Преимущества комбинированного производства энергии
На объектах малой энергетики
Потребители устанавливают малые электростанции в рамках местных, локальных или распределённых энергетических систем. Часто модернизация технологических процессов для подобных установок идёт по пути создания когенерационных и тригенерационных систем, так как такие системы позволяют обеспечить повышение коэффициента использования топлива.
Когенерация предлагает механизм экономического стимулирования:
1. Высокие затраты на энергию могут быть уменьшены в несколько раз.
2. Уменьшение доли энергии в себестоимости продукции позволяет существенно увеличить конкурентоспособность продукта.
Темпы роста тарифов на энергию превышают темпы роста цен на продукцию большинства отраслей хозяйства. Это является одной из причин увеличения удельного веса затрат на энергию в себестоимости продукции.
При уменьшении выпуска промышленной продукции в 3-4 раза потребление энергии на предприятиях сокращяется всего лишь в 1,5-2 раза. Использование в производстве морально и физически устаревшего оборудования, объясняемое, прежде всего, отсутствием у большинства промышленных предприятий средств на его замену или модернизацию, приводит к нерациональному расходу энергетических ресурсов и лишь усугубляет ситуацию.
3. Некачественное электроснабжение – фактор замедления экономического роста. Когенерация является практически самым оптимальным вариантом обеспечения надёжности снабжения электрической энергией.
|
|
4. Энергозависимая экономика требует все больше и больше энергии для работы и развития. При традиционном энергообеспечении возникает множество организационных, финансовых и технических трудностей при росте мощностей предприятия, поскольку часто необходимы прокладка новых линий электропередач, строительство новых трансформаторных подстанций, перекладка теплотрасс. В тоже время, когенерация предлагает крайне быстрое решение в наращивании мощностей, может осуществляться как малыми, так и достаточно большими долями.
5. Стоимость прокладки коммуникаций и подключение к сетям могут по стоимости сравняться или превзойти стоимость проекта когенерации. Особенно это актуально для стран с большим количеством отдалённых от крупных городов поселений и объектов потребления. Малые ТЭЦ не требуют протяжённых энерголиний.
Когенерация позволяет воздержаться от бесполезных и экономически неэффективных затрат на средства передачи энергии, к тому же исключаются потери при транспортировке энергии, так как энергогенерирующее оборудование установлено в непосредственной близости от потребителя. Нормативные потери в теплосетях – 5 %, а реальные, в среднем, 12-16 % от передаваемой тепловой энергии.
|
|
6. Топливом электростанций на когенерации является газ, его преимуществом является относительная дешевизна, мобильность и доступность.
Когенерация уменьшает затраты на топливо/энергию – КПД производства энергии из первичного топлива увеличивается в 2-3 раза, потребители сокращают затраты на топливо на две трети и получают возможность эффективного применения утилизируемого тепла (сушка, охлаждение, кондиционирование и так далее).
Когенерация оптимизирует потребление природного газа – снижаются затраты на приобретение газа, требования к газовой инфраструктуре и беспокойство касательно запасов газа.
Когенерация фактически идеальная форма обеспечения энергией с точки зрения безопасности энергоснабжения.
Требования к энергоснабжению формулируются просто ‒ надёжность, постоянство. И для многих становится ясно, что на сегодня единственный путь иметь продукт высшего качества – произвести его самому.
В случае использования системы когенерации потребитель застрахован от перебоев в централизованном энергоснабжении, время от времени возникающих либо вследствие крайнего износа основных фондов в электроэнергетике, либо природных катаклизмов или других непредвиденных причин.
|
|
Когенерация обеспечивает огромный выигрыш в энергетическом КПД. Это происходит за счёт утилизации тепла выхлопных газов, в водяной рубашке охлаждения, в теплообменнике охлаждения масла и в промежуточном охладителе топливной смеси (данные действительны для большинства первичных двигателей).
Около 67% энергии первичного топлива, при традиционном способе генерации электроэнергии, выбрасывается в окружающую среду. В дальнейшем имеют место потери при передаче электроэнергии.
Утилизируемое тепло может быть использовано в технологических процессах, для производства холода, для отопления и кондиционирования помещений, для подогрева воды и т.д.
Вместе с тем существует возможность повышения КПД энергоустановки по отпуску электроэнергии на базе ДВС при обеспечении принципа комбинирования, аналогичного парогазовым установкам (ПГУ). В этом случае «горячим источником» для паросилового контура комбинированной установки является выхлоп ДВС, а не газовой турбины (рис. 14).
Выхлопные газы газопоршневой установки 1 поступают в котёл-утилизатор 2 и там нагревают питательную воду до состояния перегретого пара. Пар срабатывает в паровой турбине 3 и поступает в конденсатор 4. Затем основной конденсат проходит через теплообменник, где происходит его нагрев. Данный теплообменник обеспечивает
|
|
Рис. 14 – Принципиальная схема комбинированной мини-ТЭС:
1 – газопоршневая установка (собственно ДВС), 2 – котёл-утилизатор с дымовой трубой, 3 – паровая турбина, 4 – конденсатор, 5 – теплообменник рубашки охлаждения ДВС, необходимой для нормального функционирования двигателя,
6 – деаэратор, 7 – вентиляторная градирня
Выбор ГПУ (на базе газопоршневой установки JenbacherJMS 620 JS) обусловлен высоким электрическим КПД и температурой выхлопных газов (табл. 2), так как последняя позволит обеспечить относительно высокую температуру острого пара в паросиловом контуре.
Таблица 2 – Основные характеристики ГПУ Jenbacher JMS 620
Наименование показателя | Величина |
Номинальная мощность, кВт | 3044 |
Электрический КПД, % | 44,1 |
Расположение блоков | V-образование |
Количество цилиндров, мм | 20 |
Диаметр цилиндра, мм | 190 |
Ход поршня, мм | 120 |
Объём двигателя, л | 124,8 |
Объём выхлопных газов, нм3/ч | 13666 |
Температура выхлопных газов, ºС | 425 |
Габаритные размеры | |
Длина, мм | 8900 |
Ширина, мм | 2200 |
Высота, мм | 2800 |
Сухой вес, кг | 12000 |
Удельная стоимость, долл/кВт | 560 |
С учётом характеристик принятой ГПУ, параметры паросилового контура составляют P0 = 39 бар; t0 = 400°С; PК ≈ 0,1 бар.
Котёл-утилизатор может представлять собой конструкцию, состоящую из трёх контуров и барабана, последовательно обеспечивающих нагрев воды, испарение, сепарацию пара и его перегрев (рис. 15).
Рис. 15 – Компоновочная схема котла-утилизатора:
Б – барабан, ВЭ – водяной экономайзер, И – испаритель,
ПП –пароперегреватель, ЦН – циркуляционный насос
В результате исследования котла-утилизатора, проведённых с учётом положений, определены его тепловая мощность, паропроизводительность и некоторые другие характеристики (табл. 3).
Таблица 3 – Характеристики котла-утилизатора
Наименование параметра | Величина |
Тепловая мощность котла, МВт | 1,57 |
Паропроизводительность, т/ч | 2,0 |
Давление пара в барабане, бар | 43 |
Давление острого пара, ºС | 39 |
Температура острого пара, ºС | 400 |
Температура питательной воды, ºС | 111 |
Расход газов, тыс. м3/ч | 13,6 |
Температура газов на входе, ºС | 425 |
Температура уходящих газов, ºС | 167 |
Поверхность нагрева, м3 | |
водяного экономайзера | 90 |
испарителя | 141 |
пароперегревателя | 25 |
Площадь сечения для прохода газов, м3 | |
водяного экономайзера | 1,13 |
испарителя | 1,26 |
пароперегревателя | 1,26 |
Площадь сечения для пара и воды, м3 | |
водяного экономайзера | 0,0021 |
испарителя | 0,0079 |
пароперегревателя | 0,0039 |
Диаметр труб, dн/dвн, мм | 32/26 |
Габаритные размеры, м | |
длина | 11,4 |
Ширина | 5 |
Высота (без учёта барабана) | 6 |
Во-первых, теплового потока от покидающих ГПУ дымовых газов достаточно для того, чтобы сгенерировать около 2 т/ч пара с температурой ≈ 400 °С. Во-вторых, габаритные размеры котла-утилизатора позволяют выполнить его в модульной компоновке.
Дальнейшими расчётами показано, что полученный в котле-утилизаторе острый пар позволяет обеспечить работу паровой турбины мощностью около 0,5 МВт. Конструкторский расчёт паровой турбины позволил сформировать схему проточной части (рис. 15), из которой видно, что турбина имеет ступень скорости, десять активных ступеней и один нерегулируемый отбор для обеспечения работы деаэратора.
