Ответ на домашнее задание (в виде сканкопий, фотографий или документов Microsoft Word)
МДК.03.04. ТЕХНОЛОГИЯ АВТОМАТИЧЕСКОГО И МЕХАНИЗИРОВАННОГО НАПЛАВЛЕНИЯ
Сварщик (электросварочные и газосварочные работы)
ПЛАН УРОКА № 4
Группа: СВ-4-18
Дата: 08.05.20 г.
Преподаватель ПТП: Л.Н.Иванова
Тема программы: АВТОМАТИЧЕСКАЯ НАПЛАВКА ПОД ФЛЮСОМ.
ТЕМА УРОКА: ПАРАМЕТРЫ РЕЖИМА АВТОМАТИЧЕСКОЙ НАПЛАВКИ.
Цель урока: познакомиться с параметрами режима автоматической наплавки под флюсом.
На предыдущих уроках мы уже определили, что автоматическая наплавка под флюсом по сравнению с ручной дуговой имеет ряд преимуществ:
а) улучшение качества наплавленного слоя;
б) увеличение производительности труда;
в) уменьшение расхода наплавочных материалов и более экономное расходование легирующих элементов;
г) уменьшение расхода электроэнергии;
д) улучшение условий труда.
На форму и размеры наплавленных валиков при автоматической наплавке под флюсом значительное влияние оказывает большое количество факторов.
ОСНОВНЫЕ ПАРАМЕТРЫ РЕЖИМА АВТОМАТИЧЕСКОЙ НАПЛАВКИ целесообразно определять со схемой, приведённой на рисунке 1.
Одним из основных факторов, определяющих эксплуатационные свойства восстановленных поверхностей, является марка электродной проволоки. Для механизированной наплавки под флюсом можно использовать сварочные проволоки (ГОСТ 2246-70) и наплавочные (ГОСТ 10543-82).
Состав флюса и его грануляция оказывают существенное влияние не только на устойчивость горения дуги, но и на форму и размеры наплавленного слоя. Флюсы сварочные наплавленные выпускаются в соответствии с ГОСТ 9087-81. Для механизированной наплавки углеродистых и низколегированных сталей углеродистыми и низколегированными наплавочными проволоками применяются флюсы АН-348, АН-348-АМ, АН-348-В, АН-348-ВМ, ОСЦ-45, ФЦ-9, АН-60.
Флюсы АН-348 обеспечивают удовлетворительную стабильность дуги при любом роде тока и хорошее формирование валиков наплавленного металла. Флюс обладает пониженной склонностью к образованию пор и дает удовлетворительно отделяемую шлаковую корку.
Флюсы ОСЦ обладают пониженной склонностью к образованию пор в наплавленном металле. Хорошее формирование валиков наплавленного металла получается при повышенном напряжении дуги. Недостатком этих флюсов является значительное выделение вредных фтористых газов.
Флюс АН-60 является заменителем флюсов АН-348-А и ОСЦ-45. Он обеспечивает хорошую отделяемость шлаковой корки. В сочетании с углеродистыми и низколегированными проволоками позволяет получить более высокую твердость наплавленного металла в сравнении с АН-348-А.
При автоматической наплавке под флюсом, тщательном выполнении процесса и хорошем формировании валика припуск на механическую обработку равен 1,5 - 2,0 мм на сторону.
Диаметр электрода зависит от формы наплавляемых деталей и толщины наплавленного слоя.
При восстановлении цилиндрических поверхностей под флюсом целесообразно учитывать диаметр детали и длину поверхности по образующей. Если длина наплавляемой поверхности небольшая, то в процессе наплавки деталь не успевает прогреться и отделяемость шлака будет удовлетворительной. В этом случае диаметр электродной проволоки можно увеличить.
Величина тока наплавки:
Јн=рdэл2ј /4
Јн =3,145260/12,5=245А.
Плотность тока ј = 9 - 12,5 А/мм².
Обычно большие величины плотности тока выбирают для меньших диаметров электродных проволок и наоборот. При этом следует иметь в виду, что наплавку деталей малых толщины и диаметров целесообразно во избежание прожогов металла выполнять на малых точках, а больших - на больших точках с целью повышения производительности труда.
Обычно наплавку различных деталей производят при напряжениях дуги 25-40 В. Более точно напряжение дуги можно подсчитать по формуле:
Uд=22+Јн/50
Uд =22+245/50=27 В.
Скорость подачи электрода:
Vэл= (4б Јн)/(рdэлс),
где бр - коэффициент расплавления, г/Ач;
Јн - ток наплавки, А;
dэл - диаметр проволоки, мм;
с - плотность металла проволоки, г/см³.
Vэл =411245/3,1457,8=88,03 мм/ч.
![]() |
ДОМАШНЕЕ ЗАДАНИЕ: составить краткий конспект по теме урока.
|
|
|
|
|
|
|
|
Ответ на домашнее задание (в виде сканкопий, фотографий или документов Microsoft Word)
прислать на электронный адрес:
larisanikolaevna.epgl@yandex.ru
ИНТЕРНЕТ-РЕСУРСЫ:
1. http://www.shtspt.ru/files/Metod_kop_Dolgoduch_10.pdf
2. https://helpiks.org/1-47283.html
3. https://studopedia.ru/14_136613_rezhimi-naplavki.html
4. https://pvrt.ru/regim/regim-63.html
Дата добавления: 2021-04-24; просмотров: 45; Мы поможем в написании вашей работы! |
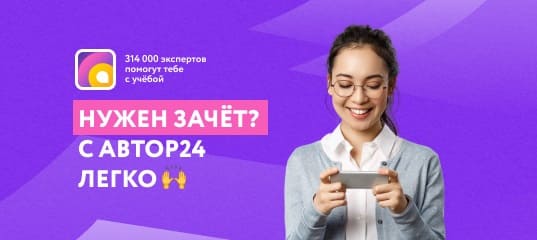
Мы поможем в написании ваших работ!