В СОЛЕСОДЕРЖАЩЕЙ ЧАСТИ ГЕОЛОГИЧЕСКОГО РАЗРЕЗА
Для качественного вскрытия солесодержащей части разреза в скважине и создания благоприятных условий для последующего формирования в ней герметичной крепи буровой раствор должен отвечать следующим требованиям:
1. Не оказывать негативного влияния на горные породы в открытом стволе скважины – не растворять и не разупрочнять солевые и другие горные породы, слагающие стенки, быть насыщенным по наиболее легкорастворимой соли вскрываемого разреза, или по комплексу солей, обеспечивающим минимизацию темпа растворения наиболее легкорастворимой соли.
2. Обладать запасом надежности, т.е. сохранять способность не растворять солевые породы при попадании в него ограниченного количества (до 5% от объема циркулирующего раствора) пресных или маломинерализованных подземных или поверхностных вод.
3. Иметь плотность, достаточную для предупреждения газодинамических явлений при вскрытии солей, создания необходимого противодавления на стенки скважины для предупреждения «течения» солей, способствовать сохранности соляного керна в керноприемной трубе в процессе его отбора.
4. Иметь низкие значения показателей реологических и фильтрационных свойств в широком диапазоне изменения температуры в стволе скважины (устье – забой).
5. Сохранять высокую подвижность и прокачиваемость при низких значениях положительной температуры и при отрицательной температуре.
|
|
6. Не образовывать на стенках скважины корку (пленку), снижающую прочность связи цементного камня с солями и другими породами при цементировании обсадных колонн и производстве ликвидационного тампонажа скважин в солесодержащей части разреза.
7. Не вызывать коррозию оборудования, инструмента и труб зацементированной в предыдущем интервале обсадной колонны.
8. Не содержать в своем составе компонентов, снижающих или искажающих информативность и достоверность выполняемых в скважине геофизических исследований.
9. Быть относительно простым в приготовлении и регулировании в заданном диапазоне значений показателей технологических свойств с учетом конкретных условий его использования.
10. Быть нетоксичным и экологически безопасным для производственного персонала и окружающей среды.
11. Быть экономичным с учетом в каждом конкретном случае задач, решаемых строящейся скважиной.
Сохранение близким к номинальному диаметра скважины при бурении в отложениях легкорастворимых солей может быть достигнуто использованием буровых растворов на углеводородной основе (практически безводных и соленасыщенных инвертных эмульсий) и соленасыщенных растворов на водной основе (рисунок 2).
|
|
Однако при бурении скважин с использованием растворов на углеводородной основе на стенках скважины, а впоследствии и на спускаемых для ее крепления обсадных трубах, налипает углеводорсодержащая пленка, препятствующая в дальнейшем формированию плотного контакта цементного камня, как со стенкой скважины, так и обсадной колонной. Для удаления этой пленки при проведении работ по цементированию обсадных колонн в скважинах необходимо использовать специальные буферные отмывающие составы, которые, как показывает практика, не могут в полной мере обеспечить требуемое качество подготовки ствола скважины. Применение бурового раствора на углеводородной основе также не позволяет в процессе вскрытия соляной толщи получать объективную информацию о содержащихся в ней свободных газов. Кроме того, растворы на углеводородной основе требуют специального оборудования для их приготовления, использования и очистки, они представляют повышенную пожароопасность, трудоемки в применении и экологически небезопасны для персонала и окружающей природной среды.
![]() | |||
|
|
|
Из растворов, использующихся в отечественной практике бурения скважин в соленосных отложениях, в том числе содержащих бишофит и карналлит, перечисленным выше требованиям к буровым растворам в наибольшей степени отвечает магнийсодержащий моносолевой соленасыщенный раствор на водной основе – хлормагниево-фосфатный буровой раствор ХМФБР и полисолевой буровой раствор ПСБР.
ХМФБР представляет собой стабилизированную неорганическими полимерами (оксихлоридофосфатами) соленасыщенную систему, основой которой является водный раствор, насыщенный по хлориду магния.