Рис. 16 – Схема проточной части турбины с указанием отбора
Таблица 4 – Характеристика паровой турбины
Наименование параметра | Величина |
Мощность турбины, кВт | 475 |
Расход пара, кг/с | 0,566 |
Давление пара перед/после стопорного клапана, МВт | 3,9/3,78 |
Располагаемый теплоперепад, кДж/кг | 1064 |
Давление в конденсаторе, кПа | 10 |
Давление в нерегулируемом отборе, Мпа | 0,15 |
Расход пара в нерегулируемом отборе, кг/с | 0,0021 |
Число ступеней, шт. | 11 |
Внутренний относительный КПД, % | 78 |
Высота лопаток последней ступени, мм | 87 |
Периферийный диаметр последней ступени, мм | 550 |
Длина ротора турбины, мм | 1380 |
Габаритные характеристики паровой турбины также позволяют выполнить её в блочно-модульном варианте.
Следует отметить, что для предлагаемой установки основным видом топлива является газ, при этом содержание оксидов азота в выхлопных газах не превышает 250 мг/м3, а высота дымовой трубы по расчёту составляет около 10 м при обеспечении ПДК в приземном слое атмосферы и с учётом фонового загрязнения, характерного для городских территорий.
Коэффициент полезного действия по отпуску электроэнергии
где Nгпу – мощность газопоршневой установки, МВт; Nпту – мощность паротурбинной установки, МВт; B, Qн р – расход, кг/с и низшая теплота сгорания топлива (МДж/кг) топлива.
КПД составит η = 50 %, что на 6 % выше, чем у заявленного КПД ГПУ JenbacherJMS 620 JS, и достаточно близок к показателям современных мощных парогазовых установок. При этом столь высокий показатель эффективности использования топлива обеспечен без любого рода оптимизации как термодинамических параметров комбинированной тепловой схемы установки в целом, так и термодинамических и конструктивно-компоновочных характеристик её силовых агрегатов.
Кроме энергетической эффективности предложенной схемы интерес представляют и некоторые технико-экономические оценки. Капиталовложения в котёл-утилизатор по массе основного металла:
где V – объём металла поверхностей нагрева и барабана, м3; ρ – плотность металла, кг/м; Ц – цена металла, руб/кг; k1 – коэффициент запаса, учитывающий затраты на необогреваемые трубы; k2 – коэффициент запаса, учитывающий затраты на каркас, обмуровку и изоляцию; k3 – коэффициент запаса, учитывающий затраты на изготовление.
Капиталовложения в паровую турбину, паропроводы и газопроводы, тягодутьевое оборудование, дымовую трубу, электрическую часть (эл. генератор, трансформатор, распредустройство, автоматику и КИП), низкопотенциальную группу определены по степенным зависимостям вид:
где K0 – базовые капиталовложения в соответствующую систему; ci – коэффициенты приведения, учитывающие тип турбины (К, Т, ПТ, Р и др.), тип привода питательного насоса, тип градирни, регион строительства и другие подобные факторы; xo j , x j – базовые и текущие значения влияющих параметров и показателей в виде параметров пара, мощности турбины и генератора, коэффициента собственных нужд, расхода и давления питательной воды, числа часов использования установленной мощности, высоты дымовой трубы и т.п.; n j – показатели степени; n – число коэффициентов приведения; m – число учитываемых влияющих параметров.
Себестоимость электроэнергии определена с учётом стоимости топлива (4300 руб/тыс. м3), отпуска электроэнергии с шин установки и издержек, руб/кВт·ч:
В этом выражении Ит , Иам , Ирем , Ифот – издержки на топливо, амортизацию, ремонт и заработную плату соответственно, руб; Э, кВт·ч – отпущенная с шин энергоустановки электроэнергия.
Результаты технико-экономических оценок имеют оценочный характер, так как во многом зависят от текущей конъюнктуры цен на оборудование, топливо, материалы, курсов валют (при закупке оборудования за рубежом), инфляционных процессов и других факторов экономического характера. Вместе с тем, проведённые расчёты позволяют сделать предварительную оценку экономической эффективности предлагаемой мини-ТЭС на основе газопоршневой и паротурбинной установок (табл. 5).
Таблица 5 – Технико-экономические показатели мини-ТЭС
Наименование показатели | Величина |
Расход натурального топлива, м3/с | 0,207 |
Низшая теплота сгорания топлива, кДж/м3 | 34000 |
Число часов использования, час/год | 6000 |
Установленная мощность, кВт | 3519 |
Отпуск электроэнергии, кВт*ч/год | 20,9∙104 |
Коэффициент собственных нужд, от ед | |
Мощность оборудования собственных нужд, кВт | |
Принудительная циркуляция | ,0 |
Тяга | 8,2 |
Циркуляционный насос | 4,9 |
Питательный насос | 12,0 |
Вентиляторная градирня | 2,1 |
КПД установки нетто, % | 50 |
Капиталовложения, руб | 80,3∙104 |
В том числе | |
ГПУ | 68∙104 |
Котёл-утилизатор | 2,0∙104 |
Паровая турбина | 6,1∙104 |
Паропроводы и газопроводы | 0,124∙104 |
Тяга и дутье | 0,156∙104 |
Насосная группа | 0,326∙104 |
Дымовая труба | 0,078∙104 |
Электрическая часть вместе с КИПиА | 1,526∙104 |
Низкопотенциальная группа с системой регенерации | 2.0∙104 |
Издержки, руб/год | 26,02∙104 |
В том числе | |
топливо | 19,3∙104 |
амортизация | 3,2∙104 |
Ремонт | 1,2∙104 |
ФОТ | 2,32∙104 |
Себестоимость энергии, руб/кВт | 1,24 |
Себестоимость электроэнергии при работе ГПУ, руб/кВт | 1,34 |
При всей условности технико-экономических оценок результат показывают, что комбинированная технология мини-ТЭС на базе ГПУ и паровой турбины может позволить снизить себестоимость электроэнергии на ≈ 8% по сравнению с работой ГПУ в автономном режиме даже без учёта оптимизации параметров схемы и оборудования. Такой результат может представлять интерес при принятии решений о размещении местной, локальной или распределённой системы электроснабжения.
Приложение 5
2018 г.
https://docplayer.ru/46092863-Kombinirovannaya-vyrabotka-elektricheskoy-i-teplovoy-energii.html
Газопоршневые мини-ТЭЦ
Газопоршневые установки на микро-турбинах, ввиду их компактности, позволят минимизировать затраты на подключение к централизованной сети, а также могут быть размещены в любом из помещений уже построенного здания.
В качестве второй проблемы можно выделить стоимость топлива, в связи с непостоянством позиций, которые необходимо постоянно учитывать в контексте энергетики. Однако и эта проблема легко решается посредством возведения мини-ТЭС. Газопоршневые электростанции работают на дешёвом виде топлива – на газах и их смесях, и, в зависимости от внешних обстоятельств, вы легко можете перестроить работу подобной электростанции с одного топлива на другое.
Газотурбинные электростанции отличаются от газопоршневых меньшей мощностью, это не критично при скромном энергопотреблении. Если вести рассмотрение с точки зрения оборудования, то при его покупке необходимо учитывать оптимальное соответствие региону заказчика и нуждам потребителя.
Благодаря своим техническим характеристикам, мини-ТЭС достаточно легко возводятся в краткий срок. Кроме того, при эксплуатации газопоршневой электростанции, как и другие виды мини-ТЭС, могут легко и точно регулироваться и работать в режиме экономичного расхода топлива, что обеспечивает их быструю окупаемость.
Ещё одно преимущество мини-ТЭС – их надёжность и экологичность. Газотурбинные электростанции, также как и газопоршневые, не наносят вред ни здоровью людей, живущих и работающих рядом с ними, ни окружающей среде в целом.
Проблема генерации собственной электрической и тепловой энергии стала заметно актуальнее с активным ростом тарифов на данные ресурсы. Многим крупным и средним предприятиям стало выгоднее генерировать собственную электроэнергию из газа. В таблице 6 представлены альтернативные способы генерации электроэнергии и тепловой энергии.
Таблица 6 – Альтернативные способы генерации электроэнергии и теплоты
Проблема | Способы решения | Цена вопроса за 1 кВт энергии | Трудоёмкость (дополнительные факторы) |
Излишняя трата предприятия на электроэнергию | Газопоршневые электростанции | 1000 евро | Сравнительно с микротурбинами частая смена газосмазочных материалов |
Микротурбины | 2000 евро | Долгое и трудоёмкое технологическое обслуживание | |
Паровые электростанции | 500-800 евро | Низкий КПД |
Преимущества газопоршневых установок:
1. Газопоршневые электростанции имеют более высокий КПД по сравнению с газотурбинными.
