы. Стадии создания».
5) ГОСТ 34.602-89 «Информационная технология. Комплекс стандартов на автоматизированные системы. Техническое задание на создание автоматизированной системы».
6) ГОСТ 34.603-92 «Информационная технология. Виды испытаний автоматизированных систем».
7) ГОСТ 24.701-86 ЕСС АСУ. «Надежность автоматизированных систем управления. Основные положения».
8) ГОСТ 24.702-85. ЕСС АСУ. «Эффективность автоматизированных систем управления. Основные положения».
9) ГОСТ 3.05.07-85 «Системы автоматизации».
10) РД 50-34.698-90 «Методические указания. Информационная технология. Знание этих документов поможет правильно поставить и решить задачу проектирования (модернизации) системы управления технологическим процессом предприятия, на котором будет осуществляться Ваша инженерная деятельность.
Условные обозначения ТСА в схемах. Обозначение измеряемых (регулируемых) величин в соответствии с ГОСТ 21.404-85
Изображение ТСА на схемах технологических процессов производится в соответствии с ГОСТ 21.404-85 [1] «Система проектной документации для строительства. Автоматизация технологических процессов. Обозначения условные приборов и средств автоматизации в схемах» (табл. 1.1). Авторы максимально использовали основные положения ГОСТа и рекомендации Международной организации по стандартизации (ISO). Цель раздела – изучение условных графических обозначений стандарта, а также обозначений измеряемых (регулируемых) величин и функциональных признаков ТСА. Условные обозначения ТСА, применяемые в схемах, включают графические, буквенные и цифровые обозначения. В верхней части графического обозначения наносят буквенные обозначения измеряемой величины и функционального признаков ТСА, определяющего его назначение. В нижней части графического обозначения наносят цифровое (позиционное) обозначение ТСА, первая цифра которого соответствует № локальной схемы, вторая - № ТСА в данной локальной схеме. Отборное устройство для всех ТСА изображают сплошной тонкой линией, соединяющей технологический трубопровод или аппарат с ТСА. Толщина линий, используемых в графических условных обозначениях на схемах, составляет: технические средства автоматизации - 0,6 мм; контуры технологического оборудования и трубопроводные коммуникации 1,5 мм. При необходимости указания конкретного места расположения отборного устройства (например, внутри технологического аппарата) его обозначают кружком Æ = 2 мм.
Дата добавления: 2021-05-18; просмотров: 62; Мы поможем в написании вашей работы! |
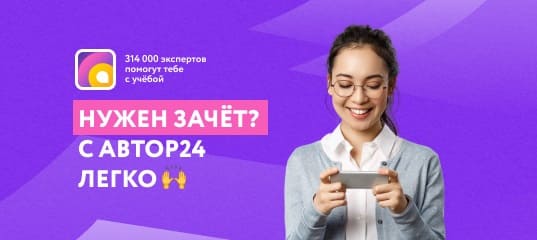
Мы поможем в написании ваших работ!