ХМФБР получают обработкой насыщенного водного раствора бишофита технической ортофосфорной кислотой и каустическим магнезитовым порошком в количестве 0,80-0,85% по массе каждого реагента к объему раствора. Технологическая схема приготовления хлормагниево-фосфатного бурового раствора приведена на рисунке 3.
Существенными отличиями ХМФБР от известных буровых растворов на основе водных растворов хлорида магния являются низкие значения и стабильность во времени показателя фильтратоотдачи, реологических и структурно-механических свойств.
Применение ХМФБР в интервалах залегания калийно-магниево-натриевых солей позволяет обеспечить:
|
|
- получение и сохранение во времени близким к номинальному диаметра скважины в интервале залегания солей;
- получение представительного керна солей различного минерального состава, включая карналлит (рисунок 4);
- предотвращение газодинамических явлений, вызывающих в ряде случаев разрушение стенок ствола скважины;
- получение данных по газосодержанию соляной толщи, которое является одним из показателей, определяющих фактор опасности развития газодинамических явлений при освоении соляного массива [6];
![]() | |||
|
Интервал | Описание пород | Фотография керна | |
Интервал: 313.0-322.0м Проходка =9.0м Керн =9.0м Вынос =100% | Слой 1, толщина 0,4м. Карналлит оранжева-красный, средне и крупнозернистый, зерна неправильной формы, гигроскопичен. | ![]() | |
Слой 2, толщиной 4,9м. Каменная соль серая, белая, с прослоями глины и карналлита оранжево-красного толщиной до 20см. | ![]() | ||
Слой 3, толщиной 3,1м. Карналлит мясо-красный, оранжево-красный, средне и крупнозернистый. | ![]() | ||
Слой 4, толщиной 0,7м. Переслаивание каменной соли и карналлита оранжево-красного. | ![]() | ||
Интервал: 322.0-331.0м Проходка =9.0м Керн =9.0м Вынос =100% | Слой 1, толщиной 2,0м. Карналлит оранжевый, средне и крупнозенистый, брекчивидной формы. | ![]() | |
Слой 2, толщиной 2,8м. Каменная соль серая, светло-серая, полупрозрачная. | ![]() | ||
Слой 3, толщиной 1,6м. Карналлит оранжево-красный средне и крупнозенистый, брекчивидной формы. | ![]() | ||
Слой 4, толщиной 0,6м. Каменная соль серая, светло-серая, полупрозрачная. | ![]() | ||
Рис. 4. Керновый материал, извлеченный в процессе бурения разведочной нефтяной скважины № 779Р Ю-Юрчукской площади на территории ВКМКС
- формирование на поверхностях бурового оборудования, бурильной и обсадной колонн, контактирующих с ХМФБР, защитной фосфатной пленки, препятствующей их коррозии (рисунок 5).
Рис. 5. Фрагменты фосфатной пленки на поверхности обсадных труб в интервале использования ХМФБР
ПСБР представляет собой сбалансированную трехкомпонентную водно-солевую систему (KCl-NaCl-H2O), насыщенную по обеим солям и содержащую их избыток в тонкодисперсном состоянии – в виде рекристаллизованной соли. Насыщенность раствора по обеим солям устанавливается по значению плотности фильтрата – не менее 1235 кг/м3 при температуре +8…+20оС. Необходимое количество рекристаллизованной соли в водно-солевой системе обеспечивается взаимным высаливанием KCl и NaCl (хлористый калий и каменная соль соответственно) при растворении их в воде.
Необходимый уровень стабилизации ПСБР, а также его агрегативная устойчивость обеспечиваются добавкой крахмалосодержащего реагента.
Лабораторными исследованиями и многолетним практическим опытом применения полисолевого раствора доказано, что его использование позволяет:
- полностью исключить растворение каменной соли и сильвинита;
- резко снизить скорость растворения карналлитовой породы и замедлить процесс кавернообразования в интервале ее залегания;
- обеспечить требуемый запас надежности бурового раствора – сохранять насыщенность по KCl и NaCl при попадании в него пресных и слабоминерализованных вод в количестве до 3 % к объему раствора.