2. Незначительное снижение КПД газопоршневых мини-ТЭЦ при снижении электрической нагрузки в диапазоне регулирования. При 50 % нагрузке КПД газовой турбины снижается в 1,5 раза от КПД при номинальной нагрузке, в то время как КПД газопоршневого генератора в тех же условиях снижается лишь на 2,5-3 %.
3. Стабильность КПД газопоршневой установки при изменении параметров окружающей среды. Эффективность газотурбинного двигателя в большей степени зависит от температуры воздуха на всасывании компрессора. Если температура окружающего воздуха увеличивается, электрический КПД газотурбинного генератора значительно падает. Для газопоршневых установок эта зависимость носит менее критичный характер.
4. Меньшая (по сравнению с газотурбинными установками) чувствительность газопоршневых мини-ТЭЦ к частым пускам и остановкам.
5. Простота обслуживания газопоршневых мини-ТЭЦ. Техобслуживание и ремонт газопоршневых генераторов проводится по месту установки, в то время как ремонт газовых турбин производится, как правило, на заводе изготовителе.
ГПЭ представляет собой двигатель внутреннего сгорания с внешним смесеобразованием и искровым зажиганием горючей смеси в камере сгорания, использующий в качестве топлива газ. Энергия, которая выделяется при сгорании топлива, в газовом двигателе производит механическую работу на валу, использующуюся для выработки электроэнергии генератором электрического тока. Газовые двигатели используются для работы в составе генераторных установок, предназначенных для постоянной и периодической работы (пиковые нагрузки) с комбинированной выработкой электроэнергии и тепла, а также в качестве аварийных источников энергии. Кроме того, они могут работать как в составе холодильных установок, так и для привода насосов и газовых компрессоров.
За счёт собственной генерации энергии потребитель платит только за используемый газ, и тариф на электроэнергию среднем в 3-3,5 раза дешевле, чем тариф от централизованного тепло и электроснабжения. Качество теплоснабжения повышается за счёт того, что тепло генерируется рядом с местом потребления и не успевает потерять своих свойств при передаче потребителю. Тариф на тепло уменьшается в среднем в 2 раза.
Окупаемость внедрения ГПЭ зависит от мощности установки ГПЭ, чем мощнее электростанция, тем быстрее она окупится, в среднем окупаемость 4-5 лет без учёта повышения тарифов на электроэнергию и тепло централизованного энергоснабжения.
Газопоршневые установки (электростанции, станции) предназначены для производства электричества и дешёвой тепловой энергии. Среди типов силовых агрегатов, газопоршневые установки отличает простота, надёжность конструкции и самый высокий электрический КПД. Электрический КПД современных газопоршневых установок при работе на российском природном газе составляет примерно 41-44 % Большинство марок газопоршневых станций (установок) может работать в режиме когенерации, то есть как теплоэлектростанции. Температура выхлопных газов на выходе из двигателя газопоршневой установки равна примерно 390 ± 30 °С. Такая температура на выходе станции позволяет отдавать достаточно высокие объёмы бесплатной тепловой энергии.
Соотношение выдачи двух видов энергий при работе газопоршневой электростанции на номинальном режиме составляет пропорцию 1:1. То есть на 1 МВт установленной электрической мощности можно получать 1 МВт тепловой энергии (1 МВт = 0,86 Гкал/час). При необходимости возможно получение промышленного пара.
Система охлаждения газопоршневых установок жидкостная. В случае использования воды для охлаждения поршневых агрегатов станции желательна её химическая подготовка, но в 99 % применяются обычные незамерзающие жидкости. Расход моторного масла газопоршневой станции составляет примерно 0,3-0,95 кг/ч на 1 мегаватт выработанной электрической энергии. Уровень расхода моторного масла связан с характером и равномерностью электрических нагрузок.
Стоимость моторного масла для газопоршневых силовых агрегатов электростанций составляет примерно 100-150 руб./л. В целом для будущих владельцев газопоршневых станций размер затрат на приобретение моторного масла не столь важен и критичен – у современных газопоршневых установок стоимость масла в структуре стоимости произведённого киловатта электроэнергии не превышает 2-3 копеек. Все эксплуатационные расходы газопоршневой установки перекрываются её экономичностью в отношении расхода газа ‒ основной затратной статьи автономной электростанции с силовыми агрегатами любого типа.
Высота дымовой трубы для ГПЭ определяется уровнем содержания предельно допустимых концентраций (ПДК) в окружающей среде, а также незначительным объёмом вредных эмиссий самой газопоршневой установки. Средняя высота труб равна 20-30 метрам. Уровень шумов, производимых газопоршневой установкой, составляет 75-78 дБ. При работе поршневой установки возникают незначительные вибрации, что иногда требует установки виброопор.
Можно прийти к выводу, что предприятия, внедряющие ГПЭ, получат выгоду от собственной генерации электроэнергии с помощью газопоршневых установок. В целом, внедрение ГПЭ позволит повысить качество электроэнергии и тепловой энергии на предприятии, а так же позволит снизить расходы на ремонт и обслуживание ТЭЦ на предприятиях.
Приложение 6
2017 г.
Газотурбинные мини-ТЭЦ
В мини-ТЭЦ на основе газовых турбин воздух, сжатый в компрессоре и газ под давлением подаются в камеру сгорания. В камере сгорания осуществляется сжигание газа. В процессе сжигания газа образуются продукты сгорания (уходящие дымовые газы), которые направляются в газовую турбину. Проходя через турбину, уходящие дымовые газы расширяются и, тем самым, передают свою энергию генератору. За счёт расширения продуктов сгорания, генератор газовой турбины вырабатывает электроэнергию, которая затем поступает к потребителям.
После газовой турбины для теплоснабжения потребителей предусматривается установка газо-водяного теплообменника-утилизатора или парового котла-утилизатора (рис. 17). В этих аппаратах используется теплота продуктов сгорания (с температурой 420-500 ºС) для нагрева сетевой воды или для выработки пара.
Рис.17 – Принципиальная схема газотурбинной мини-ТЭЦ:
1 – Воздушный компрессор, 2 – Газовая турбина, 3 – Генератор,
4 – Камера сгорания, 5 – Дожимающий компрессор, 6 – Газо-водяной теплообменник-утилизатор, 7 – Насос, 8 – Дымосос
Примерно 40 % энергии от сгорания газа приходится на выработку электроэнергии, остальные 60 % используются для производства теплоты. Электрический КПД газотурбинных мини-ТЭЦ в среднем равен 25–35%. Общий коэффициент использования теплоты (по сумме электрической + тепловой мощности) у газотурбинных мини-ТЭЦ достигает 75–85%. Спектр выпускаемых газотурбинных мини-ТЭЦ достаточно широк и лежит в диапазоне от 2,5 до 25 МВт по электрической мощности. Тепловая мощность газотурбинных мини-ТЭЦ (при температуре уходящих дымовых газов 100-115 ºС) составляет от 1,5 до 27 Гкал/ч. Как правило, газотурбинные мини-ТЭЦ выпускаются в виде модулей полной заводской готовности для стационарного размещения или в блочно-контейнерном исполнении.
К достоинствам ГТУ-ТЭЦ относятся:
‒ способность работать на различных видах топлива (газообразном и жидком).
‒ длительность периода, на протяжении которого оборудование ГТУ-ТЭЦ может эксплуатироваться без остановки (до 9000 часов).
‒ незначительный расход смазочного масла для оборудования ГТУ-ТЭЦ (до 1,3 тонн в год).
‒ малые выбросы вредных веществ в окружающую среду (NOX = 25–50 ppm; CO = 60–75 ppm).
‒ высокое значение отношения отпускаемой теплоты к производимой электроэнергии.
‒ возможность производства пара в котлах-утилизаторах.
Направления повышения эффективности когенерационной ГТУ:
В соответствии с поставленной задачей повышения эффективности когенерационной ГТУ, которые могут быть как энергетические, так и приводные, необходимо повысить КПД двигателя. Эта задача решается при сохранении начальной температуры газа перед турбиной в двигателе, за счёт применения сложных термодинамических циклов ГТД.
Рис. 18 – Схема когенерационного ГТД
Н – нагрузка, К – компрессор, КС – камера сгорания, Т – турбина,
КУ – котёл-утилизатор
Усложнение ГТД простого цикла возможно произвести нетрадиционным способом посредством применения перерасширения газа на выходе из силовой турбины (рис. 17), что позволит получить за вычетом энергии на дожимание газа дополнительную работу, которая повысит КПД и удельную мощность двигателя. Конструктивно реализуется такой метод посредством присоединения к выхлопу двигателя турбокомпрессорного утилизатора (ТКУ). ТКУ состоит из турбины перерасширения (ТП), дожимающего компрессора (ДК) и охладителя газа между ними. Охладитель газа в ТКУ используется в качестве водогрейного котла-утилизатора.
Рис. 19 – Схема когенерационного ГТД с турбокомпрессорным утилизатором:
Н – нагрузка, К – компрессор, КС – камера сгорания, Т – турбина, ТП – турбина перерасширения, ДК – дожимающий компрессор, КУ – котёл-утилизатор
На втором этапе усложнение когенерационного ГТД простого цикла традиционно проводится путём введения регенерации теплоты выхлопных газов двигателя для подогрева сжатого в компрессоре воздуха перед камерой сгорания (рис. 20). При применении регенерации теплоты растёт КПД двигателя, в конструкции двигателя появляется дополнительный элемент – подогреватель воздуха (регенератор).
Дальнейшее повышение энергоэффективности когенерационного ГТД осуществляется посредством сочетания приведённых выше двух способов повышения экономичности ГТД. Конструктивно эта схема реализуется встраиванием регенератора после турбины перерасширения в ТКУ, так как газ после турбины перерасширения обладает ещё достаточным тепловым потенциалом. Такая схема представлена на рис. 20.
Рис.20 – Схема когенерационного ГТД с регенерацией теплоты:
Н – нагрузка, К – компрессор, КС – камера сгорания, Т – турбина,
Р – регенератор; КУ – котёл-утилизатор
Рис.21 – Схема ГТД с турбокомпрессорным утилизатором:
Н – нагрузка, К – компрессор, КС – камера сгорания, Т – турбина,
ТП – турбина перерасширения, Р – регенератор, КУ – котёл-утилизатор,
ДК – дожимающий компрессор, КП – клапан перепуска воздуха
С целью определения характеристик и основных особенностей цикла ГТД с турбиной перерасширения их можно представить в виде цикла Брайтона, последовательно усложненного применением силовой турбины перерасширения, в которой газ расширяется до давления меньше атмосферного, в охладителе газа охлаждается, и далее дожимающим компрессором выбрасывается в атмосферу (рис. 19). Далее в модель вводится регенерация теплоты, осуществляемая за турбиной перерасширения. При степени повышения давления в ДК πдк=1 модель для сложного цикла становится пригодной для определения характеристик цикла ГТД с регенерацией теплоты, а при πдк=1 и степени регенерации σ = 0 определяются характеристики простого цикла.
На рис. 22 показаны зависимости эффективного КПД (ηе) и удельной мощности (nуд) циклов ГТД с регенерацией теплоты (σ=0,85), с турбиной перерасширения (πдк=2,25) и ГТД с ТП и Р (сложного цикла) от изменения величины степени повышения давления в компрессоре двигателя πк. На рис. 5 для сравнения приведены параметры ГТД простого цикла (кривая П). Обозначения для ГТД с регенерацией теплоты принято (Р), для ГТД с турбиной перерасширения (ТП).
Рис. 22 – Зависимости эффективного КПД (сплошные линии), и удельной мощности nуд (прерывистые линии) при Т3 = 1373 К, φ=0,85 и ηдк = 2,25
На представленных зависимостях на рис. 22 видно, что увеличение КПД (ηе) для цикла ГТД с регенерацией теплоты по сравнению с циклом Брайтона относительно составляет 10-12 %. Удельная мощность (nуд) во всем диапазоне изменения πк несколько меньше, чем в простом цикле.
Температура газа перед дожимающим компрессором была принята равной 323 К, при этом увеличение эффективного КПД и удельной мощности для цикла ГТД с турбиной перерасширения относительно составило 10-15 % по отношению к ГТД простого цикла.
Необходимо отметить, что оптимальные по КПД πк для цикла ГТД с ТП и простого цикла практически совпадают, что обеспечивает совместную работу ГТД простого цикла и турбокомпрессорного утилизатора.
Сочетание двух способов повышения экономичности ГТД применено в цикле ГТД с турбиной перерасширения и регенерацией теплоты (ГТД с ТП и Р, рис. 21). Установлено (см. рис. 22), что увеличение эффективного КПД для цикла ГТД с ТП и Р относительно составляет 20-25 % по сравнению с простым циклом. Оптимальные по КПД πк в цикле ГТД с ТП и Р даже несколько меньше, чем в цикле ГТД и Р и составляет значения от 4 до 6. Наибольшие значения удельной мощности в циклах ГТД с ТП и Р смещены в сторону меньших πк и значительно превышают значения для ГТД и Р.
Таким образом, анализ характеристик ГТД показывает, что ГТД с ТП и Р может быть создан на базе унифицированного газогенератора ГТД с Р.
Для когенерационных ГТУ, обеспечивающих энергией автономные коммунальные и промышленные объекты, характерна работа на частичных нагрузках, причём не только в пределах сезона, но и в течение суток. Обычно при изменении электрической нагрузки, тепловая мощность часто должна быть более стабильной. Поэтому выбор оптимальной тепловой и конструктивной схемы установки для реализации гибких когенерационных технологий являются важным эксплуатационным фактором.
Вал газогенератора с блокированной силовой турбиной воспринимает генераторную нагрузку, при которой обороты турбины на всех режимах нагружения поддерживаются постоянными.
В схеме ГТД с турбиной перерасширения ТКУ присоединяем к выхлопу ГТД, то есть механически не связан с силовой турбиной. Степень повышения давления в дожимающем компрессоре ηдк определяется из баланса мощностей между ТП и ДК.
На рис. 23 показаны зависимости характеристик ГТД с блокированной силовой турбиной (СТ) и ТКУ (схема 1Б+ТП) от относительной эффективной мощности 𝑁 ̄𝑒.
Рис. 23 – Характеристики циклов ГТД с ТКУ (схемы 1Б+ТП и 1СН+ТП) на частичных генераторных нагрузках при Т3 = 1373 К, ηк = 18; ηдк = 2,25
Рис. 24 – Теплотехнические характеристики ГТД с ТКУ (схема 1Б+ТП и 1СН+ТП) на частичных генераторных нагрузках при Т3 = 1373 К, ηк = 18; ηдк = 2,25
При всех значениях относительной мощности 𝑁 ̄𝑒 эффективный КПД ηе в схеме ГТД с ТКУ (схема 1Б+ТП) выше, чем в ГТД простого цикла (1Б).
Когенерационная установка должна обладать высокой общей энергоэффективностью на всех эксплуатационных режимах. Для оценки теплотехнических характеристик газотурбинных установок, имеющих в своём составе устройство для внешней поставки теплоты, применим удельный показатель: теплотехнический (общий) КПД ηтт.
Результаты расчетов теплотехнических характеристик ГТД с ТКУ на частичных генераторных нагрузках показывают, что каждая схема имеет свои закономерности изменения теплотехнических характеристик. Если в ГТД с блокированной СТ относительная теплотехническая мощность 𝑁 ̄ТТ изменяется пропорционально 𝑁 ̄𝑒, то в ГТД со свободной СТ и ТКУ на эксплуатационных режимах при 𝑁𝑒 =0 ,6-1,0 остаётся практически стабильной. Указанное свойство предпочтительно для когенерационных
ГТУ обеспечивающих энергией предприятия городского хозяйства, особенно в зимний период.
Отдельно стоит вопрос определения характеристик когенерационных ГТД с регенерацией теплоты на переменных режимах. Для обеспечения энергией локальных объектов (здания, сооружения) применяются микрогазотурбинные установки, которые, как правило, в рабочем цикле содержат регенерацию теплоты.
На рис. 25 и 26 показаны зависимости характеристик ГТД сложных циклов с регенерацией теплоты от изменения относительной эффективной мощности 𝑁 ̄𝑒. Для сравнения определялись характеристики на частичных нагрузках одновального ГТД (схема 1Б). На рис. 25 и 26 представлены характеристики ГТД с Р (схема 1Б/Р), а также ГТД с ТП и Р (схема 1Б/Р+ТП). Во всех схемах вал генератора сблокирован с силовой турбиной.