Предотвращение растворения галита и сильвинита связано с насыщенностью ПСБР по KCl и NaCl. Резкое замедление скорости растворения карналлитовой породы в контакте с ПСБР обусловлено значительным снижением активности воды в насыщенной водно-солевой системе KCl-NaCl-H2O и блокированием поверхности карналлитовой породы на стенках скважины кристаллами NaCl и KCl вследствие высаливания их при растворении MgCl2. Технологическая схема приготовления полисолевого бурового раствора ПСБР приведена на рисунке 6.
ТЕХНОЛОГИЧЕСКИЕ ЖИДКОСТИ ДЛЯ КРЕПЛЕНИЯ СКВАЖИН В СОЛЕСОДЕРЖАЩЕЙ ЧАСТИ ГЕОЛОГИЧЕСКОГО РАЗРЕЗА
Срок службы нефтяных и газовых скважин как долговременных капитальных горных выработок, сообщающих разрабатываемую залежь с поверхностью земли, определяется, главным образом, надежностью и долговечностью их крепи и, в первую очередь, состоянием во времени основных элементов этой крепи – цементного камня и обсадных колонн, сохранностью во времени плотного контакта цементного камня со стенками скважин и обсадными трубами.
Особенно важно достижение гарантированной надежности и долговечности элементов крепи скважин в условиях, когда районы их строительства и последующего функционирования приурочены к территориям, в недрах которых разрабатываются или предполагаются к разработке подземным способом другие виды полезных ископаемых. В этих условиях разрушение во времени любого из элементов крепи скважины в интервалах нахождения подземных горных выработок может привести к аварийным ситуациям.
Наиболее характерной в этом отношении является территория на севере Пермского края. Здесь в пределах контура распространения промышленных запасов разрабатываемого подземным способом Верхнекамского месторождения калийных солей (ВКМКС) ведутся буровые работы с целью поисков, разведки и разработки нефтяных месторождений, приуроченных к подсолевым отложениям, предполагается сооружение подземного хранилища газа в соляном массиве. Аналогичное сочетание полезных ископаемых (калийные соли и нефть в подсолевых отложениях) характерна для крупнейшей в мире калиеносной провинции на территории Восточной Сибири (Непское месторождение калийных солей).
Особенностью месторождений водорастворимых калийных солей и других, склонных к растворению минеральных солей, является их повышенная уязвимость: сообщение подземных горных выработок соляных рудников с источниками поступления флюидов (поверхностные, грунтовые и пластовые воды) обычно приводят к безвозвратной потере части геологических запасов ископаемых солей, а в ряде случаев – к затоплению и гибели рудников. При ведении буровых работ на территории месторождений солей скважины становятся потенциальными каналами поступления флюидов к соляной толще. Поэтому перекрывающие солесодержащую часть разреза обсадные колонны подлежат тщательному цементированию, гарантирующему долговременное разобщение солесодержащих и водосодержащих горизонтов. Очевидно, что это может быть достигнуто использованием специальных тампонажных материалов, которые обеспечат не только надежную защиту стальной обсадной колонны от высокоагрессивных соляных пород (карналлит, сильвинит, бишофит, каменная соль и др.) и пластовых вод высокой степени минерализации, но и защиту продуктивной соляной толщи от попадания в нее флюидов из надсолевых и подсолевых водоносных горизонтов как на стадии строительства скважин, так и в период их последующей эксплуатации.
Выбор вида и состава тампонажного материала, размещаемого за обсадными колоннами, разобщающими солесодержащую часть разреза от над- и подсолевого водосодержащих комплексов, осуществляется исходя из конкретных горно-геологических и термобарических условий вскрываемого разреза.