Рис. 25 – Характеристики циклов ГТД с регенерацией
теплоты на частичных (генераторных) нагрузках
Рис. 26 – Теплотехнические характеристики ГТД с регенерацией теплоты на частичных (генераторных) нагрузках
Анализ характеристик ГТД установил, что КПД (ηе) ГТД с ТП и Р и ГТД с Р выше, чем в ГТД простого цикла как на номинальной нагрузке, так и частичном нагружении при всех значениях относительной мощности 𝑁 ̄𝑒. Преимущество ГТД с ТП и Р особенно ощутимо при уменьшении нагружения двигателя.
Когенерационная установка должна обладать высокой общей энергоэффективностью на всех эксплуатационных режимах. Для оценки теплотехнических характеристик газотурбинных установок, имеющих в своем составе устройство для внешней поставки теплоты, применим удельный показатель: теплотехнический (общий) КПД ηтт.
В целом теплотехнический КПД показывает степень использования располагаемой теплоты сгорания топлива на выработку механической и тепловой энергии.
На рис. 26 представлены теплотехнические характеристики когенерационных ГТД при генераторном нагружении на частичных режимах работы. Теплотехнический КПД ГТД с ТП и Р на частичных нагрузках более высокий, чем в ГТД с Р. Это объясняется тем, что в ТКУ относительная тепловая мощность 𝑁 ̄Т на частичных нагрузках более высокая, чем в утилизационных котлах ГТД с Р и ГТД простого цикла.
Увеличить тепловую мощность когенерационного ГТД с ТП и Р на частичных нагрузках можно посредством перепуска циклового воздуха мимо регенератора. Такой способ позволяет перераспределить тепловой поток за турбиной перерасширения между регенератором и охладителем газа – утилизационным котлом.
На рис. 26 пунктирной линией показаны значения относительной тепловой мощности 𝑁_ТТ при равномерном увеличении перепуска воздуха мимо регенератора в ГТД с ТП и Р и ГТД с Р. Хотя эффективный КПД при этом несколько падает, но на режиме от 𝑁 ̄𝑒=1 до 𝑁 ̄𝑒=0,6 в ГТД с ТП и Р тепловая мощность практически постоянная.
Увеличив долю перепуска воздуха, можно поддержать постоянство 𝑁 ̄ТТ на режимах меньшей нагрузки:
‒ Когенерационные ГТД сложного цикла более экономичны по сравнению с когенерационным ГТД простого цикла как на номинальных, так и на частичных нагрузках.
‒ Тепловые и конструктивные схемы ГТД с турбиной перерасширения и регенератором приспособлены к изменению рабочего процесса в двигателе и позволяют реализовать гибкие когенерационные технологии, то есть создать когенерационные установки с управляемыми потоками энергии.
‒ ГТД с турбокомпрессорным утилизатором могут быть созданы на базе газогенераторов ГТД простого цикла, выпускаемых в настоящее время промышленностью.
Приложение 7
2020 г.
2020 г.
Дизельные мини-ТЭЦ
Наряду с централизованным способом электроснабжения потребителей от сетей энергосистем в ряде случаев необходимо предусматривать местные источники электроснабжения. К ним относятся дизельные электростанции, которые широко используются также в качестве резервных установок, обеспечивающих электрической энергией потребителей при отключении питания в случае аварий на линиях энергосистемы. Для потребителей с повышенными требованиями к бесперебойности электроснабжения установка резервных источников электроснабжения обязательна.
Сегодня в малой электроэнергетике преобладающими являются дизельные электростанции (ДЭС). Широкое применение ДЭС определяется рядом их важных их преимуществ перед другими типами электростанций:
‒ высокий КПД (до 0,35-0,4) и, следовательно, малый удельный расход топлива (240-260 г/кВт · ч);
‒ быстрота пуска (единицы-десятки секунд), полная автоматизация всех технологических процессов, возможность длительной работы без технического обслуживания (до 250 часов и более);
‒ малый удельный расход воды (или воздуха) для охлаждения двигателей;
‒ компактность, простота вспомогательных систем и технологического процесса, позволяющие обходиться минимальным количеством обслуживающего персонала;
‒ малая потребность в строительных объёмах (1,5-2 м3/кВт), быстрота строительства зданий станции и монтажа оборудования (степень заводской готовности 0,8-0,85);
‒ возможность блочно-модульного исполнения электростанций, сводящая к минимуму строительные работы на месте применения.
Главными недостатками ДЭС являются высокая стоимость топлива и ограниченный по сравнению с электростанциями централизованных систем срок службы (ресурс).
По назначению дизельные электростанции и электроагрегаты подразделяют на стационарные и передвижные, а по исполнению-- сооружаемые во временных и постоянных помещениях. В зависимости от объёмов автоматизации станции и электроагрегаты могут быть 1,2 и 3-й степени автоматизации. Они могут быть выполнены с воздушной, водовоздушной или радиаторной, а также водоводяной -- двухконтурной системами охлаждения.
На дизельных электростанциях применяют генераторы типов СГД (синхронный генератор, дизельный), ЕСС (единой серии с самовозбуждением), ЕС (единой серии), МСД открытого и МСА защищённого исполнения с самовентилированием и другие.
Передвижные дизельные электростанции выполнены как комплектные электроустановки, смонтированные на каком-либо транспортном средстве и защищённые от атмосферных воздействий. Дизельные электроагрегаты также выполняют как комплектные установки в виде отдельных блоков, чаще всего смонтированными на общей раме.
Стационарные дизельные электроустановки предназначены для нормальной работы и выработки электроэнергии необходимого качества при температуре окружающего воздуха от 8 до 40 °С, высоте над уровнем моря не выше 1000 м и относительной влажности воздуха до 98 % при 25 °С.
Основным элементом дизельной-электроустановки (станции или агрегата) является дизель-генератор, состоящий из дизельного двигателя, электрического генератора, трёхфазного переменного тока, систем охлаждения, смазочной, топливоподачи и пультов управления.
Для обеспечения протекания рабочего процесса, эффективного и безаварийного функционирования дизельного двигателя, предназначены системы ДЭУ (главная энергетическая установка). К системам, обслуживающим работу дизеля, относятся:
‒ топливная система;
‒ система смазки;
‒ система охлаждения;
‒ система воздухоснабжения;
‒ система газоотвода;
‒ система управления;
‒ система регулирования и контроля.
Топливная система обеспечивает подачу топлива в рабочие цилиндры. Она состоит из топливных систем низкого и высокого давления.
Топливная система низкого давления предназначена для предварительной подготовки топлива и подачи его к топливной системе высокого давления. Предварительная подготовка включает в себя подогрев топлива до необходимой температуры (снижение его вязкости), фильтрацию, ввод присадок и прочие необходимые операции. Топливная система низкого давления включает в себя следующие основные элементы: запасные и расходные топливные цистерны, фильтры, насосы, сепараторы, подогреватели топлива и топливопроводы низкого давления.
Топливная система высокого давления осуществляет точную дозировку топлива в зависимости от режима работы дизеля, распределение топлива по цилиндрам и впрыскивание топлива в камеру сгорания двигателя с необходимым давлением. Топливная система высокого давления включает в себя: топливный насос высокого давления – ТНВД, форсунки и топливопроводы высокого давления. Топливные системы высокого давления могут исполняться разделённого и неразделённого типов. В разделённых системах ТНВД и форсунка соединены между собой топливопроводом высокого давления, в неразделённых – объединены в общем корпусе и образуют систему насос–форсунка.
ТНВД в МОД (малооборотный двигатель) и СОД (среднеоборотный двигатель) обычно выполняются автономными для каждого цилиндра. Для ВОД (высокооборотный двигатель) как правило используются блочные насосы, в которых плунжерные пары, состоящие из плунжера и втулки, размещаются в общем корпусе (рядном или V-образном). Привод ТНВД судовых дизелей обычно выполняется механическим от кулачкового распределительного вала.
Форсунки предназначены для впрыскивания порции топлива в камеру сгорания двигателя в мелко распылённом виде. Обычно в дизельных двигателях применяются форсунки различных типов: открытые, нормальные закрытые, клапанно-сопловые и штифтовые. Тип используемой в дизеле форсунки определяют: способ подачи топлива в цилиндр и необходимая при сгорании форма факела.
Насос-форсунки применяют для получения высокого давления впрыска, превышающего 100 МПа. Насос-форсунка объединяет в одном агрегате насосную секцию и распылитель форсунки. Это позволяет избежать применения толстостенных топливопроводов высокого давления. Насос-форсунки устанавливаются, как правило, непосредственно на крышке цилиндра и имеют индивидуальный рычажный или штанговый привод.
Основными функциями топливоподающей аппаратуры являются:
‒ точная дозировка подачи топлива на цикл;
‒ обеспечение требуемого давления впрыска топлива на определённом участке рабочего цикла в течение короткого промежутка времени;
‒ возможность изменения моментов опережения впрыска топлива;
‒ равномерное распределение топлива по отдельным цилиндрам;
‒ обеспечение оптимального характера протекания процесса впрыска;
‒ обеспечение надёжной работы аппаратуры на всех заданных режимах.
Схема типичной топливной системы дизельной энергетической установки, работающей на тяжёлом топливе, изображена на рис. 27.
Изображённая на рисунке система приспособлена для работы на мало- и высоковязком топливе, а также их смеси в различных пропорциях. Перед запуском главного двигателя ГД система должна быть заполнена лёгким топливом, не требующим подогрева. Топливо из расходной цистерны лёгкого топлива РТЦ ЛТ через расходомер Р подаётся в смесительную цистерну. Маловязкое топливо из смесительной цистерны поступает к топливоподкачивающим насосам ТПН и через фильтр тонкой очистки Ф1 к насосу высокого давления ТНВД и форсункам ГД, минуя ветвь подогревателя ТП. На установившемся режиме работы ГД его можно переводить на высоковязкое топливо. Для этого предварительно подогретое топливо из цистерны тяжёлого топлива РТЦ ТТ через расходомер Р начинают подавать в смесительную цистерну, а подачу маловязкого топлива из цистерны лёгкого топлива прекращают.
По мере увеличения содержания высоковязкого топлива в смесительной цистерне вязкость смеси растёт, и смесь подаётся к двигателю через ветвь подогрева с регулятором вязкости РВ, воздействующим на расход греющей среды через подогреватель топлива. Двигатель переходит на высоковязкое топливо. Отсечное топливо от насосов высокого давления и форсунок возвращается в смесительную цистерну по трубопроводу. Через отдельный трубопровод производится подача маловязкого топлива к дизель-генераторной установке – ДГУ. Возможна подача на ДГУ подогретого тяжёлого топлива через фильтр Ф2. В качестве греющей среды в подогревателе топлива могут использоваться: пар от вспомогательной котельной установки, вода системы охлаждения двигателя.
Рис. 27 – Схема топливной системы ДЭУ, работающей на тяжёлом топливе
Система смазки обеспечивает подачу масла к трущимся поверхностям дизельного двигателя с целью уменьшения сил трения, отвода теплоты, выделяющейся при трении, очистки поверхностей трения от продуктов износа, нагара и других посторонних частиц.
Системы смазки, применяемые в судовых ДЭУ, можно классифицировать по следующим признакам:
‒ по способу обеспечения напора: на гравитационные, принудительные и комбинированные. В гравитационных системах необходимое давление масла обеспечивается за счёт напора столба жидкости при размещении расходной масляной цистерны над двигателем. В принудительных системах необходимое давление смазки создаётся масляным насосом.
‒ по движению масла: на циркуляционные (замкнутые) и линейные (лубрикаторные). В циркуляционной системе масло проходит через смазываемый узел и многократно совершает замкнутый цикл; В линейной системе масло подводится к поверхности смазки один раз и обратно в систему не возвращается (сгорает в цилиндрах двигателя вместе с топливом).
‒ по количеству марок масла: на одномасляные и многомасляные. В одномасляных системах на все смазываемые узлы подаётся масло одной марки. В многомасляных системах для части смазываемых узлов подаётся масло своей марки. В мощных судовых дизелях, как правило, применяются три независимые системы смазки: 1) – для смазки подшипников коленчатого вала, шатуна, крейцкопфа, механизма привода газораспределения и топливных насосов; 2) – для смазки зеркала цилиндров и поршней; 3) – для смазки подшипников турбокомпрессора;
‒ по способу смазки поверхности цилиндра: на системы с принудительной подачей масла и с подачей масла разбрызгиванием. В системах с принудительной подачей смазка небольшими порциями подаётся на внутреннюю поверхность втулки цилиндра через отверстия от специального насоса – лубрикатора. В системах с разбрызгиванием смазка зеркала цилиндра осуществляется каплями, разбрызгиваемыми кривошипами в объёме картера.
‒ по размещению масла в системе: на системы с сухим картером, с мокрым картером и комбинированные. В системах с сухим картером масло из поддона через специальное отверстие стекает в цистерну и не скапливается в картере двигателя; в системах с мокрым картером картер служит в качестве ёмкости для масла; в комбинированных системах часть масла находится в картере, часть сливается в расходную цистерну.
В состав масляной системы обычно входят: запасные и расходные масляные цистерны, масляные фильтры, маслоохладители и маслоподогреватели, масляные насосы, регуляторы температуры масла, арматура, трубопроводы, КИП (контрольно-измерительные приборы).
На рис. 28 изображены типичные схемы систем смазки МОД.
Рис. 28 – Схемы циркуляционной (а) и лубрикаторной (б)
систем смазки МОД
В циркуляционной системе смазки (рис. 28а) циркуляция масла осуществляется масляными насосами МН, которые обеспечивают прокачку масла через фильтры МФ и маслоохладитель МО к узлам трения главного двигателя. Один из масляных насосов находится постоянно в работе, второй является резервным. Для поддержания необходимой температуры масла параллельно маслоохладителю включена обводная линия с терморегулирующим клапаном ТРК. После смазки узлов двигателя масло стекает в картер, откуда через фильтр забирается масляными насосами и подаётся снова в систему.
В лубрикаторной системе (рис. 28.б) цилиндровое масло из расходной масляной цистерны РМЦ самотеком поступает к блоку насосов-лубрикаторов Л и затем под давлением – в цилиндры двигателя. В цилиндрах двигателя масло, осуществив смазку, полностью сгорает и обратно в систему не возвращается.
Заполнение расходной масляной цистерны РМЦ из запасной ЗМЦ производится через фильтр с помощью маслоперекачивающего насоса 1 с электроприводом или ручного масляного насоса 2.
Система охлаждения предназначена для охлаждения деталей, нагревающихся от трения и теплоты сгорания топлива, и для отвода теплоты от рабочих жидкостей (масла, топлива, воды) и наддувочного воздуха.
Системы охлаждения, применяемые в судовых ДЭУ, можно классифицировать по следующим признакам:
‒ по числу водяных контуров: на одноконтурные (проточные) – в которых для охлаждения используется забортная вода; и двухконтурные (замкнутые) – в которых имеется два контура охлаждения: внутренний (пресная вода), охлаждающий полости ГД, и внешний (забортная вода), охлаждающий через теплообменник воду внутреннего контура. Масло, топливо и наддувочный воздух охлаждаются обычно забортной водой.
‒ по температурному уровню: на низкотемпературные – температура охлаждающей воды до 50 °С (как правило, одноконтурные системы); умеренные – температура охлаждающей воды в пределах 70 ÷ 90 °С (как правило, двухконтурные); высокотемпературные с повышенным давлением (температура охлаждающей воды > 100 °С) и испарительные с частичным испарением (температура охлаждающей воды ~ 100 °С при нормальном давлении);
‒ по направлению движения охлаждающей воды в двигателе: на системы с естественным направлением движения потока – охлаждающая вода подводится в нижнюю часть полости охлаждения, поднимается вверх по мере повышения температуры и отводится из верхней части; термосифонные – вода подводится в верхней части полости охлаждения, а отводится из нижней.
В состав системы охлаждения обычно входит следующее оборудование:
‒ водяные насосы, обеспечивающие циркуляцию охлаждающей воды в системе; В двухконтурных системах применяются насосы забортной воды и насосы пресной воды;
‒ теплообменники, обеспечивающие отвод в охлаждающую воду избыточной теплоты от жидкостей (топлива, масла, воды внутреннего контура) и наддувочного воздуха;
‒ расширительная цистерна, предназначенная для компенсации расширения воды вследствие изменения её температуры, восполнения потерь воды вследствие утечек и испарения, удаления из системы воздуха и водяных паров;
‒ терморегуляторы, обеспечивающие автоматическое поддержание температуры воды и охлаждаемых жидкостей в заданных пределах;
‒ трубопроводы, КИП и арматура.
Для улучшения охлаждения поршней мощных крейцкопфных двухтактных дизелей иногда применяется отдельная система охлаждения со своим насосом. В качестве рабочей жидкости в такой системе используется дистиллированная вода.
Принципиальная схема двухконтурной системы охлаждения ДЭУ изображена на рис. 29.