Качество крепления глубоких скважин в отложениях водорастворимых минеральных солей определяется степенью соответствия свойств тампонажного раствора-камня, размещаемого за обсадными колоннами в составе крепи скважин, следующим требованиям:
Тампонажный раствор должен обладать:
- низкими значениями показателей реологических и фильтрационных свойств на весь срок выполнения раствором своих функций до момента начала его загустевания в кольцевом пространстве между обсадной колонной и стенками скважины;
- высокой седиментационной стабильностью;
- отсутствием какого-либо негативного влияния на солевые породы, слагающие стенки скважины (в первую очередь – не растворять их);
- отсутствием негативного влияния на материал обсадных труб;
- технологически необходимым временем загустевания и сроками схватывания, регулируемым в относительно широком диапазоне.
При твердении тампонажный раствор должен:
- формировать высокопрочный, низкопроницаемый, безусадочный (расширяющийся) цементный камень, характеризующийся долговечностью в контакте с пресными и маломинерализованными водами, хлоридами магния, калия, натрия и водными растворами этих солей высокой концентрации, а также при воздействии на него пластовых вод с высоким содержанием сероводорода, быть стойким против магнезиальной агрессии;
- формировать высокопрочную кристаллохимическую (адгезионную) связь цементного камня с горными породами (в том числе с солями) и металлом обсадных труб.
Традиционно используемые в практике строительства нефтяных и газовых скважин тампонажные материалы на основе портландцементов, глиноземистых цементов, шлакопортландцементов и др. не отвечают перечисленным требованиям, особенно в отношении коррозионной стойкости цементного раствора-камня в условиях магнезиальной агрессии. Поэтому для разрезов, солесодержащая часть которых включает залежи магнийсодержащих солей (карналлит, бишофит), наиболее легкорастворимых любыми флюидами, не насыщенными по MgCl2, при выборе базового варианта вяжущего предпочтение отдается тампонажным составам на основе магнезиального цемента, характеризующегося высокой устойчивостью к магнезиальной коррозии. Этот цемент используется в практике цементировочных работ при проходке шахтных стволов калийных рудников и для ликвидационного тампонирования скважин при ведении геологоразведочных работ на калийные соли.
Вяжущей компонентой магнезиального цемента (цемента Сореля) является порошок магнезитовый каустической ПМК, в составе которого содержится не менее 75% оксида магния MgO. ПМК является пылеуносом процесса обжига природного магнезита MgCO3 при температуре 600-800 оС. При хранении на воздухе ПМК теряет активность вследствие образования на поверхности его частиц MgCO3 и Mg(OH)2 в результате взаимодействия оксида магния с влагой воздуха и содержащимся в нем углекислым газом.
Для получения вяжущей системы порошок магнезитовый каустический затворяется водным раствором хлорида магния (бишофита MgCl2·6H2O). В результате протекания в системе физико-химических процессов образуется быстротвердеющая композиция, преимущественно состоящая из метастабильного пентаоксихлорида магния 5Mg(OH)2·MgCl2·8H2O. Кроме этого соединения, в зависимости от соотношения исходных компонентов, термобарических условий и ряда других факторов, в продуктах твердения реакционной массы могут присутствовать не прореагировавший оксид магния, гидроокись магния и стабильная форма – триоксихлорид магния 3Mg(OH)2·MgCl2·8H2O.
Магнезиальные цементы относятся к воздушным вяжущим, т.е.могут твердеть и сохранять прочность в воздушно-сухой среде. Систематическое их увлажнение в контакте с водами невысокой степени минерализации быстро приводит к разрушению цементного камня. Начало и ход процесса разрушения обусловлен повышением рН жидкости, контактирующей с цементным камнем, за счет растворения в ней гидроокиси магния, которая образуется за счет запоздалой гидратации не прореагировавших частиц MgO в цементном камне. В результате происходит восстановление частично окисленного иона хлора в составе оксихлорида до начального валентного состояния, приводящее к разложению оксихлорида на легко вымываемый MgCl2 и не обладающую вяжущими свойствами гидроокись магния Mg(OH)2.
Магнезиальные вяжущие в чистом виде являются быстросхватывающимися и быстротвердеющими. Сроки схватывания составляют: начало – не менее 20 минут, конец – не более 6 часов (при затворении ПМК водным раствором хлорида магния плотностью 1200 кг/м3). Прочность цементного камня магнезиального вяжущего через сутки достигает 35-50%, а через 7 суток – 60-90% наибольшего значения при твердении в воздушной среде при температуре 20±2 оС.