Рис. 29 – Принципиальная схема двухконтурной системы охлаждения
Главный двигатель и ДГУ охлаждаются пресной водой, подаваемой в магистраль насосом пресной воды НПВ. Через охладитель ОПВ пресная вода поступает на охлаждение ГД, а затем через деаэратор ДР и водоопреснительную установку ВОУ подаётся к приёмному патрубку НПВ. По второй ветви пресная вода через охладитель пресной воды ДГУ – ОПВ ДГУ поступает на охлаждение дизельгенератора. Циркуляция пресной воды осуществляется по замкнутому контуру насосом пресной воды.
В систему включён расширительный бак, который служит для пополнения утечек и компенсации тепловых расширений пресной воды. В него же отводится паровоздушная смесь из полостей охлаждения двигателей и теплообменных аппаратов.
Система забортной воды состоит из отдельных функциональных участков, соединённых между собой с целью резервирования механизмов. Из кингстонных ящиков КЯ забортная вода через фильтры ФЗВ поступает в распределительный канал. Главный циркуляционный насос забортной воды НЗВ подаёт забортную воду в общесудовую магистраль, откуда она идёт на охлаждение теплообменников и затем сливается за борт через отливные кингстоны ОК. На ГД забортной водой прокачиваются следующие теплообменники: охладитель наддувочного воздуха ОНВ, маслоохладитель МО, охладитель пресной воды ОПВ, охладитель масла газотурбонагнетателя охл. ГТН и охладитель топлива охл. ТЛ. Также забортная вода подаётся на охладители масла и воздуха ДГУ(на схеме не показаны). Насос РН является резервным на случай выхода из строя насосов пресной или забортной воды.
Для подачи забортной воды в систему обычно используются насосы центробежного типа. На крупных судовых двигателях водяные насосы имеют автономный привод. На дизелях малой мощности насосы пресной, и часто забортной воды, приводятся в действие от коленчатого вала двигателя.
Система воздухоснабжения предназначена для подачи воздуха, необходимого для сгорания топлива и продувки цилиндра, в определенном количестве и с заданными параметрами.
Системы воздухоснабжения дизельных двигателей можно классифицировать по следующим признакам:
‒ по числу ступеней сжатия воздуха: на одноступенчатые, в которых воздух сжимается однократно в одноступенчатом компрессоре; многоступенчатые, в которых воздух сжимается несколько раз, переходя из одной ступени сжатия в другую (обычно используется 2 ступени сжатия); без предварительного сжатия;
‒ по числу компрессоров: на бескомпрессорные; однокомпрессорные, в которых воздух подаётся во все цилиндры от одного компрессора; и многокомпрессорные;
‒ по способу поддержания параметров воздуха, поступающего в цилиндр: на нерегулируемые, в которых параметры наддувочного воздуха изменяются самопроизвольно с изменением внешних условий или режима работы двигателя); и регулируемые, в которых с помощью специальных устройств поддерживается постоянное значение какого либо параметра воздуха (температура, давление, расход) или их изменение по заданному закону в зависимости от нагрузки ГД.
Основными элементами системы воздухоснабжения дизеля являются:
‒ компрессоры, служащие для повышения плотности воздуха и перемещения сжатого воздуха;
‒ теплообменники, предназначенные для повышения плотности воздуха за счёт снижения его температуры;
‒ воздуховоды, ресиверы, служащие для равномерного распределения воздуха по цилиндрам дизеля;
‒ глушители шума – для снижения уровня шума системы воздухоснабжения.
Рис. 30 – Системы воздухоснабжения дизелей:
а – двухступенчатая нерегулируемая; б – с регулированием параметров
В нерегулируемой системе воздухоснабжения (рис. 30.а) компрессор первой ступени К1 забирает воздух из атмосферы, сжимает его и подаёт по воздуховоду в промежуточный охладитель ПОВ. Уплотнённый воздух поступает в компрессор второй ступени сжатия К2, откуда направляется через концевой охладитель воздуха ВО в наддувочный ресивер Р, и далее в цилиндры дизельного двигателя.
В двухтактных дизелях часто предусматривают дополнительный компрессор ДК, который подаёт воздух через невозвратный клапан в ресивер двигателя в аварийных случаях, в период пуска двигателя и при работе на малых нагрузках, когда производительности основных компрессоров не хватает для подачи потребного количества воздуха в цилиндры.
В системе воздухоснабжения с регулируемыми параметрами воздуха (рис. 30.б) основной компрессор ОК, работающий в режиме, зависящем от режима работы двигателя, подаёт воздух во вспомогательный компрессор ВК, который, благодаря автоматически регулируемому приводу, обеспечивает оптимальное значение давления воздуха. Сжатый воздух через распределитель РУ поступает в охладитель ВО, охлаждаемый забортной водой, и нагреватель НВ, в который подаётся горячая вода из контура охлаждения двигателя. В зависимости от внешних условий, распределитель регулирует смесеобразование холодного и горячего воздуха, чем оптимизирует его температуру перед поступлением в цилиндр.
В системах воздухоснабжения используются центробежные, поршневые и роторно-лопастные компрессоры. Их компоновка и способы привода весьма разнообразны. Центробежные компрессоры чаще всего используются в агрегатах газотурбинного наддува. Поршневые и роторно-лопастные используются в качестве продувочных компрессоров в системах двухтактных дизелей и приводятся в действие от коленчатого вала двигателя.
Система газоотвода предназначена для обеспечения наиболее рационального отвода отработавших газов из цилиндров двигателя.
Под рациональным отводом понимается такая организация газовыпуска, которая способствует максимальному использованию энергии рабочего тела как в цилиндре двигателя, так и вне его, а также качественной очистке и наполнению цилиндров.
Системы газоотводов дизельных двигателей можно классифицировать по следующим признакам:
‒ по глубине утилизации теплоты: без утилизации, в этих системах отработавшие газы выбрасываются в атмосферу; с умеренной утилизацией, в которых энергия газов используется в газовой турбине для осуществления турбонаддува дизеля; с глубокой утилизацией – как механическая так и тепловая энергия газов используется в специальных устройствах-утилизаторах, как правило, утилизационных паровых котлах.
‒ по особенностям движения газа в коллекторах: на изобарные, в которых давление газов в коллекторе постоянно; импульсные, в которых давление газов в коллекторе переменно и зависит от числа цилиндров двигателя; комбинированные, имеющие переменное давление газов в коллекторе, но выравнивающееся перед поступлением в газовую турбину.
В общем случае, в систему газоотвода может входить следующее оборудование:
‒ выпускные коллекторы, предназначенные для отвода газов из цилиндров двигателя с максимально возможным сохранением их энергии;
‒ глушители шума, снижающие акустическое поле при работе двигателя;
‒ утилизационные газовые турбины и паровые котлы, преобразующие кинетическую и тепловую энергию газов в механическую работу или тепловую энергию рабочего тела для частичного возврата её в цикл дизельной установки;
‒ трубопроводы (газоходы).
Типичная схема системы газоотвода ДЭУ с глубокой степенью утилизации теплоты в импульсной газовой турбине и утилизационном паровом котле изображена на рис. 31.
Рис. 31 – Схема системы газоотвода дизеля с глубокой степенью
В системах с глубокой утилизацией теплоты отработавшие в цилиндрах газы поступают в коллектор малого объёма, затем в утилизационную газовую турбину УГТ, преобразующую кинетическую, потенциальную и тепловую энергию газов в механическую работу сжатия воздуха в компрессоре К. Из УГТ газы поступают в утилизационный паровой котёл УПК, где тепловая энергия отработавших газов передаётся питательной воде ПВ. Из УПК охлаждённые продукты сгорания попадают в глушитель шума ГШ и выбрасываются в атмосферу.
Утилизационные газовые турбины могут быть: наддувочными, в которых механическая энергия, полученная при расширении газов, передаётся компрессору наддувочного воздуха; и силовыми, передающими механическую энергию через передачу на общую линию вала или генератор.
Утилизационные паровые котлы могут вырабатывать водяной пар для использования его на судне в различных целях, либо служат для получения горячей воды или паров других жидкостей.
Система управления предназначена для пуска и остановки дизельного двигателя, изменения направления и частоты вращения коленчатого вала.
Для запуска двигателя необходимо создать условия, обеспечивающие самовоспламенение топлива в цилиндрах. Это достигается раскруткой коленчатого вала двигателя и созданием в цилиндрах давления и температуры воздуха, при которых происходит воспламенение топлива.
Раскрутку коленчатого вала дизельного двигателя можно осуществить следующими способами:
‒ приложением крутящего момента к КШМ извне (вручную, гидро-, пневмо- или электродвигателем (стартером) или за счёт использования штатного электрогенератора, работающего в режиме пускового электродвигателя (для дизельгенераторов);
‒ созданием в цилиндре усилия, которое приведёт в движение КШМ (подача в цилиндры дизеля пускового воздуха).
Устройства воздушного пуска часто используются для торможения КШМ с целью ускорения остановки двигателя при реверсировании путём подачи в цилиндры контрвоздуха.
Системы управления дизельных установок можно классифицировать по следующим признакам:
‒ по схеме воздушного пуска: на полнопроточные (с автоматическими пусковыми клапанами). В таких системах управления весь пусковой воздух, направляемый к пусковым клапанам, проходит через воздухораспределитель; и частично проточные (с пневматически управляемыми пусковыми клапанами). В этих системах через воздухораспределитель проходит только та часть воздуха, которая управляет открытием и закрытием пускового воздуха;
‒ по способу реверсирования двигателя: с заменой кулачковых шайб переднего хода на кулачковые шайбы заднего хода путём перемещения кулачкового вала; и с изменением угла заклинки шайб за счёт проворачивания кулачкового вала относительно коленчатого вала;
‒ по типу: на механические, гидравлические, пневматические, электрические, электронные и смешанные.
Система управления дизельной установкой состоит из следующего оборудования:
‒ постов управления, предназначенных для ввода команд на выполнение какой либо операции;
‒ пусковых устройств, предназначенных для первоначальной раскрутки КШМ с целью приведения двигателя в действие;
‒ механизма реверсирования, предназначенного для изменения вращения вала двигателя в противоположную сторону, обеспечения правильного чередования и изменения фаз распределения органов пуска, газораспределения, топливоподачи, а также реверсирования навешенных на двигатель механизмов;
‒ блокирующих устройств, предотвращающих пуск двигателя при включенном валоповоротном устройстве, отсутствии давления масла в системе смазки, закрытых захлопках газоходов и других нештатных ситуациях.
В основе системы управления лежит система пускового воздуха, состоящая, как правило, из следующего оборудования: пусковых баллонов, редукционного клапана, пневмостартера, пневмомотора агрегата прокачки топливом и маслом, блока электропневмоклапанов, предохранительного клапана. Схема системы пускового воздуха дизельного судна изображена на рис. 32
Рис. 32 – Система сжатого воздуха
Системы сжатого и пускового воздуха на дизельных судах аналогичны. Баллоны пускового воздуха главного двигателя БПВ ГД и дизельгенераторов БПВ ДГ заполняются с помощью главных компрессоров ГК1 и ГК2 через водомаслоотделитель ВМО. Из баллонов часть воздуха через редуктор ВР направляется на хозяйственные нужды. По мере расходования воздуха и снижения давления в баллонах пополнение осуществляется автоматически с помощью подкачивающего компрессора небольшой производительности ПК. При больших расходах пускового воздуха, что наблюдается при маневрировании главного двигателя, автоматически включается в работу один из главных компрессоров. Начальное или аварийное заполнение баллонов (при отсутствии электропитания) осуществляется автономным дизель-компрессором ДК с ручным пуском.
Система регулирования и контроля обеспечивает поддержание заданного режима работы двигателя и значений его отдельных параметров в допустимых пределах, а также контроль показателей, характеризующих режим и состояние работающего двигателя.
Системы регулирования и контроля, в зависимости от объёма автоматически выполняемых операций, должны обеспечивать:
Первая степень автоматизации – А1:
‒ автоматическое регулирование частоты вращения вала дизеля, напряжения и температуры в системах охлаждения и (или) смазки;
‒ местное и (или) дистанционное управление пуском, остановом, предпусковыми и послеостановочными операциями, а также частотой вращения (нагруженном) реверсированием;
‒ автоматическую подзарядку АБ, обеспечивающих пуск и (или) питание средств автоматизации (при электростартерном пуске);
‒ автоматическую аварийно-предупредительную сигнализацию и защиту;
‒ индикацию значений контролируемых параметров на местном (дизельном) щитке и (или) дистанционном пульте.
Вторая степень автоматизации – А2 (дополнительно к А1):
‒ дистанционное автоматизированное и (или) автоматическое управление пуском, остановом, предпусковыми и послеостановочными операциями, частотой вращения (нагруженном) и реверсированием при его наличии;
‒ автоматический приём нагрузки при автономной работе или выдача сигнала о готовности к приёму нагрузки;
‒ автоматизацию совместной работы двигателей, в том числе автоматический приём нагрузки в ходе синхронизации при параллельной работе ДГ между собой или с внешней сетью;
‒ автоматическое поддержание двигателя в готовности к быстрому приёму нагрузки;
‒ автоматическое регулирование вязкости тяжёлого топлива и автоматизированное управление переходом с одного вида топлива на другой;
‒ автоматизированный экстренный пуск и (или) останов;
‒ исполнительную сигнализацию.
Третья степень автоматизации – А3 (дополнительно к А1 и А2):
‒ автоматическое пополнение расходных ёмкостей: топлива, масла, охлаждающей жидкости и сжатого воздуха;
‒ автоматизированное и (или) автоматическое управление вспомогательными агрегатами и (или) отдельными операциями обслуживания двигателя.
Четвертая степень автоматизации – А4 (дополнительно к А1, А2, А3):
‒ централизованное управление двигателем с помощью управляющих машин;
‒ централизованный автоматический контроль;
‒ автоматизированное и (или) автоматическое техническое диагностирование состояния двигателя в целом или его отдельных частей.
В зависимости от степени автоматизации ДЭУ время необслуживаемой работы установки составляет:
А1 – 4 часа (8, 12 часов);
А3 – 150 часов (250 часов);
А2 – 24 часа; (36, 50 часов);
А4 – 250 часов (375 часов).
(в скобках указано время для ДЭУ с Ne >100 кВт )
Во время работы двигателя его мощность или крутящий момент при заданных частотах вращения должны быть равны мощности или крутящему моменту потребителя. В случае несоответствия между развиваемой двигателем мощностью и нагрузкой число оборотов двигателя может чрезмерно увеличиться (двигатель пойдёт вразнос) или уменьшиться (двигатель остановится).
Возможны следующие способы регулирования мощности и частоты вращения двигателей внутреннего сгорания:
1. Количественное регулирование – изменение количества свежего заряда, поступающего в цилиндр двигателя. В этом случае для понижения мощности двигателя уменьшают количество свежего заряда, не изменяя состава горючей смеси. Такое регулирование можно осуществить установкой дополнительного сопротивления в виде дроссельной заслонки во впускном трубопроводе. Чем больше прикрывает заслонка проходное сечение впускного трубопровода, тем больше сопротивление впуска и меньше наполнение цилиндра, а следовательно, и развиваемая двигателем мощность.
Количественное регулирование применяется в двигателях с внешним смесеобразованием и принудительным воспламенением смеси (карбюраторных и газовых двигателях).
2. Качественное регулирование – изменение количества топлива, впрыскиваемого через форсунку в цилиндр двигателя, при постоянном расходе поступающего в цилиндр воздуха. Такой способ регулирования приводит к изменению качества горючей смеси (изменение коэффициента избытка воздуха).
Этот способ регулирования применяется во всех дизельных двигателях.
3. Смешанное регулирование – используется в газовых двигателях и сочетает в себе качественный и количественный способы регулирования. При смешанном регулировании изменение мощности в области больших нагрузок производится путём изменения состава смеси в пределах допустимых значений коэффициента избытка воздуха, а в области малых нагрузок – путём изменения количества смеси, поступающей в цилиндры.
Регулирование температур и расходов охлаждающей воды, смазочного масла, воздуха, уровней в цистернах, температуры топлива и др. параметров работы двигателя осуществляется локальными регуляторами. Обычно в качестве регуляторов используются механические, гидравлические и пневматические устройства. Но в последнее время вместо этих типов регуляторов все чаще применяют электронные датчики и микропроцессорные блоки управления, что позволяет значительно снизить габариты систем регулирования и обеспечивает выполнение вычислений для оптимизации процессов регулирования работы дизелей.
Приложение 8
Судовые энергетические установки. Дизельные и газотурбинные установки. Болдырев О.Н. [2003]
Дата добавления: 2021-04-24; просмотров: 447; Мы поможем в написании вашей работы! |
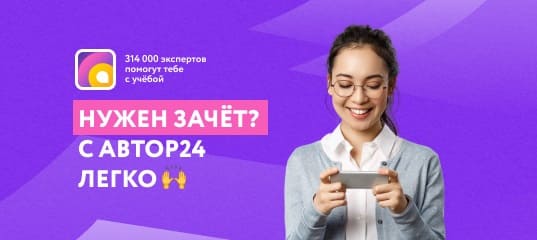
Мы поможем в написании ваших работ!