При выборе базового вяжущего в качестве основы для разработки составов тампонажных систем, используемых при креплении скважин в отложениях солей, предпочтение отдано магнезиальным цементам потому, что они не только являются коррозионно-устойчивыми к магнезиальной коррозии, но в наибольшей степени отвечают перечисленным выше требованиям к тампонажным материалам, т.к. они:
- имея в качестве жидкости затворения высококонцентрированный водный раствор хлорида магния, не растворяют ни одну из солей в стенках скважины (карналлит, сильвинит, бишофит, галит) при движении тампонажного раствора в заколонном пространстве;
- в течение короткого промежутка времени формируют высокопрочный цементный камень;
- характеризуются повышенной адгезией практически ко всем горным породам вскрываемого разреза и металлу обсадных труб.
К недостаткам, присущим раствору-камню магнезиальных цементов в чистом виде с позиций перечисленных требований к тампонажным материалам, следует отнести: короткие сроки схватывания, невысокую коррозиеустойчивость в контакте с пресными и маломинерализованными водами, усадочные явления в твердеющем камне. Однако, все они устраняются изменением соотношения исходных материалов тампонажной композиции и включением в ее состав химических реагентов и добавок, направленно изменяющих свойства тампонажного раствора-камня.
Например:
- сроки загустевания и схватывания магнезиального тампонажного раствора регулируются изменением активности порошка магнезитового каустического, смешиванием порошков различной активности, вводом в сухую смесь инертных наполнителей, изменением плотности и температуры жидкости затворения и т.д.;
- водостойкость повышается использованием фосфорсодержащих реагентов;
- усадка цементного камня устраняется вводом противоусадочных добавок, использованием которых достигается формирование расширяющегося цементного камня.
Знание характера и степени влияния перечисленных технологических приемов регулирования свойств магнезиального тампонажного раствора-камня позволяет оптимизировать состав, режим приготовления и использования тампонажного раствора с учетом конкретных условий и видов выполняемых тампонажных работ при строительстве и эксплуатации скважин.
Технологические схемы приготовления РМФТМ (расширяющегося магнезиально-фосфатного тампонажного материала), предназначенного для использования при цементировании обсадных колонн, перекрывающих солесодержащую часть разреза в скважинах на территории ВКМКС, и РМФТМ-МКП (расширяющегося магнезиально-фосфатного тампонажного материала), предназначенного для цементирования межколонного пространства между технической и эксплуатационной колоннами в скважинах на территории ВКМКС, приведены на рисунках 7, 8.
Значения показателей свойств раствора и формирующегося цементного камня магнезиальных тампонажных материалов приведены в таблице 3.
Жидкость затворения Сухая тампонажная смесь
Жидкость затворения Сухая тампонажная смесь
Таблица 3
Наименование показателя | Значение | |
РМФТМ | РМФТМ-МКП | |
Тампонажный раствор: 1. Плотность, кг/м3 2. Начальная консистенция, УЕК, не более 3. Условная вязкость (УВ100), с, не более 4. Фильтратоотдача, см3/30 мин, не более 5. Седиментационная стабильность, кг/м3, не более 6. Время загустевания до 30 УЕК, мин, не менее 7. Сроки схватывания, час-мин начало, не ранее конец, не позднее Цементный камень: 1. Увеличение объема цементного камня через 2 суток твердения (отсчет производится с момента начала схватывания тампонажного материала), % 2. Предел прочности на сдвиг с наружной огибающей поверхностью через 2 суток твердения, МПа, не менее 3. Предел прочности при изгибе через 2 суток твердения при температуре 20±1оС, МПа, не менее 4. Предел прочности при изгибе через 3 суток твердения при температуре 8±1оС, МПа, не менее 5. Проницаемость, 10-3 ×мкм2 | 1760-1850 6,0 60 12,0 60 90 2-00 10-00 0,3-1,2 0,8 2,7 2,7 0,2-0,4 | 1830-1890 9,0 80 не реглам. 10 90 2-00 6-00 0,3-1,2 1,0 6,0 7,0 0-0,4 |
С 1976 года бурение глубоких нефтяных скважин на территории ВКМКС в солесодержащем интервале, перекрываемом технической колонной, осуществляется с использованием в качестве промывочной жидкости насыщенного по хлориду магния хлормагниево-фосфатного бурового раствора ХМФБР и полисолевого бурового раствора ПСБР – водно-солевой системы, насыщенной по хлоридам натрия и калия. Эти буровые растворы, разработанные специально для условий разреза ВКМКС, в наибольшей степени отвечают перечисленным выше требованиям обеспечения высокого качества вскрытия солей и сохранности близким к номинальному диаметра скважины в солесодержащей части разреза.
С использованием ХМФБР вскрывалась солесодержащая часть разреза во всех скважинах, пробуренных до 1981 года (31 скважина). С 1981г. по 1986г. (период проведения опытных работ по освоению технологии приготовления и использования ПСБР) ХМФБР использован при бурении 74 скважин, ПСБР – при бурении 35 скважин.
С 1987 г. – с момента ввода в действие РД 39-0148369-6.033-86 – основной объем бурения под техническую колонну выполнен с использованием в качестве промывочной жидкости ПСБР. Только в скважинах, где бурение по продуктивной соляной толще велось с отбором керна (скважины ОГН и первые в кустах), в качестве промывочной жидкости в интервале отбора использовался ХМФБР. Этим обеспечен вынос 90-100 % керна из солевых отложений за счет более высоких, чем у ПСБР, значений плотности и смазывающей способности.
Суммарная проходка с использованием указанных растворов в 970 скважинах, пробуренных с апреля 1976 г. по декабрь 2009 года, составила около 630 тыс. метров, из них около 408 тыс. метров пройдено по солевым отложениям, в том числе почти 37,3 тыс. метров – в отложениях калийно-магниевых солей.
Для проведения анализа и оценки качества вскрытия солесодержащей части разреза ВКМКС глубокими нефтяными скважинами использованы результаты по скважинам, для которых в полном объеме имеется исходная информация, необходимая для качественной характеристики состояния ствола скважин, построенных на участках ВКМКС с нормальным разрезом. Этот разрез отличается наличием в нем надсолевой водозащитной толщи (соляно-мергельная толща + покровная каменная соль), продуктивной карналлито-сильвинитовой толщи и подсолевой водозащитной толщи (подстилающая каменная соль + глинисто-ангидритовая толща). Таких скважин на различных участках территории ВКМКС за рассматриваемый период пробурено 687.
О качестве вскрытия солесодержащей части разреза и водозащитных толщ с использованием буровых растворов ХМФБР и ПСБР свидетельствуют значения коэффициента кавернозности ствола скважины (табл. 4): в целом для интервала бурения под техническую колонну в большинстве скважин (94 %) он находится в пределах значений до 1,16, а для интервала залегания отложений калийно-магниевых солей – до 1,24 в 86 % скважин. Достижением таких результатов вскрытия солесодержащей части разреза в пробуренных скважинах создаются благоприятные условия для обеспечения высокого качества цементирования технических колонн, перекрывающих соляную толщу и разобщающих ее от флюидосодержащих отложений разреза территории ВКМКС.
Таблица 4
Дата добавления: 2021-04-24; просмотров: 397; Мы поможем в написании вашей работы! |
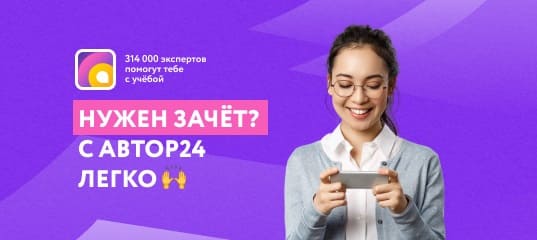
Мы поможем в написании ваших работ!